Fertilizer International 500 Jan-Feb 2021
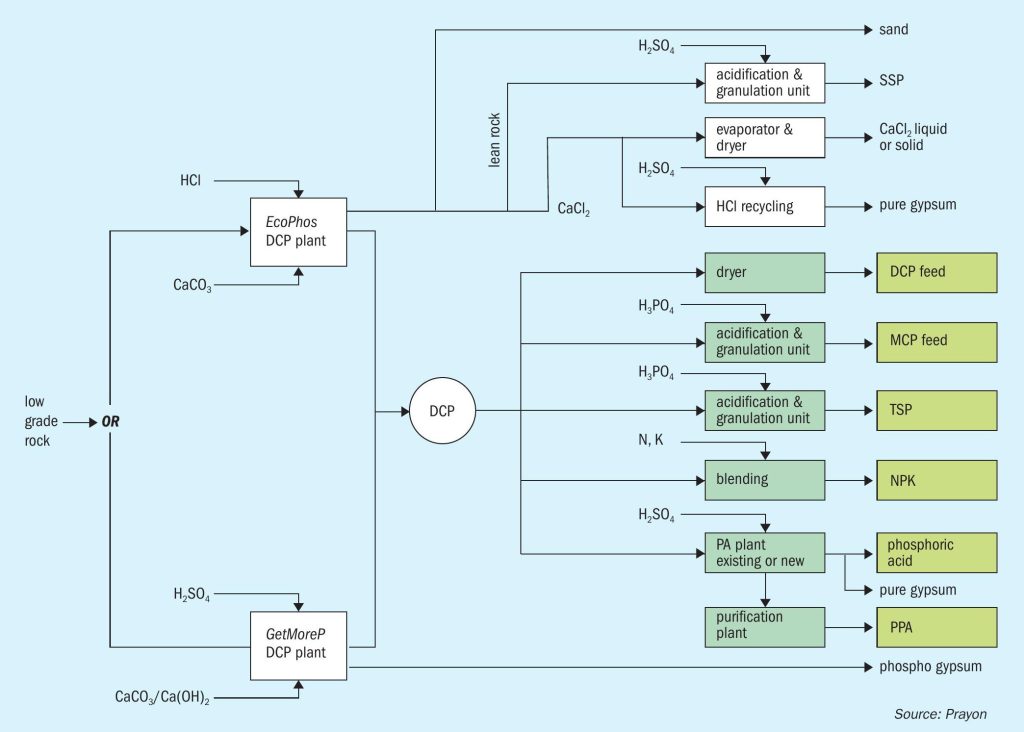
31 January 2021
Innovations in phosphate production
PRODUCTION TECHNOLOGY
Innovations in phosphate production
Prayon’s Hadrien Leruth and Marc Sonveaux highlight the latest phosphate production developments at the company – and share their experience of how innovative ideas are validated, industrialised and turned into commercially-viable technologies.
Prayon rhymes with innovation
Prayon is renowned for its commitment to research and development. The Belgium-headquartered company constantly invests in innovation to maintain its status as a global leader in technical- and food-grade phosphate production and phosphoric acid technologies. In the current world context – especially in the phosphates market – Prayon believes that innovation is a must, if we are to tackle present and future planetary challenges.
The company invests more than e10 million in innovation each year. This spending is funnelled through Prayon’s R&D centre in Belgium, where it is used to develop and validate new technologies for the phosphates industry.
New to the technology portfolio
Prayon also pursues innovation through acquisitions, most notably the recent purchase of the technology patents and know-how from EcoPhos. Importantly, the acquisition of the EcoPhos brand also included full ownership of its Bulgarian R&D site – which includes the Technophos pilot and demonstration plants.
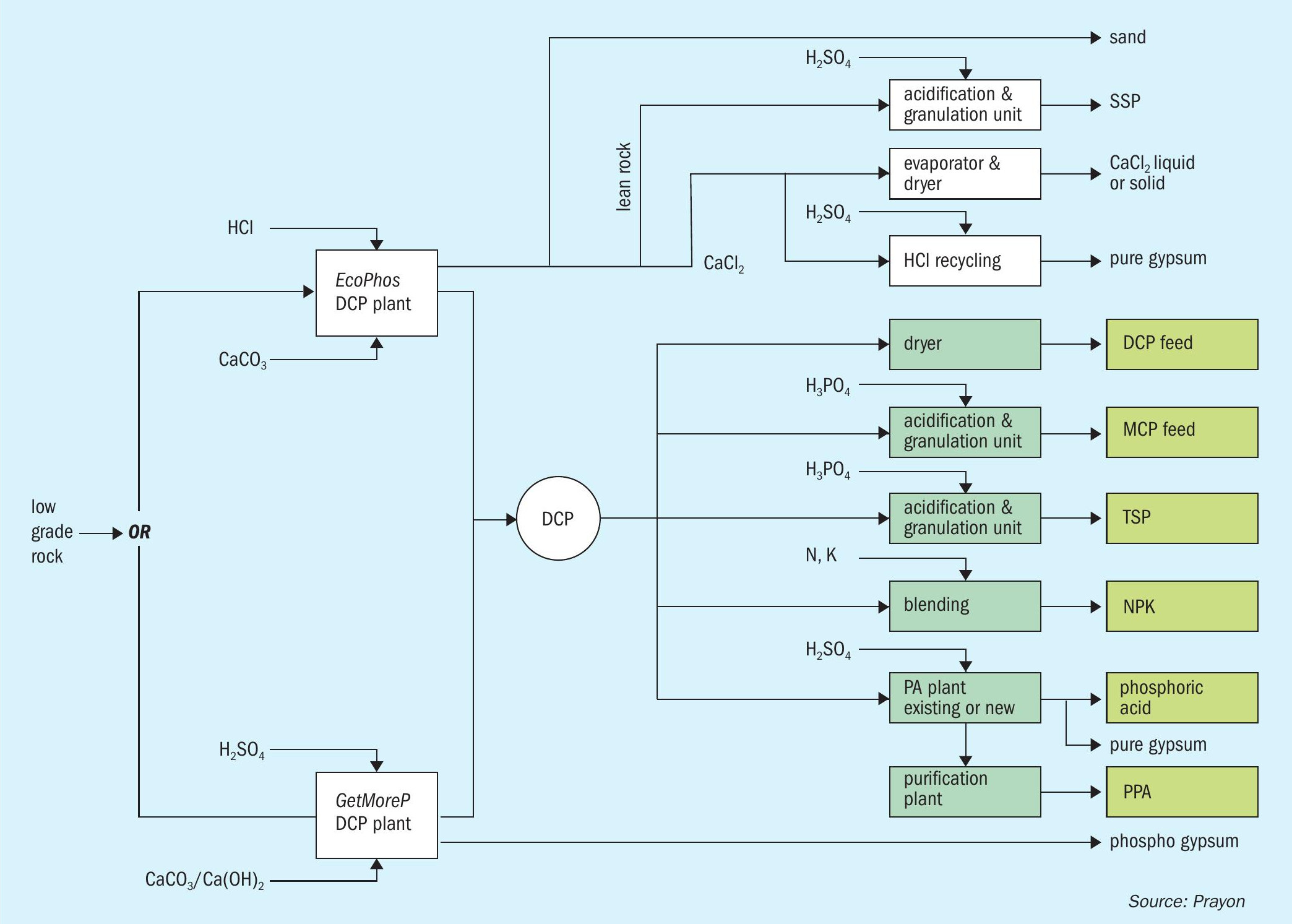
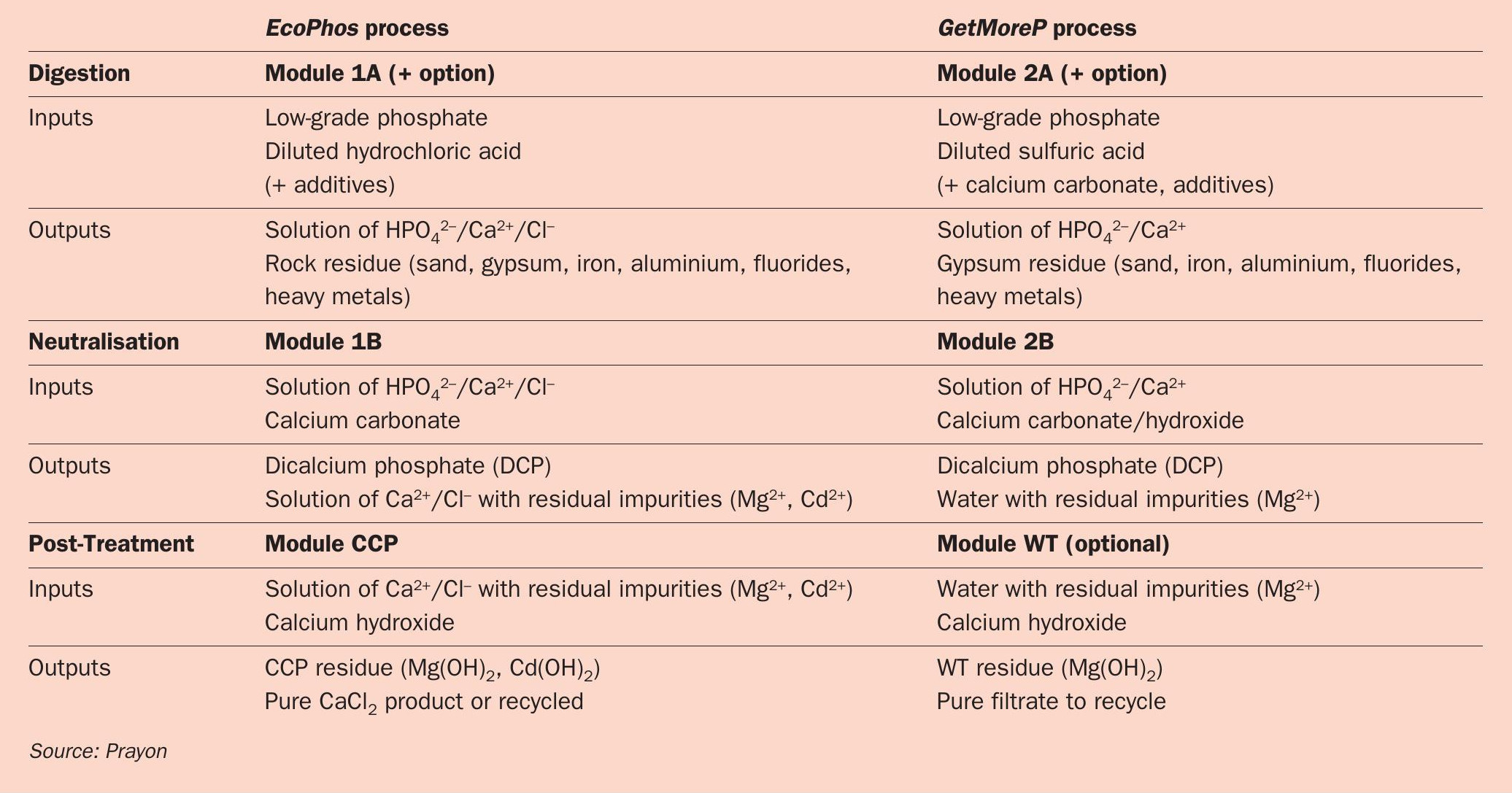
The purchase of EcoPhos has enabled Prayon to extend its technology portfolio into new market areas. Indeed, the company – through its Prayon Technologies licensing division – plans to introduce a raft of new technologies to complement its famed and widely-used phosphoric acid production processes.
The new technologies include:
- The chemical beneficiation of low-grade phosphate rock
- Secondary phosphate recovery/recycling processes
- The PUMA membrane purification system
- The new DA-HF phosphoric acid production process.
Each of these innovations are described below. Bringing these to market will help Prayon Technologies achieve its mission to deliver the best technical solutions to customers by meeting two targets: making production sustainable while at the same time boosting its profitability.
Chemical beneficiation technologies
Prayon has recently shown a huge interest in developing and acquiring new technologies that are capable of recovering phosphate commercially from low-grade deposits. This has become an imperative, given the steady decline in both the size and quality of phosphate rock resources globally.
It has become clear that chemical beneficiation, when applied to low-grade phosphate rock, is potentially more profitable than traditional physical beneficiation techniques as it is more efficient and consumes less energy.
With this in mind, Prayon now offers two chemical processes (Figure 1) in its portfolio for beneficiating low-grade phosphate rock:
- The recently-acquired EcoPhos process – an innovative technology based on the use of dilute hydrochloric acid
- GetMoreP, a similar in-house technology developed by Prayon based on the use of dilute sulphuric acid.
Both processes generate dicalcium phosphate (DCP). This flexible end-product can be directly marketed as an animal feed additive. Alternatively, it can be used as a high purity intermediate feedstock (3941% P2 O5 and 32-34% CaO) for phosphoric acid plants, enabling the manufacture of a range of other phosphate products.
The EcoPhos and GetMoreP processes have a number of similarities:
- They are both modular (Figure 2)
- They generate the same quality DCP product
- Each are capable of consuming low-grade phosphate rock.
Their main differences are:
- The stages at which impurities are removed
- Different co-products are generated due to the use of different types of acid to digest phosphate rock.
Individual modules for both processes with their contrasting inputs and outputs are shown in Table 1.
The EcoPhos process
The EcoPhos process has four main modules (Figure 2).
- Module 1A
- Module 1B
- Module CCP
- Module 4.
Each of the above modules, by combining a reaction step with a filtration step, generates a filtrate (solution) and a filter cake (solids).
In the first process step, Module 1A, phosphate rock is digested using dilute hydrochloric acid. These benign process conditions enable the selective digestion of phosphate. Many impurities (silica, gypsum, iron, aluminium, most heavy metals and fluoride), meanwhile, are directly eliminated at this stage as a rock residue. This insoluble fraction is removed by filtration, yielding a clear phosphate solution.
This filtrate consists of soluble monocalcium phosphate (MCP), phosphoric acid and calcium chloride, together with some residual impurities such as magnesium or cadmium.
In the next step, Module1B, by adding calcium carbonate or limestone, the pH of the solution is gradually increased to recover the phosphate from the filtrate. This crystallises as DCP and is recovered as a solid cake by filtration.
In Module CCP, the pH of the solution is again raised to precipitate any remaining heavy metals as part of a solid residue. The remaining soluble calcium chloride solution is very pure. It can be crystallised and dried and directly sold as a de-icing or de-dusting product, as a setting agent for the concrete industry, or marketed at the oil industry.
Alternatively, using Module 4, calcium chloride can be recycled to the process by adding sulphuric acid to convert it back into hydrochloric acid. This final module, by closing the loop, decreases hydrochloric acid consumption in Module 1A while, valuably, also precipitating gypsum as a very pure co-product.
The GetMoreP process
The GetMoreP process, similar to the EcoPhos process, selectively digests phosphate from low-grade rock – this time using dilute sulphuric acid instead of hydrochloric acid. In the initial process step, Module 2A, phosphate is digested with sulphuric acid and enters solution, while calcium, alongside other impurities such as silica, iron, and aluminium, precipitates as gypsum. A further adjustment to pH removes even more impurities – mainly fluorides and heavy metals – leaving a relatively pure filtrate of soluble monocalcium phosphate (MCP) and phosphoric acid.
In Module 2B, phosphate is crystallised as DCP by neutralising the solution with calcium carbonate or limestone. This generates a reasonably clean filtrate with only limited levels of dissolved impurities. This can be further polished, if required, using an optional water treatment module (Module WT) to eliminate magnesium and other remaining contaminants.
Secondary phosphate technologies
The medium- to long-term scarcity of phosphorous raises questions about security of supply, especially in Europe. However, dependence on external primary phosphate resources in Europe, and other phosphate rock deficient regions, could be reduced by the large-scale recovery of phosphorus from waste streams. This has dual benefits as it would also cut global phosphate losses.
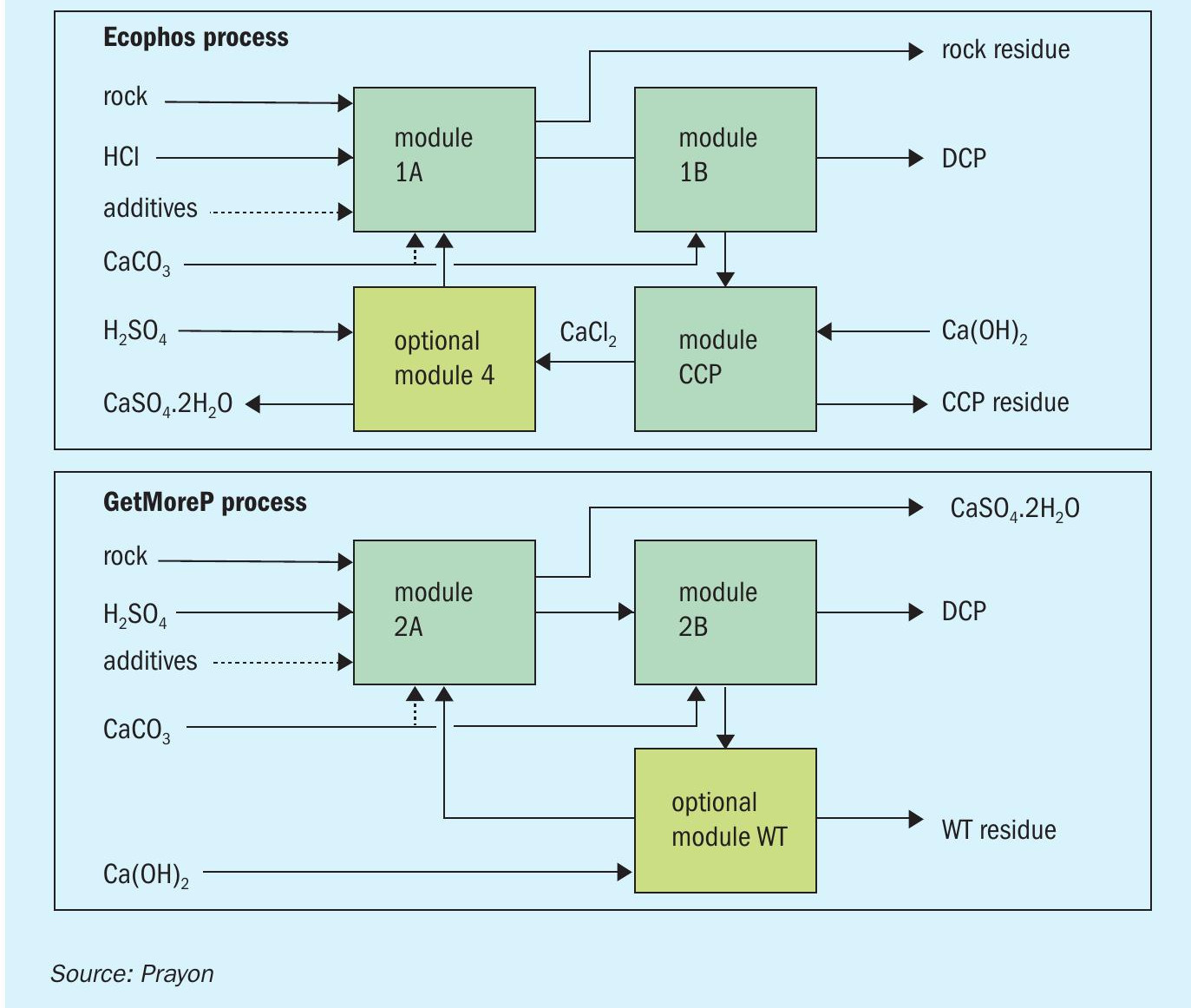
The following technology options from Prayon are capable of recovering phosphorus commercially from various secondary/waste sources:
- Recovery from phosphate beneficiation wastes (slimes, rejected rock) using the EcoPhos or GetMoreP processes
- Recycling industrial phosphoric acid waste by membrane purification
- Recovering phosphate from sewage sludge fly ash.
Recovering phosphorus via sewage sludge incineration is highly challenging due to the complexity and composition of the iron- and aluminium-rich fly ashes obtained – these typically containing up to nine percent and eight percent iron and aluminium, respectively.
Prayon offers two types of recovery technologies for sewage sludge fly ash. These are selected according to the composition of the fly ash, its location and the required end-product:
- Technical-grade phosphoric acid production. This two-stage process firstly involves the digestion of fly ash in phosphoric acid, followed by the purification of the resulting solution by ion exchange and, optionally, nanofiltration. Phosphoric acid is partly recovered as the final product and partly recycled to digest more fly ash. The ion exchange resin is regenerated by hydrochloric acid. Depending on their composition, the solutions arising from regeneration can be valorised as a de-icing product (Ca/Mg Cl solutions) or sent for wastewater treatment (Al/Fe Cl solutions). This process is safe, performed at reasonably low temperatures, and can be easily installed at sewage sludge incineration sites.
- Fertilizer-grade dicalcium phosphate (DCP) production. This process is very close to those used to digest low-grade phosphate rock described above. The main difference is that, due to their high concentration in filtrates, both aluminium and iron need to be removed by ion exchange to obtain high-quality DCP. The DCP product can be used directly as fertilizer or converted into triple superphosphate (TSP) instead.
Process selection depends on the installation location (at the incinerator or not) and the target product (DCP, TSP or phosphoric acid) – and, of course, fly ash composition.
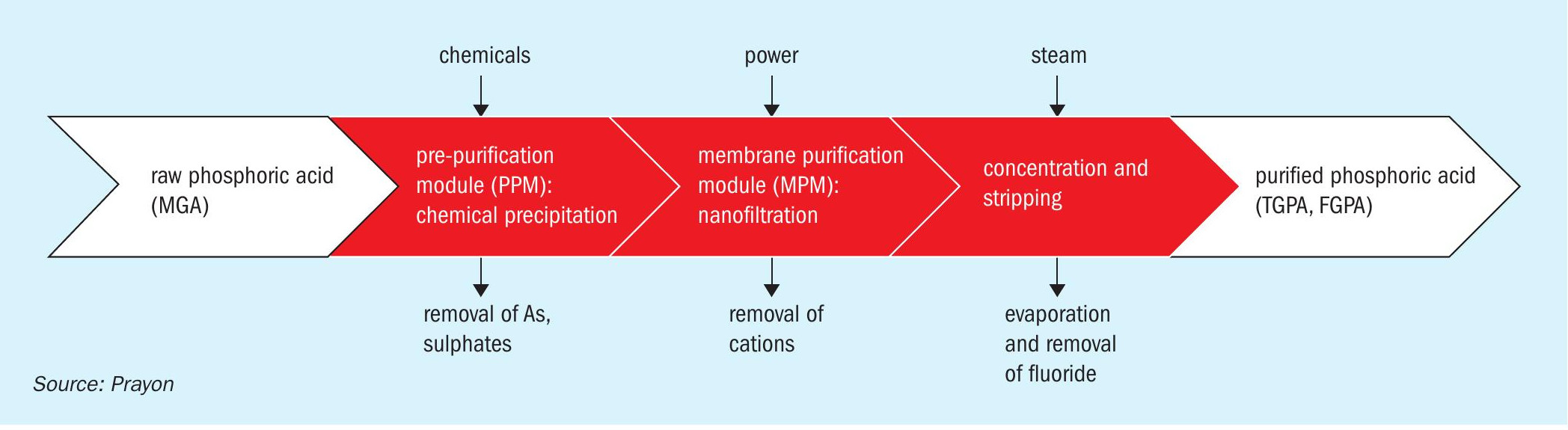
PUMA membrane purification
This innovative purification system from Prayon converts merchant-grade phosphoric acid (MGA) into technical- or food-grade phosphoric acid. The technology has been validated at the Technophos semi-industrial plant in Bulgaria (see below). Achieving food-grade quality from raw phosphoric acid requires three modules used in combination (Figure 3):
- The pre-purification module (PPM). This preliminary stage improves phosphoric acid quality to a suitable level for subsequent purification. Selected elements (As, F, SO4 etc.) are precipitated and organic matter is removed.
- The membrane purification module (MPM). This purifies phosphoric acid by removing impurities. It can be combined with an ion exchange resin finishing step, if required.
- The concentration module. The desired P2 O5 content is achieved in an evaporator and fluoride is removed.
This new purification technology offers the following advantages:
- The small size of the units means they can be delivered partially containerised in a skid – thereby limiting construction time and lowering installation costs
- The modular process is easy to install, simple to operate and only requires limited maintenance
- The highly-resistant membrane (Figure 4) developed for the process has a lifetime of more than 700 days
- It is solvent-free, making the process safe and environmentally-friendly.
PUMA membrane purification technology is perfectly practical at small- to medium-scale (typically 10,000-40,000 t/a P2 O5 capacity) and can be fully integrated within an operational phosphoric acid or fertilizer plant. Effluent and retentate streams can also be recycled to avoid almost all phosphate losses. Installation at an MGA or fertilizer production plant not only avoids water emissions it achieves yields of close to 100 percent by recycling all P containing process streams.
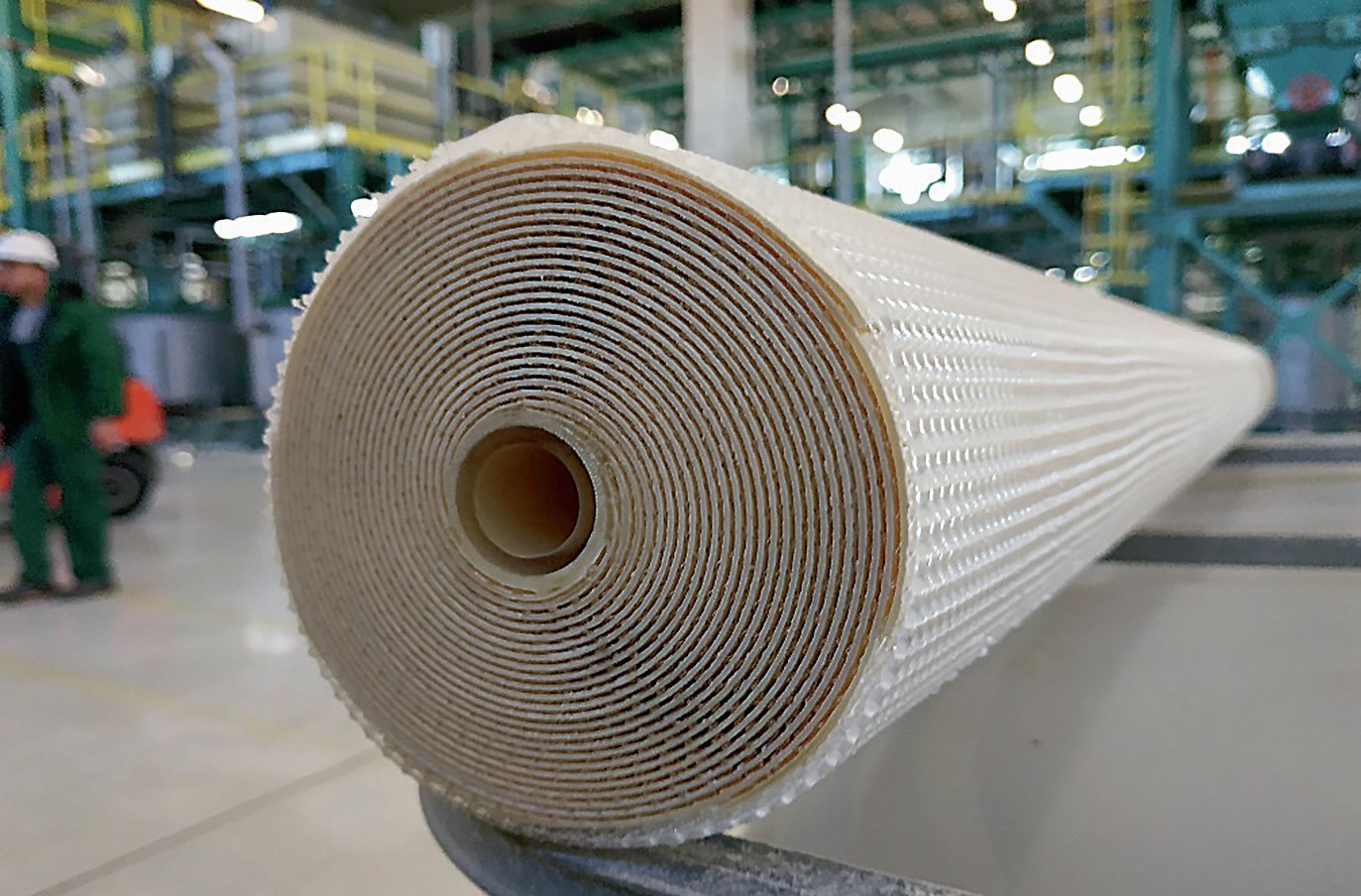
Prayon’s new DA-HF Process
Most of the world’s phosphoric acid is produced via the DH (Di-Hydrate) process route. For some years now, Prayon has been developing an improved phosphoric acid production process known as DA-HF (Dihydrate Attack-Hemihydrate Filtration).
DA-HF and its underlying assumptions have been thoroughly tested at pilot-scale at Prayon’s Engis site in Belgium.
Compared to the standard DH process, Prayon’s DA-HF process has a number of distinct advantages:
- The weak product acid contains higher P2O5 levels of up to 34 percent
- This allows merchant grade acid (MGA, 54% P2 O5 ) to be produced using smaller concentration units
- A higher process efficiency with P2 O5 recovery above 97 percent
- Less water is consumed during washing of the calcium sulphate cake
- The hemi-hydrate (HH) calcium sulphate by-product obtained is suitable as a cement additive.
The DA-HF process was recently installed at Grupa Azoty’s plant in Police, Poland, as part of a revamp project (Fertilizer International 496, p52). This has demonstrated that DA-HF can be easily and successfully implemented at existing DH phosphoric acid plants with only a limited number of modifications. This first-of-its-kind DA-HF plant increased:
- Plant P2 O5 capacity from 420 t/d to 500 t/d
- Its global efficiency – with total P2 O5 content in the discharged cake decreasing from 2.5 percent to 1.2 percent
- The P2 O5 content in the product acid to 32-33 percent
- The quality of the calcium sulphate by-product
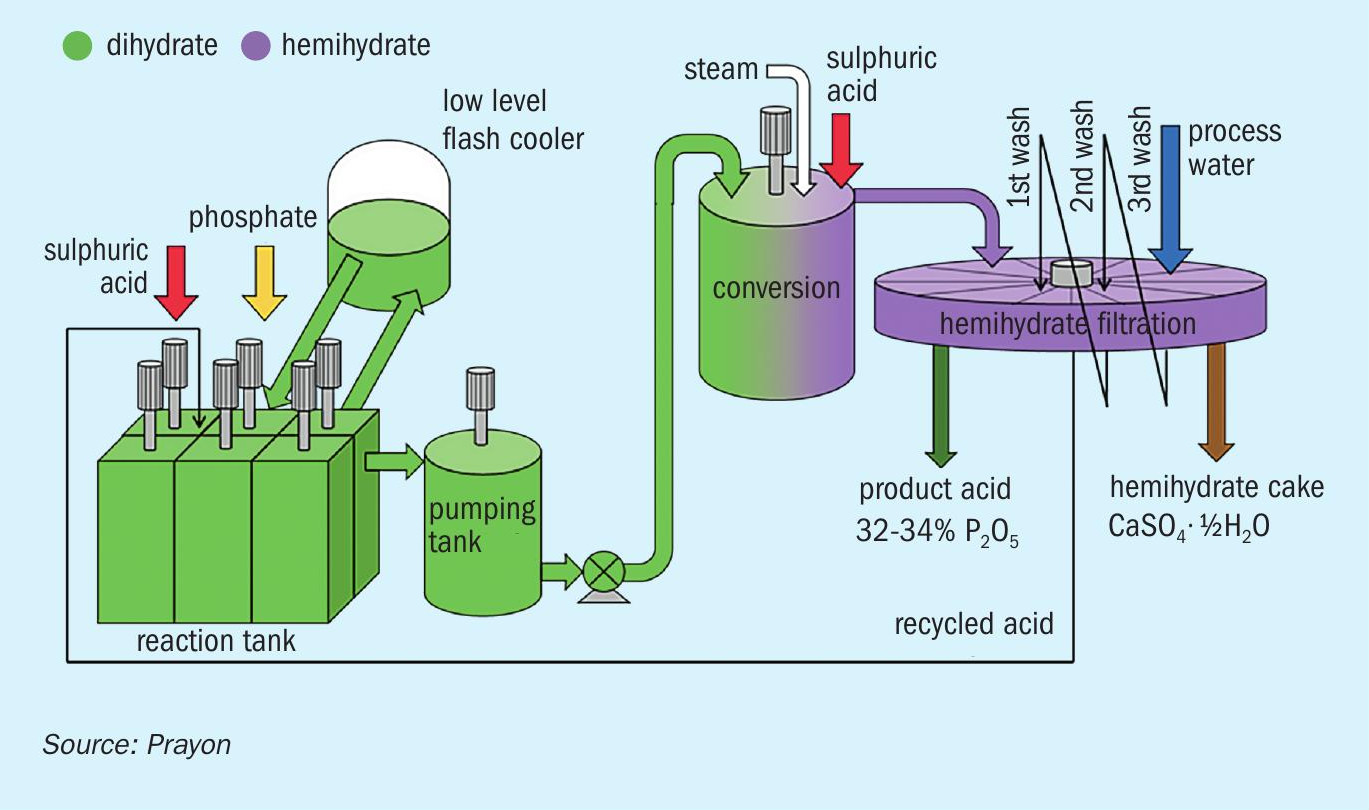
Unlike the very high efficiency CPP (Central Prayon Process) operated by Prayon in Engis, Belgium, only one single filtration stage is required in DA-HF. This makes DA-HF simpler and easier to operate compared to CPP. Beneficially, the process also removes undesirable cadmium at the concentration stage.
Process validation at Technophos
In addition to its R&D centre in Belgium, Prayon owns the Technophos testing site in Varna, Bulgaria (Figure 6). This centre of excellence, which originally opened in 2016, can validate most of Prayon’s innovative technologies at pilot or semi-industrial scale.
Technophos is able to mimic full-scale industrial plant conditions, housing a large array of scaled-down equipment items within in a modern 3,000 square metre building. The available items include press-filters, reactors fitted with agitators, vacuum belt filters (Figure 7), hoppers, buffer tanks, granulators, dryers, multiple conveyors etc.
While Technophos was originally designed for the EcoPhos hydrochloric acid based process, it is also perfectly suited to running the GetMoreP process at semi-industrial scale. Both processes can be operated at feed capacities of up to 500 kg/h (Modules 1A or 2A).
Additionally, Technophos also offers several pilot-scale units that allow process parameters to be adjusted and validated before scaling-up to semi-industrial capacity. This has allowed the PUMA purification process to be demonstrated at pilot–scale with the testing of specific membrane configurations to optimise purity.
Technophos is also a training centre where future plant operators can learn about production processes first-hand by operating the semi-industrial plant on their own. An experienced team of 35 staff are also on site to offer their guidance and coaching to trainees.
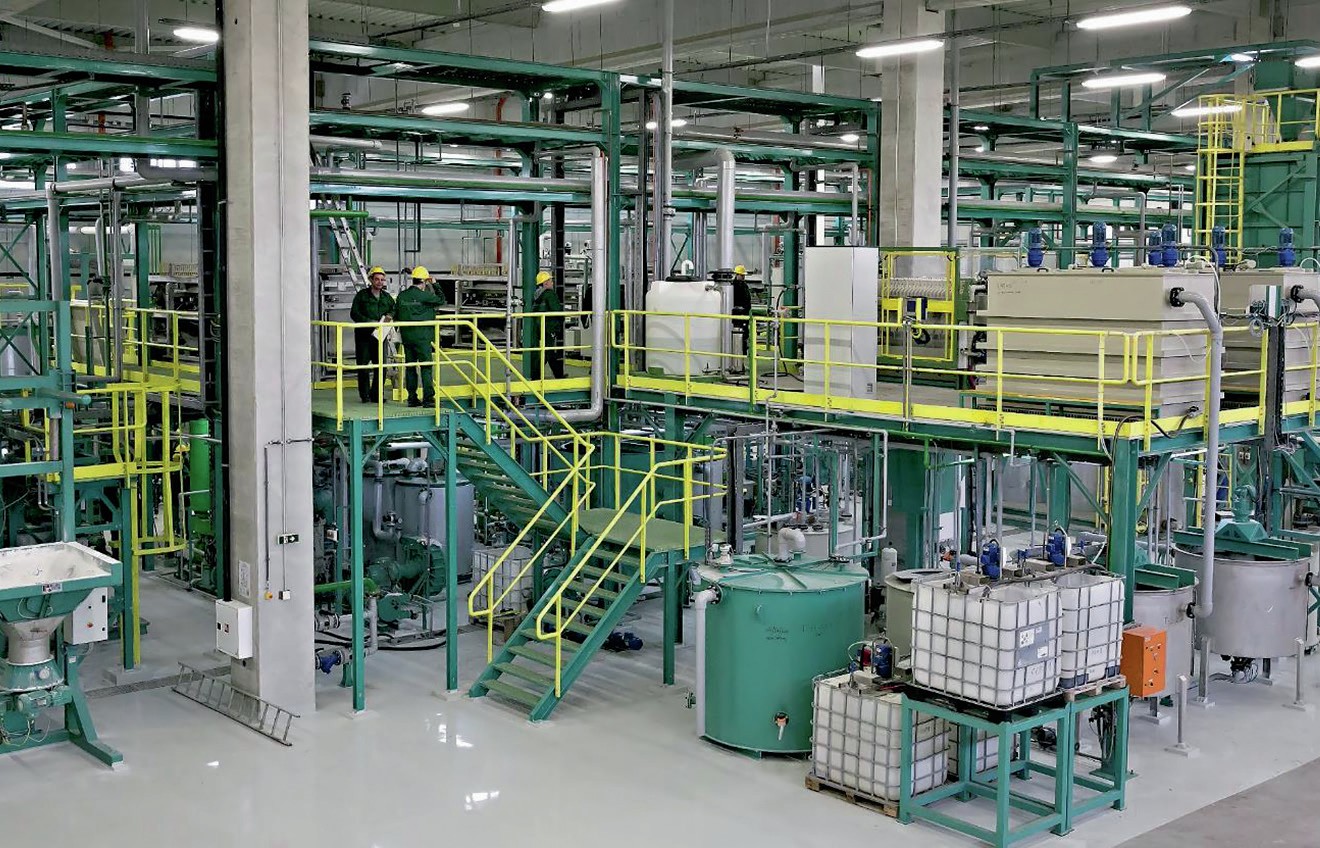
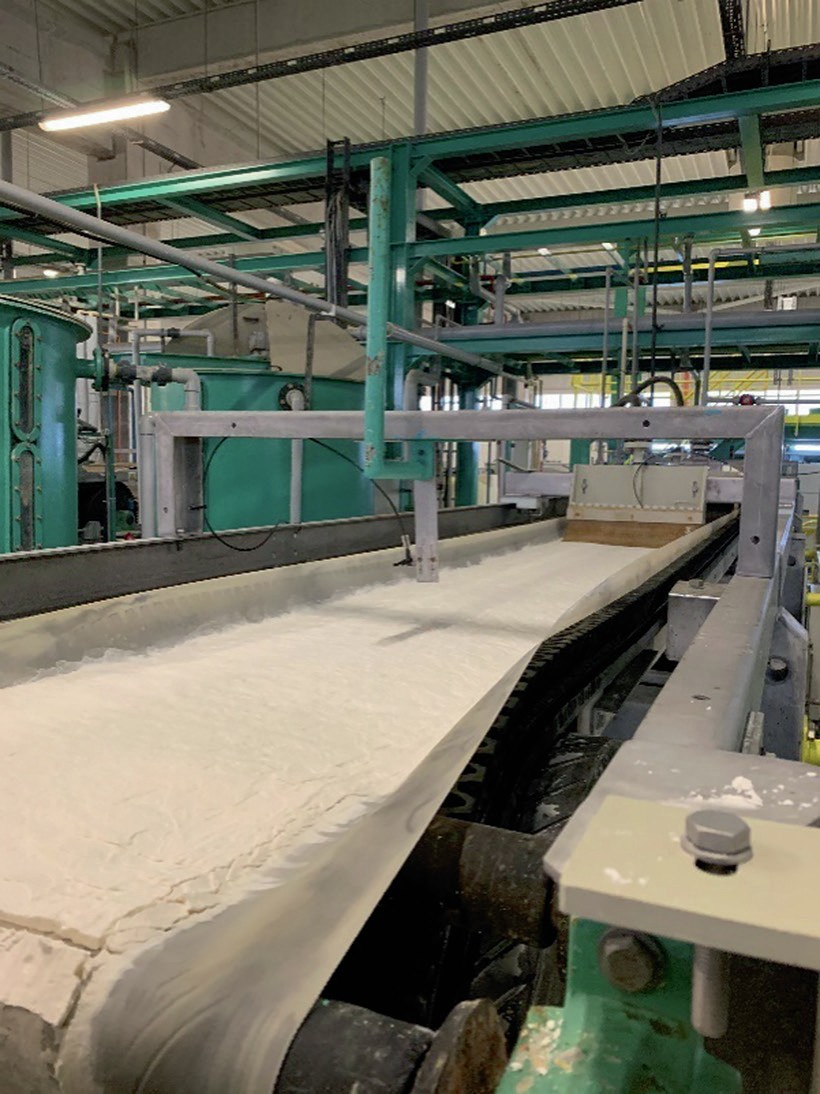
Conclusions
The phosphate technologies described in this article are the tip of the iceberg – being just the latest innovations to emerge from continuous large-scale investment in research and development. Indeed, with its expanded portfolio, Prayon is able to match the most suitable technology, both economically and environmentally, with individual project requirements.
Prayon’s business activities are unusually broad – encompassing process technology and licencing, projects, equipment manufacture, production and products. Such wide-ranging phosphate industry expertise is beneficial, as it allows the company to offer customers unrivalled support, both on operational improvements and the installation of new technologies. Prayon itself has been an international producer of high-quality phosphates for many decades, operating four plants in Belgium, France and the United States. Collectively, the breadth and depth of its expertise allows Prayon to take innovative ideas, validate and test these at scale, and transform them into commercially-viable technologies.