Sulphur 389 Jul-Aug 2020
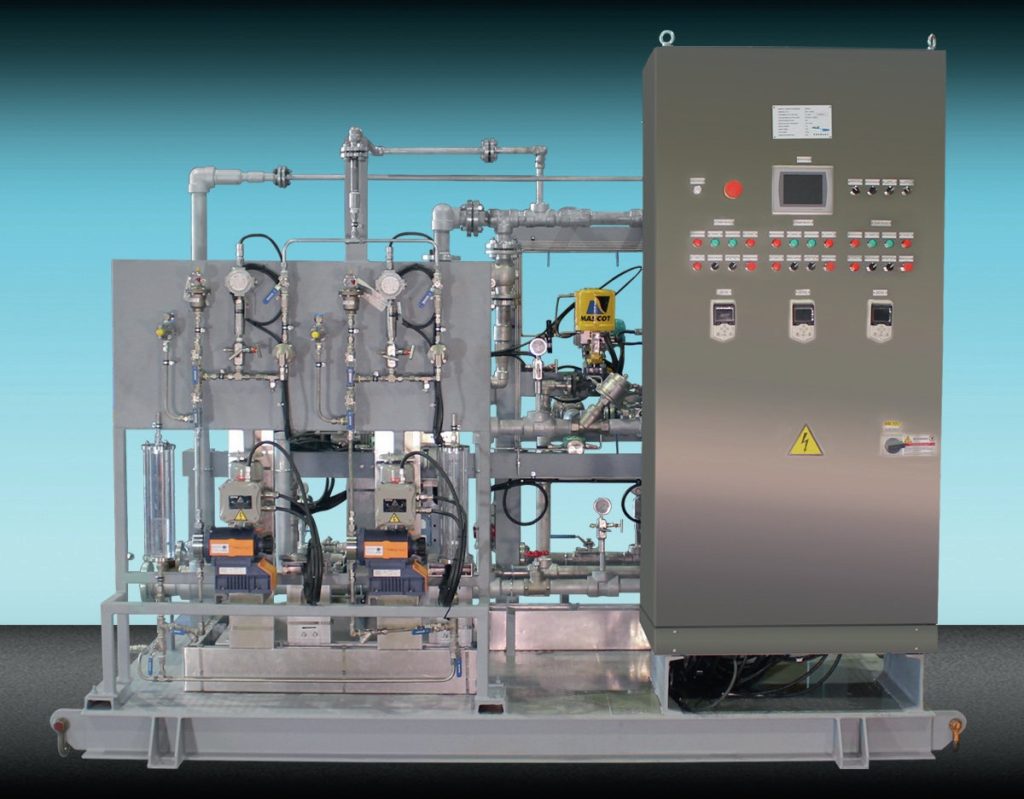
31 July 2020
Sulphur dust control through suppression
SULPHUR HANDLING
Sulphur dust control through suppression
Fugitive dust emissions during the handling and storage of formed sulphur can result in negative environmental impacts and under specific conditions result in an explosion hazard. Enersul has developed a dust suppression system specifically targeted at controlling sulphur dust particles. The Enersul SafeFoam Transfer System (STS) reduces sulphur fines at critical transfer points throughout any sulphur handling system, resulting in a significantly safer and more environmentally friendly sulphur handling system.
Sulphur deficiency in arable soil has been becoming a major concern in the agricultural industry in recent years. Factors contributing to sulphur deficiency in soils include the fact that more sulphur is being removed from the soil due to the increase in agricultural production and less sulphur is being added back into the soil due to the use of sulphur-free fertilizers and lower sulphur dioxide emissions throughout the world. Sulphur is an essential nutrient required for plant growth and sustainability. Sulphur deficient soils produce crops that are both low in yield and in quality. Use of sulphur fertilizer helps to overcome these potential problems, increases overall fertilizer efficiency and consequently results in better economics for the producers.
Sulphur by nature is a combustible element and care must be taken during the handling and storage of solid sulphur. In any material handling process there is potential for dust formation due to shifting of product from one location to another. Fugitive dust emissions during the handling and storage of formed sulphur can result in negative environmental impacts and under specific conditions can engender an explosion hazard. A dust explosion will occur when fine dust in a certain concentration suspended in air is ignited. Combined with a confined environment, the burning mixture will release large quantities of harmful gaseous product, resulting in a pressure rise and therefore a possible explosion. The LEL (lower explosion limit) for sulphur dust particles in air is 35 g/m3 , making sulphur dust one of the easiest ignited materials found in the bulk handling industry. Sulphur dust clouds found above the lower explosion limit of 35 g/m3 also have a very low ignition energy of 15 mJ; this means that that these dust clouds can be set off with the presence of a frictional or static spark, which is a common occurrence during the handling of solid sulphur. As mentioned earlier, the initial explosion will occur within a confined environment, but if the reaction from this initial explosion disturbs settled layers of dust in the surrounding area it can cause a secondary, much bigger explosion. Lack of consideration in sulphur handling can be costly economically, but it can also become a major safety issue. It is critical to put careful consideration into both the design of material handling systems and proper mitigation operational procedures.
The design of the material handling system must be carefully examined and standard precautions should be taken to eliminate any potential risks. The focus needs to be on reducing the potential for the creation of fines (particles less than 500 μm in diameter) and keeping any fines that are generated from becoming airborne. The design and operation of storage and handling facilities needs to recognise the importance of regular housekeeping to keep the plant running safely, limiting the amount of horizontal surfaces where dust can build up, using rubber and non-sparking material for conveyor belt material, designing electrical equipment for the proper hazardous area zones and never using compressed air to remove dust from a surface as this can create dust clouds. Other considerations should look at minimising the drop heights at product transfer points, and application of dust suppression systems should be considered.
Even after efficient design, dust generation cannot be completely eliminated and hence must be controlled. The two main dust control system available are dust collection and dust suppression. Dust collection is usually done by one of two methods, by using a dry dust collector or by using a wet dust collector which is also known as a wet scrubber system. Both of the dust collection techniques have distinct benefits and drawbacks. The wet dust collector is an objectively effective and safe mechanism for collecting sulphur dust. The wet scrubber system collects dust at the point of application, uses water to capture this dust in an air stream and then releases the collected dust in the form of a slurry byproduct. The issue with this solution is that the slurry byproduct is very corrosive to any metallic plant equipment it comes into contact with and that it requires proper disposal. The dry dust collector also collects dust at the point of application, but it does not use any water so there is no slurry byproduct. One major issue with the dry dust collector is that it captures fine sulphur dust particles in a confined environment and consequently provides the conditions for a possible explosion to occur. This issue generates the need for either use of explosion venting to provide a controlled release mechanism or the use of a gas inerting system to suppress the explosions. Explosion venting does not get rid of the explosion problem, it is only used as a protection measure and gas inerting is a highly complex system itself. There are very high operating and maintenance costs associated with both of these systems and therefore this is not the most economical or preferred solution for controlling sulphur dust.
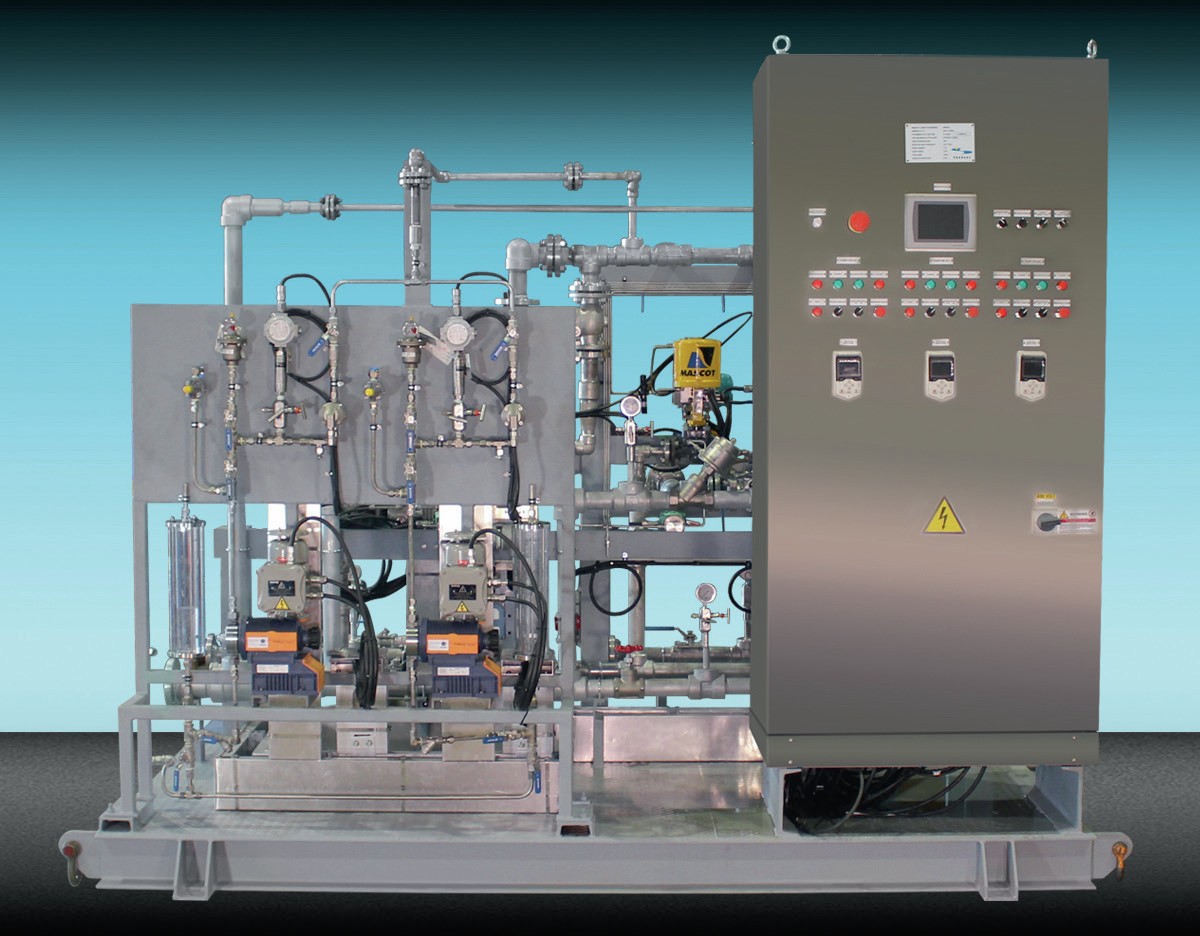
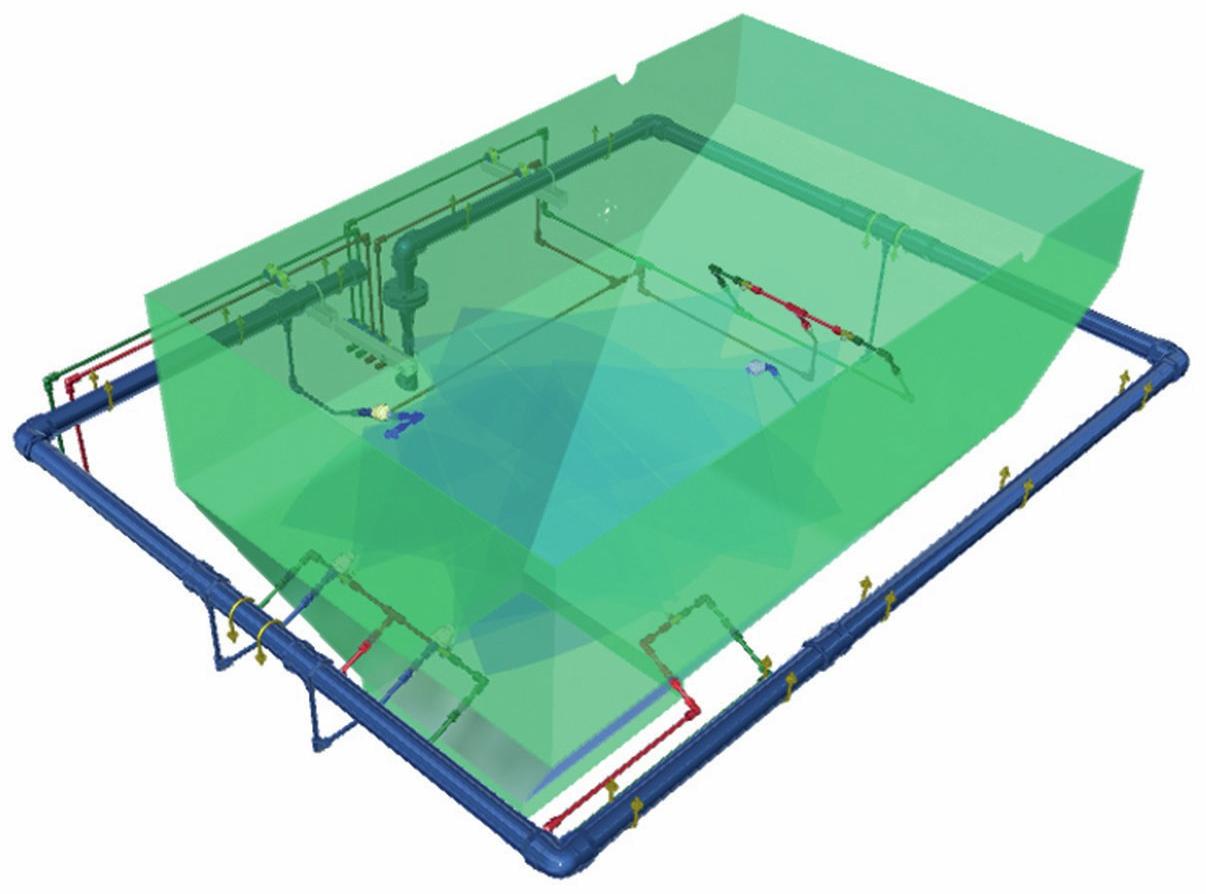
In place of dust collection there is another means of dust control; dust suppression systems. This method looks at controlling the propagation of the dust and ensuring that it does not become airborne. There are many dust suppression systems available in the market but the major drawback of most of these systems is that they use large quantities of water to suppress the dust. There are a few issues with using large amounts of moisture to suppress the dust. First of all the combination of moisture and elemental sulphur can be very corrosive to steel and therefore this may largely affect the lifetime of the equipment and plant. Corrosion further produces a byproduct of iron sulphide, which when mixed further with wet bio-oxidised elemental sulphur forms a dangerous hydrogen sulphide gas. Presence of hydrogen sulphide is a huge safety concern which must be closely monitored and controlled.
In response to increasingly stringent environmental and safety standards Enersul has developed a SafeFoam Transfer Dust Suppression System called STS, specifically targeted at controlling fugitive sulphur dust. This system uses a 1:100 water chemical mix to control the dust, which minimises the amount of additional moisture added to the product and also provides a coating that adheres to the product for a longer duration of time, allowing the product to be transported through the system without the need for additional dust suppressant application.
The innovative aspect of Enersul’s system, along with the modular skid and dust suppression chemical, is the arrangement of the nozzles. The nozzles are sized to generate adequate fineness of mist and are arranged in such a manner to be able to coat majority of the fines resulting in a high degree of dust suppression. The chemical leaves a thin layer on the product and degrades only marginally with time. Enersul generally does not design the system as a one-size-fits-all application that is simply placed at all transfer points and results in over-coating the product with dust suppression chemical; rather Enersul uses its many years of experience to assess the material handling system and recommend the best location for dust suppression to be applied. The key to effective dust suppression is not to drench the product in dust suppression chemical at each transfer point, this can lead to high chemical costs and objectionable increase in moisture content of the product; instead application at selective locations is most effective.
STS description
Water and chemical are mixed in a ratio of 100:1. This mixture is piped to a header mixing chamber at the selected transfer points where air is injected to convert the mixture to foam. This foam is then discharged through the spray header nozzles and is applied to the product. Fig. 1. shows the modular dust suppression skid which is used for the metering and control process.
Chemical supply system
Dust suppressant chemical is pumped from chemical storage tanks to the common water/chemical header by a metering pump. The chemical mixes with the stream of water and the mixture flows under pressure to the spray header installed at individual dust control points.
Water supply system
Plant water is generally utilised for the dust suppression system. An on-skid water pump is used to boost the water pressure to an optimum level (3 barg) as required for foam formation.
Atomising air system
Plant service air is utilised for atomising the water/chemical mix and spraying it at the right amount of pressure to capture the fugitive dust at the various installation points. The required pressure for effective atomisation is around 7 barg which is finalised during commissioning based on water flow rates. Fig. 2. Shows a typical spray pattern at an application point.
System control
A local PLC is used to monitor pressures, flow rates, and liquid levels. These parameters are used to control the water flow rate and detect anomalies such as nozzle plugging. Should any adverse conditions develop, the PLC will automatically provide system alarms to warn the system operator of the process variations outside normal parameters.
Benefits of STS
The benefits of the STS dust suppression system:
- “foam” stays with sulphur granules during transport and storage;
- minimises additional moisture content;
- minimises operating costs;
- product is applied based on actual product loading rate;
- drastically reduces adverse environmental impact;
- eliminates empty belt spraying.
The SafeFoam Transfer System skid is pre-assembled and shipped ready to be installed on site. Transportation and construction are consequently much easier as each unit arrives on site 90% assembled. This reduces not only assembly time and costs but also commissioning time; as most system checks are completed prior to shipment.
Sulphur inherently needs proper care. Due to the properties of sulphur, using a dust suppression system is the most effective way of controlling fugitive sulphur dust.
Enersul, who has been a leader in the sulphur forming and handling industry for over 60 years has had much experience in both forming and handling sulphur products and has used this knowledge to develop the SafeFoam Transfer System, one of the most effective dust suppression systems specifically targeted at controlling sulphur dust particles.
With the proper material handling procedures in place and effective implementation, the risks associated with sulphur handling can be easily managed and safe plant operations can be obtained.