Sulphur 389 Jul-Aug 2020
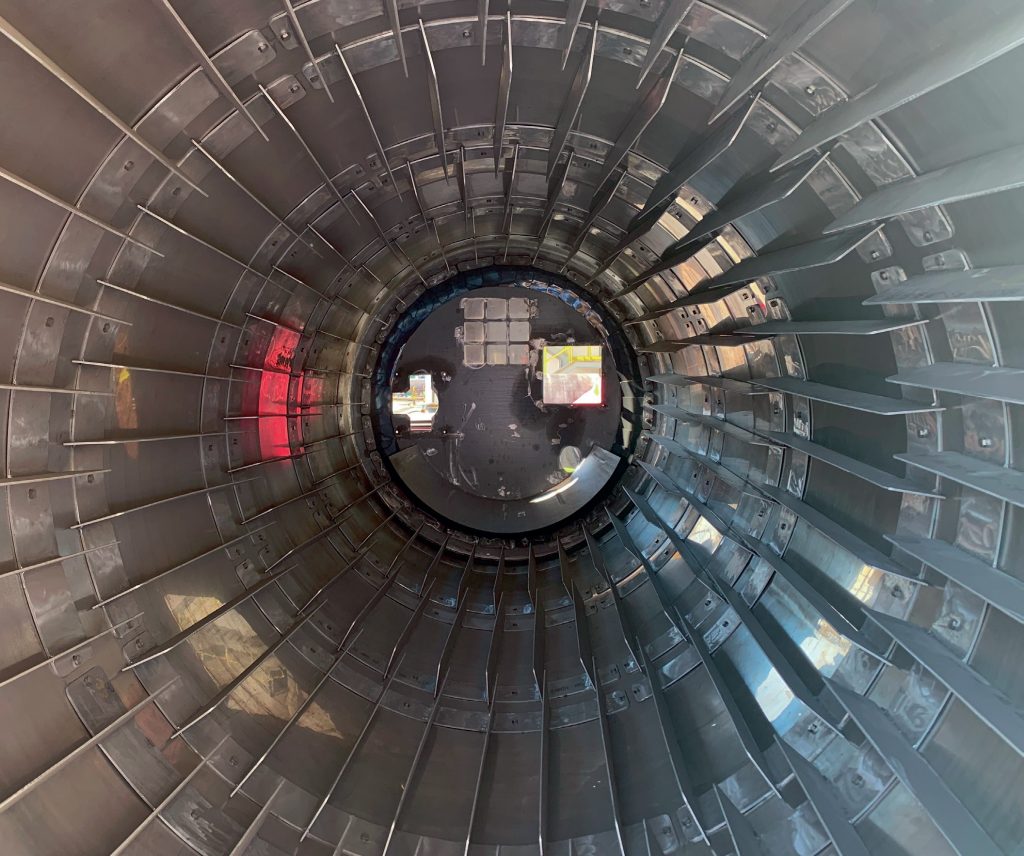
31 July 2020
IPCO’s first drum granulation plant in Europe
SULPHUR FORMING
IPCO’s first drum granulation plant in Europe
IPCO provides an update on its latest activities, with flexible processes enabling IPCO’s project for the first drum granulation plant in Europe to remain on track despite unprecedented Covid-19 restrictions.
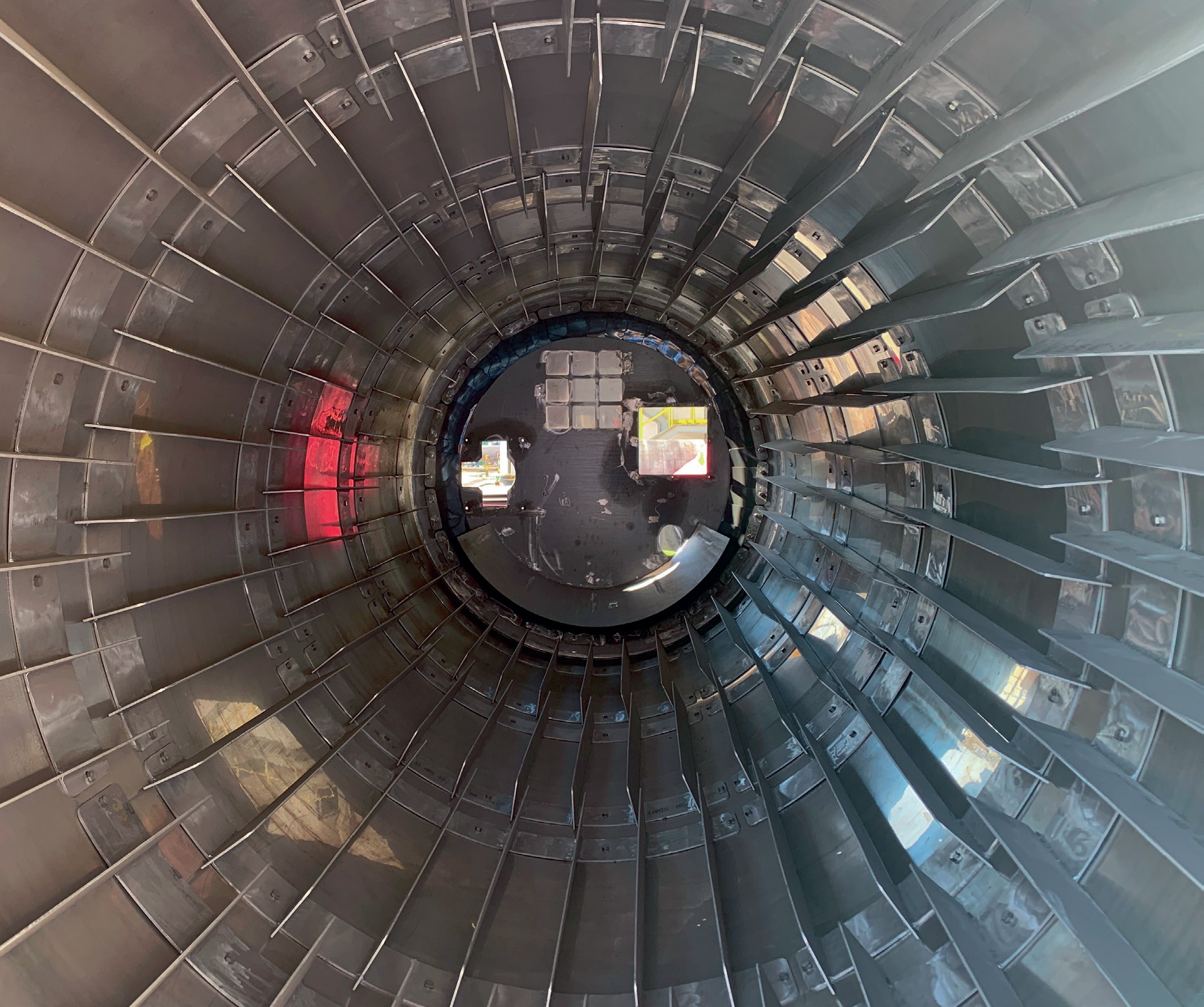
IPCO, one of the world’s leading suppliers of sulphur processing and handling systems, is working to deliver what will be its first mid-capacity drum granulation plant in Europe. The project, scheduled for commissioning in Q3/Q4 2020, remains on track despite restrictions imposed due to the coronavirus pandemic.
IPCO’s SG20 sulphur granulator has a solidification capacity of 500 -800 t/d. Based on rotating drum technology, this sulphur granulator is a fully automated process delivering high productivity ‘once through’ performance and a uniform end product of a definable size.
The company also produces an SG30 model, a unit capable of granulating up to 2,000 t/d, the highest capacity solution available to the sulphur processing industry.
Seed or nuclei particles of solid sulphur are generated outside the drum by freezing sprays of liquid sulphur in a water bath at controlled pressures to form the desired size range. These particles are then augered into a slowly rotating drum with appropriately placed flights attached to its inner surface. The flights create curtains of particles inside the drum as well as gently moving them towards the discharge end.
As the nuclei particles travel along the drum, they are progressively enlarged to the required size by means of sulphur sprayed from a bank of nozzles running the length of the drum. The temperature in the drum is moderated by the evaporation of water from spray nozzles located inside the drum.
A fan is used to draw a stream of air through the drum to sweep out the water vapour as well as any fugitive dust inside the drum. The dust is scrubbed out of this exhaust stream using a wet scrubber before the process air stream is released to the atmosphere.
The underflow from the wet scrubber cyclone is pumped to the same settling/ dewatering tank that is used to generate the seed particles. Here the fines settle out and are augered up along with the sulphur particles generated by the seed generator sprays.
IPCO sulphur granulators are supplied prefabricated for quick and easy installation, and are designed to offer high productivity with low maintenance requirements. A simple design with minimal rotating equipment enables continuous operation with no need for routine shutdown, while the horizontal 0° drum minimises stress to keep maintenance requirements low. No sulphur pre-conditioning is required and no solid waste streams or liquid effluents are produced.
The spherical shape of the granules, along with the repeated spraying and cooling of thin layers of molten sulphur as they pass through the granulator, accommodates the natural shrinkage of the product as it completes the transition from melt to solid, without weakening the product.
SUDIC quality product
The SG20 will produce a high quality product that satisfies the shape criteria and Stress Level I and II friability parameters of the SUDIC product specification. This ensures efficient, clean and environmentally safe storage and handling during transportation (formed sulphur can be handled as many as 15 times between solidification and subsequent reprocessing).
Another major factor in terms of achieving SUDIC specification is moisture content; excess moisture not only adds weight, leading to unnecessary transportation and melting costs, but also results in increased acidity, causing corrosion in conveyors, silos, trucks, rails cars and ship holds. A ‘wetter’ product is also more susceptible to freezing into lumps during cold weather, a significant factor in colder climates.
According to the SUDIC definition, quality sulphur will meet the specifications shown in Table 1 21 days after forming.
Complete family of sulphur processing and handling systems
The development of the SG sulphur granulator family is just the latest addition to a range of sulphur solidification and handling systems that began in 1951 with the installation of a continuous sulphur slating line at an oil refinery in Mexico.
IPCO has since expanded its capabilities to encompass equipment for liquid sulphur degassing (capable of reducing hydrogen sulphide to less than 10 ppm), molten loading for truck and rail, downstream storage and reclamation, as well as bulk loading for truck, rail and ships.
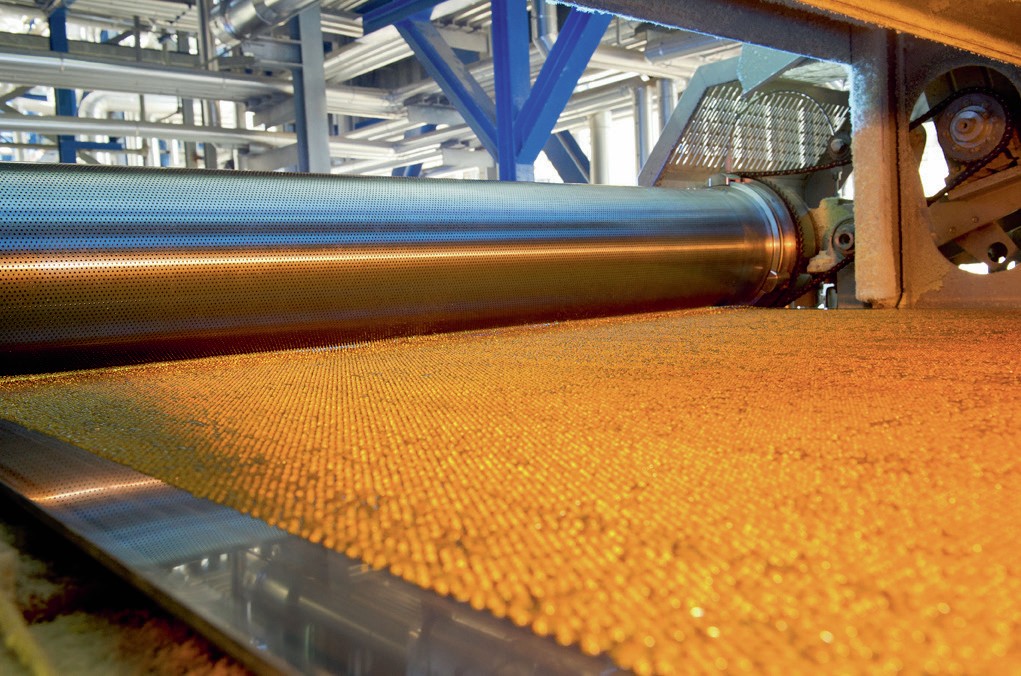
In terms of solidification, systems are available to meet all throughput requirements. Block pouring offers a practical and economical solution for the medium to long term storage of high volumes of sulphur, and IPCO can provide a full consultancy service as well as the physical equipment such as pouring towers and forms. Complementing this is a range of low maintenance, skid-mounted remelters with predictable, high capacity throughput.
Rotoform sulphur pastillation systems
For small to mid-size capacity solidification requirements, IPCO’s proven Rotoform system is a single step, liquid-to-solid process that, like the SG granulators, produces a SUDIC-quality premium product. The uniform shape and size of Rotoform pastilles makes them free-flowing for easy handling, while high bulk density is a major advantage in terms of storage and transportation.
With more than 750 installations completed to date, Rotoform is the world’s most widely used process for the production of premium quality sulphur. While the basic operating principle has remained unchanged since the first model was introduced in the 1980s, the Rotoform family has undergone constant improvement and the latest models specially designed for sulphur processing are the Rotoform S8, with a capacity of 140 t/d, and the Rotoform HS, a high speed model with a capacity of up to 350 t/d.
The Rotoform consists of a heated cylindrical stator, which is supplied with molten sulphur via heated pipes and filter, and a perforated rotating shell that turns concentrically around the stator. Drops of the product are deposited by the nozzle bar across the whole operating width of a continuously running stainless steel belt.
A system of baffles and internal nozzles built into the stator provides uniform pressure across the whole belt width, providing an even flow through all holes of the perforated rotary shell. This ensures that all pastilles are of uniform size, from one edge of the belt to the other.
The rotation speed of the Rotoform is synchronised with the speed of the steel cooling belt to allow gentle deposition of the liquid droplets onto the moving belt. Heat released during cooling and solidification is transferred via the steel belt to cooling water sprayed underneath.
This water is collected in tanks and returned to the water recooling system; at no stage does it come into contact with the product.
After the drop has been deposited onto the steel belt, any product residue on the outer shell is returned to the Rotoform via a heated refeed bar which keeps the outer shell clean.
The sulphur droplets are then discharged as solid, hemispherical pastilles at the end of the cooling system. To eliminate the possibility of damage to the pastilles during discharge, a thin film of silicon-based release agent is sprayed onto the steel belt.
This process offers a number of environmental advantages. As the cooling water never comes into direct contact with the sulphur, there is no risk of cross contamination. Secondly, solidification takes less than ten seconds so there is little time for H2 S to escape, resulting in very low emission values. And low levels of sulphur dust levels mean no need for exhaust air treatment.
End-to-end systems and engineering partnerships
IPCO’s expertise, gained through nearly 70 years’ close involvement with the oil and gas industry, extends to the design, supply and commissioning of complete end-to-end systems covering everything from receipt of molten sulphur to storage and loading of solid material.
The company has partnerned with several international engineering companies that service the petrochemical industry. Activities range from cooperation during FEED (front-end engineering design) to EPC (engineering procurement construction) contracts, and turnkey solutions include liquid sulphur supply, solidification and downstream handling of solid sulphur as well as utility equipment and control systems.
IPCO can also provide what it refers to as its Life Cycle Concept. An extensive after sales service is available to provide customers with continual support throughout the lifespan of the equipment supplied, including inspection and preventative maintenance contracts.
Facing up to the challenges of the Covid-19 crisis
This end-to-end capability, built on an in-depth understanding of customer needs and priorities, has held IPCO in good stead in these unprecedented times, enabling the company to continue to support refineries around the world with both new installation and the servicing and maintenance of existing systems and equipment.
With a local presence in more than 30 countries, IPCO’s global service capability has been a key factor in this. By following World Health Organization guidelines and adhering to local restrictions, the company’s service teams have been able to provide a basic level of support.
The restrictions on travel and face-toface meetings due to the coronavirus crisis have driven IPCO to look at new ways of working. For example, client meetings, and many internal ones too, now take place on Teams or Zoom instead of in an office.
IPCO has also been making use of video streaming to offer system trials from its productivity centre in Fellbach, just outside of Stuttgart.
“We had a number of customer visits scheduled for Q2,” says Johan Sjögren, Managing Director of IPCO’s Equipment division. “Instead of cancelling, we have made use of digital media to allow these customers to assess our systems remotely. Our aim is to try to maintain a level of service as close to normal as the current circumstances permit.”
This ability to provide support, reassurance and delivery guarantees has been key to keeping the SG20 sulphur granulator on track. However, with markets suffering understandable uncertainty, other orders in the pipeline have been put on hold. “Previously you would have got on the next plane and flown directly to the customer to clarify the situation but this simply isn’t possible now,” says Sjögren.
“We all have to get used to new ways of communicating. Flexibility and the ability to think outside the box will be key and we need to demonstrate that we can continue to work effectively and offer customer-oriented solutions.”
Industrial Internet Of Things (IIOT)
It is obvious that digitisation will have a central role to play in future ways of working and IPCO had already made significant moves in this direction before the arrival of Covid-19.
“The market is changing,” says Johan Sjögren. “Customers are looking for suppliers whose capabilities go beyond the simple provision of hardware, however efficient it might be.”
To this end, IPCO has been focusing on the connectivity of its systems, a capability often referred to as the Industrial Internet of Things (IIOT). In this instance, digitisation means offering remote access to the control panel based on a cloud solution, recording and evaluating of process-related parameters, ‘messenger’ functions and visualisation of maintenance intervals with indication of the required spare parts.
This ability to monitor, collect and analyse information remotely has the potential to transform system performance and productivity, driving efficiencies throughout the sulphur solidification and handling process.
As Johan Sjögren explains: “Access to real-time production data offers a window into the efficiency of a system and can reveal potential for additional capacity. Sensors can enhance safety, providing alerts to issues before they have a serious impact, and machine-to-machine communication can streamline production across every stage of the process, from receipt of molten sulphur, through solidification, to downstream storage and loading.”
“We have customers who are looking for production support or even the complete operation of their plant. A combination of digitisation and our existing application expertise will enable us to offer completely new levels of customer care and support.”