Sulphur 393 Mar-Apr 2021
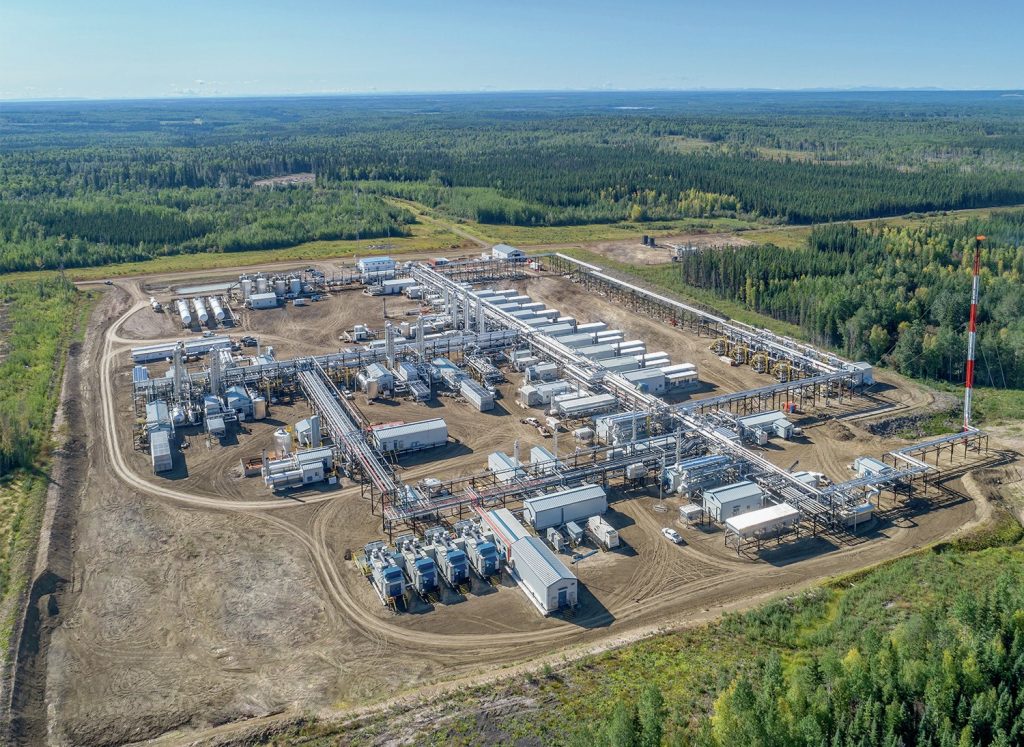
31 March 2021
Treating highly sour gas
SOUR GAS
Treating highly sour gas
Sour gas processing presents a number of unique challenges, especially at high levels of hydrogen sulphide and carbon dioxide content.
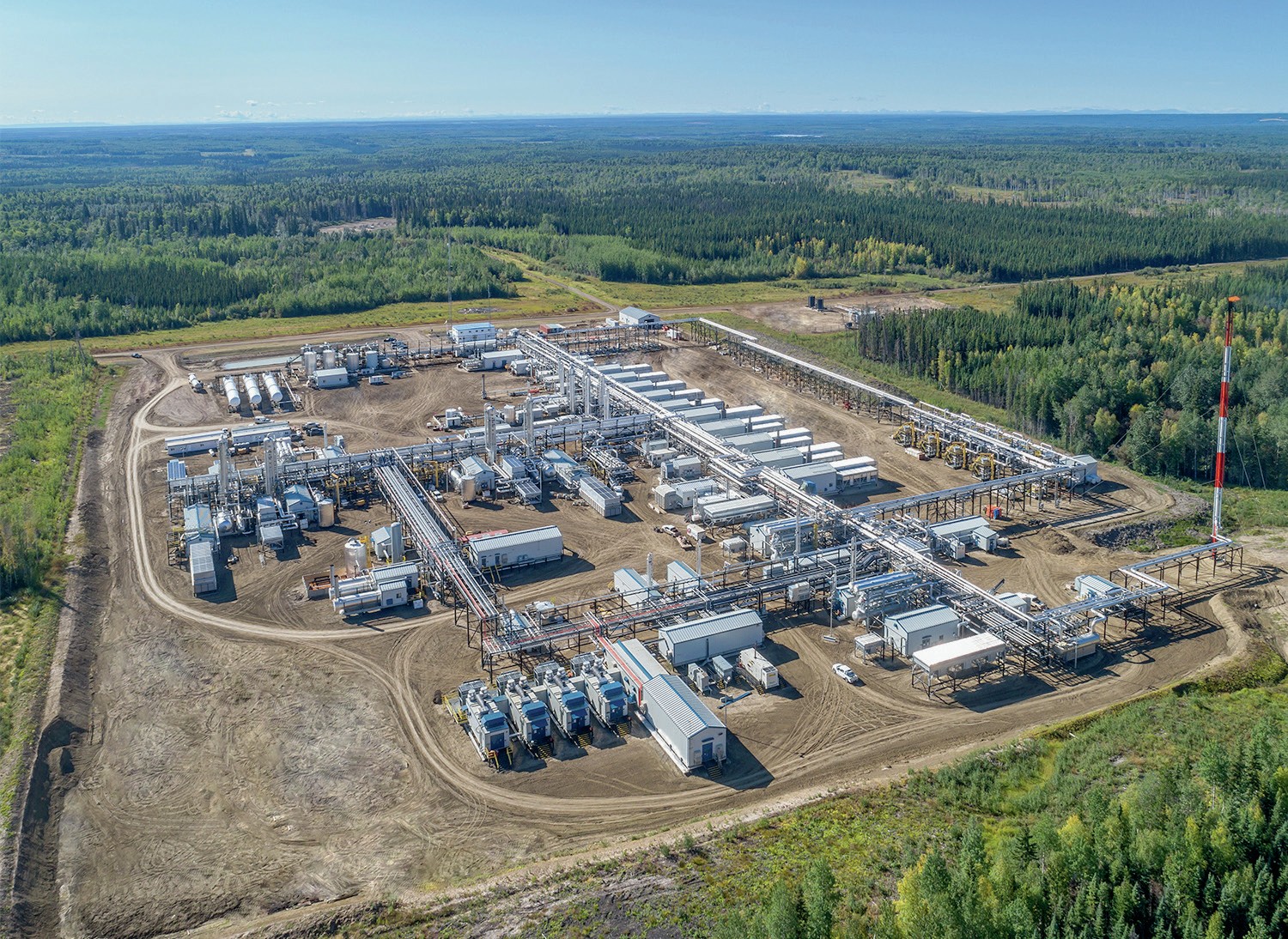
Approximately 40% of the global natural gas reserves, either standalone or associated with oil production, are classified as ‘sour’, due to their content of either hydrogen sulphide (H2S) or carbon dioxide (CO2 ). Among these, about 30% (12% of total gas reserves) contain more than 10% CO2 , and 15% (6% of total gas reserves) contain more than 10% H2S. Major H2S-containing fields are present in Abu Dhabi (10-35% H2S), Kazakhstan (18% H2S), southern Russia (30% H2S) and Alberta (ca 35% H2S). Some sour gas also remains in France (15% H2S). High CO2 -content gas can be found in Indonesia, Thailand and Malaysia (25-70% CO2 content), and North America (20-65% CO2 ). In all of these cases, the sour component must be removed before usable sales gas can be produced.
Treating sour gas
The main way of removing H2S and CO2 from gas streams is via solvent systems, either chemical solvents, physical solvents, or hybrids. Chemical solvents tend to be based on an amine blend, typically a variant on monoethanol amine (MEA), diethanolamine (DEA) or methyl diethanol amine (MDEA). Tertiary amines like MDEA require less reboiler duty, although it is less good at removing CO2 . Amines are typically are the lowest cost option for low to moderate levels of H2S/CO2 removal, and can also remove carbonyl sulphide (COS) from gas streams. They also typically have low solubility for hydrocarbons, which otherwise can affect downstream Claus processing. However, they have low selectivity for mercaptans, which may need further processing to remove, and require low pressure steam to regenerate the solvent, which can become expensive for high concentrations of acid gases. Using natural gas to generate the steam means that as acid gas concentrations increase, the proportion of sales gas generated can fall rapidly, with costs doubling every 20-25% increase in H2S/CO2 concentration. However, it is possible that these requirements could be met in other ways; at the 2019 SOGAT conference, ADNOC reported on feasibility studies of using solar power to regenerate solvent to free up more fuel gas for sale.
Physical solvents such as Selexol work purely by solubility in proportion of the partial pressure of the acid gas, with no chemical reaction. As a result the solvent circulation rate is not highly proportional to the quantity of acid gas removed. This means physical solvents can achieve higher acid gas loading at high acid gas concentrations than amine systems, and can be regenerated at lower cost. However, co-absorption of hydrocarbons is significant and can result in product losses, especially for higher chain components, which can restricts the use of physical solvents for many gas treating applications. As a result, there are hybrid systems like Shell’s Sulfinol which blend the two types of solvents for specific applications, in such a way as to maximise the benefits and minimise the limitations of each type of solvent. Prosernat’s Sprex process combined cryogenic separation with an ‘energised’ MDEA amine recovery section.
Other separation methods can be used, for example using fractional distillation via refrigeration. Fractionation can be smaller and simpler compared to a large gas treating system, but does require an energy intensive refrigeration system to condense the acid gas. ExxonMobil has developed a variant – the controlled freeze zone (CFZ) process, which can recover almost pure methane from a sour gas stream, suited for high acid gas concentrations (>30%). Different methods can be used in series to achieve the specific mix of gas component removal and/or recovery, for example to recover H2S for Claus processing but reinject carbon dioxide for enhanced oil recovery.
Semi-permeable membranes can also be used for physical separation of gas components. Membrane systems are best suited for feed gas at high pressure and are most attractive when the CO2 content of the gas is greater than 25%. At high H2 S concentrations the hydrogen sulphide can soften some membrane materials, but UOP have developed cellulose acetate membranes for high H2S service.
Process or reinject?
Once the acid gas has been separated from the sales gas, the question then arises as to what to do with it. Claus recovery of sulphur from H2 S used to be the standard treatment method. However, prices for sulphur can be volatile and are often quite low. Storage of large volumes of sulphur is not always a practical option, especially in a region like Central Asia where producing sites may be distant from markets. Emission of carbon dioxide from the acid gas is also becoming increasingly problematic as carbon pricing and emission limits continue to spread. Consequently there is an increasing trend towards reinjecting the acid gas back into the well or other suitable site, potentially generating additional reservoir pressure and possibly assisting with associated oil recovery, where present. Of course, acid gas injection (AGI) requires a geologically suitable site nearby for the gas to be injected into. It also may offer potential problems when the AGI system is down for whatever reason – flaring of the acid gas may not be possible due to local regulations, and the entire gas plant would therefore need to be shut down.
It is theoretically possible to recover some of the energy of the H2S by burning it and converting it to SO2 before reinjection, but the feasibility of such a process remains to be demonstrated at large scale.
Health and safety considerations
Handling large volumes of hydrogen sulphide offers the possibility of deadly leaks. A comprehensive risk management strategy must therefore form part of any large scale sour gas operation. This can put a particular focus on layout choices for the sour gas facility. At ADNOC’s Shah sour gas plant in Abu Dhabi, for example, this meant separating the well heads from the main working areas by a couple of kilometres. However, this of course means longer pipe racks and therefore more expense.
Reliability of equipment, especially seals, also becomes paramount, as well as monitoring and maintenance of the plant.
Corrosion
H2S and CO2 are acidic when mixed with water, as the name acid gases suggests. High partial pressures and higher water content can lead to severe corrosion of steel pipework, and can lead to catastrophic leaks. The experience of the Kashagan project in Kazakhstan shows the time and expense that such corrosion can cause. The highest grade steels must be used for acid gas pipework, which can increase the expense of an operation, and there must also be constant corrosion monitoring.