Sulphur 390 Sept-Oct 2020

30 September 2020
Unlocking the potential of gas processing assets
GAS PROCESSING
Unlocking the potential of gas processing assets
G. Bowerbank and W. Blas of Shell Catalysts & Technologies discuss low cost strategies to maximise value at existing gas processing facilities. Changing solvents, introducing advanced column internals or a combination of both are relatively simple and cost-effective options for boosting production or revenue with minimal investment.
As 2019 drew to a close, the global gas market was poised for a period of healthy growth, with no fewer than 50 new projects at the pre-final investment decision stage. The change in the first quarter of 2020 could not have been more dramatic, with a sharp fall in oil prices and economic uncertainty linked to the Covid-19 pandemic. Consequently, it appears that only 10 of the 50 projects will now go ahead.
Lockdowns have reduced gas demand by about half in the three largest markets in Europe and lower oil prices have slowed gas imports to India. The drop in demand is likely to be temporary and to reverse once lockdowns end. The effects of the deferrals and cancellations of pre-final investment decision projects, however, will be felt for years to come. How will the major gas suppliers respond? How will countries adapt to meet their energy transition targets?
For most gas producers, long-term disruption of site activities is an unfamiliar problem. For some, it may provide an opportunity to implement improvement or debottlenecking projects or to take an “opportunity shutdown” that will help them maintain their competitive position once the market starts to recover. Despite the uncertainty and a much more cautious approach to capital investment, there is some upside for gas and liquefied natural gas producers.
Make the most of what you’ve got: The case for revamps
Revamping, repurposing or upgrading existing assets can be more capital efficient than adding new units or trains and can provide operators with more margin for their expenditure. Projects of this kind often require small, incremental investments, which can be highly appropriate in today’s market, as they carry a low investment risk, generate credibility with investors and provide the ability to respond flexibly as market conditions change.
These projects seek to reuse existing equipment and any new items purchased, such as new column internals, heat exchangers, small pieces of equipment and upgraded solvent systems, generally have a modest capital cost. The revamping team can also seek synergies with units that are already in place, which further enhances the return on investment or helps to manage changes to expected feed gas sources, rates and compositions.
The implementation of revamp projects is generally more challenging than implementing grass-roots initiatives. Project planners must ensure that the revamp does not disrupt the continuing operation of the facility and align their implementation plans with shutdown time constraints.
A proven approach in uncertain times
Changing solvents, introducing advanced column internals or a combination of both are relatively simple and cost-effective options for boosting production or revenue with minimal investment. The potential benefits include:
- increased capacity;
- reduced energy consumption;
- deeper removal of contaminants;
- reduced solvent degradation rate; and
- improved performance for managing increased levels of contaminants.
Operators in upstream oil and gas facilities often have to deal with increasing feed gas contaminant levels caused by changes in field characteristics or the addition of hydrocarbons from new reservoirs or fields. There is also the challenge of meeting more stringent treated gas specifications. Most of the solvent swap opportunities that Shell has evaluated over the past decade have been driven by these changes, along with capacity increases resulting from higher amine loading capacity. Solvent swaps can be performed on- or offline. The choice depends on the similarity of the solvents. For example, swapping from aqueous methyl diethanolamine to Sulfinol-X can be done “on the run” if the existing solvent is of acceptable quality, but a swap from Sulfinol-D to ADIP-X or Sulfinol-X has to be performed offline.
Changes in feed often mean increasing contaminant levels, which can lead to reduced capacity. To address the need for enhanced absorption performance, Shell developed Shell Turbo Trays. These provide additional benefits for existing assets by increasing the hydraulic capacity and contaminant handling capacity. In addition, the trays offer substantial operational benefits, including increased operational flexibility, reduced fouling and increased resilience to foaming.
The examples below demonstrate the value of revamp solutions at four different assets.
Case study 1
Processing higher levels of feed gas contaminants1
In this example, the new feed to a gas plant had double the hydrogen sulphide (H2 S) content and 30% more carbon dioxide (CO 2 ) than the plant had been designed to handle (Table 1). The operators had to find a way to process this new feed while meeting the same treated gas specifications. The existing process configuration used Sulfinol-D solvent, as shown in Fig. 1.
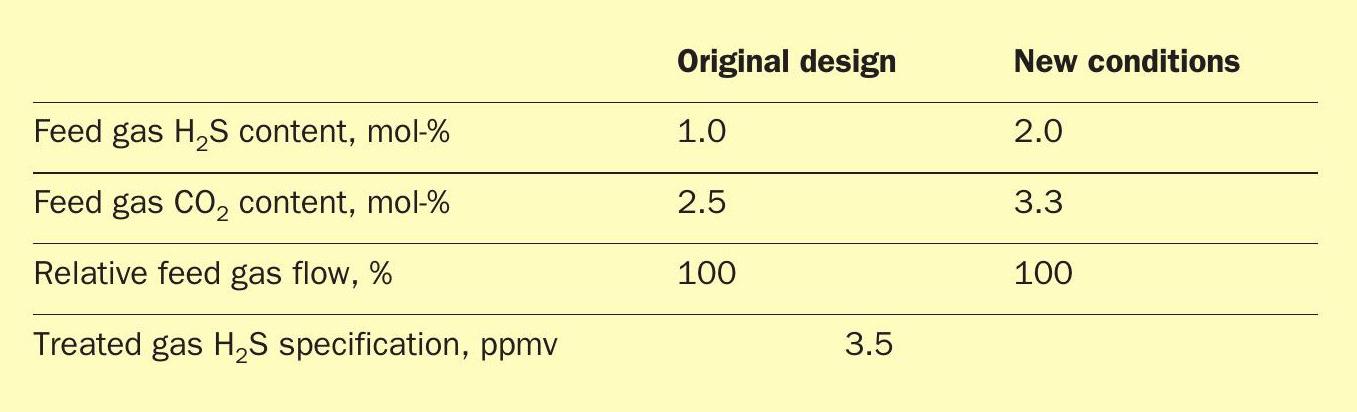
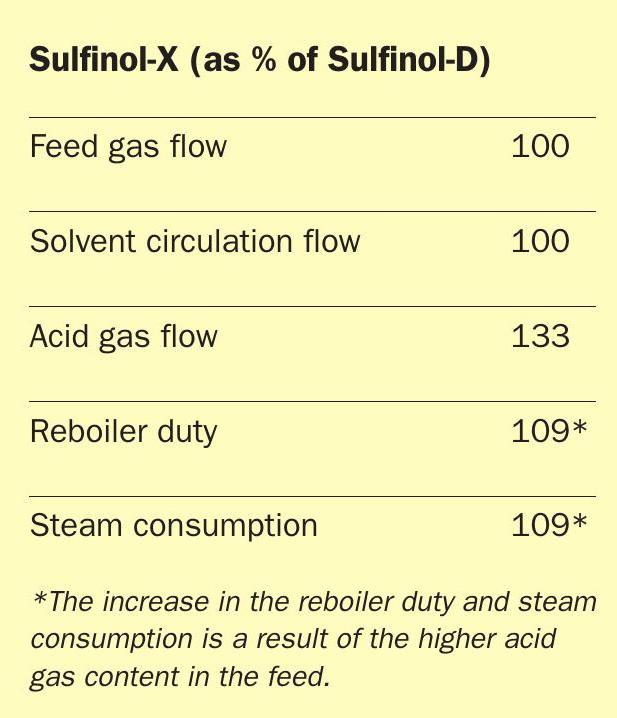
The plant operator asked Shell Catalysts & Technologies to look at potential solutions. Two options were considered: installing a new pretreatment acid gas removal unit (AGRU) or a solvent swap.
Option 1
Installing a new pretreatment AGRU would reduce the feed gas H 2 S and CO 2 content to the design values for the existing Sulfinol-D system. However, depending on the resultant acid gas quality, an acid gas enrichment section might also be required (Fig. 2). This optional equipment would require considerable capital investment and plot space, and add operational complexity, which would likely reduce unit reliability.
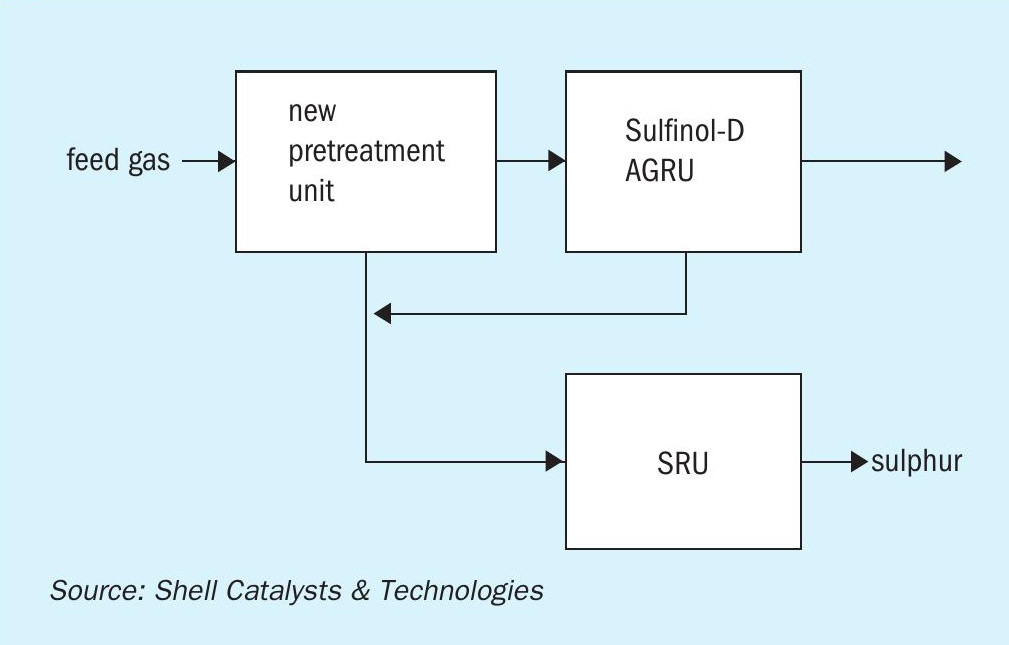
Option 2
Swapping the existing Sulfinol-D solvent for Sulfinol-X was also considered (Fig. 3). This approach had the potential to improve unit performance for a minimal investment and without needing major modifications or new equipment.
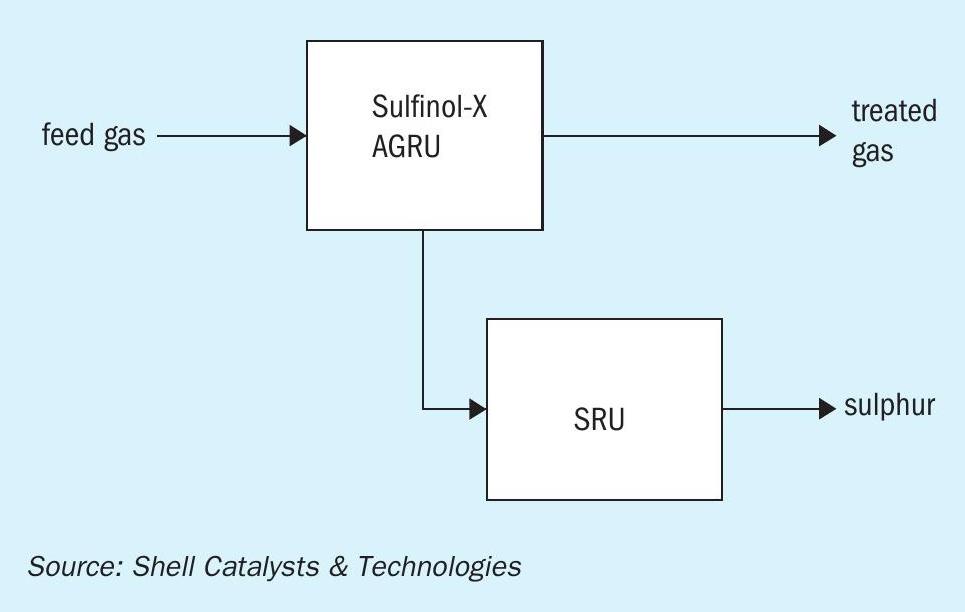
The revamp team modelled the unit performance improvement for Sulfinol-X compared with the existing solvent (Table 2). This showed that the treated gas H 2 S, CO 2 , carbonyl sulphide (COS) and mercaptan specifications could be achieved with a similar solvent circulation rate. The lean solvent temperature to the absorber column would also be similar. Reboiler duty and steam consumption would be about 9% higher owing to the much higher acid gas flow. However, the higher duty was within the equipment design specifications, so there would be no need to modify the reboiler. The evaluation work showed that the solvent change would not require any major equipment modifications.
As Sulfinol-X has similar fluid properties to Sulfinol-D, the swap would have no impact on pump seals or seal material and the solvent circulation would be within the operating range of the pumps.
There would be substantial benefits derived from this solvent swap. Sulfinol‐X has a higher loading capacity than Sulfinol-D, which means that higher amounts of H 2 S and CO 2 can be removed from the feed gas at the same solvent rate. Methyl diethanolamine (MDEA) reacts 1:1 with CO 2 whereas diisopropanolamine (DIPA) reacts 2:1. This makes it possible to load an accelerated MDEA-based solvent more (up to 1 mol CO 2 /mol amine) compared with a DIPA-based solvent (up to 0.5 mol CO 2 /mol amine).
Increased loading provides operational cost savings, as less solvent pumping and a lower heating duty are required, and helps to debottleneck capacity for existing Sulfinol-D units.
The swap would require very little capital expenditure, as there would be no major equipment modification. The operating costs would also be considerably lower than for a new pretreatment unit and the solvent swap would not increase the operational complexity.
The evaluation concluded that a solvent swap to Sulfinol-X would be the most attractive option for meeting the new feed gas contaminant levels. It would provide the existing unit with the means to treat more highly contaminated feed gas at considerably lower capital investment and operating expenditure than the alternative while maintaining the same level of operability and reliability.
Case study 2
Mitigating solvent losses and degradation to reduce operating costs1
An operator in the Middle East had been using a DIPA based solvent for a gas-sweetening unit, but increasing amounts of CO2 in the feed gas were going to result in unacceptable rates of solvent degradation. DIPA reacts with CO2 to form carbamate, which then reacts irreversibly to form oxazolidone. In this case, the increased partial pressure of CO2 would have accelerated the build-up of oxazolidone and other related degradation products.
A solvent swap to Sulfinol-X was proposed to combat this problem. With Sulfinol-X, the gas-sweetening unit met the required specifications for CO2 and sulphur (H2 S, COS and mercaptans) removal using a similar solvent circulation rate. Compared with Sulfinol-D, Sulfinol-X requires a lower reboiler duty for the same sulfolane content to remove the same amount of CO2 in the regenerator, as the overall heat of reaction for the accelerated aqueous methyl diethanolamine is lower than that of DIPA. In this example, the reboiler duty was about 10% lower compared with the Sulfinol-D case.
The DIPA-based Sulfinol solvent had been performing well, but continuing to use this solvent with feed gas that contained high volumes of CO2 would have meant higher operational expenditure as a result of frequent solvent replenishment or the additional capital cost of a new solvent reclamation unit because of DIPA’s contribution to the solvent degradation.
The solvent swap was made without additional capital cost and required no equipment modification in the gas-sweetening unit or the downstream units. The solvent circulation requirement was within the operating range of the pumps and had no effect on pump seals or seal materials. The composition chosen for Sulfinol-X was within the material selection guidelines for sulfolane-based solvents, so there was no impact on material selection from the solvent change.
The performance of the unit was checked for a higher gas throughput. The unit can handle 10% additional gas throughput with about a 12% higher solvent circulation rate. The solvent composition for Sulfinol-X has lower sulfolane content compared with Sulfinol-D. This gives a lower solvent temperature in the reboiler and, hence, increased reboiler capacity. In this case, the reboiler duty was limiting the capacity. So, instead of reducing its duty (steam requirement), the reboiler was kept close to full capacity to increase the gas processing capacity. This unit has now been running successfully with Sulfinol-X for several years.
Case study 3
Improving performance to meet tighter specifications1
A gas processing operating company wanted to reduce the total sulphur content of its final product to meet tighter gas specifications. In collaboration with Shell Catalysts & Technologies, a solvent swap from diethanolamine to Sulfinol-X was proposed. The feasibility study showed that using Sulfinol-X in the AGRU (Fig. 4) would reduce the total sulphur content in the treated gas to the target levels.

Modelling also demonstrated that Sulfinol-X would remove H2 S, CO2 , mercaptans, COS and organic sulphides to the required treated gas product specifications in a single process.
With diethanolamine, the process was achieving more than 100 ppm total sulphur in the product; the higher performance of the Sulfinol amine enabled treating down to 5 ppm total sulphur.
By opting for a solvent swap, the operator would maintain the same equipment count, in contrast to the alternative multi-process line-ups, and avoid unnecessary capital costs. Without the need to invest in additional equipment, there would be no impact on availability and reliability. Operating costs could also be reduced, as Sulfinol-X has a lower steam requirement for stripping of the absorbed acid gases compared with alternative aqueous amine solvents.
Case study 4
Increasing throughput and CO2 handling capacity2
A liquefied natural gas facility was facing an imminent rise in feed gas CO2 concentration from about 1 to 4 mol-%. The plant was using a proprietary solvent and conventional trays. An initial assessment concluded that a solvent swap to ADIP ULTRA would be feasible. However, increasing contaminant levels would mean a 25% reduction in the gas processing capacity, even when the existing design margins on the unit were utilised (point 2 in Fig. 5). Shell Catalysts & Technologies was then asked to consider what maximum throughput the facility could achieve at 4 mol-% CO2 concentration with minimal capital investment.
Shell Turbo Trays offered a higher mass transfer benefit that enabled increased solvent loading without other equipment changes. The new trays would provide an 18% increase in the gas throughput for only the capital cost of the trays (point 3 in Fig. 5). The subsequent limitation at this point was the reboiler capacity, which the client investigated for potential debottlenecking.
On the assumption that additional regeneration capacity could be added, the maximum gas throughput that could be processed by the absorber at the higher CO2 concentration was simulated and was determined to be 182% of the original design throughput (point 4 in Fig. 5). The revamp would, therefore, deliver a substantial increase in maximum gas flow with fewer trays (Table 3).
The key principle behind Shell Turbo Tray technology is the combination of contacting and separation zones in an integrated tray package. This integrated tray design offers two distinct advantages over conventional trays and packing for the same column cross-sectional area:
- higher gas and liquid handling capacity with effective gas–liquid separation achieved at each tray; and
- improved mass transfer, as near equilibrium is achieved owing to the higher liquid–gas ratio and the intense contacting in the contacting boxes.
Fig. 6 shows a schematic of gas and liquid flows on a single Shell Turbo Tray through the contacting (a) and separation (b) zones.
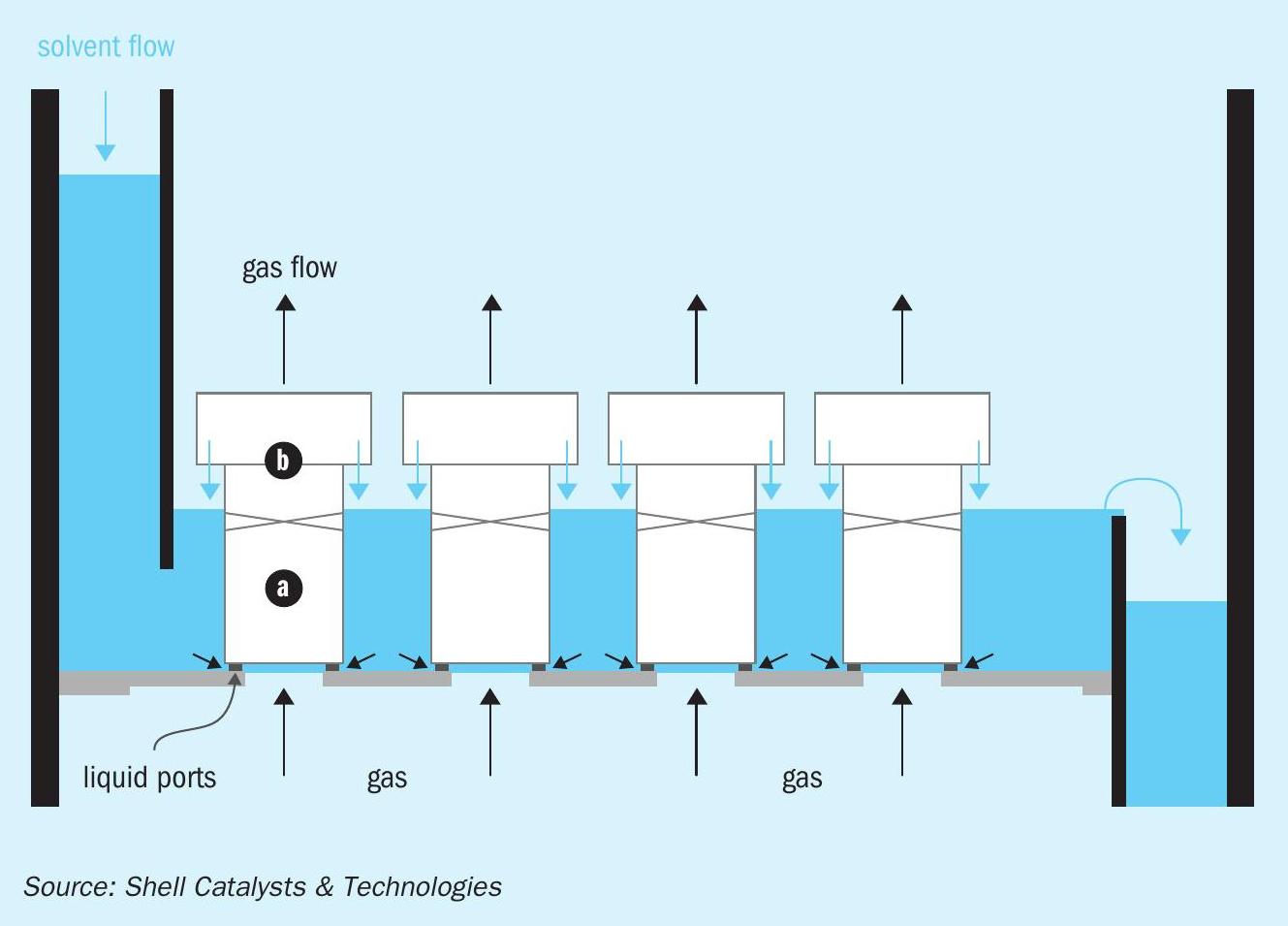
Conclusions
Solvent swaps can increase the potential of existing gas processing trains with little or no capital expenditure. The case studies above show that major performance benefits can be obtained without purchasing equipment or extensive modifications. The combination of a solvent swap and the installation of Shell Turbo Trays has been shown to deliver cost-effective debottlenecking solutions in challenging operating conditions.
Effective planning and execution are important for the success of solvent swaps in brownfield assets. In certain circumstances, an on-the-run solvent swap, which avoids shutting down the unit, can be performed with appropriate procedures and monitoring.
References