Fertilizer International 502 May-June 2021
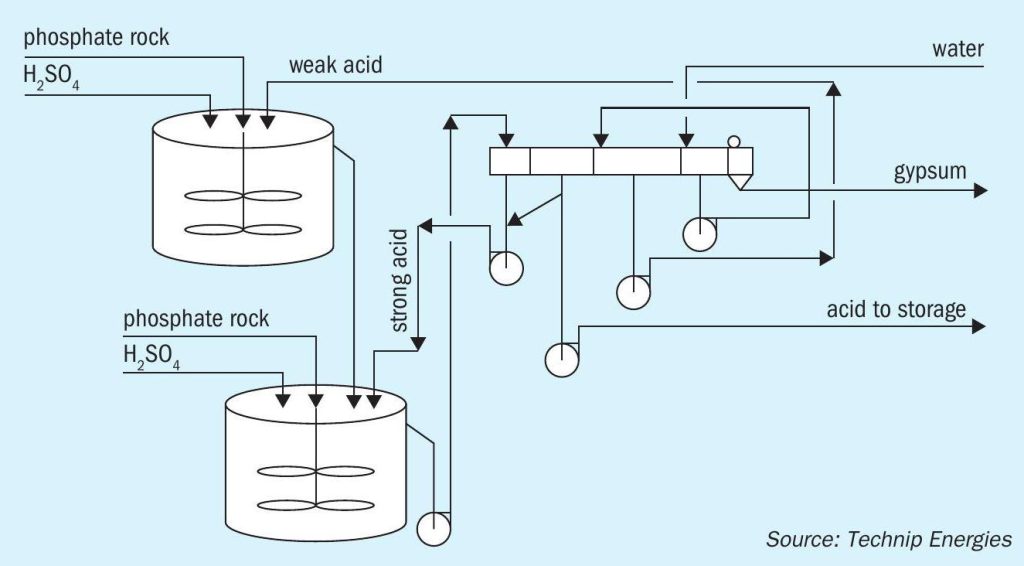
31 May 2021
Phosphogypsum in a circular economy
PHOSPHOGYPSUM USE
Phosphogypsum in a circular economy
Philippe Malsan of Technip Energies explains how high recovery Diplo phosphoric acid technology can generate phosphogypsum suitable for industrial reuse. Industrial cases studies for Senegal and Austria show how phosphogypsum from this process has been successfully recycled on a large scale for cement, plaster and other end uses.
Until recently, phosphogypsum (PG) produced from the wet phosphoric acid process, was mostly managed as a waste, stacked on land or rejected into the environment. Industrial practice is, however, evolving fast.
A recently published study by the International Fertilizer Association (IFA) reveals that up to 25 percent of phosphogypsum produced annually is now reused for a range of applications, such as mine restoration, agriculture, plaster and cement manufacture1 .
While other usage estimates are less optimistic, there remains a clear upward trend with more PG recycling over the last decade. This trend is expected to continue in the 2020s, along with new regulations and industrial technologies promoting more sustainable resource use.
While phosphogypsum for construction – in plaster, cement and other building materials – is one of the main reuse options, this market imposes strict limits on certain contaminants such as phosphorus (P2 O5 ), fluorine and radionuclides. That places additional constraints on phosphoric acid producers looking to reuse PG.
In the future, such quality considerations may favour phosphoric acid production technologies offering high P2 O5 recovery from phosphate rock. These technologies could help reduce the residual P2 O5 content of PG, and levels of other unwanted contaminants, so avoiding or minimising the need the need for purification treatment prior to reuse.
This article highlights Technip Energies’ high recovery di-hydrate (DH) technology – particularly its ability to generate high quality PG suitable for industrial reuse. This is illustrated by industrial cases studies for Senegal and Austria. These show how PG from this DH process has been successfully recycled commercially on a large scale for cement, plaster and other end uses.
Processing phosphate rock
There are several options for producing phosphoric acid from phosphate rock via the wet process route. Differences between these process options are mainly determined by calcium sulphate (gypsum) crystallisation conditions. Generally, gypsum is either precipitated in di-hydrate (DH) or hemihydrate (HH) form, or as a combination of both in successive steps. Crystallisation is a particularly important parameter when selecting a process technology that generates ‘clean’ gypsum as the desired by-product.
Standard single step DH process
The single-step DH process is widely used to produce phosphoric acid. The phosphate rock is treated with sulphuric acid to precipitate calcium sulphate as DH in one step in a reactor under agitation. A large recycling flow is achieved by agitation and/ or by external circulation associated with a flash cooling system.
The single-step DH process is a longstanding and mature industrial-scale technology that has been implemented since the 1950s. This process is by far the most flexible, compared to other phosphoric acid production routes, especially in terms of tolerance to phosphate rock impurities. Because of this, the DH process can handle a wide range of phosphate rock types. Its flexibility, together with low capex and high operability, are probably the main reasons why a large majority of the world’s phosphoric acid plants utilise the DH route.
It is generally accepted that the standard DH process achieves recovery yields of approximately 95-96 percent – this corresponding to typical reaction yields of 96-97 percent P2 O5 . If left untreated, with no removal of soluble impurities, this leaves approximately 0.8-1.1 percent residual P2 O5 remaining in the gypsum, unfortunately exceeding the quality standards for plaster or cement production.
The hemihydrate (HH) process
The single-step HH process has been successfully implemented in different countries around the world as an alternative to the DH route. The HH route presents several advantages, such as the production of higher strength acid (39-42 percent) containing less impurities. But the process does have a lower P2 O5 recovery (typically around 92 percent) compared to the DH route.
The PG produced from the HH route also contains more P2 O5 and more impurities, compared to PG produced via the DH route. The fact that HH gypsum reverts to the DH form, at a certain point post-production, is another constraint limiting the purification of PG. For these reasons, the HH route is generally not an option when there is a need to recover phosphogypsum for industrial applications.
Recrystallisation processes: DH-HH and HDH
Those technologies based on recrystallisation – either Hemihydrate to Di-Hydrate (HDH) or Dihydrate to Hemihydrate (DHH) – offer the highest P2 O5 recovery. This is due to the liberation of the co-crystallised P2 O5 during recrystallisation. These processes can also produce acid at higher strength compared to DH.
These advantages are offset by other factors, particularly the lack of flexibility of recrystallisation processes towards impurities. Because of this, their performance can depend strongly on the nature of the phosphate rock used as a raw material. Plants based on recrystallisation processes, being more complex and requiring more equipment, have lower plant availability, higher capex and higher maintenance costs, compared to DH plants. Neither do recrystallisation processes provide significant advantages in terms of contaminant levels in phosphogypsum (fluorine, sodium, organic matter etc.). This makes additional treatment of PG necessary before further use.
The two-stage Diplo process
In the 1980s and 1990s, a new approach to the DH method was developed by the French company Rhône Poulenc, the phosphoric acid technology predecessor to Technip Energies. The main purpose of this evolution in DH technology was twofold: firstly, to obtain higher P2 O5 yields and, secondly, to increase the concentration of the dilute acid produced at filtration.
This new approach successfully generated both higher P2 O5 yields and acid concentration, while keeping the original operational advantages of the DH route. This was of particular interest to producers in Europe who were sourcing from the merchant rock market and facing strong economic pressure to reduce their operating costs.
In the Diplo process, phosphate rock is digested using two reactors in series, with each reactor being fed phosphate rock, sulphuric acid and recycled phosphoric acid in set proportions (Figure 1). The conditions of the reaction – including temperature, P2 O5 concentration, and concentration of free sulphate in the acid – are optimised at each stage. In doing so, the Diplo process allows overall process performance to be optimised, according to the requirements of the producer, while still retaining most of the advantages of the traditional DH process.
As already stated, higher acid concentration and higher P2 O5 recovery can be obtained through this process, compared to the usual DH approach. These performance advantages depend on the nature of the phosphate rock:
- Enhanced P2 O5 recovery occurs with reactive sedimentary rocks.
- Higher concentrations of phosphoric acid, exceeding 35 percent P2 O5 , can be produced from some phosphate rocks such as Togo or Taiba.
Another advantage of the Diplo process is the high stability offered by its optimal two-stage reaction/filtration treatment step. This reaction-filtration system offers higher performance stability relative to the traditional DH system.
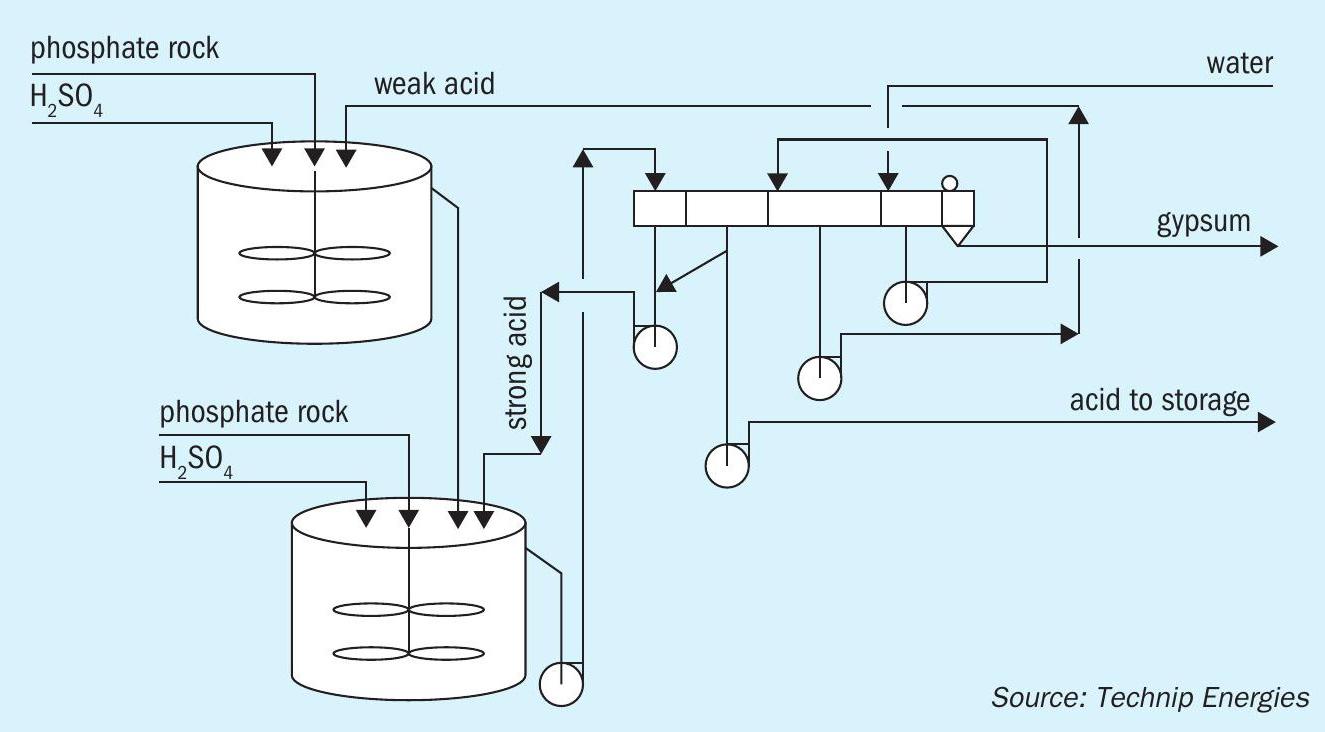
Diplo process for high P2 O5 recovery
When targeting high P2 O5 yields, 70-90 percent of the phosphate rock is reacted in the first reactor. The first reactor is operated at lower P2 O5 concentration, higher temperature and with higher excess sulphuric acid. Combined, these conditions tend to reduce co-crystallised losses in gypsum. The remaining phosphate rock is reacted in the second reactor, increasing the P2 O5 concentration of the acid. Excess sulphuric acid in the second reactor slurry is typically regulated close to 25-28g/l. This limits unreacted P2 O5 losses and avoid excess sulphate in the phosphoric acid produced.
Impact of PG impurities on plaster and cement production
Residual contaminants present in phosphogypsum obtained after filtration can be detrimental to PG reuse and may have to be removed or reduced below certain limits (Table 1).
Impact of the phosphate rock
The phosphate rock used in phosphoric acid production is the main source of residual impurities present in the phosphogypsum generated. For this reason, the composition and purity of phosphate rock raw materials have an important impact on the quality of the phosphogypsum.
Igneous phosphate rock types, such as apatite ore from Kola, Russia, and Phalaborwa, South Africa, and calcined rock have lower impurity levels and organic content compared to sedimentary rocks. The phosphogypsum produced from these rock types, depending on the phosphoric acid production technology used, can be sufficiently pure to avoid further treatment, or only require simple washing of the re-pulped gypsum to reach the required purity. However, these phosphate rock types only represent 15-20 percent of overall world production and are generally more expensive compared to sedimentary phosphates.
Sedimentary phosphate rocks, in contrast, generally contain higher levels of mineral and organic impurities relative to their igneous counterparts. Consequently, when sedimentary rocks are consumed as raw materials for phosphoric acid – as is the case in most plants globally – the amounts of impurities remaining in the phosphogypsum are correspondingly higher, and a purification step is therefore generally necessary.
Regardless of the technology used for phosphoric acid production, some contaminants, such as soluble impurities and organics, will still affect the quality of phosphogypsum and therefore need to be removed prior to reuse.
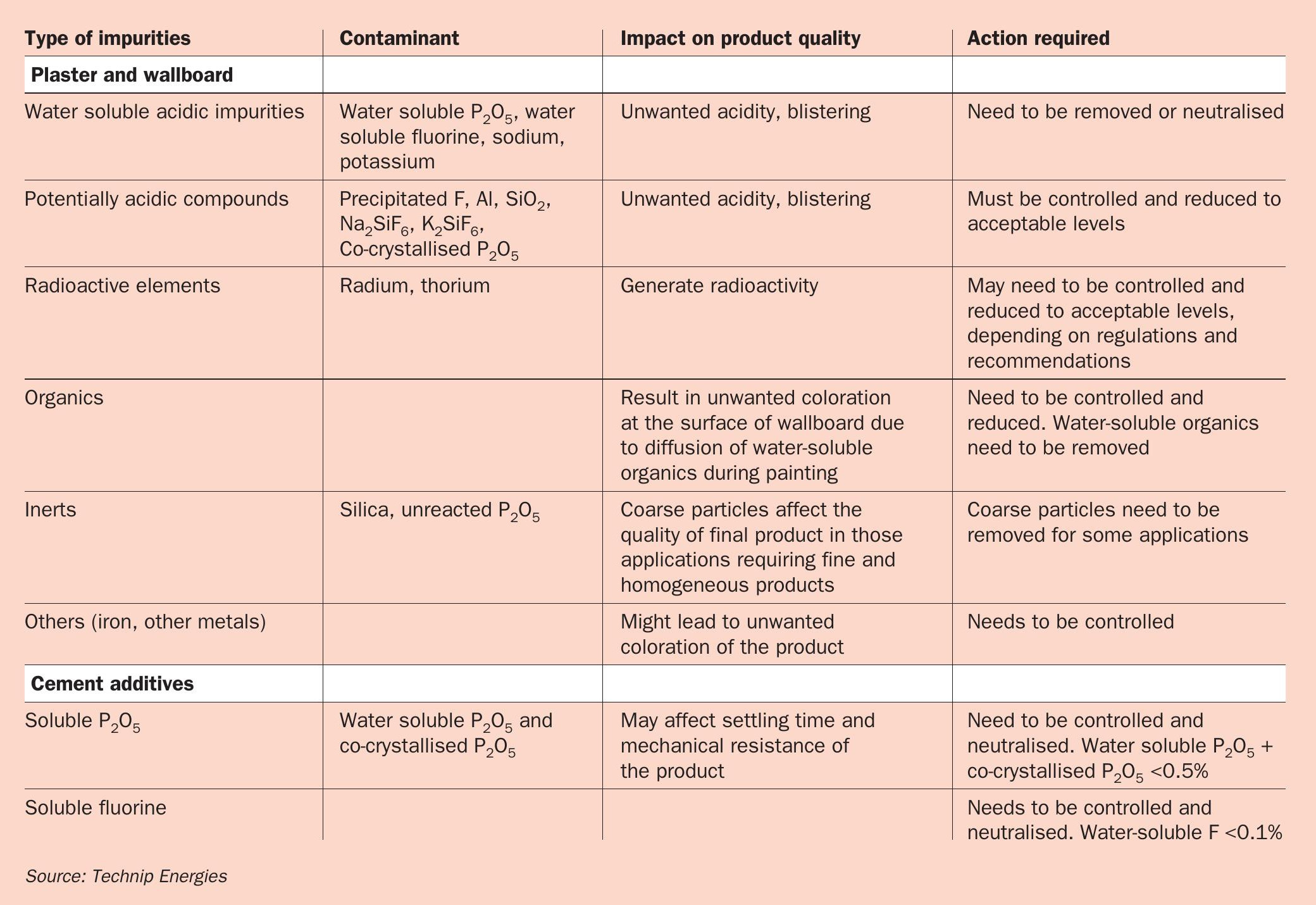
Case study: reuse of PG for cement in Senegal
Industries Chimiques du Senegal (ICS) is the largest producer of phosphate fertilizer products in sub-Saharan Africa and the third largest producer on the continent. The company began mining phosphate rock in 1960 and later started producing phosphoric acid in 1984.
Following the acquisition of ICS by Indorama in 2014, a rehabilitation programme has improved phosphoric acid output with levels expected to recover to 600,000 t/a P2 O5 . ICS Indorama currently operates two phosphoric acid trains – Darou 1 and Darou 2 – both based on Technip Energies’ technology.
Darou 2, the second train, was started in 2002 with a nameplate production capacity of 1,200 t/d (reaction-filtration), and a nominal capacity for 53 percent phosphoric acid of 1,015 t/d. This unit, which is based on Technip Energies’ two-stage Diplo technology, is designed to consume a blend of Taiba rock phosphate concentrate and slimes. This allows Darou 2 to achieve a reaction yield of 97.7-98 percent P2 O5 recovery. The corresponding 2-2.3 percent P2 O5 reaction losses represent insoluble P2 O5 , this consisting of a 50:50 mixture of unreacted P2 O5 and co-crystallized P2 O5 locked in the gypsum. The total insoluble P2 O5 remaining in the gypsum is below 0.5 percent.
At ICS Indorama, the PG produced by the phosphoric acid plant is discharged dry and stacked, where it is then exposed to the prevailing weather including both rain and sun. Under these repeated wetting and drying conditions, a decrease in mainly soluble P2 O5 and fluorine occurs. The residual humidity – an important factor for the economics of phosphogypsum reuse – is also reduced below ten percent free water due to natural drying.
Aged phosphogypsum is reclaimed and directly used as an additive for clinker production without further treatment. An analysis of ICS phosphogypsum sampled from various depth in the stack is provided in Table 2.
ICS Indorama is exploring other potential markets for phosphogypsum, including use as an agricultural soil amendment and use in the remediation of saline soils. The company has developed a new phosphogypsum formulation for soil amendment purposes. This granulated product functions as a calcium source, and contains residual P2 O5 and useful secondary elements such as magnesium and sulphur, all of which contribute to soil fertilization.
This use of phosphogypsum as a constituent in roadbed construction is another potential application being targeted by ICS Indorama. As a result of these efforts, industrial and agricultural sales of phosphogypsum have increased substantially in recent years, generating additional revenues for the company.
Historic case study: reuse of PG for plaster production in Austria
Donau Chemie was a major European phosphoric acid producer in the 1980s and 1990s. The Austrian company combined production of phosphoric acid for fertilizer production with the manufacture of plaster from phosphogypsum. The latter was sold into the local European market as wallboard and other high-quality products.
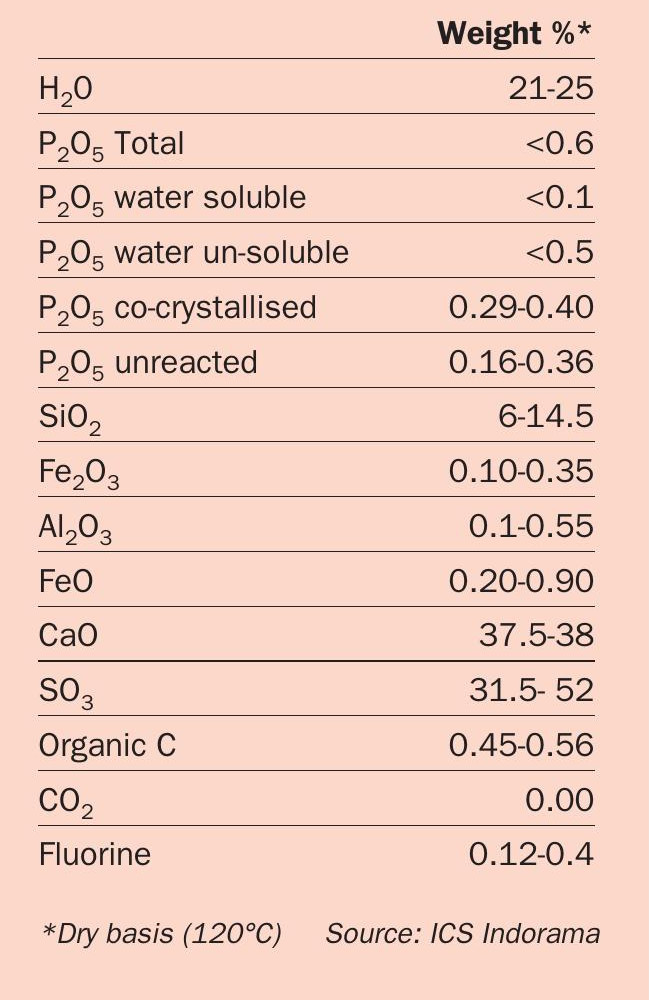
Donau Chemie converted its phosphoric acid plant to the high recovery two-stage Diplo DH process in 1987. This sourced sedimentary phosphate rock as a raw material from various countries such as Algeria, Jordan, Syria and Israel. The converted Diplo plant achieved its expected performance levels, with a reaction yield slightly above 97.7 percent P2 O5 , as well as generating phosphogypsum suitable for plaster production.
The phosphogypsum underwent a treatment process prior to plaster production. This involved repulping PG from the phosphoric acid filter, energetic washing and screening, and two- or three-stage hydrocyclone separation, before being filtered in a final dewatering step (Figure 2).
This treatment process separates off soluble impurities, impurities such as organics absorbed at the surface of crystals, and insoluble impurities that concentrate in the coarse and fine fractions. The treatment also successfully reduced the radioactivity of the final gypsum product, enabling it to meet the Austrian standard for building materials.
This simple and robust treatment process was successfully operated in-line with the phosphoric acid plant. This enabled Donau Chemie to send the purified gypsum by-product obtained directly to the plaster plant for calcination.
Table 3 compares the performance of two different phosphogypsum treatment processes: a simple filtration process with counter-current washing versus hydrocyclone size separation plus filtration.
Conclusions
In a circular economy, where greater reuse of phosphogypsum will be expected, phosphoric acid production via the DH process offers the most promise. This process route is adaptable to most commercially-extracted phosphate rock types globally, whether low- or high-grade, being more tolerant to raw material impurities.
While the HDH and DHH recrystallisation processes deliver high rates of P2 O5 recovery, they have several drawbacks compared to DH. They are less accepting of variations in phosphate rock quality, especially more impure lower-grade rock. Higher capex, increased maintenance costs and lower plant availability also tend to offset their other advantages.
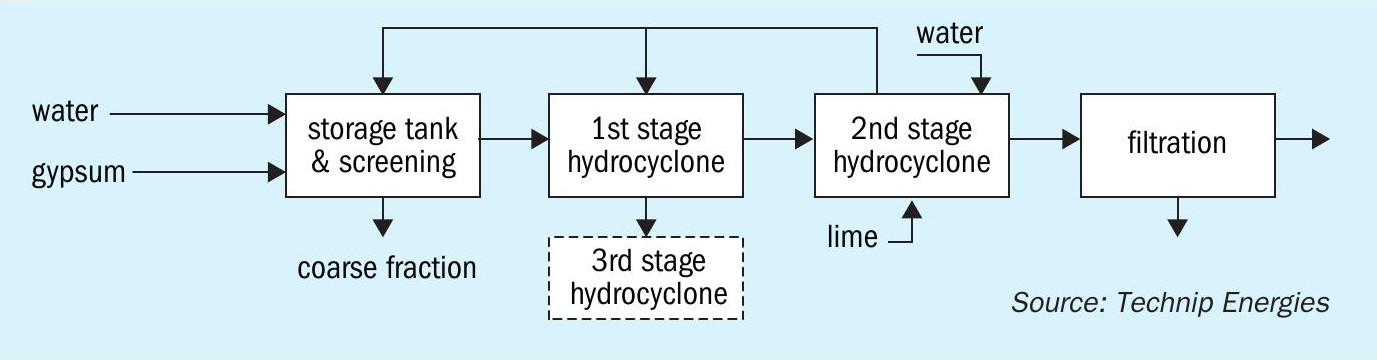
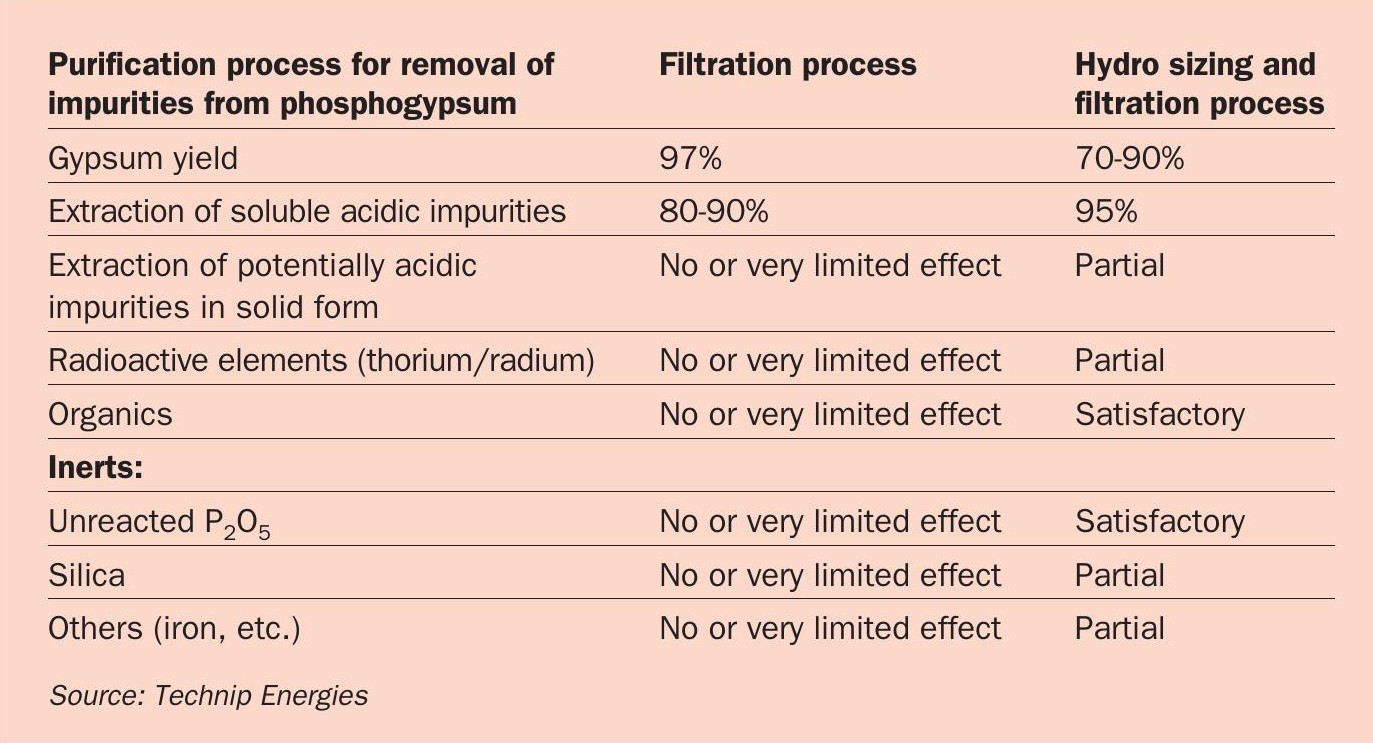
When using sedimentary phosphate rock as a raw material – and independent of whether a HDH, DHH or DH process is used – a phosphogypsum purification step is generally recommended to ensure product quality reaches an acceptable standard.
The high recovery, two-step Diplo process from Technip Energies combines significant P2 O5 recovery with the typical advantages of the DH route, such as the flexibility to accept different sedimentary phosphate rock types. Depending on the phosphate rock source, the process can solubilise around 97.5-98.5 percent of the P2 O5 during the reaction step. The Diplo process can also be easily combined with a simple phosphogypsum purification process, avoiding the need to consume costly high-quality phosphate rock. Other benefits include: process simplicity, ease of operation, low maintenance cost, high plant availability and low capex.
Currently, most phosphoric acid plants globally operate the DH process due to its advantages over other production routes. Looking ahead, the DH route is expected to remain the first option for most phosphoric acid producers in future, at least in the medium term. In this scenario, robust production processes, such as high recovery Diplo technology from Technip Energies, will be required to meet the challenge of greater phosphogypsum recycling and reuse.
References