Nitrogen+Syngas 367 Sept-Oct 2020
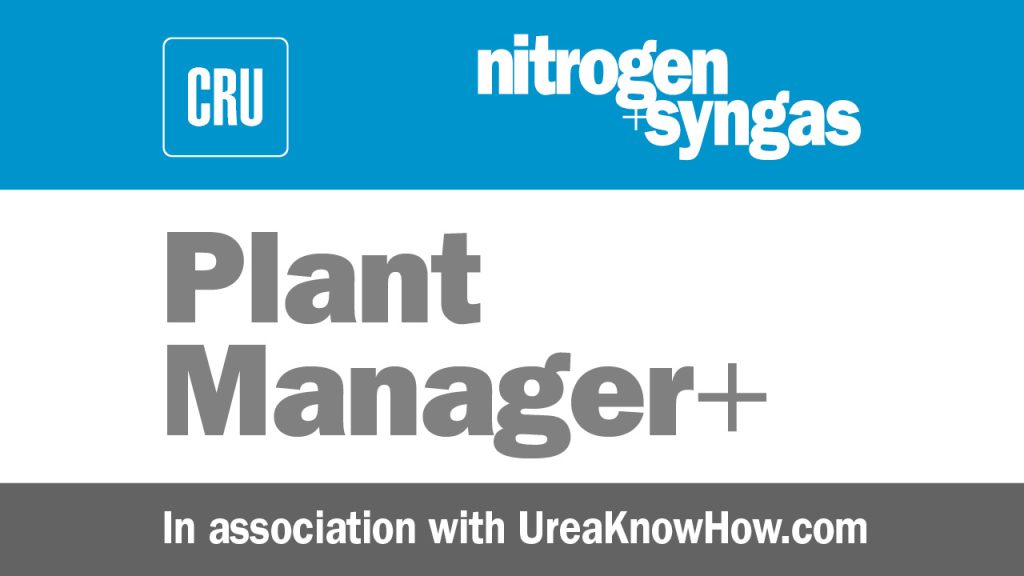
30 September 2020
Incident No. 2: Leak in weld overlay in urea reactor bottom
The following case study reports on a serious incident in a urea plant where a leak in the weld overlay in the urea reactor bottom resulted in a costly plant shutdown and near miss of rupture of the high pressure vessel. It is known that carbon steel can corrode with rates of 1000 mm/year not taking into account erosion due to flashing. The impact of the NH₃ / CO₂ ratio on the corrosion rate is questionable.
The following prevention measures are suggested:
- Perform corrosion inspections during turnarounds (measure weld overlay thickness).
- Apply proper design of inlet nozzle devices to assure sufficient saturation of liquid with oxygen and avoid high velocities (erosion corrosion) and condensation corrosion (in case of 316L UG).
- Apply higher alloy materials for overlay welding such as 25-22-2 or (super) duplex.
- During operator plant tours look for potential leaks of overlay welding in HP equipment.
Event description
Operators noted a leak (first fumes, then large quantities of solution) in the bottom forged head of the urea reactor in a conventional technology 1,000 t/d urea plant from 1969.The incident happened four months after an inspection during a turnaround. The plant was running stable at 95% load. A hole of 38 mm X 6.4 mm was found with no signs of bulging or deformation visible on the outside. Four other corroded areas of 20 to 50mm in depth were also found.
Immediate response action
The plant was shut down when the leakage was identified. The reactor bottom forging was repaired (rewelded) and overlay welding was performed with Thermanit 19/15 H electrodes. A Japanese fabricator was involved in the repair and future corrosion inspections.
Causes
Since the weld overlay metal is less resistant to corrosion, the combination of heat of reaction and high flow velocity over the ten years of service, aside from any possible upset in the control of the residual O2 and the NH3 /CO2 ratio, must have resulted in a gradual thinning of the overlay until in some areas, it was gradually consumed making the carbon steel totally exposed, which then corroded at an accelerated speed in a very short period. The reactor was inspected every turnaround but it seems only visually. The carbamate and ammonia feed nozzles were replaced.
Consequence
Near miss of rupture of high pressure vessel and a shutdown of 18 days costing US$ 1 million.
Urea reactor design
The urea reactor, from a Japanese manufacturer, is designed to operate at 280 kg/cm2 and 204°C and was operating at 226 kg/cm2 and 196°C. The plant operating data at the time of the incident was 219 kg/cm2 , 194°C, 1.7 ppm Fe and 2500 ppm O2 . The reactor has a diameter of 1.52 m and length of 27.43 m. The bottom forging is 83-94 mm thick − A212 Gr.B FBQ Class P 1 (ASME A-515, Gr.70, C = 0.31 max.). The stainless steel weld overlay was deposited using E-316L welding rods. The bottom forging has three 108 mm diameter nozzles located 60° apart feeding ammonia, carbon dioxide and carbamate respectively with a stainless steel baffle plate umbrella over the three nozzles.
Risk level
The likelihood of a major consequence was moderate but the risk level was high.
Prevention safeguards
Corrosion inspections should be carried out during turnarounds.
Mitigation safeguards
In case of a leak, confirm and locate the leak, shut down the plant and drain the synthesis section as soon as possible.
Possible causes
- 50 mm distance of deflector umbrella to overlay welding is too small risking erosion corrosion and/or condensation corrosion. Note that NH3 and CO2 form carbamate releasing a lot of heat. Typically a mixer is applied.
- E316L overlay welding.
- Influence of bottom flange weld.
- Besides visual inspections, were thickness measurements also performed during the turnaround?
Weld overlay thickness measurement Weld overlay thickness measurement is performed with a Duals-cope/Permascope using magnetic induction. It is only possible on Austenite materials (316L/25.22.2) with a ferrite content of less than 0.6%. However, it gives deviating readings when the overlay gets thinner (<6 mm) due to the presence of ferrite in first layer. The layer thickness reading does not define the layer of the real corrosion resistant part. The material used for the first layer is 309 type, with PWHT after the first layer.
When layer becomes thinner make use of a calibration block and use the ferritescope.
Drill a hole in the overlay and etch − the transition will be visible and the layer can be measured.
This case study report is one of many serious incident reports on UreaKnowHow.com’s Fertilizer Industry Operational Risks Database, FIORDA, which has been created for collecting and sharing process safety and reliability information among participating companies in the fertilizer industry.