Fertilizer International 494 Jan-Feb 2020
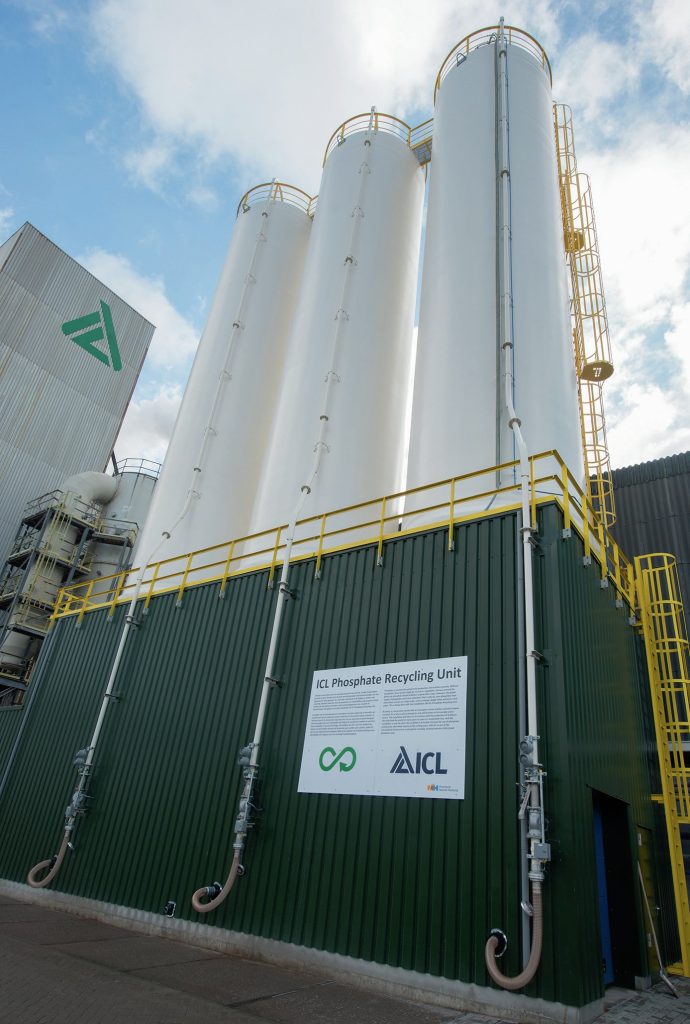
31 January 2020
Fertilizer production goes green
GLOBAL STEWARDSHIP
Fertilizer production goes green
Leading nitrogen and phosphate producers, including ICL, OCP and Yara, have all launched major sustainable fertilizer production projects. The aim is to incorporate recovered nutrients or low-carbon feedstocks into their manufacturing processes.
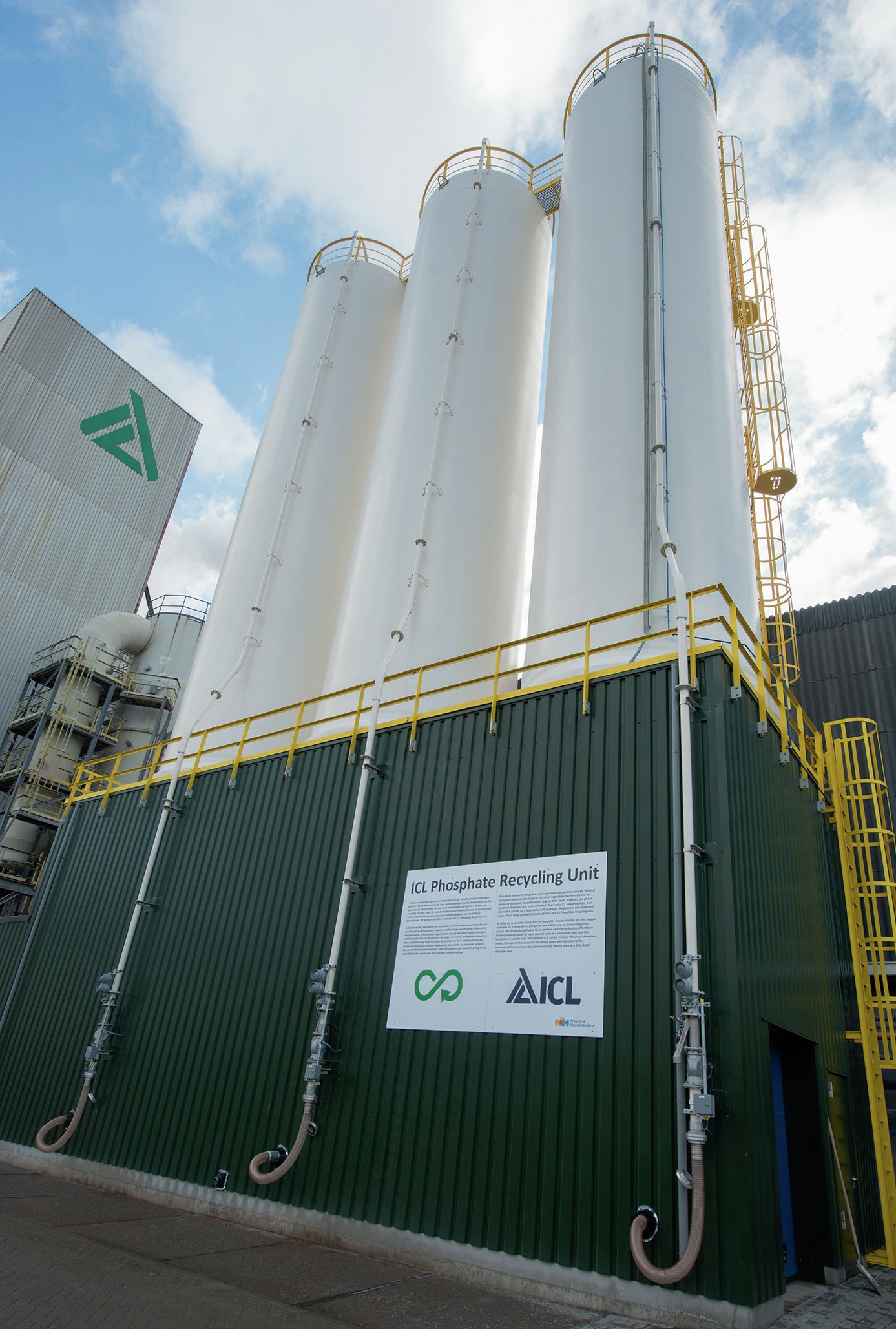
The last 18 months has been a breakthrough period for fertilizer industry sustainability. A number of major fertilizer producers, in tandem with leading technology providers, have committed themselves to incorporating low-carbon feedstocks and/or recovered nutrients into their manufacturing processes.
Fertilizer majors such as Yara International have gone outside of the sector to find world-class partners with expertise in low-carbon-technology and the circular economy. They include waste management giant Veolia, Nel Hydrogen – the world’s largest electrolyser manufacturer – and the French multinational electrical utility ENGIE.
Such partnerships demonstrate the fertilizer sector’s seriousness about developing new sustainable production technologies and implementing these commercially at large-scale. In this article, we describe how the fertilizer industry is embracing the circular economy and starting an irrevocable shift towards a low-carbon future.
Europe at the vanguard
European-based companies and institutions, in particular, are leading the way when it comes to taking practical steps towards low-carbon fertilizer production and nutrient recovery. Casale, Haldor Topsoe and thyssenkrupp Industrial Solutions, for example, are all developing ‘green’ ammonia production processes (Fertilizer International 488, p33).
Fertilizers Europe helped set the tone by launching ‘Feeding Life 2030’, its new long-term strategy for the European fertilizer industry at the end of 2018.
The strategy, released to coincide with the trade association’s 30th anniversary, has two major themes: firstly, the importance of plant nutrients in moving towards a more productive, sustainable food system in future and, secondly, the need to shift to lower-carbon or carbon-free fertilizer manufacturing, particularly for ammonia production.
The future of EU farming will involve “applying more knowledge per hectare”, according to the strategy, an approach which echoes Yara International’s “knowledge grows” ethos.
“Rapid technological development and innovation offer the prospect of meeting future food needs more sustainably. Digital farming offers big potential for further progress in nutrient management in Europe,” said Javier Goñi del Cacho, president of Fertilizers Europe and Fertiberia’s CEO.
Fertilizer manufacturing in Europe will also need to reduce its carbon footprint to meet EU climate and energy policy objectives. The strategy sets out a vision in which around 10 percent of the EU’s ammonia production by 2030 will come from hydrogen generated by water electrolysis powered by renewable energy. Large-scale and low-cost production of ammonia via water electrolysis – the so-called ‘green’ ammonia route – could be economically-viable within a decade, according to some estimates.
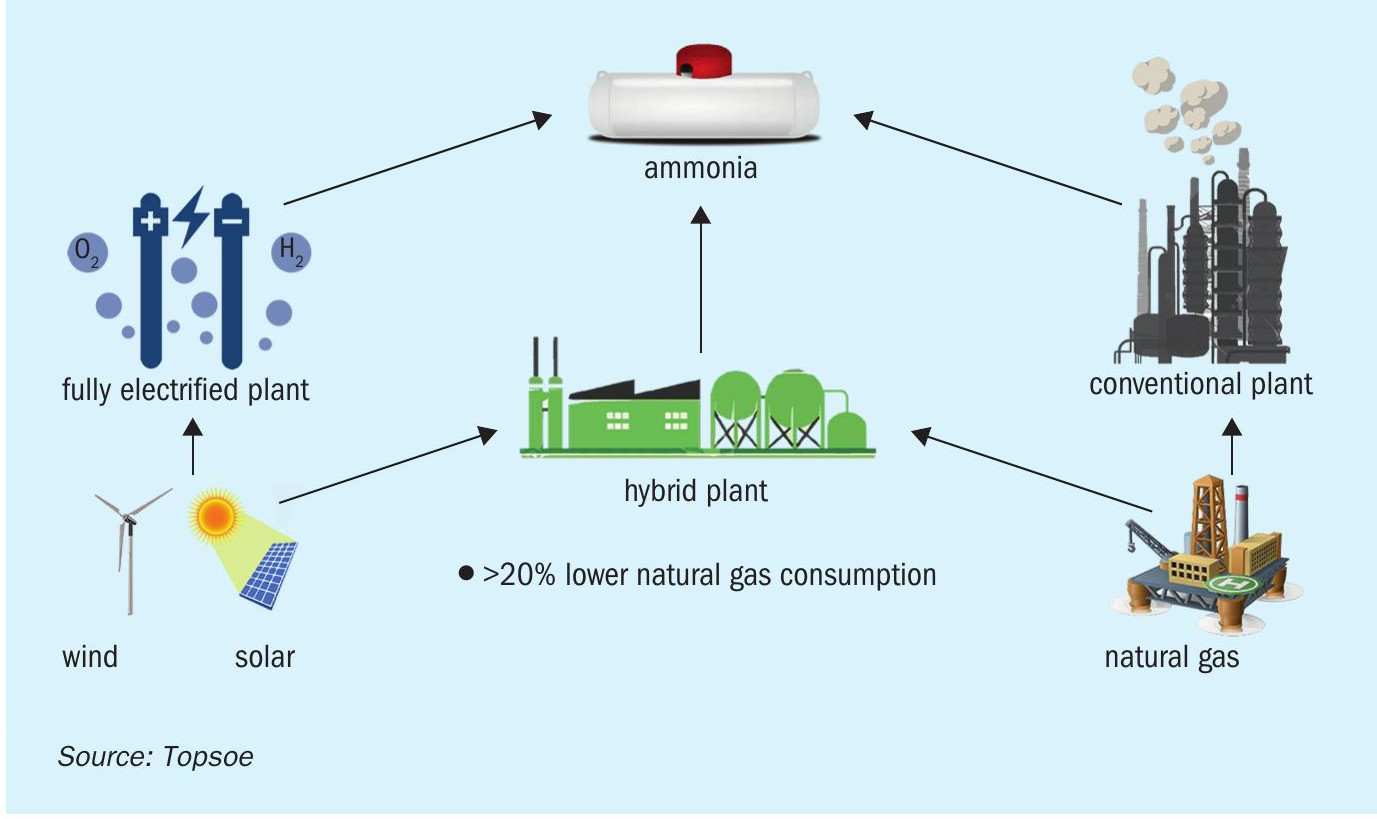
The strategy also proposes a valuable role for ammonia as a liquid energy carrier and storage medium, to help level-out the fluctuations in intermittent renewable electricity generation.
“Europe is forging ahead with the transition to clean energy, and is relying increasingly on renewable energy sources. We are a part of this drive. The nitrogen fertilizers industry, as a producer of ammonia, offers the key to unlocking clean energy potential by acting as a carbon-free energy storage medium,” commented Javier Goñi del Cacho.
‘Feeding Life 2030’ is aligned with EU policy for a decarbonised and carbon-neutral European economy by 2050. This is to be achieved by a mix of energy efficiency, higher renewable electricity generation, adoption of low-carbon energy carriers, and carbon pricing.
Europe should be well-placed to take advantage of any shift to green ammonia production as the region has world-leading engineering companies for both wind power generation and water electrolysis. thyssenkrupp Industrial Solutions (tkIS), for example, is a global leader in the manufacture of large-scale electrolysis units.
One pathway for introducing and rolling-out green ammonia technology is installing water electrolysis units as part of revamps, creating hybrid steam methane reforming (SMR)/electrolysis ammonia plants (Figure 1).
Conventional SMR could also be converted into a carbon-free production process using carbon capture and storage (CCS) – the so-called ‘blue’ ammonia route. CCS may become a reality in parts of Europe by 2030, suggests Fertilizers Europe.
The use of ammonia as a liquid energy carrier could also grow into a lucrative end-market for European producers. Such a development could help Europe’s nitrogen industry diversify and become an important and integral part of the EU’s emerging low-carbon energy infrastructure.
Yara creates low-carbon and circular economy business units
In January 2019, Norway’s Yara International stepped up its sustainability efforts by creating two new business units. The two units, Decarbonise and Circular Economy, are headed by Sam Van Den Broeck and Maria Silvia Tonti, respectively.
The Decarbonise unit has been given the task of reducing Yara’s overall greenhouse gas (GHG) emissions. Its role will include the ramp-up of zero carbon nitrogen (e.g. green ammonia) production, reducing in-field agricultural GHG emissions and developing green energy carriers. The Circular Economy unit will take a lead on resource efficiency – doing more from less. It will also seek to generate value from waste through nutrient recovery and recycling.
Yara kick-started its decarbonisation efforts in February last year by unveiling a new partnership with giant French electricity utility ENGIE. The focus of this new collaboration will be the use of green technology in fertilizer production.
The two companies are initially working together on a feasibility study. The goal is to design a green hydrogen plant that can be integrated with Yara’s existing ammonia plant in Pilbara, Western Australia. The Pilbara region is the ideal location for the study, says Yara, due the abundance of sun and seawater – the two key constituents in renewable hydrogen production.
The ultimate goal is to convert the Pilbara plant from its complete reliance on natural gas to an ammonia plant that sources a significant share of its hydrogen needs from renewable power instead. Achieving this goal will help Yara cut Pilbara’s CO2 emissions.
The two partners have much to gain from the new collaboration. ENGIE’s is aiming to become a major player in renewable hydrogen, for example, while Yara is stepping up efforts towards making carbon-free fertilizers. Renewable hydrogen generation is the starting point for CO2 -free ammonia production – green ammonia – which in turn is a key ingredient for carbon-free fertilizer production.
“Yara and ENGIE have the complementary expertise and experience to take on such a complex project, but the key ingredient in this venture is our mutual commitment to a healthier planet and a sustainable future,” said Yves Bonte, Yara’s executive vice president for new business.
“This project is in line with ENGIE’s goal to be a pioneer in the new energy world, a decarbonized world, accessible to everyone everywhere,” added Michèle Azalbert, the CEO of ENGIE Hydrogen.
Because renewable electricity generation from solar and wind sources is highly variable, green hydrogen looks set to become a key component in future energy networks. But reducing the costs associated with producing, storing and transporting green hydrogen will be vital for its future deployment. Valuably, the green hydrogen plant at Yara Pilbara will allow a real-world, real-time analysis of costs and processes.
“Together, Yara and ENGIE are acting to better understand how to make green hydrogen technology work. For Yara, it is of particular importance to understand how this can help us to make our fertilizers carbon-free at an acceptable cost,” said Bonte, in conclusion.
Yara has also taken a first step towards integrating fertilizer production within Europe’s emerging circular economy. Last January, it signed an agreement with French conglomerate Veolia to develop a circular economy approach to nutrient recycling, one that involves the creation of nutrient loops.
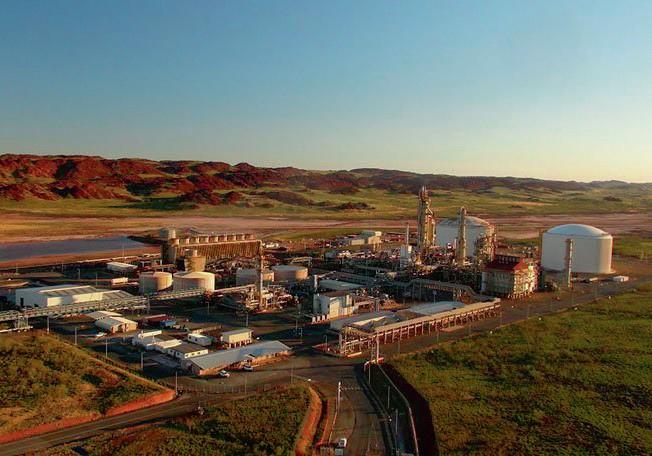
The idea is to integrate Veolia’s access to growing volumes of recovered nutrients – and its expertise in organic materials handling – with Yara’s mineral fertilizer production expertise and crop nutrition knowledge. The new partnership hopes to begin closing the nutrient cycle by joining together the start and the end of today’s linear food production chains.
“Reducing global resource depletion and nutrient loss by increasing the recycling of nutrients such as nitrogen and phosphorus is an important task,” commented Svein Tore Holsether, president and CEO of Yara. “The collaboration with Veolia is a contribution to our mission to responsibly feed the world and protect the planet.”
Veolia and Yara have agreed to work together to scale-up nutrient recycling. This will require new business models for highquality fertilizer production based on nutrient recycling. The local recovery, processing, distribution and sales of nutrient products will be a cornerstone of the new circular economy approach.
The two companies will also create reverse ‘food-to-agriculture’ value chains by collecting and processing food surpluses in cities. This will link together the organic fertilizer expertise of Veolia subsidiary Sede Angibaud with Yara’s market knowledge of organomineral fertilizers and soil improvement products – for both rural and peri-urban agricultural markets. Finally, Veolia and Yara will also develop new business opportunities based on industrial symbiosis. The goal will be to integrate nutrient and chemical flows between different industrial companies and sectors, by exchanging by-products, raw materials and waste.
“We are delighted that Yara has chosen Veolia to support its circular economy strategy. Veolia and Yara already aim to have several new initiatives fully operational by 2024, including the launch of new fertilizer products and the start-up of nutrient recovery installations in several major European cities.” said Veolia chairman & CEO Antoine Frérot. “The collaboration between our companies is a step closer to effectively closing the nutrient cycle.”
A circular economy loop, which recycles ammonia by composting green waste and wastewater sludge, has already been set up by Yara and Veolia. The recycled ammonia is processed to produce sodium nitrate. This chemical is then reused in wastewater treatment plants to prevent odour and corrosion.
The new EU fertilising products regulation will permit and promote the use of recovered nutrients in crop nutrition products. Several EU member state are also putting in place their own national regulations limiting waste disposal and mandating nutrient recovery.
The economic potential of nutrient recycling in the European fertilizer market could be as high as two billion euros, according to some estimates.
To encourage a fundamental redesign of the food value chain, Yara and Veolia are creating an umbrella group, the Nutrient Upcycling Alliance. Farmer associations, food brands, retailers, waste stream managers, and municipal and government bodies, will all be invited to join.
Porsgrunn green ammonia project
Yara International has teamed up with Nel Hydrogen to pilot water electrolysis technology at its Porsgrunn ammonia plant in Norway. The two Norwegian companies are collaborating on the installation of a five megawatt (MW) capacity electrolyser at the Porsgrunn plant by 2022. This is expected to contribute around one percent to Porsgrunn’s hydrogen output initially.
Nel’s next-generation, pressurised alkaline water electrolyser technology will be tested by Yara under real operating conditions as part of a collaborative project unveiled in August 2019. The goal is to produce hydrogen commercially using renewable electricity. This in turn will be used for either sustainable fertilizer production or the production of green ammonia.
The project is supported by Norway’s Research Council, Innovation Norway and Enova through the PILOT-E programme – a funding scheme that aims to speed-up the development and implementation of green energy technology.
Yara views the link-up with Nel as an important step towards it ambition to become carbon neutral by 2050.
“We’re excited to formally launch the partnership with Nel and work towards developing green ammonia and low carbon fertilizer. We have already removed about half of our direct GHG emissions in the past few decades, and we’re working towards carbon neutrality by 2050. Producing fertilizer with carbon-free hydrogen will be a very important step towards that goal,” said Yara’s Tove Andersen, its executive vice president for production.”
“We are very pleased with the partnership with Nel. Our ammonia plant will make the first small step towards carbon-free fertilizer production. When further developed, Yara Porsgrunn will be in a unique position also due to the low carbon footprint from our nitric acid plants,” added Jon Sletten, the Porsgrunn plant’s manager.”
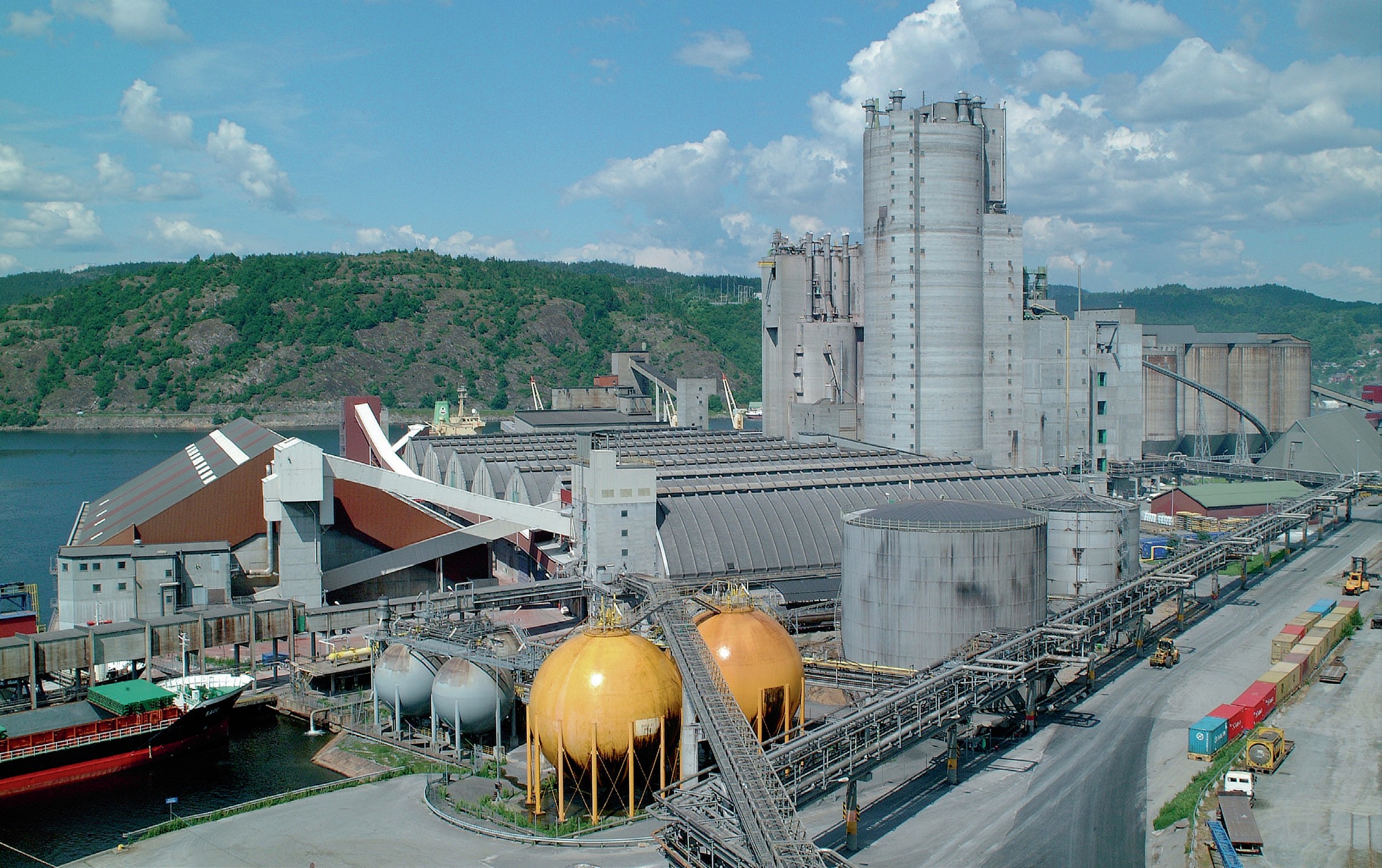
Water electrolysis holds the key
Yara says its ultimate goal is to be a “market shaper” for green ammonia and low-carbon fertilizer production. Nel Hydrogen, being the world’s largest electrolyser manufacturer, should be a strong partner in helping bring this about.
Nel can trace its roots back to 1927, when Norsk Hydro – the company which later became Yara – first developed largescale electrolysers to generate hydrogen to produce ammonia for fertilizer manufacture. Nel has sold more than 3,500 electrolyser units in 80 countries globally since it first began selling these in the 1970s.
Today, Nel manufactures both alkaline and PEM (proton exchange membrane) electrolysers, and operates production plants in both Notodden, Norway, and in Wallingford, Connecticut in the US. The company is currently developing the next generation of large-scale, pressurised alkaline electrolysers as well as larger PEM stacks. These should help deliver substantial cost reductions.
Nel has also unveiled plans to scale-up its manufacturing capacity by opening a new production plant for alkaline electrolysers at Herøya Industrial Park in Norway. This should increase its electrolyser production capacity by 360 MW/year initially, with a further potential expansion to 1 GW/year in future.
Green ammonia is a hot industry topic currently, particularly in Europe. Another low-carbon energy collaboration, this time in the Netherlands, was announced between Proton Ventures and Duiker Combustion Engineers (CE) in July last year. The strategic link-up will turn green ammonia – generated by Proton’s mini ammonia plants from renewable electricity – into high temperature heat using Duiker CE’s stoichiometry controlled oxidation (SCO) technology.
Hans Vrijenhoef, CEO Proton Ventures, said: “The SCO technology of Duiker CE opens new possibilities in applying local ammonia production… such as the conversion of power plants to cleaner fuels.”
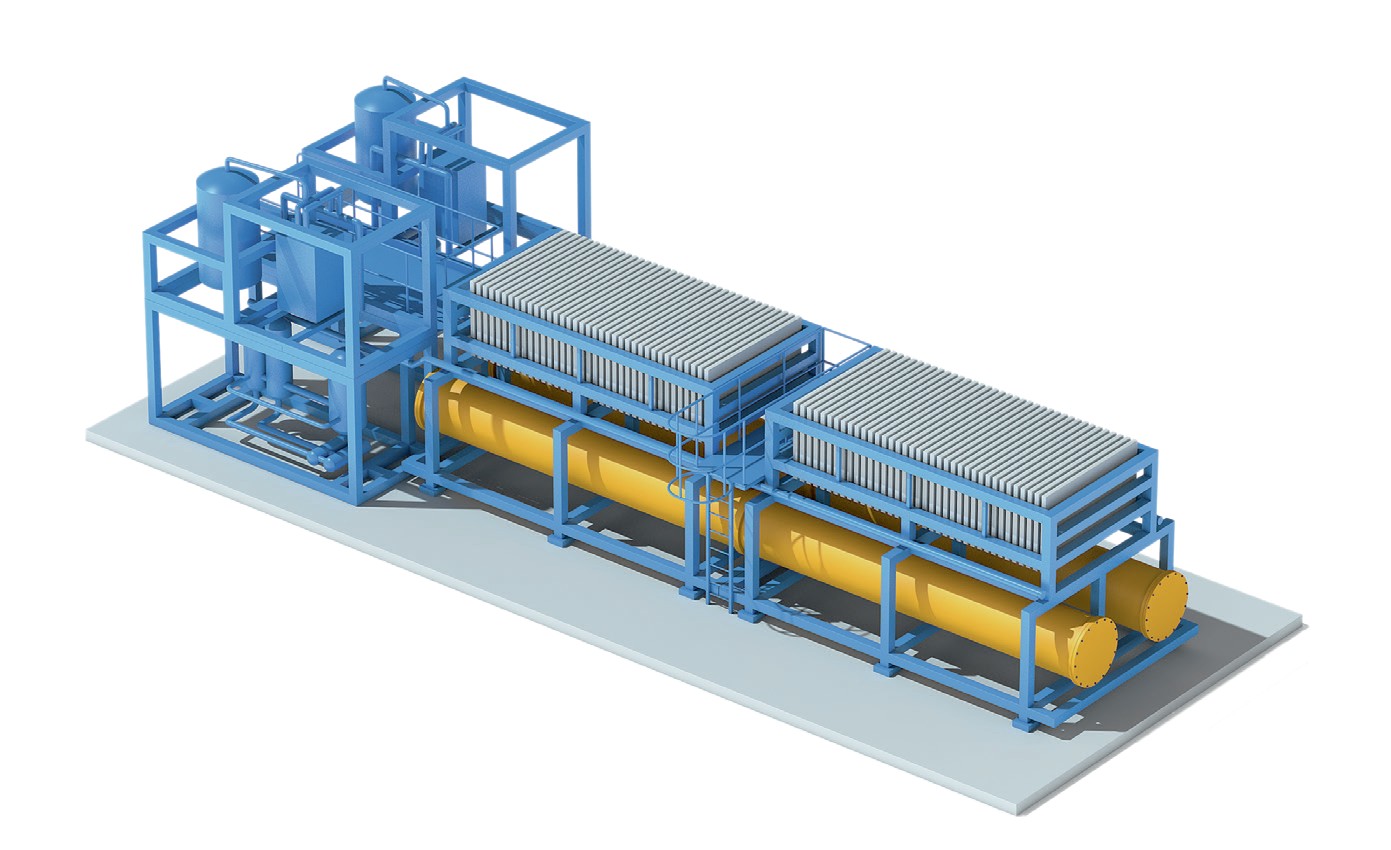
thyssenkrupp launches new water electrolysis tech
Germany engineering giant thyssenkrupp is also focussed on making hydrogen production from renewable energy economically feasible. The company launched a new industrial-scale water electrolysis unit in mid-2018.
The new highly-economical electrolysis unit developed by thyssenkrupp produces hydrogen at scale by using a large area active cell (2.7 m2 ) at an efficiency of more than 82 percent. The innovative cell incorporates ‘zero-gap’ technology which almost eliminates the distance between electrodes and the membrane.
Sami Pelkonen, CEO of the electrolysis and polymers technologies business unit at thyssenkrupp Industrial Solutions said: “With our water electrolysis process, we have successfully brought a technology to market maturity which is of major significance for the energy transition. Green hydrogen, as a clean, CO2 -free starting point, can be used in a variety of ways: for energy storage, mobility, and the production of sustainable chemicals.”
Importantly, the technology is modular. The pre-fabricated skid-mounted modules are easily integrated into existing plants (Figure 2). Projects can be scaled-up by adding a number of these modules, potentially delivering hundreds of megawatts of capacity. The technology has already been commissioned successfully as part of thyssenkrupp’s Carbon2Chem project. This is using steel production emissions as raw materials for chemical production.
Haldor Topsoe unveils green ammonia project
Haldor Topsoe, is collaborating with academia and industry on the new SOC4 NH3 research project. The partners are developing solid oxide cell electrolysis for CO2 -free green ammonia production. The project is aiming to demonstrate the technology and bring it closer to commercial breakthrough.
Topsoe, a world-leader in electrolysis technology and ammonia production, is heading the DKK 26.8 million project. The University of Aarhus, Technical University of Denmark, Energinet, Vestas, Equinor and Ørsted Wind Power are other participants. The Danish Energy Technology Development and Demonstration Program (EUDP) is backing the project through DKK 15.9 million of funding support.
“We expect that ammonia can be used for transportation and efficient storage of energy. The greatest advantage of ammonia is that it has a high energy density which makes it an effective fuel and energy storage option – and it can thereby solve some of the most important challenges of creating a sustainable energy system of the future,” said project leader, John Bøgild Hansen, senior principal scientist at Haldor Topsoe.
“Ammonia can be used for transportation and efficient storage of energy. The greatest advantage of ammonia is that it has a high energy density…”
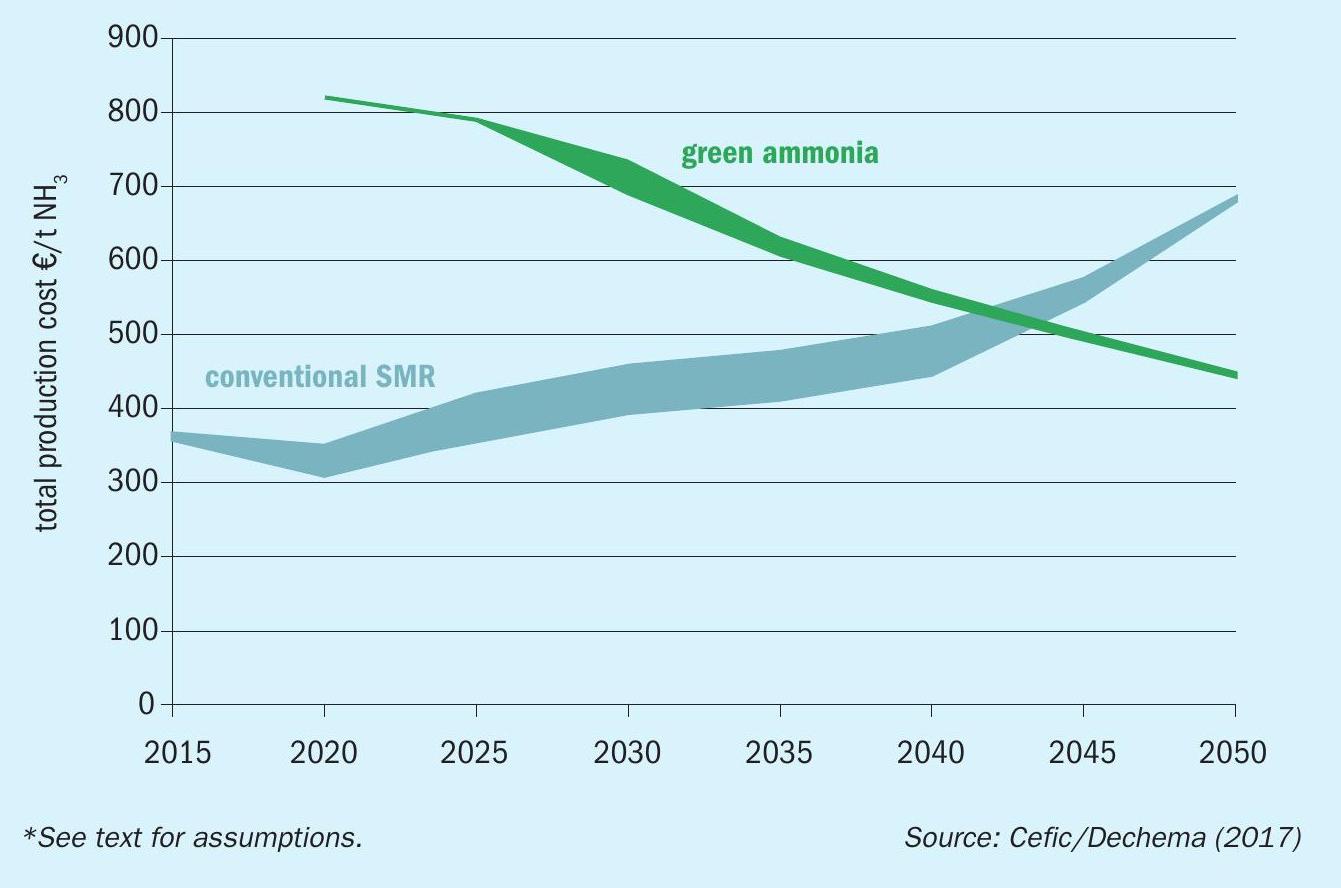
“In the Foulum research facility we will demonstrate an especially efficient technology which will enable us to produce ammonia solely by using certified wind-power, water and air. The method is much more climate-friendly than conventional ammonia production which today makes up as much as one per cent of the world’s total energy consumption and CO2 emissions,” said Lars Ottosen, head of biological and chemical engineering, University of Aarhus.
”We see an interesting potential in using ammonia for creating more stable green energy production – one that can be stored – and at the same time start electrifying heavy transport and the chemical industry. With more than 100 GW wind energy installed all over the world, Vestas has demonstrated that wind energy can deliver the large amounts of energy necessary to convert other sectors to a sustainable future,” added Bo Svoldgaard, senior vice president, innovation & concepts, Vestas.
The SOC4 NH3 project plans to make a major contribution to the energy transition. In doing so, it hopes to strengthen Denmark’s leading international position in renewables and other green technologies – providing the country with a strong foundation for future growth, exports and jobs.
Cost reductions and investment crucial
Cefic, the European Chemical Industry Council, published a landmark study on low-carbon energy and feedstocks in 2017. This set out a pathway for the transition of Europe’s chemical sector to carbon neutrality by 2050 (Fertilizer International 483, p20).
The Cefic study suggested that green ammonia produced using renewable energy could become cost-competitive with conventional ammonia production in Europe within 20-25 years (Figure 3). This would require green ammonia production costs to fall below e500/tonne – plus a number of major assumptions, including:
- A stable electricity price of around e40/ MWh
- Drastic falls in the investment (capex) cost of water electrolysis units from e1,450/kW to e375/kW
- A large rise in the carbon price (CO2 emissions certificates) in Europe to e196/tCO2 .
If and when the above conditions are met, the massive ramp-up of investment necessary is likely to be the main barrier to the low-carbon transition. Cefic calculated, for example, that an industry-wide transition to green ammonia in Europe – in terms of retrofitting and new plant capacity – could be as high as e76.6 billion out to 2050. That is 7-8 times higher than the business-asusual investment of e9.1 billion expected over the next 30 years. These figures do not include the extra investment necessary to decarbonise urea production, potentially an additional e32.9 billion (Fertilizer International 483, p20).
OCP targets renewable feedstocks
Morocco’s OCP Group has launched its own ‘green’ fertilizer production initiative in collaboration with Germany’s Fraunhofer Institute.
The two partners will work jointly on producing hydrogen and ammonia using renewable electricity. The collaboration forms part of memorandum of understanding (MoU) between OCP Group and the Fraunhofer Institute for Microstructure of Materials and Systems (IMWS) signed in 2018.
Fraunhofer IMWS will help OCP to develop a green ammonia project at the Green Energy Park in Ben Guerir, Morocco. The option of establishing an African Institute for Solar Ammonia is also being discussed. A pilot plant to produce hydrogen from renewable sources is already being built in Leuna, Germany, as part of a project led by the Fraunhofer Institute.
Professor Ralf Wehrspohn, director of Fraunhofer IMWS, said: “Green hydrogen and green ammonia offer tremendous potential to… supply raw materials to the fertilizer industry. They also reduce the industry’s dependency on oil, natural gas and any other fossil fuel.”
Mostafa Terrab, OCP Group’s chairman, said: “Responsibility for the environment has always been important to us… as a fundamental principle of our circular economy approach. The use of green ammonia fits in with this strategy. It can help conserve valuable resources and provide our customers with sustainable new products. That’s why we are looking forward to strengthening our cooperation with Fraunhofer.”
ICL opens phosphate recycling unit
ICL opened an innovative phosphate recycling unit at its Amsterdam fertilizers production site in the Netherlands in 2019.
In an industry first, the new unit allows ICL to incorporate recovered phosphate from secondary sources in the industrial-scale production of phosphate-based fertilizers.
The unit, which uses large-scale alternative sources of phosphate such as sewage sludge ashes and bone meal ashes, was formally opened by officials from the City of Amsterdam and the province of North Holland in March last year.
ICL described the unit as a “circular innovation” and an example of the company’s strong commitment to sustainability.
“By using phosphate from alternative sources, we provide society with an innovative circular solution and also prepare ourselves for a future where phosphate rock will become an increasingly scarce source. This installation will allow ICL to continue with the production of fertilizers that help feed the world for many years to come in a sustainable way,” ICL said in a statement.
The company made clear that the unit was just the start of its plans: “Our ambition is to further increase the use of phosphate coming from alternative sources in the coming years, with ICL as one of the international frontrunners in phosphate recycling.”
ICL to sell recovered nutrients
ICL Specialty Fertilizers have also entered into a long-term sales and distribution agreement and strategic partnership with Vancouver-headquartered Ostara Nutrient Recovery Technologies.
As part of these new agreements, ICL will now market and sell Ostara’s Crystal Green, a struvite-based phosphate fertilizer, into the EU, supplying the turf and lawncare markets.
Crystal Green is recovered from municipal wastewater at 15 plants worldwide using Ostara’s Pearl technology. It is a continuous-release fertilizer incorporating the company’s trademarked Root Activated phosphorus.
Advantageously, Crystal Green contains virtually no cadmium or other heavy metals. It also only releases phosphorus, nitrogen and magnesium in response to the organic acids produced by growing roots. This ensures that phosphorus is available for uptake when required by plants, while at the same time reducing the environmental impact caused by leaching and nutrient run-off.
“It is more important than ever before to grow higher quality turf grass with lower inputs, and we at ICL Specialty Fertilizers are dedicated to bringing new products and technologies to our global network that support this philosophy,” said ICL spokesman Arne Padt. “Our partnership with Ostara provides ICL Specialty Fertilizers access to a unique, clean, circular economy phosphorus source with a technology that has proven to give better rooting to turf grass than traditional phosphorus sources.”
Padt added: “As phosphorus is recognized by the EU as a critical raw material, ICL Specialty Fertilizers is proud to use this clean phosphorus source derived from recycling.”
“Ostara is forging the path in resource recovery and reuse. Together [with ICL Specialty Fertilizers] we are excited to offer the European market a product that exemplifies the circular economy concept while also improving plant health,” said Molly Biedenfeld, Ostara’s vice president for nutrient market development and sales. “With the EU’s increased scrutiny of cadmium levels and other heavy metal concentrations in fertilizer, Crystal Green is uniquely positioned to benefit EU market participants.”
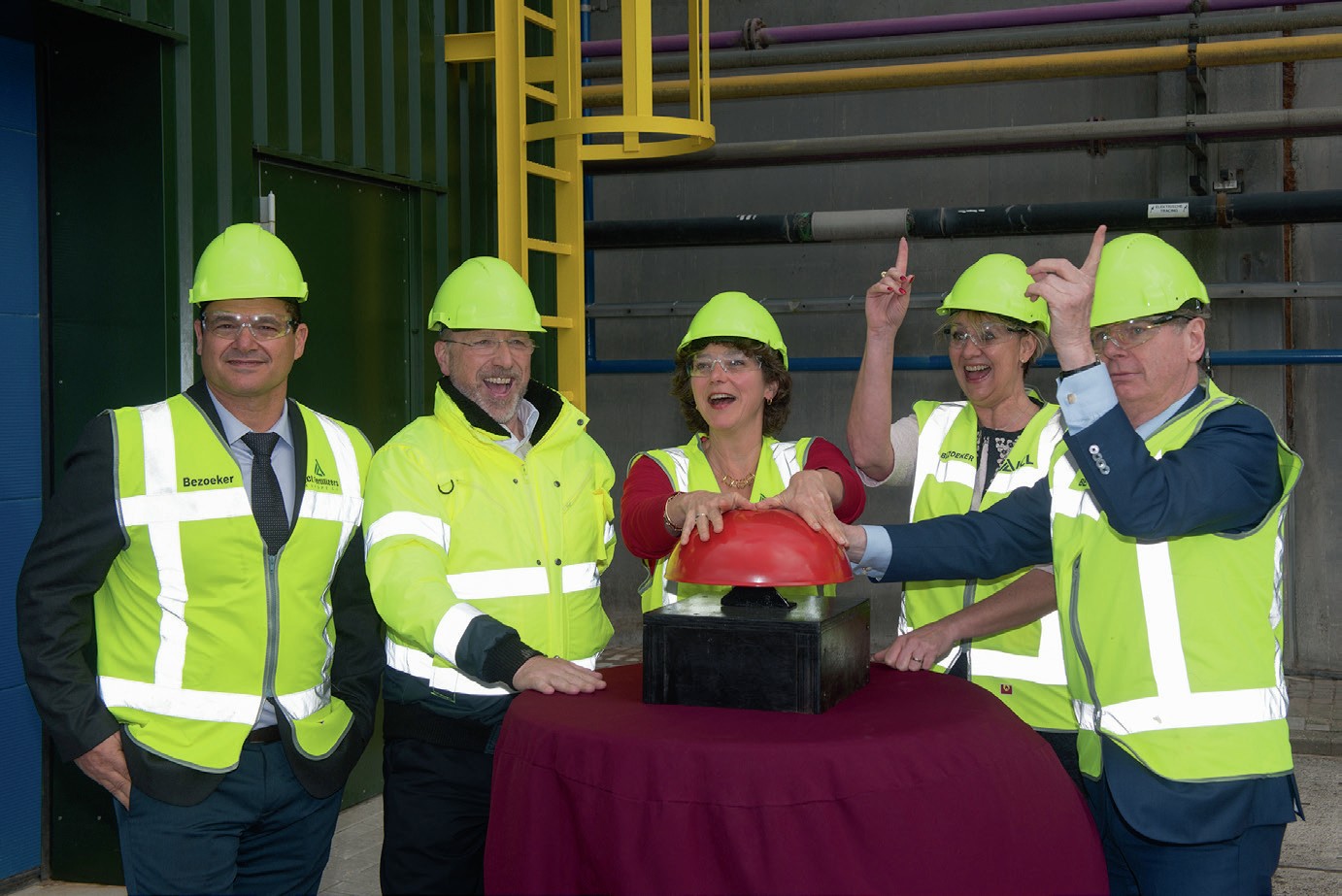
“Novaphos IHP technology can make a major impact on phosphate sustainability by opening up new sources of phosphate rock while significantly reducing wastes.”
Novaphos produces high-quality acid
Florida-based Novaphos Inc (formerly JDCPhosphate) has successfully manufactured high-quality super-phosphoric acid (SPA) continuously using its proprietary improved hard process (IHP).
This was finally achieved in 2018 during prolonged operation of the company’s IHP demonstration plant in Fort Meade, Florida.
Highly-innovative kiln-based IHP produces phosphoric acid from a low-quality phosphate rock feedstock, without creating phosphogypsum waste. Instead, the process generates J-Rox, a commercially-useful aggregate, as co-product.
During recent operations, Novaphos was able to continuously manufacture super-phosphoric acid using locally-sourced phosphate mine waste. This contained around 14 percent P2 O5 alongside high levels of silica and other impurities such as magnesium oxide. This was combined with clay and petroleum coke to form the feed for the kiln.
A high-grade SPA end-product was obtained (68 percent P2 O5 ) with minimal impurity levels (<2.5 percent). The process eliminated up to 90 percent of cadmium in the phosphate feed. This was captured in the plant’s pollution control scrubbing system, leaving levels of around two ppm in the SPA. The process also significantly reduced levels of lead and arsenic.
“This is a major milestone for Novaphos and our technology, showcasing IHP’s value as a cost-efficient and scalable new process,” said Timothy Cotton, Novaphos’ CEO.
He added: “Given the limited phosphate rock reserves in the world, it will be critical for future generations that we waste as little as possible of these vital resources. At the same time, we need to minimise the production of toxic phosphogypsum wastes and reduce the level of harmful impurities in phosphate products.”
GREEN AMMONIA: KEY FACTS
Wind, solar and other forms or renewable energy can be exported as electricity or converted into ‘green’ ammonia or hydrogen. Green ammonia could lead to a future where farmers use fertilizers manufactured by sunlight, ammonia producers become leaders in the new energy market, and ammonia capacity worldwide increases exponentially.
Green ammonia vs green hydrogen
Advantages over hydrogen:
- Ammonia has better power density than hydrogen and does not have to be kept at extremely low temperatures or under high pressure to be stored
- Ammonia is regarded as one of the more attractive options for zero emission shipping due to its energy density and ease of handling
- A premium price could be demanded for green ammonia products
- Ammonia as an energy carrier could command a high price relative to hydrogen fuel.
Green ammonia as a fuel
Main advantages:
- Zero carbon fuel l Well-established trade
- Can be 100 percent produced from electrical energy
- Can be easily converted into hydrogen and nitrogen
- High energy density – can be stored at <20 bar
- Low opex and losses in storage
- High hydrogen density
- Low risk of fire – a specific ratio of NH3 and air (15-25%) is required to sustain combustion.
Main weaknesses:
- NOx emissions
- Odour and toxicity.
World hydrogen market
- Today, most of the approximately 55 million tonnes of hydrogen produced annually is not CO2 -free
- Ammonia production accounts for >50 percent of the total hydrogen market which is currently >95 percent fossil fuel based (from gas, oil, coal etc.)
- Green hydrogen produced from renewable power via electrolysis is fully renewable and CO2 -free
- But only one percent of hydrogen is produced from water electrolysis currently, the rest coming from steam methane reforming and gasification
- Green hydrogen has the potential to decarbonise a large range of applications l It offers massive CO2 reduction potential for power, gas, transport and industry.
Luc Maene, former director general of the International Fertilizer Association (IFA), commented, “For many years I have been hoping that innovative technologies will improve the sustainability of the phosphate sector, which is so critical for food production and so dependent on a limited natural resource. Novaphos IHP technology can make a major impact on phosphate sustainability by opening up new sources of phosphate rock while significantly reducing wastes.”
As a next step, Novaphos plans to commercially deploy IHP technology, after completing process design engineering for a full-scale production process. The company says it has started a dialogue with major phosphate producers and engineering companies to fully commercialise Novaphos technology.
“Our new name [Novaphos] signifies our readiness to move into the next phase,” said Timothy Cotton. “We will work with industry partners to commercialise our technology for making phosphate products that are vital to global food production.”