Sulphur 390 Sept-Oct 2020
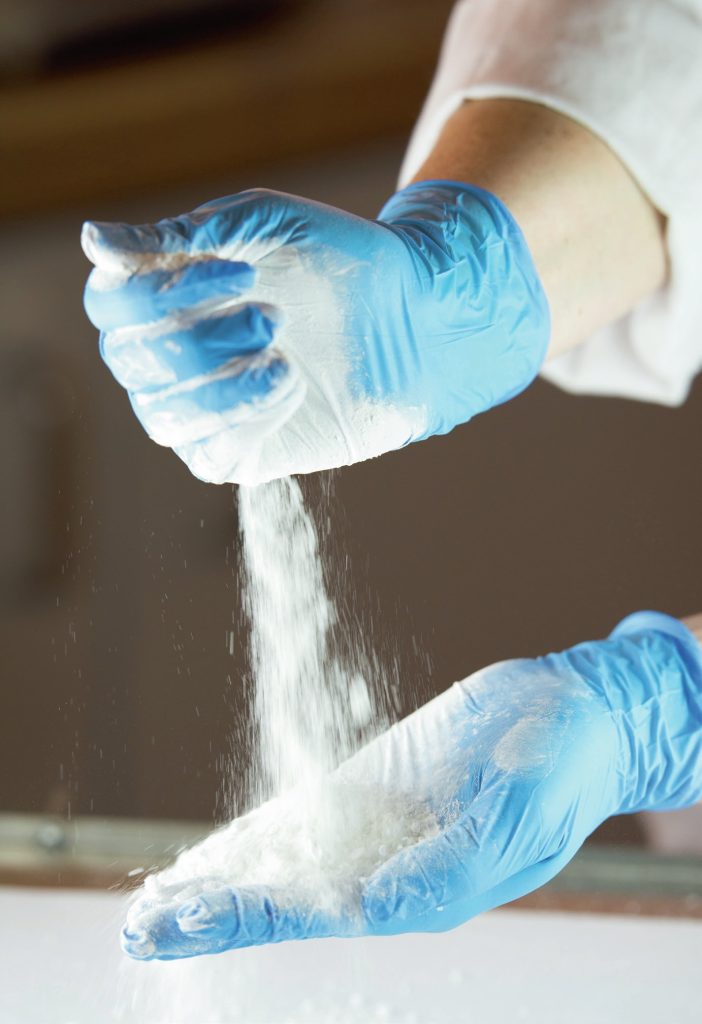
30 September 2020
Sulphuric acid in the titanium dioxide industry
TITANIUM DIOXIDE
Sulphuric acid in the titanium dioxide industry
Reg Adams of pigments and titanium dioxide consultancy Artikol reviews the demand for sulphuric acid in the manufacture of TiO2 , and the prospects for consumption over the next few years.
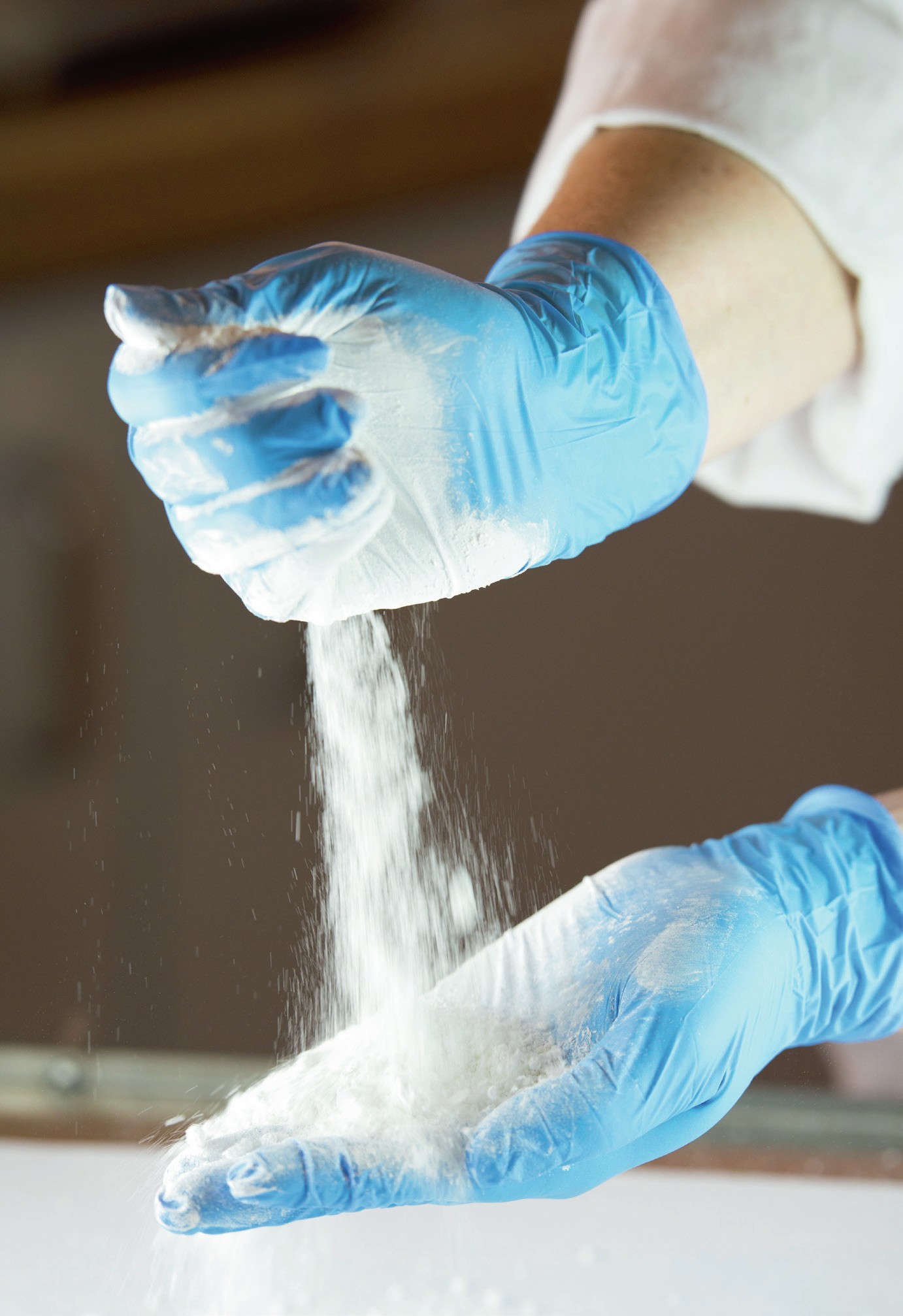
Nearly 15 million tonnes of sulphuric acid (as 100% H2 SO4 ) were used for the manufacture of titanium dioxide (TiO2 ) last year. China’s TiO2 manufacturers accounted for about 77% of the total, while TiO2 manufacturers in the rest of the world accounted for 23%.
Thanks to its high refractive index, its light scattering ability and its relative chemical inertness, TiO2 is unrivalled as an opacifier and as a white pigment. In addition, TiO2 has certain properties which make it extremely suitable as an ultraviolet absorber (for sunscreens and cosmetics), as a catalyst (for denitrification of exhaust-gases), as a photocatalyst (for self-cleaning and germicidal applications), as a delustrant (for synthetic fibres) and as a component of solar cells (for power generation). For many years, TiO2 has been comfortably within the top 20 in the world league of inorganic chemicals – albeit with much lower consumption (in volume terms) than sulphuric acid and the major fertilizer products. At an average price of about $3/kg, however, TiO2 claims a place in the top ten inorganic chemicals in value terms; it is a $20 billion industry.
Assured long-term demand
World consumption of TiO2 amounted to 6.17 million tonnes in 2019, of which Europe (including Russia and the CIS countries) accounted for 17%, North America for 17%, Latin America for 7%, the Middle East and Africa for 4%, China for 37%, Japan for 4% and the rest of the Asia/Pacific region for 15%. Dry powdered TiO2 has a very long shelf-life, given suitable storage conditions. This is one reason why world TiO2 consumption, measured as aggregate manufacturers’ shipments, fluctuates quite significantly from year to year as a result of variations in consumer inventories. Over the long term, however, say 1989 to 2019, the increase in world TiO2 consumption has averaged 2.5% per annum. This is similar to the long-term average growth rate for global GDP. TiO2 is difficult to recover from post-consumer waste or scrap, so there is no serious threat of recycled material troubling the consumption of virgin TiO2 . Also, there is no serious threat of substitution of TiO2 in any of its important end-use applications.
Paint and plastics are the two major end-use sectors for TiO2 . In most countries, the paint industry accounts for 50-80% of TiO2 consumption. In the world as a whole, paint accounted for 56% of consumption in 2019, plastics for 25%, décor paper for 7%, printing inks, textiles and catalysts for 3% each and sundry niche sectors for the remainder.
Chloride versus sulphate route
There are two groups of processes for manufacturing TiO2 : the chloride-route and the sulphate-route. Whichever route is chosen for making the “chemically pure” TiO2 , the final steps involved in converting this into a finished pigment are essentially the same. The aims of the pigment-finishing process are to break up aggregates and agglomerates, then to mill the material to a more or less uniform particle size, and then to coat the TiO2 particles with various chemicals designed to improve durability, dispersibility, wettability and other properties suited to the specific end-use in paints, plastics, inks, etc.
It is generally acknowledged that higher-quality TiO2 pigment can be manufactured at a chloride-route plant. Essentially, this is because the technology facilitates a narrower particle size distribution, which translates to better light-scattering, hiding power and brightness. For certain applications, e.g. automotive paints, consumers insist on chloride-route TiO2 . However, for many other applications, e.g. in paint and plastic formulations with a significant loading of pigment extenders (kaolin or calcium carbonate), good quality sulphate-route TiO2 is fully competitive with chloride-route TiO2 on performance and appearance. In fact, for printing inks, sulphate-route rutile-type TiO2 pigments are generally preferred because they are slightly less abrasive. For certain niche applications, such as food colorants, catalysts and textile delustrants, anatase-type TiO2 is required and this is only available from sulphate-route plants. Overall, about 10% of the world’s total TiO2 requirement can only be satisfied by sulphate-route TiO2 ; about 10% can only be satisfied by chloride-route pigment; and the remaining 80% can be satisfied by either sulphate-route or chloride-route TiO2 , of suitable quality.
On the supply side, there are massive differences between the regions in terms of the chloride versus sulphate split. In China, where end-2019 capacity amounted to 4.05 million t/a (47% of the world total), 89% is sulphate route, 11% is chloride route. In the rest of the Asia/Pacific region, the split is 55% chloride-route, 45% sulphate-route. In Europe (including Ukraine and Russia), the split is 44% chloride-route, 56% sulphate-route. In North America, with a total capacity of 1.49 million t/a, 99% is chloride-route and only 1% is sulphate-route. In the rest of the world (namely Brazil, Mexico and Saudi Arabia), the split is 90% chloride-route versus 10% sulphate-route.
Chloride-route technology essentially involves reacting the TiO2 feedstock with elemental chlorine in the presence of petroleum coke at a temperature of 8001,000°C to produce titanium tetrachloride, then oxidising with oxygen to produce TiO2 . In several process designs, the oxidation stage is carried out at pressures of 400600 kPa. Because of the highly corrosive nature of titanium tetrachloride, chlorine and chlorine oxides, equipment made from specialty alloys is required. The detailed chemical engineering is quite complex and the intellectual property associated with successful operation of a chloride-route TiO2 plant has been remarkably well protected. Just four companies – Chemours, Kronos, Tronox and Venator – are responsible for the technology employed at all the world’s 19 chloride-route plants currently operating outside China. Within China, the major chloride-route TiO2 producers have plants which were designed and engineered by Ti-Cons (of Germany).
Sulphate-route technology essentially involves reacting the TiO2 feedstock with sulphuric acid (typically 85-95% H2 SO4 ) at a temperature of 100-150°C to produce titanyl sulphate and iron sulphates. This acid digestion step is followed by clarification of the cooled black liquor, with unreacted solids being filtered out. Elemental iron is added to the digest solution so as to reduce all the ferric ions to ferrous ions. The liquor is then heated so as to concentrate the sulphates and then the copperas (ferrous sulphate) is separated out as crystals. The titanyl sulphate is hydrolysed to produce a colloidal TiO2 hydrate, which needs to be washed and filtered prior to feeding into a calciner at 900-1,250°C so as to produce TiO2 . If TiO2 -rich slag is used as the feedstock instead of ilmenite, the copperas removal step is not necessary.
Acid consumption
There is a wide variety of sulphate-route plants. At one end of the spectrum are the small-scale plants, running a series of batch-type processes, lacking automated control systems and producing TiO2 with a significant content of iron impurity, which imparts a yellowish tinge to the final product. At the other end of the spectrum are large-scale plants and plants that are equipped with systems for very precise process control systems for the hydrolysis and calcination stages, producing high-quality white pigments and specialty grades of TiO2 .
The quantity of sulphuric acid consumed mainly depends on the type of feedstock. For plants using Kronos ilmenite (45% TiO2 content) – such as the Fredrikstad (Norway) and Nordenham (Germany) plants – the consumption of acid (as 100% H2 SO4 ) is 4.2 tonnes per tonne of TiO2 output. For plants using Velta’s Ukrainian ilmenite (55% TiO2 content) – such as the Prerov (Czech Republic) plant – the consumption of acid is 3.5 tonnes per tonne of TiO2 output. For plants using Rio Tinto’s Sorel slag (78% TiO2 content) – such as the Varennes (Canada) plant – the consumption of acid is 2.5 tonnes per tonne of TiO2 output. Several plants use a blended ilmenite/ slag feedstock, so that the acid requirement is around 3.0 tonnes per tonne of TiO2 output.
The sulphate ion ends up in the copperas and in acid-rich waste effluent. At many plants, the copperas is converted into marketable by-product ferrous sulphate for use as a water-treatment chemical, soil-conditioner or cement additive. Copperas generated at Venator’s Duisburg-Homberg TiO2 plant is used to supplement the pyrite feedstock for the captive on-site acid plant. Copperas generated at Precheza’s TiO2 plant is used at the captive on-site iron oxide pigment plant. Acid-rich waste effluent – about 8-10 tonnes (at 20-23% H2 SO4 content) – is generated at the hydrolysis stage. At several plants, this acid is cleaned and then converted into marketable by-products, such as white gypsum. Alternatively, it is piped for mixing with stronger acid as an input for local phosphate fertilizer or ammonium sulphate plants. At many other plants, the acid is neutralised with lime and dumped at suitable landfill sites. Historically, acid-rich waste effluent from many TiO2 plants was discharged into major fast-flowing rivers or coastal waters; this practice is now confined to small plants in India and China. At a few TiO2 plants, e.g. Venator’s Krefeld-Uerdingen plant, waste acid concentration plants are operated for re-concentrating the acid to 70% or 90% strength and this acid is then recycled for TiO2 production, thus reducing the requirement for virgin acid input by up to 50%.
China’s surge in sulphate capacity
World production of TiO2 has naturally increased in line with world demand, but there have been several major changes in the structure of the TiO2 industry over the past 30 years. At the end of 1989, total world capacity was 3.32 million t/a, of which 43% was accounted for by chloride-route plants and 57% by sulphate-route plants. China’s sulphate-route plants accounted for only 2% of the total, while sulphate-route plants in the rest of the world accounted for 55%. By the end of 2019, global capacity had increased to 8.61 million t/a. The global capacity split between chloride-route and sulphate-route was again 43:57, but now China’s sulphate-route plants account for just under 42% of the total and plants in the rest of the world account for just under 15%. While sulphate-route capacity in the rest of the world has declined at a gentle rate of 1% per annum from 1.82 million t/a at the end of 1989 to 1.35 million t/a at the end of 2019, China’s sulphate-route capacity has conversely surged at an average rate of 15% per annum from 62,000 t/a to 3.6 million t/a.
There are now 25 chloride-route plants in the world, of which six are in China. There are 68 sulphate-route plants, of which 40 in China and 28 in the rest of the world. The majority of the Chinese plants were built during the past 20 years. Altogether, there are 12 sulphate-route plants in China with a capacity of 100,000 t/a or more, located at: Binzhou, Jinan, Yan-tai and Zibo (all in Shandong province); Mianzhu and Panzhihua (both in Sichuan); Baiyin (Gansu); Maanshan (Anhui); Nanjing (Jiangsu); Jiaozuo (Henan); Qinzhou (Guangxi); Ningbo (Zhejiang). Elsewhere in the world, there are only three sulphate-route plants with a capacity of 100,000 t/a or more: the two Venator plants in the Ruhr Valley region of Germany and the plant at Armyansk (Crimea) owned by Group DF (a Moscow-registered company controlled by Dmytro Firtash).
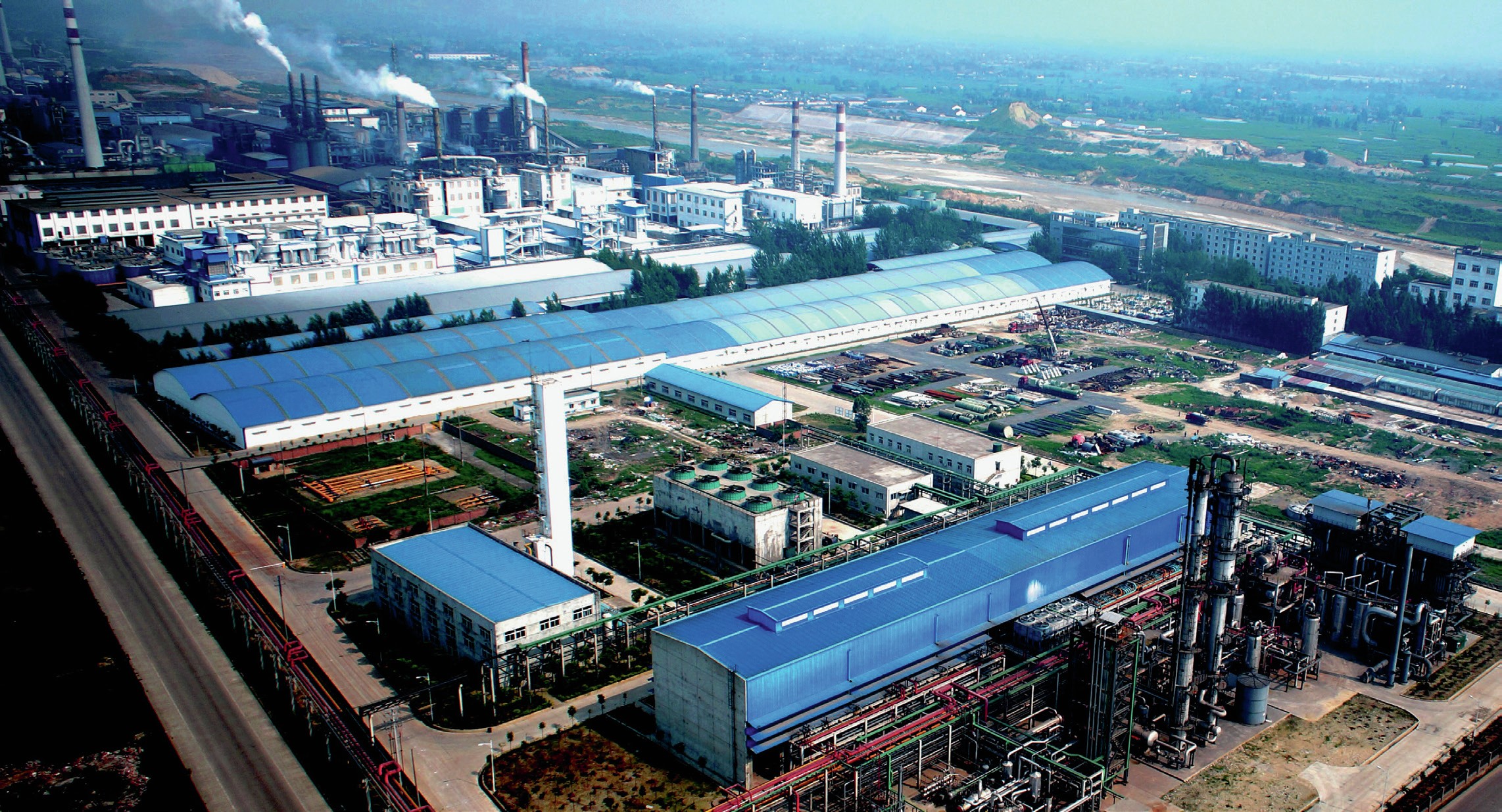
Outside of China, there have been very few new greenfield TiO2 plants built in the past 30 years. There was a wave of new chloride-route plant construction during the early 1990s, the latest in that wave being the KuanYin (Taiwan) plant of Chem-ours, which now has a capacity of 150,000 t/a. Three small sulphate-route plants were built in India – at Kalyani in 1993, Thoothukudi in 1994 and South Silukkanpatti in 2010. The latest world-scale sulphate-route plant – Venator’s plant at Teluk Kalung (Malaysia), now running at 60,000 t/a – was commissioned in 1992. No new chloride-route plants have been built since 1994 and no new sulphate-route plants have been built since 2010.
Changes in ownership structure
The structure of ownership within the TiO2 industry has also changed markedly over the past 30 years, particularly in recent years. Back in 1990, the major TiO2 producers functioned as units within large multi-activity corporations, notably Bayer, DuPont, Hanson, ICI, Ishihara, Kemira, Kerr-McGee, Metallgesellschaft, NL Industries and Rhône-Poulenc. Between them, these ten companies controlled 85% of global TiO2 capacity.
After a sequence of acquisitions and demergers, involving Rockwood, Millennium, Cristal, Huntsman and others, the major players in the TiO2 industry today all derive a large portion, if not all, of their profit and revenues from TiO2 and related products. The top five producers – Chem-ours, Tronox, Lomon Billions, Venator and Kronos – have a combined capacity of 4.37 million t/a, representing 53% of total global capacity.
Chemours, which was created by demerger from DuPont in July 2015, is the world’s largest TiO2 producer, with a capacity of 1.25 million t/a derived from four large chloride-route plants in the US, Mexico and Taiwan.
Tronox, which was created by demerger from Kerr-McGee in November 2005, has a total capacity of 1.08 million t/a, derived from six chloride-route plants in Australia, the Netherlands, Saudi Arabia, the UK and the US and three sulphate-route plants in Brazil, China and France. Tronox substantially raised its global prominence in April 2019 thanks to the $2.2 billion acquisition of Cristal’s TiO2 assets. The three sulphate-route plants – a 60,000 t/a unit at Arembepe; a 46,000 t/a unit at Fuzhou (Jiangxi province) and a 32,000 t/a unit at Thann – were all included in the Cristal acquisition.
Lomon Billions, the largest TiO2 producer in China and the third largest producer in the world, was created in October 2016 when Henan Billions acquired the TiO2 business of Sichuan Lomon. It now has a total capacity of 1.015 million t/a derived from a 300,000 t/a chloride-route plant at Jiaozuo (Henan), a 60,000 t/a chloride-route plant at Chuoxing (Yunnan), a 255,000 t/a sulphate-route plant at Mianzhu (Sichuan), a 250,000 t/a sulphate-route plant at Jiaozuo (Henan) and a 150,000 t/a sulphate-route plant at Xiang-yang (Hubei).
Venator was created by demerger from Huntsman in August 2017. Huntsman itself had entered the TiO2 industry in 1999 as a result of the acquisition of Tioxide, ICI’s wholly-owned subsidiary. Under Huntsman’s ownership, the company closed four sulphate-route plants in the UK (2009), France (2015), South Africa (2016) and Finland (2018) and acquired two sulphate-route plants in Germany (2014). Venator now has a total capacity of 657,000 t/a, of which 230,000 t/a is chloride-route and 427,000 t/a is sulphate-route. The chloride-route capacity consists of a wholly-owned 150,000 t/a plant in the UK and a 50% stake in a 160,000 t/a plant in the US. Venator has five sulphate-route plants: a 107,000 t/a plant at Krefeld-Uerdingen (Germany); a 100,000 t/a plant at Duisburg-Homberg (Germany); an 80,000 t/a plant at Scarlino (Italy); an 80,000 t/a plant at Huelva (Spain); and a 60,000 t/a plant at Teluk Kalung (Malaysia).
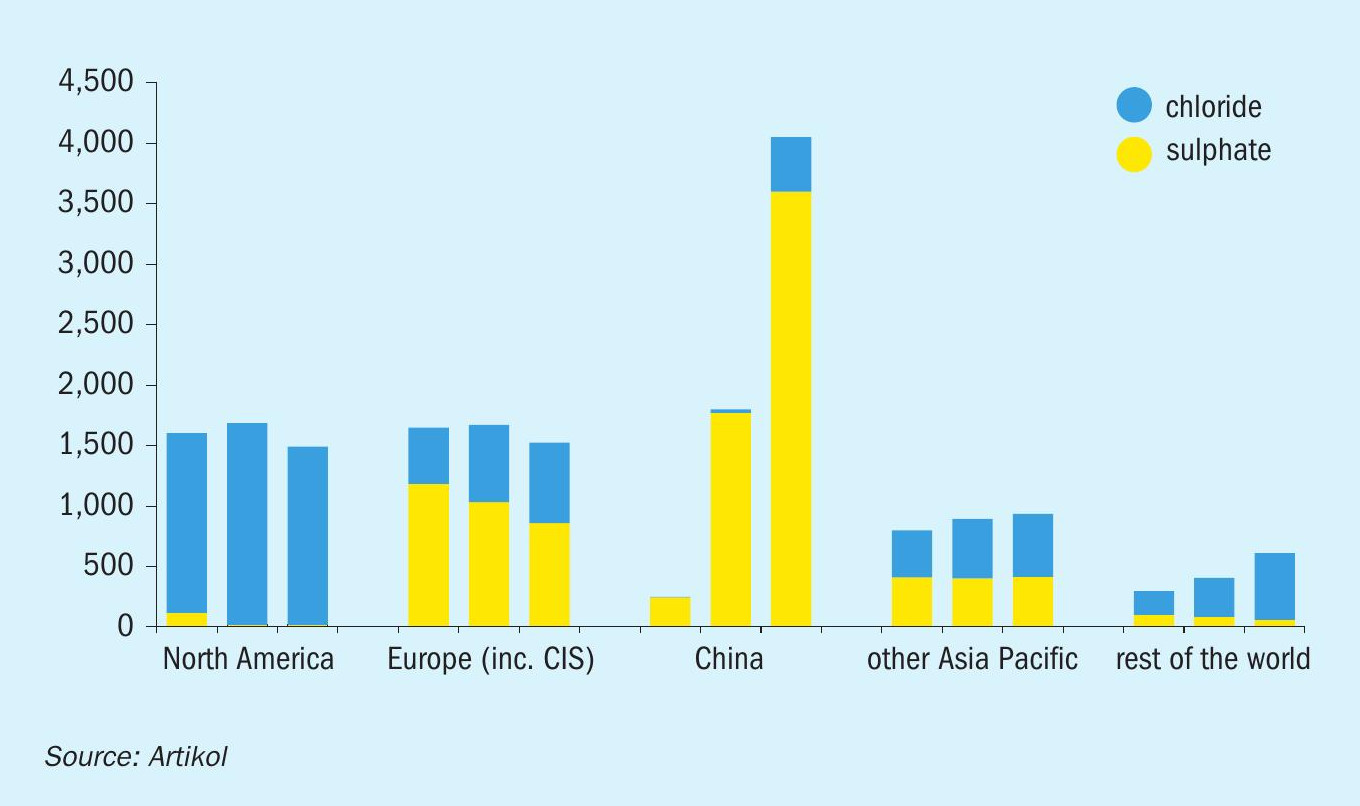
Kronos was created as a separate entity by demerger from NL Industries in 1989, but in fact NL Industries and affiliates within the Contran group still own directly or indirectly 75% of the equity of Kronos. It currently has a total capacity of 564,000 t/a, of which 422,000 t/a is chloride-route and 132,000 t/a is sulphate-route. Kronos has three wholly-owned chloride-route plants in Belgium, Canada and Germany plus a 50% stake in a 160,000 t/a plant in the US. Kronos also has four sulphate-route plants in Canada, Norway and Germany.
Most of the world’s chloride-route TiO2 plants are owned by one or other of the five majors. The only other owners of chloride-route plants are: Ineos (with two plants in the US), Ishihara (Japan), Kerala Minerals & Metals (India), Pangang, Citic Jinzhou, Yibin Tian-yuan and Luohe Xingmao (all four in China).
The ownership of sulphate-route plants is much more widely spread. Of the 68 plants operating at the end of 2019, the majors own 15. Venator has five, Kronos has four, Tronox and Lomon Billions have three each. There are no other owners besides the five majors with sulphate-route capacity in North America, Latin America, the Middle East or Africa.
In addition to Lomon Billions, substantial owners of sulphate-route TiO2 capacity in China (ranked in order, by size) comprise: CNNC HuaYuan, Jilin GPRO, Shandong Dongjia, China National Bluestar, Wuhan Fangyuan, Lubei Enterprise, Ningbo Xinfu, Panzhihua Taihai, Yunnan Dahutong, Shandong Dawn, Guangxi Jinmao and Guangxi Cava. Each of these companies controls at least 100,000 t/a of sulphate-route TiO2 capacity.
In Europe, sulphate-route plants are operated by: Cinkarna (72,000 t/a at Celje, Slovenia); Group DF (110,000 t/a at Armyansk, Crimea); Grupa Azoty (45,000 t/a at Police, Poland); Khimprom Sumy (50,000 t/a at Sumy, Ukraine); and Precheza (62,000 t/a at Prerov, Czech Republic).
In Asia/Pacific, sulphate-route plants are operated by: Beach Minerals (15,000 t/a at South Silukkanpatti and 5000 t/a at Kalyani, both in India); Cosmo Chemicals (40,000 t/a at Onsan and 25,000 t/a at Incheon, both in South Korea); Ishihara (86,000 t/a at Yokkaichi and 13,000 t/a at Kobe, both in Japan); Sakai Chemical (60,000 t/a at Onahama, Japan); Tayca (60,000 t/a at Saidaji, Japan); Titan Kogyo (4,000 t/a at Ube, Japan); Travancore Titanium Products (18,000 t/a at Thiruvananthapuram, India); and VV Pigments (30,000 t/a at Thoothukudi, India).
Slow decline in acid consumption
What is the future for the TiO2 industry and for the sulphate-route sector in particular? In fact, against the background of an anticipated 5-8% drop in TiO2 consumption in 2020 and uncertainty about the pace of recovery in 2021/22, none of the existing TiO2 producers has confirmed plans for expanding capacity. Chemours has deferred a previously planned 125,000 t/a capacity increase spread over its four chloride-route plants. Lomon Billions and Yibin Tianyuan had both announced ambitious plans for expanding their chloride-route capacity in China, but these will probably be scaled back. There have been no definitive announcements of significant expansion of sulphate-route capacity by any of the Chinese producers. Nor have there been any definitive announcements of retrenchment and the wave of closures of small sulphate-route plants that had failed to meet new pollution guidelines enforced by Central Government inspectors seems to have ended.
On the downside in Europe, Kronos has announced that it will close its 36,000 t/a sulphate-route plant at Leverkusen (Germany) by the end of this year and Venator has indicated that it is going to reduce capacity at its 100,000 t/a sulphate-route plant at Duisburg-Homberg (Germany).
On the upside worldwide, TNG Ltd. has a well advanced project for building a new 150,000 t/a sulphate-route TiO2 plant at Darwin (Australia) and has awarded the design and engineering contract to Ti-Cons. Nyanza Light Metals plans to build a 70,000 t/a sulphate-route TiO2 plant at Alton North, near Richards Bay (South Africa), with provision for doubling capacity in a second phase of the project. Velta (the Ukrainian ilmenite supplier) is planning to build a 40,000 t/a sulphate-route plant at Mishkor Rotem (Israel), with provision for raising capacity to 70,000 t/a as warranted by demand. Assuming that all these plans come to fruition, these projects would provide a significant boost to sulphuric acid consumption in the TiO2 industry.
Overall, however, annual world consumption of sulphuric acid for TiO2 production is more likely to decline than increase over the next 5-10 years, with chloride-route TiO2 output gradually displacing sulphate-route TiO2 output, especially in China.