Nitrogen+Syngas 368 Nov-Dec 2020
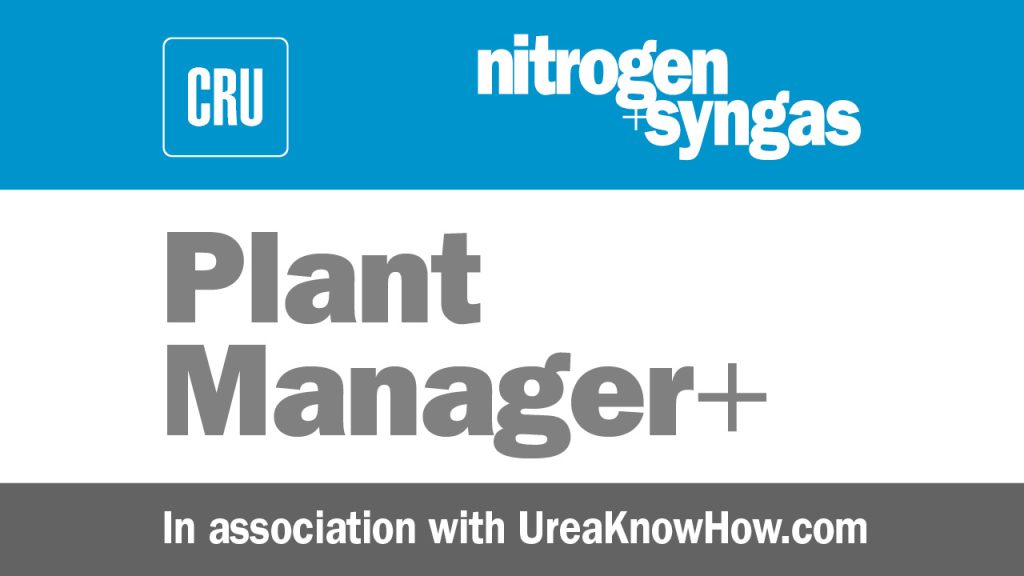
30 November 2020
Incident No. 3: Backflow in pressurised leak detection system for loose liner of HP scrubber
Furthermore, in this case the process fluid did not contain urea and is less sensitive to clogging, even though it did. In cases where the process fluid contains urea the situation is even more critical.
From this incident it can be learned that a pressurised leak detection system requires tracing and insulation of all tubing in the leak detection circuits. However, this will only temporarily reduced the risk of clogging. In the opinion of the FIORDA team, an active vacuum leak detection system is a more reliable choice.
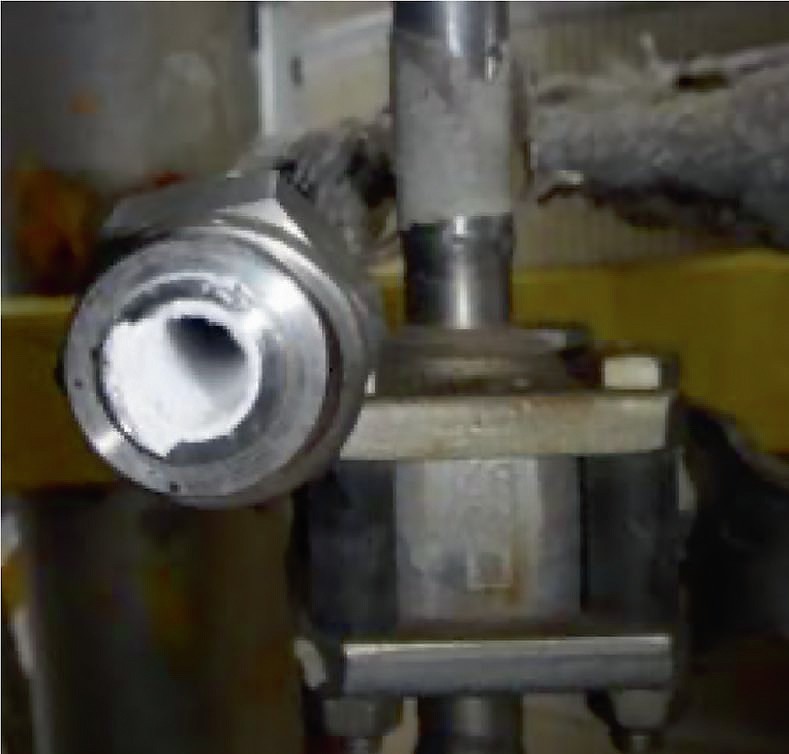
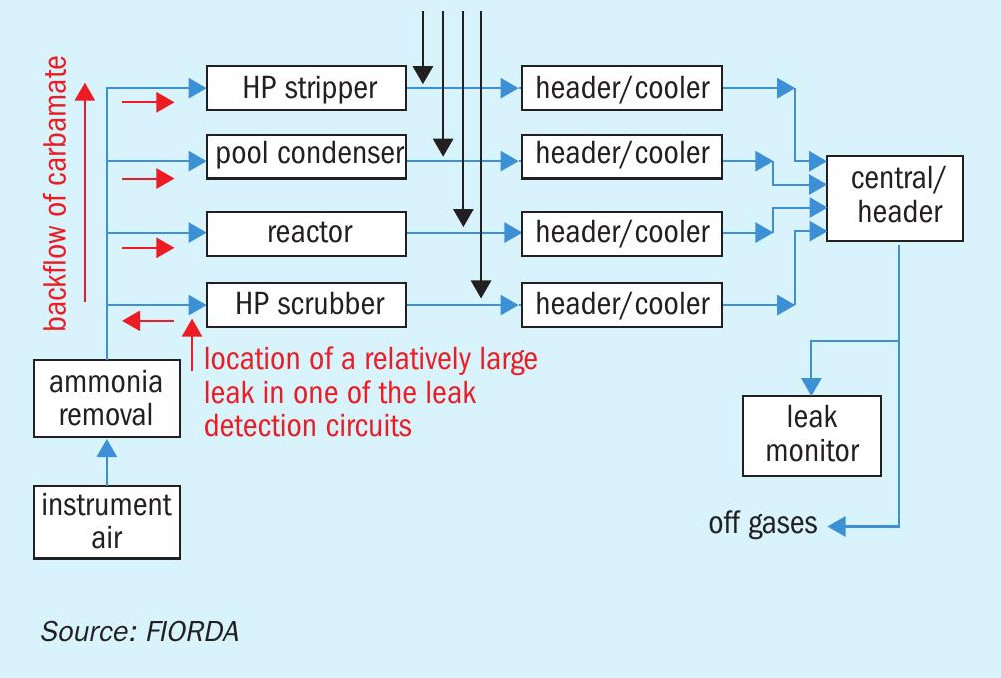
Event description
In 2010, a 25-22-2 urea grade liner was installed on a 316L UG older overlay weld in the bottom of a HP scrubber dating from 1980. As the ammonia analyser was unavailable due to maintenance, the outlet vent of the pressurised leak detection system was checked for ammonia with a pocket ammonia analyser every four hours.
On one occasion, ammonia was detected and further investigation revealed that a lot of tubing had been clogged (see Fig. 1 and photo above). After opening the HP scrubber it was revealed that the liner showed cracks.
Immediate response action
The plant was stopped for further inspections. By analysing the tubing with more carbamate, it was concluded that backflow had occurred and contaminated the leak detection circuits of all three HP equipment items.
Causes
The leak rate was so large that the flowmeter acted as a flow restriction, pressure built up and backflow occurred leading to clogging of the leak detection circuits in all of the other high pressure equipment items.
Primary consequence
As a result of the timely shutdown the risk of a rupture was successfully avoided.
Secondary consequence
There was an unplanned shutdown, extensive work was required to clean and open all leak detection circuits and carry out a repair/relining job.
Risk level
The likelihood of a major consequence was moderate, but the risk level was high.
Prevention safeguards
Assure proper functioning of your leak detection system. Safe plant operation is only possible with a good working leak detection system, including an accurate and reliable ammonia analyser.
Mitigation safeguards
In case of a leak, confirm and locate the leak, shut down the plant and drain the synthesis section as soon as possible.
Corrective recommendation
The leak detection system was refurbished and made operational before start-up of the plant. All plant operators received renewed instructions. An inspection and maintenance program was also implemented to increase the reliability and availability of the existing leak detection system.
This case study report is one of many serious incident reports on UreaKnowHow.com’s Fertilizer Industry Operational Risks Database, FIORDA, which has been created for collecting and sharing process safety and reliability information among participating companies in the fertilizer industry.