Nitrogen+Syngas 366 Jul-Aug 2020
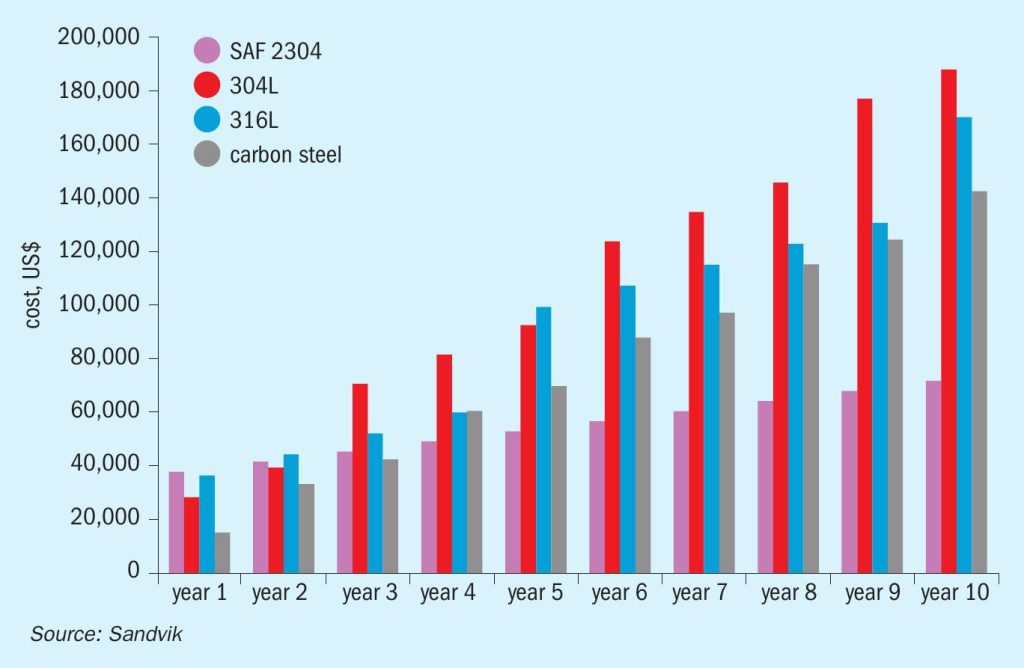
31 July 2020
Lean duplex improving on-stream times
AMMONIA CONDENSERS AND COOLERS
Lean duplex improving on-stream times
Many fertilizers plants are looking to reduce the overall maintenance costs of their critical heat exchangers. Barinder J. S. Ghai of Sandvik Materials Technology takes a look at the life cycle costs of tube materials for heat exchangers in ammonia plants.
It is no secret that huge amounts of money are spent every year on the replacement of materials which corrode in ammonia plants. The extent of corrosion varies depending on numerous factors. One way of dealing with this problem is to control the process parameters, which is an ongoing process. An alternative solution is to replace the materials that are failing with more corrosion resistance alloys. When selecting alternative materials of construction, both material cost and life of the equipment need to be considered.
Heat exchangers, e.g. waste heat recovery boilers, shift conversion heat exchangers, lean amine coolers, carbon dioxide stripper overhead condensers, compressor inter-stage coolers, ammonia condensers, convertor effluent coolers etc. play a vital role in the ammonia production process. The tubes used in heat exchangers constitute more than 60% of the cost of these heat exchangers. Any premature failures of the tubes can lead to loss of production, higher maintenance and replacement costs and, not least, safety risks.
The most commonly used materials for heat exchangers in ammonia plants are carbon steel followed by 304L stainless steel. While duplex stainless steel has been used extensively in many chemical plants due to its superior properties, its initial investment cost has been a major obstacle to replacing traditional materials in ammonia plants.
The cost of lean duplex stainless steel, however, falls between low cost carbon steels and austenitic stainless steels and the more expensive and highly alloyed steels, making it an attractive solution for lowering maintenance costs and reducing tube replacement frequency e.g. in plants where heat exchangers with low alloys such as carbon steel have to be re-tubed every two to four years.
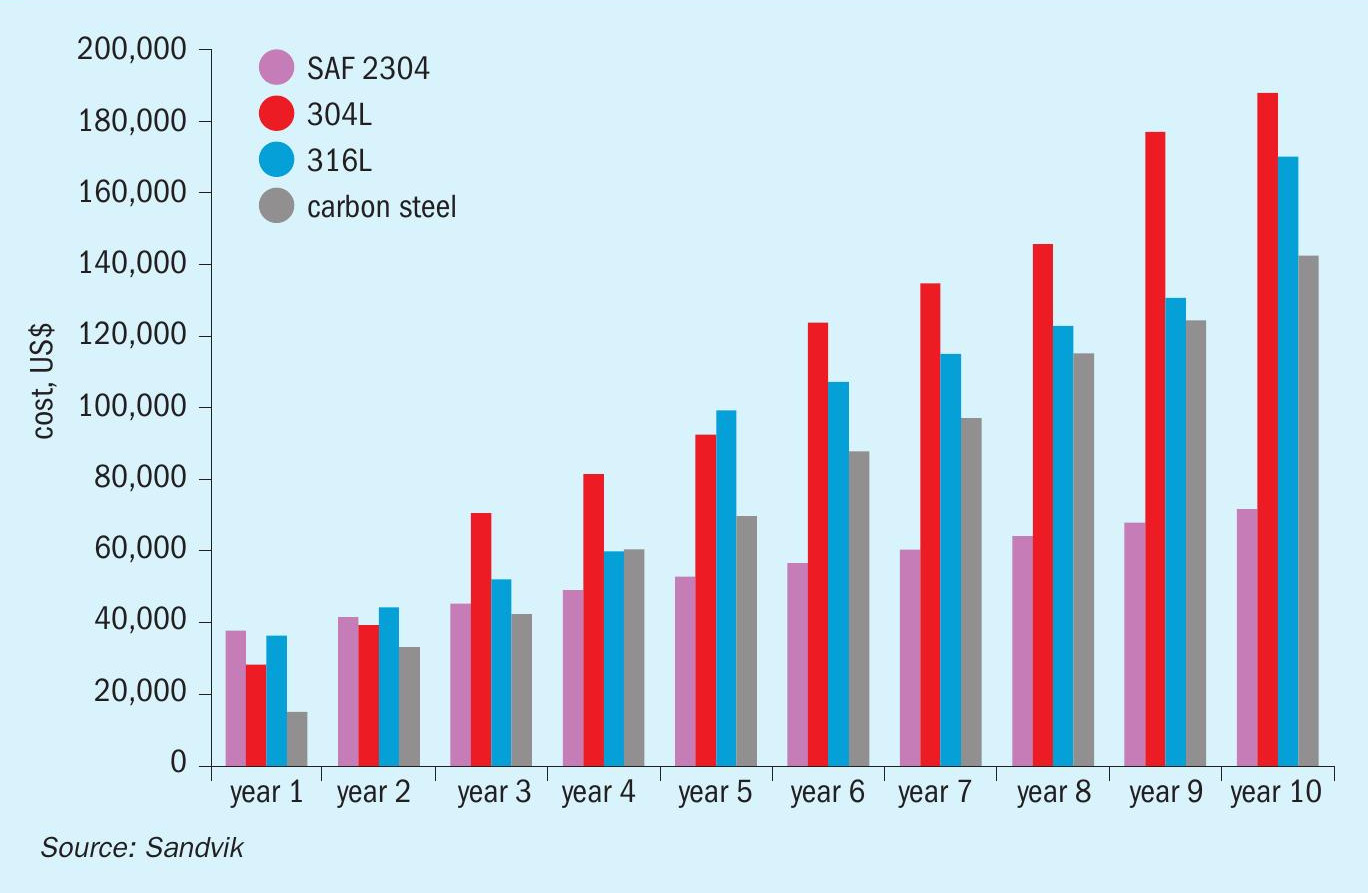
Sandvik’s SAF 2304™ lean duplex stainless steel was developed as a cost effective solution for various industries, including refining and petrochemicals, but is particularly suitable for applications in ammonia plants. Thanks to its dual phase (50% austenitic and 50% ferrite), it also possesses very high mechanical strength. When replacing carbon steel tubes with duplex tubes, the wall thickness is reduced because corrosion allowance is no longer needed. Wall thickness reduction is also possible compared to 304L and 316L.
The initial cost for carbon steel/304L tubes is cheaper compared with SAF 2304™ , however SAF 2304™ outperforms these materials in the long term, subject to no retubing and no maintenance or replacement costs. Fig. 1 shows the life cycle cost of SAF 2304™ compared to 304L, 316L and carbon steel over a ten year period.
Chloride-containing water is one of the most common causes of corrosion in heat exchangers. Depending on the level of chlorides and the temperature, this can lead to stress corrosion cracking, pitting corrosion and/or crevice corrosion. Resistance to pitting and crevice corrosion largely depends on the amount of chromium, nitrogen and molybdenum in the material of construction. Here, due to its high chromium and nitrogen contents, lean duplex performs much better than carbon steels and 304L.
As for all duplex stainless steel, SAF 2304™ exhibits a high resistance towards chloride-induced stress corrosion cracking, performing much better than 304L and 316L.
Sandvik SAF 2304 duplex heat exchanger tubes have been installed, amongst others, in an ammonia plant in India where they have been successfully in service for more than 12 years.