Nitrogen+Syngas 365 May-Jun 2020
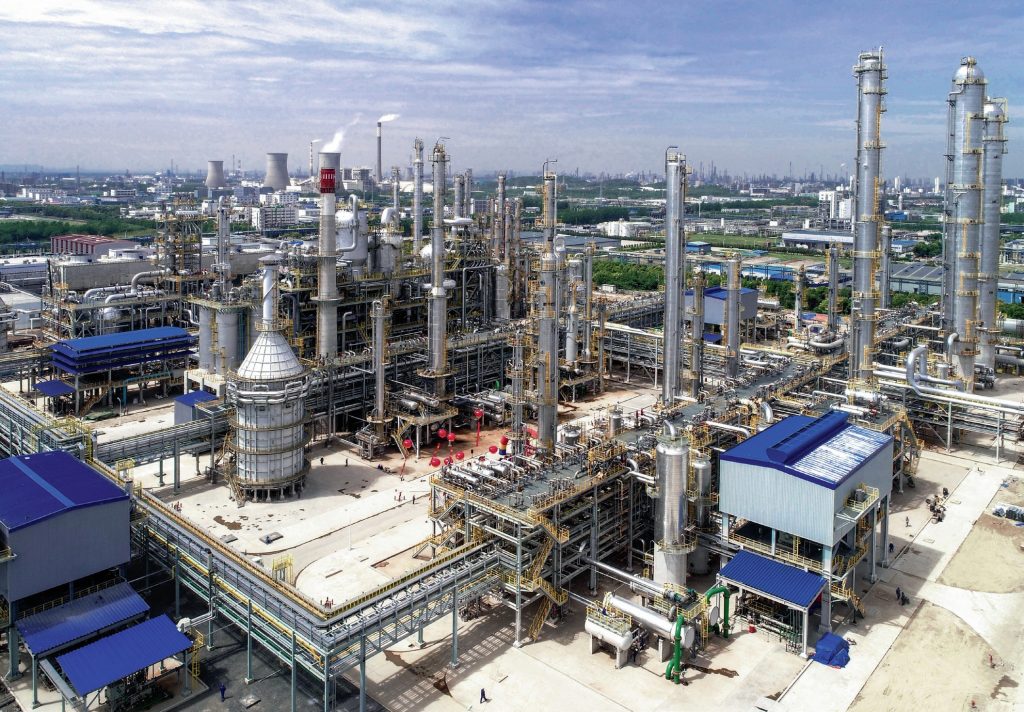
31 May 2020
Methanol demand for olefins production
METHANOL TO OLEFINS
Methanol demand for olefins production
Olefins production from methanol, particularly in China, has come to dominate the methanol market over the past few years. However, environmental and market concerns complicate the outlook there.
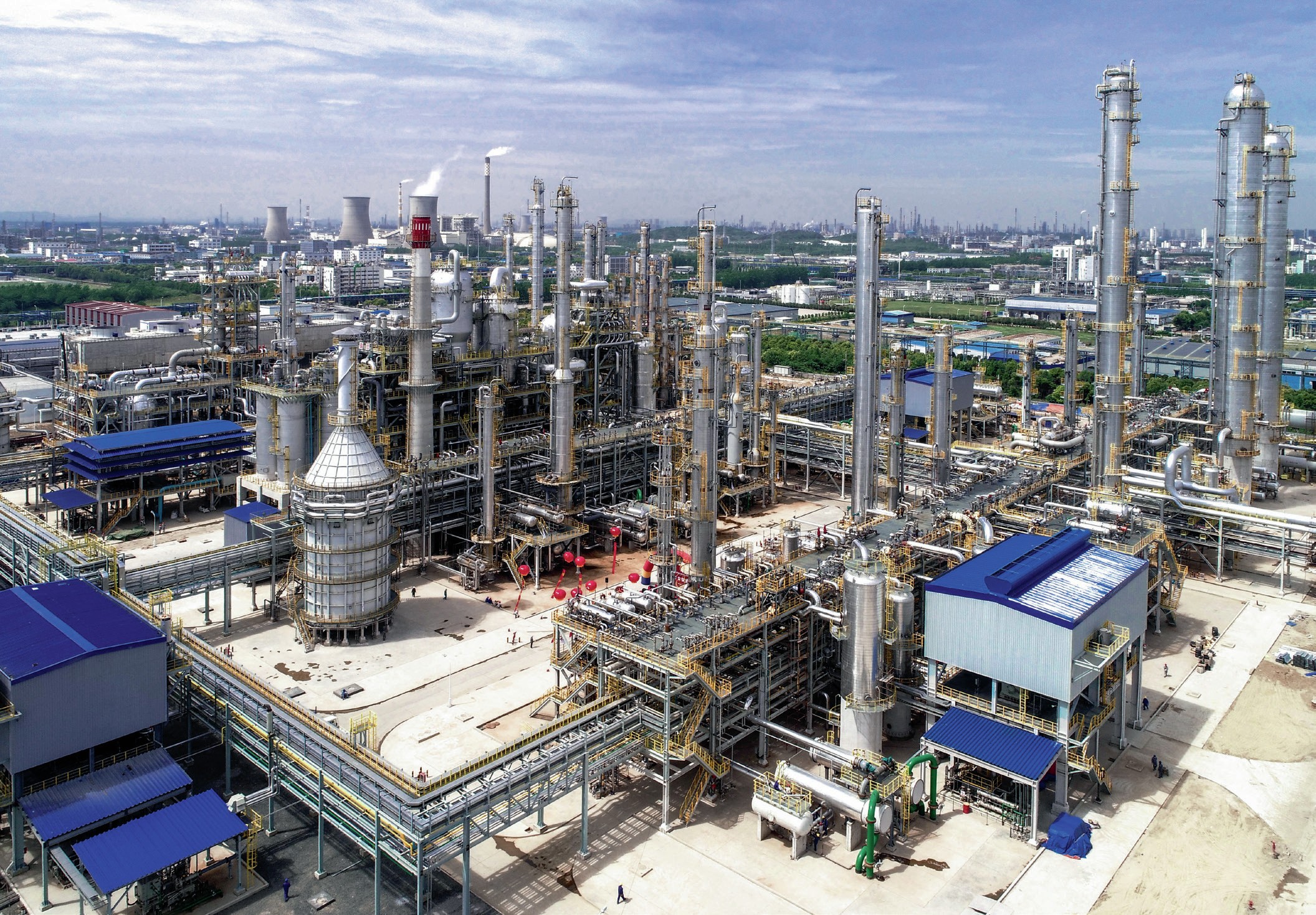
As a syngas derivative, demand for methanol continues to see a faster rate of growth than ammonia. Over the past decade, methanol consumption has increased by more than 70%, from about 49 million t/a in 2010 to an estimated 84 million t/a at the start of 2020, representing an average annual growth rate of 6-7%. This is more than triple of the equivalent figure for ammonia, which has run at about 2% per year. Although methanol’s rate of demand growth has slowed with China’s slowing economy – now to closer to 4% year on year, it is still projected to reach more than 96 million t/a by 2023, by which time it would be just under half the size of the ammonia market.
Methanol’s spectacular growth has been driven almost entirely by China’s rapid industrialisation, and specifically due to two major strategic decisions by the Chinese government – firstly to try and replace oil-derived gasoline and liquefied petroleum gas (LPG) with coal-derived methanol and its derivative dimethyl ether (DME) as blendstocks to try and rein in China’s increasing reliance on imported fuel. The second decisions has been to try and replace oil and gas-derived propylene and ethylene for plastics production with propylene and ethylene made from coal-based methanol instead; so-called methanol to olefins (MTO) production. MTO consumption has risen rapidly in China, from nothing in 2010 to millions of tonnes per year. So rapidly that, as Figure 1 shows, by 2023 it will have become the second largest end use for methanol globally, eclipsing more mature chemical uses such as acetic acid and methyl methacrylate (MMA).
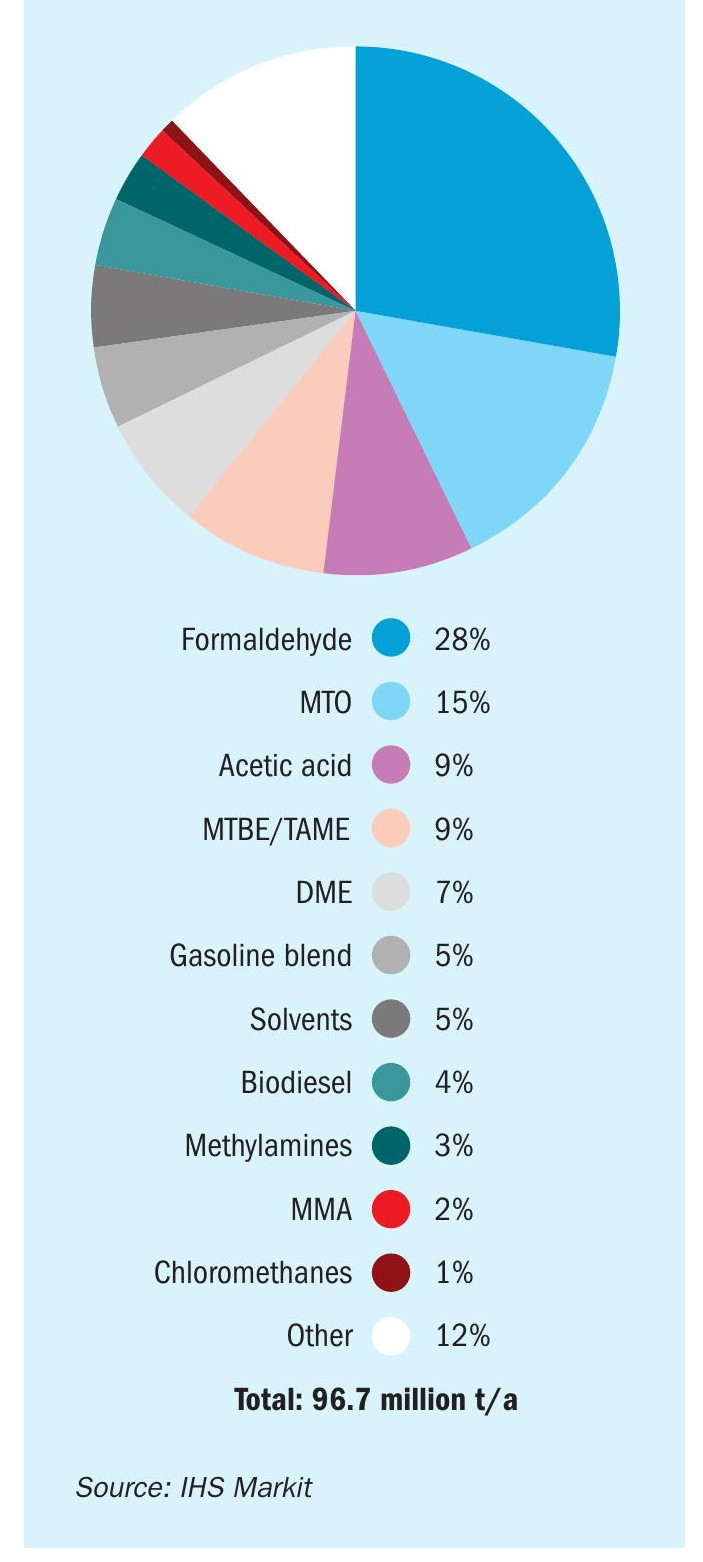
Methanol to olefins
The methanol to olefins process was developed by Mobil in the 1970s during their attempt to perfect the methanol to gasoline (MTG) process. Like MTG, MTO uses a zeolite catalyst in a fluidised bed to convert methanol into longer chain molecules, but stops the reaction sooner to produce predominantly a mix of ethylene and propylene. Zeolites are on a microscopic scale an aluminosilicate framework which can act as a ‘molecular sieve’, and this can control access to reactive sites. Mobil’s work did not go beyond the demonstrator stage, but in the 1980s UOP (formerly Universal Oil Products, now owned by Honeywell) replaced silicon with phosphorus at some of the active sites to produce the SAPO-34 zeolite catalyst, which became the genesis of a commercial MTO process. UOP installed the technology at a demonstrator site in Norway in 1995 using commercial methanol as feedstock and showed that it could produce a tuneable mix of ethylene and propylene, as well as some higher chain molecules. In conjunction with a downstream olefin cracking process (OCP) provided by Total, which broke down higher chain hydrocarbons, and a polymerisation process, such as had been developed by ExxonMobil, commercial polyethylene and polypropylene could be produced.
However, there was limited interest in the methanol industry at the time, mainly because the process was perceived as being too expensive to compete with olefins produced the traditional way, from steam crackers. This began to change during the 2000s, for two reasons. Firstly, methanol plants were getting bigger, with 5,000 t/d becoming a standard size. This made achieving economies of scale easier. Secondly, UOP continued its catalyst development, producing UZM-8, which made the process more economical. A 10 t/d unit started up at Total’s petrochemical complex in Feluy, Belgium in 2008the first commercial UOP MTO plant. By now other companies were developing processes. Lurgi (now Air Liquide), already a major methanol technology licensor, introduced its methanol to propylene (MTP) process in 2002, and a unit was built in Iran in the mid-2000s. In China, the Dalian Institute of Chemical Physics had used a modified SAPO-34 catalyst to develop its own process in the 1990s, which was scaled up to a 16,000 t/a unit (in terms of methanol feed) at Sinopec Luoyang in 2006. Sinopec subsequently developed this into its own MTO process, and another came from China’s Tsinghua University.
It was China which proved to be the game-changer, with methanol derived from coal rather than natural gas as the feedstock. The first commercial-scale plant became operational in 2010 at Baotou in Inner Mongolia. Since then, from 20102019, 25 plants have been built, with a total capacity of 15 million t/a of olefins production (equivalent to 26 million t/a of methanol demand). About 60% of this (9 million t/a olefins, 16 million t/a methanol equivalent) was in integrated facilities where the full production cycle of coal gasification, methanol production and olefins manufacture were present, mainly in the northeast of the country; the majority of coal production lies in the northern provinces of Inner Mongolia, Shanxi and Shaanxi, responsible for over 60% of domestic supply. However, the remainder depend on ‘merchant methanol’, and are often in coastal locations, buying methanol either from other producers within China, or on the international market, and these plants are responsible for China’s rising tide of imports of methanol from overseas.
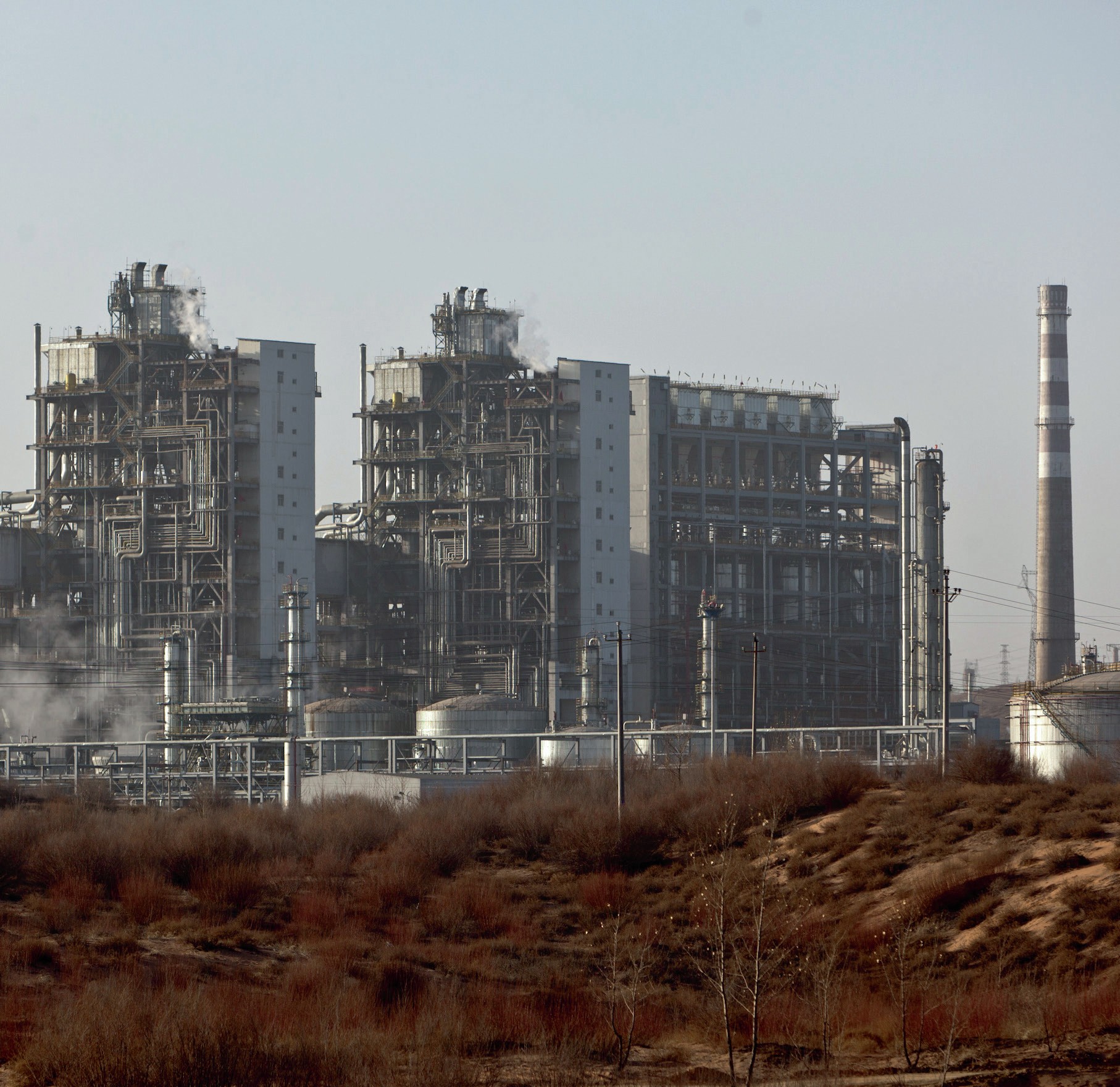
Changing environment
However, China’s methanol and MTO capacity building is slowing down, for a number of reasons. The first and perhaps most important has been economic. When oil prices were high and coal prices were low, coal-based MTO capacity enjoyed a considerable margin over rival naphtha crackers. In the early 2010s, Brent crude prices were trading between $100-120/ bbl. But from mid-2014, oil prices started to slide, as the Chinese economy started to slow, and increased production started coming on-stream from US tight/shale oil producers. At the same time, methanol prices were high, as demand from the slew of new Chinese MTO plants occasionally outpaced supply. From 2016, Chinese coal prices also started to rise, driving methanol prices back up at a time when oil prices remained more subdued, and leading to shutdowns in some Chinese MTO capacity.
The second reason has been environmental. There has been a concerted government crackdown on pollution, especially of coal-burning factories close to built-up areas. There is also an attempt to tackle the country’s greenhouse gas emissions by encouraging moving to natural gas for power and chemicals production. During the current Five Year Plan, China is targeting a reduction in coal’s share of energy from 68% in 2015 to 58% in 2020.
Ethylene and propylene
The ethylene and propylene markets are also changing. On the propylene side, a switch to lighter crude slates and more ethane use at steam crackers, especially in the US, due to shale oil and gas production, has reduced propylene production from these plants. That has led to the development of more “on-purpose” propylene production facilities. There were some ideas that this could drive demand for more MTO production, especially focused upon propylene production. However, in the US on-purpose propylene production has mainly been filled by propane dehydrogenation (PDH) plants instead. MTO has captured only 6% of the propylene market in 2018, at 7.1 million t/a.
On the ethylene side, in 2019, total ethylene capacity from MTO units reached 5.21 million t/a, accounting for 21% of China’s total ethylene capacity. However, China has decided to build a massive swathe of new ethylene steam crackers to take advantage of cheaper oil and gas prices. Between 2020 and 2025, 15 new steam crackers with a combined capacity of 17 million t/a are due to come on-stream in China.
China is still building MTO plants. Ningxia Baofeng started up a 600,000 t/a MTO plant in September 2019, with a 1.8 million t/a captive methanol unit due to begin production in April 2020, and Nanjing Chengzhi Yongqing Energy’s 600,000 t/a MTO plant, which depends on buying methanol from the merchant market, came on-stream in June 2019. Connell Chemical commissioned a new 300,000 t/a MTO plant in April 2020, using UOP’s technology. Around 20% of China’s new ethylene capacity out to 2025, or around 2.4 million t/a (4 million t/a in terms of methanol demand), is expected to come from MTO production. Some of the steam crackers were due to run on ethane imported from the US, and the rocky US-Chinese trade relationship over the past few years have very much complicated investment decisions there. However, there is no doubt that the difficult economics of the recent past due to high coal and low oil prices has very much slowed Chinese MTO investment for now.
United States
At the same time that China has been rapidly increasing methanol demand, the US has been rapidly increasing methanol production. Cheap shale gas has transformed the US chemical industry, and led to the reopening of shuttered capacity and the building of new plants, including Methanex’s relocation of 2 million t/a of capacity from Chile to Louisiana. The rapid rise of US methanol capacity has led a number of companies to look at building export-oriented plants aimed squarely at supplying Chinese MTO production, and a number of Chinese companies have become involved in trying to develop methanol projects in the US. IGP Methanol is looking at building a 1.8 million t/a methanol complex in at Myrtle Grove, Louisiana, in partnership with China Cosco Shipping Energy Transportation Co., Ltd, and Jinguotou (Dalian) Development Co., Ltd (JGT). Yuhuang Chemical Industries is in a joint venture Koch Industries to build the 1.7 million t/a methanol Methanol One plant in St. James Parish Louisiana, due for completion this year. However, ambitious plans by the Chinese-backed Northwest Innovation Works (NWIW) to build three 1.7 million t/a methanol plants in Washington and Oregon states have run into difficulties with environmental opposition and permitting.
Other projects
Outside of China, methanol to olefin projects are thin on the ground. India has looked at the possibility of duplicating China’s success at monetising coal reserves to generate domestic chemical production, but beyond a coal-based urea plant being developed at Talcher most of this remains purely theoretical. Iran had planned to build a gas-based methanol to olefins unit at Chabahar as part of the Mokran petrochemical hub development, but the re-imposition of US sanctions has complicated financing and licensing, and there is little progress at present.
However, there are still two active gas-based MTO projects under development. In May 2019, Uzbekistan’s Ministry of Energy signed a project development agreement with a group of investors including Uzkimyosanoat, Air Products & Chemicals, Uzbekneftegaz and Enter Engineering to build a 500,000 t/a MTO plant in the country. Honeywell UOP and Haldor Topsoe are also said to be involved. Landlocked Uzbekistan is keen to develop its domestic gas reserves into downstream production, and is involved in a gas to liquids development at Oltin Yol due to be completed by the end of 2020.
Meanwhile, in Oman, China’s Mingyuan Holdings Group Company announced in 2017 plans to set up the 750,000 t/a SEZAD methanol-to-olefins (MTO) plant alongside a 1.8 million t/a greenfield methanol scheme at the China-Oman Industrial Park at Duqm in southern Oman, at a cost of around $2.8 billion. The project has spent some time in discussions over gas pricing and availability, but is said to be moving to tender at the present time.
A dose of reality?
China’s MTO boom has changed the face of the methanol market. However, all things come to an end. China’s coal-based chemicals sector is coming under increasing environmental pressure from the government to deal with emissions. It is also a major consumer of water; a significant problem given that these plants are often located in China’s dry northwestern regions, close to coal mines. In 2015 the Ministry of Environmental Protection imposed a rule limiting water usage, and some plants in dry provinces have implemented an innovative water rights trade system with farmers. Coal-based plants also generate large volumes of waste water that are difficult to cleanse and safely release.
Higher coal prices and lower oil prices – especially in the wake of the current Covid19 crisis and consequent supply glut – have also incentivised the development of steam cracker capacity that is able to operate more cheaply than MTO plants in the current price environment and which is discouraging new coal-based MTO capacity in China. Previously, integrated coal-based complexes were believed to offer the best margins for MTO conversion, as they were able to decide for themselves what they ‘charged’ as a nominal price for their feedstock, but in a low methanol price environment, merchant plants might seem to have more of an edge. They too have issues to consider however; while there is new methanol capacity being built around the world, it is mainly in the US and Iran, both of which pose potential political risks in terms of supply.
Oman and Uzbekistan still hold out some hope for non-Chinese MTO capacity, but it seems that, for now at least, the MTO boom may have been and gone.