Fertilizer International 495 Mar-Apr 2020
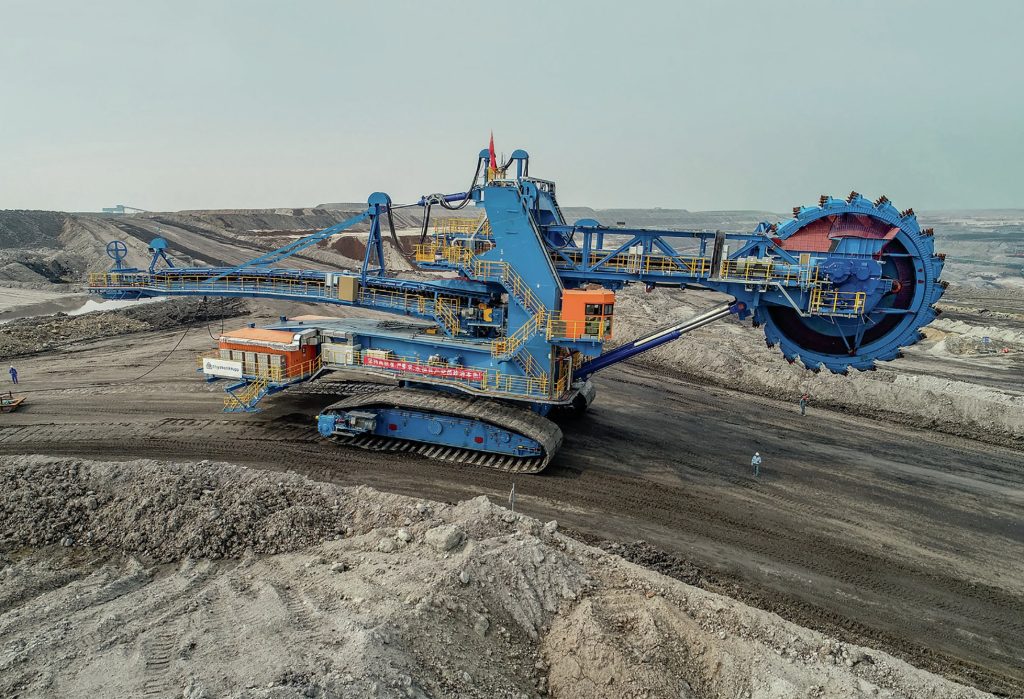
31 March 2020
Phosphate and potash mining update
MINING TECHNOLOGY
Phosphate and potash mining update
We look at state-of-the-art technology used in phosphate and potash mining, including equipment and systems for excavation, tailings thickening, transport, tunnelling and processing.
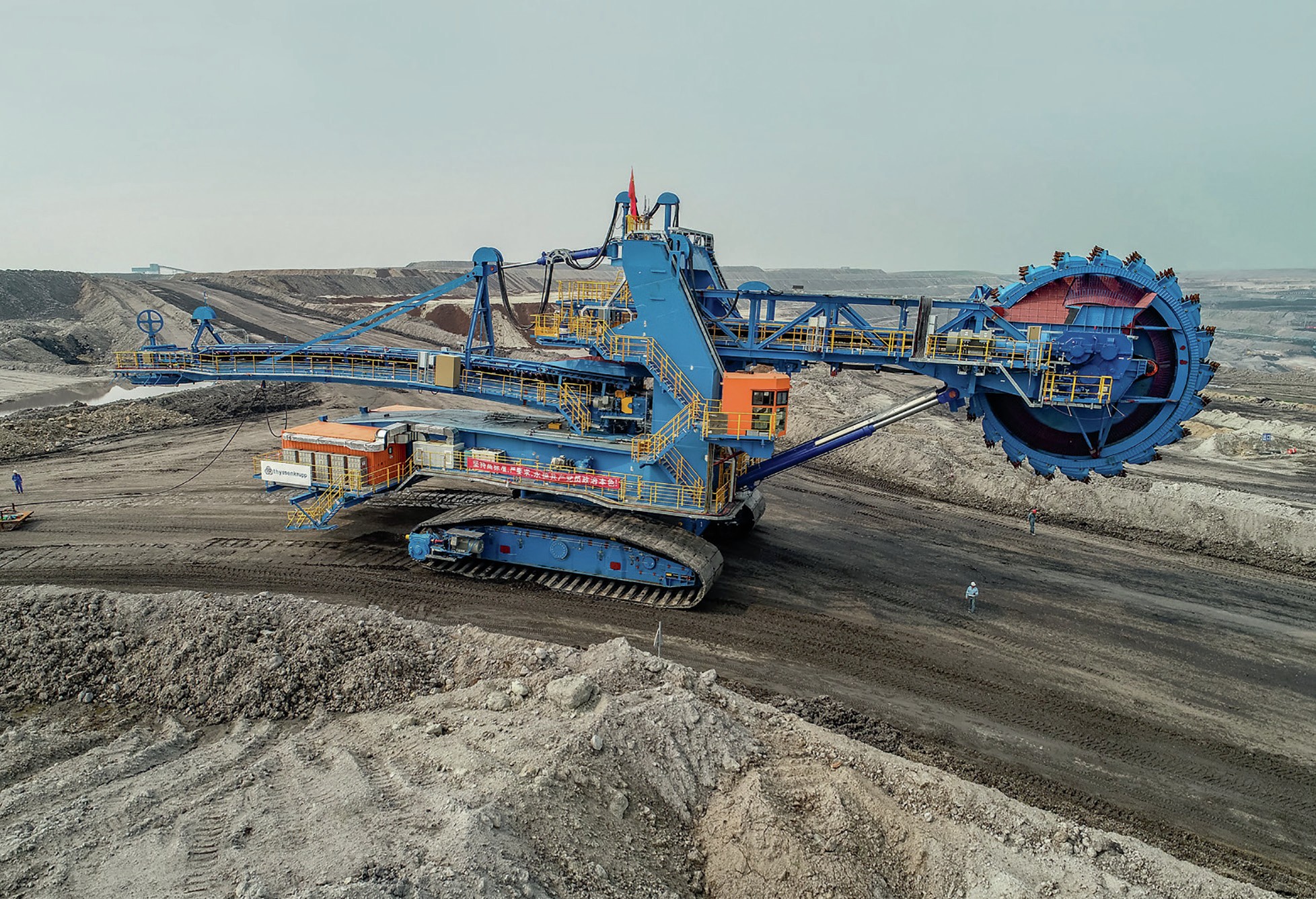
The Barracuda excavator: hard mining made easy
Germany’s thyssenkrupp Industrial Solutions (tkIS) introduced its new Barracuda range of bucket wheel excavators in 2016. These compact mining machines use a larger number of teeth per bucket to cut materials with a uniaxial compressive strength of up to 50 MPa. The Barracuda’s innovative design allows harder material to be excavated, including phosphate rock, potash and limestone, without the need for drilling or blasting operations.
By combining ore excavation, loading and the transport within a single machine, the Barracuda can seamlessly replace a complex system of multiple machines with a single mining unit. thyssenkrupp offers four versions of the Barracuda, each with different ore transport configurations. They range from a compact machine and conveyor – for a basic extraction process – to the advanced Barracuda C machine. This combines a compact bucket wheel excavator with a discharge boom operating in tandem with a conveyor system1 .
The Barracuda has three particular features that make it an attractive excavation option for mine operators, according to tkIS:
- Streamlines ore transportation
- Offers predictable operational costs
- Able to eliminate pre-blasting.
In ore transport, the possibilities for integrating the Barracuda with continuous mining/conveyor systems – combined with its ability to excavate hard materials – widens the range of potential mine applications. It can also deliver major cost reductions in comparison to conventional truck transportation. The machine’s electrical drive can also reduce the carbon footprint of mining operations.
“We already identified some cases where one Barracuda shows potential to replace a combination of more than 10 single units of other mining equipment, providing an optimisation of the operation and maintenance efforts required in the mine,” says Paulo Costa, global head of mining systems at tkIS1 .
thyssenkrupp offers a flexible contract for the Barracuda that covers the wear of selected machine parts and guarantees their replacement. This uses a ‘value-based model’ to accurately predict costs for component wear over the machine’s lifetime – one of the main sources of operational expenditures for bucket wheel excavators.
“The offering is part of the company’s digitalisation initiative,” said Stefan Ebert, global product lifecycle manager for tkIS mining systems1 . “It is a great experience to challenge ourselves [about] the individual needs and risk profiles of our customers and flexibly adjust our offering accordingly.”
But is the elimination of pre-blasting that is the main factor which overall makes the Barracuda a leaner, more cost effective and safer mining process option.
Conventional bucket wheel excavators, are unable to cope with harder ore materials and – unlike the Barracuda – still require blasting to fracture in-situ rock prior to extraction. The need for pre-blasting can add more than $0.2 per tonne to extraction costs – a major cumulative cost for multimillion tonne mining operations. The Barracuda, by removing the need for drilling and blasting, can therefore offer significant cost reductions, especially for mine expansions or new mine projects which require investment in new equipment anyway. The use of Barracuda mining machines also offer a more sustainable alternative to blasting, which is subject to increasingly stringent environmental regulations for noise, fumes, dust and vibrations1 .
Mining companies have been quick to buy the Barracuda. Italian-Thai Development Plc has placed an order for two, as has China’s Huaneng Group. Commissioning of these machines is advanced with both companies expecting to begin operations in the coming months1 .
The ideal method to dewater tailings?
The mining industry is urgently looking for alternative methods of storing tailings. The disastrous tailings dam collapse at the Brumadinho iron ore mine in Brazil in January highlighted the ongoing risks associated with dam failure – particularly the loss of life and environmental damage that can result.
One of the safest ways of reducing or eliminating such risks is to reduce the water content in tailing storage facilities (TSFs). This has the added advantage of increasing water recovery – a major environmental and financial concern when mining in dry climates – and reducing the installation’s overall geographical footprint.
The options for reducing stored water content – so-called dry tailings solutions – still face key challenges, however. These include increased operating and equipment costs, and how to handle the dry waste solids that are generated. The technical challenge of dewatering tailings is also exacerbated by particle-size reduction, an industry-wide trend that increases plant yields, improves water efficiency and reduce manpower and electricity costs.
Nevertheless, dry tailings solutions do offer substantial cost reductions over the total lifecycle of the mine. This overall savings is revealed when the costs of closure, land, water balance and carbon footprint are all taken into account, in addition to the upfront capex and opex of the project.
Because every mining application and every ore is different, no single approach provides the best universal method for dewatering tailings. Below, Weir Minerals highlight the main advantages and disadvantages of three promising technologies able to deliver dry tailings, as well as their associated cost factors2
- Paste thickener with GEHO® pump
- Continuous separation with centrifuge
- High pressure filtration with filter press.
Isodry™ paste thickener with GEHO® pump
In this flowsheet, a paste thickener is used to produce an underflow paste (65% w/w) without any free water (Figure 1). This method combines a Weir Minerals Isodry™ paste thickener system with a Warman® centrifugal pump feeding positive displacement pump, such as a GEHO® piston diaphragm. The resulting high solids content slurry is transported by pipeline to the TSF.
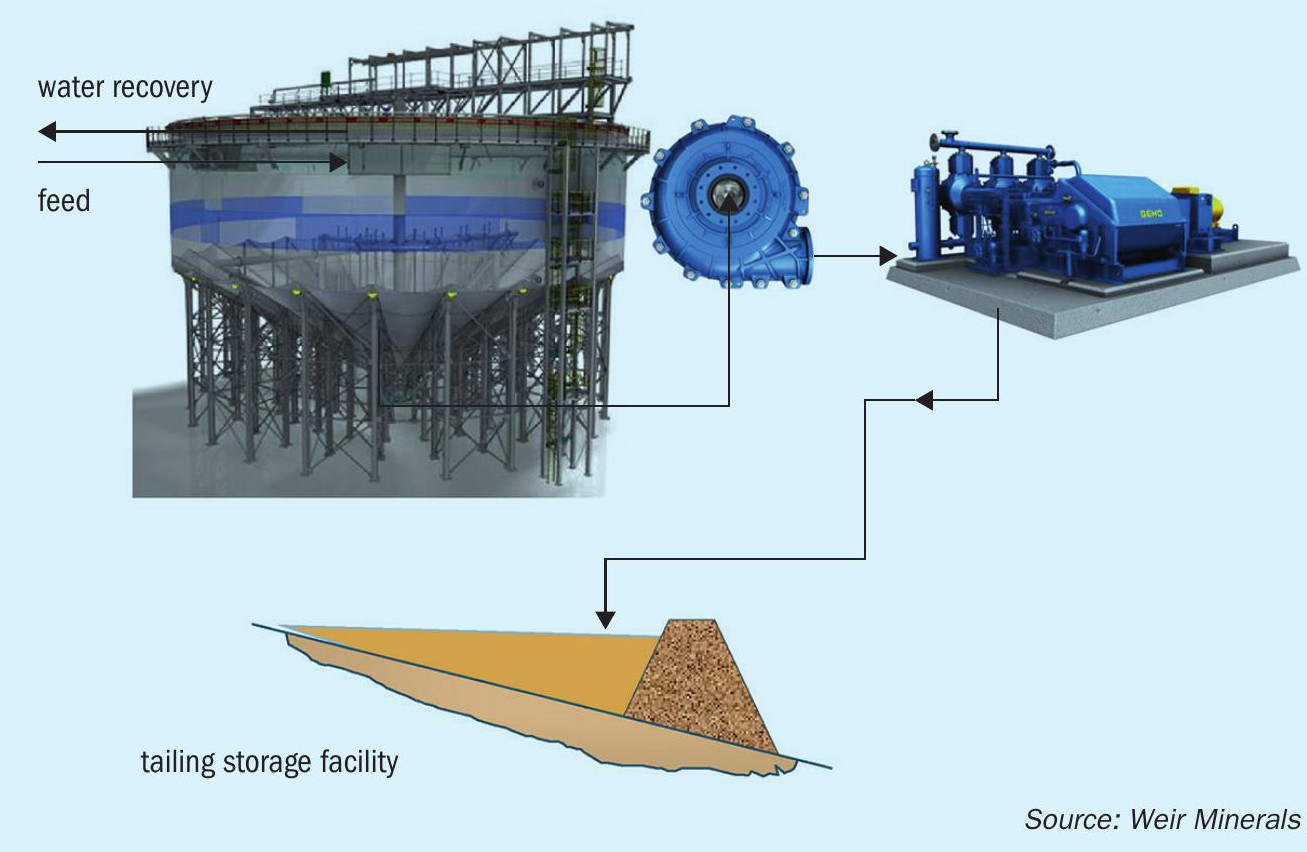
Combining a paste thickener and a positive displacement pump provides the easiest disposal method for slurries without free water. The automation of these operations would require advanced process controls and pump management.
Weir carried out a study to mitigate the risks and design the best system for this disposal method. A pilot pipe loop test was used to find the optimum balance between solids content and pressure drop in pipe line.
The study considered three paste thickeners with a 60-degree cone angle and a high wall height. Advanced process control is necessary to make sure the paste thickener will produce the desired solids content in the underflow – and to control the pumping system and its standby/duty mode. The desired underflow solid content was 65 weight percent with 1,000 m3 /h flow rate at over 200 bars, although Weir Minerals has previously delivered a pumping project for phosphate tailing with 70 percent solids.
Continuous separation with centrifuge
To achieve a higher solids content than is possible by paste thickening, tailings needs to be dewatered using a mechanical separation process.
The continuous separation equipment options are limited to decanter centrifuges, vacuum disk filters and screw presses. The solids contents obtained using centrifuges and vacuum disk filters are both similar, based on Weir Minerals’ experience, with a similar opex/capex too.
Continuous separation is capable of achieving water contents above what is possible with a paste thickener. While dryness levels are still below those delivered by a filter press – which are the highest achievable – this method has the advantage of being continuous not a batch process.
Although disk filters are commercially available in higher capacities, decanter centrifuges will provide a better separation if high percentages of ultrafine particles (<20µm) are present. Therefore, for each project, performing a separate feasibility test for a centrifuge vs a vacuum disk filter can be a valuable exercise.
The Weir Minerals study focussed on a decanter centrifuge producing a solids content of 75 percent. A thickener is also incorporated into the flowsheet to increase and maintain a constant solids content to the separation machine (Figure 2). The use of a single thickener should have a positive effect on capex and opex by reducing the number of centrifuges required
Flocculant will need to be added to the decanter centrifuge feed if clear water is required, although this can double opex. However, in the proposed flowsheet, flocculant is only added to the thickener. The decanter centrifuge actually produces the highest solids content without the addition of flocculant in the centrifuge feed. Concentrate from the centrifuge is fed back into the thickener and the thickener overflow is the only source of water recovery.
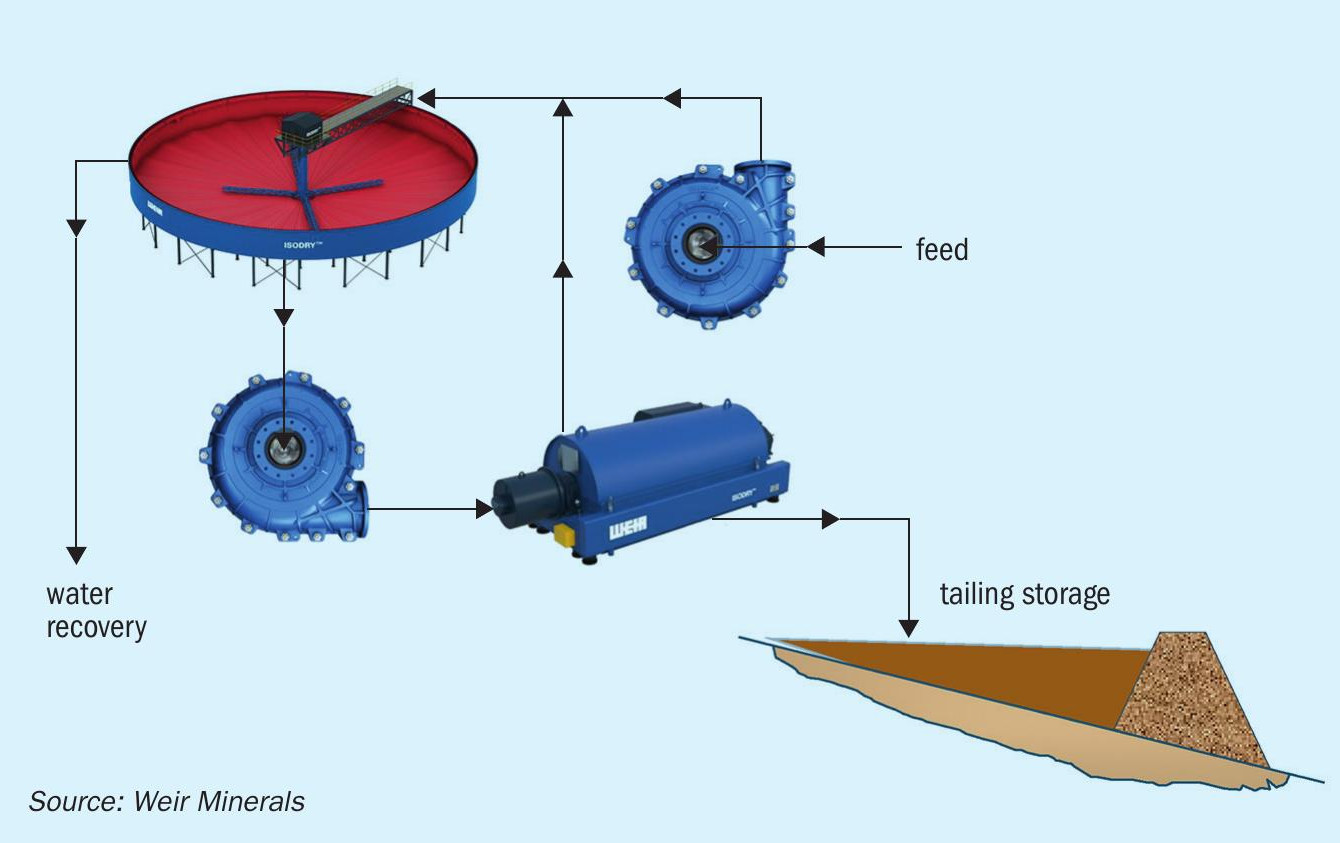
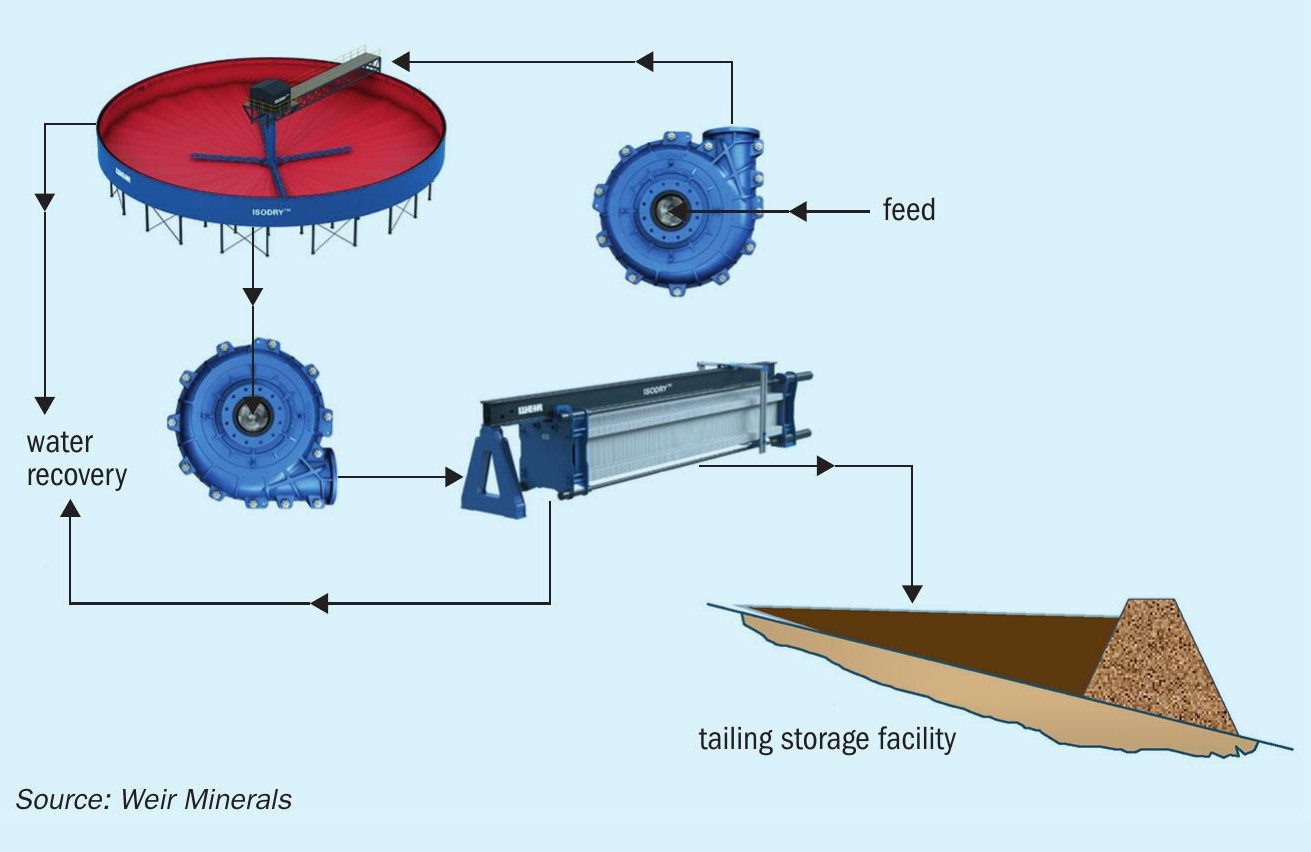
A belt conveyor could be used for conveying separated solids from the centrifuge. The other transport option – after pilot test pumping – would be a positive displacement pumps such as a GEHO® hydraulic driven piston pump.
As a dry tailings solutions, the decanter centrifuge should have the following features:
- High solid capacity
- High torque gearbox
- High speed to separate small particle size
- Low energy consumption – because the main operating cost of this machine is the electrical power (along with flocculant, if needed).
The Weir study considered a system with: one thickener, 18 decanter centrifuges, feed pumps, and one high solid content positive displacement pumping system – with automation to control the feed, machine parameters and washing of the machine when needed.
High pressure filtration by filter press
Filter presses are the best available machines for achieving the highest dryness levels that are often requested for dry stacking projects. The filter press is a batch machine, sized according to its operating volume and cycle time. It can produce a wide variety of tailings products by adjusting the timing of the cycle.
Filters do not require any flocculant. This is because the filtrate is only ‘dirty’ momentarily, in the initial seconds of the filtration process, becoming crystal clear as soon as the cake is formed.
Modern high capacity filter presses for tailings now have a much shorter cycle time and larger production capacity, thanks to the increase in their plate size.
Modern filters typically have between 100-200 large plates and a cycle (mechanical operation) time of 2-5 minutes. Tests are required to optimise the cycle time and the different steps between feeding, squeezing, cake blow etc. The product with the highest dryness is achieved through high-pressure squeezing. A pressure of up to 15 bars is usually sufficient, although in some projects we observed an operational difference at over 20 bars. The cake blow stage, for a large surface filter press, needs large motor compressors (over 500kW) and receivers. These auxiliary compressors can be opex intensive, if not properly designed and for projects where no compromise on dryness is permitted.
The filter cloth is also an important parameter to consider, as the quality of the cloth can influence filtration properties. The cloth itself is also a wear part and generally needs to be changed every few thousand cycles. In high capacity filter presses with a short cycle time, however, filter cloths only need to be changed between four and twelve times every year. Large plates are perfect for high capacity operation, but removing and installing new cloths can be labour intensive, as people are needed to supervise operations and physically change the cloths.
In our study, we considered one thickener, nine filter presses plus all their auxiliaries (feed pumps, valves, squeezing system, compressors, conveyors etc.) and a dry stacking system (Figure 3). Producing a cake with the desired solids content (85% w/w) achieved a water recovery of 95 percent. The gains from this method, in terms of the reduction of TSF volume at an eight degree angle of repose, come at a considerable cost – requiring 10 times more opex, 20 times more capex, together with a team in a dewatering plant to operate the filter press plant.
The ideal dewatering solution?
All flowsheets have their advantage and disadvantages. There is no single ideal method or flowsheet for dewatering tailings which performs best in every key criteria described above. The ‘perfect’ solution is instead site- and project-specific, being influenced by the desired characteristics of the tailings to be produced, the location of the TSF and how the customer wishes to manage their tailings.
Water, mining and the phosphate industry
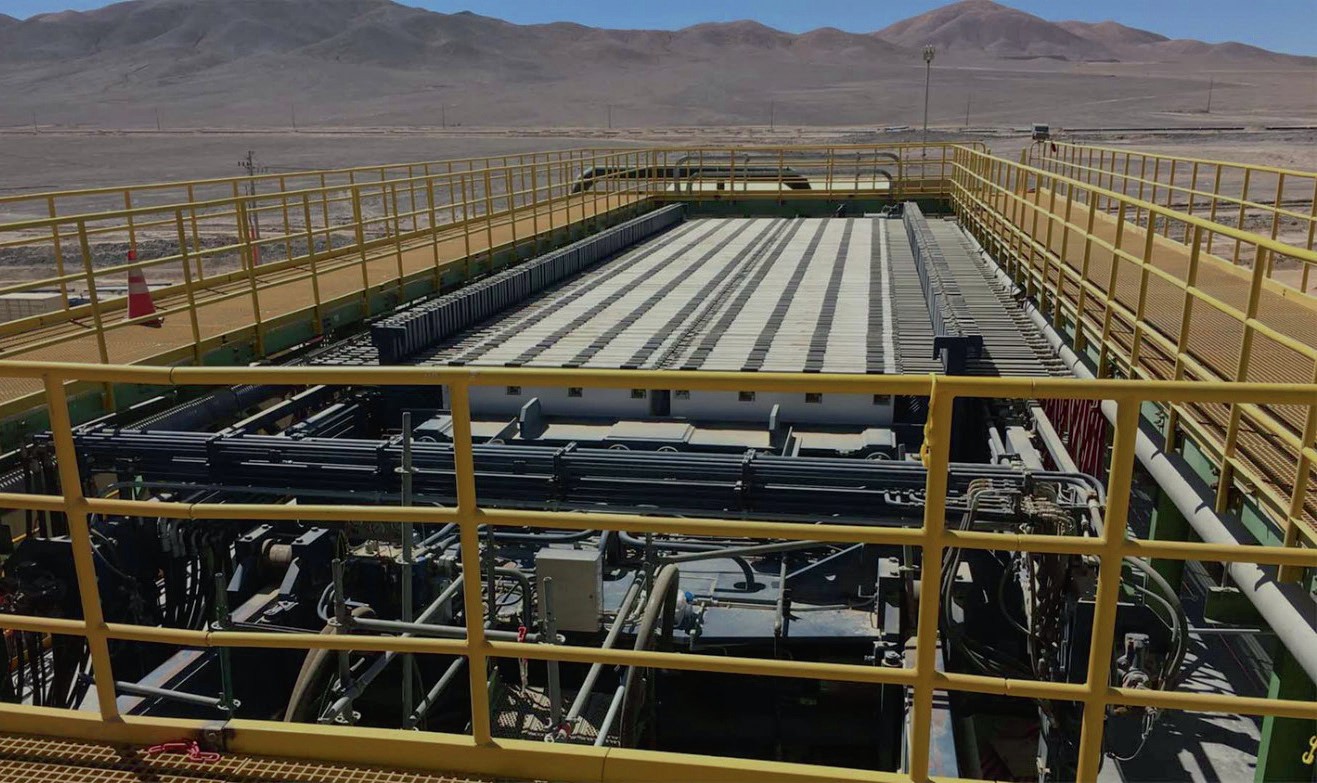
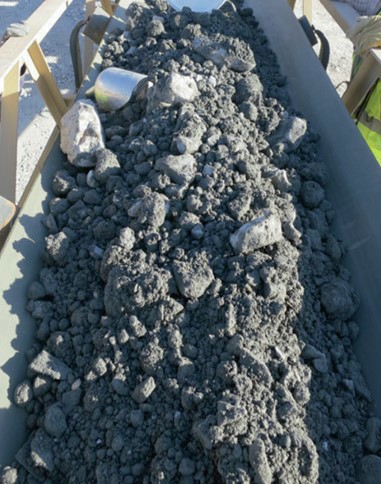
The phosphate industry consumes vast amounts of water and generates large volumes of tailings. Recovering water from these tailings economically, and disposing of the solids, is an increasing challenge for the industry’s miners and producers, as FLSmidth’s Lucy England explains3 .
Shift to dry stack tailings?
The use of pressure filters to recover water has been commonplace in the mining industry for many years. Yet the majority of these are small, low-throughput installations – as the cost of largescale tailings filtration generally becomes too prohibitive at higher tonnages. Tailings are therefore typically dewatered using small pressure filters, with subsequent air drying of the filter cake to an optimum moisture content. Using trucks for tailings transport and placement also adds an additional cost of over $4 per tonne.
To mitigate the risks associated with wet tailings disposal, many mining companies are looking for a step change in filtration and waste disposal technology. This will be necessary if dry stack tailings are to be developed – as a viable replacement for tailings dams – with low enough capital and operating costs to make high-tonnage, low-grade operations viable.
The Colossal filter from FLSmidth
FLSmidth is one of the world’s leading suppliers of solid-liquid separation equipment. The company has been at the forefront of many product developments in thickening and filtration throughout its existence, stretching back more than a 135 years.
There is currently a pressing need to treat, reuse and recycle wastewater, according to FLSmidth. In its view, the mining industry needs to stop thinking of wastewater as waste and start thinking of it as a new industrial water source instead.
As part of this shift in thinking, FLSmidth believes it is vital to recycle as much water from tailings as possible – especially given that the scale of mine production is increasing as water is becoming scarcer. Consequently, there is a particular need for technologies able to dewater large tonnages of tailings, with minimal power consumption, and utilises larger equipment to benefit from economies of scale.
FLSmidth is currently working on solutions that minimise the use of wet tailings, as well as developing methods that make tailing more stable by recycling as much water as possible. To meet industry’s requirement for a large-scale filter press, FLSmidth has developed the Colossal filter. This offers the following benefits:
- Reclaim up to 95% of water for re-use, cutting your costs
- Environmental impact is reduced
- Dry cake material eliminates risk of failures
- Dry cakes can be safely conveyed and even compacted
- Dry material can be restored and re-vegetated.
FLSmidth has also designed a larger Colossal filter for a co-mingling process called EcoTails™ developed in collaboration with Newmont (formerly Goldcorp). This is a fully-integrated waste solution that combines waste rock with dry tailings to create a material called GeoWaste. The tailings fill the void space between rock particles, so reducing oxygen flow and acid rock drainage. The presence of coarse waste rock particles also provides GeoWaste with good shear strength and physical stability. The EcoTails™ process also recycles 90 percent of process water.
The mining industry has traditionally been comparatively slow at adopting new technology and methods, with the capital and operational costs of new equipment being typical barriers to adoption.
“The big question is usually who will be the first to adopt a new approach as new solutions have to be proven before commercial use and there is perceived higher risk in being the first adopter,” says Lucy England of FLSmidth’s wet processing mining division. “Sometimes, the risk is higher when you don’t do anything. Eventually, we hope to see the industry change fully to dry stack tailings, eliminating the risk of wet tailing dam failure.”
England adds: “We strongly believe that water management will be a limiting factor for many mines in the near future, if not already. The time has come to recycle, treat and reuse as much water as we can.”
A pilot test is therefore a necessary prerequisite to properly choose between the different dewatering methods. Allocating time and money on this preliminary step is well spent, as it will result in an optimised project and mitigate the risks that can be associated with tailing projects. Close collaboration between various experts in separation, slurry transport and geotechnics is also required to discover the optimum solution for successful tailings management.
Slavkaliy potash project order
FLSmidth secured a DKK 360 million ($53 million) order from CITIC Construction in February to supply liquid-solid separation equipment to the under-construction Slavkaliy project in Belarus. CTIC is the construction contractor for the greenfield mining project.
Slavkaliy is currently developing a potash mine and production complex to exploit the Starobinskoye potash deposits in the Nezhinsky area of Belarus. The order placed with FLSmidth includes a large number of thickeners, clarifiers, pan-filters and horizontal belt filters.
The items will be supplied as a number of fully-automated ‘equipment islands’. These will be integrated within the plant’s overall automation system, designed previously by FLSmidth.
Equipment deliveries will start by the end of this year and continue into 2021. FLSmidth engineers will then supervise the assembly and commissioning of equipment to ensure the timely completion of the project. The new complex is expected to be completed before the end of 2023. It will have the capacity to produce between 1.1-2.0 million tonnes of potassium chloride annually.
Manfred Schaffer, FLSmidth’s mining president, said: “After the plant engineering order booked in the third-quarter of 2019, we are especially pleased to have now secured this equipment order from CITIC Construction, the contractor for Slavkaliy.
“We are confident this will be a leading, cutting-edge operation with a strong focus on productivity, efficiency and sustainability. The significant level of automation and digitalization, in combination with our equipment, will also mean the lowest possible on-site energy consumption.”
EuroChem’s Usolskiy and VolgaKaliy projects
EuroChem Group’s $2.1 billion Usolskiy project in Russia’s Perm region is now fully operational, while engineering work continues at its sister project, the $2.9 billion VolgaKaliy mine in the Volgograd region, to enable it to begin production in late 2020.
The same potash mining equipment is being installed at both mines. Ural-20R mining machines, transfer hoppers and shuttle cars will be used to transfer ore to each mine’s main line conveyor systems:
- Ural-20R mining machines: these cut an arched roof 3.1 metres high and 5.1 metres wide. Each machine is approximately 12 metres long and weighs 100 tonnes. They are crawler-mounted and electrically-powered each with an average annual capacity of around 600,000 tonnes.
- Transfer hoppers: these operate immediately behind the Ural-20. Being electrically-powered, and approximately 8.4 metres long and 2.3 metres wide with a capacity of 16 tonnes, they are equipped with a conveyor system to transfer ore to waiting shuttle cars.
- Shuttle cars: these bring ore to the conveyor system, which in turn transports the ore to the shaft where it is lifted to the surface. The cars operates using a trailing cable on a reel, allowing them to travel a distance of up to 400 metres. Each shuttle car is approximately 9.0 metres long and 2.6 metres wide, weighs 19 tonnes, and has a 17 tonne payload capacity.
The Ural-20R continuous mining machines are manufactured by Kopeysk Machine-Building in Russia’s Chelyabinsk region. Each of these machines is capable of mining an impressive 600,000 tonnes of ore annually. Usolskiy was operating 20 Ural units last year and will add more over time to keep up with the mine’s ramp-up schedule.
Veolia to supply VolgaKaliy expansion
EuroChem Group has selected Veolia as a technology provider for the expansion phase of its VolgaKaliy potash project in Russia’s Volgograd region.
The mine, which began production in 2018, will incorporate Veolia’s crystallisation technology as part of an expansion scheduled to begin in 2021.
Veolia’s HPD PIC Crystallizer System ™ will be used to manufacture two million t/a of high-purity potassium chloride fertilizer from brines extracted from conventionally-mined potash ore. Veolia Water Technologies will provide the major process equipment required, including multiple HPD PIC Crystallizers, ™ recirculation and transfer pumps, vapour condensers and centrifuges.
“With their proven experience and talented team, EuroChem is pleased to be working with such a strong partner as Veolia,” said Clark Bailey, EuroChem’s head of mining “The expansion phase of our VolgaKaliy project will increase the plant’s capacity to 4.3 million tonnes per year of potash, in grades suitable for both agricultural and industrial applications.”
Klaus Andersen, CEO of Veolia Water Technologies, added: “We are proud to partner with EuroChem on this prestigious project. With the experience from more than 50 references in the fertilizer market, we were able to offer a custom-built system that offers the flexibility to meet a wide range of production requirements.”
State-of-the-art rail wagons
EuroChem ordered 700 bespoke rail wagons for Usolskiy from United Wagon in 2018. Each wagon has a volume of more than 100 cubic metres and is fitted with heavy-duty 25-tonne-axleload bogies, enabling it to carry approximately 77 tonnes. The larger volume of the wagons also lowers their centre of gravity, making them more stable and difficult to overturn.
Wagon hatches are stamp-welded, improving durability and rigidity, and fitted with wear-resistant moulded rubber strip seals. The inside of each wagon is also protected from corrosion using a two-component polymer coating. The new wagons can be used for up to eight years, or one million kilometres [620,000 miles] between overhauls, says United Wagon. That compares with just two years or 110,000 kilometres (68,000 miles) for conventional wagons.
Similarly, K+S Potash Canada (KSPC) ordered 531 custom-built rail cars for its Bethune potash mine site in Saskatchewan. The rails cars, divided between three trains, are used to transport potash from the Bethune mine to KSPC’s Port Moody potash facility in British Columbia. The rail cars begin their journey along a 30 kilometre spur constructed by Canadian Pacific (CP). This connects the 14 kilometres of rail track owned and operated by KSPC at Bethune to CP’s mainline rail track at Belle Plaine.
The rail cars, designed by National Steel Car, can be loaded while in motion and are built to an innovative design. They have the capacity to hold the same volume as a regular rail car while being slightly shorter in length. This optimises rail transport and the timely and efficient delivery of products.
“When trains arrive at our facility in Port Moody, they are unloaded by automatic conveyor to our warehouse or directly onto a ship at one of the world’s most modern potash handling facilities,” said Steffen Brill, K+S Group’s senior director for logistics procurement and execution.
The 531 rail cars met KSPC’s initial requirements for weekly ore transport to Port Moody. The procurement of more cars was planned for when production at Bethune reached full capacity, according to Brill, to transport additional product to the US market.
The Woodsmith mine project
Sirius Minerals is developing the Wood-smith Mine project in the UK. This under-construction polyhalite mine is located six kilometres south of Whitby on England’s North Sea coast. Project construction, which began in May 2017, is scheduled to be completed in 2023.
Sirius expects the polyhalite project to ramp-up to its full capacity of 10 million t/a by the end of 2024.
The project has been in six-month review since September 2019, following a decision by Sirius to withdraw its second-stage financing plan. Mining giant Anglo American subsequently stepped in, making a firm £405 million cash offer for the Woodsmith Mine project at the end of January. The takeover was due to be completed on the 17th of March.
The Woodsmith Mine will access an underground polyhalite seam (up to 70 metres thick) at a depth of around 1,500 metres via two deep shafts – one shaft dedicated to production with the other retained as a service shaft. Shaft sinking contractor DMC Mining Services will use the Herrenknecht shaft boring roadheader (SBR) to construct both shafts. The SBR successfully completed the excavation of two deep shafts for BHP’s massive Jansen potash in Saskatchewan, Canada, recently.

The SBR is suspended from cables connected to winches on the surface. As the SBR descends, a permanent lining is inserted in sections from an upper working deck.
The SBR is designed for much higher sinking rates, while also providing maximum safety for working personnel, compared to conventional shaft sinking methods. The SBR is equipped with a roadheader boom and a rotating cutting drum. This enables the shaft diameter being cut to be varied between eight and twelve metres. The telescopic SBR boom allows the entire shaft cross-section to be excavated to a depth of one metre in a single cycle.
Primary mine development within the polyhalite seam – and most mine production – will be by conventional ‘room and pillar’ mining using continuous miners (CMs). Polyhalite will be also extracted by drill and blast (D&B) production, easing a combination of large drill rigs and battery-powered load haul dump (LHD) loaders.
During the first 25 years of the Wood-smith Mine’s life, approximately 35 percent of the total mined tonnages will come from the D&B production areas, with 65 percent coming from the CM production. Flexible conveyor trains (FCTs) will be used behind the CMs to transport ore. Sirius made the decision to adopt shuttle cars and large battery LHDs to provide more flexibility in the onward movement of ore from the CM and D&B production units.
References