Sulphur 388 May-Jun 2020
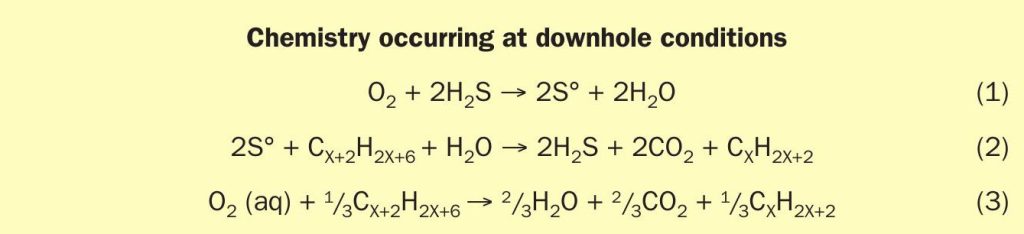
31 May 2020
Degradation of chemical additives under downhole conditions
H2S PRODUCTION IN SHALE RESERVOIRS
Degradation of chemical additives under downhole conditions
When producing from shale reservoirs, technologies such as horizontal drilling and hydraulic fracturing have been used successfully to access hydrocarbons that otherwise could not be. A less publicised issue in producing from certain hot shale gas reservoirs (T > 100°C) is the presence of H2 S and organo-sulphur compounds in the production fluids. In trying to understand the non-biogenic sources of H2 S, Alberta Sulphur Research Ltd has been involved in studying the decomposition of chemicals used in hydraulic fracturing when exposed to high temperature and high pressure.R.A. Marriott, J.J. Marrugo-Hernandez and R. Prinsloo of ASRL discuss the findings of the study.
Fossil fuels, at present, provide around 85% of the world’s energy need1 . At the same time, energy demand is expected to grow worldwide by an average of 1.2%. As such, CO2 emissions could increase by 30% by 2030, even if the increases in energy efficiency and the intensification in renewable and nuclear energy is accounted for. Consequently, to sustain the energy demand, industry is continuously exploring alternative fuels which can help drive down the carbon footprint.
Among the multiple alternatives, natural gas appears to meet the short term requirements in helping to lower CO2 emissions.
Natural gas can be found in conventional and unconventional reserves2 . While conventional plays have been extensively explored, drilled and produced successfully in the last century, the more challenging unconventional plays have only emerged in the last 20 years3 . The late exploration and production of shale plays have coincided with the advancement in combined technologies of horizontal drilling and hydraulic fracturing, leading to economically feasible extraction of natural gas.
Hydraulic fracturing fluid is a combination of water, proppant (approximately 10%) and chemical additives (0.5-3%). Each additive is incorporated into the fracturing fluid to achieve a desired result, be it corrosion inhibition, anti-foaming, lubrication, among others and it is specifically formulated for a selected well. Two wells within the same reservoir could be fractured with different additives (different fracture packages), as physical and chemical conditions are known to vary within wells producing from the same reserves. Many of the chemicals used for fracturing applications in the US and Canada have been disclosed to the public via online databases such as Fracfocus. While the list of chemicals is quite extensive and many of them have been widely applied in multiple processes, the degradation and possible reactivity under downhole conditions is still unknown.
Although native shale gas is often regarded to be sweet (low H2 S); in reality, shale gas can contain tens to several hundred parts per million of native hydrogen sulphide (H2 S). However, when producing from hot shale reservoirs (T > 100°C), the H2 S levels have been reported to increase once production is ongoing for a few months. This is particularly challenging for producers who are required to treat gases with variable concentration of H2 S.
Anecdotal field evidence shared with the authors suggests that shale gas can show an increase in total sulphur concentration in the gas phase, from undetectable levels to percent levels over the course of several months.
ASRL’s research group has been studying the degradation of chemical additives under downhole conditions for several years4,5,6,7,8 . Initially, the decomposition of sulphur-containing surfactants, corrosion inhibitors and biocides were investigated. Under high temperature and high pressure, several of these additives were capable of producing hydrogen sulphide and organo-sulphur compounds through various mechanisms9 .
In trying to better link the degradation of sulphur-containing additives with the delayed souring of shale gas, ASRL has come to realise that the water used for hydraulic fracturing is not degassed and is saturated with oxygen at field conditions. Consequently, during fracturing, the oxygen present in the fluid can rapidly react with native H2 S producing elemental sulphur at downhole conditions (reaction 1). Once the elemental sulphur is generated, it can react with geogenic or anthropogenic hydrocarbons present in the reservoir (reaction 2).
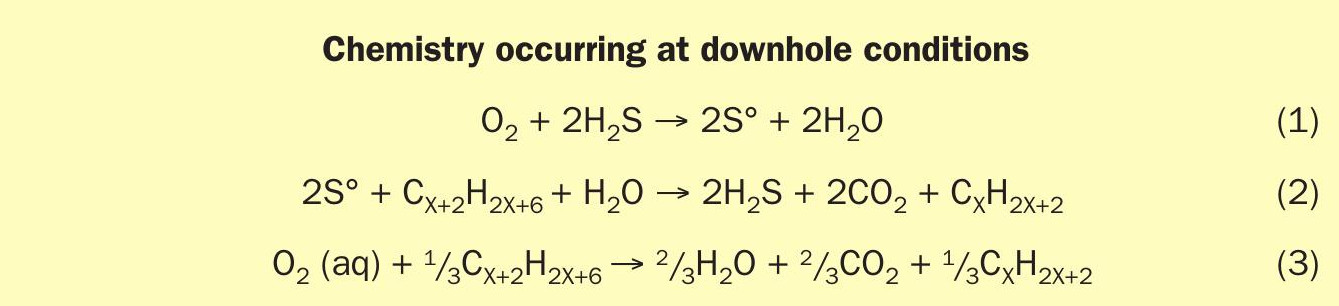
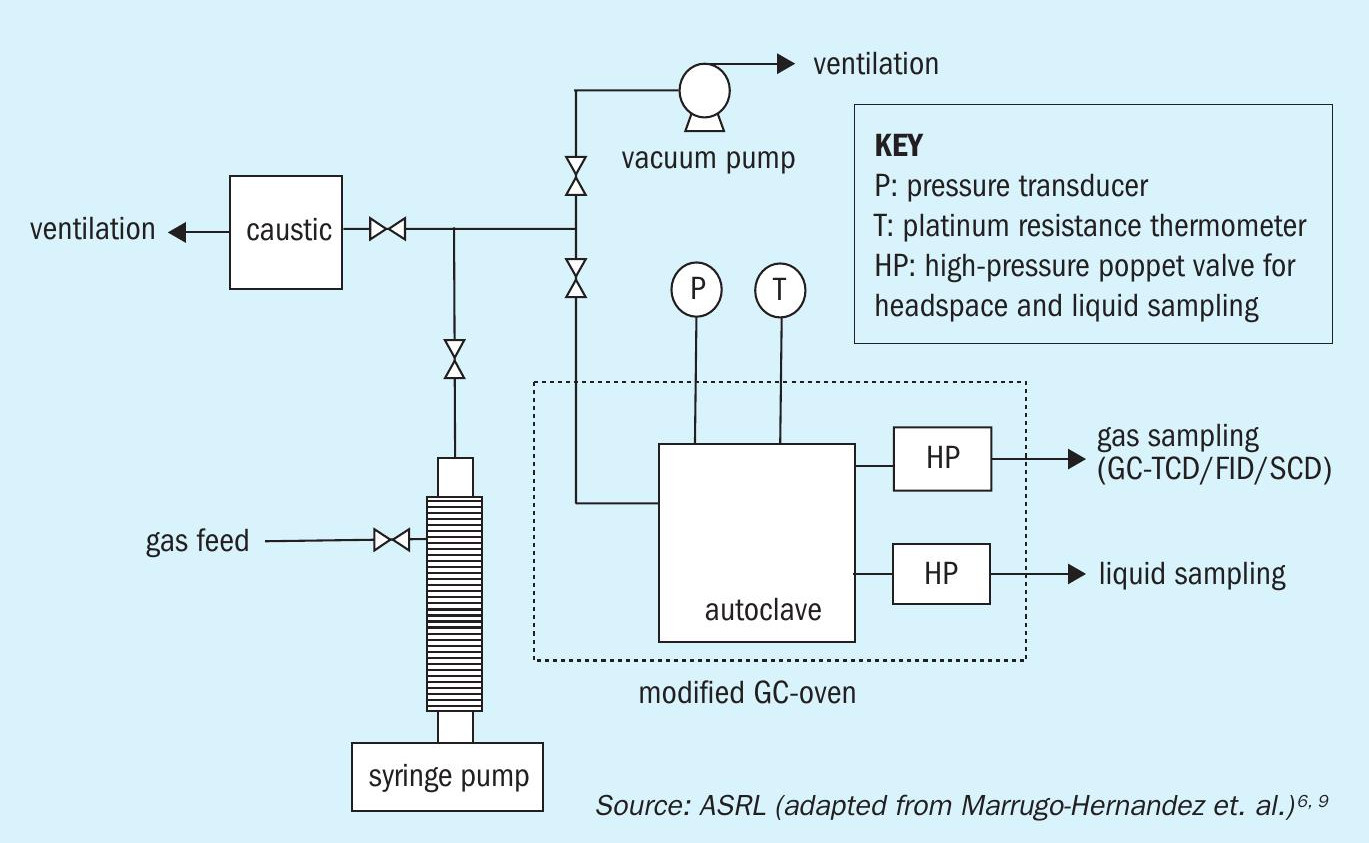
When combining both reactions 1 and 2 (reaction 3), it can be seen that the oxygen present in the fracturing fluid can temporarily scavenge the native H2 S and regenerate it later when reacting with hydrocarbons. As such, by studying the H2 S formation kinetics of sulphur-oxidation reactions involving chemical additives, the understanding of the chemistry occurring at downhole conditions can be enhanced to explain better the shale gas souring observed on the fields. In the study presented here, six commonly used chemical additives were selected (due to their higher disclosure rate and variable organic functional groups) and reacted with elemental sulphur at various downhole conditions. The H2 S concentration was measured over time, and kinetic parameters of each additive were determined. All six additives were used individually and later combined as a mixture when reacting with elemental sulphur.
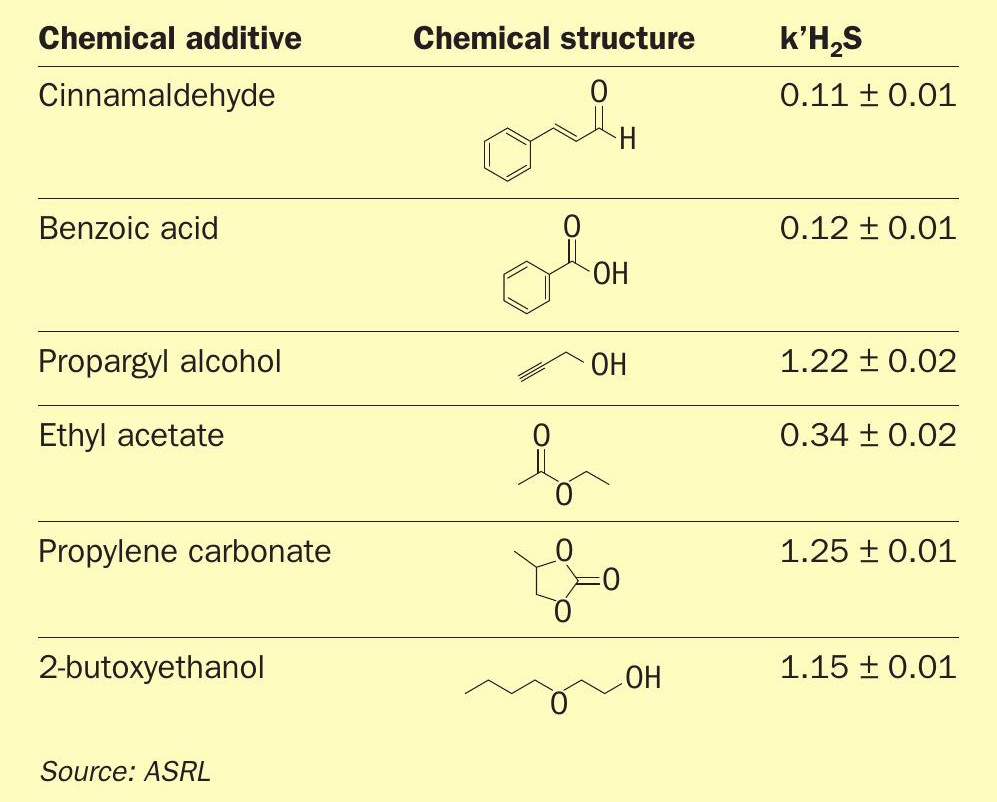
Materials and methods
All the additives and phosphoric acid (85 wt-%) were purchased from Sigma-Aldrich. The water was polished to a resistivity of 18.2 MΩ·cm (EMD Millipore model Milli-Q type 1) and then degassed under vacuum for a minimum of 12 hours. Control of pH was achieved by the addition of 25 mM phosphate buffers.
Experiments were completed in an overhead-stirred 50 mL autoclave (316 stainless steel, fully protected with a corrosion-resistant tantalum film) with operating conditions up to p = 24.1 MPa and T = 300°C, previously described by Marrugo-Hernandez et al (Fig. 1)10 . The system was held isothermally by a modified Hewlett-Packard 5890 GC oven. The temperature of the system was measured by two 100 ohm, four-wire platinum resistance thermometers connected to a Pico Technology PT-104 data logger.
The high purity N2 gas was delivered and used to maintain constant pressure throughout the experiment via a high-pressure syringe pump (Teledyne ISCO Model 260D). The pressure in the system was monitored by a Keller PA-33X pressure transducer. The sampling of the headspace gas was automatically controlled by a high-pressure poppet valve (HP). When sampling, the HP valve was opened for 100 milliseconds, permitting the release of an aliquot of the high-pressure gas from the headspace to flow into the online gas chromatograph.
Before running the experiments, each additive was prepared to a concentration of 500 ppmw. The reactor was loaded with 50 mL of the mixture (water + additive + buffer) and the required amount of elemental sulphur.
The reactor was then pressurised and heated up to the target pressure and temperature. During the reaction high-pressure and high-temperature gas aliquots were withdrawn, and gases concentration were quantified on regular time intervals via the online GC coupled with thermal conductivity detector (TCD), flame ionisation detector (FID) and a sulphur chemiluminescence detector (SCD).
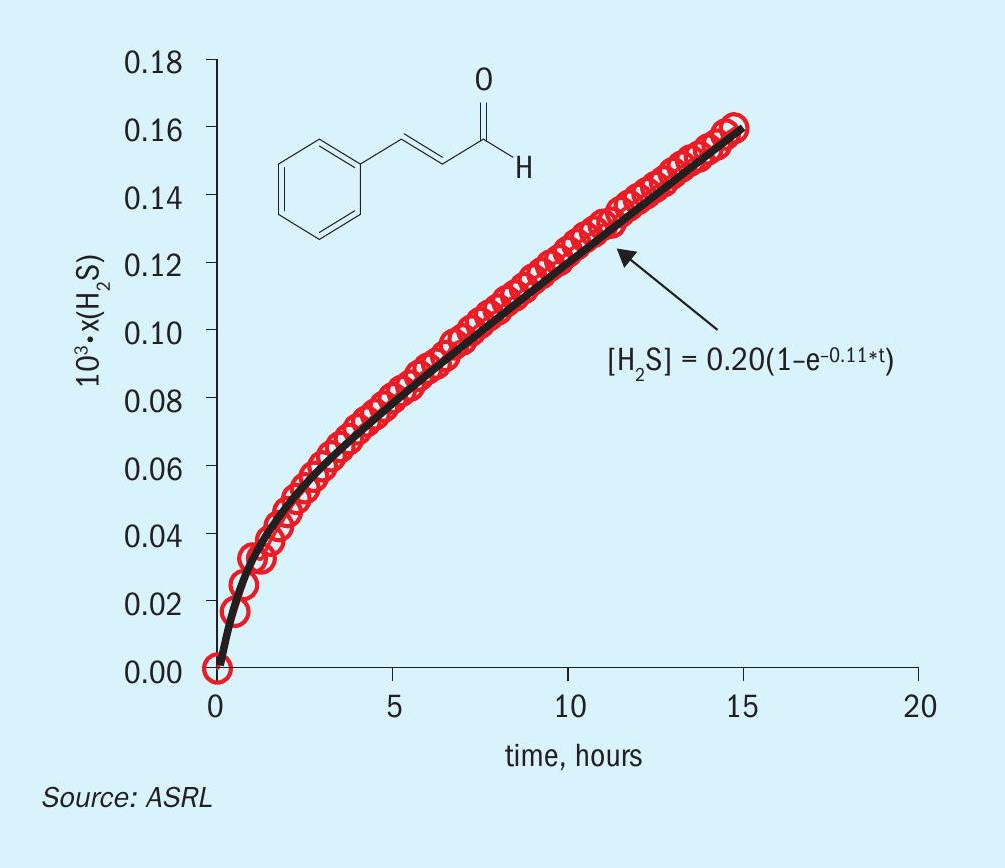
Results and discussion
The six common chemical additives are highlighted in Table 1 with their respective chemical structures and corresponding rates. These chemicals were selected based on the study of Sumner and Plata, in which a spatial statistical analysis was performed on all the publicly available databases, and a list of the most frequently used additives was constructed11 . Note that the compounds selected for this study did not contain any halogen atoms, to avoid possible formation of corrosive chlorine or bromide.
When reacting the chemical additives with elemental sulphur at high-temperature (125°C ≤ T ≤ 175°C) and high-pressure (p = 140 bar), the only species observed in the gas phase were H2 S and CO2 . Note that no organo-sulphur species were detected as by-products for the additives used in this study.
As the reaction progressed, the change in the concentration of these species (H2 S and CO2 ) over time was monitored. Once finalised, one can obtain the H2 S evolution graphs for each compound (Table 1). With the data obtained from the evolution plots one can fit a first-order product generation equation ([H2 S] = α(1-e-kH 2St )) and therefore, obtain various kinetic parameters such as the H2 S formation rate constant (kH2 S).
In Fig. 2, the H2 S evolution plot is shown for the sulphur dehydrogenation reaction of trans-cinnamaldehyde.
The solid line corresponds to a first-order product formation. Each chemical additive was reacted individually with elemental sulphur at T = 150°C and p = 140 bar and the H2 S kinetic parameters are listed in Table 1.
Note that Fig. 2 shows a pseudo rate up to 15 hours, where the reaction has a constant concentration of soluble sulphur (sulphur is in excess of saturation). Once the sulphur is no longer in excess, the rate decreases with decreasing sulphur concentration. The kinetic parameters in Table 1 are reported for the early portion of the plot, where they are considered pseudo first order (k’ = kKsatn [S8 ])
These additives can be arranged in decreasing order as follows: propylene carbonate > propargyl alcohol > 2-butoxyethanol > benzoic acid > cinnamaldehyde. This trend follows the water solubility of these compounds, and it could be inferred that the higher the solubility (more hydrophilic), the faster the dehydrogenation reaction with elemental sulphur was at downhole conditions. Note that it is possible that the chemical additives first undergo hydrolysis and the hydrolysis products are dehydrogenated by elemental sulphur at downhole conditions. H2 S formation is unlikely to occur in a single step. This could explain why the higher the solubility, the faster it generates H2 S.
The sulphur mass balance of these experiments was found to be lower (50% to 65%) when compared to previously studied systems. When accounting for the carbon mass balance it was found that the numbers were less than 10% of the loading for all the chemical additives studied. However, CarSul (carbon-sulphur polymers) formation was evident once the reactor was cooled to room temperature and cleaned for subsequent experiments. CarSul formation could impact production as it could damage the reservoir and limit future production.
Finally, the results illustrate that certain chemical additives used for hydraulic fracturing can react with elemental sulphur at downhole conditions and generate H2 S. It is essential to highlight that shale plays have variable bottom-well temperatures (variability in well depth), therefore changing the kinetics of the H2 S being formed by this mechanism. In lower temperature wells, a slower reaction would be expected in comparison to a hotter well. Consequently, it would take longer for the H2 S concentrations to reach a significant level in colder wells. Although these results exemplify one of the multiple mechanisms by which a shale well could sour, the overall souring of a shale well could be a combination of multiple mechanisms, due to the complex nature of these chemical processes.
Conclusions
The sulphur dehydrogenation reaction with six chemical additives (propylene carbonate, propargyl alcohol, 2-butoxyethanol, benzoic acid, cinnamaldehyde) resulted in variable amounts of H2 S, CO2 and CarSul at downhole conditions. The H2 S formation rate was determined for all six additives and was found to follow the water solubility trend. Finally, it is essential to bear in mind that the fracturing fluids are composed of hundreds of chemical additives, and each chemical can potentially be hydrolysed or dehydrogenated by elemental sulphur. Therefore, one can expect a much more complex mixture, where multiple chemical reactions could contribute to the total H2 S being generated. Therefore, future research in this area is expected.
Acknowledgement
The authors are grateful to the member companies of ASRL and for Discovery Grant support from the Natural Science and Engineering Research Council of Canada (NSERC). Juan J. Marrugo-Hernandez is grateful for support from the Vanier Program.
References