Nitrogen+Syngas 364 Mar-Apr 2020
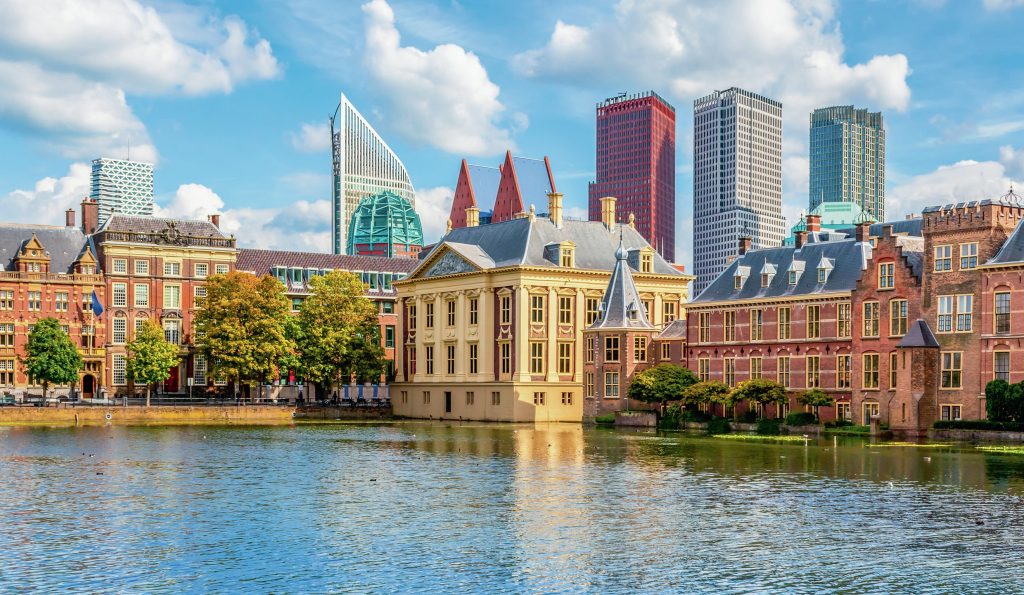
31 March 2020
Nitrogen + Syngas 2020
CONFERENCE REPORT
Nitrogen + Syngas 2020
This year’s Nitrogen + Syngas conference was held from 17-19 February in The Hague, Netherlands.
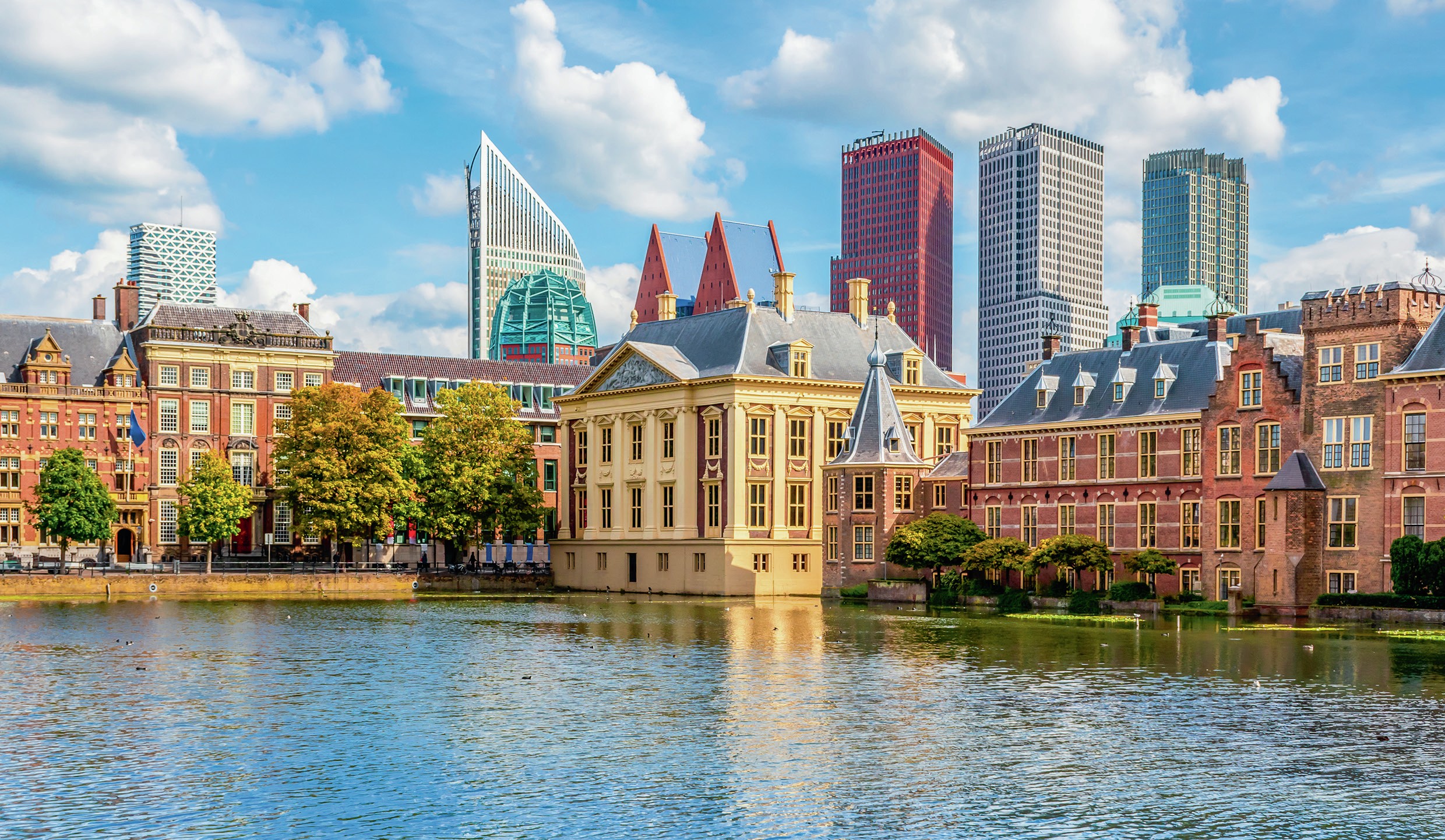
In spite of some slight nerves about coronavirus, CRU’s annual Nitrogen + Syngas conference went ahead in the middle of February at The Hague, and may have proved to be the last major industry gathering for some months. Attendance was brisk, and this year the exhibition had grown to a size that necessitated a move to a purpose built conference centre rather than a hotel, in this case the World Forum.
The meeting began with a morning of technical showcases on the Monday, short 15 minute presentations covering measurement and analysis, boilers, reforming and materials development.
Market papers
The additional of the technical showcases meant that the keynote plenary session was pushed back to Monday afternoon. Following the usual welcome from conference organiser Amanda Whicher, CRU’s chief nitrogen analyst Laura Cross began with an overview of the global nitrogen market. Last year had seen some surprises, including China exporting 4.7 million tonnes of urea, far more than the 2.9 million tonnes expected, and India importing a huge 9.7 million tonnes – the latter drawing out most of those additional Chinese tonnes. India had faced subsidy issues at its naphtha-based urea plants and technical issues at some others, and so needed to import more in spite of the start-up of the new 1.3 million t/a Gadepan plant. Although three more new urea plants are on the 2023 time horizon, India is still expected to import 6.8 million t/a in 2020 and 2021, and could be higher if domestic production issues continue or the new plants face delays.
Demand fundamentals look strong, with the US returning to higher application levels and forecast demand increases in Brazil as Petrobras leaves the market which will offset falling Chinese demand. Changes to Indian subsidy rates in the April budget could still cause some change to this however. Overall CRU predicts urea demand will rise from 162 million t/a in 2018 to 178 million t/a in 2023, with South and Southeast Asia, and Central and South America the major sources of new demand, but African demand is also rising rapidly, and more demand is expected in North America and Europe.
China continues to switch from expensive and less efficient anthracite coal-based urea production to bituminous, with 9 million t/a of new capacity coming onstream at the same time that 13 million t/d of older capacity closes. Exports are likely to continue to fall, depending on industrial sector demand and global prices.
A low cost wave of new export capacity is on the horizon, in Nigeria and Brunei, but will be offset by Chinese closures, though China will remain the marginal producer.
Keshni Sritharan of CRU followed with a paper on energy markets. Geopolitics were leading to market volatility, she said, with oil prices falling as economic fears of a global slowdown triumph over supply cutbacks (cutbacks which, as we have seen very recently, have since been reversed). Coronavirus, the US-Chinese trade war and Iranian drone strikes on Saudi Arabia are all weighing on oil markets.
On the gas front, oil and gas prices are steadily decoupling in Europe, and though they remain linked in Asia Pacific, a shift to market pricing is expected over the coming years. However, regulated pricing still predominates in Eurasia, South America, Africa and the Middle East. The lowest gas cost regions – North America, Russia, the Middle East and Africa continue to see the most investments in new ammonia-urea capacity. Russia in particular has benefitted from the weak rouble and is seeing new capacity investments. Gas prices are at decade lows, with Henry Hub prices dragging indicators and markets down. But US LNG suppliers are not making money at current prices and cutbacks and a price recovery were expected. CRU was forecasting a gas price floor in late 2020/early 2021, by which time European prices could have fallen as low as $2.00/MMBtu.
Sustainable production
As the effects of climate change become more pronounced, there is increasing recognition in the industry that more needs to be done to help tackle emissions of CO2 and CO2 -equivalent gases, and a number of papers covered this topic. A German government-funded programme to help producers deal with nitrous oxide emissions from nitric acid production was the topic of Volker Schmidt of the German Company for International Cooperation (GIZ). N2 O emissions from nitric acid plants have become a focus for regulators because they offer a relatively cheap way of abating emissions in terms of CO2 -equivalence. There is a relatively centralised global industry – only 580 plants – and a high potential impact: 1.7 gigatonnes of CO2 emissions which could occur between 2021 and 2030 if not abated. At the COP-21 summit in 2015, the German government launched an initiative to try and reduce these emissions worldwide, with euro 70 million of federal funding. It comprises a grants programme for remediation technologies, administered by GIZ, and a National Climate Change Action Group auctions programme implemented by the World Bank. The initiative covers secondary and tertiary N2 O emissions reduction and is technology neutral – the final decision is down to the plant operator, though competitive tendering is required. Of the 580 plants worldwide, 100 plants in 30 countries are eligible for financial support. The grants application deadline has been extended to December 2020, and the NACAP auction programme to 2025.
John Pach of JM showcased what his own company was involved in as regards sustainable nitrogen and methanol production. With some questions over the short-term scalability of ‘green’/renewable hydrogen production, he suggested that ‘blue’ production – conventional production using carbon capture and storage (CCS) was vital to deliver scalable CO2 reductions in the short to medium term. CCS of course presents challenges – large gas volumes with low partial pressures of CO2 requiring a large flow of absorption solution and higher capex. The solution is to design hydrogen plants differently. For example, JM’s LCH (leading concept for hydrogen) process uses a gas heated and autothermal reformer and generates no flue gas stream. All of the CO2 is contained at pressure and easier to remove for lower capex and opex. Compared to a CCS add-on to a conventional plant, LCH+CCS can deliver 40% lower capex and 15% less CO2 as well as 15% more nitrogen gas efficiency. It has been selected for the Hynet project in the UK (see Syngas News, this issue); a 330 MW hydrogen plant (equivalent to 1,000 t/d of hydrogen) and the Acorn project in Scotland (250 MW hydrogen).
Stephan Buss of thyssenkrupp Industrial Solutions described some other ways that plants could be made “fit for the future”. He also focused on NOx emissions; a typical nitric acid plant emits NOx at about 150 ppmv. Low NOx burners can reduce this to 50 ppmv, and the addition of tertiary selective catalytic or non-catalytic reduction (SCR/SNCR) using ammonia can reduce this to 5 ppmv or below. tkIS has its own Envinox system for post-combustion cleanup, which reduces NOx emissions to below 10 ppmv, and which removes 99% of all nitrous oxide emissions above 430°C. For lower temperature operations (>315°C), a different set-up is required, which can reduce NOx to virtually zero with moderate hydrocarbon feed consumption. Other innovations Stephan covered included digitisation, either model driven (‘digital twin’ plants) or data driven, via neural networks.
Joey Dobree of Stamicarbon looked at the possibility of producing nitrates from renewable energy. Of course this means water electrolysis to generate hydrogen for ammonia production, and Stamicarbon’s parent Maire Tecnimont has been able to partner with other technology developers, such as Siemens for electrolysers. Joey considered the case of a 100,000 t/a CAN plant based on renewable ammonia. Of course the economics are very location dependent, but he said that, for example, inland Kenya or elsewhere in southern Africa has a combination of high solar flux, and remote locations which can make importing fertilizers expensive. At such a site an electrolysis-based plant is already competitive today, he argued, and as the cost of electrolysis comes down, and with the additions of carbon taxes or government incentives, it could easily become competitive elsewhere.
Catalyst developments
Several companies reported new catalyst developments. Haldor Topsoe launched its new TITAN reforming catalyst series, based on hibonite calcium aluminate support which the company says is more stable under reforming conditions. A full discussion of the catalyst can be found in the article in our previous issue, Nitrogen+Syngas 363, Jan-Feb 2020, pp59-61.
Matthew Wilson of Johnson Matthey updated delegates on progress with JM’s new Catacel engineered metal support structure for catalysts, which coats metal ‘fans’ that are then stacked in catalyst tubes, offering a 10-20% lower pressure drop and greater long-term structural integrity, as well as a higher surface area for greater reactivity and heat transfer. It has now been used in a number of revamping operations, and has allowed increased throughput – a hydrogen plant at a refinery saw a 17% increase, for example. It can be changed during a standard maintenance shutdown, although some debottlenecking may be required in associated production units to allow for higher throughput. In new plant designs, thinner, shorter reformer tubes could instead be used, lowering the capex of the reformer box. It can also be used in a hybrid tube filling, with the top half packed with Catacel for higher activity and the bottom half conventional catalyst for robustness and economy.
Christian Berchtold of Clariant and Sergio Panza of Casale presented a refinement of Clariant’s AmoMax ammonia synthesis catalyst; AmoMax-Casale, with higher activity at higher temperatures and increased resistance to poisoning and long term stability. A fuller discussion of the technology can be found in our article on pages 44-48 this issue.
Linde and BASF have been engaged in collaborative research on reforming, and Klemens Wawrzinek and Virginie Lanver described the result of their companies’ work. BASF has developed a new catalyst – Synspire G1-110 – for reforming in low steam and high CO2 conditions, featuring a unique metal oxide carrier which prevents carbon accumulation and catalyst deactivation. This is a feature of Linde’s new Dryref ‘dry’ reforming process, allowing it to operate at a lower steam: carbon ratio and avoid the necessity of a pre-reformer. CO2 is recycled to the reformer and can be supplemented by additional CO2 to control reforming conditions. The companies claim a 3-5% reduction in operating expenditure as well as a lower CO2 footprint.
Finally, in a similar catalyst/process technology joint development Stefan Gebert of Clariant and Stephane Walspurger of TechnipFMC jointly introduced a recuperative reforming innovation called EARTH – the Enhanced Annular Reforming Tube for Hydrogen. The aim is to generate energy efficiency improvements in reforming which lower CO2 emissions. Like JM’s Catacel, it uses a structured metal foil catalyst support which gives high surface area and heat transfer, while the recuperative reforming tube reduces fired heat demand via internal heat recovery. The tubes are available as a retrofit for existing plants as a drop-in insert consisting of the structured reforming catalyst and concentric internal heat transfer tubes. From a plant reference already in operation, the companies claim 10% higher efficiency and 10% lower CO2 footprint, albeit with 50% lower steam export.
Reforming
Outside of the catalytic arena, a number of papers dealt with other issues in reforming. Hadj Ali Gueniche of Zohn Zink Ham-worthy Combustion showcased a laser reformer monitoring system called ZoloS-CAN which, tied into a process monitoring software suite, can allow real time balancing of gas flows in the reformer by adjustment of the burners.
Daniel Znidersic of BD Energy Systems and Jeffrey Bolesbrusch of Blasch Precision Ceramics showed how the installation of Blasch’s Stablox modular reformer tunnels at the bottom of a reformer can transport flue gas out of the radiant section in a uniform way, avoiding turbulence and hot spots at the bottom of reformer tubes. The Stablox do not require mortar – a potential point of failure in conventional systems – and feature inserts allowing fine tuning of reformer flue gas flow.
Soren Gyde Thomsen of Haldor Topsoe shared some operator experiences with Topsoe’s heat exchange reformer in ammonia plants, including a revamp at PetroVietnam’s Phy My plant that delivered a 20% capacity increase, and a new HTER reformer as part of a 1,600 t/d plant for Duslo in the Czech Republic.
Urea plant operations
In the conference’s urea section, a number of case studies described operator experiences. Some, concerning plant start-up and commissioning, are covered in more detail in our article elsewhere in this issue (pp34-42). Others included NIIK’s work on revamping Acron’s urea plant in Russia, and Koch Agronomic Services expanding its product portfolio at Enid, Oklahoma via the addition of a new plant section integrating urease and nitrification inhibitors into its urea granules. GPIC, in conjunction with thyssenkrupp Fertilizer Technology, showed the results of using tkFT’s new advanced spray nozzles in their urea plant’s granulation section, while Pakistan’s Fauji Fertilizer Company covered modifications to the foundation of a heat exchanger in their urea plant.
Melamine
Two papers also looked at melamine production. The first, by Casale, described the first installation of Casale’s new Low Energy Melamine (LEM) process, for Gujarat State Fertilizers and Chemicals (GSFC) in India. The installation uses CO2 and ammonia from the ammonia plant rather than urea as a feedstock and so has its own integrated urea synthesis and melamine sections. The plant was commissioned in January 2019 and achieved capacity in April.
The second paper, by Eurotecnica, considered some of the advantages of adding a melamine section to a fertilizer plant, including the rapidly growing market for melamine and downstream resins, and the fact that existing prilling or granulation plant capacity may limit any increase in production from a urea plant, allowing excess urea to be used for melamine production instead.