Fertilizer International 501 Mar- Apr 2021
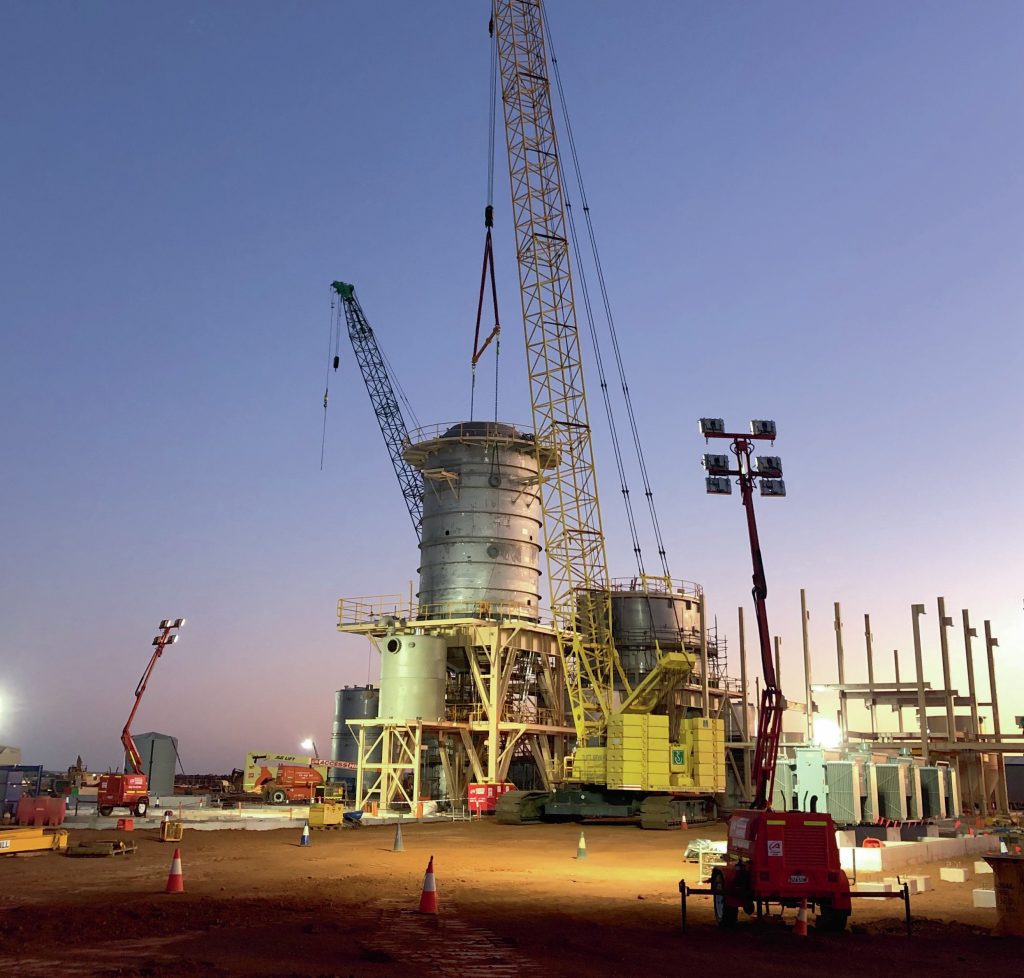
31 March 2021
State of the art potash production
POTASH TECHNOLOGY
State of the art potash production
We report on the latest potash mining and processing technology from Andritz, Ebner, Köppern, K+S and Veolia. Recent case studies for potash projects globally are also provided.
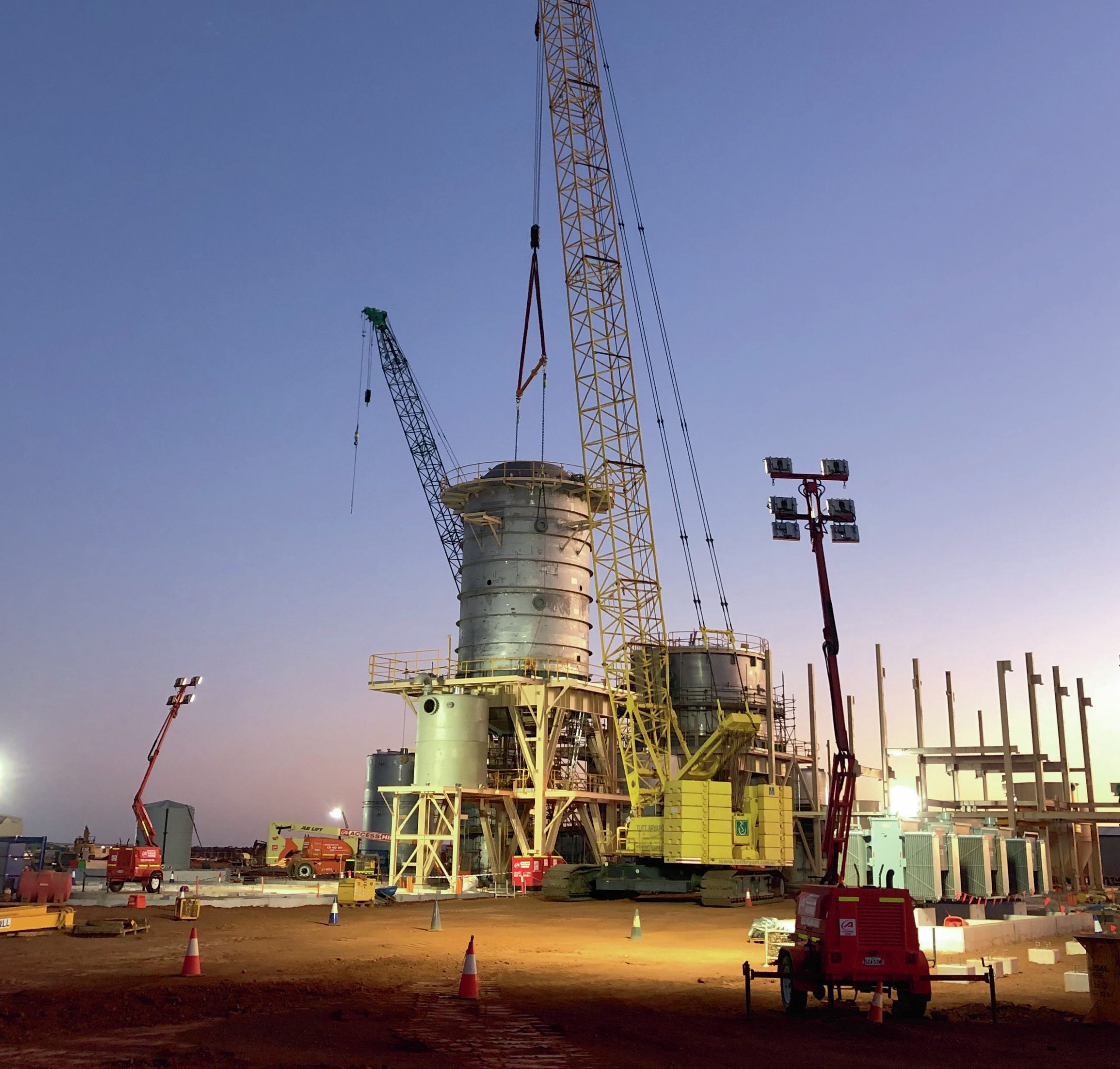
EBNER TECHNOLOGIES
Family-owned crystallisation and evaporation specialist
Germany’s Ebner GmbH & Co KG is a family-owned specialist designer and manufacturer of evaporation and crystallisation plants. The company develops tailor-made plants completely inhouse, from the customer’s first enquiry to final delivery, having expertise that encompasses plant design, fabrication, erection, and start-up. Ebner has extensive experience in the design and manufacture of evaporators and crystallisers for the potash industry. Two recent case studies are provided below.
German technology for Australian SOP project
In October 2019, Ebner and K-UTEC Salt Technologies were jointly awarded a potash engineering contract by the Australian, ASX-listed mining company Kalium Lakes Limited (KLL).
The contract covered the engineering, supply, erection, supervision and start-up of a 90,000 t/a capacity production plant for KLL’s flagship Beyondie SOP (sulphate of potash) project. Ebner and K-UTEC joined together to form a special consortium, EBTEC, to deliver this contract.
Kalium Lakes’ vision was clear from the moment it first contacted K-UTEC in 2015. It wanted to be the first Australian company to bring domestically-produced SOP to market. Because all the SOP currently consumed in Australia is 100 percent imported, there was a unique, ground- breaking opportunity for a local producer to supply the domestic agricultural industry with SOP for the first time.

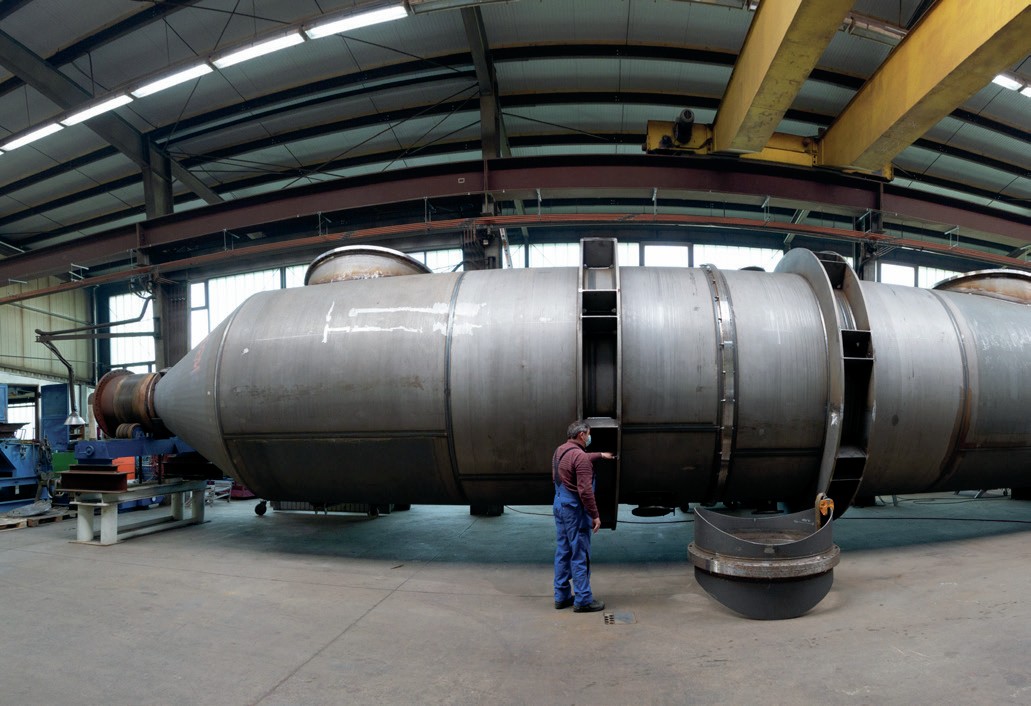
The proposed Beyondie SOP plant was located in the remote Pilbara region of Western Australia, about 1,400 kilometres north of Perth and 240 kilometres by road from the nearest town. The plant was designed to produce high-purity SOP by selectively precipitating salts present in a saline brine. This was to be extracted from nearby salt lakes and underground aquifers using a network of trenches and wells.
K-UTEC’s main project expertise is in geophysical exploration, process development, design engineering and basic engineering. This includes the technical and economic assessment of full-scale industrial plants and the piloting of complete process routes. The company developed a suitable SOP production process for the Beyondie project in 2018. This involved initial test drilling, preliminary studies, feasibility studies and practical test work – to demonstrate the most commercially-viable production route. In the production process selected for the SOP project by K-UTEC, salt is firstly generated by concentrating a brine solution in large solar evaporation ponds, each with a surface area of around 400 hectares. This salt is then refined in a processing plant to obtain a high-purity SOP fertilizer product.
The Beyondie project reached financial close in December 2019. The financing included AUD 102 million of senior debt funding from KfW IPEX-Bank, with approximately half of this amount supported by a guarantee from Euler Hermes, the German government’s export credit agency. Once project finance had been secured, EBTEC went ahead and designed and delivered the processing plant.
The EBTEC consortium was able to ship the main equipment, including dissolution, flotation and crystallisation apparatus, to Australia on schedule, despite Covid-19 restrictions. Backed by 50 years of plant manufacturing experience, Ebner was able to handle everything in-house, including the fabrication of individual components in its own workshops and the overall completion of the plant. The company’s engineering know-how, capabilities and experience were vital for the successful completion of the contract.
The Beyondie SOP project is currently in the assembly phase. This is being carried out by an Australian co ntractor under the joint supervision of EBTEC and Kalium Lakes. Site infrastructure has already been completed and the process plant is in the process of being built. SOP production is scheduled to start-up in September 2021.
Large-scale MOP crystallisation plant for Slavkaliy
In February 2020, Famako Anlagenexport GmbH, with Ebner as subcontractor, were awarded a major engineering contract by Slavkaliy for its Nezhinsky potash project in Belarus. The contract encompassed complete project design, manufacturing, delivery and start-up of a large-scale crystallisation plant for the production of MOP (muriate of potash).
In the Nezhinsky processing plant, potassium chloride will be obtained from hot-saturated brine by vacuum cooling crystallisation using the classic hot leaching process. In total, two production lines at the plant will produce around two million tonnes of MOP annually. Both lines are designed to operate as independent seven-stage vacuum crystallisation plants.
For Slavkaliy, the design and delivery of the crystallisation plant will be critical for the overall success of the Nezhinsky mining and production complex.
To ensure the vacuum crystallisation plant operates efficiently, vapour generated during the expansion of the hot solution will be used to reheat the cold circulation-brine obtained from the salt separation. This minimises steam consumption requirements during hot leaching. At the same time, this process configuation also reduces the plant’s cooling water consumption to the lowest level possible.
Most of the individual components of the crystallisation plant were made of high-quality special materials. Due to their size, these were prefabricated in Germany for onward transport to Belarus (see photo). The project’s schedule necessitated justin-time delivery and the careful choreography of logistics for such a large plant. Ensuring individual components were available on time and ready for transport was a particular challenge, especially against the backdrop of a global pandemic.
As a contractor, Famako is responsible for project financing, coordination with suppliers and project logistics. The company, which is active in the former Soviet Union (FSU), specialises in the planning, delivery and commissioning of conveyors and other systems for processing fertilizers and other bulk materials. Ebner, meanwhile, provides project knowhow and is responsible for plant design. This expertise is delivered by in-house staff, from the initial design computations through to the final design specification.
Thanks to the relevant experience of both companies, and closely coordinated project management, the project remains on-track with the processing plant scheduled to be fully assembled in 2023. Ebner and Famako are proud to have successfully completed their project work for Slavkaliy, given the challenging global conditions currently, especially as the contract with Slavkaliy is the largest ever undertaken by both companies in financial terms. n
ANDRITZ
Process automation
With over 90 years of experience, Andritz is a market-leading supplier of liquid/solid separation equipment to the potash industry. The company installed its first potash centrifuge in 1926. Since that time, Andritz-manufactured equipment has been adopted by many large-scale potash producers globally, including conical screen bowl decanters, large-diameter disc filters and proprietary fluidised bed systems.Indeed, Andritz is the brand behind some of the mining industry’s best-known separation equipment suppliers – including dryer, centrifuge, filter and fluidised bed manufacturers such as Bird, KHD Humboldt Wedag, Krauss Maffei and Escher Wyss.
Andritz has a total of around 600 potash references around the world, including:
- 425 centrifuges
- 100 fluidised bed systems
- Dozens of filters, plate dryers and thickeners.
Impressively, these have been installed on five continents in every major potashproducing region. In recent years, large-diameter Andritz disc filters have a been adopted by potash operators in Belarus, Russia, and South America, while its innovative conical screen bowl decanters have entered operation in North America.
The installation of a high-capacity, energy-saving Andritz dewatering system in Belarus, for example, has delivered major operational improvements at Belaruskali’s Plant No 1. These included a 10 percent increase in production capacity, 15 percent lower energy costs and a 30 percent reduction in residual product moisture (Fertilizer International 484, p64).
Control system for Compass Minerals
Andritz also has expertise in automated production systems for the potash industry, having notably supplied a complete control system to Compass Minerals. This was part of a 2016 project to commission and integrate a new crystalliser and compaction plant at the company’s Ogden, Utah, sulphate of potash (SOP) production site in the United States.
Andritz was tasked with:
- Validating the process design
- Designing and supplying the control system
- Supplying the proprietary BrainWave advanced controller for the SOP crystalliser
- Supplying power distribution and motor control equipment
- Developing a simulation-based operator training programme.
Virtual plant to predict behaviour
Compass Minerals wanted to reduce the project’s implementation costs, minimise start-up risks, and predict how the new project would affect its existing operations. To help deliver on these objectives, Andritz modelled the new compaction process, and used its dynamic IDEAS process simulator – essentially a ‘virtual plant’ – to accurately predict the behaviour of the new SOP crystalliser. The benefits of the complete automation package delivered by Andritz included:
- Reduced errors, risks, costs, and project uncertainty
- Optimisation of the SOP process
- Successful plant start-up and then ramp-up to full production
- Completion of simulation-based operator training before start-up
- Only minimal project impact on existing operations.
The overall outcome was that, from the very first day of start-up, Compass Minerals had access to a fully-functioning and integrated SOP production control system that was already up and running.
KÖPPERN
Potash compaction-granulation
Köppern, a family-run business founded in Hattingen, Germany, has been manufacturing briquetting, compaction and comminution machinery since 1898.The company has been supplying compaction and granulation equipment and plants to the fertilizer industry for more than 70 years. Its sales include several hundred roller presses in over 60 countries.
Granular potash is produced almost exclusively by a compaction-granulation process. Fine-grained potash feed is generally compacted on roller presses to produce flakes with a density close to that (>95%) of natural potash. These flakes are then crushed and screened to produce a closely-sized (often 2-4 mm) granular product.
Three key components
A typical compaction-granulation plant for MOP (muriate of potash) consist of three key components – roller presses (compactors), crushers and screens – configured in closed-circuit. The feed is firstly compacted at an elevated temperature. Köppern typically installs compactors with a 1,150 mm diameter and 1,000 mm working width. Multiple compactors are often installed within one potash plant. These presses have a maximum flake throughput of approximately 140 t/h and a gross granular potash capacity of 40-50 t/h. After compaction, impact and roller mills, working in a closed-loop cycle with multi-deck screens, crush the flakes into granulate with an approximate density of 1.9-1.95 g/cm3 .
Since the 1990s, the preferred flake capacity of potash compactors has increased to 110-130 t/h. The majority of new compactor investments made by potash producers in recent years have been in designs of at least 100 t/h flake.
Design innovation
Köppern has introduced a number of innovations and design changes to ensure compactors of this size are safe, reliable to operate and deliver excellent flake quality. This has involved the modification of various subassemblies, including the frame, feeder, roll design, roll drive and the hydraulic systems.
Vibrations are a particular operational problem when de-aerating and compacting potash – as they can result in severe juddering that damages equipment. The risk of this can be reduced by lowering roll speed and/or feed rate. However, changing the compactor drive design to increase mechanical stiffness is a preferable way of solving this problem at source. This approach also maintains throughput, and is therefore less of a compromise for customers.
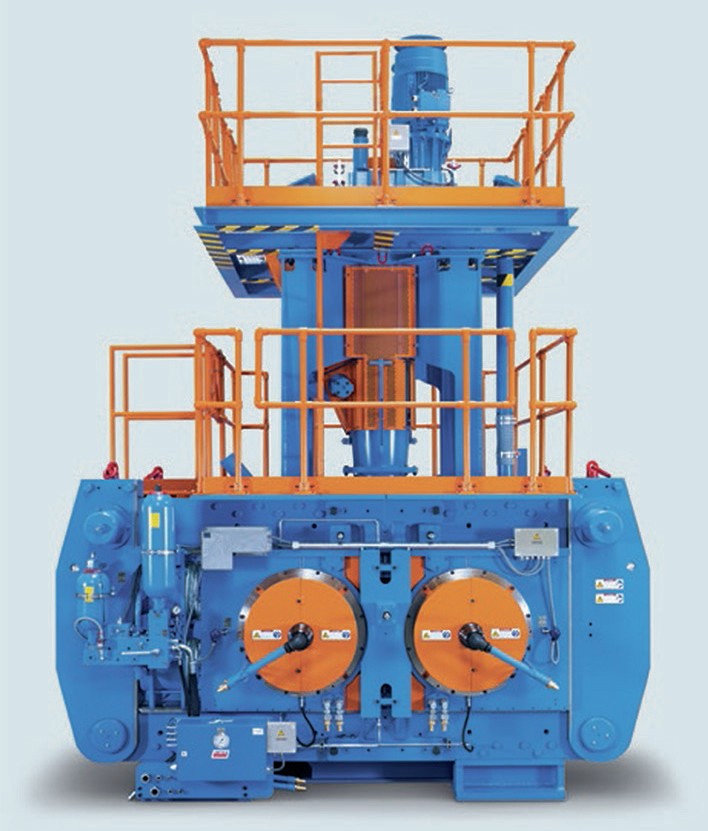
For many years, Köppern has stiffened the drive train of large roller presses by manufacturing these with planetary gear reducers mounted directly onto the roll shafts. The company delivered its first large potash compactor (130 t/h) with this drive technology to Germany in 1998. Since then, compactors with this drive design have been widely-adopted worldwide. For example, Köppern’s fertilizer compaction customers in Brazil, Canada, China, Croatia. Hungary, Jordan, Italy, Russia, Serbia and Spain have either modified or ordered new roller presses fitted with this type of main drive.
All large potash compactors supplied by Köppern since the early 1990s have also been supplied with a hinged frame. This allows quick access to rollers for assembly or maintenance. Rollers can be picked up easily without dismantling any part of the frame or feeder.
The feeder is an important component of the compactor. It needs to transport large volumes of material, de-aerate this effectively and distribute it evenly over the entire working width of the roller. The ability to independently adjust screw speeds also prevents misalignment by controlling the gap between rollers. Meeting these requirements prompted Köppern to develop a special double-screw feeder design. This design was first introduced into the potash industry in the mid-1990s in roller press upgrades in Germany and Belarus. The newly developed double-screw feeder was subsequently supplied to K+S in Germany and further clients in Canada, Chile and Belarus.
It is also economically advantageous to provide the roller body with exchangeable tyres, as this allows refurbishment of the tyre profile after wear.
Most of the above improvements and new design features, developed by Köppern over the years, can be found in many compactors used today by the potash industry globally.
K+S GROUP
Kainite crystallization flotation (KCF) unit
Werra, K+S Group’s biggest potash plant, is a large-scale complex spread across four sites in two German states: Hattorf and Winter-shall in Hesse, and Unterbreizbach and Merkers in Thuringia. The plant produces fertilizers alongside numerous technical and industrial products. These have a wide-range of uses, including pharmaceuticals, foodstuffs and animal feed.
Major investment in the Werra site
K+S has invested heavily in new production technology at Werra in recent years. In particular, the commissioning of the kainite crystallization flotation (KCF) unit at the Hattorf site in 2018 has allowed the company to dramatically cut the volume of wastewater discharged into nearby rivers. This major investment was also designed to safeguard the future of Werra as K+S’s largest potash operation in Germany.
The new e180 million KCF unit recycles saline solutions generated by ore processing operations at the Hattorf and Unterbreizbach sites. Valuably, it improves operational efficiency by extracting more saleable product from process water, using new technology developed in-house by K+S.
Improving efficiency, reducing wastewater
The implementation of kainite crystallisation downstream of ore processing has delivered two main benefits. Firstly, the KCF has cut the volume of saline water generated by production annually by fifty percent. Secondly, the new unit recovers large amounts of reusable product materials annually, by recycling saline solution from upstream processes at both the Hattorf site in Hesse and the Unterbreizbach site in Thuringia.
The KCF operates via four main process steps:
1. Partial capture of process and wastewater streams: The KCF captures over two-fifths of the wastewater at the Werra plant and recycles this to reclaim economically-valuable materials.
2. Evaporation step: A salt mixture, made up of kainite (MgSO4 •KCl•3H2 O), sylvite (KCl) and halite (NaCl), is firstly obtained by an evaporation step using process steam from the Hattorf site’s power plant.
3. Crystallisation and flotation step: The recyclable components are then separated from this salt mixture and further processed to produce sulphate of potash (SOP, K2 SO4 ) fertilizer.
4. Cutting saline wastewater discharge: The KCF reduces the volume of saline wastewater discharged to the Werra river, or disposed of underground, from 7.0 million m3 to 5.5 million m3 . The unit also reduces the salt load present in wastewater discharges by more than 500,000 t/a.
Mammoth construction project
Construction of the KCF was a mammoth project, due to the scale of the new e180 million processig unit (74 metres-long, 20-metres wide and 58 metres-high). The structure required around 5,500 tonnes of steel, for example, enough to build the Berlin Radio Tower nine times over. The need to excavate 36,000 cubic metres of soil during earth moving for the project further illustrates the massive scale of this undertaking. Constructing the KCF also required:
- More than 1,000 valves
- 180 kilometres of cabling
- 86 pumps l 82 items of equipment and machinery
- 35 kilometres of piping.
“K+S has invested heavily in new production technology at Werra in recent years.”
The KCF’s heaviest single component is the heat exchanger which weighs 110 tonnes – about 90 times the weight of a typical family car. The largest item, the V1200 evaporator, is 16 metres long, has a diameter of seven metres, and weighs 82 tonnes when empty. To manufacture and install specialised items of this size and weight, K+S awarded contracts to a number of German manufacturing and engineering companies including Ebner. n
VEOLIA WATER TECHNOLOGIES
Lake Way potash project
The speciality fertilizer SOP (sulphate of potash, K2 SO4 ) is a premium source of potassium with a rapidly growing global market demand. The product is favoured by many higher value crops, many of which are chloride-intolerant. That makes chloride-free SOP an increasingly popular fertilizer of choice for these crops. In regions such as Asia-Pacific and South America, demand for premium fertilizers such as SOP is thriving – thanks to the expansion of micro-irrigation and greenhouse-based horticulture.
Pioneering the production of SOP in Australia is Salt Lake Potash Ltd, the developer of the Lake Way potash project. This sustainable mining project is aiming to produce up to 245,000 tonnes of premium SOP annually. Suitable for use in organic farming, this will be extracted and refined from dry salt lake deposits in the Northern Goldfields region of Western Australia.
Process description
The Salt Lake Potash production plant is designed to produce SOP using a natural potassium-bearing source as a feedstock. The process involves recovering SOP from hypersaline brine extracted from salt lakes. Initially, potassium-rich salts are harvested by concentrating and transporting these brines through a series of solar ponds.
Veolia Water Technologies is supporting the project by designing and supplying the crystalliser technology packages. These are capable of converting the harvested salts (schoenite) into premium-grade SOP. Veolia’s proprietary HPD® SOP crystalliser will grow and purify potassium sulphate crystals. A second crystalliser, meanwhile, will recover secondary schoenite salts [K2 Mg(SO4 )2 •6(H2 O)] from recycled SOP mother liquor. To maximize SOP yield, these recovered secondary schoenite salts are combined with primary schoenite salts in the feed to the primary SOP crystalliser.
Operational flexibility allows potassium chloride (KCl) to be added to the crystallisation system. This can increase SOP production capacity by up to 32 tonnes/ hour (245,000 t/a).
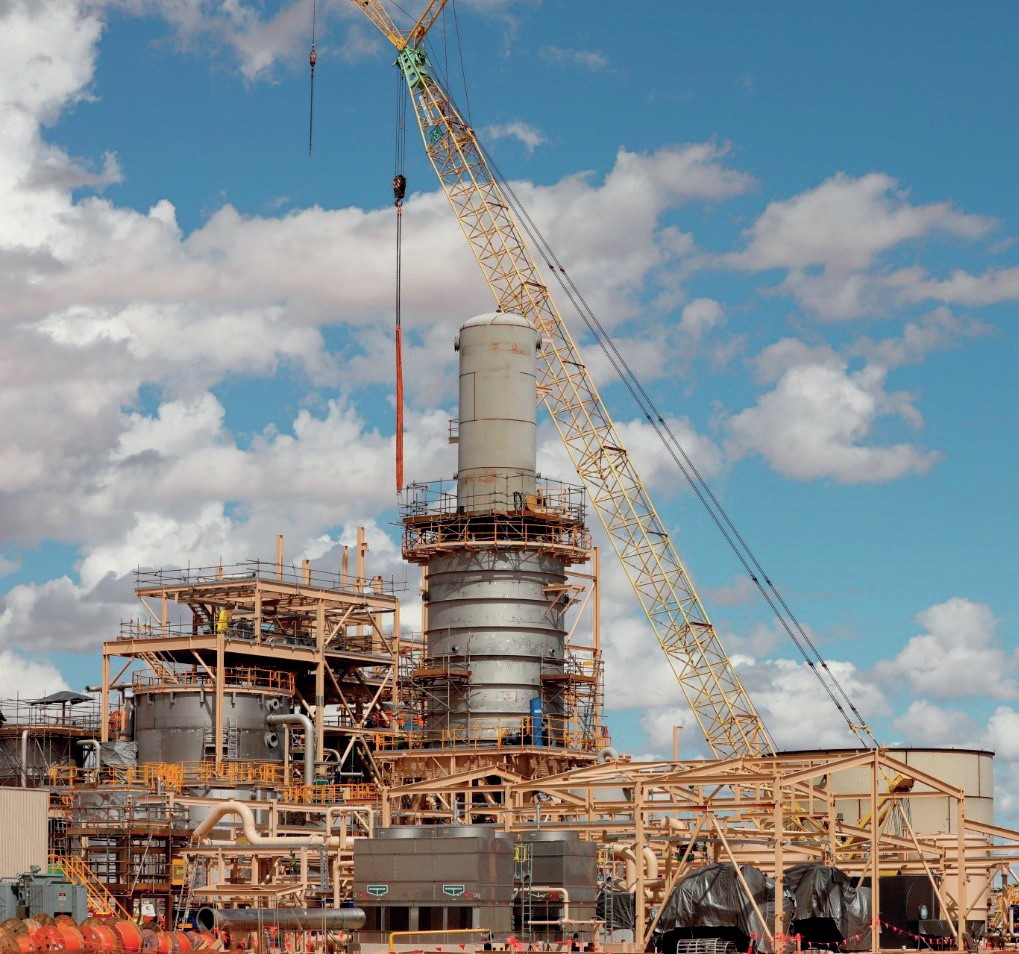
More performance, less risk
To support the development of the Lake Way potash project, continuous bench-scale crystallisation testing was carried out at Veolia’s Phillip J Stewart Technology center in Plainfield, Illinois. Tests were performed on actual harvested salts from on-site pilot evaporation ponds, together with process water from the site, and KCl sourced from the Dead Sea. The crystallisation of both SOP and secondary schoenite was tested under various conditions. The results obtained were then used to design the optimal process flowsheet and the full-scale commercial crystallisation equipment.
By validating the feed chemistry, simulating the optimal flowsheet design, and confirming process performance projections, the test work also helped to de-risk the project.
Basic engineering and bench-scale testing were both staged simultaneously – to further accelerate this fast-track project and deliver the client’s objectives on schedule. This approach, as well as helping optimise capital costs, also kept operating costs low, as the system design ensured that fouling and cleaning requirements were minimised.
The project packages were delivered to the Lake Way site ahead of schedule, ready for erection and installation by contractors GR Engineering Services. Plant commissioning is expected to begin in March, with first production and sales of SOP expected in the second-quarter of 2021.
Approximately 90 percent of Lake Way’s SOP production output is destined to be exported to customers globally. This includes volumes supplied to Helm, WeGrow, Unifert, Fertisur, Mitsui & Co and Indagro under long-term offtake agreements. The remaining balance of production will be reserved for the domestic market.
Salt Lake Potash has control of a portfolio of salt lake resources within the Northern Goldfields. The company’s ultimate ambition is to develop an entire SOP province through a series of lake expansions.