Nitrogen+Syngas 365 May-Jun 2020
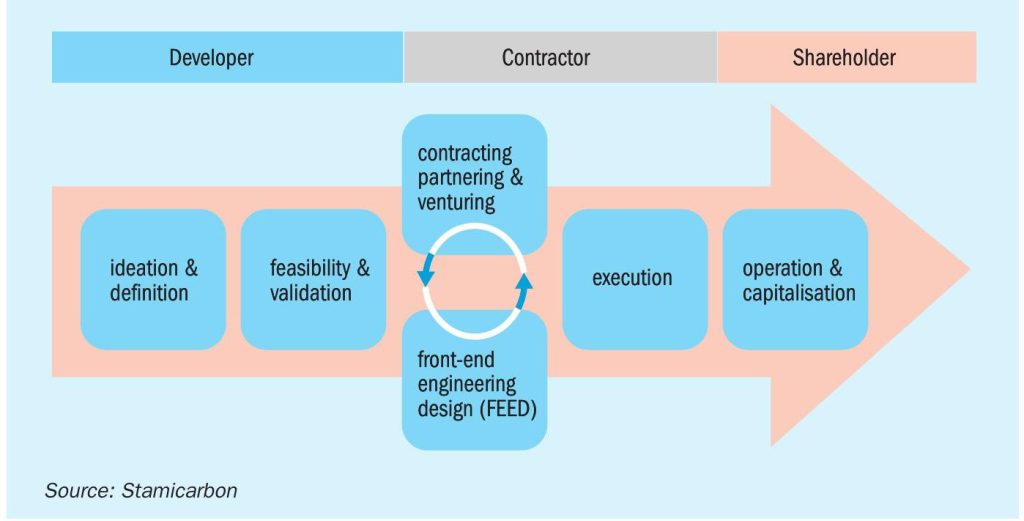
31 May 2020
Sustainable production of nitrates from renewable energy
NITRATE FERTILIZER PRODUCTION
Sustainable production of nitrates from renewable energy
Paving the way for commercially attractive, sustainable, decarbonised fertilizer production, J. Dobrée of Stamicarbon BV discusses the latest developments for nitrate fertilizer production based on renewable feedstocks sourced from solar and wind energy. Stamicarbon has upgraded plant designs used in the past to create a new type of small-scale fertilizer plant capable of producing a product mix that can be adjusted to meet specific local requirements with maximised output value, thereby maintaining a competitive position towards imported products and large-scale producers.
The chemical industry is showing an increased interest in using renewable or carbon recycled chemicals to reduce its environmental and carbon footprint.
The availability of renewable energy sources creates new opportunities for the use and geographical location of nitrate fertilizer production, while providing a clear path for sustainable and decarbonised fertilizer production.
Power-to-fertilizers
The energy section is facing a huge transition from fossil fuels to renewable feedstock sources, such as wind and solar energy. The increasing capacity of renewables has created economy of scale, which today results in competitive electricity pricing that can match and, in some regions, even beat electricity produced from fossil fuels.
However, the large quantities of renewable energy create pressure on the grid, especially in Europe, and create an issue in relation to the stability of supply. In addition, interesting solar and/or wind locations lack grid connection or a market and are therefore not utilised.
The interest in renewable, carbon free or carbon recycled fertilizers is increasing slowly, considering the substantial environmental footprint of the agriculture, while industrial partners face the pressure of stake and shareholder to improve the sustainability of their operations.
“…providing a clear path for sustainable and decarbonised fertilizer production.”
Another driver for reducing the environmental footprint of fertilizer production lies in the governmental pressure that can be seen in various regions on fertilizer producers to push for sustainable solutions, facing location regulation and possibly carbon taxation.
This article introduces Stamicarbon’s approach for the sustainable production of nitrates from renewable energy sources. It covers the background of current developments in the field and shows the commercial viability of carbon free nitrate production today. The article follows the strategic direction of Stamicarbon set out during its Future Day in April 2019, which announced Stamicarbon’s engagement to develop projects covering the production of ammonium nitrate or urea-based fertilizers from renewable energy sources.
Project approach
For projects in the field of renewable energy and carbon free or carbon recycled feedstock, a dedicated approach is considered via project development. The approach needs to ensure that the hurdle of new technologies can be overcome and that the commercial benefits can be realised. Stamicarbon, as part of the Maire Tecnimont Group, can rely for such involvement on its Project Development and Venturing Group, which coordinates the whole process as well as the various financial, institutional and technical actors involved, while leveraging advanced technical and financial skills to promote sustainable fertilizer projects. The set-up is shown in Fig. 1.
Full process co-ordination is required with a dedicated consortium, as the development of projects driven by renewable feedstock utilise state-of-the-art technology in all of its building blocks.
Having the right consortium in place is considered critical to secure a successful result, as the targeted projects consider technical challenges that are partially under development and require customisation dedicated for the purpose and anticipated site location.
Conceptual plant configuration
In order to serve an increasing market demand for small-scale facilities, Stamicarbon has developed a niche technology referred to as LAUNCH MELT™ Small Scale Design for urea and the LAUNCH Nitric Acid Mono Pressure Design for nitrate production.
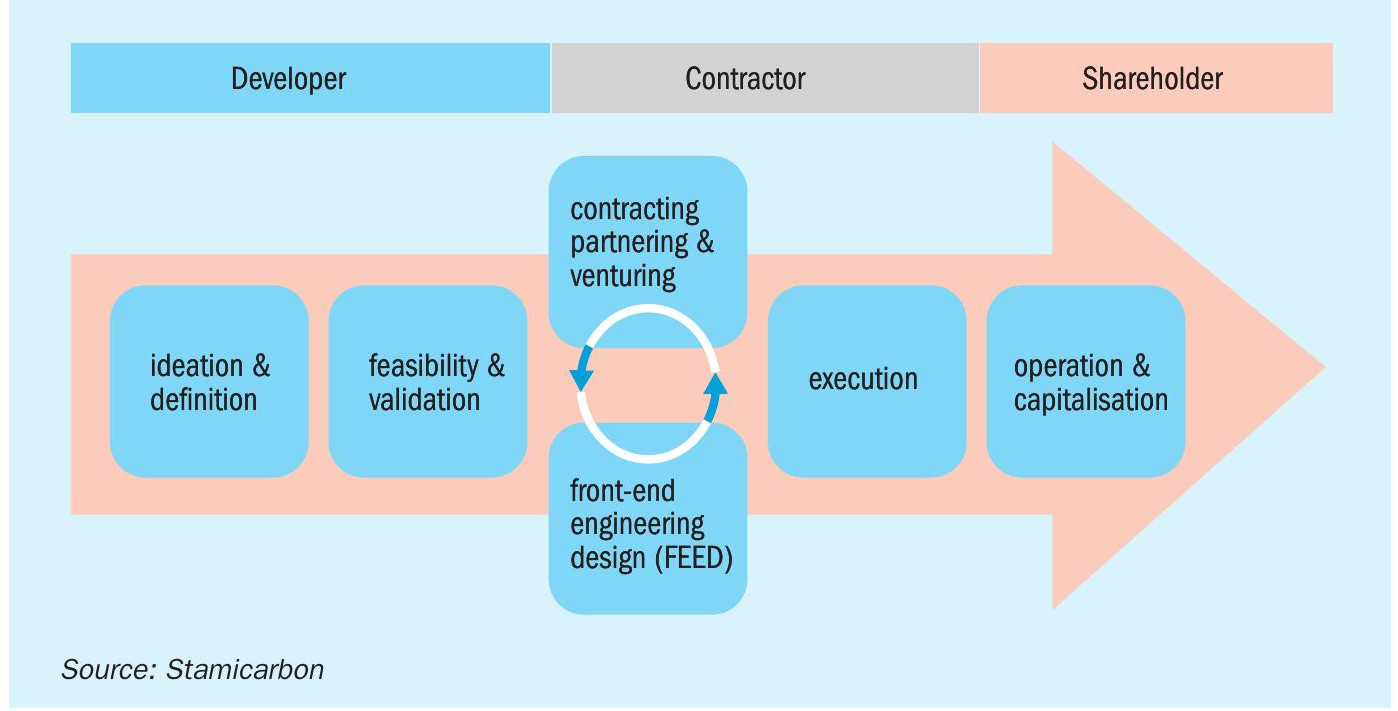
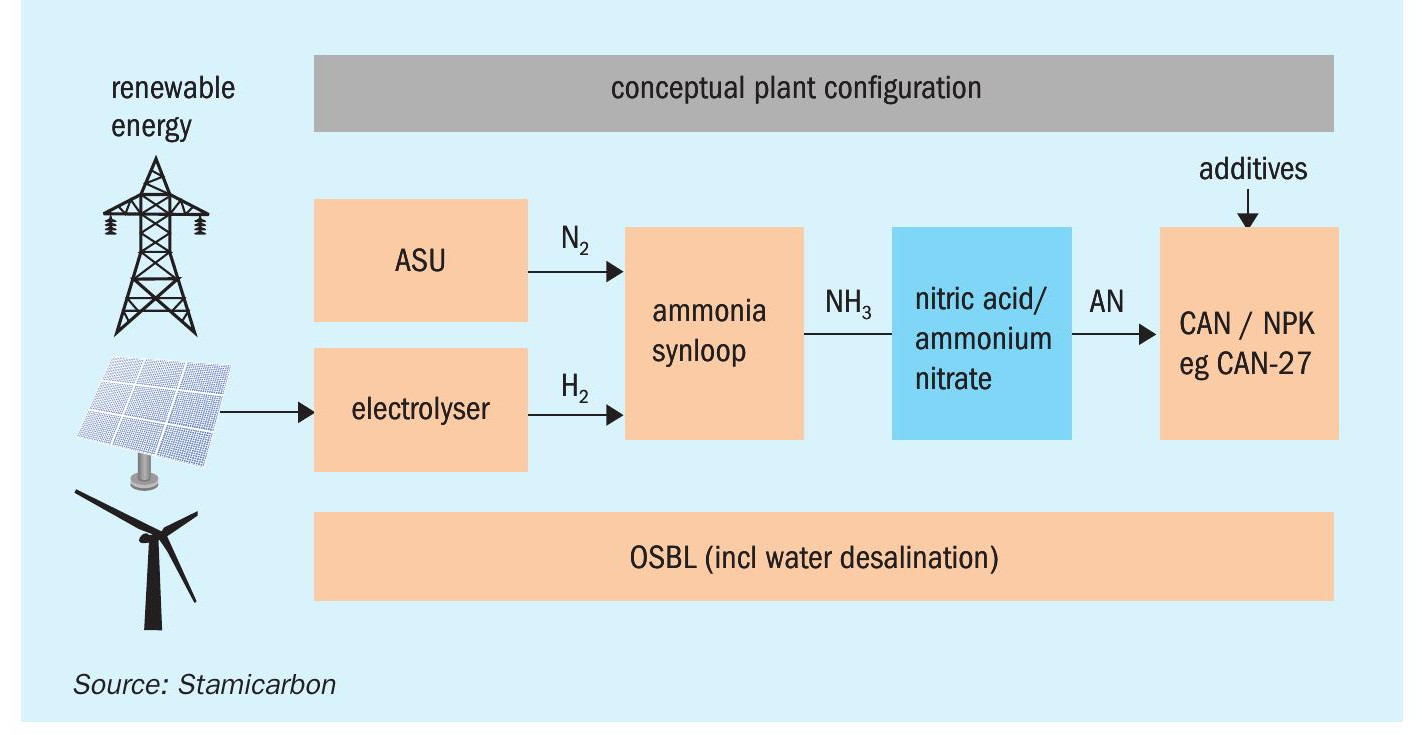
Stamicarbon’s design for sustainable nitrate production (Fig. 2) is focused on the merger of various available technologies. The core technology is Stamicarbon’s mono pressure nitric acid technology, which results in ammonium nitrate production for a capacity of 100 or 200 kt per year CAN. The final product can be various nitrate types, but for the conceptual design calcium ammonium nitrate (CAN) with 27% Nitrogen (CAN-27) is used as the reference point.
The design follows the same principle of the small-scale fertilizer production available for urea technology and is focused on supplying local nitrogen demand, extended with the production of specialty fertilizers for specific local soil and crop requirements. For example, Stamicarbon’s state-of-theart LAUNCH MELT™ Small Scale Design is capable of producing AdBlue® /DEF, urea for melamine, enriched urea, UAS, UAN, as well as direct application coated urea with e.g. controlled release coating.
Stamicarbon nitric acid technology
The unit design for nitric acid production originates from Stamicarbon’s heritage and has been upgraded to state-of-the-art technology, which allows nitric acid production of up to 1,600 t/d and more. Stamicarbon mono pressure technology is derived for the application of small-scale fertilizer plants capable to produce a product mix that can be adjusted to meet specific local nitrogen requirements and demand. It can also be considered for the production of explosives if necessary. The origin of the Stamicarbon mono pressure technology dates back decades, to a time when it was being used in Egypt, based on hydro power.
The core of the value proposition brought by the mono pressure technology overcomes logistic deficiencies, while minimising capex. In order to provide a competitive solution for producers that have interest to produce locally on a small-scale or to tap into a niche product market, key elements have been considered to provide a successful technological solution:
- minimise capex with minimum equipment to optimise the financial model;
- highest energy efficiency;
- robust and reliable plant design with possibility for remote support, as relative limited plant staff and operational competences will be available at site;
- modularised construction approach possible by using prefab skids to reduce local construction;
- compliant to most stringent environmental standards for NOx and N2 O;
- highest quality and safety as per Stamicarbon standards;
- flexibility to process renewable or bio-based feedstock, which may be variable in supply and/or entail logistic deficiencies;
- based on a long track record of historical references.
The mono pressure technology is standardised for small-scale plant sizes with a minimum capacity of around 100 t/d, following a reputable track record with over 40 references worldwide.
The main technological feature of the mono pressure technology, besides the compact and low capex design lies in the use of an innovative ammonia burner design and smart heat exchanger network. This results in core advantages:
- highest energy efficiency/team export;
- lowest NOx and N2 O emissions;
- corrosion prevention by design without the need for exotic construction materials;
- plant design suitable for digital automation.
As is the case for all Stamicarbon plants, the nitric acid plant has a characteristic compact design. The lay-out is focused on reduced capex by utilising modularisation and the optimum design has been engineered without compromising Stamicarbon’s performance, reliability and safety requirements.
For nitrate finishing, Stamicarbon has a partnership with INCRO, which provides a wide array of nitrate finishing technology for CAN and NPK production. For UAN production, Stamicarbon relies on its own reliable UAN technology, which has stood the test of time in various plants across the world over the last decades.
New geographical reality
The fertilizer technology portfolio of Stamicarbon has the capability to facilitate renewable or carbon recycled feedstock, depending on the desired fertilizer. Examples considered are the use of feedstock originating from refuse derived fuel (RDF) gasification units, which produces syngas based on municipal waste or feedstock derived from furnace off-gas from the steel industry. Another example could be the combination of green ammonia production from renewable electricity derived from wind, solar, thermal or hydro, while using the carbon dioxide from carbon capture units from conventional power plants or industry. In the case of nitrate production, the focus is primarily on the use of carbon free feedstock sources, such as wind, solar, thermal and/or hydro.
In light of current developments related to the reduction of carbon footprint and the ambition to produce chemicals in a more sustainable way, the interest of project developers is slowly shifting from power production to the production of chemical and fertilizers instead. By doing so, nitrate production from renewable energy can be considered as a green CAN-27 in this case.
The change of approach, the use of renewable sources as feedstock for fertilizer production, creates a new geographical reality for the nitrate market. Renewable sources are mainly available in areas with high load factors, which can be suitable for chemical or fertilizer production. However, areas with high load factors are not by definition typical for present day production locations of nitrate fertilizer from fossil fuel.
This creates new opportunities for the industry to service markets that were difficult to access in the past by local supply. On the other hand, fertilizers are easily transported over the globe, which makes the location of production less relevant to the end market, whereas in the past, location of production always tended to be dictated by the availability of attractive fossil fuel-based feedstock. This paradigm might shift in the future, considering the high load areas for renewable energy, indicated in Fig. 3, which provides a new view on the ideal production locations, especially in the light of reducing costs as a result of economy of scale of renewable wind and solar energy, which in some areas has outperformed fossil alternatives. In addition, any possible carbon taxation can act as game changer.
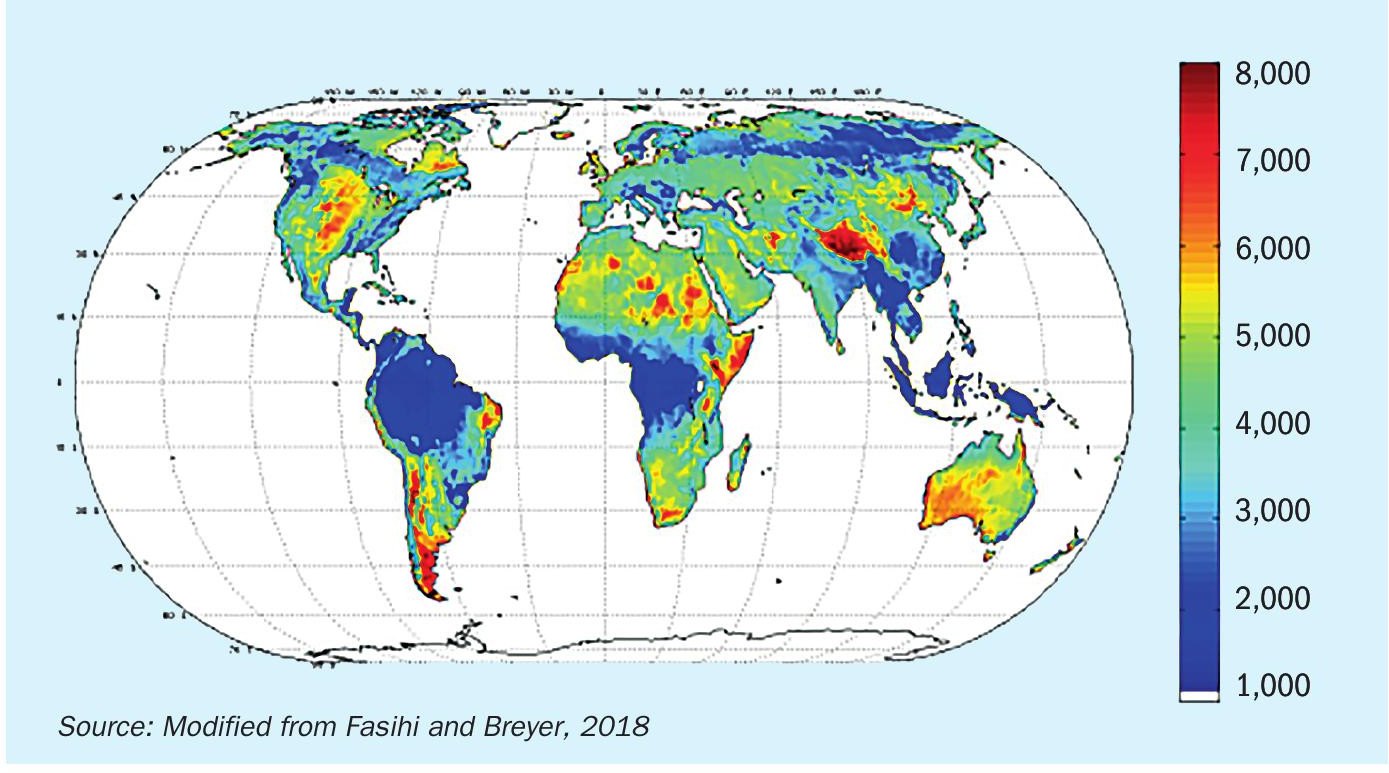
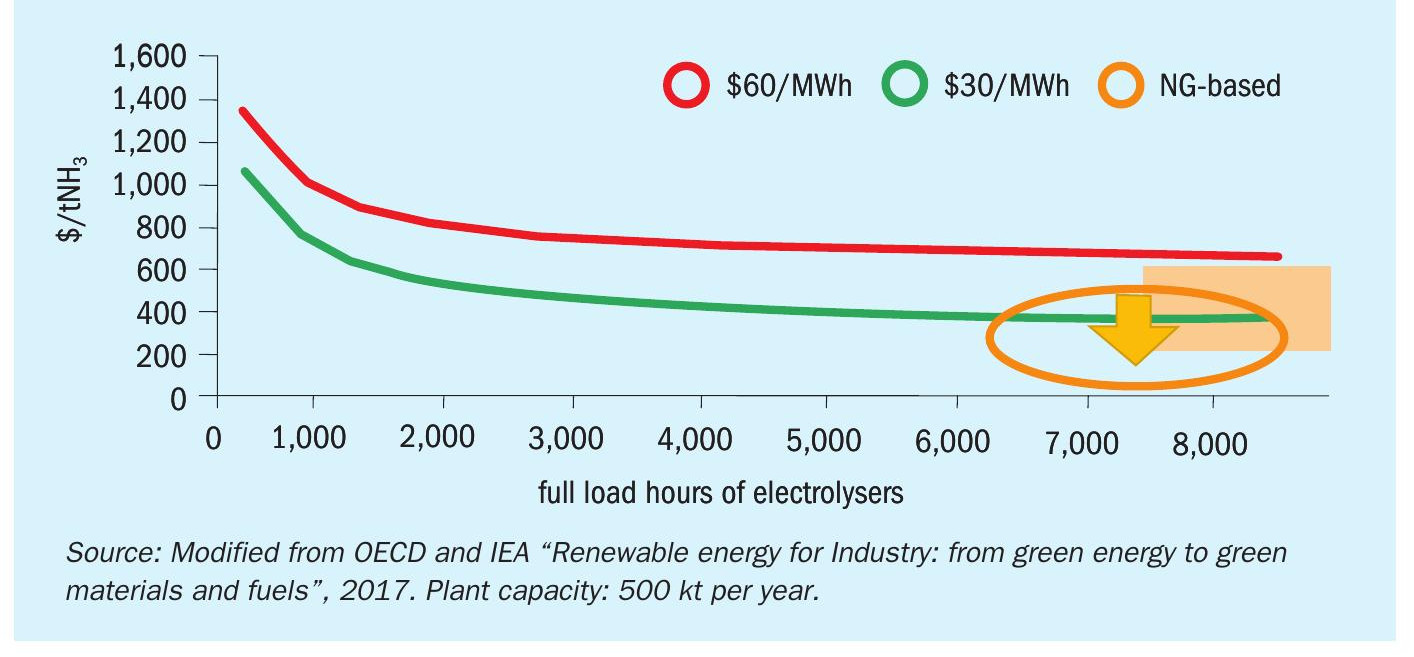
The consideration of renewable production of nitrate fertilizers will follow a new approach driven by various (new) types of reasoning:
- competitiveness and availability of feedstock with distinction between renewables or fossil fuel;
- needs of local production, special types of fertilizer (blends) for special applications or explosives;
- carbon taxation, which can be applied upstream or downstream;
- incentives for sustainable fertilizers, e.g. by taxation or the application of premiums;
- governmental pressure to greening the brown;
- corporate vision and/or shareholder pressure;
- economic feasibility.
Despite slow moving regulations in the direction of carbon taxation, the economic feasibility is always the main driver. However, the modern-day view of investors, such as, for example, pension funds, are more and more focused on sustainable investments. This pressure on shareholders is becoming more relevant, making companies look at how they will operate in the future, which is a great driver for the development of sustainable fertilizer production. The critical question remains: Is nitrate fertilizer production based on renewable energy commercial attractive?
Economic feasibility
When developing a renewable project, the project size is typically small-scale. For these types of projects full understanding of the economics is critical, since small sized plants are only attractive in specific market conditions. Clear focus on the high value product mix, the ideal location and the right technology selection are key success factors.
One of the drivers of the cost price is the feedstock source, which is indicated by the cost of electricity. The International Energy Agency (IEA) studied the potential production cost of renewable ammonia for a plant with a theoretical production capacity of 500 kt per year, which is illustrated in Fig. 4. At an electricity cost of $30/MWh, the cost of production should be feasible below $400 per tonne at high load hours compared to natural gas feedstock.
However, the interesting development since the publication of the graph in 2017 is that in some tenders the cost of renewable energy has already achieved electricity prices below $20/MWh for solar and wind, e.g. in areas of Brazil, Mexico and Saudi Arabia.
Considering the improved economy of scale towards reduced cost of electricity below $20/MWh and high load areas, able to support electrolyser production above 6,500 hours per year, it can be concluded that in specific locations renewables are already proven as a competitive alternative to natural gas, as indicated in Fig. 4 with the orange circle and indicative orange arrow.
Specific business case for inland Africa
The economic feasibility can be illustrated with a feasible business case for inland Africa. Today all fertilizers used in inland Africa are imported from overseas. This results in two complicating factors, as a result of the long supply chain: l affordability of fertilizers; l availability of fertilizers on time.
In the current day situation the import of a tonne of CAN results in an estimated inland pricing in the range of $450-$500 per tonne minimum, while more than 20% of the cost originates from the logistics specifically for the domestic location inland Africa. The case is illustrated in Fig. 5. The cost can also increase in case of scarcity during peak season or supply chain issues, as was the case, for example, during the cyclone Idai in March 2019, which is unfortunately not an exception. The cyclone hit the port of Beira in Mozambique and thus the main gateway for fertilizers towards inland Africa.
In this case supply to a domestic location in inland Africa is subject to availability, due to the dependency on imports and high pricing as a result of the logistics and the inefficiency thereof. The alternative to produce fertilizers from natural gas is not an option, as the availability of natural gas in these areas is typically restricted or not available.
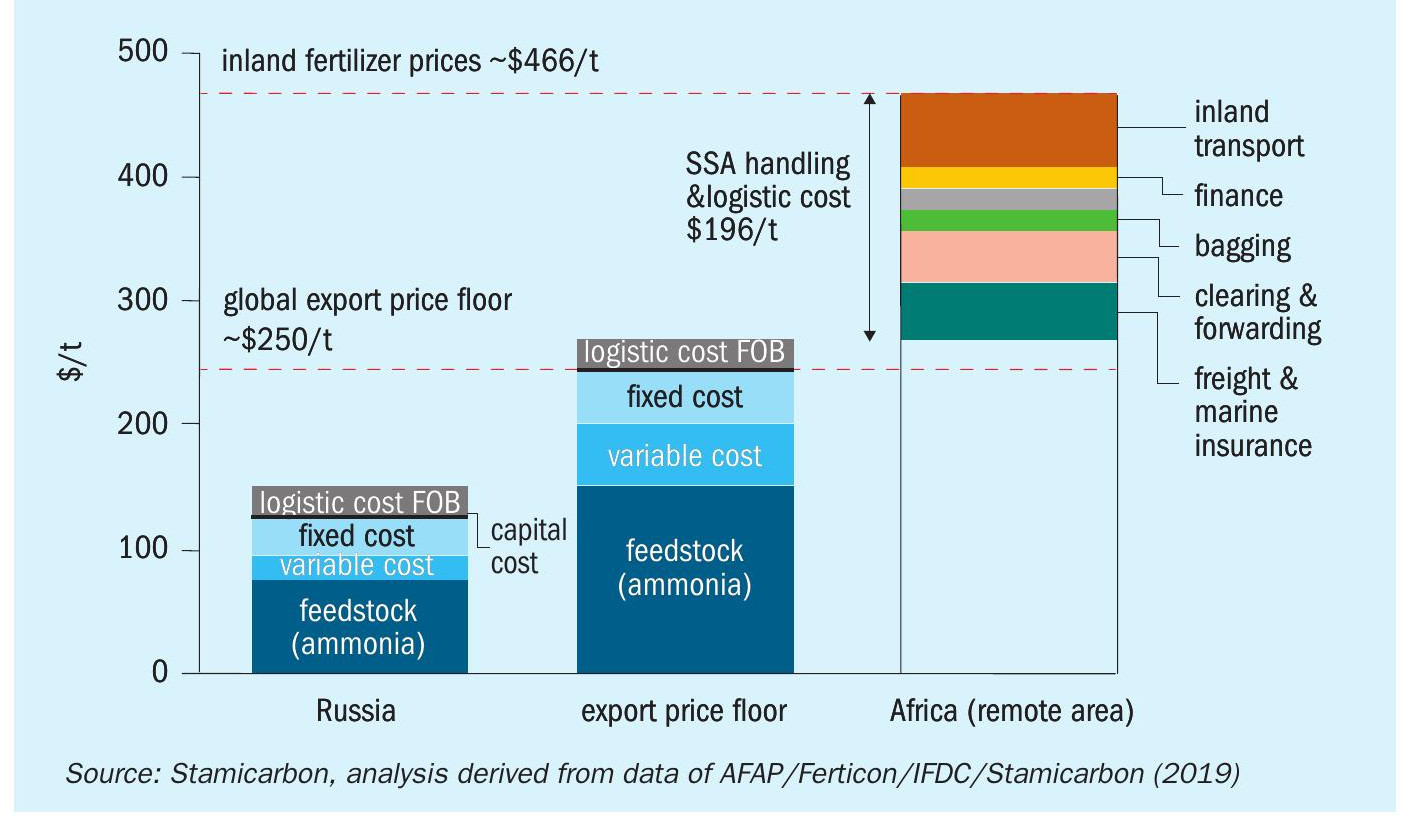
However, renewable energy sources are available, which can be found in solar, wind, hydro and geothermal sources. This can therefore create the basis to justify local small-scale fertilizer production with the focus on high value fertilizers, dedicated to the local market. Market availability is not an issue as current imports are sufficient to sustain a small- to medium-sized plant, and application rates are currently very low. The latter might be solved by improving the availability and affordability of fertilizers, which could boost local fertilizer consumption and improve the application rate. This effect was observed after the recent commissioning of a urea plant in Nigeria.
The key question for the economics remains the competitiveness of the small-scale plant. Being aware of the relevant variables and parameters for the financial model, key characteristics of a typical 100 kt per year CAN plant have been optimised for this specific purpose. The measures taken allow for a very interesting business case. For the financial modelling the entire complex of the process plant is taken into consideration, which has resulted in an IRR of 10-15% for this specific example for the combined facility including full EPC.
These validated figures indicate that a sustainable future based on a renewable nitrate grade fertilizer can be realised with surprisingly good economics for carbon free fertilizer, and it is feasible today.
Especially in the light of anticipated economy of scale for power generation, electrolysers and the scale of production, we are at the beginning of a new way to produce nitrates. The main issue today seems to be the availability of renewable energy.
Conclusion
Nitrate production from a renewable source can technically be achieved and is already competitive with nitrate production from natural gas in specific regions today. At the moment the logistics, inefficiencies and investment costs are the major differentiators compensating the economy of scale effect to justify the small-scale plant.
Improving the economy of scale within power generation based on wind and solar and the electrolysers will further improve the proposition and will allow larger scale production utilising economy of scale in production as well. Stamicarbon’s nitric acid technology allows for competitive small-scale nitrate plants in geographical locations where they overcome logistic deficiencies or access niche market.
In the light of the full plant design based on a renewable source, hydride solutions can also be considered as an intermediate step to replace brown hydrogen with a green version to improve the environmental footprint or to facilitate capacity debottlenecking. This is especially relevant during the transition phase as the availability of renewable energy will prove to be the main issue now.
Renewable nitrates will eventually make the fertilizer industry sustainable and positions nitrates as a potential substitute for other fossil fuel-based fertilizers in the future. The technology is already available and can be implemented with an acceptable business case today. The path towards sustainable fertilizer will be long and challenging, but it is the future and the future is now.