Fertilizer International 494 Jan-Feb 2020
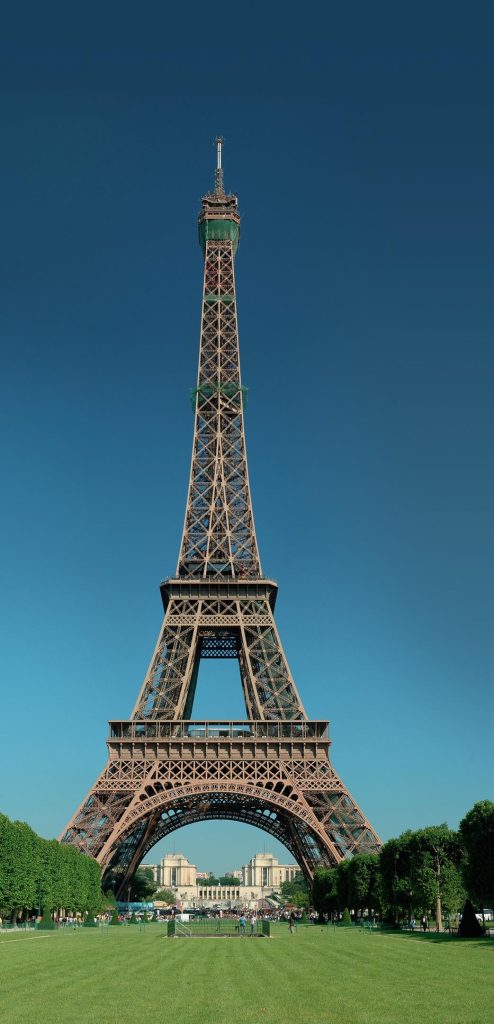
31 January 2020
Phosphates 2020
CONFERENCE PREVIEW
Phosphates 2020
CRU events will convene the 2020 Phosphates International Conference & Exhibition in Paris at the Marriott Rive Gauche between 8-10 March.
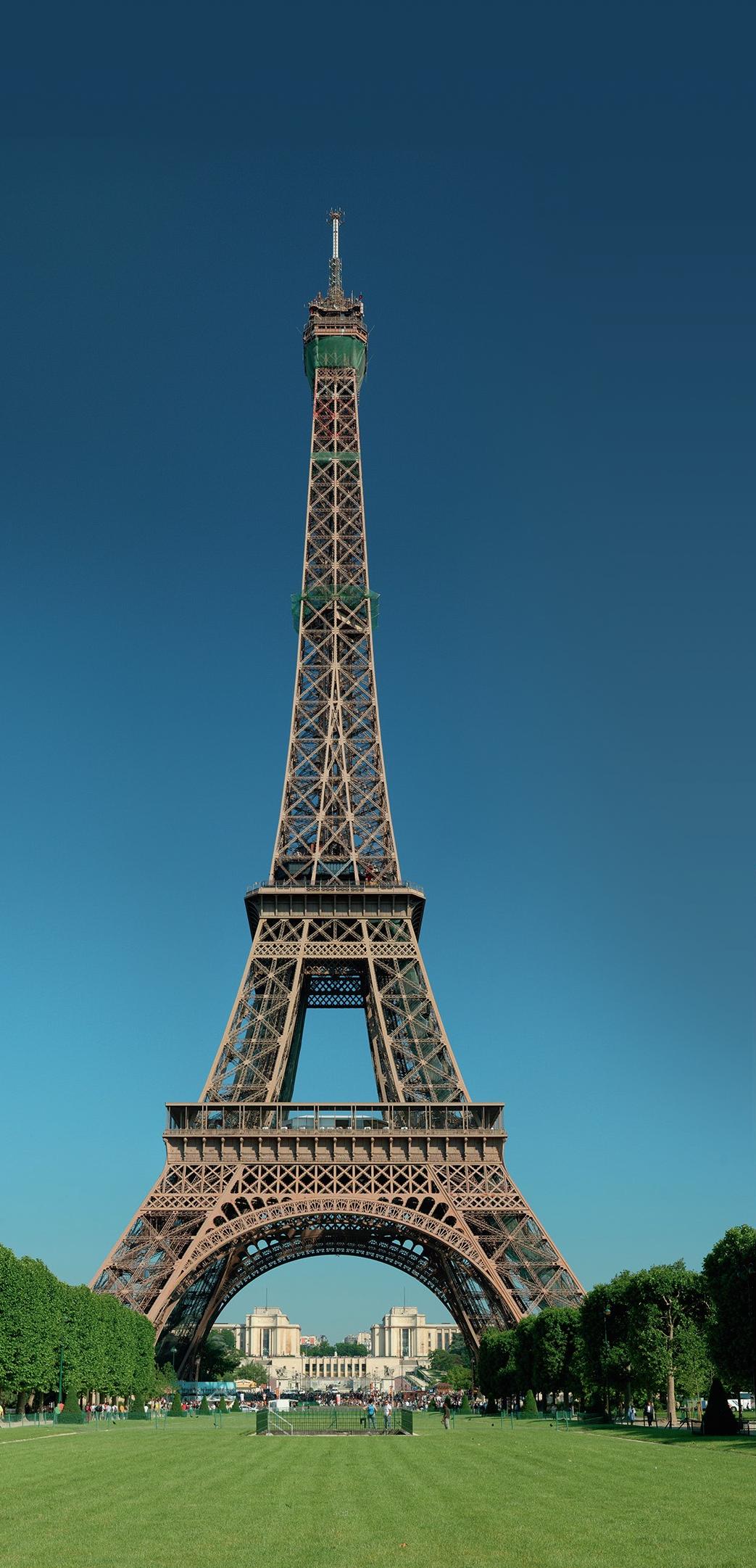
Paris, one of the world’s great capitals, is the setting for Phosphates 2020, the annual international meeting for the global phosphates industry. The event is a must-attend phosphates sector gathering and is celebrating its thirteenth anniversary in 2020.
Last year’s conference attracted more than 420 delegates from over 53 countries. This year’s three-day event promises an equally wide-ranging and topical mix of subjects. Policy and regulation, project economics, disruptive technologies and product diversification are all likely to be key talking points. Leading international phosphates producers, traders and engineering, technology and equipment providers are all expected to attend.
Uniquely, CRU Phosphates combines a commercial agenda with a technical agenda in one single event. This enables the conference to cover the entire value chain of the phosphate industry – including the fertilizer, feed and industrial segments – from both an operational and market perspective.
Phosphates 2020 features a typically strong commercial programme. This will offer up key insights and in-depth market information on phosphate raw materials, intermediates and finished products. Programme highlights include:
- Global and regional market outlooks
- Phosphate rock market dynamics
- Mining projects update
- Market developments for complex and specialty fertilizers
- Feed, industrial and specialty products. The event also offers a separate but equally strong technical and operational programme (see page 42).
Some key reasons to attend:
- Get the CRU View on phosphate supply, demand and prices across the globe in 2020 and beyond
- Hear from incumbent producers and new project developers
- Gain an understanding of the new EU Fertilising Products Regulation (FRP)
- Learn about new technologies, processes, materials and equipment innovations in the technical showcase
- Understand the key drivers shaping the feed, industrial and specialty markets
- Let expert exhibitors answer your technical questions.
Phosphates market overview
Chris Lawson, CRU’s head of fertilizers, sets the scene for Phosphates 2020 with this personal take on the state of the industry:
Phosphate markets end the decade at a new low
“Phosphate fertilizer markets suffered consistent losses throughout 2019, ending the decade with the lowest prices since 2006. A combination of poor demand and new volumes entering the supply chain from Morocco and Saudi Arabia tipped the market into oversupply. With ammonia and sulphur prices also tanking, DAP and MAP prices were unrelenting in the slide downwards, with margins to producers also squeezed.
“Producers in China remain under increasing pressure. Tight environmental regulations remain, although new measures were few and far between in 2019. More pressing was yet another decline in domestic consumption, offsetting production cuts and resulting in another year of strong export sales – adding to global oversupply.
“While China is undoubtedly the marginal producer and exporter, producers in the US took the mantle of swing producer in 2019. Mosaic twice announced production cuts to attempt to balance the market, most recently idling its Faustina facility in Louisiana for three months. This is evidence of the structural supply shift that has occurred over the past decade – in 2010 the US imported 0.5 million tonnes of DAP+MAP and exported almost 6 million tonnes… come 2019 we estimate it imported 3.3 million tonnes and exported 3.2 million.
“Producer margins tightened throughout 2019, and as the year closed out Mosaic, OCP, PhosAgro and the Chinese consortium of producers all announced short-term cut backs in production. This has helped to place a floor on prices in some markets and spur a recovery in others, meaning the market has begun 2020 on a more positive note.
“Poor North American demand in 2019 was a weather-related blip, rather than a structural consumption shift, and is expected to recover sharply in 2020. Meanwhile, the outlook for consumption for other countries (excluding China) remains strong for 2020 and beyond. This, combined with a slowdown in new supply over the medium-term, will be more supportive of prices. A gradual recovery is anticipated in 2020, before more substantial increases beyond 2021.
“Despite the currently depressed state of the market, investment interest remains active. New capacity developments for Russia, Morocco, Saudi Arabia, Egypt and even Togo were announced through 2019. Investments in these low-cost regions will continue to shift the structure of the industry. But developments in China will remain the most important factor to determining prices – and future investment and strategic decisions – over the coming five years.
“Outside of market fundamentals, the concept of environmental and social governance, new project economics, potentially disruptive technologies and product diversification are the key industry talking points. All of these will be discussed in detail at the upcoming CRU Phosphates conference.”
Technical programme highlights
A selection of abstracts from Phosphates 2020’s technical and operational programme.
How much metallurgical testing is enough?
Metallurgical testing requires an understanding of geology, particularly the variability of the ore in the ground. Bulk samples from large diameter cores can be used for test purposes. But a trial mining pit is typically required for the larger samples (i.e. 50 to 100 tonnes) needed for pilot plant testing.
Worley asks how much metallurgical testing is necessary to guarantee the success of a phosphate rock project. Essentially, the test programme needs to assess if beneficiation is capable of producing a saleable concentrate or product for use downstream. This firstly requires an appraisal of ore mineralogy and characteristics, especially mechanical properties such as grindability, abrasion, density etc. Results obtained are used to formulate a suitable approach for upgrading run-of-mine ore and delivering a commercially-acceptable phosphate rock concentrate.
The second stage of metallurgical test work then optimises the process, including reagents, to improve ore grade, recovery and operating costs. Finally, proving the flowsheet requires semi-continuous pilot plant testing.
Beneficiation of rock phosphates using X-Ray sorting machines
TOMRA shares the lessons learnt from two-years of operational experience at the Ma’aden Wa’ad al Shamal Phosphate Corporation (MWSPC). TOMRA’s sorting machines are installed at MWSPC’s 13.5 million t/a capacity beneficiation plant where they pre-process run-of-mine (ROM) ore using XRT (X-Ray Transmission) technology.
TOMRA’s machines can treat 1,800-2,000 t/h of feed material, about 50-60 percent of the total ROM. The machines, which recognise and separate materials based on differences in atomic density, reduce silicon content by removing unwanted chert from phosphate (apatite).
Importantly, XRT technology achieves a high apatite recovery during the sorting process. Eliminating chert also realises substantial cost savings for MWSPC by reducing downstream equipment wear and associated maintenance costs.
Gemini anionics – a new surfactant family for phosphate flotation
Results are presented for a novel family of anionic Gemini surfactants from Nouryon. These environmentally-friendly dimeric compounds have been developed and evaluated as collectors in the direct flotation of apatite from carbonate-rich and siliceous phosphate ores. Using these novel dimeric collectors, it was found that a significant reduction in dosage (half or more) is achievable, in comparison to currently-used monomeric collectors. Gemini surfactants are not only more dose-efficient, they also show outstanding selectivity for apatite in phosphate/carbonate/silicate systems.
Purified phosphoric acid from low-grade phosphate rock
Tenova Advanced Technologies (TAT) have developed a process for producing food-grade purified phosphoric acid (PPA) from low-grade phosphate rock. The process involves leaching highly impure (up to 2.5% Fe2 O3 and F <4.5%) and low-grade (25-30% P2 O5 ) phosphate rock and recovering P2 O5 by solvent extraction (SX). This delivers food-grade PPA as final product (>61% P2 O5 , <5 ppm Fe, <10 ppm F and <1 ppm heavy metals). Overall recovery is 87 percent minimum.
Optimising industrial processes with a digital platform
Prayon shares its experience of developing a digital platform specifically for phosphates production. This automates the collection of industrial data from a phosphate manufacturing plant. Using machine learning and artificial intelligence, the platform can then help operators control their plants properly by predicting and explaining operational deviations. In future, by working out generic solutions and creating specific tools, digital platforms have the potential to keep phosphate plants within their ‘excellence zone’ and operating at peak performance.
What is eco-friendly and sustainable?
In fertilizer production, it is important to understand exactly what being sustainable or eco-friendly entails. In this presentation, ArrMaz takes a deep dive into sustainable chemistry – what it is, how it can be applied, and what it means for the fertilizer industry. Case study results are presented for eco-friendly ArrMaz coatings. These renewable and biodegradable coatings generate zero or minimal waste during production. They are suitable for phosphates and other industry substrates such as nitrogen- and potash-based fertilizers.
PHOSFLOW® technology for the mitigation of scale growth
Mineral scale accumulates on heat exchangers and in pipelines when dissolved elements become supersaturated at different points in the phosphoric acid production process. The use of chemical inhibitors can reduce the rate of mineral scale accumulation – and are an effective way of avoiding the production inefficiencies scaling can cause. The use of Solvay’s PHOSFLOW® technology has been successfully demonstrated at the Grupo Fertinal-Agroindustrias plant in Mexico. In this case study, PHOSFLOW® 1400 was used in the plant’s heat exchangers for scale inhibition. Trial results show the benefits for the operational lifetime and efficiency of the evaporator.
IMACID expansion project increases phosphoric acid production
Andritz Separation supplied IMACID with a new tilting pan filter as part of an expansion project. IMACID was looking for a new filter that could produce up to 950 tons/day P2 O5 , offered maximum reliability, and used a minimal amount of water for filter cloth washing.
Andritz supplied IMACID with its model 36-250 tilting pan filter designed for arid climates. The company has already supplied six of these models to the Umm Wu’al phosphoric acid plants in Saudi Arabia. The new tilting pan filter was able to take full advantage of the excess sulphuric acid available and, consequently, was able to produce 22 percent more P2 O5 capacity (1,650 tons/ day P2 O5 ) than the plant’s rated capacity of 1,350 tons/day P2 O5 .
Solving foaming problems in phosphoric acid production
Managing the formation of foam is a common challenge in the phosphate production process. It can decrease production output and be a safety concern. Although foaming is a notable reactor problem, it can also occur in other parts of the process. Its downstream effects can also be widespread, with consequences for beneficiation, evaporation and granulation. In this presentation, Nalco Water will discuss its recent experience of solving foam problems in the phosphate production process. An effective approach that combines advanced chemistries with advanced application technologies is described.