Nitrogen+Syngas 369 Jan-Feb 2021
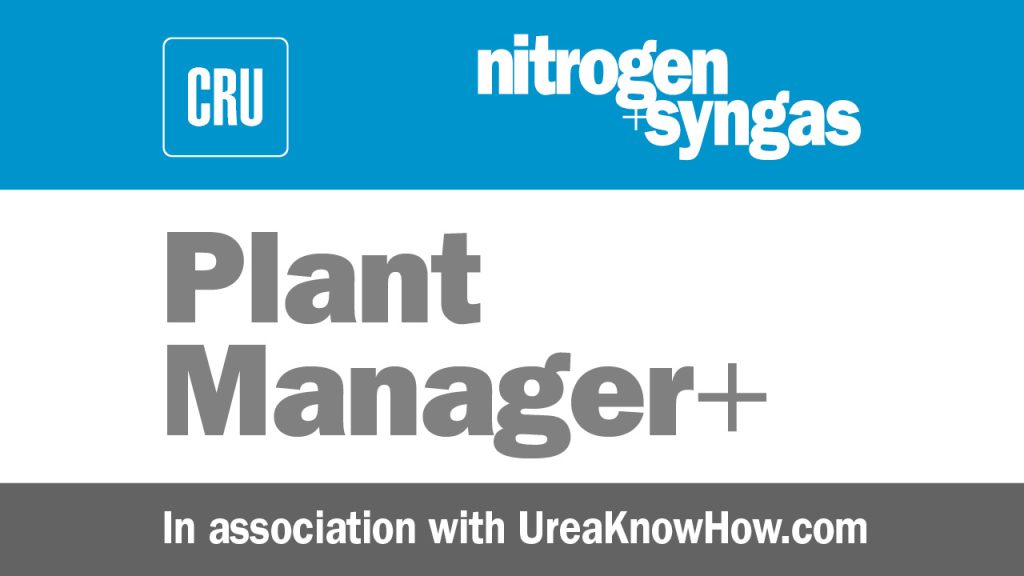
31 January 2021
Incident No.s 4 & 5: Leak detection system failures in urea plants
The following case studies describe serious incidents associated with leak detection system failures. Incident 4 relates to the failure of the active pressurised leak detection system for the loose liner of a urea reactor and Incident 5 relates to a passive leak detection system which failed to work leading to serious corrosion of the carbon steel wall of the HP scrubber.
Incident No. 4
Event description
During a daily routing plant tour the plant operator observed a crystallised white product deposited on the insulation sheeting of the urea reactor which worsened quite quickly over time. Some ammonia vapour was also noticed.
Immediate response action
Initially a leak at the manway cover was assumed, since the active pressurised leak detection system was not indicating any leak. A closer look, however, indicated a possible leak in the liner and so the plant was stopped for inspection.
Causes
The installed active pressurised leak detection system failed to warn operations. The pinhole leak in the liner had created severe corrosion attack of the carbon steel pressure shell and the reactor was taken out of service just in time. The state-of-the-art leak detection had failed to indicate the leak due to a combination of wrong commissioning of the system and failure of some components, as well as insufficient inspection and maintenance of the system.
Primary consequence
There was a near miss of the high pressure vessel rupturing.
Secondary consequence
The incident led to an unplanned shutdown. A temporary repair was carried out initially, with a full repair executed within one year.
Prevention safeguards
Assure proper functioning of the leak detection system. Safe operation of the plant is only possible with a good working leak detection system.
Mitigation safeguards
In case of a leak, confirm and locate the leak, shut down the plant and drain the synthesis section as soon as possible.
Corrective recommendation The leak detection system was refurbished and made operational before start-up of the plant. In addition, an inspection and maintenance program was implemented to increase the reliability and availability of the existing leak detection system. All plant operators received further training.
Incident No. 5
Event description
In February 2018, a leak was visible in the spherical dome part of a HP scrubber of a 1,750 t/d Stamicarbon CO2 stripping urea plant. The plant was shut down.
Upon opening of the HP scrubber sphere it became clear that severe corrosion had occurred on the 316L UG liners. The liner was covered with a large amount of corrosion products and many cracks were visible. The cracks had resulted in leaks that had gone unnoticed by the passive leak detection system, likely due to clogging. Therefore, corrosion of the carbon steel pressure part commenced undetected. Many cracks were also found in the carbon steel wall and grooves and holes were partly blocked by corrosion products.
Immediate response action
The plant was stopped to attend the leak.
Causes
In the passive leak detection system it takes too long for the leak to show up at the analyser. The leaks in the liner had already clogged the tubing (the leaks were cracks).
Primary consequence
A rupture of the high pressure vessel was avoided by luck.
Secondary consequence
There was an unplanned shutdown of about two months for extensive work to repair the HP scrubber.
Risk level
The likelihood of a major consequence was moderate, but the risk level was high.
Risk level The likelihood of a major consequence was moderate, but the risk level was high.
Prevention safeguards
Assure proper functioning of the leak detection system. Safe operation of the plant is only possible with a good working leak detection system, including an accurate and reliable ammonia analyser.
Mitigation safeguards
In case of a leak, confirm and locate the leak, shut down the plant and drain the synthesis section as soon as possible.
Corrective recommendation
The leak detection system was refurbished and made operational before start-up of the plant. In addition, an inspection and maintenance program was implemented to increase the reliability and availability of the existing leak detection system. All plant operators received further training.