Fertilizer International 498 Sept-Oct 2020
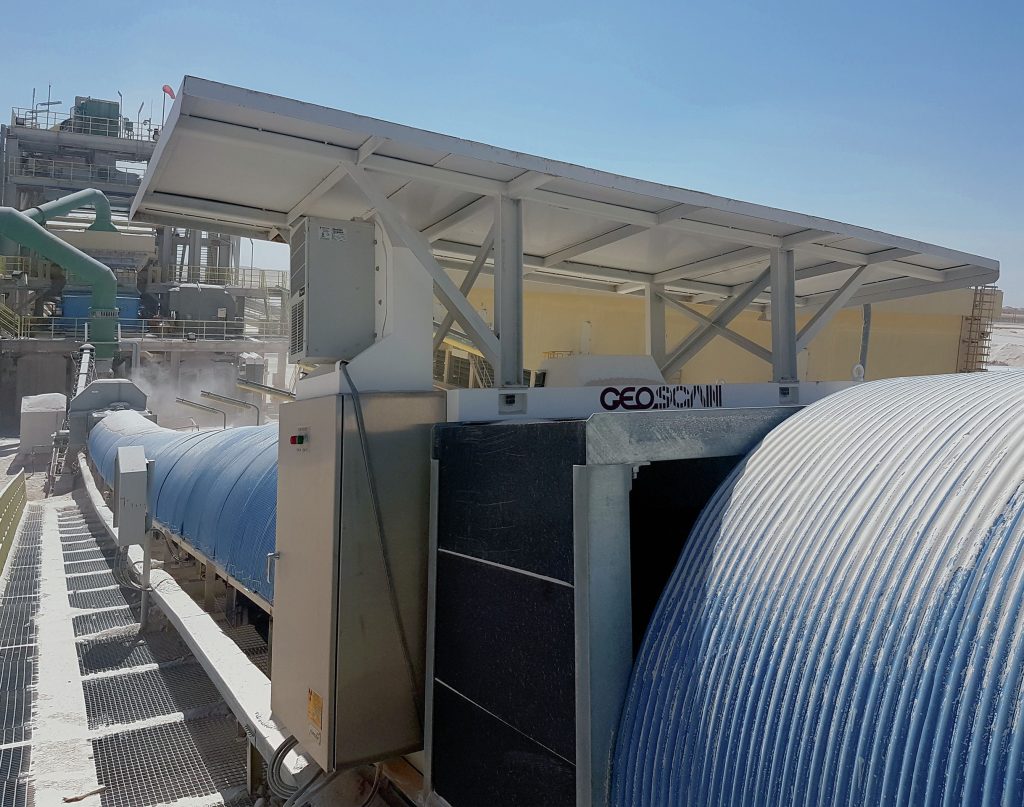
30 September 2020
Phosphate process analysers
PROCESS CONTROL TECHNOLOGY
Phosphate process analysers
Sophisticated control of phosphates production is now possible thanks to the availability of real-time process analysers. We assess the range of technologies currently on the market and their key advantages.
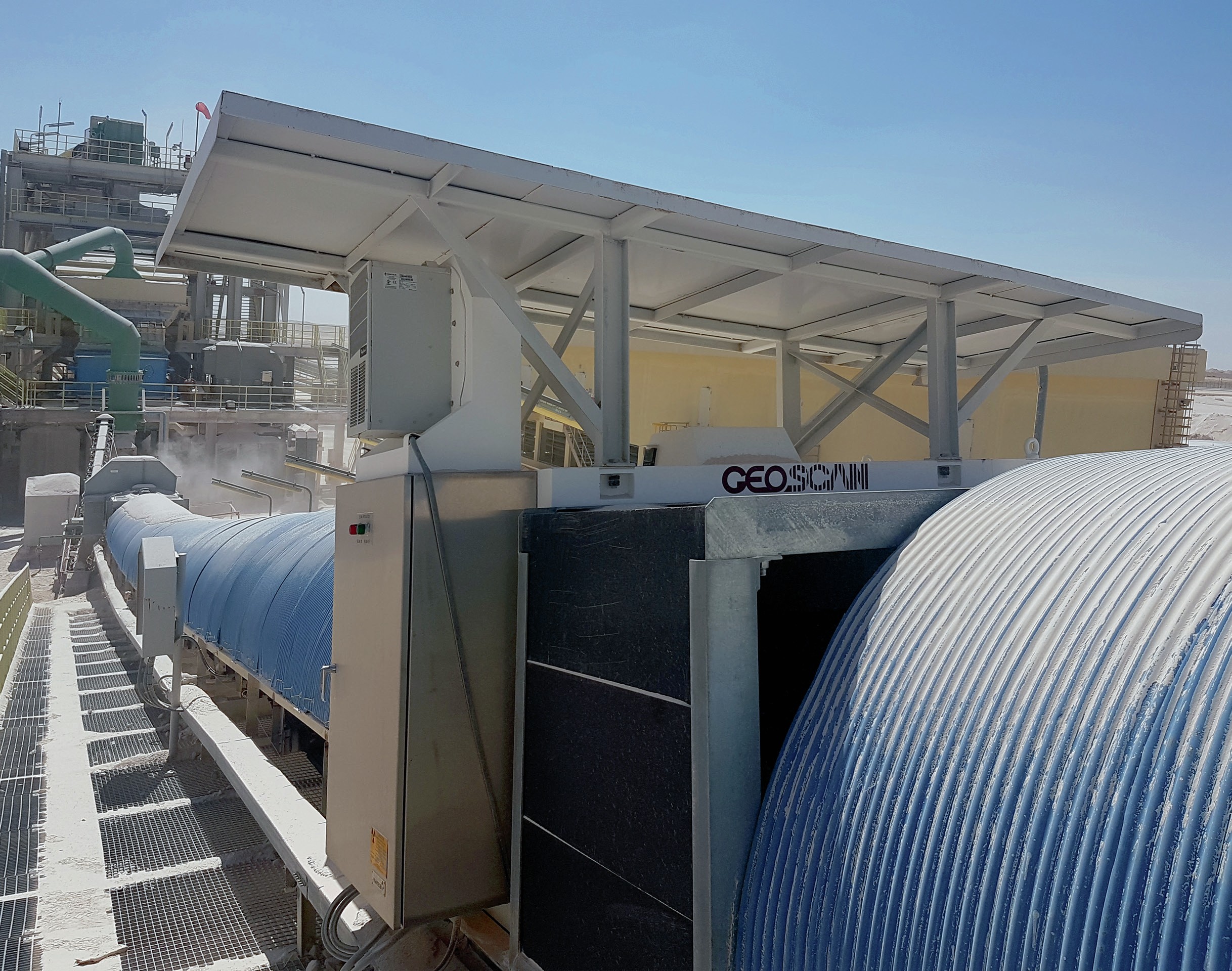
It’s been a challenging 12 months for phosphate fertilizer production, particularly in North America. At a market low point towards the end of last year, high inventories and weak prices in the region led to production cuts of 650,000 tonnes a month. Some producers were still reporting significant operating losses in the second-quarter of 2020. While gross margins per tonne – a crude measure of phosphate production economics – have recovered, they had fallen into negative territory earlier in the year.
Realised prices on products have been depressed too. The current diammonium phosphate (DAP) price is flat year-on-year at $329/t (Tampa f.o.b.), and down about one-fifth on the start of 2019, a recent highpoint.
Driving down production costs
This challenging environment means that there is more pressure than ever – and an economic imperative – for phosphate producers to cut their operating costs. This, in turn, requires a much greater degree of process control.
But fine tuning the phosphates production process remains problematic. Traditional laboratory methods for analysing the grade (P2 O5 content) of mined phosphate rock, concentrates and chemical plant feed materials are time-consuming and labour intensive. The length of time taken between sample collection and the delivery of results also limits their usefulness in process control at phosphate mines and plants. Infrequent and intermittent sampling also means that lab test results are not always representative. Because of this, lab-based analysis is only able to provide a fragmented, incomplete picture of the production process.
Typically, phosphate fertilizer producers can only rely on getting lab results every 4-6 hours, meaning that process stages such as phosphate rock mining, froth flotation and phosphoric acid reactors are effectively flying blind when it comes to P2 O5 feed control.
It is therefore unsurprising that phosphate plant operators are increasingly adopting automated on-line technologies for process and feed control These generate results rapidly, often in near real-time, and deliver tangible benefits in terms of improved phosphate plant efficiency and yield.
They can also deliver surprisingly quick returns on investment. For a typical beneficiation plant, an improvement in P2 O5 recovery of just two percent, for example, can deliver annual savings of half a million dollars, according to some calculations.
Three proven types of automated analytical systems for process control in the phosphates industry are reviewed below.
Nuclear magnetic resonance
Massachusetts-headquartered LexMar Global is the world’s leading provider of Nuclear Magnetic Resonance (NMR) analysers for process control. Within the industry, these installations are commonly called Industrial Magnetic Resonance (IMR) systems.
The company has installed more than 400 analysers globally in 45 countries, and operates regional service centres in Belgium, Texas, Morocco, Abu Dhabi, and China. Phosphate industry customers include major players Ma’aden, Mosaic, Nutrien and OCP, as well as chemical and oil giants such as ExxonMobil, Dow and Borealis. The company supplies other markets including polyolefin resin manufacturing and mining.
LexMar Global produces the MagModule II IMR analyser for on-line process measurements on phosphate slurries. These are supplied with either multiplexer or metallurgical sampling systems. The advantages of NMR technology include:
- Direct analysis of phosphate content – as either weight percentage Ca3 (PO4 )2 (BPL, bone phosphate of lime) or P2 O5
- Powders, pellets, slurries and liquids can all be measured
- Non-destructive, rapid analysis with results in less than five minutes
- Stable calibration – no routine re-calibration required
- No sample preparation necessary
- Analysis is independent of particle size
- Robust instrumentation with rugged industrial design and construction
- Avoids use of radioactive materials.
MagModule II on-line phosphate analysers can be installed at different process stages. Units can be placed at the beneficiation stage, to monitor and help regulate froth flotation, further downstream in acid reactor feed control, or upstream in mining operations. The benefits of this include:
- Greater P2 O5 recovery with consequently better usage of phosphate rock reserves and less wastage
- Increased plant efficiency and higher production rates
- Lower production costs
- Avoidance of contract penalties.
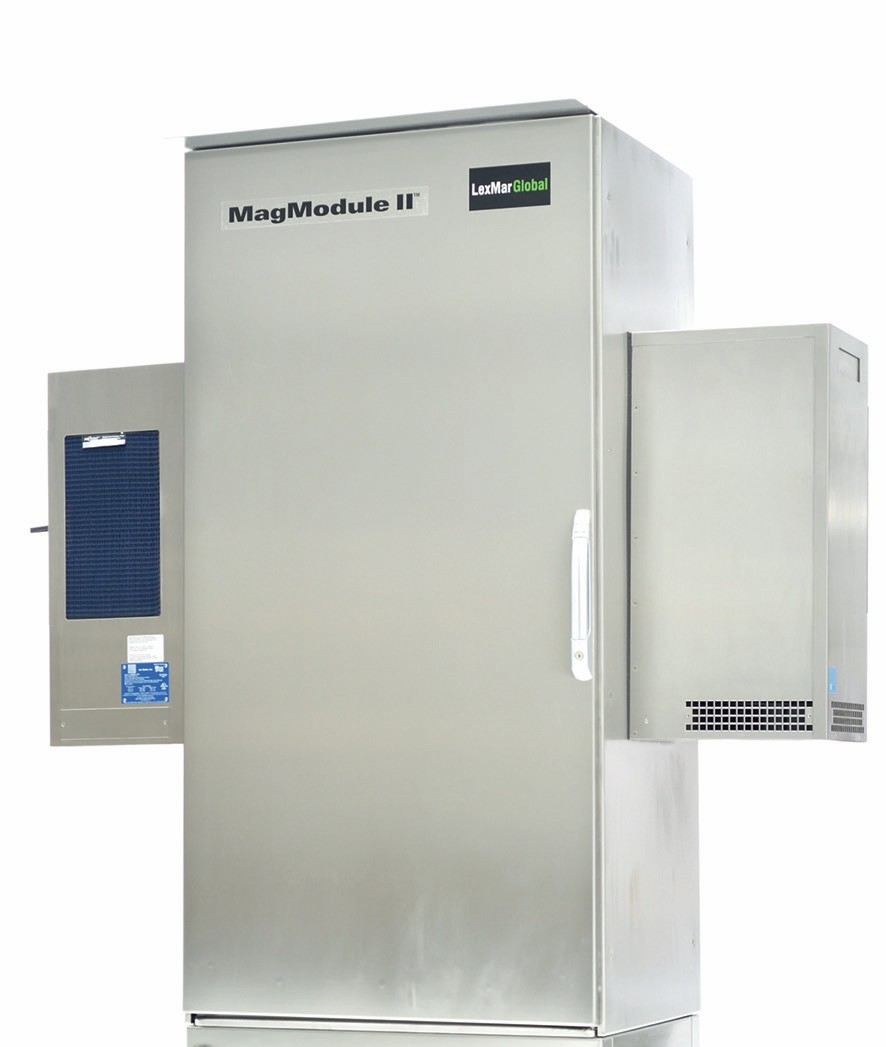
Samples are collected for analysis using either a metallurgical sampler or a multiplexer. Coupling the analyser to an automated multiplexer is advantageous as it allows a single analyser to take routine measurement from multiple sample points without interrupting operations.
IMR technology is capable of delivering comparable, consistent results. Analysers are calibrated for P2 O5 content by comparing IMR results with laboratory reference measurements over a range of different phosphate compositions. According to LexMar Global, IMR calibrations are intrinsically more stable than those required for alternative techniques such as X-Ray fluorescence (XRF) or prompt gamma neutron activation analysis (PGNAA).
One of the main benefits of on-line IMR analysis is that it allows more timely process decisions to be made which, in turn, leads to more consistent product quality. The resulting process improvements can deliver large annual savings and rapid payback.
“Improved process control is the primary benefit of incorporating on-line analysers into your plant,” explains Dr Olaf Kohlmann, LexMar Global’s NMR product manager and strategist. “On-line magnetic resonance will give you phosphate concentration readings within a few minutes. Having real-time information about the process status 24/7 allows the engineers to optimize production for a plant.”
He adds: “Even if you could only improve P2 O5 recovery by one single percent, the payback is significant, and the lifespan of your reserve is improved. The amount of material moving through your process decreases. Efficiency, production costs, opex, will all start to go in the right direction.”
IMR analysis of conveyor belt feeds provides continuous real-time information on the grade (BPL) of phosphate rock, enabling precise quality control at the very start of the process. It also helps reduce rock waste.
In froth flotation, IMR analysis again provides real-time BPL data for flotation feeds, concentrates and tailings, improving P2 O5 recovery during beneficiation and preventing the over- or under-application of flotation chemicals. When combined with an automatic multiplexer, MagModule II has the ability to sequentially sample from and analyse up to four different process streams.
IMR on-line analysers can also be installed further downstream at the reactor stage in the phosphate production process. Using the technology to monitor feedstock helps optimise reactor control and improves P2 O5 recovery and efficiency. Other tangible benefits include reduced production costs and improved product quality and consistency.
The installation of IMR on-line analysers provides rapid payback on investment and delivers long-term profits, according to LexMar Global, even if P2 O5 recovery is improved by just a small percentage, due to the operating cost reductions achieved and longer mine life.
The growing need for mining industry automation will open up even greater opportunities for on-line analysis in future, in Dr Kohlmann’s view. “As limited global reserves are expended, but demand increases, innovative process optimisation techniques and refinement efficiencies will become increasingly necessary to compete in the global market,” he concludes.
Prompt gamma neutron activation analysis
Prompt gamma neutron activation analysis (PGNAA) is a proven on-belt technology used for the real-time monitoring, bulk sorting and blending of ore materials on conveyors.
The Geoscan range of on-belt PGNAA analysers developed by Australia’s Scantech International have been widely-used for the monitoring of bulk industrial materials such as cement, coal and minerals for more than two decades. The Geoscan-M analyser is suitable for ore and concentrate analysis in the minerals industry, and enables operators to measure and control feed and product quality. There are more than 100 Geoscan analysers installed and working in mining and processing plants worldwide, including iron ore, manganese, zinc-lead, bauxite and copper operations, with more than 20 units operating in the phosphate sector.
The Geoscan-M is installed directly on the conveyor system, with the belt passing through the instrument’s analysis tunnel (see photo). Its compact design uses only one metre of belt space, enabling it to be fitted between standard idlers. One of three different frame sizes can be selected to suit any conveyor with belt widths up to 2.4 metres and bed depths up to 0.53 metres. All material that passes through the analysis tunnel is continuously analysed and reported for a truly representative analysis. Being a fully penetrative analysis technique, it avoids the issues associated with surface analysis methods.
Geoscan-M installations emit neutrons from a californium-252 source located below the conveyor. These are absorbed by elements present in the material being conveyed, with each element emitting a unique gamma ray spectrum. The resulting spectra are monitored by proprietary detector array located above the conveyor, and processed to provide independent multi-elemental analyses (Si, Al, Fe, Ti, K, Mn etc.). The Geoscan unit then reports these to the plant – typically every two minutes – where they are interpreted to make process decisions. Results are combined with microwave measurements which detect and report moisture content.
The main applications and benefits of PGNAA in phosphate mining and processing include:
- Measuring beneficiation feed quality for plant control
- Sorting phosphate rock received at chemical plant stockpiles
- Blending to improve feed quality and meet specification
- Blending acid reactor feed
- Controlling sulphuric acid additions to the acid reactor, based on phosphate rock feed chemistry, to maximise P2 O5 recovery, recover Ca to gypsum, and optimise acid consumption.
“After notching up numerous successful installations in a variety of sectors of the minerals industry, we turned our hand towards the phosphates sector in the early 2010s,” comments Scantech’s Dr Luke Balzan. “After testing in our factory in Adelaide, Australia, we deployed our first Geo-scan in the phosphate industry in 2014. Consequently, we were the first supplier to successfully yield positive process control outcomes and deliver excellent and reliable analysis results. From there, we’ve been able to work in all the major phosphate markets globally, with more than 20 phosphate installations contributing to our total of more than 1,200 analysers worldwide”
He continues: “One of our Middle Eastern customers, as a result of having a Geoscan installed close to the front end of their process, has been able to obtain greater plant stability – and reduce the costs and delays associated with laboratory analysis. The delivery of results every two minutes has enabled the site to make process control decisions in real time.
“One of our American customers has an installation on the feed to their chemical plant – so they’ve been able to use Geoscan data to increase their yield by actively controlling their acid reactor process, as well as controlling what gets fed to the plant. Geoscan has therefore enabled them to make some very significant gains in production.”
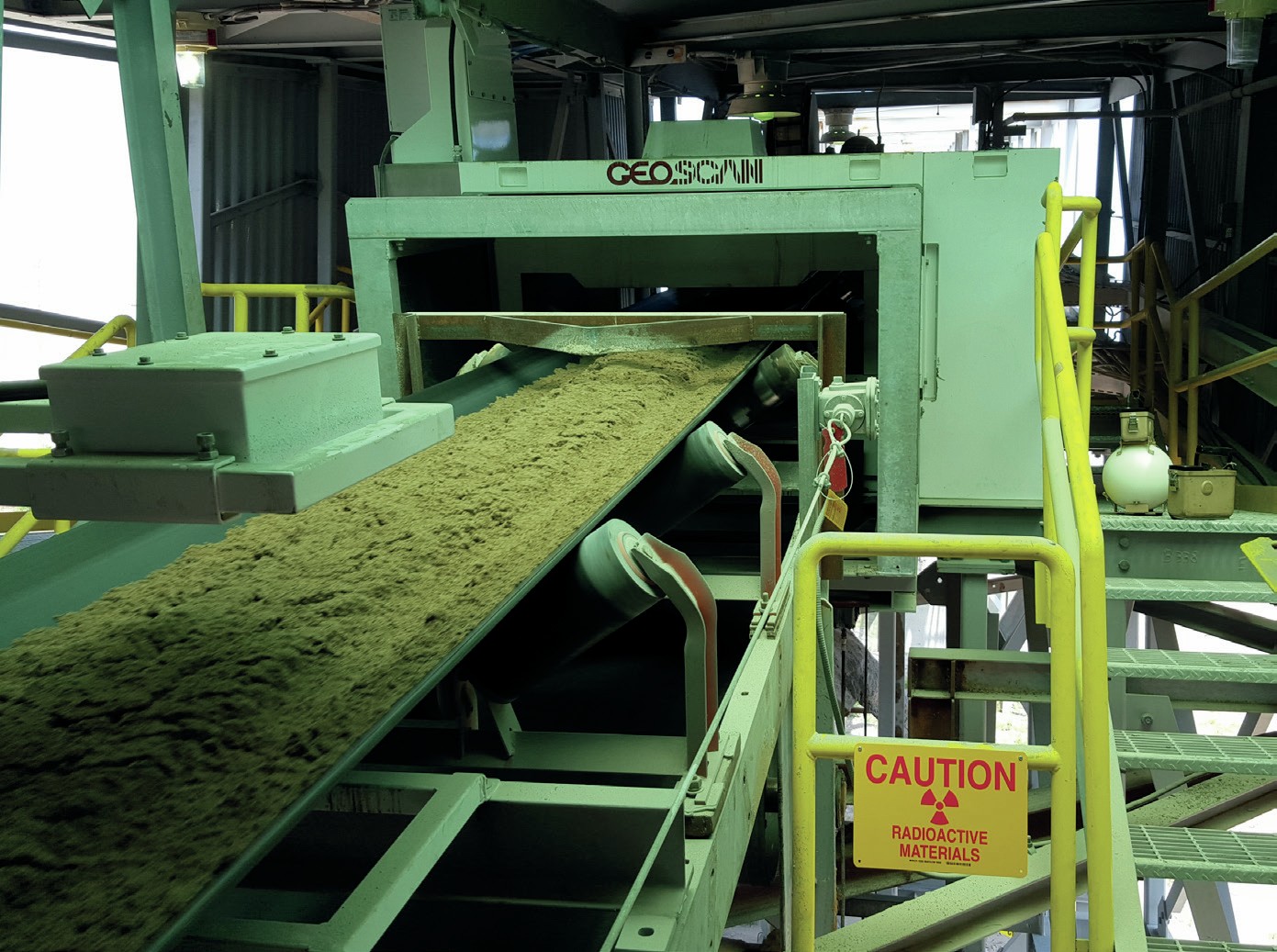
Such process improvements and production cost reductions are not widely publicised.
“Obviously, our customers like to keep what they’re doing close to their chest!,” comments Dr Balzan. “But they really do see a competitive advantage with PGNAA. We’re simply pleased that our extensive past experience in minerals, as well as our focus on customer service and support, has enabled the phosphate sector to make such gains.”
PGNAA offers a number of advantages for on-belt analysis, suggests Scantech, relative to other on-line methods:
- Comprehensive measurement: across the full cross section of the belt continuously, 6 monthly standard calibration checks, accuracy improves as more material is measured
- Deep penetration: through the entire bed depth
- Large-scale sampling: tonnages limited only by belt size and depth (~17,000 t/h)
- Reliable analysis: no mineralogy or matrix effects (Ca, Fe), unaffected by layering, particle-size, dust and belt speed
- Low maintenance: solid state components, low cost, non-contact, remote units.
PGNAA technology has also been developed for slurry analysis by San Diego-headquartered SABIA, Inc. The company manufactures two types of on-line analysers. ‘On-belt’ analysers continuously measure the elemental composition of bulk material on a conveyor, while ‘on-pipe’ analysers are mounted around a slurry pipe to continuously measure the complete slurry stream.
Both types of PGNAA analyser have been installed by major North America phosphate producers (see box). Two of the SABIA’s Model X1-XP Slurry Analysers, for example, have been successfully installed at JR Simplot’s Vernal phosphate beneficiation plant in Utah (Fertilizer International 477, p52).
Both PGNAA analyser types perform full stream, continuous, on-line multi-elemental analysis. This penetrates the material flow for a completely representative analysis without the need for frequent sampling or multiplexing. This non-intrusive multi-elemental analysis allows operators to simultaneously monitor elements of interest and see percentage composition changes/trends in essentially real-time.
The technology is uniquely suitable for high throughput (t/h or kg/m3 volumes) and fast flowing (m/s) bulk materials. SABIA analysers have no moving parts and are easy to install. Their integrated electronics only require two cables – for power and network access.
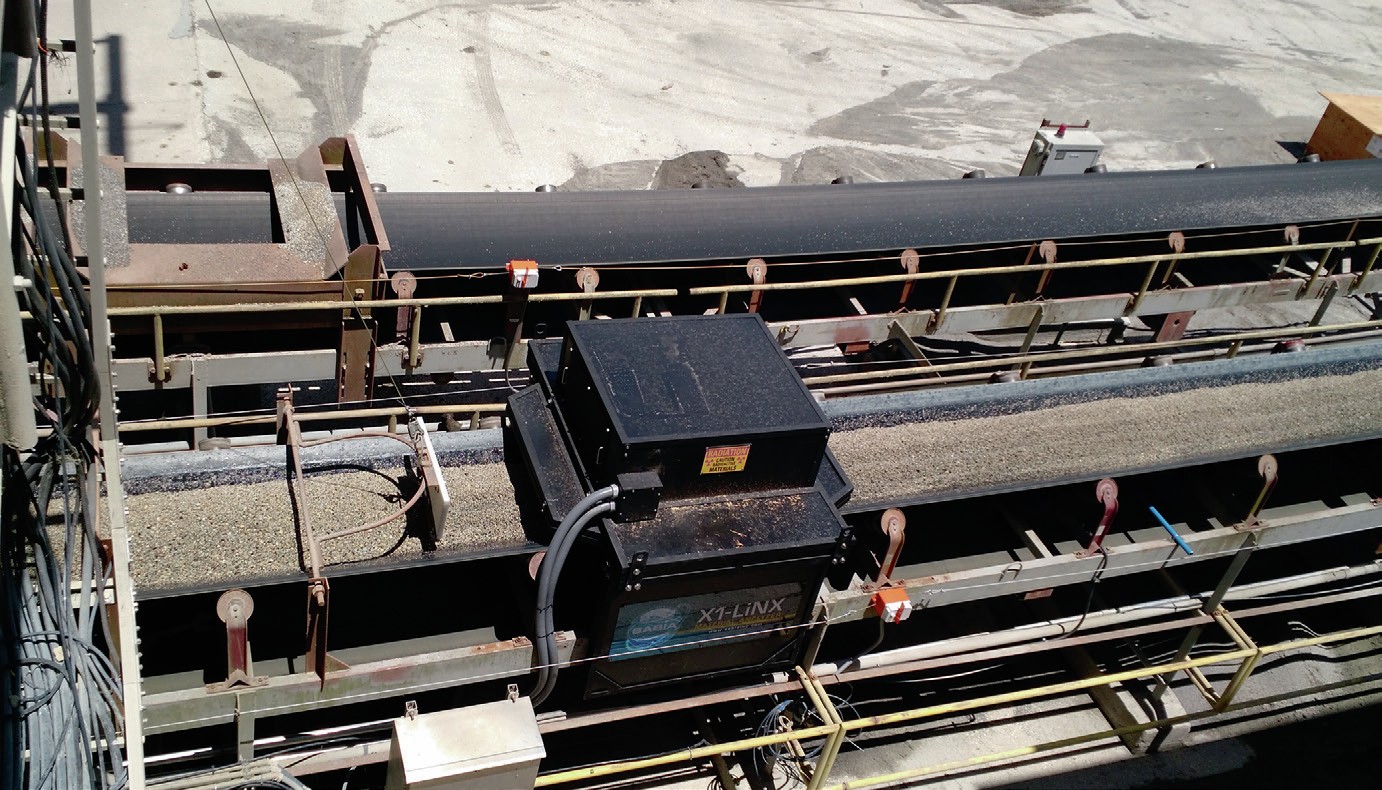
Spotlight on PGNAA applications
Major phosphate producers in North America have installed SABIA’s PGNAA analysers in the following applications:
Beneficiation feed tuning
The analyser is located on 12-inch slurry pipe discharging into a flotation feed surge tank ahead of the primary flotation de-sliming circuit. Continuous measurement of P2 O5 and MgO allows incoming feed grade monitoring and quick validation of downstream control decisions. Operators can adjust the primary flotation circuit to increase grade by slowing down the incoming feed rate and fine-tuning reagent control.
Final product validation
The analyser is located on an 8-inch slurry pipe after sizing and thickening. The MgO content of the final concentrate is continuously monitored and compared with quality targets. The challenge for this specific ore body is liberating P2 O5 , but without over grinding as this liberates MgO-containing dolomite and contaminates the phosphate concentrate. Continuous online analysis allows quick validation of upstream process decisions to keep the concentrate on target. PGNAA measurement reduces control response validation to 90 minutes, down from 12 hours for conventional sampling and lab analysis. Maintaining a final product target for MgO (<0.80%) eliminates the reaction and filtration issues associated with high MgO content at the final product processing plant.
Run of mine (ROM) pebble sorting, first example
The analyser is placed, after the mechanical sampling system and before the shuttle belt feeding bins, for diverting waste. The main aim is sorting and separating high MgO compositions in batch runs. MgO content typically varies from 0.5-7.0 percent, with 2-3 percent being an ideal range.
Run of mine (ROM) pebble sorting, second example
The analyser is located after a mechanical sampling system and before two piles. Continuously measuring percentage MgO allows sorting between the low and high concentration piles. Grade variations are bimodal with MgO levels holding consistently for extended periods of time at either one or four percent. The main aim is to quickly detect the switchover (bimodal transition) from low to high MgO. For these sorting decisions, using a five-minute rolling average of the MgO measurement provides greater statistical certainty.
Many global phosphate producers are considering installing PGNAA to optimise their downstream processing, improve mine grade control, and carry out stockpile blending more expertly. The range of applications includes:
- Run of mine (ROM) bulk sorting
- Stockpile reclaim analysis
- Monitoring of washed phosphate stockpile
- Mine loadout tracking for trains or trucks.
A number of additional applications are also under evaluation:
- Fertilizer feed acid blending
- Food-grade purified acid monitoring
- Carbonate concentrate/tailings
- Low-grade kiln feed
- Beneficiation recovery
- Flotation final products
- Chlorine/water balance
- Blending/reagent control in flotation cells.
Laser-induced breakdown spectroscopy
Laser-induced breakdown spectroscopy (LIBS) has been developed for monitoring and control applications in mining and mineral processing. One advantage of LIBS is its ability to detect and measure light elements, unlike conventional analytical techniques such as XRF analysis. The technology can be installed to analyse dry granular materials on conveyor belts or slurry materials.
Outotec launched its Courier 8 SL LIBS-based analyser in 2013 for on-line measurement of elemental concentrations in beneficiation plant feed, tailing, and concentrate slurries. According to Outotec, the benefits of using LIBS for on-line analysis of slurries include:
- Accurate monitoring of changes in feed mineralogy
- Improved control of concentrate quality
- Improved recovery through early detection of process disruptions
- Reduced need for time-consuming and labour-intensive manual sampling
- More efficient use of energy and raw materials.
Phosphates processing and concentration is one of the main target markets for the Courier 8 SL. Its applications include:
- Final concentrate quality control: measurement of P content and Ca/P ratio
- Flotation recovery optimisation and reagent control: measurement of P in feed, concentrates, and tailings
- Measurement of ‘penalty’ elements: Mg and Si.
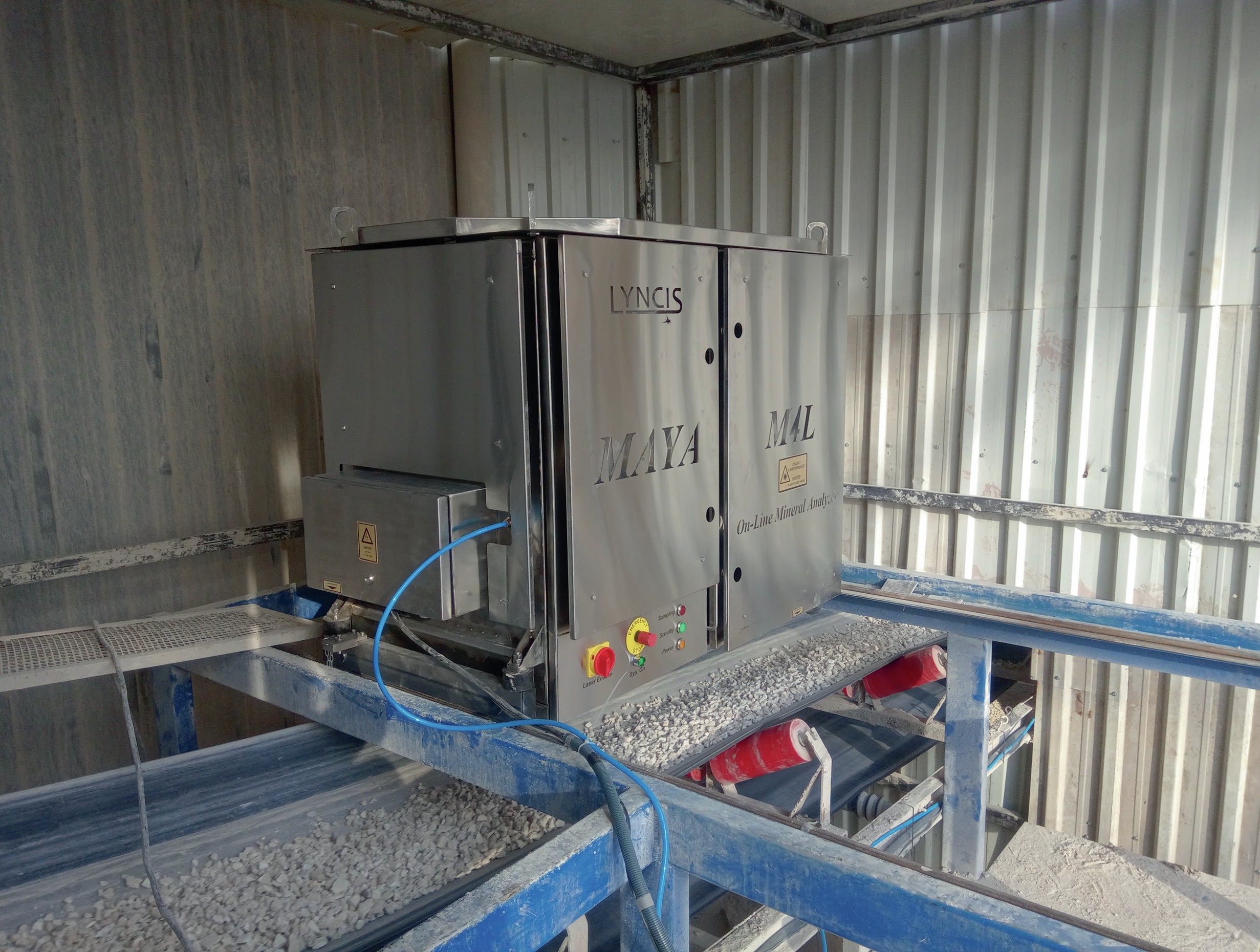
The MAYA on-line laser analyser, a LIBS-based system manufactured by LYNCIS, provides direct, safe, efficient and accurate elemental analysis of phosphates and potash on conveyor belts.
LYNCIS has extensive experience of developing LIBS analysers for mining and industrial applications. The company has direct access to the latest innovations, being headquartered in Lithuania, one of Europe’s biggest hubs for laser, optical and spectral technologies.
MAYA analysers come equipped with state-of-the-art optical systems and can accurately report phosphate content as either BPL or P2 O5 . They can also successfully detect and measure Al2 O3 , SiO2 and other undesirable impurities in phosphate rock and process feed.
LIBS-based analysers manufactured by LYNCIS have been installed by two leading fertilizer companies, the US phosphates producer Mosaic and Russian potash producer Uralkali. These provide real-time elemental analysis for process monitoring and control.
MAYA analysers have the following applications in phosphate and potash production:
- Controlling ore quality based on elemental analysis (K, Na, P, Ca, Mg, Fe, C, etc.)
- The regulation of flotation reagent dosage and water, according to the quality of the ore, resulting in increased P2 O5 recovery
- Determining the content of insoluble precipitates
- Controlling final product quality.
Having compositional information for the phosphate rock feed prior to beneficiation is particularly valuable, suggests LYNCIS, as it makes early and timely process interventions possible. These can improve production outcomes and save on operational costs. MAYA analysers offer safety, simplicity and low cost of ownership, according to the company, by ensuring high performance conveyor belt measurements based on robust calibration.
The first MAYA analyser in the phosphates industry was sold to US producer Mosaic in 2008. This unit was installed for continuous control of the ore feed quality by discarding high MgO rock (> two percent MgO pebble content). For this installation, calculations suggest that using instantaneous LIBS measurement to reject high MgO rock, rather than the delayed results of laboratory analysis, could potentially improve plant profitability by $5.9 million. This estimate was based on a production level of 1.9-2.0 million tonnes and other pricing and technical assumptions. These cost savings are partly delivered by lowering the water and flotation reagent consumption required in the beneficiation of high MgO ore.