Nitrogen+Syngas 369 Jan-Feb 2021
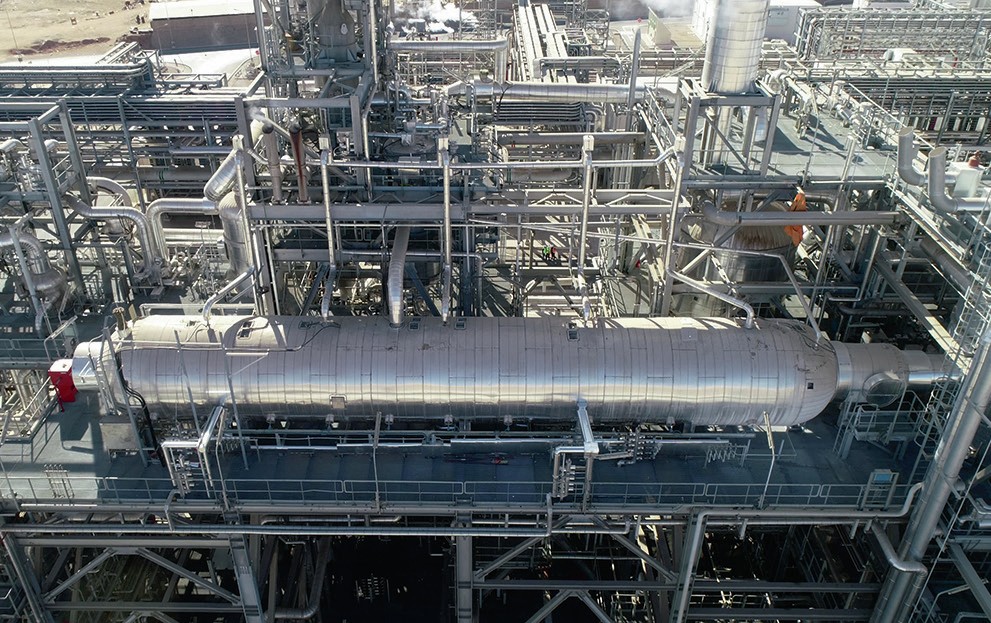
31 January 2021
Getting the job done during a global pandemic
REMOTE INSPECTION AND COMMISSIONING
Getting the job done during a global pandemic
The year 2020 will be remembered as an uncertain, demanding and challenging year. When faced with a global pandemic, companies have adopted new approaches and remote inspection, monitoring and training using the latest digital tools has been key for the successful completion of projects. Stamicarbon, Casale and KBR share some of their experiences of the past year.
The coronavirus Covid-19 pandemic is the defining global health crisis of our time and the greatest challenge we have faced since World War Two. The pandemic is much more than a health crisis, it’s also an unprecedented socioeconomic crisis, stressing every one of the countries it touches. During this time of unprecedented challenges companies have been forced to react quickly and creatively to overcome many hurdles. In this article we learn how Stamicarbon, Casale and KBR have successfully met project challenges thanks to a huge commitment, great leadership and strong co-operation between relevant partners.
Stamicarbon proves resilient amidst pandemic
When the Covid-19 pandemic started to spread around the world, Stamicarbon, the innovation and license company of Maire Tecnimont Group, was confronted with a new situation and swiftly reacted in synergy with the whole Group’s network. In response to the spread of Coronavirus Covid-19, Maire Tecnimont Group immediately committed itself to ensuring that all work activities in offices and sites were carried out in compliance with the maximum health and safety standards, closely following the protocols of the official bodies. The clear priority was to ensure the health and safety of its employees and collaborators and their families, while guaranteeing the continuity of the business in the countries where it operates.
The Group’s continuous commitment to foster an already well rooted HSE-driven culture – which in mid-2019 gave birth to the branding of the HSE campaign “Safethink” – enabled all companies of the Group to rapidly adapt to the new situation. Thanks to significant investments in digital transformation technologies as well as in smart-working solutions and training both for executives and employees during the last four years, the Group was able to carry out remotely numerous working activities and to virtualise several processes, ensuring business operations and activities to keep running. Given the context of global health emergency, in which correct information is essential to face an ever changing situation and manage the risk effectively, Maire Tecnimont set up an HSE Crisis Coordination Team to coordinate actions in all Group locations, to issue guidelines for behaviour to be adopted by all employees. The spin-off of the Safethink brand, “Safethinkcovid-19” was rapidly conceived to cover all aspects of the pandemic emergency and the correct measures to be taken to conduct daily activities both in the home office and at sites were promptly implemented.
Business continuity
Stamicarbon rapidly adapted by increasing the use of videoconferencing and other cloud-supported software. The digitalisation exceeded meetings with clients, supporting webinars, remote equipment inspections, classroom training of client’s plant operating personnel (launching their plant operator training simulator in the cloud) and even remote commissioning and start-up support. The resilience demonstrated, stimulated all colleagues to continue looking for other solutions and ways to show Stamicarbon’s continued commitment to clients. A proactive approach in each ongoing project and the ability to manage all steps of the crisis, fostering tailor-made solutions according to the latest advice, enabled all operators to handle a challenging situation while educating all involved.
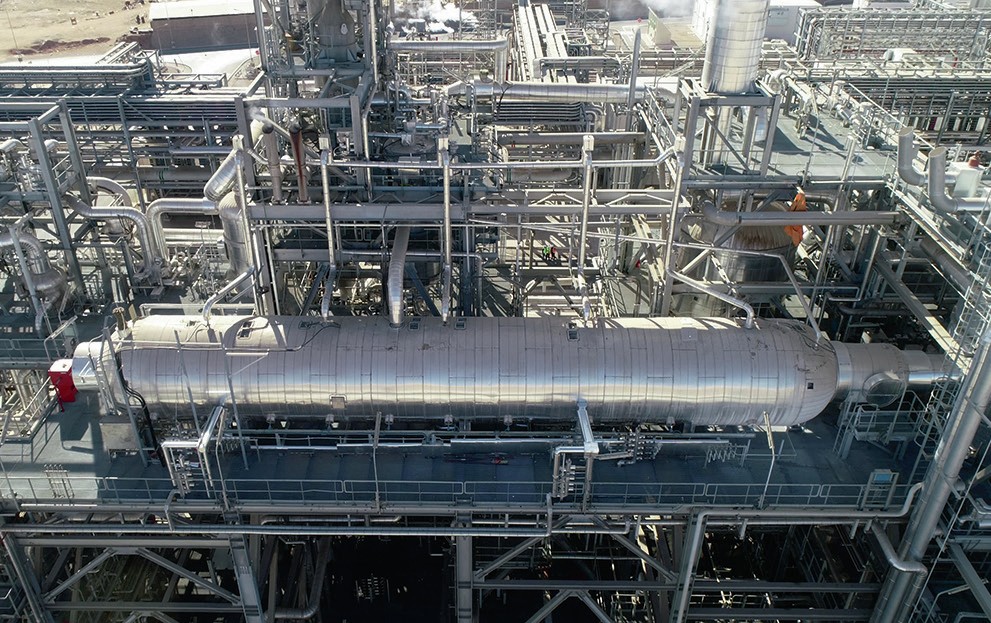
Start-ups/training
One of Stamicarbon’s first start-up projects that had to tackle the impact of the coronavirus was the performance test for the Kima ammonia-urea complex (Fig. 1) in Egypt. This was a joint project involving Stamicarbon as urea technology licensor and its sister company Tecnimont as EPC contractor.
The project teams were challenged to finalise the test run in the wake of increasingly difficult implications of Covid19 in its early days in Egypt and Europe. Stamicarbon employees provided valuable guidance to Kima staff, helping them to run the plant smoothly and meet guarantee figures. They returned home just before the area went into lockdown and continued to provide remote assistance via digital communication tools. Meanwhile the Tecnimont team stayed on site and implemented new safety practices to protect the health of personnel. They helped each other 24/7 and worked as one team to successfully meet the challenge.
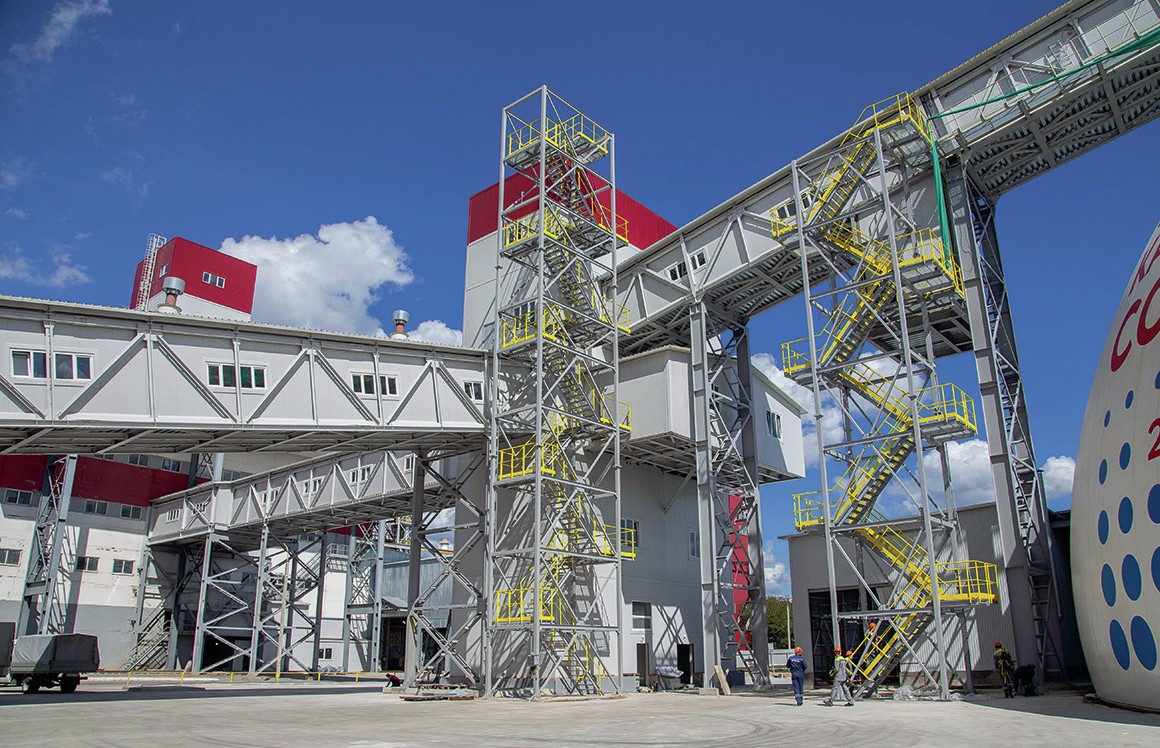
The second challenge was the commissioning of JSC Acron’s urea granulation plant in the Russian Federation (Fig.2). Acron had to start up its new Stamicarbon granulator without any assistance of Stamicarbon representatives on site. Operators who normally operated prilling towers had to be ready to operate a granulation plant. It was the first time for remote operator training in which the client’s video conferencing system had to be connected to the Stamicarbon system to give startup instructions via the screen. The client discussions and training were carried out successfully despite the distance between all involved.
New build projects were not the only activities affected by the travel restrictions. A major urea revamping project in the United States also had to be realised without the on-site presence of Stamicarbon specialists. The old urea CO2 stripping plant, was being revamped to increase capacity, reduce ammonia emissions, lower energy consumption and improve plant safety by using Stamicarbon’s medium pressure add-on technology and the installation of a high pressure after-reactor. Stamicarbon was able to give remote start-up services. In the final stage, four engineers were on-hand to provide support, 16 hours a day, working in pairs across two shifts. By sharing a live video connection to the client’s DCS system, Stamicarbon engineers received live images from the plant and were able to respond with advice, discuss settings with operators and other technical staff and immediately see the consequences of modifications of certain process parameters. The revamp was realised successfully.
Equipment deliveries
Proprietary equipment supply forms an integral part of Stamicarbon’s business. High quality vessels, piping and other products complement and support their plant designs. This equipment is manufactured by different supplier workshops, inspected by Stamicarbon engineers and shipped and delivered to the construction sites.
As Stamicarbon has a well filled order backlog of proprietary equipment, it also has a busy schedule of equipment deliveries, which under Covid-19 circumstances and restrictions posed new challenges.
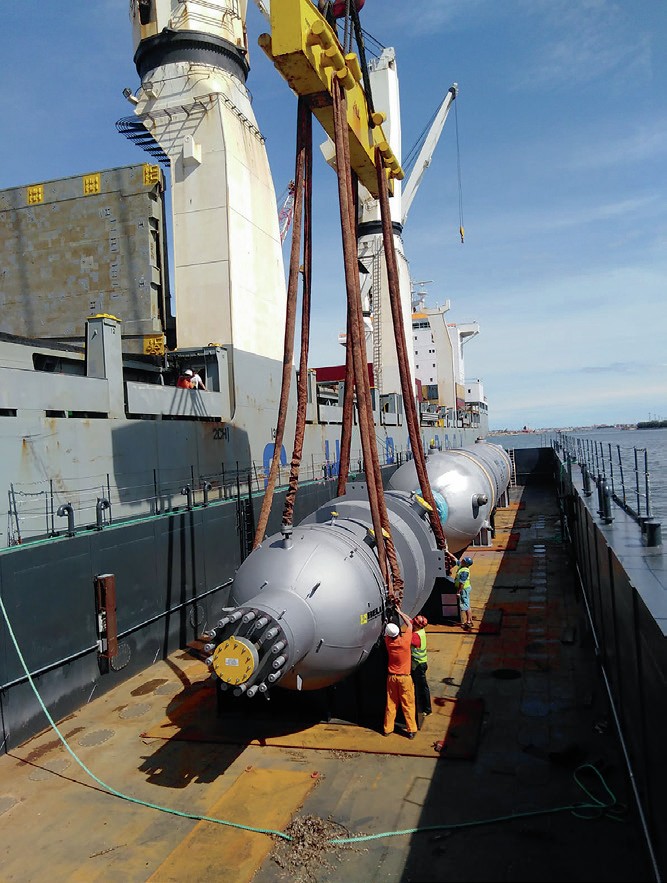
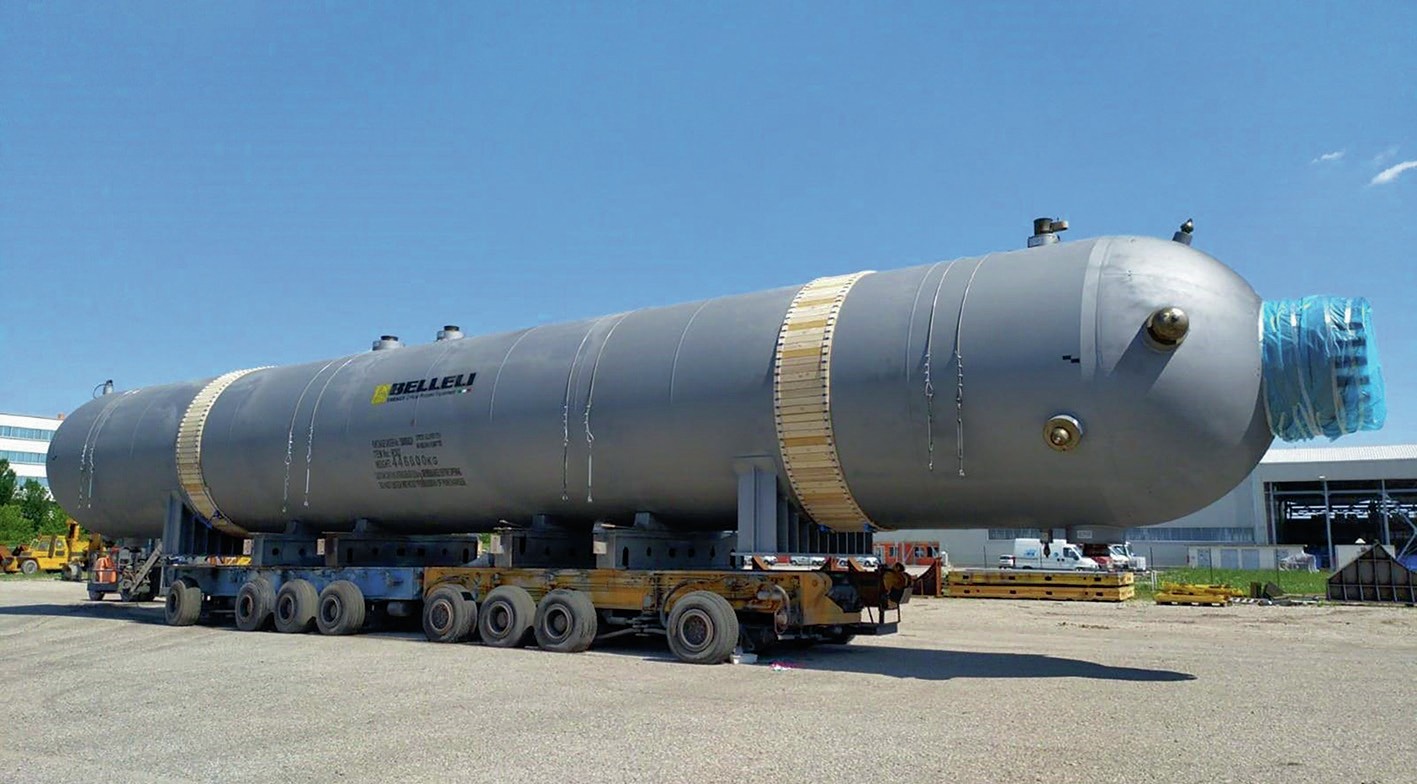
From mid-May until August, Stamicarbon had to deliver, on average, one major piece of equipment per week. The orders consisted of ten high pressure vessels (four pool reactors, three strippers, one reactor, two HP-scrubbers), plus a granulator and an MMV scrubber for clients in China, Egypt, the Russian Federation and the United States. Most items were for grass root projects (Figs 3 and 4), while two were replacements.
In addition to remote inspections, Stamicarbon arranged resident inspection engineers for several months for a few projects facing potential delays. The teams ensured the utmost commitment and highest performance to execute design and welding inspections in order to minimise delays and maximise production time.
Meanwhile arrangements had to be made to transport equipment. Many air and sea ports were closed or restricted and containers were held outside closed ports, making it extremely difficult to arrange sea and air cargo. Without an incredible team effort from all parties, it would not have been possible to maintain the fabrication sequence, solve technical issues and stay on schedule to deliver the equipment on time to the construction sites.
Events
As a consequence of the coronavirus virtually all industry events entailing physical presence were put on hold, including the well-known Stamicarbon Symposium, which is held every four years and was originally set for May 2020, but had to be postponed. In order to inform producers, contractors and suppliers about new developments and technologies, Stamicarbon started hosting a series of free webinars featuring some of the topics that were planned for the symposium. Engineers delivered live presentations on proper piping inspections, fighting corrosion by using Safurex, nitric acid technology, the Ultra-Low Energy design concept, revamping and scrubbing solutions. All webinars were well attended and highly appreciated by participants.
Pandemic long term effects
The Covid-19 pandemic has shaken up the whole world and has put everything in a new spectrum. It has changed our way of thinking and working. While face-to-face discussions with clients stay preferred in some cases, Stamicarbon has learned that there are more possibilities and opportunities to serve clients remotely than previously imagined. Covid-19 has certainly shifted the boundaries on what’s possible. Without its strong partnerships with suppliers and the teamwork, commitment, perseverance, resilience and sense of ownership of its employees, Stamicarbon would not have been able to continue business in such a successful way in 2020. One thing is certain: the emerging “new normal” will be more flexible and innovative than ever before.
Casale commissioning and startup of a new nitric acid plant
JSC Navoiyazot, commissioned in 1964, is the largest chemical company in Uzbekistan and a leading producer of mineral fertilizers and other products. The chemical complex is currently undergoing a major modernisation programme to meet modern energy efficiency requirements. As part of this modernisation, JSC Navoiyazot awarded Casale, as EPCC contractor, the project for a new nitric acid plant (Fig. 5), with a nominal capacity of 1,500 t/d 60 wt-% HNO3 , to replace the 50 year-old outdated production capacities. The project was managed and executed by Casale as a single point of responsibility from conceptual phase to EPCC lump sum turnkey phase.
The new nitric acid plant project was in the final stages of the installation and commissioning works when the Covid-19 pandemic made its impact in the first half of 2020. The water treatment section had not yet been completed and some key equipment such as the turbo-set were under mechanical completion, for instance the shaft alignment had not yet been completed.
Casale top management, the project director and the entire site team reacted promptly to rapidly assess the company capability and flexibility with respect to these challenges. Faced with strict travel restrictions, Casale and Navoiyazot were forced to think creatively and rapidly devise a new approach to accomplish the last phases of the project. A reduced Casale staff on site granted the minimum necessary operability, while Casale head office provided assistance and support remotely together with the manufacturers of key equipment. The strong commitment to proceed on site, was testament to the professionalism of the people involved, notwithstanding the personal issues that those involved had being absent from home during this time.
The global travel restrictions, in conjunction with internal HSE policies, forced key vendors to take the decision to rapidly demobilise their personnel from the site. Getting new specialists to the site, from Casale or from other key vendors, also became extremely difficult. As a result, the headcount of the Casale site team was badly impacted, putting the entire project schedule at risk. The situation also made it impossible to have the direct supervision of vendor specialists during the critical commissioning activities of key equipment. It is typically a contractual right of the vendors to witness the critical phases of installation and commissioning as conditions of the warranty. And, of course, there was the new and increased risk of starting such a complex plant with a reduced number of key personnel.
A dedicated technical risk assessment of the new scenario was carried out at Casale head office, taking into account the increased risks in starting the plant in this situation, including the risk of damage to equipment when starting the plant without direct supervision, as well as the HSE safety concerns in conducting the commissioning of the plant with a reduced site team. Logistic solutions were identified to move materials and private jets were organised to enable key people to reach the site from Europe.
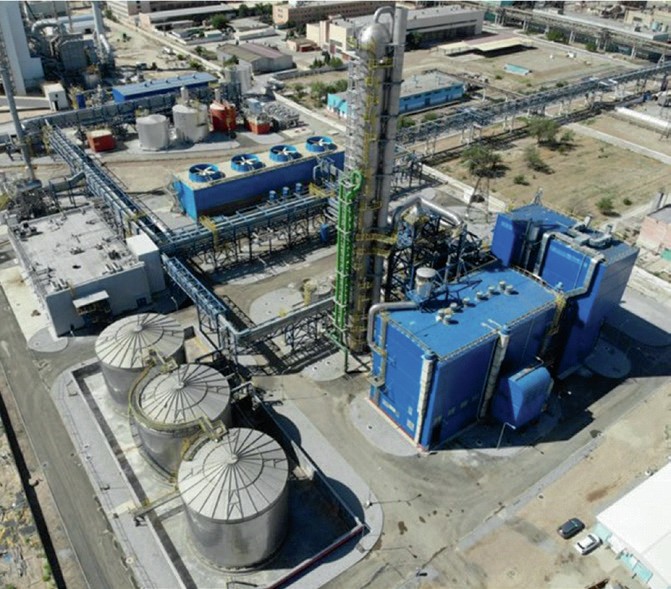
Key vendors placed trust in Casale’s abilities and offered remote support for the completion of the critical activities which were still pending at site, and which normally require a mandatory presence of a vendor’s specialist to assure correct installation.
Finally, after careful review of the situation, Casale top management gave the green light to complete the project with a world first approach based on remote assistance in commissioning the plant.
Solutions adopted by Casale to face the pandemic challenge included the following:
- remote support provided by MAN for completion of the cold and hot commissioning of the turbo-set;
- installation of the catalysts with remote assistance from the vendor;
- the DCS was connected to the head office for remote assistance by Yokogawa;
- several commissioning issues were encountered on the boiler, as usually happens in this phase when the equipment is loaded up for the first time, and were successfully solved with remote support from the vendor;
- a flexible approach to commissioning was adopted for the water treatment – in particular, a temporary solution was adopted to by-pass part of the system and achieve the requested demi-water production required for the commissioning of process unit and plant start-up;
- as anticipated, Navoiyazot provided several experts and specialists to support and reinforce the Casale site team. This experience increased the already high level of partnership between the two companies and allowed the customer to get familiar with the plant;
- Casale made the decision to invest some resources to transport key personnel to the site by private jet.
Commissioning of the turbomachinery
At the heart of the nitric acid plant is the turbomachinery equipment, supplied by MAN Energy Solutions, consisting of two compressors, one turbine, one expander and auxiliary equipment. The equipment was manufactured, assembled and packaged in Germany and delivered to site. At the beginning of 2020 the delivered equipment was mechanically complete and the “cold commissioning” had started.
In March 2020, due to Covid-19 and the lockdown, MAN experts left Uzbekistan and continued the cold commissioning remotely, from its offices in Germany, Casale offices in Switzerland, and with the support of the local Uzbek team.
MAN had trust in Casale’s capabilities and in the technical skills of Navoiyazot to give the green light to go ahead without direct supervision with the machines under warranty.
The daily activities on site were completely reorganised for better communication with the head offices, in particular:
- A daily conference call with participation of MAN and Casale head offices was set at a convenient time for Uzbekistan and Europe, to assist the site team with the required input information, to strictly monitor the status of completed activities and expedite the solution of issues and outstanding works.
- A dedicated WhatsApp group was created, to share instructions and information available on site.
- A mobile phone was dedicated to communication with MAN via its Primeserve Eyetech registered software.
- A Casale senior rotating equipment engineer was assigned full time to follow this activity.
- Two MAN commissioning supervisors were involved on a daily basis, ten hours per day, six days per week, one focused on the instrumental and control side and the other focused on the mechanical side.
- A Casale expert in the installation of turbomachinery and an expert of Siemens S7 PLC (MAN architecture), were specifically hired on a contract basis for this task, and urgently sent to site by private jet.
- Thanks to the MAN ES equipment being designed for digital, by using the installed hardware and software it was possible to remotely connect to the control system of the turbomachinery equipment from Europe via an internet connection and directly access the local programmable logic controller (PLC) and human-machine interface (HMI) for data analysis and tuning of control parameters.
The first task completed via remote support was the shaft alignment of this complex train that was finalised on 3 April 2020. During this month the instrumental loop checks were performed as well as the commissioning of the auxiliaries and of the process valves in MAN‘s scope (sealing system, condensing system etc).
Having successfully completed the cold commissioning and with the lockdown and travel restrictions still in place, Casale and MAN decided to continue remotely with the “hot commissioning” .
After the successful mechanical running test of the train, the surge test of the air compressor was performed. This was an especially critical test because the air compressor is an axial machine and is very sensitive to surge. On the day of the test key personnel on site were assigned to different tasks such as the monitoring of machine noise, machine vibration, or the control of integrity and noise in the suction filter. Personnel in charge of carrying out testing and tripping of the machine in case of issues, as well as MAN specialists, were online from Germany and connected to the graphic pages and via phone.
After the surge test, several other commissioning activities were carried out and on 16 May MAN gave the green light to start the entire train for plant operation.
During the initial plant operation intense troubleshooting was carried out to solve the kind of problems that normally occur in this phase. The troubleshooting process was particularly efficient thanks to the prompt attention of MAN’s head engineering department, which was basically on-line and connected in real time to the plant, able to direct support and knowhow by remote assistance.
During the cold and hot commissioning phases, besides applying their skills and experience, the customer was also fully immersed in on-the-job training, starting to operate the equipment after a few days of operation.
Platinum gauzes and installation of catalysts
The installation of the platinum catalyst gauzes, worth millions of euros, is critical for the performance of the plant, for the emission guarantee and for the relative guarantee of the catalyst performance itself.
Due to the pandemic, the original conditions of the contract were modified, according to the new work environment but maintaining the original performance guarantee.
The Casale field department provided remote training to the Casale site worker to clarify all steps of the installation for the platinum gauzes and the secondary catalyst. All of the activities were managed by Casale headquarters with the vendor Krastvetmet providing remote support during all installation phases. The installation of catalyst for the abatement system is also a critical and essential activity to guarantee the performance of the catalyst and to satisfy the atmospheric emission guarantee. Casale field workers on site managed all of the activities with headquarters providing remote support during all installation phases. Installation was performed following the Casale Dense Loading procedure and since the catalytic reactor is a proprietary Casale item, the catalyst vendor was not involved in the remote loading (Fig. 6).
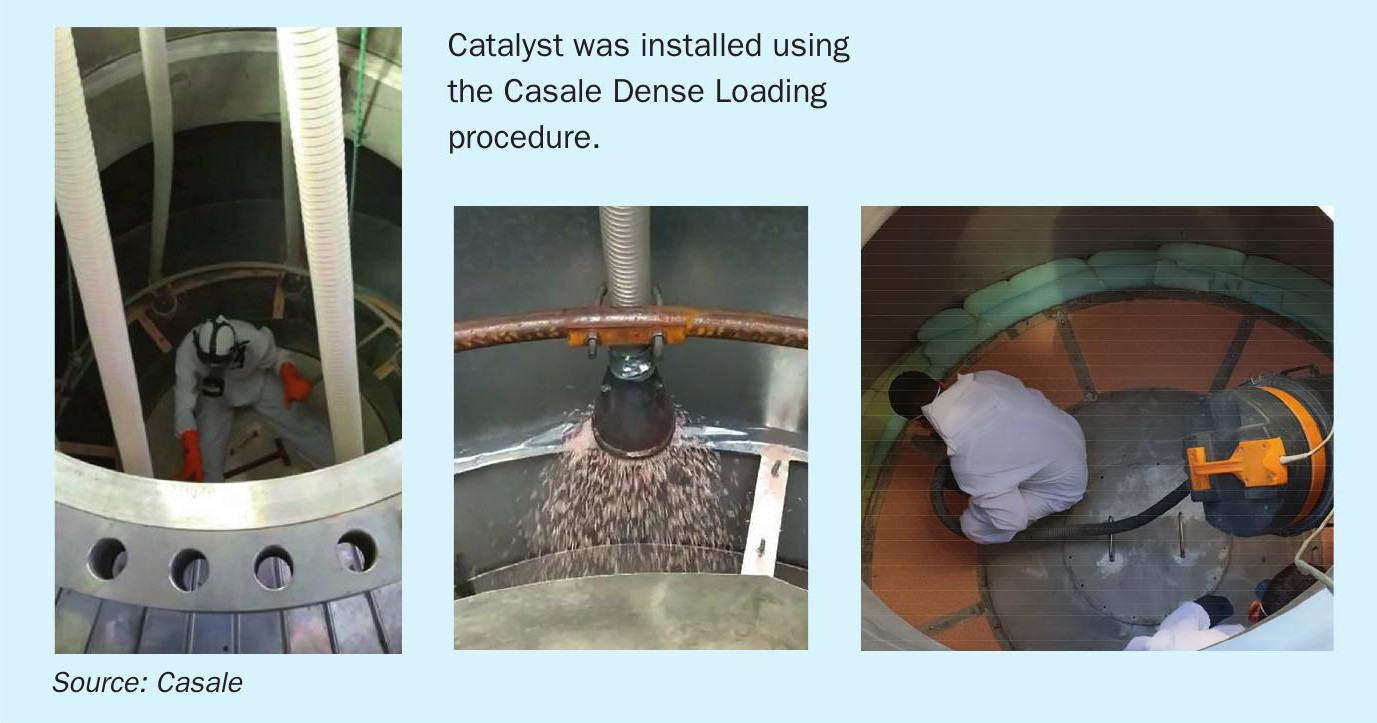
Water treatment plant
The water treatment plant, supplied by Unidro Company, is composed of several items of equipment and sub-systems (like multi-media filters, reverse osmosis, EDI, lamella clarifier, centrifuge, resin tower, evaporator, chemical dosing systems etc.), some of which are supplied by Unidro’s sub-vendors.
The equipment and sub-systems were manufactured, assembled and packaged mainly in Italy and then delivered to site.
A flexible approach to commissioning was adopted for the water treatment, in particular a temporary solution (with the use of desalted water from the client instead of raw water) was implemented to by-pass part of the system and achieve the requested demi-water production required for commissioning of the process unit and plant start-up.
By using this approach it was possible to bypass part of the system devoted to the demi water production during commissioning (filtration through multi-media filters, reverse osmosis for cooling water production, chemical dosing systems) and temporarily produce demi water with the support of only one commissioning supervisor, during border closure, at a time when other Unidro commissioning staff experts were unable to reach Uzbekistan. This approach also overcame the problem of pandemic-related delays to the delivery of some chemicals for demi water production, as chemicals were not necessary during operation with the temporary configuration of the unit. With Uzbekistan in lockdown, the earliest Unidro experts from Italy were able to reach Uzbekistan was early June 2020.
A limited group of Unidro experts dedicated to commissioning (a commissioning manager, an automation specialist, an instrument specialist and a mechanical specialist) reached Uzbekistan by private jet organised by Casale. Therefore part of the commissioning and start-up activities were remotely assisted from Unidro offices in Italy and from Casale head office in Switzerland, together with the local team in Uzbekistan, as follows:
- Two conference calls per week with participation of Unidro and Casale head office experts was implemented at a convenient time for Uzbekistan and Europe, to assist the site team with the required input information, and to strictly monitor the status of completed activities and expedite the solution for the issues and open points. Daily assistance was also assured from Casale head offices in Switzerland.
- A Casale packages section manager, utilities and off site manager and a senior process engineer E&P followed this activity from the Casale head office in Switzerland.
- A Unidro process specialist was remotely involved on a daily basis from the Italian office and then spent 15 days only on site for the most critical phase of the zero liquid discharge section commissioning.
- All sub-systems, in particular machinery, such as the centrifuge, were commissioned by Casale and Unidro commissioning specialists, by assuring the correct level of technical expertise without the support of Unidro sub-vendors specialists.
The first task which was completed in this way was the cooling and demi water production from raw water that was completed on July 30, 2020.
Successful start-up
Nitric acid production started successfully at the end of May 2020. This was a milestone for a new way of digital supported commissioning.
For the first time, tens of engineers assisted people remotely at site, coordinated the activities and the manpower in perfect symbiosis and were able to smoothly start a nitric acid plant.
This success story is a lesson for the future, and demonstrates that a remote assistance methodology during plant commissioning is not only a possibility, but also brings some great benefits: optimisation of costs, and the availability of the right competences and knowhow anytime.
KBR quality control, remote inspection & commissioning
During the coronavirus Covid-19 pandemic KBR has overcome unprecedented challenges to meet client commitments on delivery of equipment. The vital activity for manufacturing is quality control and Inspection. While quality control is a lead indicator where KBR has been a pioneer in laying out systems and procedures to surpass global standards in manufacture, inspection being a lag indicator is an essential check and balance for sound product quality. The inspection stages during manufacture and the inspection reports contribute to client satisfaction and confidence on the product delivered.
In the pandemic situation when global travel is limited, including inland travel, remote inspection, which was already in vogue, on an as needed basis, has become critical to success. KBR has swiftly adapted to the situation and implemented remote inspection with the support of manufacturing partners. Remote inspection is an alternative to an onsite physical inspection in which the person performs inspection activities remotely using sophisticated technological tools.
Benefits of remote inspection
- Efficient − flexibility
- Access global expertise without constraints of travel
- Enables concurrent decision making
- Data can be captured and recorded for future reference.
- IP Protection
- Elimination of personnel risk exposure to hazardous conditions and dangerous tasks in harsh environments
- Sustainability
– Removes geographical boundaries
– Better customer experience
– Saves money, time and travel
– Reduces organisational carbon footprints
– Identifies and mitigate risks in real time
What is quality? Quality means doing it right when no one is looking (…by Henry Ford). This is the most apt meaning under the current pandemic situation.
Why inspection? Inspection is like a medical check-up before term insurance, it meets contractual requirements and local regulations requirements.
Remote inspection, although not a new concept, has recently been getting more attention due to the Covid-19 pandemic and can also be the future of digital offerings.
The following digital tools were successfully deployed for carrying out inspection and commissioning functions remotely by KBR (see also Table 1):
- Google Glass/Epson Smart Glass;
- MS Teams/Star Leaf/Skype Business;
- tablets/mobiles/cameras;
- KBR’s Insite offerings.
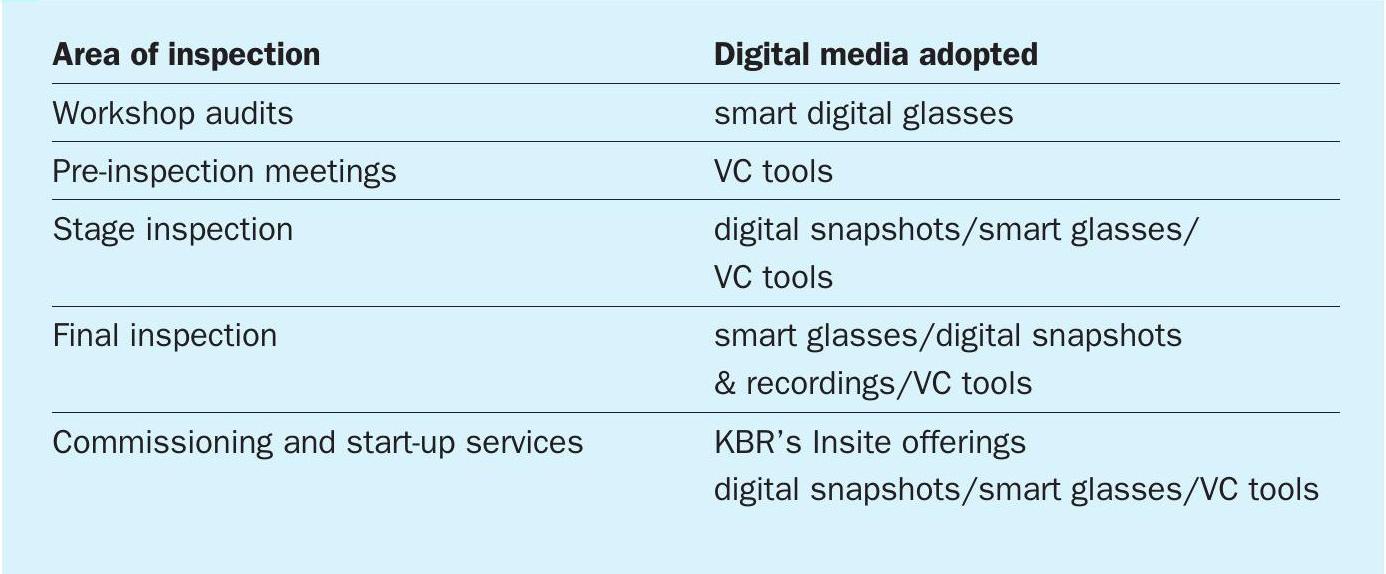
During the pandemic KBR has inspected and supplied many items of proprietary equipment (PEQ) to clients across globe. All inspections and commissioning operations were monitored remotely using high end digital tools. One grassroots ammonia plant, an FCC revamp and commissioning support for an ethylene cracking plant were all carried out remotely by KBR (Fig. 7). There are a number of prerequisites for successful remote services (monitoring/inspection/commissioning).
Supply chain partners should have:
- Digital tools such as:
– Google glass, VC Tools (MS Teams, Skype Business etc.)
- Advanced NDT gadgets
- Laser scanners
- Good internet connectivity
KBR and client should have:
- Technical and product knowledge
– understand the potential of cutting-edge ideas and apply it pragmatically
– technical expertise to create long-lasting value through collaboration
- Cloud based database to capture all real time data
– for reference in trouble shooting, maintenance and repair
– to support standardisation
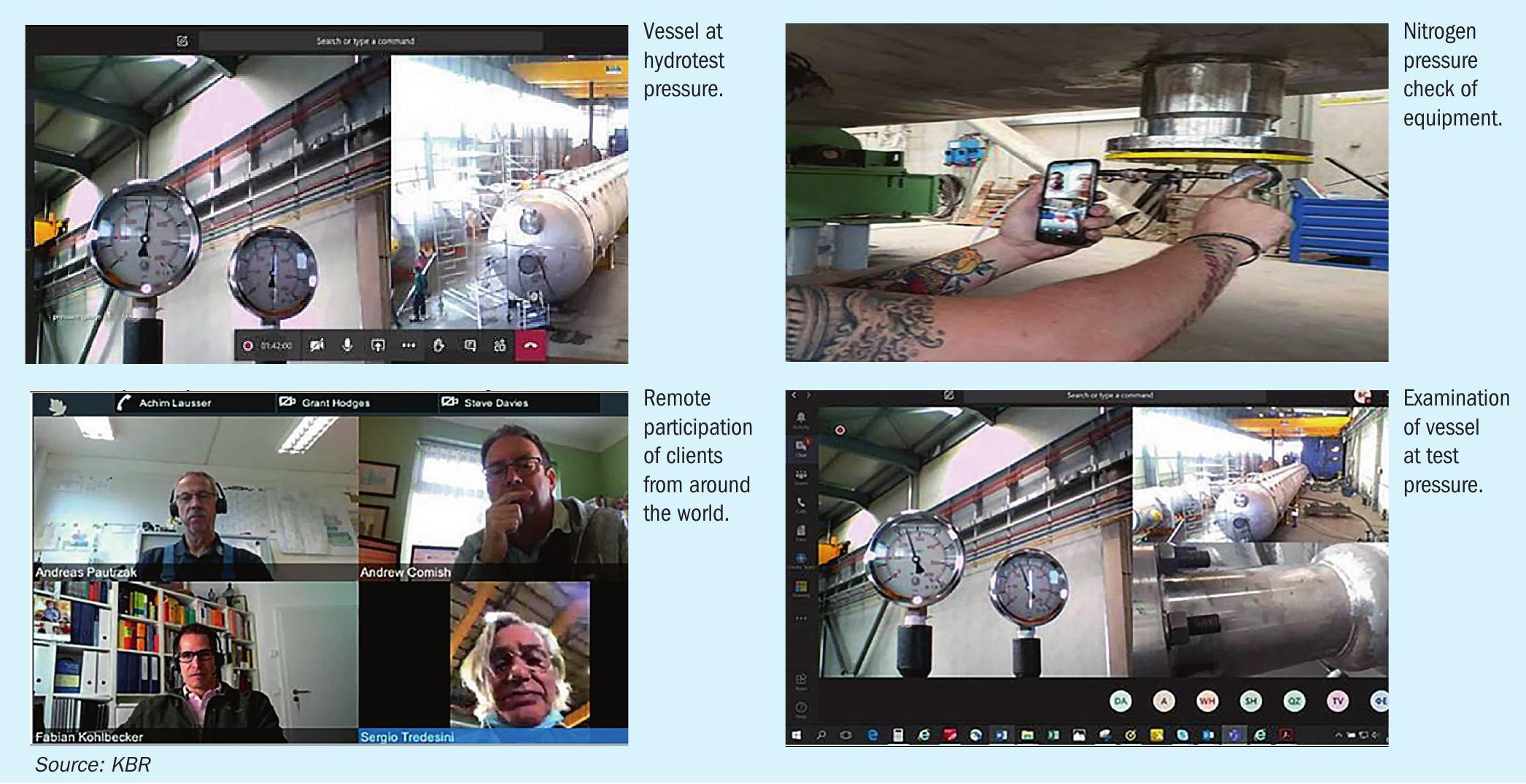
Over the last nine months, equipped with all the requisite digitisation tools and with client acceptance of the remote offering procedures in place, KBR has been able to offer the following services:
- technical assessments;
- pre-inspection meetings;
- shop survey and audits;
- in-process surveillance, notified witness or hold points, and final inspection;
- site commissioning and start-up services.
KBR is now getting actively engaged with all of its stake holders to upgrade their systems and procedures with:
- Advanced NDE examinations/techniques.
– Digital radiography of PEQ offerings
– TOFD / PA ultrasonic examinations This will enable the client/KBR to access all NDE records of a vessel from their desks.
- Laser metrology instruments for dimensional inspections – This will enable all dimensional inspections to be viewed through reverse engineered drawings.
- Drone-assisted inspection services.
With the successful implementation of these digitisation tools KBR aspires to a fusion of remote offerings with artificial intelligence (AI) for a future of safe and sustainable operations.
References