Nitrogen+Syngas 364 Mar-Apr 2020
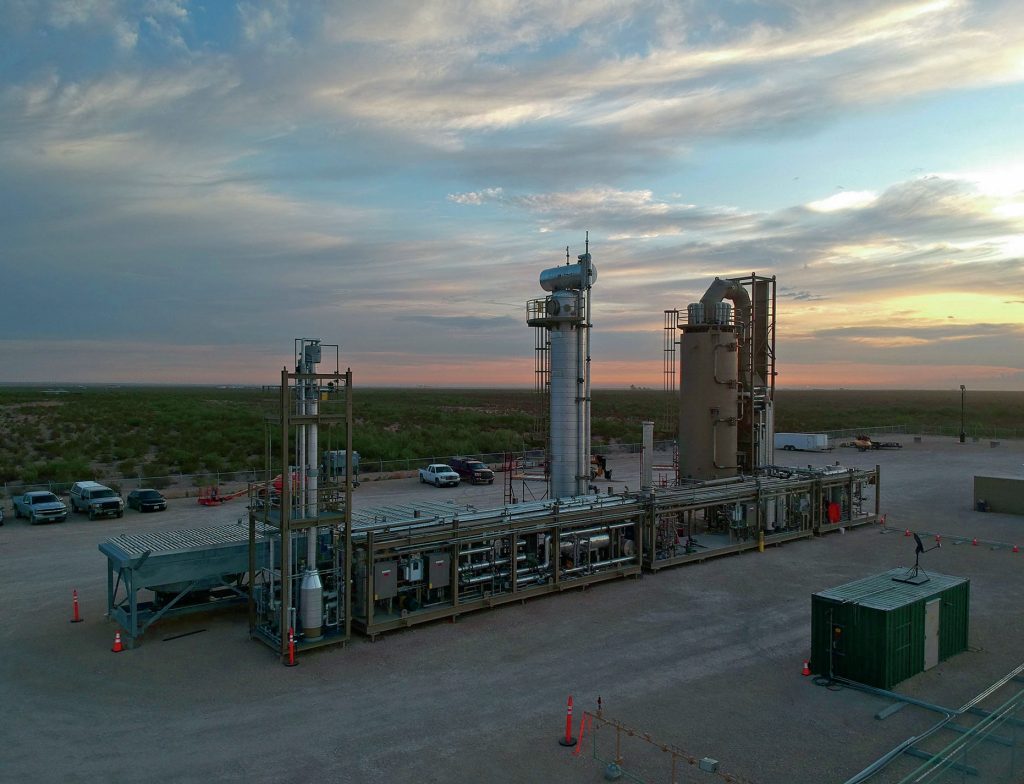
31 March 2020
Monetising ‘challenged’ gas resources
FEEDSTOCK
Monetising ‘challenged’ gas resources
The Global Gas Flaring Reduction Partnership (GGFR) is a World Bank sponsored programme to end wasteful and CO2 – intensive flaring of natural gas from oil production and stranded shale wells, and has been looking to small-scale methanol and GTL projects as a way of utilising this gas for productive ends.
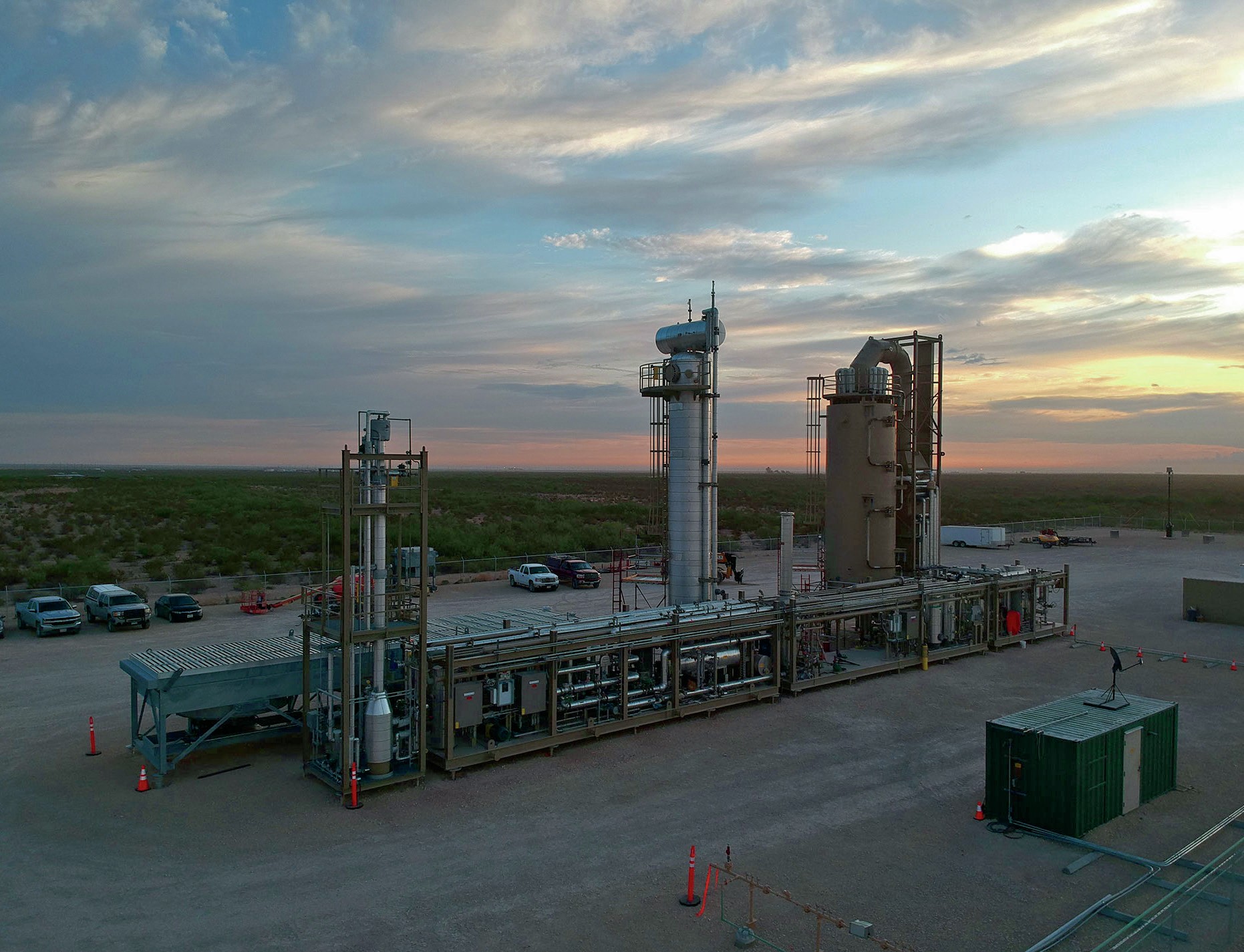
During the 1990s and early 2000s, the watchword of the methanol and to a lesser extent the ammonia/urea industries was ‘stranded’ natural gas. In essence, this meant large untapped reserves of natural gas in remote locations, where there was no pipeline infrastructure to carry the gas to market, ‘stranding’ the gas without a way of monetising it. If this could be coupled with a coastal location, for ease of export of product, then in theory natural gas could be had at a very cheap price, as there was no competing use for it, and large export-oriented syngas-based plants could monetise the natural gas, bringing benefits both for the gas reserve owner and the operating company. This became the economic basis for a wholesale shift in the ammonia-urea and methanol industries, away from established producing locations based on old heavy industry, such as Europe, Japan/Korea and the United States, and towards places with ample gas reserves but no other use for them, including the Middle East in particular, but also places such as Trinidad, North Africa, Russia and the FSU and parts of southeast Asia. The AMPCO methanol plant in Equatorial Guinea is another example of this.
Since then, the gas industry has changed dramatically. The development of a large-scale global market for liquefied natural gas (LNG) has meant that any gas reserve near a coast that is large enough to be able to sustain LNG production and an export terminal for vessels can now participate in a global gas market and find a buyer. Pipeline infrastructure has also expanded considerably, connecting up once remote locations, although gas export from some places (such as Central Asia) remains constrained by pipeline capacity. Furthermore, the rapid growth of cities and industries in developing parts of the world has led to a huge increase in demand for gas for heating and especially electricity production. This has been the case in, for example, the Middle East, where shortages of gas mean that countries that were once considered stranded gas producers, like Kuwait, Bahrain or parts of the UAE are now gas importers, while Saudi Arabia and the UAE have had to turn to exploiting increasingly difficult and more expensive sour gas reserves to generate power. In other places, such as Trinidad, maturing of gas fields has reduced the availability of local gas and led to rationing of supply to ammonia and methanol producers.
All of this has meant that ‘stranded’ natural gas in the way that it was understood 20 years ago has largely disappeared, with the exception of some large deposits still being found and exploited around the coast of Africa, which are described in our article elsewhere in this issue. However, this has not ended the issue of stranded gas, merely forced those looking to exploit it to turn towards smaller scales and niches. There are still many gas resources which go to waste because they cannot be captured and turned into useful, more easily transportable products. In particular, there is still widespread flaring of gas, often associated gas from oil production in remote area or as part of shale drilling. In 2018, it was estimated that 145 billion cubic metres of gas were flared, equivalent to 3.6% of all global gas production that year. Particular culprits were Russia, Iraq, Iran and the United States, as Figure 1 shows. As can be seen, the top seven countries were responsible for two thirds of all gas flaring. Associated gas represents about 20% of all gas production, but World Bank figures suggest that of that gas, only 27% is currently utilised – 58% is reinjected, and 15% flared. The potential gas available for use is thus even greater than the 145 bcm that is flared per year – reinjected gas represents another 455 bcm.
The Global Gas Flaring Reduction Partnership (GGFR)
As well as being a wasteful use of resources, flaring gas also contributes to climate change by releasing millions of tons of CO2 to the atmosphere. The World Bank estimates that more than 300 million t/a of CO2 are emitted to the atmosphere as a result of gas flaring, and could instead, for example, generate 750 million MWh of electricity – more than that currently used by the whole continent of Africa. The Bank has therefore tried to claim a leadership role in gas flaring reduction through its Global Gas Flaring Reduction Partnership (GGFR), a public-private initiative comprising international and national oil companies, national and regional governments, and international institutions. GGFR works to increase use of natural gas associated with oil production by helping remove technical and regulatory barriers to flaring reduction, conducting research, disseminating best practices, and developing country-specific gas flaring reduction programmes.
Participating national governments include Algeria, Azerbaijan, Cameroon, Indonesia, Iraq, Kazakhstan, Kuwait, Mexico, Nigeria, Norway, Qatar and Uzbekistan, as well as the Canadian province of Alberta and the Russian district of Khanty-Mansiysk. Corporate partners include BP, Chevron, Eni, Equinor, ExxonMobil, Occidental, Pemex, Qatar Petroleum, Saudi Aramco, Shell, SOCAR and Sonatrach. GGFR continues to urge governments, oil companies, and development institutions around the world to help reduce flaring, via initiatives such as its “Zero Routine Flaring by 2030” programme.
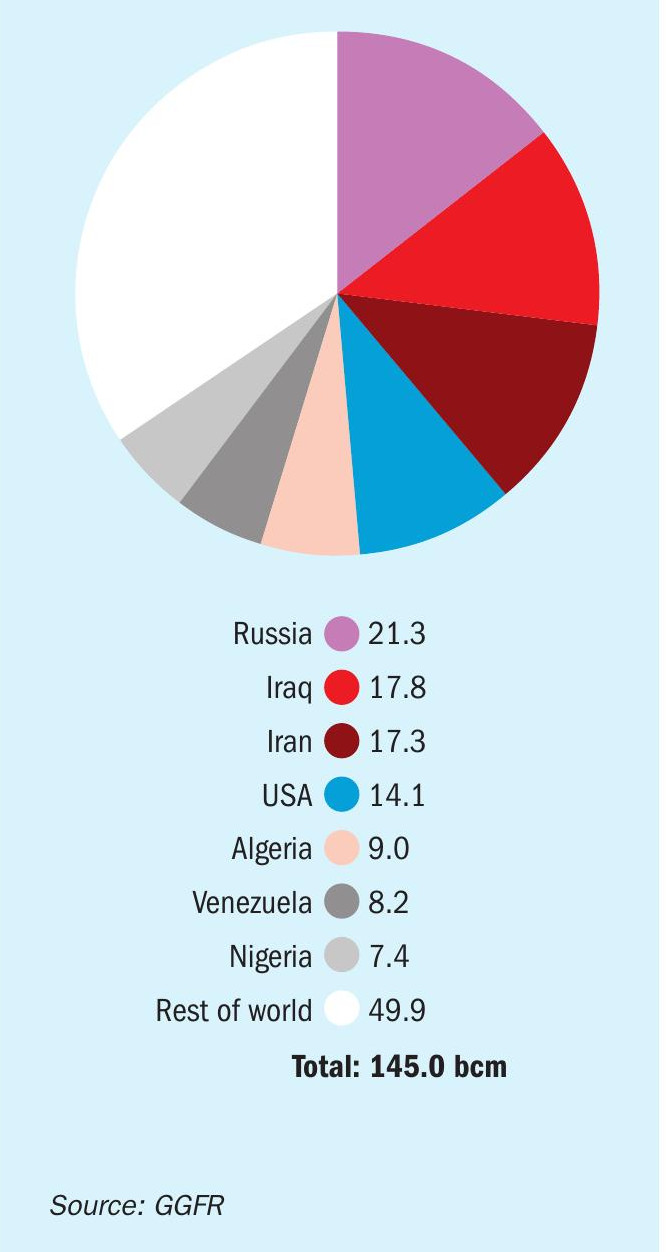
Gas utilisation
At the core of GGFR is a quest to provide alternatives to gas flaring. To this end, it monitors and advises on technologies which can be used by companies to use the gas that they are flaring. The most common use for natural gas worldwide is electricity production. However, gas flaring often takes place in locations which are not only too remote to justify gas pipeline linkages, but also electricity grid connections, and which may not produce sufficient gas for a long enough period to justify construction of a large scale gas-fired power plant. Small-scale gas turbines are available, but tend to still have a significant minimum throughput requirement (>10 million scf/d at the very lowest, and often an order of magnitude more).
GGFR has considered two other main technology routes to gas utilisation. The first onward transport, as either small scale LNG or as compressed natural gas (CNG); the latter tends to be far cheaper for small volumes (less than about 5 million scf/d) and transport over shorter distances (<700 km), and can be supplied at around $3.60-4.60/MMBtu delivered cost (without any value assigned to the gas itself). Much depends upon the availability of a local market. Mini-LNG costs tended to be much higher, starting at $9.00/MMBtu (for liquefaction and transportation costs oinly), a level unlikely to be competitive with most gas markets1 .
The second major route that GGFR has considered is small-scale gas conversion to chemicals, and this of course tends to require a syngas intermediate step.
Chemical options
GGFR looks at two main downstream chemical options for dealing with stranded associated gas; methanol production and Fischer Tropsch (F-T) gas to liquids conversion. The technologies are considered across three separate scales; ‘small scale’ production, based on 10 million scf/d of feed gas or more; ‘mini-scale’ production, based on 1-10 million scf/d of gas feed; and ‘micro-scale’ production, based on 100,000 – 1 million scf/d of gas feed2 . In its most recent GTL technology bulletin, published in September 2019, GGFR listed those companies still involved in working on methanol or GTL downstream options for flared gas3 , and the scale of their technology offerings, and these are summarised in Table 1.
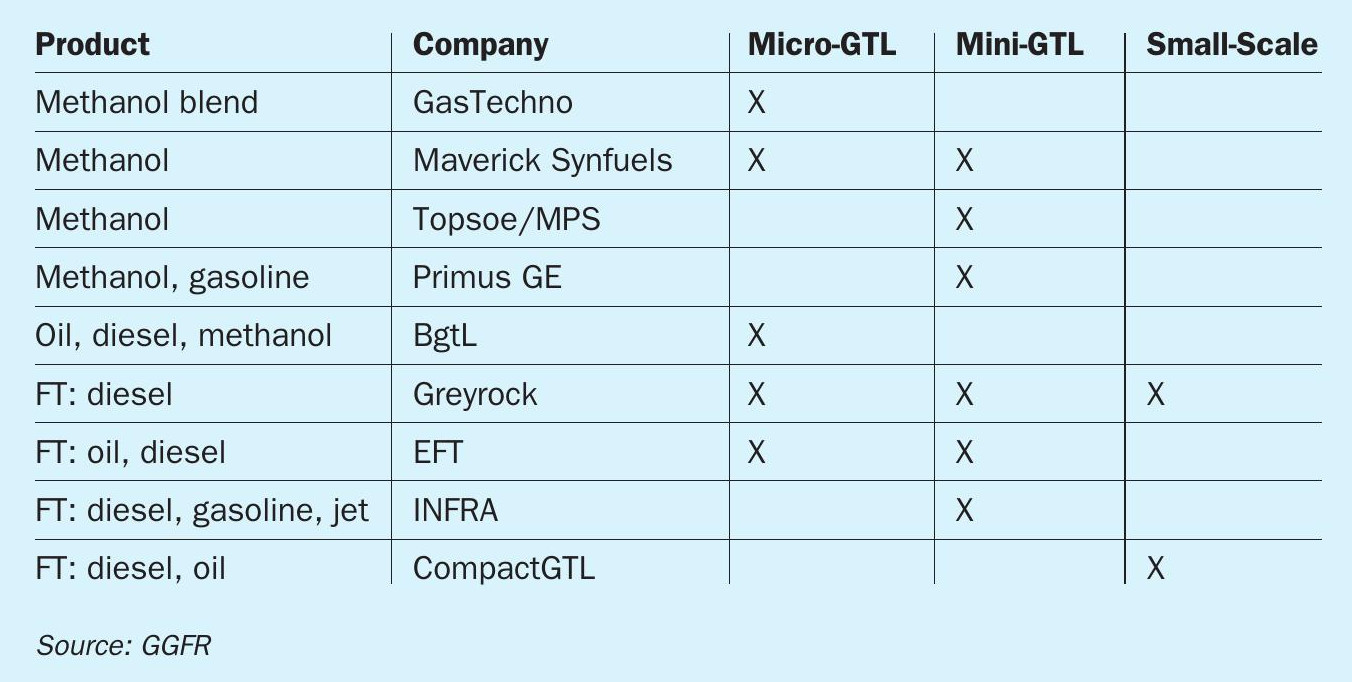
CompactGTL and Velocys
The path of using flared gas to produce chemicals has not been a smooth one, however, as illustrated by two UK-based companies who had looked to be the most promising candidates a few years ago; CompactGTL and Velocys, both offer F-T GTL technologies based on a compact modular steam methane reforming technology using mini-channel reactors to generate syngas which is then Fischer-Tropsch processed into what CompactGTL describes as syncrude – a mix of waxes, naphtha and middle distillates and which, with the addition of a hydroprocessing module, can produce synthetic diesel with zero sulphur content.
CompactGTL built a demonstrator plant in Brazil in conjunction with Petrobras in 2008, and a pilot plant at Wilton in the UK the same year. However, Velocys, based like CompactGTL in Oxford, UK, claimed that the CompactGTL process was too similar to its own, and this led to a patent infringement lawsuit in 2014 which went in Velocys’ favour. After the settlement, CompactGTL faced receivership, and was bought out by its then non-executive chairman, former BP boss Tony Hayward, together with investment banker Ian Hannam, and the company then signed an agreement with the government of Kazakhstan to build a 2,500 bbl/d GTL plant based on flared associated gas. The Kazakh government postponed a final investment decision on the project, and though CompactGTL continues to trade, there have been no further updates since 2015. Likewise plans to build larger units in Brazil to tackle flared gas have been shelved following Petrobras’ difficulties and its need to sell off various of its operations to raise cash.
Velocys, meanwhile, completed a small-scale (200 bbl/d) GTL unit in Oklahoma with ENVIA in 2014, based on landfill gas, but operations at the unit were suspended in 2018 following a coolant leak and ENVIA bought out Velocys’ interest. The company is still involved in two projects, a 60,000 t/a GTL unit in Mississippi based on gasified biomass, and a 30,000 t/a GTL unit in the UK to produce jet fuel from gasified waste, but it is no longer looking at dealing with stranded natural gas as a feedstock.
Greyrock
Into the gap left by Velocys and CompactGTL has stepped US-based Grey-rock. Greyrock offers a series of modular plants at different scales: M50, M100, P450, P2500 and P5000, with the number being the approximate output in terms of barrels/day (‘M’ means a moveable, skid-mounted unit). The process is based around a proprietary catalyst (‘Greycat’) that converts syngas into synthetic fuels without a wax component by preventing longer chain hydrocarbon formation. The company is currently involved in four projects, in the US, Canada, Mexico and the Democratic Republic of Congo to deploy its technology to produce liquid fuels from flared gas. Financing was secured and construction work began on the joint venture Canadian plant, based near Carse-land, Alberta, 60 km east of Calgary, in May 2019. The facility is a 500 bbl/d unit, based on flared gas, and is due to begin commercial production soon. In the US, Greyrock has sold an M50 (50 bbl/d, 500,000 scf/d of gas feed) plant to Advantage Midstream, who will own and operate the unit in Jackson County, Colorado, and delivered another M-class plant to Permian, Texas.
EFT
Emerging Fuels Technologies (EFT) offers a micro-scale (25 bbl/d) skid-mounted modular GTL plant which it calls Flare Buster 25, based on its proprietary Advanced Fixed Bed (AFB) Fischer-Tropsch reactor/ catalyst system. The principals in the company, Kenneth and Mark Agree, were the founders of the Syntroleum corporation. EFT has also licensed its technology to the 1,100 bbl/d Juniper GTL project in Texas, which aims to convert an existing steam reformer into a GTL plant. That project had reached the construction stage but work was halted in May 2019. However, a new investor, Calumet, came on board in October and the project still seems to be in development.
Meanwhile, EFT has recently qualified two US manufacturers to build its Flare Buster 25 plants, and says that it expects to do likewise with more manufacturers on a global basis. The cost of one of the modular units is reportedly $4 million. The company is also working with Black and Veatch and NiQuan on rescuing the Point a Pierre GTL plant in Trinidad, which remains 85% complete.
GasTechno
GasTechno is the brainchild of Walter Briedenstein, who literally built a small-scale methanol plant in his garage in Michigan in 2010, converting methane directly into methanol via a patented direct homogenous partial oxidation process. This had scaled to a demonstrator unit by 2013, working off a flared gas site nearby, and a small-scale Mini-GTL 300 commercial unit began operation in 2018 in North Dakota, and another in Utah. The ‘Methanol in a Box’ process generates an alcohol blend and requires a distillation unit to produce pure methanol. GasTechno currently offer an M-300 and an M-700 unit converting 300,000 scf/d or 700,000 scf/d respectively, for $1.5 million for the smaller plant and $2.5 million for the larger.
INFRA
INFRA developed its own Fischer-Tropsch catalyst which, like Greyrock, produces synthetic fuels without the wax component. It claims that the product stream is 65% diesel and 35% naphtha. The company installed a 100 bbl/d demonstration plant in Wharton, Texas in 2016, but commissioning and start-up ended slipping, reportedly due to issues with the front end syngas section (which did not use INFRA’s technology) which was unable to produce syngas in the correct ratio to start the F-T section. In July 2019 INFRA sold the Wharton plant to Greenway Technologies, who aim to use their own patented syngas generation technology to run the plant.
In the meanwhile, the company is continuing to look to project opportunities, and is currently in front end engineering and design work for a 450 bbl/d unit in Russia to produce winter diesel fuel and high-octane gasoline from the natural gas of the Vasylkovskoye gas condensate field. In September 2019 INFRA announced a partnership with GasTechno to jointly market methanol and GTL solutions.
Primus Green Energy
Primus Green Energy has its own STG (syngas to gasoline) technology, offering either methanol or synthetic gasoline as an end product – the gasoline is produced via a methanol intermediate step. The company built a demonstrator unit in New Jersey and had been looking to build a series of 160 t/d methanol plants in North America each converting around 6 million scf/d of gas. At the moment, however, the company’s only active project is a 2,800 bbl/d natural gas to gasoline unit for Texas. Front end engineering and design on the project began in December 2019 in conjunction with an un-named joint venture partner, and is expected to be complete in mid-2020.
Maverick Synfuels
Maverick Synfuels offers its Oasis skid-mounted modular methanol production technology, at sizes ranging from 25 t/d (800,000 scf/d equivalent) to 100 t/d methanol (3 million scf/d gas equivalent). The company had been looking to develop a 100 t/d installation at Prudhoe Bay in Alaska, but the project has been quiet for the past 18 months.
Haldor Topsoe
Finally, also looking to get in on the small-scale modular plant market, Haldor Topsoe has developed its MeOH-To-Go concept in conjunction with specialist EPC firm Modular Plant Solutions. Topsoe currently offers a single modular plant size of 215 t/d methanol capacity, requiring 7.1 million scf/d of natural gas, using the company’s heat exchange convection reformer (HTCR) technology. Topsoe says that this scheme is suited for small scale production as it is steam neutral and lower cost than conventional reformers, and it has been used for some years for small scale hydrogen production. We are not aware of any commercial projects as yet for this technology.
“At such small scales, achieving economies of scale is difficult…”
Summary
Flared natural gas is a big issue from both an environmental and economic perspective. There are a number of strategies for reducing it, including pumping associated gas back into an oil well, converting the gas to compressed natural gas (CNG) for sale, or small-scale power generation. Producing a useful co-product, be it methanol or synthetic gasoline or diesel is a potentially attractive option if the cost of installation and operation is right.
However, the world of small-scale GTL and methanol production is a fast-moving one. Companies are themselves often quite small scale and can find the financial and technical challenges of proving their concept via a working demonstrator unit and then securing new orders challenging. The failure of a single project, such as ENVIA’s Oklahoma plant, can spell disaster for a technology licensing company. For this reason a number of companies in the field have come and gone, and some other technologies not mentioned here appear to be in abeyance, at least as regards developing units for dealing with flared/stranded gas (a number of other companies are still involved in dealing with e.g. waste or biomass gasification or small-scale production using electrolysis). Indeed, it is small-scale production based on electrolysis that seems to be grabbing much of the attention at the moment.
Even so, some companies do now seem to be developing viable technologies and business models for small-scale plants based on flared/stranded gas, and establishing themselves in the field. As detailed above, Greyrock has had a number of notable successes, and GasTechno and EFT also appear to be making headway. It is possible as the field develops that we will see more of the established players moving into the world of modular small-scale plants aimed at stranded or flared gas utilisation, as Haldor Topsoe has done. These plant scales are often already available – on the ammonia side, for example, thyssenkrupp Industrial Solutions offers plants of capacities down to 250-500 t/d, and Casale offers via its A60 flowsheet ammonia plants as small as 50-300 t/d capacity. Johnson Mat-they’s Compact Reforming technology was used for a 300 bbl/d GTL plant at Nikiski, Alaska in 2001. The issue has generally been one of cost – at such small scales, achieving economies of scale is difficult and so such plants often depend for their economics upon very cheap feedstock – one reason for the concentration on waste or biomass gasification. Large scale production of small modular units could bring down per unit cost, but at the moment the market does not appear to exist for so many plants.
Furthermore, as the GGFR itself admits in a recent report, oil and gas producers are often not used to and hence not comfortable with on-site petrochemical production, and there is an education process that must go alongside technical and economic issues – selling the chemical unit as a ‘black box’ that the producer does not need to worry about.
Nevertheless, most governments are making efforts and commitments to reduce flaring as part of their ambitions to tackle emissions. Government pressure on oil and gas producers to deal with flared gas could yet be the impetus that the field needs for more widespread adoption of small-scale chemical production.
References