Nitrogen+Syngas 368 Nov-Dec 2020
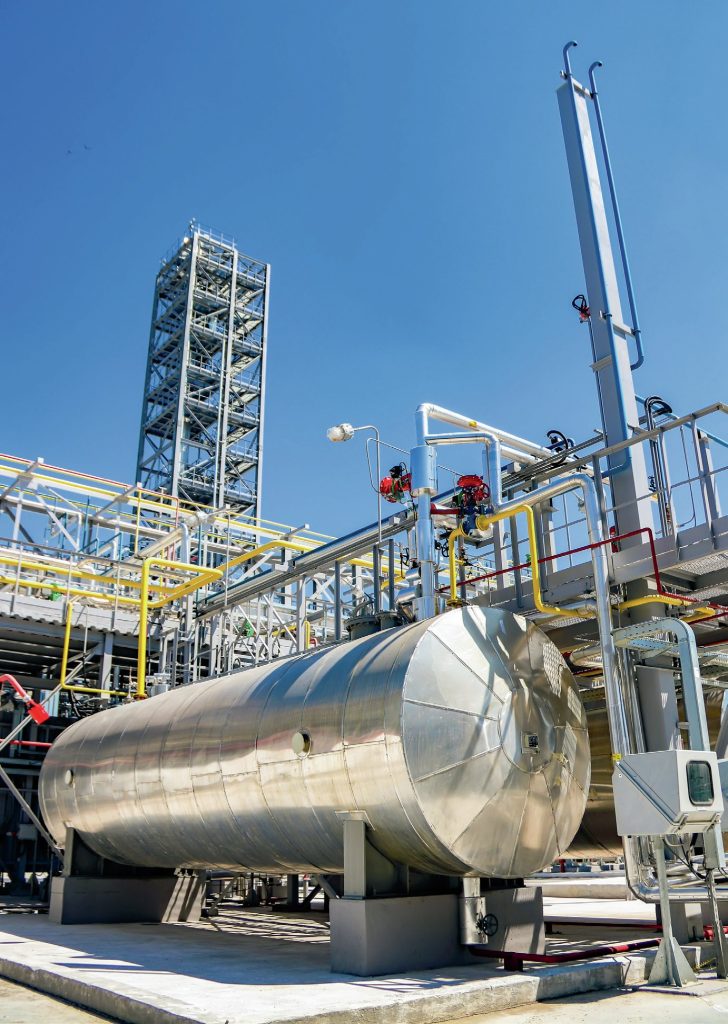
30 November 2020
The future of DME
DIMETHYL ETHER
The future of DME
A few years ago DME production from methanol gave a major boost to world methanol demand, with DME being used as a blendstock for LPG. However, demand plateaued and DME has not had the takeoff that its proponents feel it should have. Could new renewable DME processes give it the boost it needs?
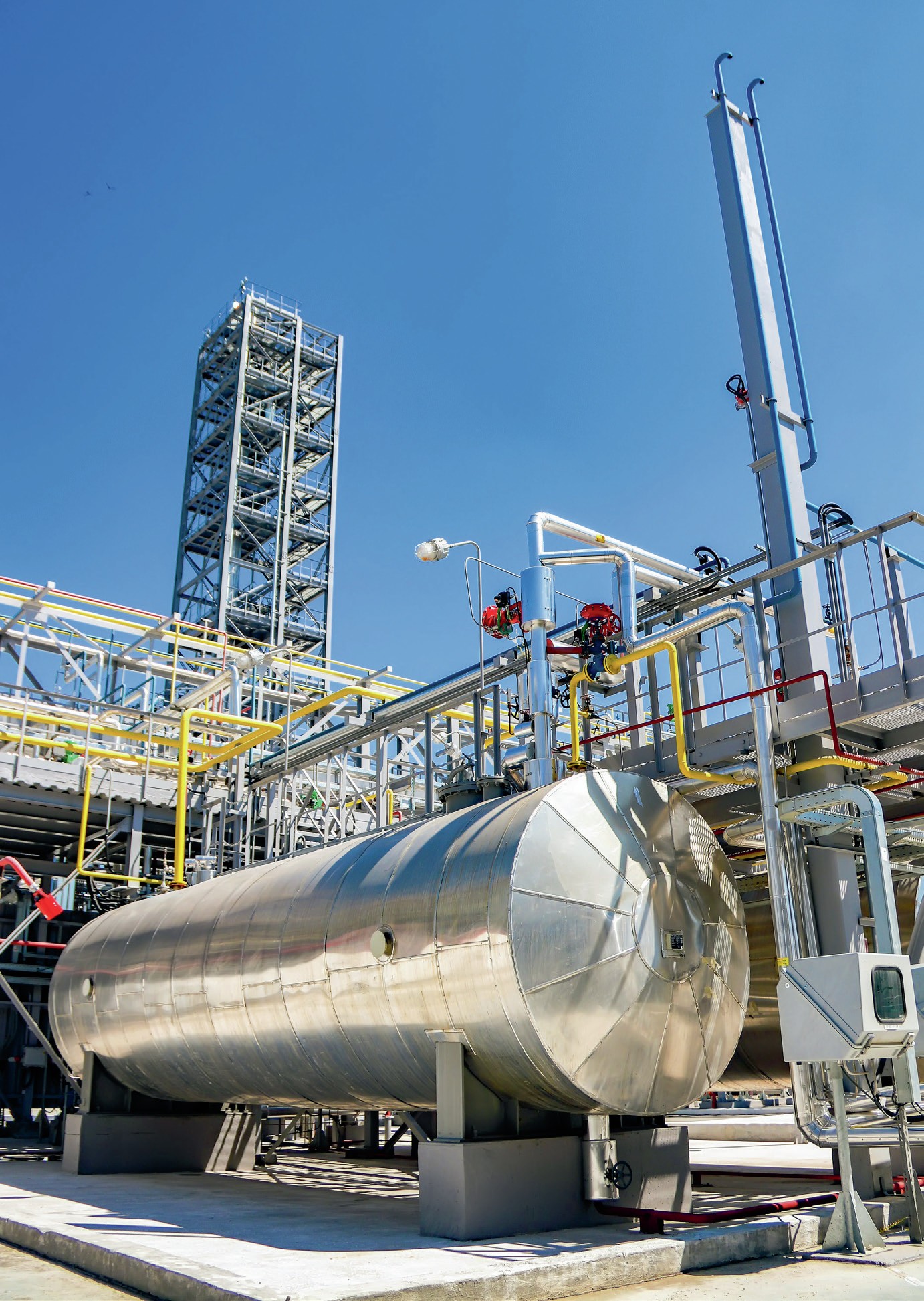
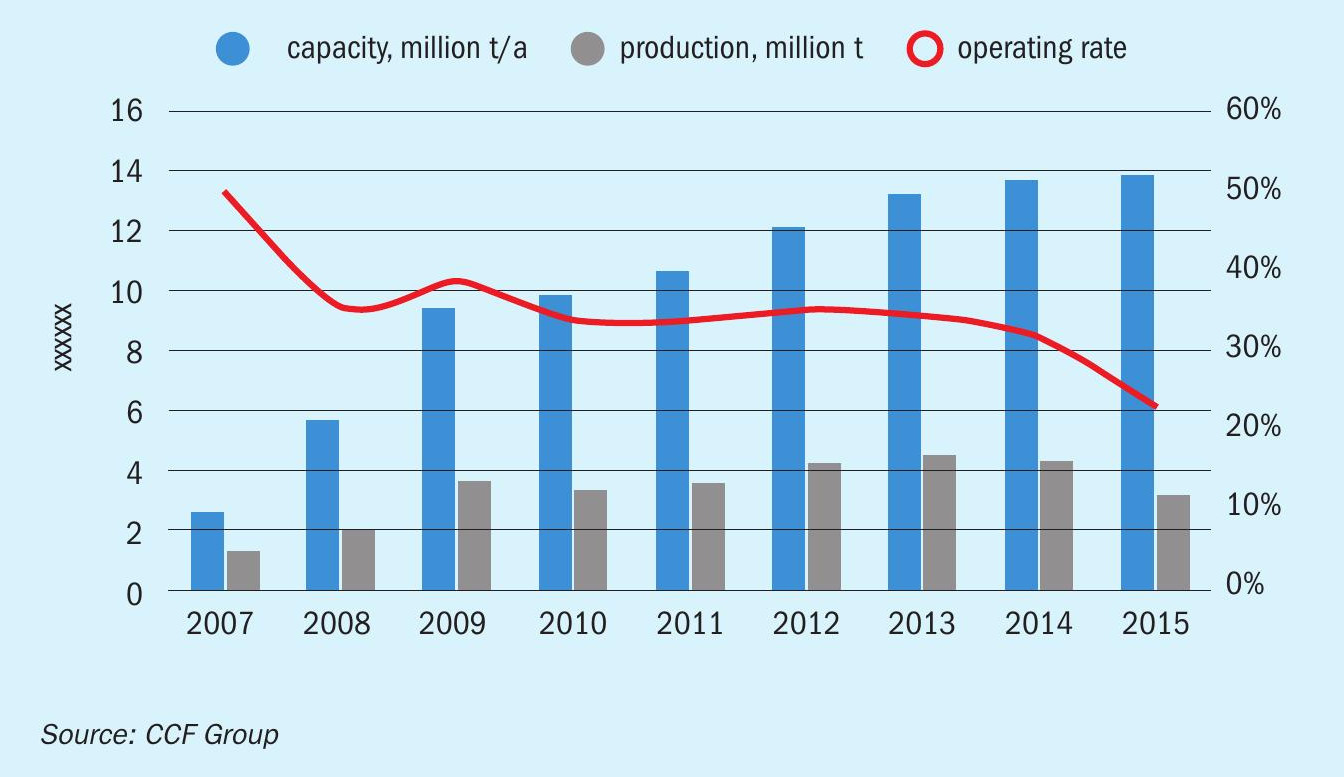
Until the mid-2000s, dimethyl ether (DME) was essentially a very minor methanol derivative used primarily as a CFC-free aerosol propellant, with a total global market size of around 1.6 million t/a. However, from about 2005, falling costs of methanol production led to interest growing in its potential use as an alternative fuel.
DME’s fuel uses are essentially threefold; as a substitute for liquid petroleum gas (LPG) in domestic cooking and heating; as a substitute for diesel in car, truck and ship engines; and as a fuel for power plants. Initially, particularly in China, DME demand began to take off in the 2000s as a blend-stock for LPG. DME made from coal-derived methanol was seen by the Chinese authorities as a way, along with direct methanol fuel blending into gasoline, of reducing China’s dependence on imported oil and petroleum products by using domestic coal reserves.
LPG
DME has similar properties to LPG, and can be blended at ratios of up to 10-20% in LPG without requiring any change in storage and distribution infrastructure. China is a major user of LPG and also a considerable importer, and coal-derived DME could be made cheaper than imported LPG. As a result,
DME capacity growth in China was phenomenal, from just 120,000 t/a in 2005 to 9 million t/a in 2010 and around 14 million t/a in 2015. However, as Figure 1 shows, such over-optimistic building of DME capacity ran far ahead of demand, and by 2013, DME consumption in China had reached only 4 million t/a, and utilisation rates were down to 30%.
There were various reasons for this. China’s National Development and Reform Committee (NDRC) concluded in a report in 2010 that downstream methanol uses like DME had been used as a justification for companies to privately ‘acquire’ access to coal resources (which were at the time otherwise treated as state assets). There was also a lack of national standards, and a great deal of illegal over-blending of DME in LPG. At too high a level, DME can corrode rubber seals. This led to leaks of LPG and consequent explosions, leading to a regulatory crackdown from 2010 onwards. A contributory factor was falling demand for LPG itself as more cities in China were brought onto the national natural gas network, as well as increased domestic production of LPG from a myriad of new domestic refineries.
More recently, Chinese methanol producers have found that they can achieve greater profits from selling into the burgeoning methanol to olefins (MTO) market, and interest in DME has waned.
The result has been that while China remains the main market for DME at present, with around 70% of global demand (90% of which is used as an LNG extender), it has not so far caught on in any major way outside China.
Indonesia
The at least partial success of China’s LPG substitution programme did lead to interest in other countries that are large users of LPG, such as Brazil, Iran, India, Nigeria, South Korea, Indonesia, and Egypt, in potentially doing the same thing. For some years Iran has had plans to build a large scale (200,000 t/a) DME plant, and a few years ago Egypt likewise explored the feasibility of building such a plant. Kogas designed a 300,000 t/a plant for Saudi Arabia but the project did not secure a gas allocation. Indeed, outside of a few up-ratings of capacity (eg at Akzo Nobel’s site in Rotterdam), a 20,000 t/a plant at Shchekinoazot in Russia for aerosol production, and the new 20,000 t/a Caribbean Gas Chemical Company side-stream on Trinidad, actual new DME capacity building has been thin on the ground.
However, Indonesia now appears to be making a concerted effort to follow the Chinese route and use domestic coal to produce methanol-based DME, with the aim of using it as an LPG blendstock. Indonesia is the fourth largest LPG importer in Asia (after China, Japan and India), and rapidly increasing consumption of LPG combined with the increasing burden of domestic subsidies for the product and diminishing production has led to the project. Indonesia’s consumption of LPG has increased from 1 million t/a to 7.6 million t/a in 2019, 75% of which is now imported.
State oil company Pertamina is now partnering coal mining company PT Bukit Asam and technology supplier Air Products and Chemicals to develop a large scale coal gasification facility which will produce DME and other downstream products for domestic consumption. The agreement follows a feasibility study conducted from 2018 by Pertamina which included an implementation roadmap and market demonstration of DME for use as a cooking fuel in the country. The plant is to be sited at Peranap in Riau Province on Sumatra, using coal from Bukit Asam’s nearby mine, and will aim to produce up to 1.4 million t/a of DME, together with 300,000 t/a of surplus methanol and 250,000 t/a of mono ethylene glycol. Front end engineering design began in February 2020, with construction work expected to be completed in 2024-25.
Vehicle fuel
As well as a blendstock for LPG, DME can also be used as a substitute for diesel fuel in vehicle engines. DME’s high cetane number delivers performance and efficiency comparable to diesel, and compared to compressed gases it has sufficient energy density (about 55% of that of diesel) to support long range transport. Like diesel, it ignites on compression and requires no separate ignition mechanism, and unlike LNG, it does not require cryogenic storage temperatures; it is handled and stored like propane, with tank pressures of only 75 psi (vs. 3,600 psi for CNG), meaning it can safely be stored on-site. Because DME contains no carbon-carbon bonds, it produces no soot, so no diesel particulate filter is necessary, which leads to weight savings, and because of the lack of cryogenic storage as compared to LNG or CNG, DME tanks can considerably lighter and considerably less complex.
The downside is that, as with LPG, use of DME does require a specially constructed engine, using higher fuel injection rates and fewer plastic components that might be corroded. Nevertheless, major commercial vehicle manufacturer Volvo became interested in DME’s potential as a vehicle fuel, and the company was able to adapt one of its existing diesel engines for DME use. The company supplied DME-adapted trucks as part of a European Union funded ‘bio-DME’ project in Sweden, which gasified a waste stream from a paper mill to produce small quantities (10 t/d) of methanol and DME using Haldor Topsoe technology. The DME produced was trialled from 2011-12 in a fleet of 10 Volvo trucks, and the project was deemed a technical success, prompting further development work by Volvo, although the pilot bio-DME site was actually closed down in 2016 after operating at a financial loss.
Volvo’s interest moved on to California. In 2013, alternative fuel developer Oberon Fuels began operations at a pilot DME plant in southern California, using natural gas as a feedstock in a small scale (3,700 t/a) modular plant to produce DME, and the same year Volvo signed a partnership agreement to provide DME-powered trucks to demonstrate DME’s potential as an alternative fuel. Progress has been slow but steady, and other US companies have begun to come on board. Mack has been demonstrating a DME-powered truck, and Ford has worked on a DME-powered passenger car. In China, there has also been work on DME commercial vehicles, including prototype garbage trucks and street sweepers.
Oberon Fuels meanwhile have concentrated – in collaboration with STV Energy – on switching to biogas as a feedstock in order to meet Californian renewable fuel mandates, and in September California’s legislature voted to reduce taxes on renewable DME to the same level as other alternative fuels.
Maritime fuel
There has also been some interest in DME as a clean burning fuel for ships, prompted in part by the new more stringent SO2 emission limits mandated by the International Maritime Organisation (IMO) from January 2020. The move has led shipowners to consider a variety of different alternative fuels, including natural gas, methanol and DME. The ‘Spireth’ (Spirits and Ethers as Marine Fuel) project ran form 2012-14, testing a mix of methanol and DME on board a Stena ‘Scanrail’ ship to evaluate its potential to reduce emissions and improve environmental performance. The project work showed that methanol and DME-based fuels are viable alternatives for reducing emissions from ships, but while it did lead to some interest in methanol-fuelled ships, so far no DME-powered ships have been built. Nevertheless, research work continues, including a project begun in 2019 by Maersk, in collaboration with a Chinese partner and researchers at the Danish Technical University (DTU). DTU has a demonstration facility for green DME production at its Risø Campus in Denmark, but admits that scale-up would present problems, including building large enough electrolysis plants and finding the requisite amount of biomass to power the process.
Renewable DME
Acceptance of any new fuel requires it to overcome a variety of challenges; technical, commercial, and legislative. Work on DME has been progressing for many years now, and most of the technical challenges have been or are being overcome. The commercial and legislative challenges remain, however, and it seems clear that in order to overcome them, DME needs an additional environmental edge. Development work is thus now coming to focus upon renewable DME (‘rDME’), in the hope that boosting its green credentials will attract tax credits and lower legislative barriers. A number of companies and research institutes are working on rDME, including the following:
Enerkem
Canadian company Enerkem has concentrated on gasification of municipal waste as a source of syngas-derived products, and in 2018 announced that it had produced fuel-grade ‘bio-DME’ at its research centre at Westbury, Quebec. The company said at the time that it had “tested and validated the production of fuel-grade bio-DME made from unrecoverable carbon-rich municipal solid waste” over course of over 1,000 hours of operations at its Innovation Centre. It also says that it intends to “further develop and optimise” this product stream, while “evaluating its potential commercial applications”.
Oberon Fuels
As mentioned above, Oberon Fuels is partnering with SHV Energy, the world’s largest LPG distributor, to accelerate the use of rDME (via a waste gasification process) to reduce the carbon footprint of transportation fuel, including propane. In 2019 the state of California awarded Oberon a $2.9 million grant to upgrade its existing DME pilot facility to demonstration scale and facilitate the first production of rDME in the United States, with a target production capacity of about 1.6 million gallons of DME per year (4,050 t/a). In February 2020 Oberon said that it is now hoping to further develop DME fuelling infrastructure and vehicle development, continue testing the use of rDME blended with propane, and leverage its collaboration with SHV Energy via its global distribution network “to facilitate greater use of rDME in numerous energy applications worldwide”. In September this year, US LPG distributor Suburban Propane Partners LP took a 39% stake in Oberon Fuels, and will have the exclusive rights to work with Oberon to market and sell rDME and rDME/ propane blends in the United States, Canada and Mexico.
FLEDGED
Fledged is a European partnership across six EU countries, including six universities and research centres, as well as Frames Renewable Energy Solutions, Quantis, Econward Tech, and Sumitomo’s Finnish subsidiary. It is developing a biomass gasification process for DME production, which will also use hydrogen generated from renewable energy. It is a four year project which concluded in October 2020, and has developed a sorption-based gasifier to convert ‘second generation’ biomass into syngas, in which a calcium oxide based sorbent circulator-gasifier and a combustor-calciner to produce a nitrogen free syngas without the use of an air separation unit; as well a sorption-based DME synthesis process which separates water using the sorbent. The process avoids use of a water-gas shift module by adsorbing and recycling CO2 from the gasifier. It can run on a variety of feeds, including woody biomass, municipal waste and agricultural waste.
CO2 to DME
Conversion of CO2 directly to DME is something of a ‘holy grail’ for renewable DME production, and a number of companies and research institutions are working on processes. One such is Gas Technology International, which has been developing a process via a US ARPA-Energy grant from 2017-2020. It now has a catalytic membrane reactor and has produced a 1 kg/ day prototype for long-term testing of fuel production. Of course, the journey from laboratory scale to working commercial plant is one often fraught with difficulties.
Meanwhile, while it is not a pure CO2 to DME process, last year BASF announced plans for scale-up and commercialisation of a technology developed in collaboration with Linde which uses a novel one-step route for DME production from syngas. The new concept is based on dry reforming of methane with carbon dioxide and the direct conversion of syngas to DME without a methanol intermediate step. BASF says that it “represents a major breakthrough that offers numerous commercial possibilities for energy-efficient, low-emission and cost-effective scaled production of DME and olefins using CO2 as a feedstock”. The process allows for a higher than 50% reduction in CO2 emissions in the production of DME compared to conventional methods. BASF says that one potential application is what it refers to as “clean olefin production” – production of ethylene and propylene from natural gas. In June 2019 BASF signed a memorandum of understanding with Sichuan Lutianhua to co-develop a pilot production plant for the process in China, which was due to be completed this year.
Elsewhere, Haldor Topsoe is building its e-SMR demonstrator plant to produce 10 kg/hour of methanol from CO2 -containing biogas in a similar hybrid process, but using electrical heating and a ‘green’ hydrogen feed to ensure fully carbon neutral production. The plant is due to be running by 2022, and of course could easily be adapted for downstream DME production using Topsoe’s own process.
The future of DME
For the past two decades DME has been a promising syngas derivative that has never quite seemed to make the breakthrough that has been expected of it. It has made some inroads into the market as a substitute for LPG, and the recent project activity in Indonesia shows that there is still scope for this to be developed outside of China, where it is currently concentrated. As a vehicle fuel, there are plenty of encouraging signs, especially in niche markets like California, but it seems likely that in order to make a bigger breakthrough, renewable DME production will need to be developed. Numerous companies and research institutes are working on this, but at present only Oberon Fuels appears to be making commercial headway. However, BASF and Lutianhua’s hybrid methane/CO2 -fed pilot plant in China could be very interesting as a commercial demonstrator of a potential lower carbon route to DME.