Fertilizer International 497 Jul-Aug 2020
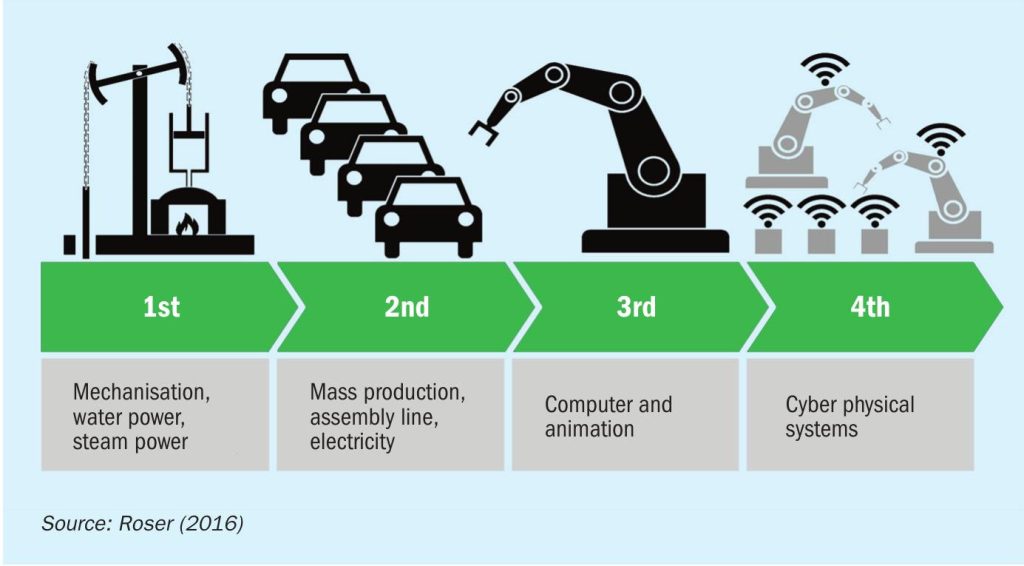
31 July 2020
Digitalisation: supporting customers remotely
DIGITAL TECHNOLOGY
Digitalisation: supporting customers remotely
As the industrial value chain for fertilizers and their raw materials manages its way through the unprecedented global Covid-19 pandemic, Metso Outotec’s Hannes Storch, Collin Bartlett & Marcus Runkel reflect on the range of digital tools installed by the company at its industrial reference plants globally.
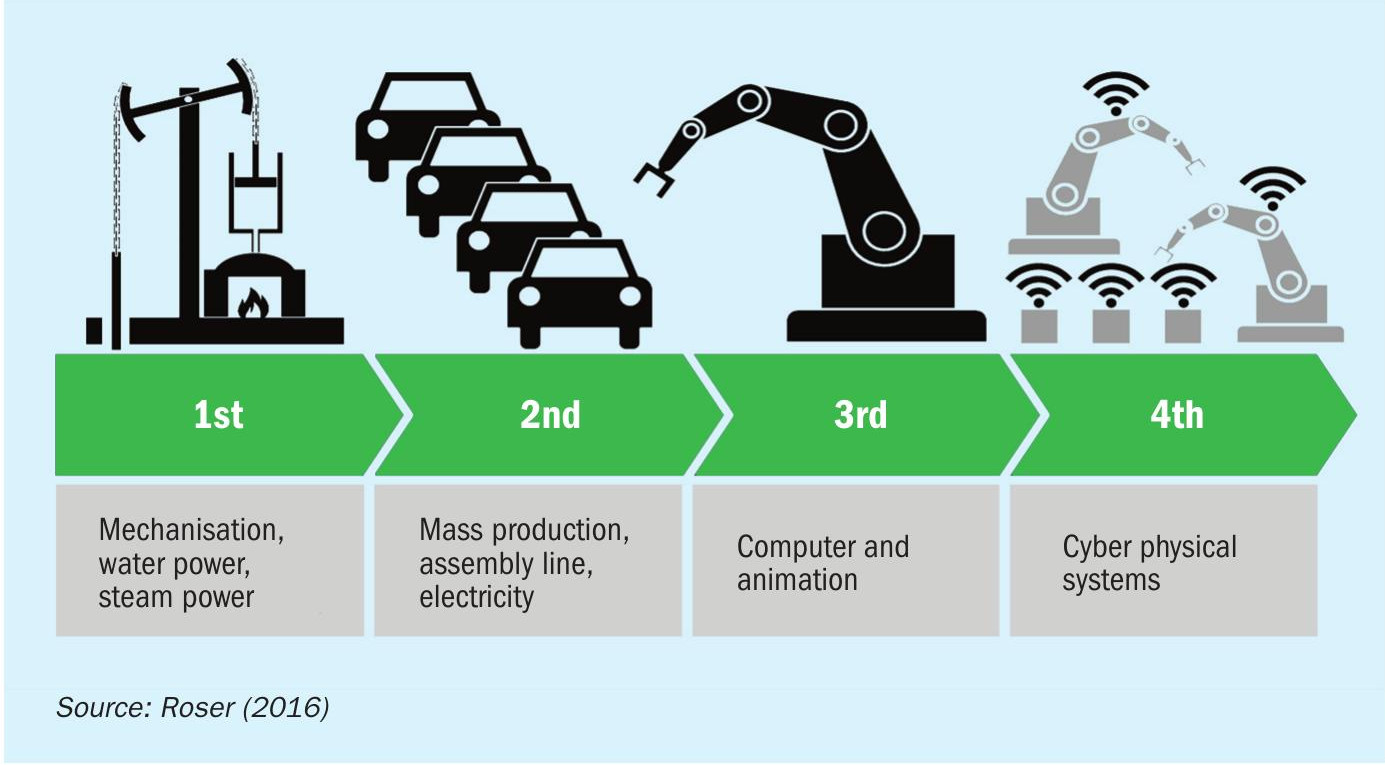
As we exit from this challenging period, all of us in business need to consider how current ways of collaborating – between ourselves and with our customers – may well need to change, if we are to be better prepared for the future.
In this article, we look at the powerful potential of digital tools for improving plant operations and the interaction between operators, engineers and technology providers. Effective communication between all those involved in plant operations is undoubtedly a key factor for success. While on-site control rooms and field operators are essential, support from the home office can be of great benefit to all too.
Digitalisation – an overview
Digitalisation – also known as ‘Industry 4.0’– is the term describing the current trend for automation and data exchange in manufacturing technologies. It includes cyber-physical systems, the internet of things (IoT), cloud computing and cognitive computing1 (Figure 1).
Industry 4.0 has its roots in the high-tech strategy devised by the German government to promote the computerisation of manufacturing. This strategy introduced a manufacturing concept in which machines are augmented with sensors wirelessly connected to a system that can visualise the entire production line and make decisions on its own.
The specific technologies associated with Industry 4.0 include:
- Cyber-physical systems (CPS)
- The internet of things (IoT)
- The industrial internet of things (IIoT)
- Cloud computing
- Cognitive computing (machine learning)
- Artificial intelligence (AI).
Industry 4.0 is also synonymous with the concept of ‘smart factories’. These create a virtual copy of the physical world and make decentralised decisions. Cyber-physical systems – via the internet of things – then communicate and cooperate with each other and with humans in real-time. This happens internally within a company, and externally through organisational services offered and used by other value chain participants2 .
Digitalisation is currently seen as the driver for realising productivity improvements – and as the first step along a long route to the ‘smart factory’ of the future. That said, digitalisation also has the potential to severely disrupt traditional business models.
Digitalisation from an EPC contractor viewpoint
Encouragingly, digitalisation has the potential to improve productivity in the engineering, procurement & construction (EPC) industry, as OECD benchmarks show. This is an acknowledgement that current approaches to complex project implementation carry the risk of delays and cost overruns3 .
By closer collaboration and integration with technology providers, operators in commodity mining and processing have a great opportunity to improve their key performance indicators (KPIs) throughout the project lifecycle. But, to fully benefit from digitalisation and its potential rewards, there is a need to optimise the digital tools that are already currently available. This, in turn, requires a re-evaluation of the ‘status-quo’ and the conventional methodologies currently employed by the industry.
Domestic EPC contractors in Germany were recently polled on which digitalisation options they considered key to their projects (see Figure 2), as part of recent studies sponsored by the German Mechanical Engineering Industry Association (VDMA).
Clearly, the digitalisation options considered most important by engineering contractor are highly dependent on: the project under consideration; the industry the project will serve; and the project’s ultimate complexity. For each individual project, the EPC contractor has to consider customer needs, budget constraints and project infrastructure, when assessing the digitalisation demands of a given project.
PORS – a simulation-based safety & operational support system
Metso Outotec’s PORS (Plant Operability Reliability and Safety) system was developed to guide and support operating personnel at sulphuric acid plants. The system enables safer and more efficient monitoring and control of the sulphuric acid process by enhancing awareness of potential operational problems and challenges.
PORS started as a safety related system associated with heat recovery. But it is now being extended to provide simulation-based support for full plant operations – encompassing the gas cleaning and acid plant as well as upstream metallurgical process steps such as the roasting plant.
A virtual simulator within the PORS system calculates ideal operating conditions. Gap analysis, by comparing ideal with real-time plant conditions, is then used to shift the plant closer to its optimal operational state (Figure 3). Metso Outotec, as a process plant supplier, has all the relevant equipment and process simulation models to undertake this exercise. The company also has the necessary experience and understanding of material characteristics, long-term process behaviour, and the conversion rates of catalytic reactions (SO2 to SO3 etc.).
Readings from a distributed control system (DCS) show the current real-time situation at the process plant. By comparing actual readings to the results of the full simulation model – for a process plant or plant site – gap analysis reveals where the process or operating conditions are not as expected. The findings can then be used in several different ways.
If an operational issue is detected, for example, operators can be provided with precise information on which setpoint needs to be changed to bring the plant closer to the theoretical optimum. (There is also the option to set these setpoints automatically.) This closes the gap between the theoretical optimum and observed operating conditions. In this way, the actual operation of the sulphuric acid plant is improved, using the theoretically possible optimum calculated by Metso Outotec’s mathematical simulations as the target.
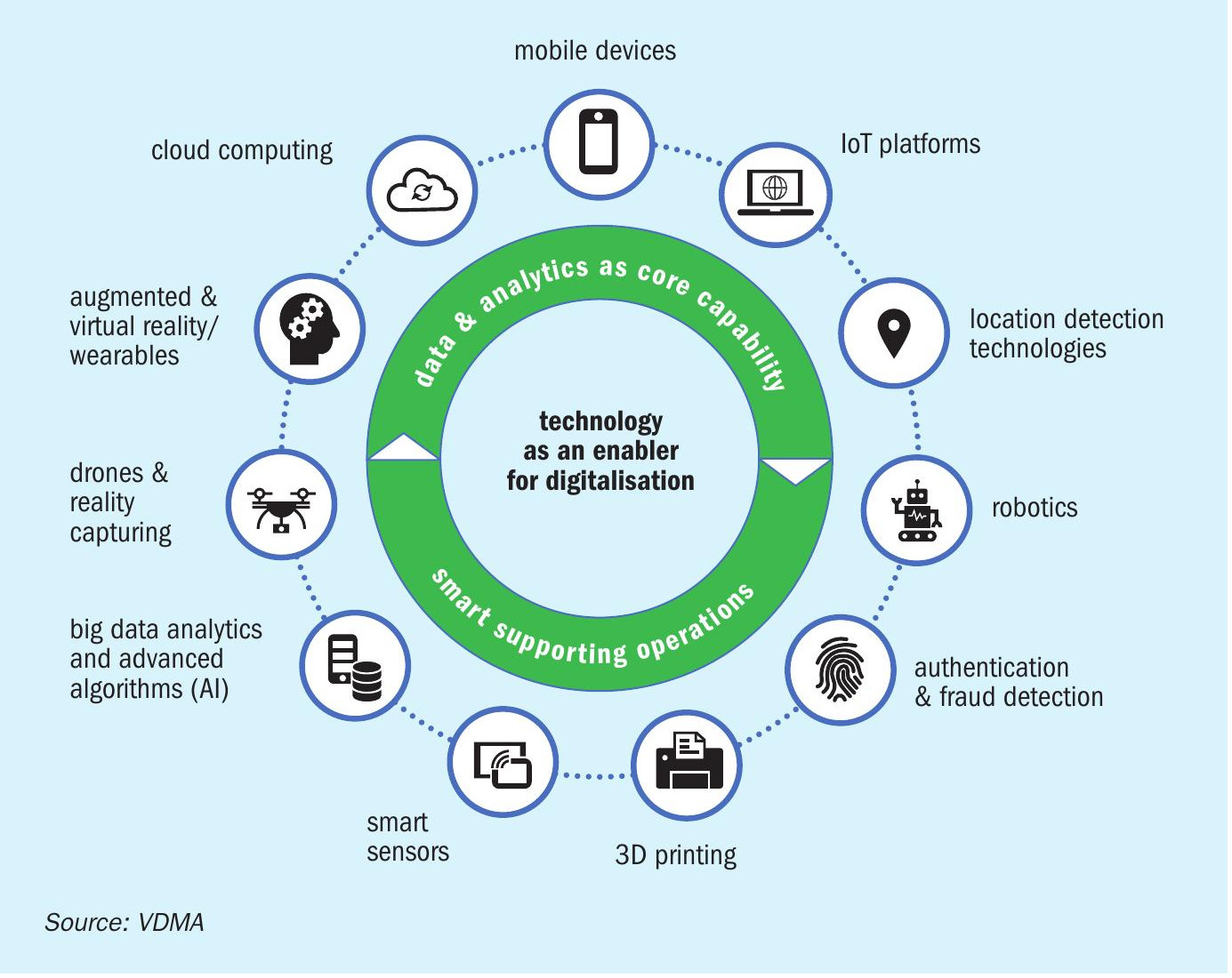
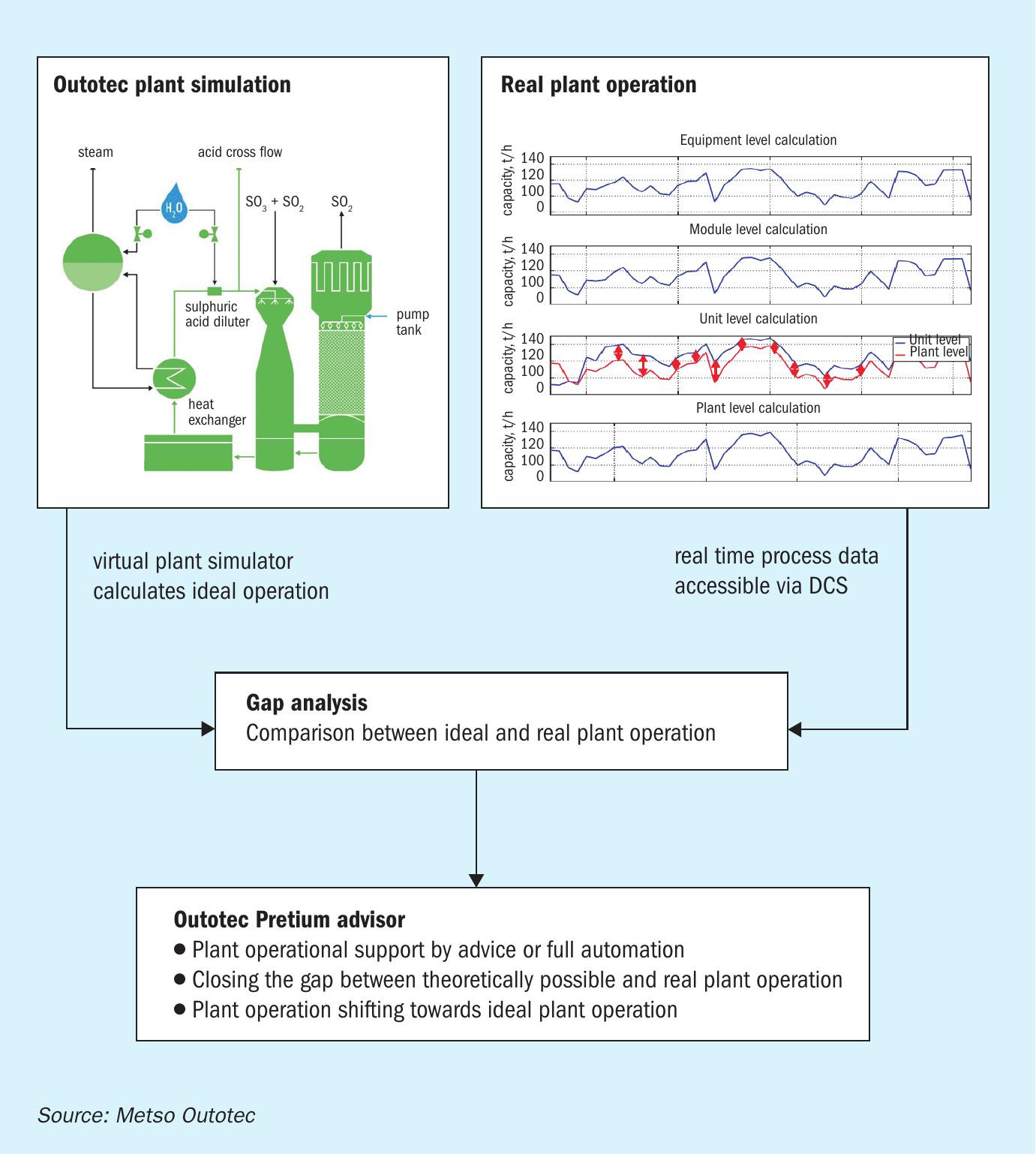
Gaps can also be caused by fouling of the different types of heat exchangers present in sulphuric acid plants. Mathematical models of heat exchangers are usually highly precise. This enables long-term monitoring to detect fouling trends. The variance between simulated and measured heat exchange can, however, have different causes. Sudden and rapidly rising gaps between theoretical and real measurements, for example, are usually a sign of leakage.
Simulation accuracy
Various Metso Outotec experts need to participate fully – in both fault detection algorithms and operational support – to achieve the required simulation accuracy. Process experts provide process know-how and flowsheet calculations, as well as plant-wide calculation models and site experience. Equipment experts furnish the necessary detailed know-how on single process units, while catalyst experts ensure detailed models for the chemical conversion from SO2 to SO3 and H2 SO4 are accurate.
The accuracy of simulated versus actual temperature readings in the simulation of a sulphuric acid plant flowsheet is shown in Figure 4. The percentage error is calculated from:
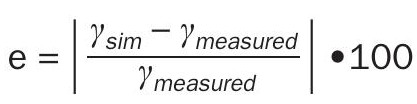
This compares the simulated temperature value (γsim ) in Kelvin (K), at each process step, with the respective temperature measurement (γmeasured ) in K, as captured by the DCS. The DCS measurements are mean values obtained over a specified time range.
Figure 4 confirms that the simulation is highly accurate, with most simulated temperature readings having an error value of below one percent. The first converter stage outflow temperature does, however, show a deviation between measured and simulated temperature of more than three percent – a discrepancy that requires further investigation. Such an error could mean that either the model parameters are inaccurate or that the catalytic converter in the first stage is showing the effects of aging.
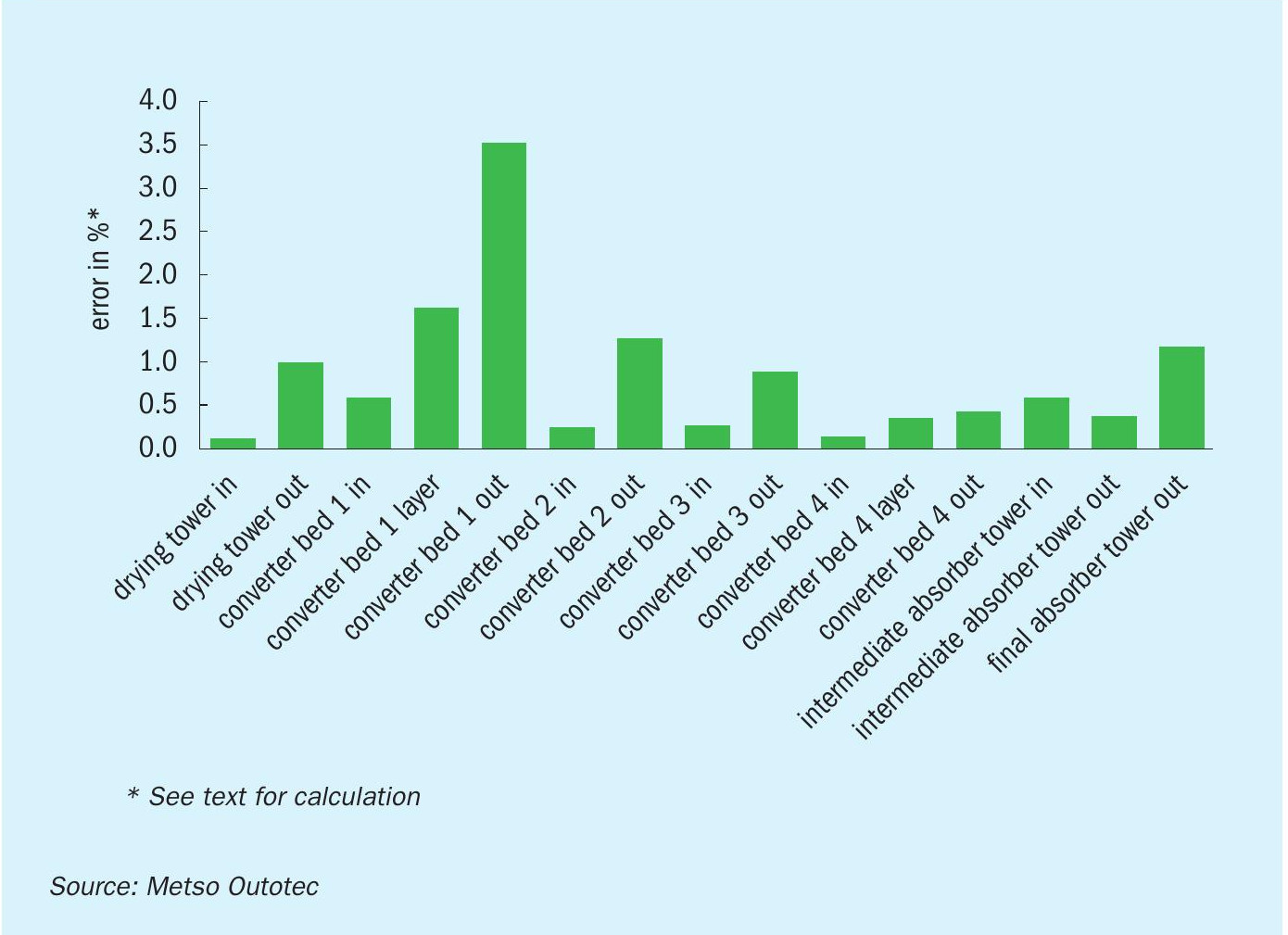
Vitally, this gap analysis of simulated results versus actual DCS measurements demonstrates just how important instrumentation engineering is – that includes equipment design, the location of instruments, measurement ranges, instrument installation and the quantity of instruments. The more precise and careful this engineering is, the easier it is to match simulated parameters with real world measurements.
In our view, the use of digital tools requires a highly diligent approach to instrumentation. A special focus is needed in the selection of instruments and how many are in standby/installed status. The placement of instruments in the right physical location is even more important.
The overall conclusion is a simple one. Unlocking the full power of digital tools is only possible if there is an intimate knowledge of the sulphuric acid plant’s prevailing flow and reaction regime.
Advanced automation – integration of upstream process steps
Metso Outotec – in addition to offering simulation-based fault detection and operational support – has rapidly ramped up its capabilities in advanced process control and automated optimisation for the whole sulphuric acid plant unit. By applying a fully-automated control and optimisation system to the upstream metallurgical roasting plant, strong improvements in the operational stability of the entire sulphuric acid and gas cleaning plant train are now possible. The system – known as Roaster-Optimizer – is currently being operated by a select group of Metso Outotec customers. This is enabling their roasters to operate at increased throughput while maintaining a high level of product quality.
The RoasterOptimizer is a multi-variable control and optimisation system that enhances roaster operation. The system – besides monitoring and taking into account various roasting plant variables – also considers process variables in the downstream gas cleaning and acid plant. As a consequence, one of the benefits of implementing RoasterOptimizer is that, by encompassing the complete process chain, it ensures and guarantees that environmental emission values are not exceeded, while at the same time increasing plant capacity.
Figure 5 shows the expected long-term environmental improvements delivered when a plant is in operation with RoasterOptimizer. This clearly demonstrates the system’s advantage, in terms of reduced emissions.
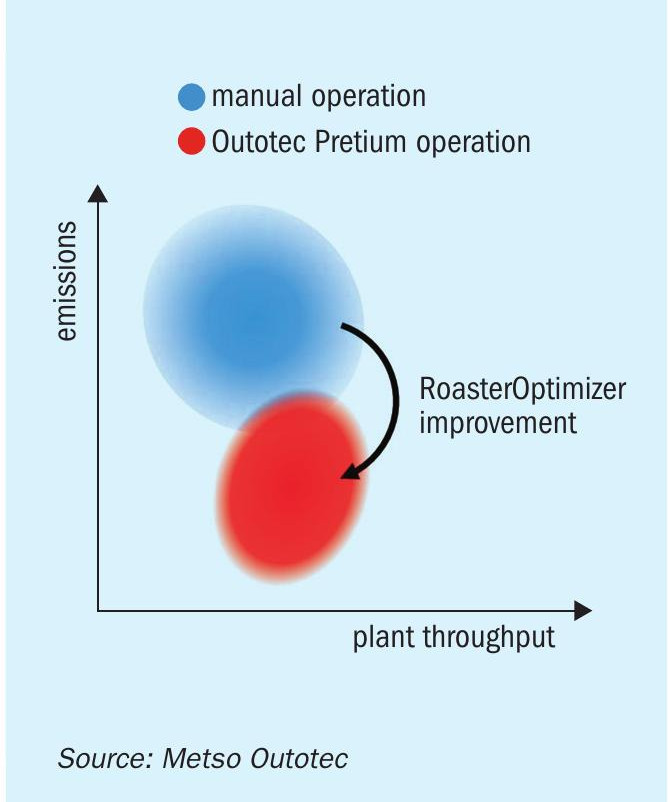

- Feed material preparation with increased blend flexibility Õ Addition of waste streams and/or low grade concentrates, production cost reduction
- Roaster plant availability and capacity increase Õ Process stabilisation, reduced stress on plant and equipment
- Acid plant environmental improvements Õ Lowering SO2 emissions, reducing bottlenecks l Leaching efficiency increases Õ Higher calcine product quality, production cost reductions in the hydrometallurgical plant.
Combining digital tools for upstream metallurgical process steps (feed preparation, roasting etc.) and downstream process steps (gas cleaning, sulphuric acid production and hydrometallurgical plant sections) reveals the full operational potential of ‘Industry 4.0’ for today’s sulphuric acid production sites.
The integration of RoasterOptimizer, for stabilising and optimising the fluidised bed-roaster, and PORS, for monitoring and supervising the full acid production process, provides a good example. This combined approach is able to optimise the full production chain of the roasting-gas cleaning-sulphuric acid-leaching plant. The leading-edge plant performance achieved, through the adoption of simulation and digitalisation, represents a significant step towards the fully-automated production processes expected in future.
Supporting customers remotely in the future
Metso Outotec has actively supported its installed plant base globally during the current pandemic, offering advice and support to our customers throughout this unprecedented disturbance to production. For our references where expert advanced monitoring and control features are installed, we are providing feedback on future developments that will ensure our digital tools offer even greater value in the future. In the section below, we reflect on the experiences gained with our installed digital tools during 2020, and outline our future digital offerings.
During the current pandemic, the remote support services for our digital tools have proved a success – as the majority of these support staff work from home-based environments under normal circumstances. Also, because these support staff already have access to our centralised process support teams, our customer technical support has in no way been disrupted.
Looking ahead, one obvious omission from our digital offering has been the lack of a complete and joined-up ‘big picture’ of the whole process. A digital system supporting a process unit – such as a smelter, hydrometallurgy plant or parts thereof – has significant inputs from upstream and side streams, for example. Yet these may not have the same level of digitalisation. Therefore, in many situations where a trend in the data is observed, there is a need for a more holistic production overview to ensure that actions are taken at the correct stage of the process.
Achieving this ‘big picture’ level of understanding is not necessarily easy. It requires communication, transparency and trust between individual production units operated by customers. The advice and input from Metso Outotec’s process support staff also needs to be seamlessly incorporated.
There is also a wide spectrum of operator attitudes towards digital tools currently. These range from total distrust (“Big Brother is watching us” and “this box will take my job away” being typical reactions) to a potentially naive reliance on digital tools as a magic bullet. Somewhere between these two extremes is the rightful and more pragmatic approach. This acknowledges that, firstly, operator skill and experience is paramount and, secondly, furnishing an operator with digital tools that he/she can trust allows that individual to make better operational decisions.
Metso Outotec is integrating existing digital tools into our current EPC services and offerings. Based on our process industry heritage and know-how, we are also pressing ahead and developing new modular analytical/autonomous solutions for our global customer base. However, regardless of what an EPC contractor develops and brings to market, the fact that the digital maturity level in the industries we serve is relatively low remains an obstacle. Our focus, therefore, must be to support ‘early adopters’ to confirm the success and applicability of digital technologies and Industry 4.0. The mantra “do what you can, with what you’ve got, where you are” – widely and indirectly attributed to Theodore Roosevelt – is a valid summing up of digitalisation in the industries Metso Outotec serves.
We are acutely aware of our industry’s general deep mistrust regarding data security and allowing ‘intimate’ access to their production data. An open-source approach between customer and engineering partner is required, in our view, to break down the ‘black box’ mentality and build the necessary trust that leads to successful partnerships. The following fundamental issues need to be addressed for all parties to reap the advantages (Figure 6) that digitalisation can offer:
- All parties are part of the solution. Transparent revenue/profit models are also necessary to benefit all those involved. An attitude of ‘sharing, but not owning’ is probably the greater challenge.
- Having open and transparent communication and trust is fundamental and needs to be part of the skillsets of all participants.
- Ensuring data security and providing guarantees that use of data will be for ‘purpose only’ are critical factors
- Industry benchmarking and industrial KPIs are areas that require more focus and attention.
Summary
Digitalisation (Industry 4.0) is seen as a driver for improving process efficiency. Its introduction can/will ultimately disrupt traditional business models as well. Digitalisation is also likely to herald a fundamental change in the relationship and balance between EPC contractors and customers.
Metso Outotec has always presented their digital tools to the industry as a ‘work in progress’. For digital solutions to be a success in industrial operations, there needs to be a strong bond of trust between us and our customer – and an acknowledgement that both parties have something valid to offer in reaching the ultimate digital solution.
Indeed, our experience to date indicates that the efficiency of the digital tool increases significantly when the trust and collaboration between process support personnel and plant operators is allowed to deepen and flourish.
Metso Outotec has always accepted the ethos of ‘sharing, but not owning’ the data associated with plant operations. Probably the greatest challenge to wider digital applications, in our view, will depend on this key issue being accepted and resolved.
Ultimately, it is our customers who will decide on the future direction of the industry. So they must also be able and willing to take a leap of faith if the ‘digital adventures’ and possibilities described here are to become a reality and a success.
References