Sulphur 392 Jan-Feb 2021
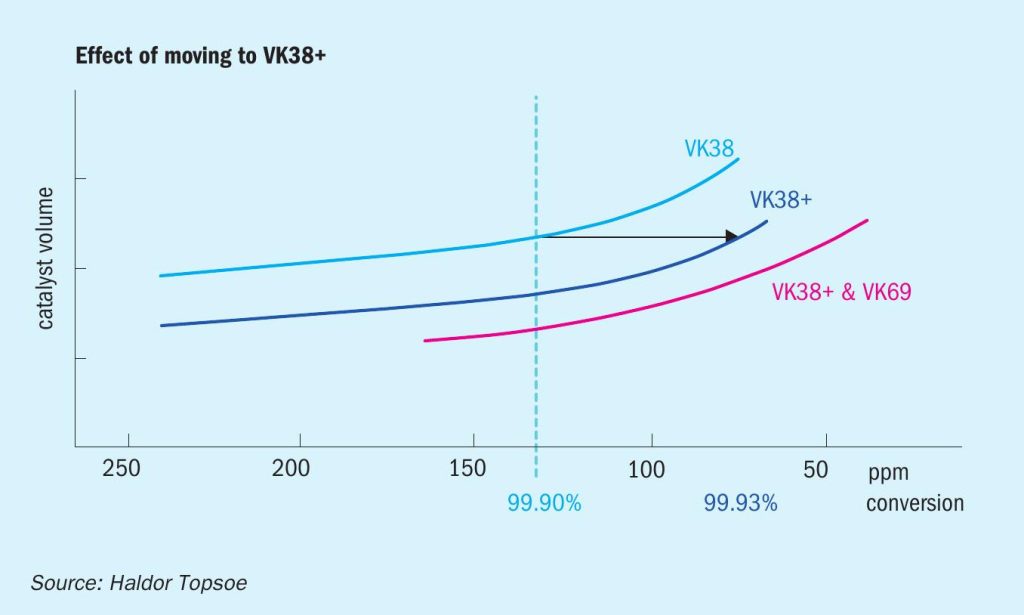
31 January 2021
New catalysts target key industry challenges
SULPHURIC ACID CATALYSTS
New catalysts target key industry challenges
Selecting the right catalysts for the SO2 converter in a sulphuric acid plant has always been about balancing expenses, gains, and compliance. With increasing demands for sustainability and in challenging economic times, operators need to adjust their plants to get even more from less. This has led to market demand for new catalytic solutions that offer better productivity and a lower climate footprint, all at the lowest cost possible. Catalyst design and formulations continue to evolve with Haldor Topsoe, DuPont Clean Technologies and BASF all adding new types of sulphuric acid catalysts to their portfolios.
HALDOR TOPSOE
Tipping the scales with VK38+ catalyst
VK38+ is a new potassium-promoted catalyst that is part of a range of proven, top-performing sulphuric acid catalysts from Topsoe. This catalyst stems from more than eight decades of catalyst innovation and is a move forward from existing solutions.
A successful catalyst needs to address three crucial parameters: high activity, good strength and low pressure drop. Typically, designing a catalyst is a compromise between these parameters. It is difficult to improve one without sacrificing at least one of the others. With VK38+, Topsoe’s R&D has succeeded in developing a new catalytic material that provides significantly higher activity than that of the regular VK38 at all relevant conditions. It does so without compromising the strength of the catalyst pellets. By using the well-proven Daisy shape, the pressure is at the same industry-leading low level as for the existing VK-range.
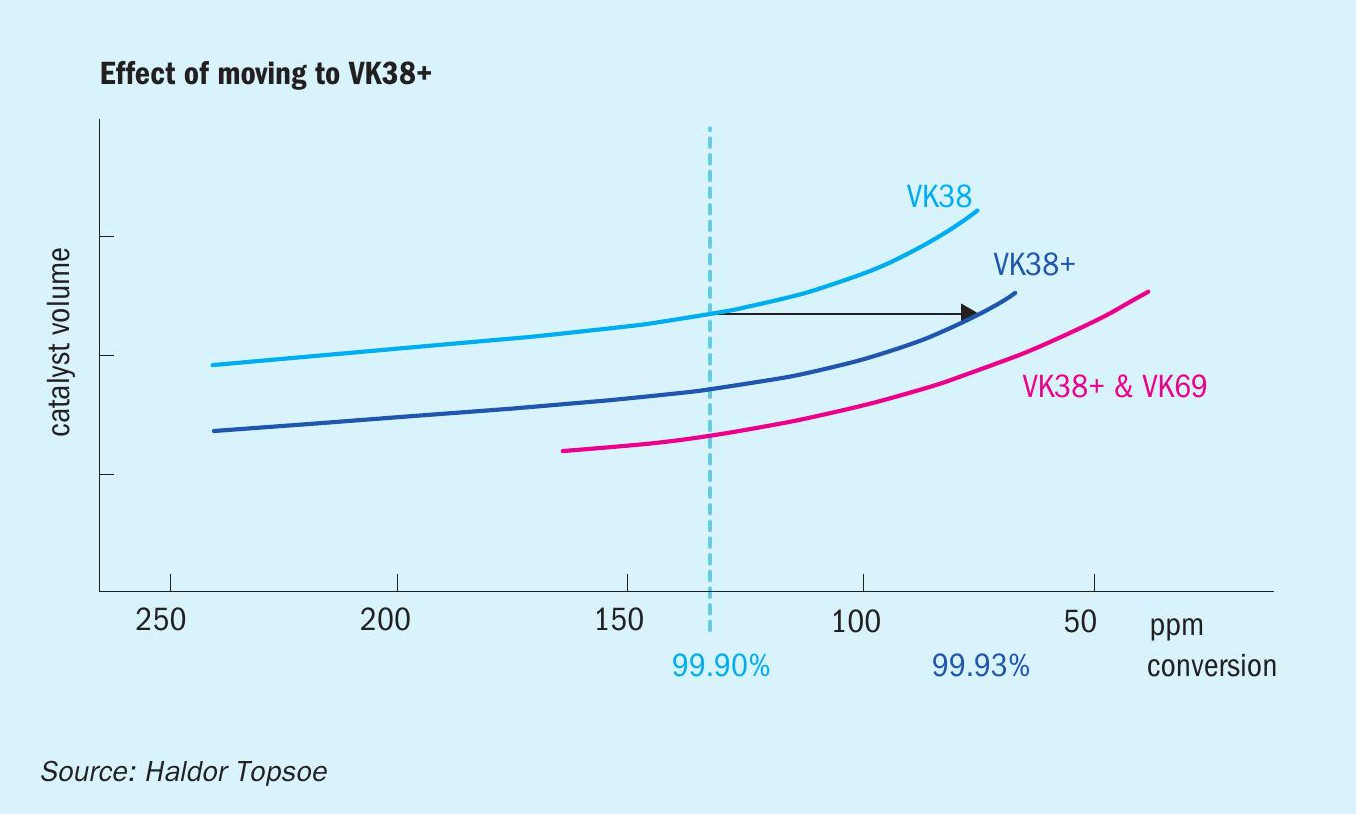
The versatility of VK38+ allows operators to target plant bottlenecks that could previously not be addressed, increase the flexibility of the plant, and ease stock management.
Fig. 1 illustrates how VK38+ can be applied to cut SO2 emissions when converter space is limited. The achievable conversion is dependent on the catalyst volume available, with VK38+ higher conversion can be achieved with a fixed volume. As an example it is possible to increase conversion from 99.9% to 99.93% by moving from VK38 to the same volume of VK38+.
The graph also shows how the new potassium-promoted catalyst is situated between a regular potassium-promoted loading and a premium solution based on a caesium-promoted catalyst.
Furthermore, the graph shows how the new catalyst can be used alone, or together with premium catalyst, depending on the specific goals and requirements of the individual plant.
VK38+ offers superb activity over a wide range of operating conditions. While most high-performance catalysts are optimised for specific conditions, VK38+ stands out as the only catalyst on the market that can boost performance in all SO2 converter beds.
Improved economics
For many operators, improving plant profitability involves maximising throughput at a minimum investment. Many operators have already taken this route and more often than not there is no room for additional catalyst. Operators are therefore forced to turn to more expensive specialty catalyst or even plant revamps to push performance further.
With VK38+, operators can tip the scales to their advantage and create a more cost-effective solution. VK38+ offers significant performance increases in all converter beds, without the cost increase associated with a caesium catalyst solution. This performance increase means there is a new option for operators who want to use increased capacity as a means to improve profitability.
Higher capacity can be achieved in two different ways: through increasing the feed gas flow or increasing the SO2 concentration of the feed gas. From a catalyst perspective, increasing the feed gas flow is easier and allows for higher capacity without compromising conversion. With higher feed gas flow, an increase of more than 15% capacity can be achieved when replacing regular potassium-promoted catalyst loading with VK38+.
Higher gas flow does, however, increase energy consumption and may not be attainable if the main blower is already operating at full capacity, or if there are other constraints.
Increased SO2 strength comes with its own set of potential bottlenecks but will typically not increase energy consumption and can still allow up to 5% higher capacity when switching to VK38+.
VK38+ is not only limited to increasing capacity. If higher capacity is not a goal, there are several other ways that it can have a positive impact on plant profitability. First, operating with higher SO2 strength can also help operators reduce energy consumption and hence energy costs. This is described more in detail in the environmental section below.
Influencing possible cycle lengths with VK38+ can also help improve profitability for situations where higher capacity is not desired. The limiting factors dictating when a particular plant needs to shut down for turnaround varies, since each plant face its own unique set of conditions and constraints. Some of these are, however, related to catalyst performance. For these plants, applying VK38+ can significantly improve cycle length, since the activity margin down to where sufficient conversion can no longer be maintained can be increased by as much as 100%.
Finally, the higher performance of the VK38+ can be leveraged for increased catalyst lifetime.
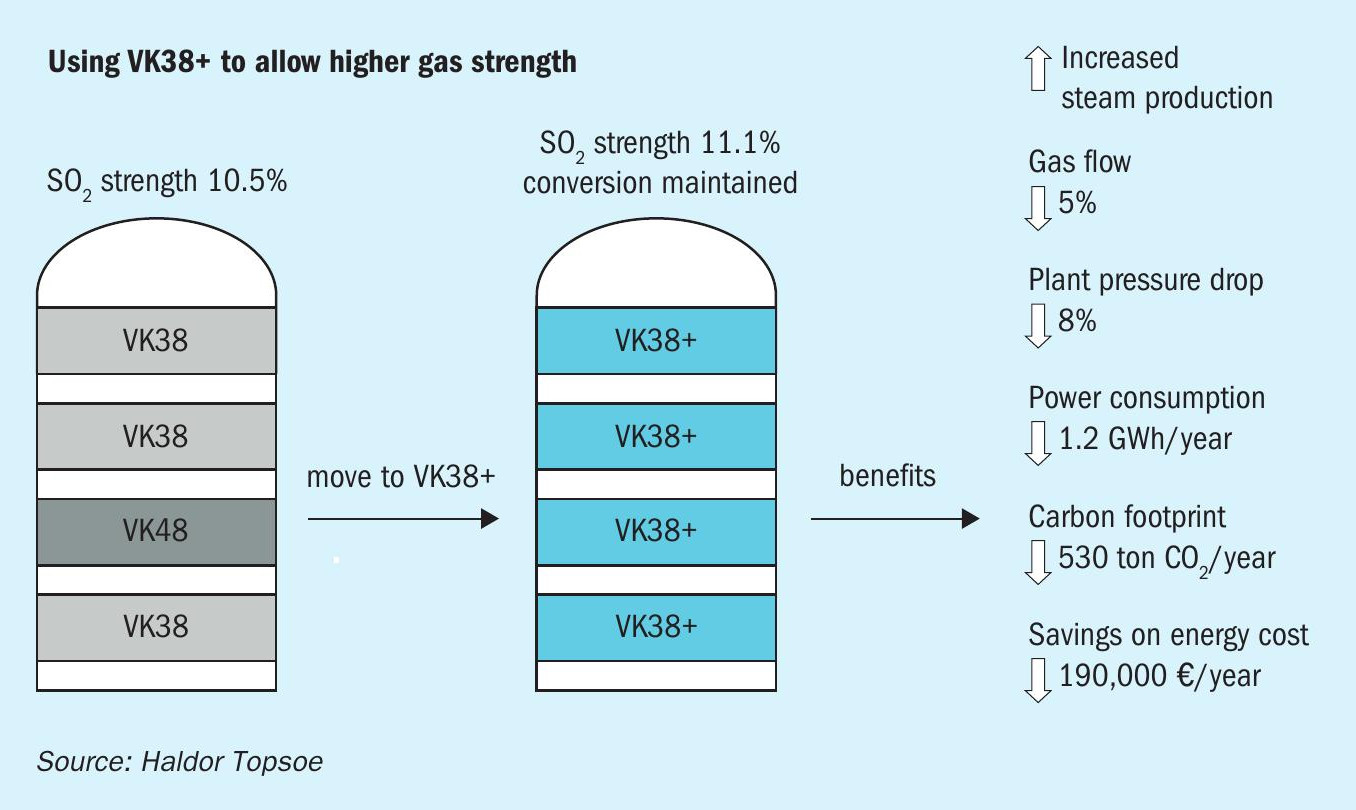
While pressure drop increase may force screening of a bed, with higher start of run activity the bulk catalyst can be used for longer before the overall activity drops to a level where the full beds need to be replaced to maintain conversion. Calculations show that the extra start of run activity translates to an up to 40% reduction of long- term catalyst spending.
Environmental performance
Environmental performance expectations are tightening globally. In Europe, a new Green Deal puts pressure on the industry to create more efficient and effective low-carbon technologies and reduce emission of SO2 through a new Best Available Techniques reference document (BREF), which is on the horizon. In the United States, there has recently been a clear drive towards lower SO2 emission on the state and federal level, and a similar Green New Deal puts focus on renewable energy and resource efficiency. The UN’s Sustainable Development Goals (SDG) also target the Asia-Pacific region, which is under pressure to develop more sustainable solutions.
One of the primary objectives for any high-performance sulphuric acid catalyst is to help operators achieve low SO2 emissions from their plants. This is important for plants to stay compliant with the new environmental legislations outlined above, and also to reduce their environmental footprint. The VK38+ is no exception, and brings some clear advantages compared to traditional solutions (see Fig. 1).
A sulphur burner operating with a feed gas of 11% SO2 can reduce emissions by around 30% by moving from a regular VK38/48 loading to a VK38+ loading of the same size. From an environmental footprint perspective, using VK38+ to reduce SO2 has another advantage. Contrary to many non-catalyst solutions, it achieves the emission reduction without causing an increase in associated greenhouse gas emissions.
As mentioned previously, the higher activity of VK38+ can be leveraged to enable plants to operate with higher feed SO2 concentration without sacrificing conversion. Higher SO2 strength in turn allows plants to reduce feed gas flows without sacrificing productivity.
Fig. 2 shows how the CO2 footprint and energy expenditures can be reduced by using VK38+ to allow unchanged capacity and emission at higher SO2 strength and lower gas flow. For example, switching from a regular potassium-promoted loading to VK38+ can allow a 1,000 t/d plant to cut its CO2 footprint by more than 500 tonnes/ year through increased SO2 strength. In addition to energy savings achieved through reduced flow, the change can also lead to increased steam production and an annual energy cost savings of e140,000.
Catalyst replacement can be dictated by a number of factors, low activity being one of the most important. Although the effects of deactivation can be temporarily mitigated through increased bed temperatures,eventually there will come a point at which it is no longer possible to maintain conversion at normal production rates. With its higher activity, VK38+ can be operated for longer, before activity falls below a point where emission targets can no longer be met. This effect and the corresponding longer lifetime are shown in Fig. 3. In this example the VK38+ is operated 55% longer before having to be replaced.
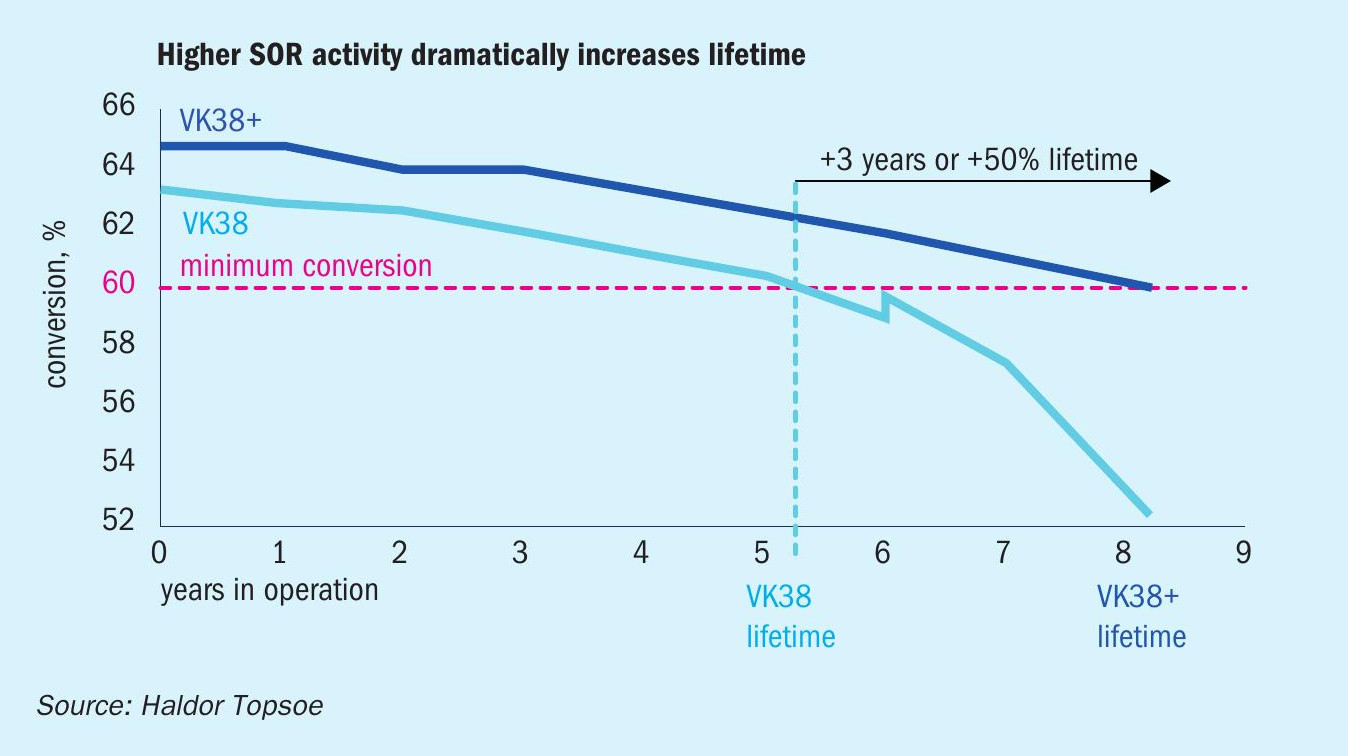
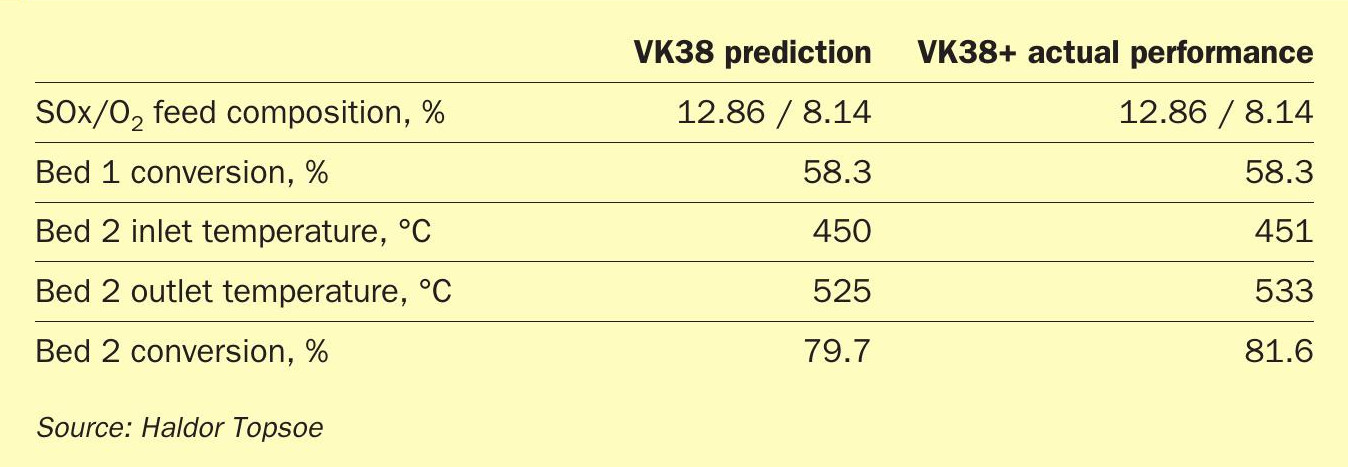
The longer lifetime presented in Fig. 3 translates to an up to 50% decrease in the volume of catalyst needed to maintain plant performance over time. With the metal content of the two catalysts being similar, the decrease in required catalyst volume also corresponds to a 50% reduction in metals needed to be mined and refined. Finally, using 50% less catalyst also means a 50% reduction in the spent catalyst that is generated in the process.
Overall, this contributes to a smaller environmental footprint for the sulphuric acid plant.
The extra flexibility discussed earlier also potentially reduces the environmental footprint. One example involves increased steam production. When operators add VK38+ to beds 1 and 2, they can also use lower inlet temperatures, which allows for increased process energy extraction as valuable high-pressure steam. Overall, this makes VK38+ a powerful tool for improving sustainability across the industry.
A complete transition to a new SO2 converter catalyst like VK38+ does not have to happen overnight, it can take place gradually and cater to the needs of the individual plant.
The new catalyst could also be phased in through the normal catalyst management scheme, replacing one or parts of a bed at a time as the existing catalyst reaches end of life.
- VK38+ allows operators to: reduce emissions by ~35% over existing VK38/48 loading;
- lower catalyst waste and raw material use by ~50%;
- reduce power consumption by ~10% due to capacity for higher feed concentration;
- increase power output with higher steam production at the same load;
- decrease or avoid chemical consumption in existing scrubbers;
- reuse more existing catalysts;
- get more out of the existing plant and avoid the environmental footprint that comes from constructing new equipment and units.
Regardless of which approach is taken, switching to a better catalyst requires a strong partnership with the supplier. With good technical service, the right catalyst management strategy can be identified to address the operator’s specific goals and constraints.
VK38+ is already in operation in two plants, one of them a 1,000 t/d sulphur burning sulphuric acid plant in Sweden. Here the new catalyst was used to replace regular VK38 that had been previously used since 2011 in Bed 2.
Together with a top-up of Bed 1, the new catalyst allowed the plant to operate with an unprecedentedly high SO2 concentration, far higher than is seen for most other sulphur burning plants. Despite the high SO2 concentration, the conversion outlet of Bed 2 is higher than what it used to be with the previous charge of VK38, and the temperature increase over the later beds decreased. While data for identical conditions are not available, the performance for the previous charge of VK38 has been simulated at the same conditions as VK38+ (See Table 1). The higher performance of the new catalyst could translate to 50% longer lifetime, or up to 5% higher capacity.
Conclusion
VK38+ is a new potassium-promoted catalyst from Topsoe that has been proven to have higher activity than any other catalyst
The development of VK38+ comes at the heels of tightening global legislation that poses challenges to sulphuric acid plants, many of which already operate with fully loaded converter beds. With VK38+, operators can better live up to these demands and decrease their plants’ environmental footprints. The result is better economics, lower emission and less waste.
References
DUPONT CLEAN TECHNOLOGIES
MECS® advanced catalysts help manage and reduce sulphuric acid plant emissions
Catalyst is at the heart of all sulphuric acid plants and plays a critical role in plant performance. This article provides an overview of the specific design features of two new types of MECS® sulphuric acid catalyst developed by DuPont Clean Technologies (DuPont), XLP-310 and SuperGEAR™ , and explains how these more advanced catalyst types can be applied to reduce emissions or increase the capacity of a sulphuric acid plant.
When asked about key challenges, sulphuric acid plant operators invariably name three issues:
- operational targets – run-times that are as long as possible and start-ups that are as fast as possible;
- emissions control or improvement;
- economic factors – aligning the objectives above with the economic reality: running the plant at the highest possible capacity while consuming as little energy as possible.
The DuPont Clean Technologies R&D team keeps all three challenges in mind when developing new and improved types of catalyst. Although there are many factors which impact catalyst performance, formulation and shape are two of the key considerations in the design of advanced new catalyst.
Impact of catalyst formulation on conversion
Catalyst is composed of alkali metal, vanadium salts and a diatomaceous earth support. Under reaction conditions, molten alkali metal vanadium pyro-sulphates are formed. These molten salts are supported within the pore structure of the diatomaceous earth. The accepted mechanism for sulphur dioxide oxidation to form sulphur trioxide is a catalytic redox cycle that involves V5+ and V4+ species in the supported liquid phase. The composition of active salts in the liquid phase, as well as accessibility to those salts by the gas stream, plays a large role in the activity level of the catalyst.
In addition to catalyst activity, conversion is impacted by many factors including, but not limited to, gas composition and inlet temperature to each pass,catalyst volume and converter design. In some cases, temperature optimisation alone can allow plants to reach their emission goals. Fig. 1 shows the typical profile of a four-pass converter (before and after temperature optimisation) and illustrates that, ultimately, the conversion of SO2 to SO3 is limited by the equilibrium curve.
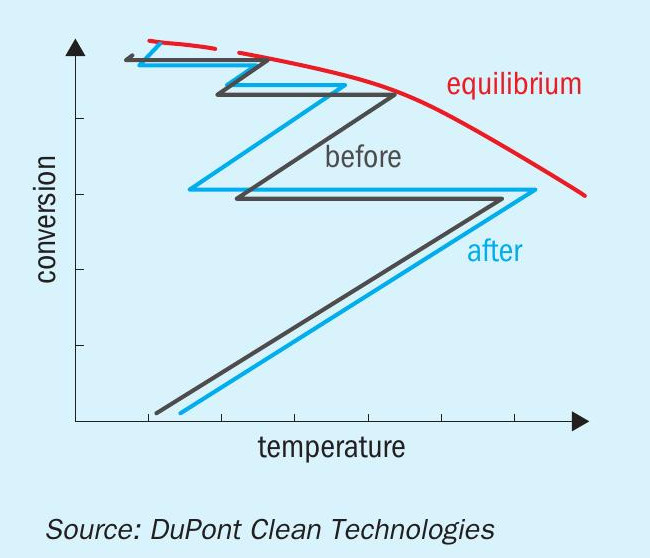
Traditionally, many plants have added caesium catalyst, which allows for lower operating temperatures and therefore a closer approach to equilibrium, to the fourth pass of their converter in order to reach their desired emission levels. However, thanks to advances in catalyst shape and formulation, many plants can now reach their emission goals without the addition of caesium catalyst through application of more active catalyst in upstream passes of the converter.
Benefits of advanced catalyst shape
For a nominal pellet size, pressure drop in the converter is largely determined by catalyst shape. Ten years ago, DuPont developed the MECS® GEAR® catalyst, which has a unique hexa-lobed ring shape. The new shape created an increased spacing between the rings and thus allowed the gas to pass through the catalyst bed more easily than was possible with traditional ring-type catalysts (see Fig. 2). That not only means a lower pressure drop but also translates into energy savings, as less power is required to operate the main blower.
Dust handling is another factor regulated by the catalyst shape. Most of the dust that enters the converter is collected in the first pass. If the dust collects at the top of the bed, the pressure drop across the bed will build up faster, which results in shorter runtime between shutdowns. The shape of the MECS® GEAR® catalyst was designed to allow dust to penetrate throughout the bed instead of accumulating at the top. In this way, more dust can be collected before it starts to block the gas flow and cause an increase in pressure drop. The net result is that operators can extend the time between maintenance shutdowns. Fig. 3 illustrates the expected bed life when using different catalyst shapes.
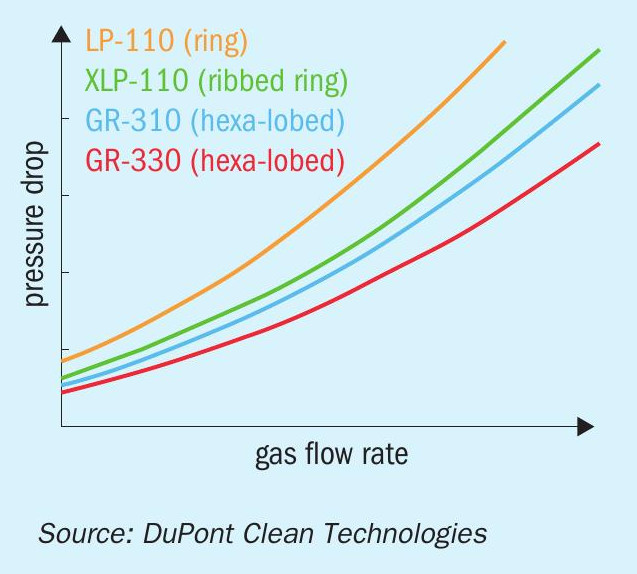
Finally, catalyst shape and the geometry of the individual lobes determine the way in which rings nest into each other and therefore decide the total catalyst surface area per volume of catalyst. The greater the surface area, the greater the interaction of the gas molecules with the catalyst and the higher the final activity. This is exactly what the MECS® GEAR® shaped catalyst set out to achieve, hence its name: GEAR – Geometrically optimised, Enhanced surface area for Activity improvement and Reduced pressure drop.
Latest catalyst advances increase activity
The most recently developed MECS® SuperGEAR™ and XLP-310 catalysts are based on an innovative, improved formulation in combination with the existing ribbed and hexa-lobed ring shapes to ensure pressure drop and dust handling levels are maintained. The enhanced formulation translates into significantly higher activity levels than the previous generation of catalyst. The volume-based activity of the XLP-310 is more than 50% higher than conventional ribbed ring catalyst and the volume-based activity of the MECS® SuperGEAR™ hexa-lobed catalyst is 65% higher. Performance of both XLP-310 and SuperGEAR™ has been proven through numerous installations in the field.
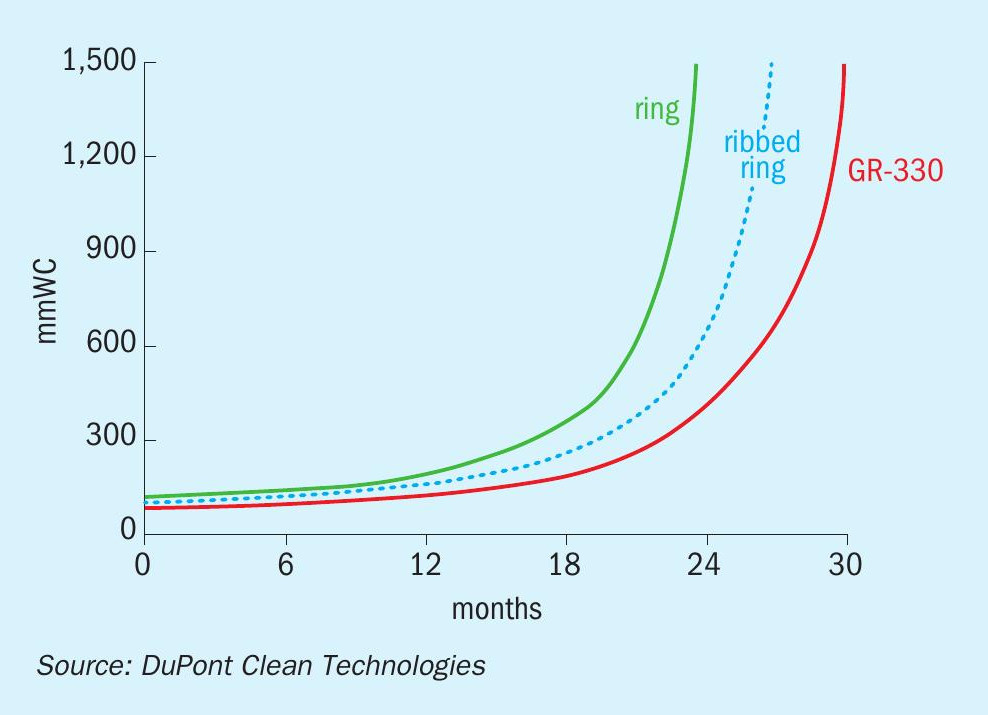
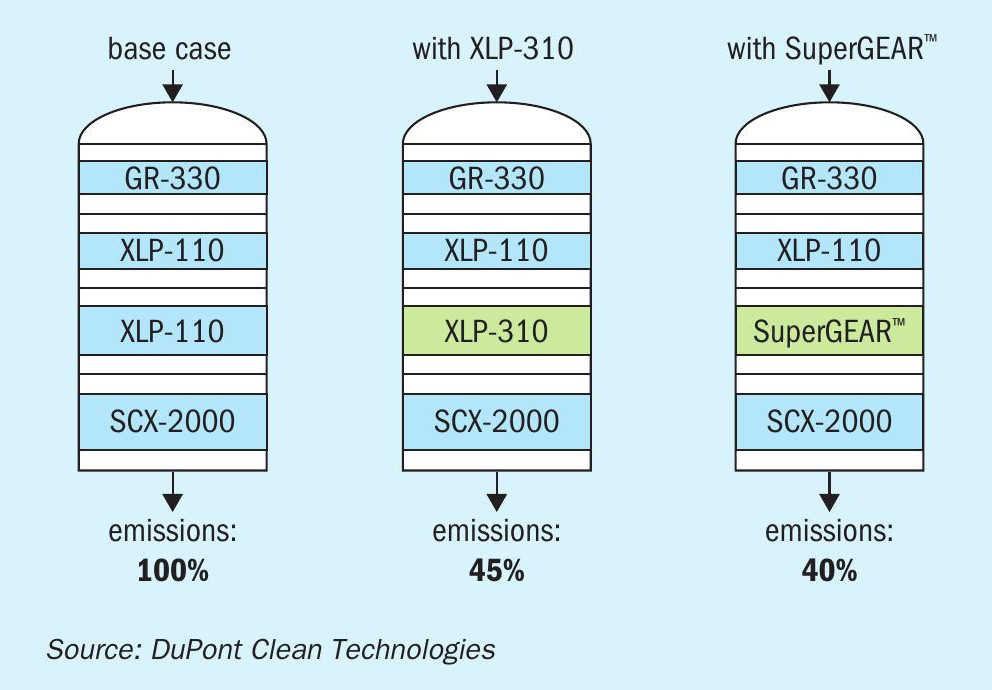
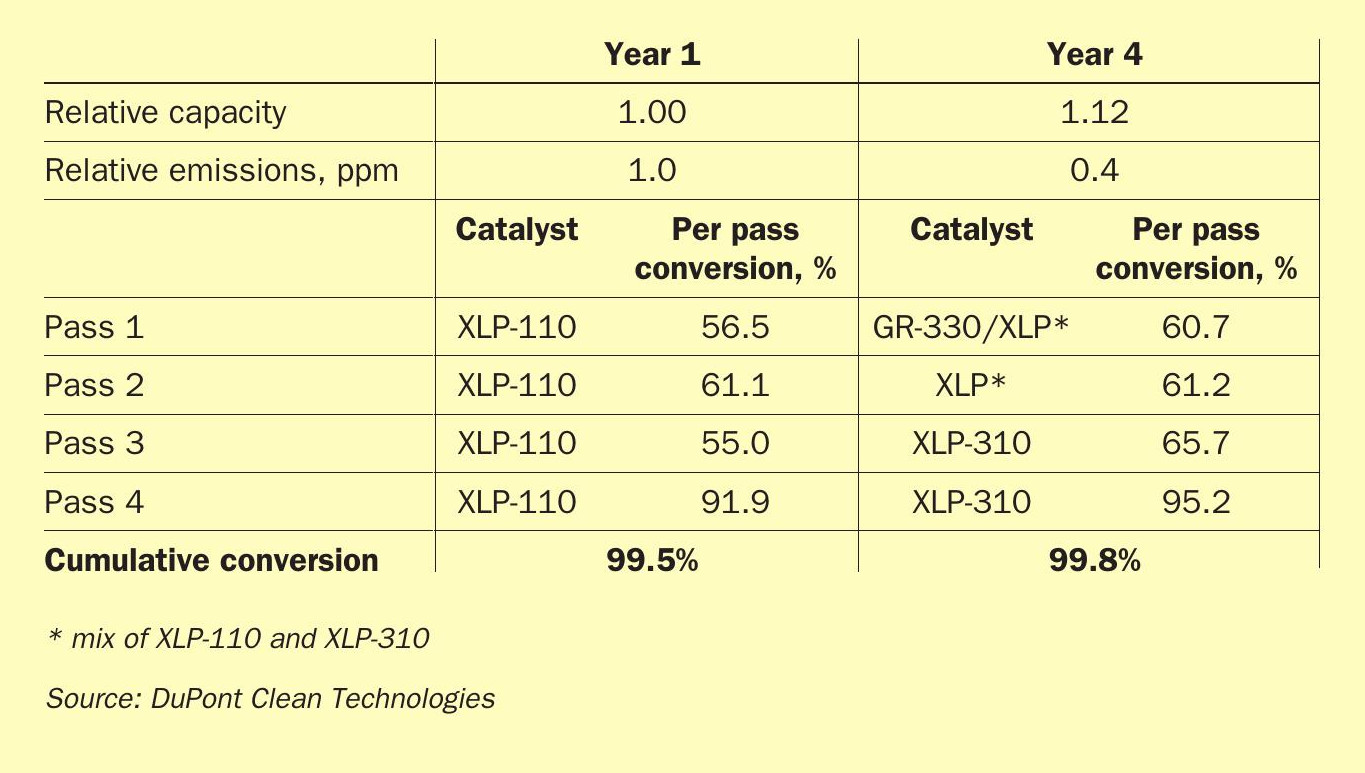
Benefits of improved activity in an existing plant
Selective addition of the catalyst to critical passes can lead to dramatic results. Plant emissions can be reduced while holding capacity steady, or plant capacity can be increased while maintaining the same emission levels. In some cases, plants may choose to lower emissions to reduce reagent costs of downstream scrubbers or to comply with new environmental regulations. Or they may expand capacity to increase production of finished goods from other parts of their site. Of course, it is only possible to improve plant capacity to the extent that other plant bottlenecks or the hydraulic limit of the blower allow.
Another way of looking at the performance of these advanced catalysts is to consider catalyst loading versus conversion. The same loading of catalyst in the bed can provide a higher conversion, or the same conversion may be obtained with a lower loading. As with all major revamps, DuPont uses its proprietary design software for MECS® catalyst to provide customers with achievable improvement levels based on current operating conditions.
The new MECS® XLP-310 catalyst
Although MECS® XLP-310 may be used in any pass, maximum benefit is derived when it is used in converter passes 2 and 3, as well as in pass 4 if there is no caesium. Fig. 4 provides a comparison with a standard XLP-110 catalyst and MECS® SuperGEAR® catalyst. As can be seen in the scenario shown, complete replacement of XLP-110 with XLP-310 in pass three, with no modifications to passes 1, 2, or 4, has the potential to dramatically reduce emissions.
The advanced MECS® SuperGEAR™ catalyst
The new MECS® SuperGEAR™ catalyst combines the pressure drop and dust handling advantages of the hexa-lobed ring shape with an improved formulation that provides greater activity. This catalyst was mainly developed for new plants where use of MECS® SuperGear™ catalyst will optimise the capex versus performance. Although maximum value is achieved in new installations, just as with MECS® XLP-310, MECS® SuperGEAR™ can also be selectively applied in existing converters, allowing for a further reduction in emissions.
Application examples
Achieving conversion goals through XLP-310 without major capex
A DuPont client, operating a very large capacity sulphur burning plant, made the decision to renew the company’s commitment to sustainable operation by setting even more stringent emission goals for its plant. At the same time, the company realised that additional capacity would be required in order to support fertilizer production. An evaluation by DuPont determined that the site could meet its goals by focusing on passes three and four of the converter, and that expensive heat exchanger or converter modifications, as initially feared, were not necessary.
Based on DuPont recommendations, the company gradually upgraded the catalyst in its converter over the course of four years. The upgrades included complete new beds of MECS® XLP-310 in passes 3 and 4, installation of MECS® GR-330 in pass one and a partial installation of MECS® XLP-310 in pass 3. The result was an overall conversion increase from 99.5% to 99.8% and a 60% reduction in emissions, at the same time as an expansion in plant capacity of 12% (see Table 1).
Increasing capacity while reducing pressure drop with MECS® SuperGEAR™
For a planned major plant revamp, one DuPont customer is choosing the superior performance of MECS® SuperGEAR™ over other ribbed catalysts. By using caps of SuperGEAR™ in passes 2 and 3, as well as MECS® SCX-2000 catalyst in pass 4 in the new converter, the company expects to increase its capacity by approximately 25%, reduce overall pressure drop and maintain conversion. The high activity of SuperGEAR™ should enable the plant to use 13% lower loading than with standard ribbed catalyst, as well as reduce the expected pressure drop by 13%. Super-GEAR™ will allow them to save on initial capital costs as well as reduce their operating costs over time.
Viability of catalyst-triggered capacity and emissions improvement
Sulphuric acid plant operators with an existing converter who want to improve emission levels should carry out a full and detailed analysis of their current operations to have a clear understanding of realistically achievable outcomes DuPont uses the MECS® PeGASyS™ analysis system which measures the SO2 conversion of every pass to provide a full picture of the performance of each bed. This data is then evaluated with the help of the MECS® catalyst design program, which predicts what improvements can be achieved using the newly developed catalysts. Sometimes, the PeGASyS™ analysis shows that a simple adjustment of the converter temperature is sufficient to achieve an improvement in plant performance. PeGASys™ measurements could also reveal if it is not the catalyst that is the root cause of a production issue, but in fact another part of the plant that requires maintenance such as the gas-togas heat exchanger.
Conclusion
If all other equipment is functioning correctly, advances in catalyst design and formulation can offer significant capacity and emissions improvements. The choice of options available allows sulphuric acid plant operators to select a catalyst mix that matches their production and emissions objectives at the same time as cutting energy consumption, accelerating start-ups and increasing run-times between shutdowns. n
BASF
Customised bed solutions with new Quattro catalysts
BASF has produced sulphuric acid for various industrial applications since 1866 and has been producing catalyst for the sulphuric acid process since the early 20th century. A first patent for a vanadium pentoxide catalyst was granted to BASF in 1913. Today, BASF is operating six sulphuric acid and 13 sulphonation plants with inline SO2 oxidation units worldwide all using BASF’s in-house catalyst technology with world class plants operating at emission levels below 50 ppm SO2 . The last 15 years have brought new challenges such as tighter emission regulations and cost pressure to the sulphuric acid market. This has led BASF to be on the forefront with cutting-edge research into one of the oldest catalysts of the portfolio.
Customer focus
In alignment with the new strategy of BASF, the focus on sulphuric acid producers and their needs is ever greater, driving improvements of catalyst technology. BASF works directly with customers to make sure customers achieve the best performance under the specific design and operation conditions of their reactors. This is enabled through BASF’s state-of-the-art testing facility and analytics combined with more than 150 years of research and experience.
New extruded shapes
Sulphuric acid catalysts are generally produced by extrusion of a precursor paste to yield shaped catalyst bodies. The extrusion process not only defines the shape of the catalyst bodies, but also impacts other crucial properties such as pore structure and mechanical stability of the catalyst. These properties are also related to the fluid properties of the precursor paste in the extrusion device. Eventually, the extrusion process has to cope with pastes of varying composition for different catalyst types. Fluid properties of precursor paste and control of the entire extrusion process are strongly determined by the specific design of extrusion dies. Especially the detailed design of internals of the dies has a significant impact on quality and capacity of extrusion. This becomes an immediate challenge, when entirely new shapes for a catalyst family shall be extruded and new dies have to be found.
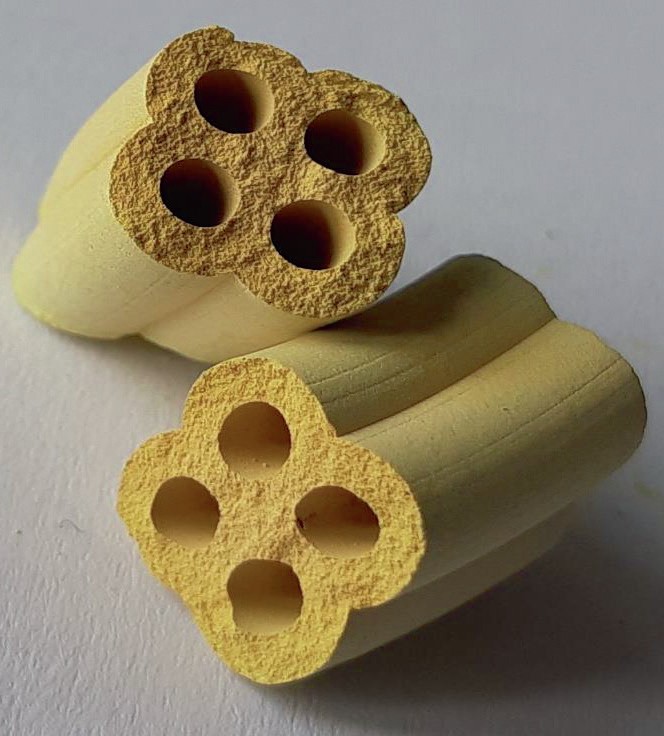
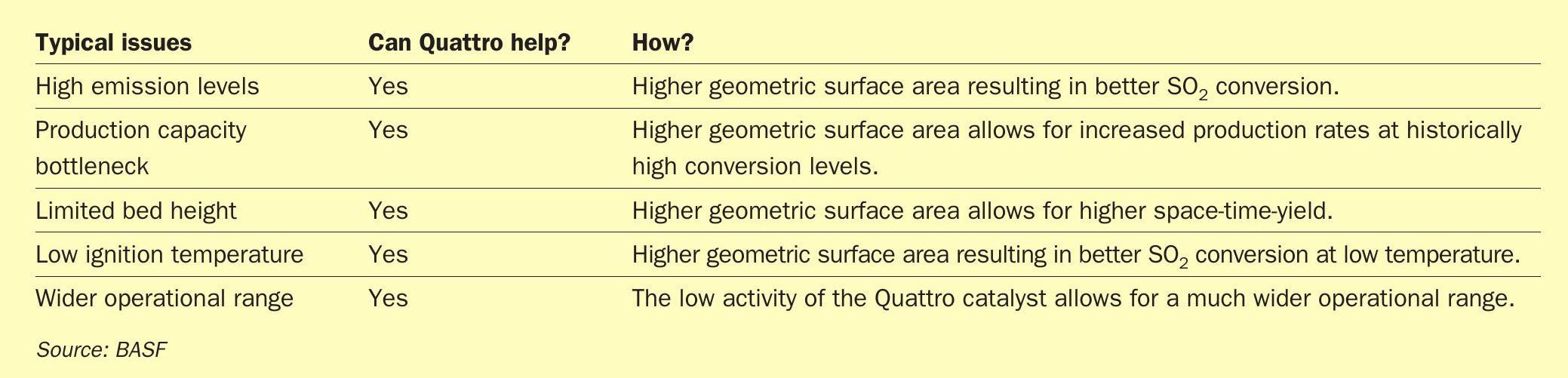
Commitment and continuous progress in extrusion technology has been a key for successfully turning a lab idea into an established and reliable commercial product. Here, BASF can make full use of the Technology Verbund with in-house competence on computational fluid dynamics (CFD) and metal powder 3D-printing technology to develop and optimise dies for extrusion devices. This is evidenced by an international patent family filed by BASF on extrusion dies for catalyst production (WO2019/219892 A1).
In 2016, after years of catalyst development, BASF launched O4-115 with the Quattro geometry (Fig. 1, WO2016/156042 A1 and WO 2019/170406 A1) leading to 5-8% increased plant capacity in the first commercial application. Many additional customers have chosen the Quattro geometry since, all benefiting from performance improvements.
In early 2020, BASF introduced the Quattro catalysts O4-110 and O4-111, the newest members of the Quattro family. These vanadium-based catalysts allow sulphuric acid producers to boost production capacity significantly, reduce SO2 emissions, extend turnaround schedules and shorten start-up time leading to significant cost savings. These latest developments allow customised catalyst bed solutions to be created for unique applications worldwide. Continuous innovation and creative thinking continue to define BASF as a global innovation leader in catalyst research.
O4-115 Quattro development and application
In 2017, first long-term results from the Quattro catalyst development were described and demonstrated:
- 5-8 % increased production capacity;
- increased conversion with increased SO2 feed content and reduced O2 /SO2 ratio;
- no increase in pressure drop across the O4-115 Quattro bed;
- flexibility across varying O2 /SO2 ratios.
The development of the Quattro shape geometry addresses several common customer challenges when operating a sulphuric acid plant (Table 1).
In 2018 the DOMO Caproleuna Plant observed a decreased conversion over the first two beds of the sulphuric acid plant. Under normal conditions, this would have led to an increase in SO2 emissions and potentially a forced shutdown to replace the catalysts in the first bed. However, BASF’s Quattro catalyst in the 4th bed of the sulphuric acid plant was able to make up for the decreased conversion in the first two reactor beds, preventing a significant increase in SO2 emission in the off-gas of the plant (Table 2).
Table 2: Conversion at DOMO Caproleuna plant 2016-2019
In addition to the significant increase in geometric surface area of the Quattro shape geometry, which yields up to 30% higher activity, the mechanical properties of the Quattro catalyst have set it into a class of its own when compared to current state-of-the-art star-ring-type catalyst geometries (Table 2).
With 50% higher side-crush-strength and approximately 50% lower attrition compared to star-ring catalysts the predicted loss on sieving for the Quattro catalyst is significantly lower than that of the star-ring type catalyst reducing refill costs.
The greatest attribute of the O4-115 Quattro catalyst is the wider operational range and the lower ignition temperature (Table 3). This allows for a much lower start-up temperature and a much broader operational range of the reactor.
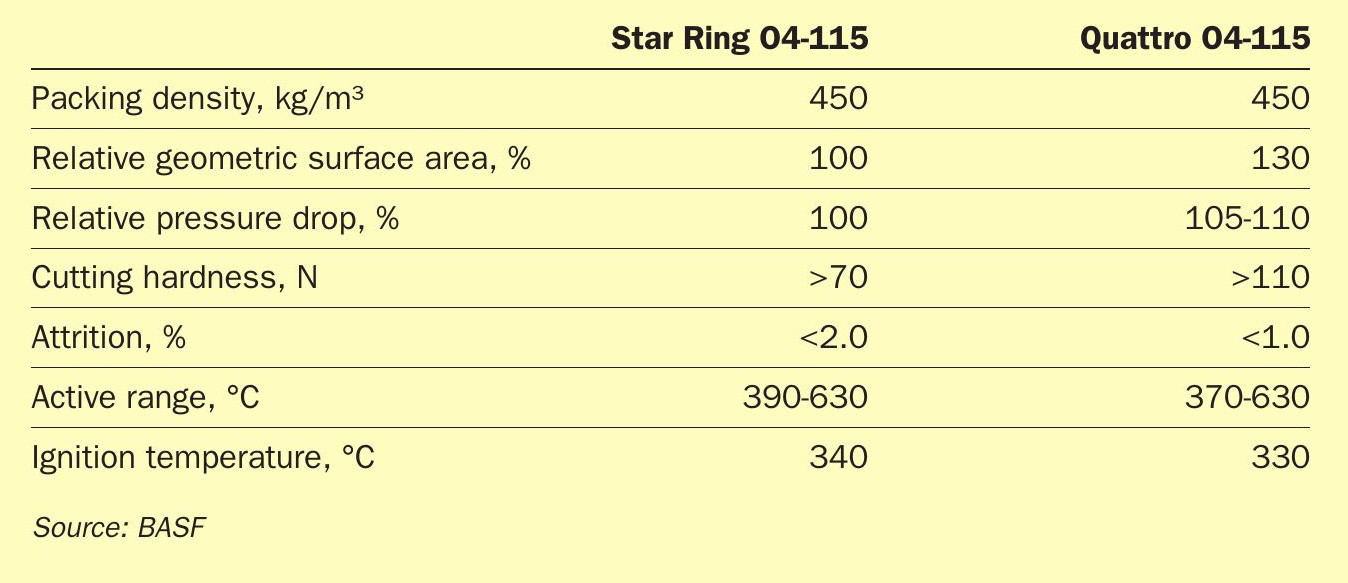
The physical data taken from the DOMO Caproleuna plant also support the original lab data detailing the decreased attrition loss and the high mechanical stability of the Quattro catalyst (Table 4).
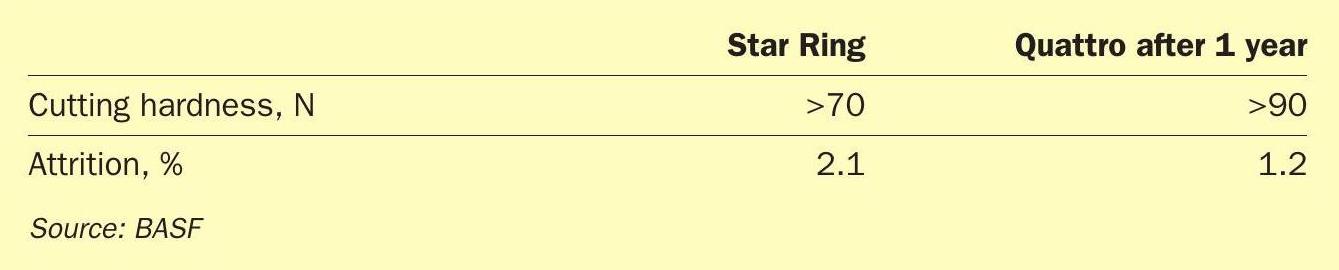
O4-110 /O4-111 Quattro development and application
Even though the O4-115 Quattro catalyst already shows a significant improvement compared to the state-of-the-art shape geometries, BASF is further committed to providing customers with the best possible solution for challenging demands such as improving throughput of existing units while decreasing SO2 emissions to meet more stringent environmental requirements.
To meet this challenge, BASF extended the Quattro family to O4-110 and O4-111 Quattro (Fig. 2). As in the case of the O4-115 Quattro catalyst advantage is taken of the increased geometric surface area of the new shape geometry to push the production capacity of existing sulphuric acid units, providing a catalyst which requires a lower loading mass and offers a significant performance advantage compared to all standard star-ring type catalysts.
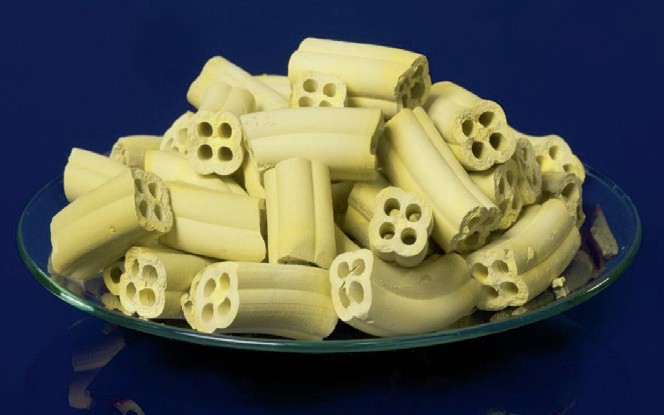
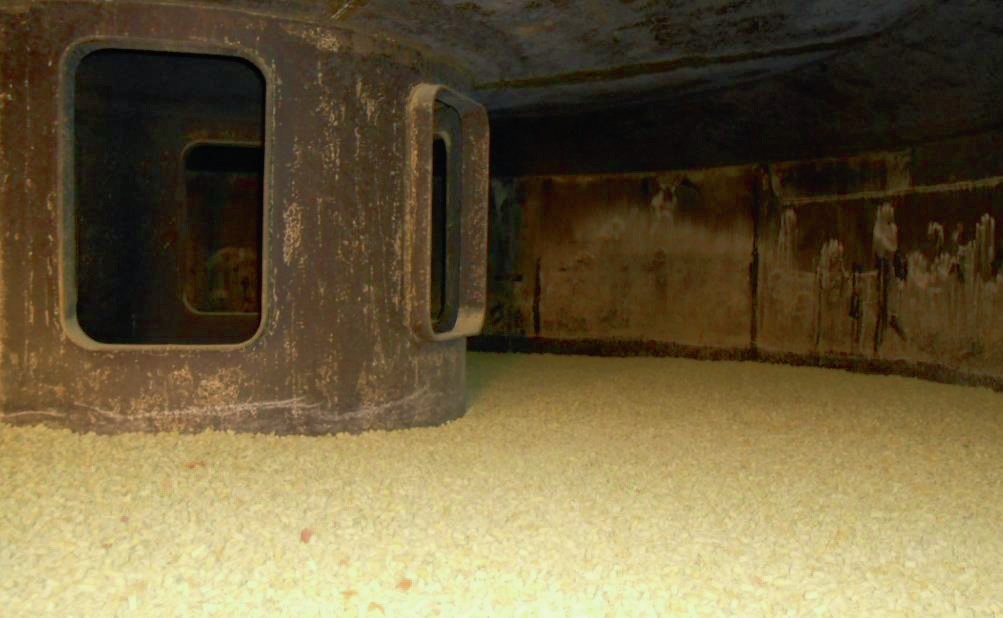
The most impressive outcome of the O4-110 and O4-111 catalyst shape geometry is the increased active range of the catalyst especially at low temperature. The decrease in ignition temperature is driven by the higher geometric surface area which allows more accessibility to the active sites at low temperature. This increases the active range of the catalyst.
Another major advantage is that sulphuric acid producers can lower the amount of catalyst required for a reactor filling while at the same time increasing conversion. This means pressure drop in the reactor can be decreased without compromising on conversion. In fact, this can even lead to the highly desirable situation of increased conversion with a lower pressure drop. The lower catalyst loading of the BASF O4-111 or O4-110 quattro catalyst is possible again due to the increased geometric surface area (Table 5).
Since 2016 the Quattro catalyst family has been installed in numerous plants globally, each time confirming the expected performance improvements described earlier: “Due to technical limitations we are not yet at full capacity, but the performance of the bed loaded with Quattro catalyst is already remarkable.”
DOMO Caproleuna, Germany, loaded two additional beds with O4-111Quattro during the turnaround in 2020. Ulf Müller, Director Operations Inorganic Precursors and Fertilizers comments, “It is clear that the new catalyst has an excellent performance. With a capacity of 3% above the project load, we still have reserves in performance and conversion. So far, we could not detect an increase in pressure drop across the catalytic converter.”
In summary, the O4-115, O4-110 and O4-111 BASF Quattro catalysts offer lower ignition temperatures, higher conversion and higher strength than conventional catalysts (Fig. 3). This directly translates into increased operational flexibility and significant cost reduction for sulphuric acid producers.
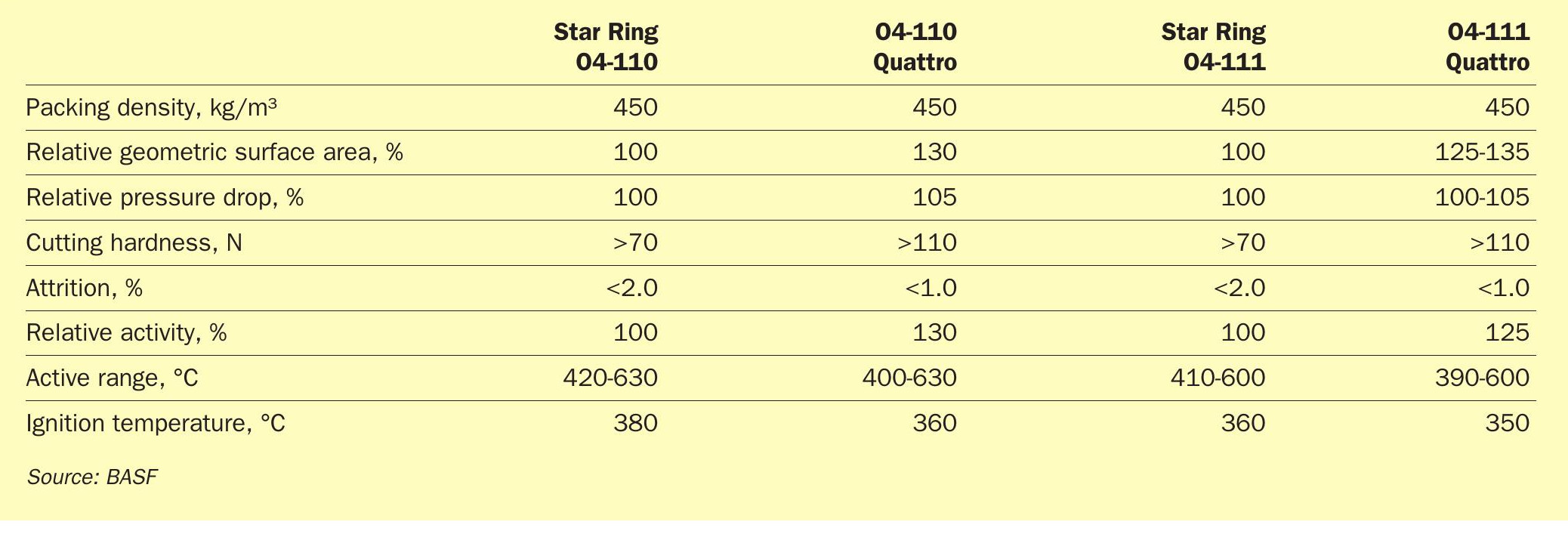