Nitrogen+Syngas 366 Jul-Aug 2020
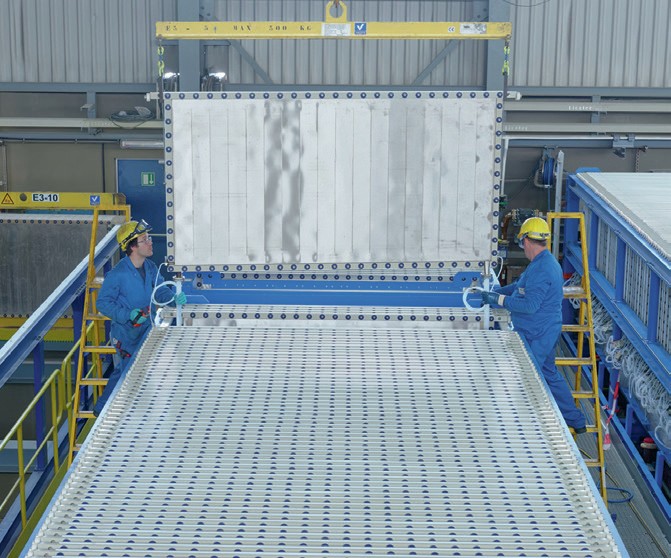
31 July 2020
Syngas News Roundup
Syngas News
UNITED STATES
Air Products and Haldor Topsoe sign global collaboration agreement
Air Products and Haldor Topsoe have signed a global alliance agreement. Under the terms of the agreement the two companies will use their combined market network for developing potential projects and the combination of their expertise on large-scale ammonia, methanol and/or dimethyl ether (DME) plants to be developed and built globally. It gives Air Products access to Topsoe’s technology licenses and the supply of engineering design, equipment, high-performance catalysts and technical services for ammonia, methanol and DME plants that are built, owned and operated by Air Products. It also allows for the integration of Topsoe’s technology into many Air Products’ technologies including gasification of various feedstocks, and synthesis gas processes.
As an example, Topsoe’s technology will be incorporated into Air Products’ recently announced world-scale coal-to-methanol production facility in Bengalon, East Kalimantan, Indonesia (see below). In addition, Topsoe technology will also be part of the previously announced world-scale Gulf Coast Ammonia production plant in Texas. Air Products will supply hydrogen and nitrogen for the ammonia production in part from its largest-ever steam methane reformer.
“The global agreement with Haldor Topsoe is very important to Air Products as we continue to expand our scope of supply to customers in developing large-scale projects around the world. We have built a reputation for successfully executing megaprojects. Having this Alliance and access to Haldor Topsoe’s technology-leading capabilities will serve to strengthen both our offerings and customer confidence in the reliability and quality of project development and performance,” said Dr. Samir J. Serhan, executive vice president at Air Products.
“We are extremely satisfied to enter this Alliance. Air Products is an industry leader, and we share their commitment to providing customers around the world with excellent, innovative, and more sustainable solutions. This alliance forms the foundation for integrated large-scale projects that will benefit from the close collaboration and combined strengths of our two companies,” said Amy Hebert, Deputy CEO and Executive Vice President at Haldor Topsoe.
MOL to provide ships for NWIW ProjectJapan’s Mitsui O.S.K. Lines (MOL) says that it will invest in the Chinese-backed Northwest Innovation Works (NWIW) methanol project in Washington State, and will provide and operate purpose-built next-generation ships to serve the planned methanol facility at the port of Kalama. The new partnership puts NWIW in the company of one of the world’s largest shipping companies, with a fleet of 740 vessels totalling 55 million dwt. NWIW is currently still bogged down in environmental permit applications for its 5,000 t/d methanol plant, which aims to convert abundant shale gas into methanol for shipping to methanol to olefins (MTO) plants in China. NWIW says that in so doing it will displace more carbon intensive Chinese coal-based methanol, bringing environmental benefits. It will also offset 100% of its greenhouse gas emissions from Kalama and use the cleanest available technologies.
Construction on hold at South Louisiana Methanol
Construction work was suspended “for an indefinite period” in April at the South Louisiana Methanol LP site in St. James Parish, Louisiana. The company said that work was halted on the $2.2 billion, 1.8 million t/a methanol plant because of the economic downturn from the coronavirus pandemic. Also said that, although it remains committed to finishing the project, it is seeking new project partners and a new debt finance package. South Louisiana Methanol is a joint venture between New Zealand-based Todd Corp. and Sabic US Methanol, the Houston-based subsidiary of Saudi Arabia’s Sabic.
AUSTRALIA
Leigh Creek Energy looking to hydrogen market
Underground coal gasification (UCG) company Leigh Creek Energy says that it is looking at commercialising hydrogen production from its in situ gasification project in South Australia, claiming that it could be the lowest cost producer in Australia, at less than A$1.00/kg H2 . The company is already looking at using syngas generated from UCG to make ammonia and downstream urea, and says that its pilot plant has demonstrated that the project can produce 200,000 t/a of hydrogen at less than $1/kg, which is “much lower than current production costs” and “cheaper than potential competitors”. The company has been monitoring the hydrogen market and governmental desire to encourage this development and said while the market has seemed “too immature” in Australia, “things are changing rapidly and the business for hydrogen now warrants further analysis”.
Leigh Creek Energy says that it validated its in-situ gasification (ISG) technology in early 2019 following the successful production of commercial syngas from its demonstration plant and announced a commercialisation plan to produce ammonia for up to 2 million t/a of urea manufacture, but added that, “If the market exists in Australia or an export market exists for hydrogen, we can divert excess hydrogen for sale as a standalone product.”
In April, Leigh Creek Energy signed an agreement with its major shareholder China New Energy (CNE) for a proposed joint venture for ISG operations in China. The company says it is also in talks with CNE’s parent company, Shaanxi Meijin about bringing its hydrogen vehicles, fuel cells and charging stations technologies to Australia.
Renewables projects looking at hydrogen storage
Infinite Blue Energy, developers of the massive $3.5 billion Project NEO renewable power project in New South Wales, says that it is aiming to use hydrogen to store excess power and turn renewable power production into 1 GW of ‘baseload’ continuous power supply by 2027. Infinite Blue Energy, which is being led by a team of executives with a range of experience previously from the oil and gas sector, said in a statement: “A traditional weakness with solar and wind energy is the variability associated with a reliance on natural seasonal changes and conditions. By converting the solar and wind energy into green hydrogen, it is possible to provide electricity when there is no wind, a cloudy day or limited to zero sun exposure at night via fuel cell technology.”
Infinite Blue Energy estimates that the project would require around 235 wind turbines, and 1,250 hectares of land for solar generation, but the company said that it would look to use high-value sites for solar and wind production, in combination with a “distributed generation model” to diversify the project’s supplies of renewable power. It says that it will begin a feasibility study and commence design work over the next 18 months and has started negotiations with potential off-takers for both electricity and hydrogen supplies.
It is only one of a number of large scale renewables to hydrogen projects under discussion in Australia. BP has also said it is considering a 1.5 GW wind and solar project in Western Australia to create renewable hydrogen, Siemens has proposed a bigger 5 GW renewable hydrogen project in the same region, and further north the Asia Renewable Energy Hub is contemplating a 15 GW wind and solar project. In Queensland, renewable energy company Austrom Hydrogen has secured land near the Port of Gladstone for a 3.6 GW solar-powered hydrogen facility.
INDONESIA
Coal-based methanol plant planned for Bengalon
Air Products has signed an agreement with PT Bakrie Capital Indonesia and PT Ithaca Resources to build a $2 billion coal-based methanol plant in Bengalon, East Kalimantan. Under the long-term on-site contract, PT Ithaca Resources will supply the coal feedstock and have committed to offtake the methanol production for sale within Indonesia. Air Products will build, own and operate the air separation, gasification, syngas clean-up, utilities and methanol production assets to produce methanol for Bakrie and Ithaca. The facility, based around Air Products’ proprietary Syngas Solutions dry-feed gasifier, will produce nearly 2 million t/a of methanol when it comes onstream in 2024.
Seifi Ghasemi, Air Products’ chairman, president and chief executive officer, said that, as Southeast Asia’s largest economy, Indonesia is committed to reduce its energy imports and efficiently convert abundant coal resources into high-value products. “We are proud to have been awarded another world-scale gasification project, where we will deploy our capital, technology and operational expertise to help Indonesia meet these important goals. This is another example of our long-term strategy to deploy capital into high-return strategic industrial gas projects,” he said.
GERMANY
Expanding electrolysis plants to a gigawatt scale
As demand continues to rise for industrial electrolysis plants which can produce ‘green’ hydrogen cost-efficiently, thyssenkrupp says that it has significantly expanded its manufacturing capacities for such electrolysis plants and can now annually produce electrolysis cells with a total power consumption of up to one gigawatt, in partnership with its strategic supplier De Nora. This production capacity is expected to be expanded in the future.
“Water electrolysis is increasingly emerging as a key technology for building a sustainable, flexible energy system and carbon-free industry. This opens up new markets for us,” said Sami Pelkonen, CEO of thyssenkrupp’s Chemical & Process Technologies business unit. Christoph Noeres, head of Energy Storage & Hydrogen added: “Especially in energy-and resource-intensive industries such as fuel, chemical or steel production, only green hydrogen opens the way to climate neutrality. For this, we need water electrolysis on a gigawatt scale. We can deliver, and as the number and size of hydrogen projects increases we will further expand our production capacities. But one thing is also clear: it won’t work without changed regulatory conditions and fair market opportunities for green hydrogen. In addition to the further expansion of renewable energies, the focus is on adjusting tax systems and crediting the CO2 -reducing effect of green hydrogen in the target markets.”
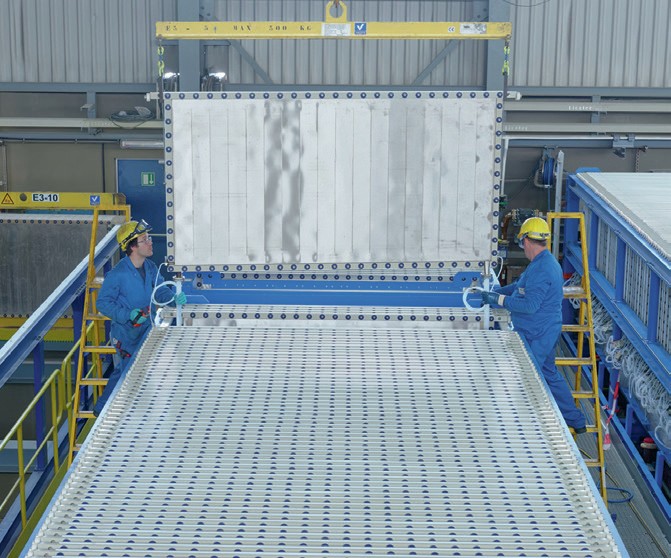
To simplify the construction of new hydrogen plants and keep costs down, thyssenkrupp offers its electrolysers as prefabricated skid-mounted modules. One module produces 4,000 m3 /h of hydrogen. The units are can be combined to realize projects of several hundred megawatts or gigawatts. The patented design of the electrolysis cells, equipped with proprietary anodic and cathodic coatings developed by De Nora, allows high system efficiencies of up to 80%, according to tkIS. So far, more than 600 projects and electrochemical plants worldwide with a total rating of over 10 GW have been installed by the company.
Hydrogen for steel production
An agreement has been signed between Rhine-Westphalia power company RWE and Thyssenkrupp Steel Europe to develop a 100MW electrolyser plant project to produce green hydrogen to supply the latter’s Duisburg steel mill. The green hydrogen will be used for pig iron production. The companies have agreed that only electricity from renewable energy sources will be used to supply the electrolyser facility.
A 100MW electrolyser, which will be built in 2022, will produce 1.7 t/h of hydrogen gas, meeting 70% of the requirements of the blast furnace at the Duisburg steel plant, leading to the annual production of 50,000 tonnes of climate-neutral steel.
RWE and Thyssenkrupp Steel Europe will establish network connections with gas network operators and relevant authorities based on their understanding that hydrogen transport via pipelines will be possible due to adaptation of natural gas transportation regulations as part of Germany’s National Hydrogen Strategy. Thyssenkrupp Steel’s aim is to be climate-neutral by 2050, which will require 750,000 t/a of hydrogen, equivalent to the annual output of over 3000 wind turbines.
FRANCE
Integrated power to hydrogen to power project
A consortium made up of Engie Solutions, Siemens Gas and Power, Centrax, Arttic, German Aerospace Center (DLR) and four European universities have contracted to develop the HYFLEXPOWER project – a way of using hydrogen to store and recover renewable power. The project, funded by the European Commission under the Horizon 2020 Framework Program for Research and Innovation, will be the first industrial-scale ‘power-to-X-to-power’ demonstrator. Incorporating an advanced hydrogen turbine, it will be built at Smurfit Kappa PRF’s site – a company specialising in manufacturing recycled paper – in Saillat-sur-Vienne, France. The purpose of the project is to prove that hydrogen can be produced and stored from renewable electricity and then combined with natural gas in ratios up to 100% to generate electricity in combined heat and power plants. For this an existing Siemens SGT-400 industrial gas turbine will be upgraded to convert stored hydrogen into electricity and thermal energy.
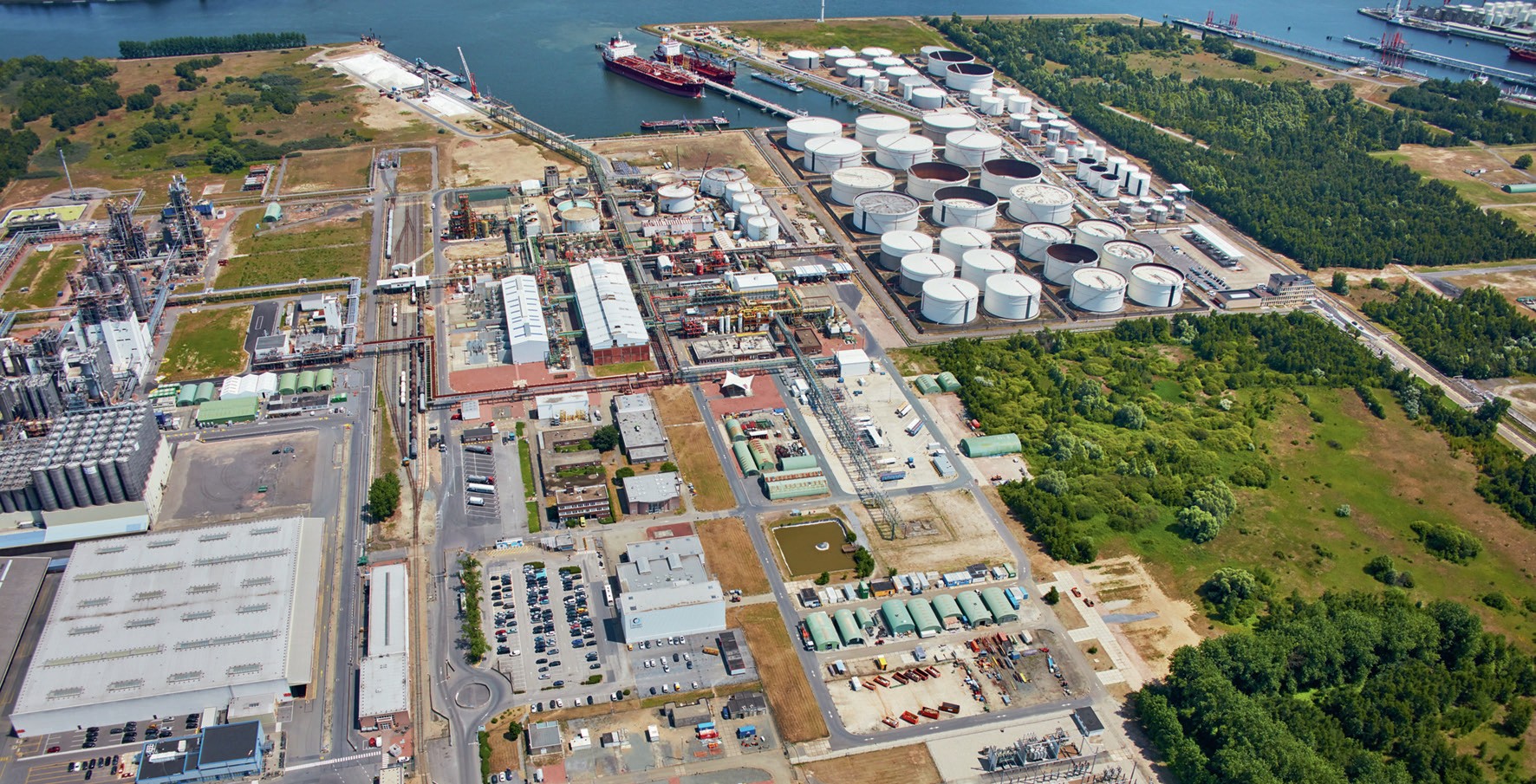
Storing fluctuating renewable energy is one of the major challenges of the transition to renewable fuels. In this context, the stakeholders involved in the HYFLEXPOWER project are developing new technologies which can be used across the whole powerto-X-to-power cycle. The installed demonstrator will be used to store excess renewable electricity in the form of green hydrogen. During periods of high demand this stored green hydrogen will then be used to generate electrical energy to be fed into the grid.
The hydrogen production storage and supply facility will be installed at the site in 2021 and the modified gas turbine in 2022. Pilot demonstrations with up to 100% hydrogen for carbon-free energy production from stored excess renewable energy are scheduled to begin in 2023.
EQUATORIAL GUNIEA
Nexant to produce feasibility study for methanol derivatives project
The Ministry of Mines and Hydrocarbons (MMH) of Equatorial Guinea, in collaboration with the Atlantic Methanol Production Company (AMPCO), has awarded Nexant the feasibility study for the construction of a new formaldehyde production plant at Punta Europa. The plant forms part of Equatorial Guinea’s Year of Investment 2020 initiative, aiming at investments across the country’s midstream and downstream industries and promoting infrastructure that adds value to the hydrocarbons industry. Key projects include a modular refinery for domestic supply, storage tanks for refined products, methanol derivatives manufacturing, an industrial mining area with a gold refinery, and a urea plant project. The feasibility study for the project is expected to be ready by mid-June 2020.
IRAN
Start-up for Bushehr
The Middle East Kimia Pars Petrochemical Company said that it began operations at its new methanol plant at Bushehr in the Pars Special Economic Energy Zone at Assaluyeh, Bushehr Province, on June 8th. The gas-based methanol plant has been constructed in 8 ha of land at the site at an estimated cost of $460 million, and will consume 1.5 billion cubic metres of natural gas per year from the South Pars gas field to produce 1.65 million t/a of methanol at capacity. Haldor Topsoe provided the technology license for the plant, catalysts and some equipment.
BELGIUM
Sustainable methanol project
INEOS subsidiary INOVYN is looking to explore options for the sustainable production of methanol for its vinyls and other downstream production at Lillo near Antwerp in Belgium. As part of a consortium including Engie, Oiltanking, Indaver, Fluxys, the Flemish Environmental Holding Company (Vlaamse Milieu Holding) and the Port of Antwerp, INOVYN is participating in a feasibility study for the use of captured carbon dioxide and sustainably generated hydrogen to produce 8,000 t/a of sustainable methanol. INEOS says that the project forms part of the company’s exploration of the potential of alternative energy and sustainable, lower carbon production of chemicals.
The new facility would generate produce methanol to be used by chemical companies in the Port of Antwerp Cluster while future development would lead to increased volumes of sustainable methanol produced for wider industry use, including as a sustainable fuel for marine and road transport.
Geir Tuft, CEO of INOVYN said: “This is a very exciting project and an excellent fit with our sustainability strategy, which includes pursuing options for alternative energy and the sustainable, lower carbon production of chemicals. Specifically, INOVYN will contribute its expertise in hydrogen production and electrolysis to the project, and has identified a suitable location for the proposed demonstration plant at our Lillo Site.”
NORWAY
Renewable aviation fuel project
Norsk e-Fuel, a consortium including Sunfire GmbH, Zurich-based carbon capture company Climeworks AG, engineering, procurement and construction (EPC) company Paul Wurth SA and green investor Valinor, which owns Norway’s largest private wind power developer Norsk Vind, has announced plans to build a commercial plant for the manufacture of renewable aviation fuel. The facility will use Sunfire and Climeworks’ technologies to convert renewable electricity into hydrogen and combine it with CO2 captured from ambient air and unavoidable CO2 sources to produce syngas, which will then be processed into renewable fuels. The plant will be built at the Heroya Industry Park in Porsgrunn, with commissioning planned for 2023. It will have the capacity to produce 8,500 t/a of renewable fuel, but there are plans to expand this to 85,000 t/a by 2026.
“To put this in perspective, only one industrial scale plant will already provide enough blended renewable fuel for the top five domestic aviation routes in Norway combined. This would effectively cut the current flight emissions between these cities by about 50%.” said Lars Helge Helvig, founder of Valinor and Chairman of Norsk Vind.
CHINA
Clariant reports on catalyst performance at hydrogen plant
Since its restart in July 2019, Zhejiang Baling Hengyi Caprolactam Co Ltd (BHCC)’s hydrogen plant at Hangzhou, Zhejiang province, has seen improved performance following a joint revamp project between Clariant and Shanghai Huaxi. Specialty chemicals company BHCC is a joint venture between SINOPEC Group and Zhejiang Hengyi Group, and runs the largest single train caprolactam plant in the world, with a capacity of 500,000 t/a. The plant’s hydrogen unit was revamped with a combination of Shanghai Huaxi’s hydrogen technology and Clariant’s stabilised copper-zinc ShiftMax 300 medium temperature shift catalyst.
Since the restart, BHCC’s hydrogen production rate has increased by 2.5% per unit of feed to 25,000 Nm3 /h. However, it is also reporting 32% lower electricity consumption and 44.4% higher steam production, with reduced capital investment, as no mechanical structures are required for the waste heat boiler. Furthermore, using ShiftMax 300 it is possible to recycle all condensate water and steam generated in the stripper as boiler feed water to reduce energy consumption. BHCC says that it expects to accrue total annual savings of around $1 million.
Clariant says that ShiftMax 300 operates at a low steam-to-dry-gas ratio of 0.31 mol/mol, with high activity at low temperatures (185°C), allowing sustained operation at high space velocities, close to equilibrium. Stefan Heuser, Senior Vice President & General Manager at Clariant Catalysts, commented, “We are extremely pleased with the results of our partnership with Shanghai Huaxi at the BHCC hydrogen unit. Our two companies’ perfectly complementary products and processes have demonstrated that they can successfully maximise our customer’s total hydrogen production, while drastically reducing costs.”
TRINIDAD & TOBAGO
Methanol plants idled, delayed
Proman says that the M3 methanol plant at Point Lisas, Trinidad has been idled since mid-April due to falling methanol prices. Proman is one of the partners in Methanol Holdings Trinidad Ltd (MHTL), which operates the M3 plant. This was followed in May by the M2 methanol plant at the same site. They are two of several shutdowns on the island. Canada’s Methanex, the world’s largest producer of methanol, idled its 850,000 t/a Titan plant on the same industrial estate on April 1st for an “indefinite” period.
Meanwhile, across the island at La Brea, the new methanol and dimethyl ether (DME) project under construction by Caribbean Gas Chemical Ltd (CGCL), a 70% owned subsidiary of Mitsubishi, remains behind schedule as a result of regulatory delays, industrial action, heavy rains in 2017 and 2018, and issues with some contractors, as well as the Covid-19 outbreak. The $1 billion plant, originally scheduled to be completed in December 2018, has a capacity of 1.0 million t/a of methanol and 20,000 t/a of DME. It was close to mechanical completion in March when Trinidad went into Covid lockdown, and is now expected to start-up in the second half of 2020. As well as the Mitsubishi consortium (Mitsubishi Gas Chemical, Mitsubishi Corporation and Mitsubishi Heavy Industry), CGCL’s shareholders include the National Gas Company (NGC), with a 20% stake; and Massy Holdings (10%).