Nitrogen+Syngas 365 May-Jun 2020
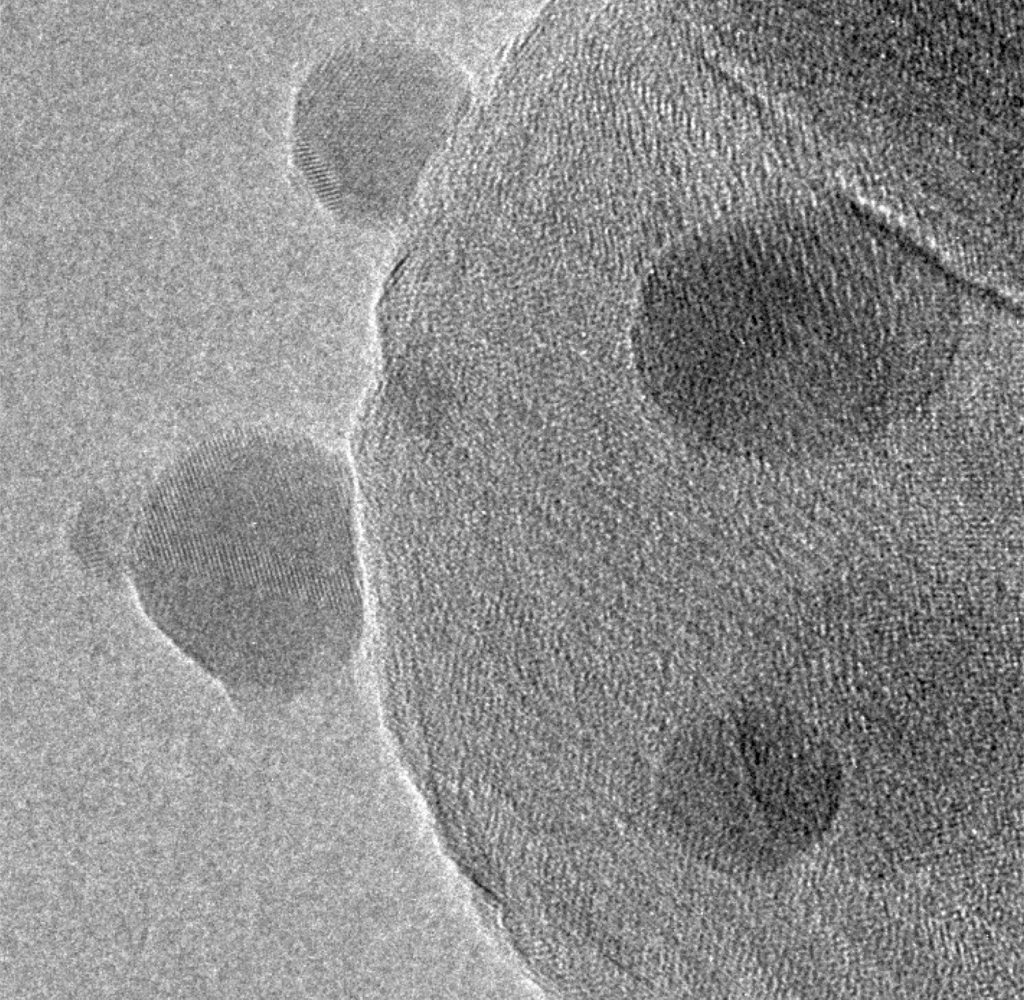
31 May 2020
A new generation of methanol catalysts
CATALYSTS
A new generation of methanol catalysts
Haldor Topsoe has launched a new methanol synthesis catalyst, MK-181 PRIME, based on new technology developed via close study of copper-zinc interactions on the catalyst surface.
The methanol market has grown at a rapid pace over the past decade, virtually doubling in size from 43 million t/a in 2009 to 84 million t/a in 2019; an average annual growth rate of 7%. Much of this growth has been driven by rapidly rising demand in China, where methanol is widely blended as a vehicle fuel or converted into dimethyl ether or polyethylene and polypropylene – the latter via methanol to olefins (MTO) processes – in addition to the conventional chemical derivatives such as formaldehyde, methyl methacrylate and acetic acid which predominate in the rest of the world.
At the same time, however, producers are also under increasing pressure to lower the environmental footprint of methanol manufacture, in particular emissions of carbon dioxide and equivalent gases to the atmosphere, which contribute to climate change. A variety of different approaches are being pursued to achieve this, from the use of alternative feedstocks, including landfill gas, biogas from the degradation of organic waste, gasification of municipal waste or biomass, or even electrolysis of water using renewable electricity to produce hydrogen, which can then be directly combined with carbon dioxide.
These different approaches impose different requirements upon reforming and methanol synthesis catalysts. In Denmark, Haldor Topsoe has been engaged in intensive research and development efforts to produce a suite of catalysts suitable for such disparate technologies, one of the most recent fruits of which has been the MK-317 SUSTAIN methanol catalyst, designed for the direct conversion of carbon dioxide into methanol with high stability towards CO2 , and capable of operating at low temperatures to achieve better hydrogen efficiency. The catalyst is expected to be installed at a renewable methanol facility in Sweden.
Increased efficiency
However, as promising as these different approaches may be, most are experimental or in development phases and only represent a small slice of world methanol production. To achieve reductions in carbon footprint on a significant scale today, and indeed for the foreseeable future until there is widespread adoption of low carbon technologies, will mean utilising present methanol production technology, mainly based on natural gas feedstock or, in China, coal. In such a case, the target must be to increase the efficiency of the process as much as possible in order to lower the energy input requirement per tonne of methanol produced. On a global scale, even an increase in efficiency of 1 or 2% for the world’s methanol production could lead to reductions in CO2 output of up to 500,000 t/a.
For such applications, Haldor Topsoe have been working on improvements to their existing catalyst range, currently based around their high performance MK-151 FENCE catalyst. Launched just over 10 years ago as an upgrade to the previous MK-121 catalyst, MK-151 uses zinc oxide (ZnO) and alumina (Al2 O3 ) to create a barrier between active highly dispersed copper particles to help prevent sintering under the reducing conditions of methanol synthesis1 .
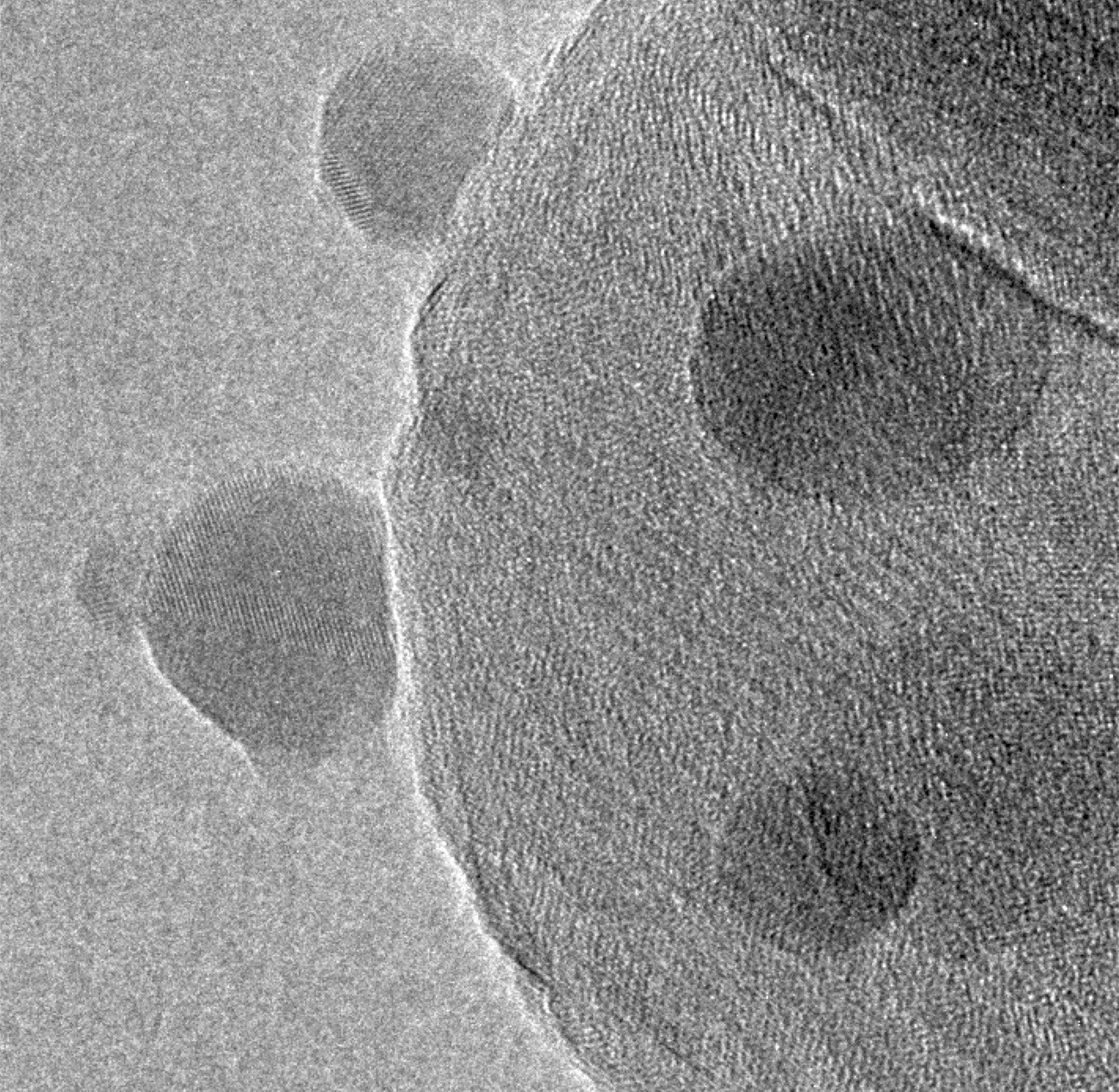
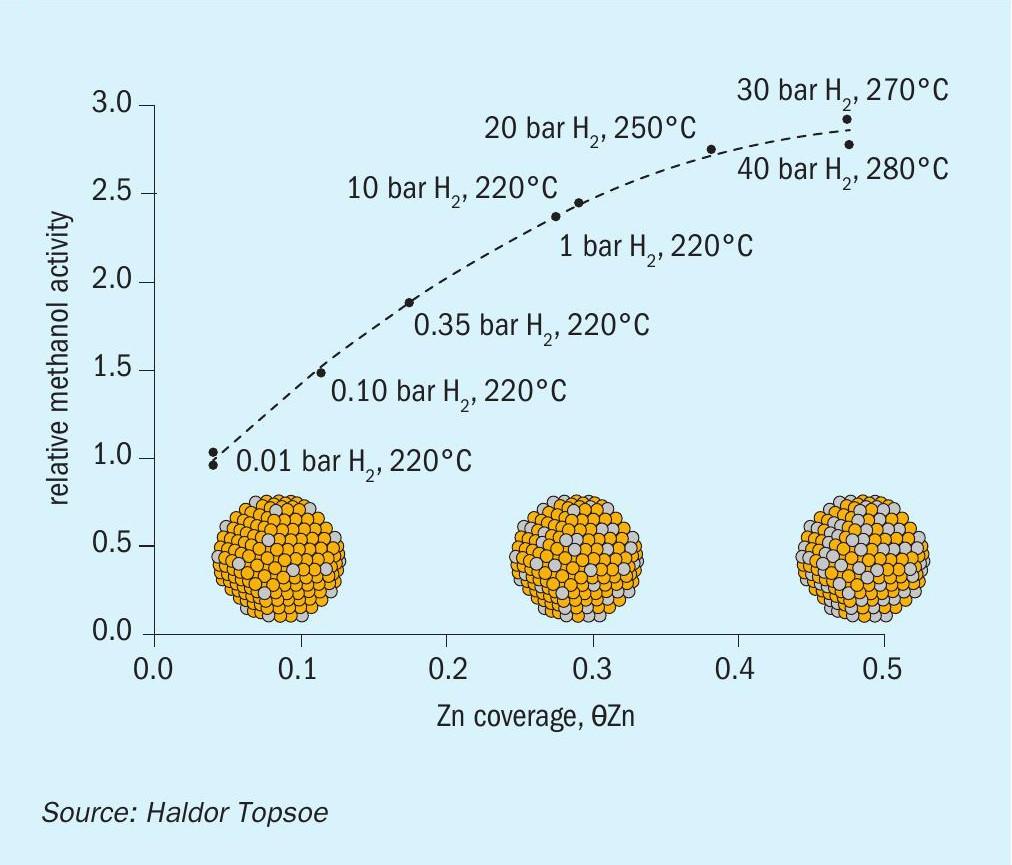
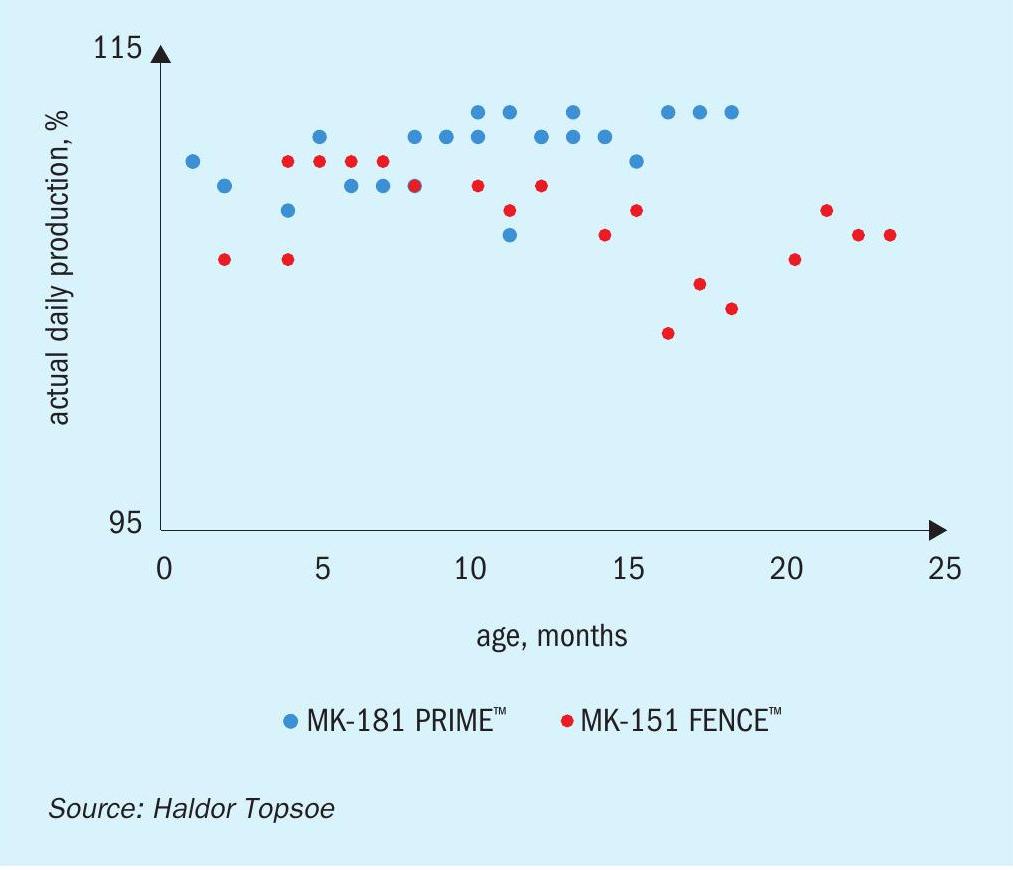
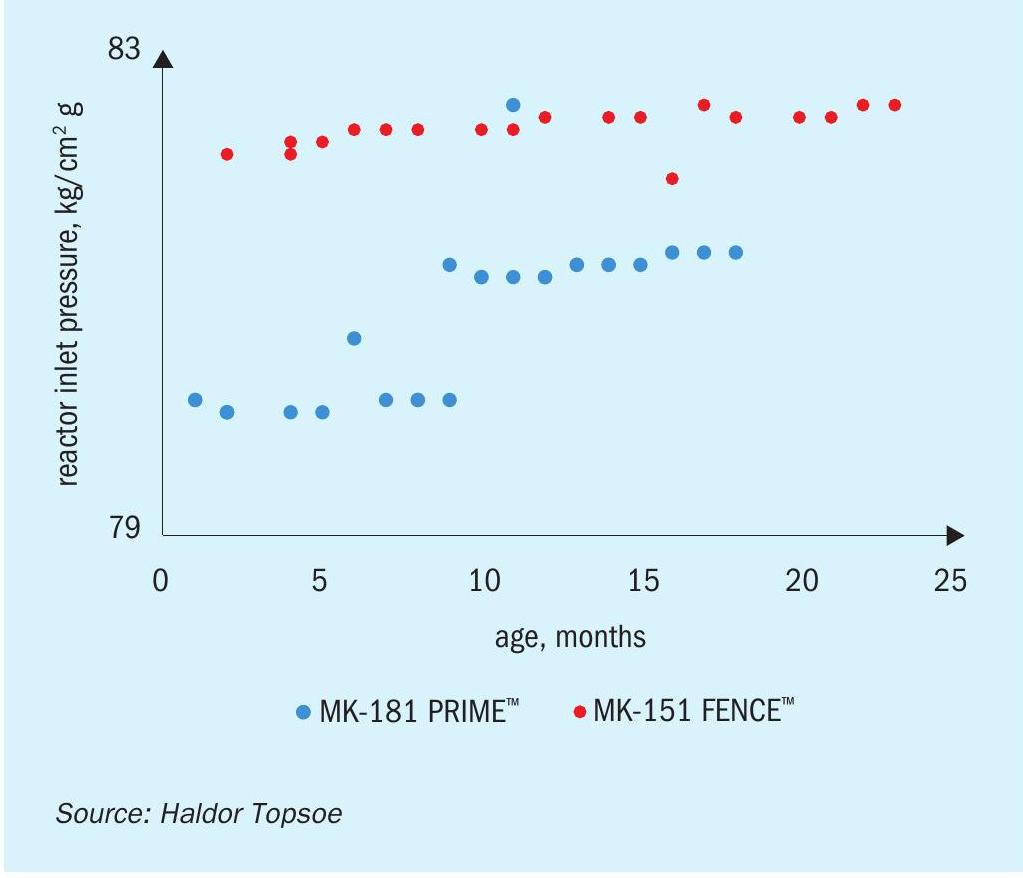
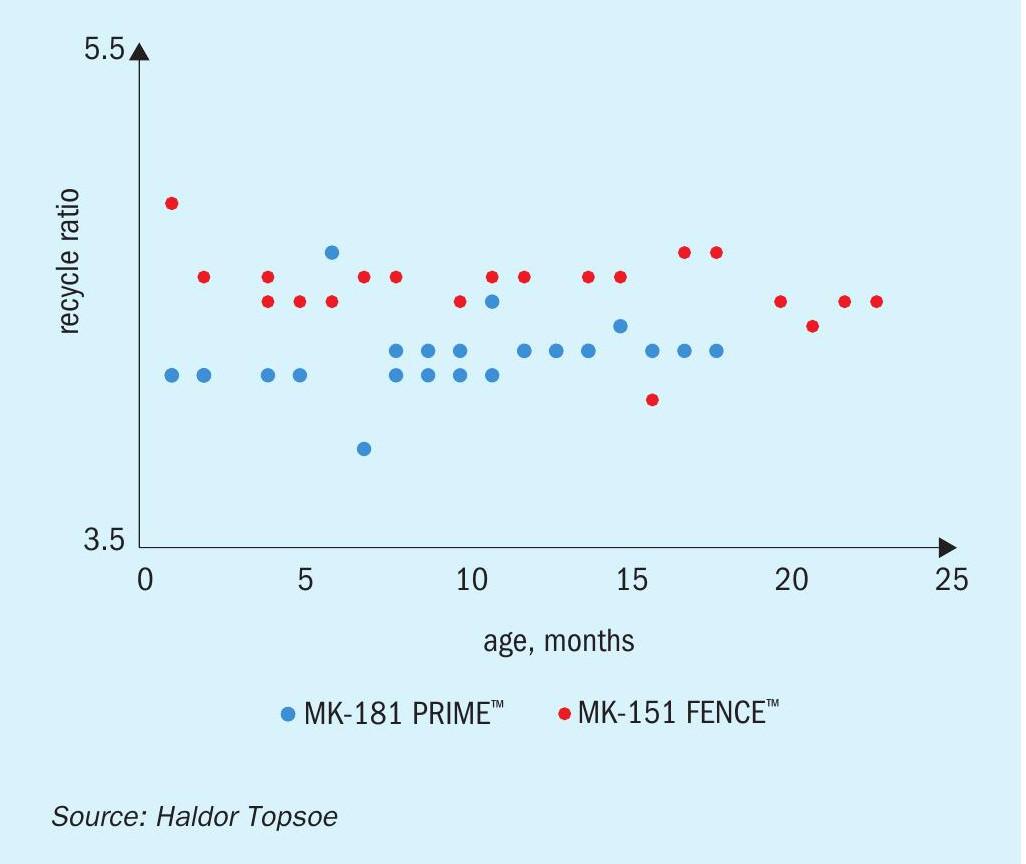
MK-181 PRIME
MK-181 is based on leading edge research to develop a methanol catalyst with the highest activity while retaining the high stability of the previous generations of MK catalysts. The aim has been to deliver higher reaction rates and hence efficiency, allowing producers to choose between achieving lower specific energy consumption or higher methanol production for a given charge of catalyst. As with previous generations it is supplied as 6mm x 4mm pellets and it is made from copper nanoparticles dispersed in alumina with a zinc oxide promoter. However, Topsoe’s research, conducted in cooperation with the Center for Individual Nanoparticle Functionality (CINF) at the Department of Physics of the Technical University of Denmark2 , showed that the size of the zinc oxide nanoparticles was found to influence the coverage of the copper surface with nanoparticles of Zn, and a higher coverage was found to result in higher activity. Based upon this insight, Topsoe has developed a unique way of boosting the methanol synthesis activity via what it calls “PRomotion by Inter-Metallic Engineering” – or PRIME™ technology.
Mechanism
A typical methanol catalyst consists of copper (Cu) nanoparticles mixed with nanoparticles of ZnO and Al2 O3 . Although Cu can function alone as a methanol synthesis catalyst, its activity is substantially boosted by the interaction with ZnO, which on its own has only negligible catalytic activity. Using transmission electron microscopy (TEM), Topsoe’s researchers studied reduced methanol catalyst and found that it consisted of an agglomeration of Cu, ZnO, and Al2 O3 nanoparticles in intimate contact. Figure 1 shows an electron microscopy image of zinc oxide particles (the small spheres) interacting with copper particles (the larger spheres). The crystalline matrix of the particles can be observed as the pattern of parallel lines on the particles. The copper lattice fringes extend to the projected surfaces of the copper nanoparticles NPs without changes in their spacing and structure, indicating that the copper surfaces are in direct contact with the surrounding gas. The copper surfaces can thus only be covered with a sub-monolayer of zinc, confirmed with x-ray photoelectron spectroscopy (XPS) measurements.
It appears that in the reducing environment of the process, a copper-zinc surface alloy is formed by incorporation of zinc atoms into the copper nanoparticles, via equation 1.
ZnO(s) + CO = Zn + CO2 (1)
High zinc coverage is observed within a few hours on exposure to synthesis gas at 220°C, eventually reaching a steady state equilibrium. Topsoe’s work with the Technical University of Denmark attempted to quantify this via modelling at different gas pressures and temperatures, representative for methanol synthesis, for a series of copper surfaces, including steps, edges, and corners. It found that zinc coverage increases steeply for lower CO/CO2 ratios and more slowly at higher CO/CO2 ratios, as a result of Zn-Zn interactions. This was then confirmed for real samples via a variety of experimental techniques. Furthermore, synthesis activity appeared to be strongly related to the amount of zinc alloyed at the copper surface (Figure 2).
The model predicts that catalysts prepared with smaller ZnO particles will be very active because of an enhanced spillover of Zn to the Cu surfaces; hence, it is the thermodynamic activity of the promoter phase, ZnO, that determines promotion of the methanol synthesis activity. It also indicates that very small Cu nanoparticles (<100Å) will lead to lower Zn coverage and hence potentially lower methanol conversion. An alternative approach to optimising the performance of the methanol catalyst is to enhance Zn in the Cu surface by increasing the reduction potential of the synthesis gas via high CO:CO2 ratios (around 10 seems to be optimal).
Benefits
Optimising the zinc coverage of the copper nanoparticles in this way allows MK-181 PRIME to have very high activity, which in turn leads to a high per pass conversion rate. This means that less unreacted gas needs to be recirculated, lowering energy consumption and improving the overall reaction efficiency. This not only lowers the cost of producing each tonne of methanol, but also reduces the CO2 generated in doing so. In addition, MK-181 PRIME is designed for the highest possible selectivity for methanol synthesis, which means that fewer by-products are formed during the reaction. This improves feedstock utilisation on the one hand, and also reduces the energy required for downstream distillation, which again reduces CO2 emissions per tonne of methanol through improved energy efficiency. Finally, the combination of PRIME and FENCE technologies in MK-181 PRIME leads to a high and stable conversion rate over the entire catalyst life cycle.
Industrial experience
Two charges of MK-181 PRIME are currently in service with major methanol producers, and have demonstrated significant improvements in plant performance. Being one of the worlds most experienced methanol producers and keen to continuously improve their production, the customer elected to assess MK-181 PRIME at their plant, which has extensive R&D capabilities. Following an initial evaluation, the company installed a charge of MK-181 in early 2018. Figures 3(a)-(c) show some of the results that have been obtained compared to the previous catalyst charge. The experienced operators have been able to optimize production to achieve an approximately 3% improvement in performance. As noted above, they found that as well as a higher production rate, the recycle ratio is also lower, providing energy savings in the recirculator. Higher per pass conversion also means that the loop pressure remains low for a longer period of time from the start of the run, and a lower reactor inlet pressure reduces the compression demand on the syngas compressor, meaning that the plant was able to simultaneously achieve higher production and lower energy consumption, boosting profits while reducing environmental impact.
References