Sulphur 394 May-Jun 2021
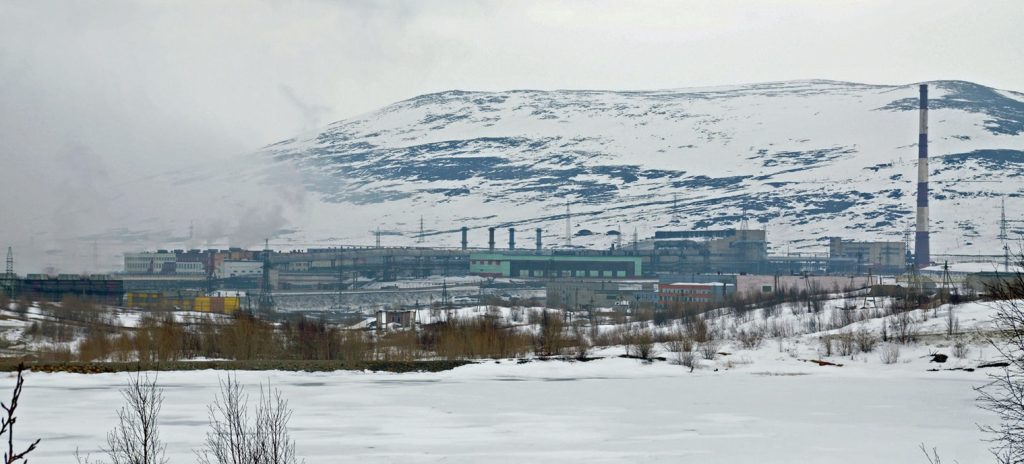
31 May 2021
Sulphuric Acid News Roundup
UNITED KINGDOM
Inovyn to close sulphuric acid plant at Runcorn
Ineos subsidiary Inovyn has announced the permanent closure of its ‘sulphur chemicals’ (mainly sulphuric acid) plant at its Runcorn site, and its withdrawal from the UK sulphur chemicals market. The company said in a statement that the decision follows a management review of the business in the light of recent events. Specifically, in October 2020, an unexpected interruption to the third-party power supply to the Runcorn site resulted in the plant being taken offline, and during restart, it was identified that a number of critical plant components had suffered significant damage. As a result, to ensure the safety and integrity of the plant it was taken back offline. Since then, in spite of significant effort and investment to rectify these issues, Inovyn says that it has become clear that it will not be possible to safely restart the plant for at least a further 18-24 months, and the company has decided to close the plant permanently.
The move has sent shockwaves through the UK sulphuric acid market. The plant produced 300,000 t/a of sulphuric acid at capacity, and was the main domestic source of acid for downstream industries in the UK, including water treatment, chemicals and fertilizer production. The UK also imports around 330,000 t/a of acid, mainly from Germany, Finland and Norway, but its ability to almost double this in a short period is very much open to question.
BOTSWANA
Metso Outotec to supply technology to copper-silver project
Metso Outotec has signed a euro 17 million contract to deliver all of the main process technologies for Sandfire Resources’ flagship Motheo copper-silver concentrator in Botswana. The 3.2 million t/a greenfield plant will be built in the Kalahari copper belt in Botswana, with the potential to expand to 5.2 million t/a in the future. Metso Outotec will deliver all key minerals processing equipment including gyratory and pebble crushers, apron feeders, semi-autogenous (SAG) mill and flotation cells, fine grinding mill, high rate thickeners, and a pressure filter. Additionally, spare parts and supervisory services will be supplied to support commissioning and plant ramp up. Delivery will take place during 2021 and 2022, and the plant is expected to start production in late 2022 or early 2023.
“We are pleased to continue our strategic partnership with Sandfire Resources. We have worked with Sandfire in the past and are very grateful to be selected again for their flagship Motheo project. Our proven proprietary and sustainable technologies will support Sandfire with achieving their international growth and diversification strategy,” said Kai Rönnberg, Vice President, Minerals Sales, Asia Pacific at Metso Outotec.
FINLAND
Metso Outotec completes reorganisation of Metals business
Metso Outotec has completed the reorganisation of its Metals business as part of the turnaround program announced in Q4/2020. As a result of negotiations with employees and other stakeholders, approximately 100 jobs will be reduced globally, including 15 in Finland. Most of the global reductions are through redundancies and the rest through other arrangements, such as retirements, non-renewal of fixed-term contracts, and voluntary resignations. In addition, over 50 employees who were in the scope of the Metals reorganization will continue in Metso Outotec in other parts of the company.
“The reorganisation of the Metals business aims for annual savings of e15 million”, said Jari Ålgars, President, Metals business area at Metso Outotec. “During the negotiations, we carefully evaluated all opportunities with the target to find the best possible options to meet the needs of our customers and employees. The now completed reorganisation empowers the Metals business lines for efficient use of resources and faster decision-making.”
UNITED STATES
ITC supports duties on phosphate imports
The United States International Trade Commission (ITC) ruled in March that subsidies associated with the import of phosphate fertilizers from Morocco and Russia are injuring the United States industry, and announced that the US Department of Commerce “will issue countervailing duty orders on imports of phosphate fertilizers from Morocco and Russia.”
Last August, the ITC announced that it would continue its investigation and said that it had “determined that there is a reasonable indication” that the United States’ industry was being harmed by the tariffs. In its accompanying publication, the ITC noted that The Mosaic Company filed petitions on June 26, 2020 alleging that it had been injured because of the subsidies given to imports of phosphate fertilizers.
Mosaic said in a press release that this decision will help make the American fertilizer industry more competitive. “Mosaic employees are proud to support American farmers by producing high quality, reliable fertilizer,” said Mosaic President and CEO Joc O’Rourke. “Today’s decision upholds our belief that fair trade is a cornerstone of a healthy U.S. economy, and that American farmers will benefit from having a more competitive American fertilizer industry.”
Mosaic reported that the Department of Commerce will levy duties of 20% for OCP, a Moroccan producer. Russian producers will have duties of 17% except for PhosAgro which will be 9% and EuroChem at 47%. These increased duties will remain for at least five years.
Leak from phosphate waste water pond
Florida Governor Ron DeSantis declared a state of emergency in early April after a waste water leak from the Piney Point phosphate mine flooded roads and threatened to pollute local watercourses. The long-abandoned mine operated from 1966 to 2001, but phosphogypsum waste from phosphate processing still sits in large piles at the site; around 5 tonnes of phosphogypsum for every tonne of phosphoric acid produced, up to 1 billion tonnes of phosphygypsum across the state as a whole. The wrinkle in Florida is that the phosphpgypsum is mildly radioactive due to the presence of uranium in the phosphate ore.
Around 215 million gallons of acidic waste water were pumped into Tampa Bay, and while around 223 million gallons remain in the pond at Piney Point, repair crews were able to stop the leak. Two additional stacks with wastewater containment ponds remain at Piney Point, and fears have been expressed that an unaddressed breach could lead to a sudden rush of water from these ponds.
Meanwhile, Mineral Development LLC has broken ground on a $70 million secondary phosphate recovery facility in Polk County, Florida. The plant is designed to produce 1.2 million t/a of high-quality phosphate rock in a range of qualities from 29% to 34% P2 O5 , extracting phosphate from mine tailings and reusing water from existing ponds. The process helps restore the land to its original state with native vegetation and natural surface water flow while providing high-grade phosphate essential to feed the world’s growing population, according to the company. MDL’s facility is the first independent phosphate beneficiation plant built in the US in over 30 years.
GERMANY
‘Next generation’ electrostatic precipitators
Dürr Megtec has launched what it describes the “next generation” of wet electrostatic precipitators (WESP) to efficiently clean industrial gases of fine particulate matter, acid mists and aerosols to meet global environmental regulations and protect downstream equipment. A strong focus was placed on the system’s high-intensity, offline automatic cleaning features, which reduce maintenance efforts, eliminate carryover of entrained matter during washing and provide better operational performance during cleaning. System components are also now easily accessible for maintenance inspections, the company says. In order to enhance the performance of its WESP, Dürr Megtec aimed at achieving a more efficient contaminant capture. This was achieved through increased operating voltage that requires less collecting surface area. Additionally, the gas distribution system was completely reimagined to optimise flow through the system, and various tube shapes and electrodes were tested to improve overall performance. Standardised modules are used in the new design, reducing engineering time and streamlining fabrication. The systems are assembled from different standard modules and adapted to customer-specific requirements. Modules with tube bundles are pre-assembled in Dürr’s production facility for shipment to the customer. All electrodes are pre-loaded and pre-aligned, for reduced installation times. The company says that its WESPs can remove up to 98% of particulate in a single stage, depending on the characteristics of the gas stream. Increased removal efficiency is possible with alternative configurations.
RUSSIA
Nornickel to close Monchegorsk
Russian metal producer Norilsk Nickel has announced that it will close its nickel smelter in the city of Monchegorsk in Russia’s Kola Peninsula near the borders with Norway and Finland as part of the company’s programme to move towards greener production. Closing the smelter will reduce sulphur dioxide emissions in Monchegorsk to less than 30,000 t/a in 2021, and taken together with the December 2020 shutdown of the smelter at Nikel, it will reduce the company’s emissions in the Kola Peninsula by 85% in 2021 compared to the figure for 2015. Next year, emissions will be limited to 22,000 t/a of sulphur dioxide, of which 8-9,000 (depending on the season) will be from the power plant, which also heats homes in Monchegorsk. Nornickel plans to upgrade the plant and build a modern copper refining facility in the town with double the annual capacity – up to 150,000 t/a – and higher environmental standards.
“The old, ineffective plant will be closed and a new one meeting the highest environmental standards will be built in its place,” said Norilsk Nickel’s Vice President for Strategy Sergey Dubovitsky. “These standards mean that almost all gases will be captured. The project also provides for utilisation of these gases and the production of sulphuric acid.”
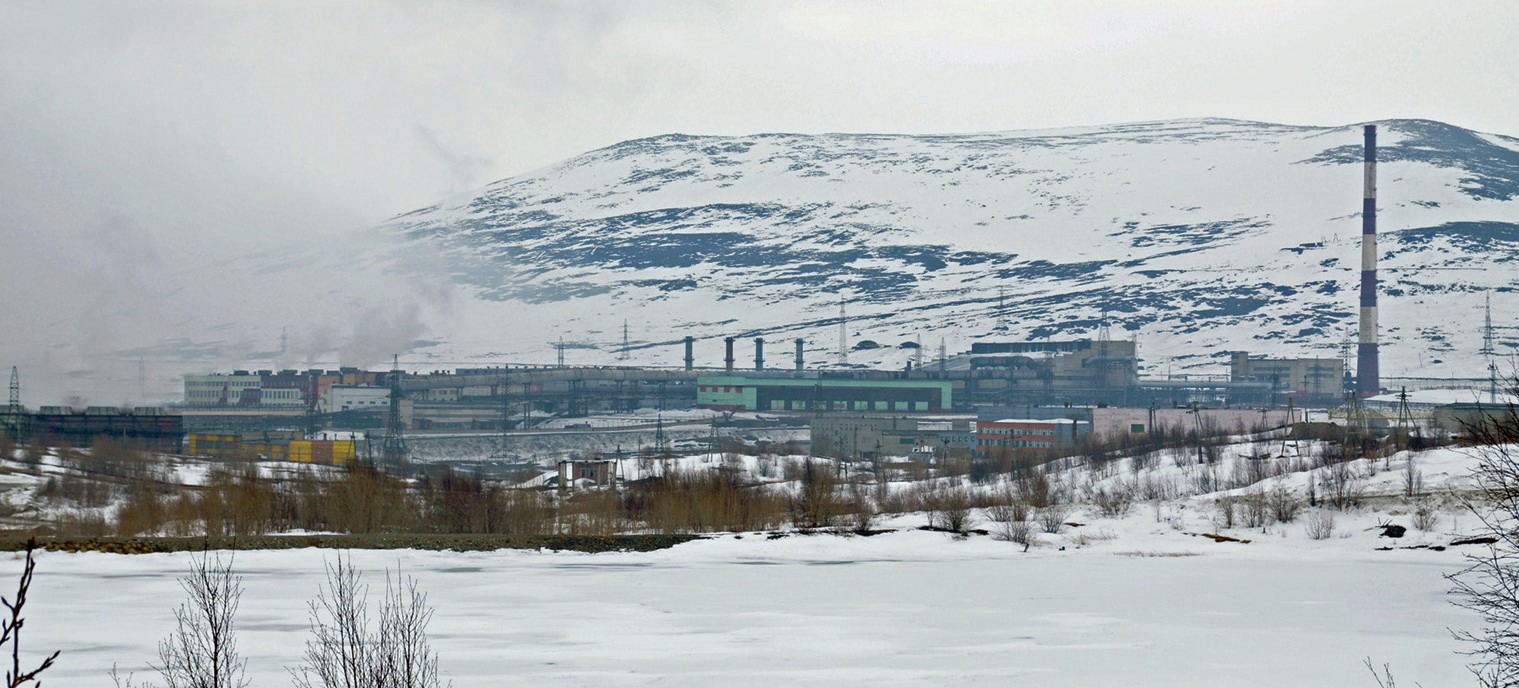
Nornickel plans to build a new copper line on the Kola Peninsula by 2025, and before that copper output will be moved to its polar division, where facilities have already been upgraded. It is also aiming to increase production at its nickel refinery in Finland due to surging demand for battery raw materials in the European market. Mainly powered by renewable energy, the Harjavalta plant uses sulphuric acid leaching for nickel semi-products to enable hydrometallurgical production of 65,000 t/a of high purity nickel using ore from Russia. Nornickel plans to increase production at the NN Harjavalta plant to 75,000 t/a in 2023 in the first phase. The production will be further increased to exceed 100,000 t/a by early 2026 in the second phase.
TURKEY
Škoda to provide steam turbine for acid plant
Czech manufacturer Doosan Škoda will supply a 15 MW steam turbine, generator and associated equipment for the Etimaden EMET sulphuric acid plant being built in Kütahya Province. The company’s engineers will also supervise assembly of the unit at the construction site. The plant will be in continuous operation for 330 days a year and the steam turbine will generate electricity from residual heat for both the plant’s own operation and the surrounding area.
“The EMET sulphuric acid production facility will make a significant contribution to Turkey’s boron treatment and boron products process which have a wide range of usage areas including but not limited to agriculture, cleaning, metallurgy, health and textile,” said Yaman Coşkun, representative of Turkish EPC contractor Ekon. “Alongside the production of sulphuric acid, the plant will also supply electricity to the EMET Boron.”
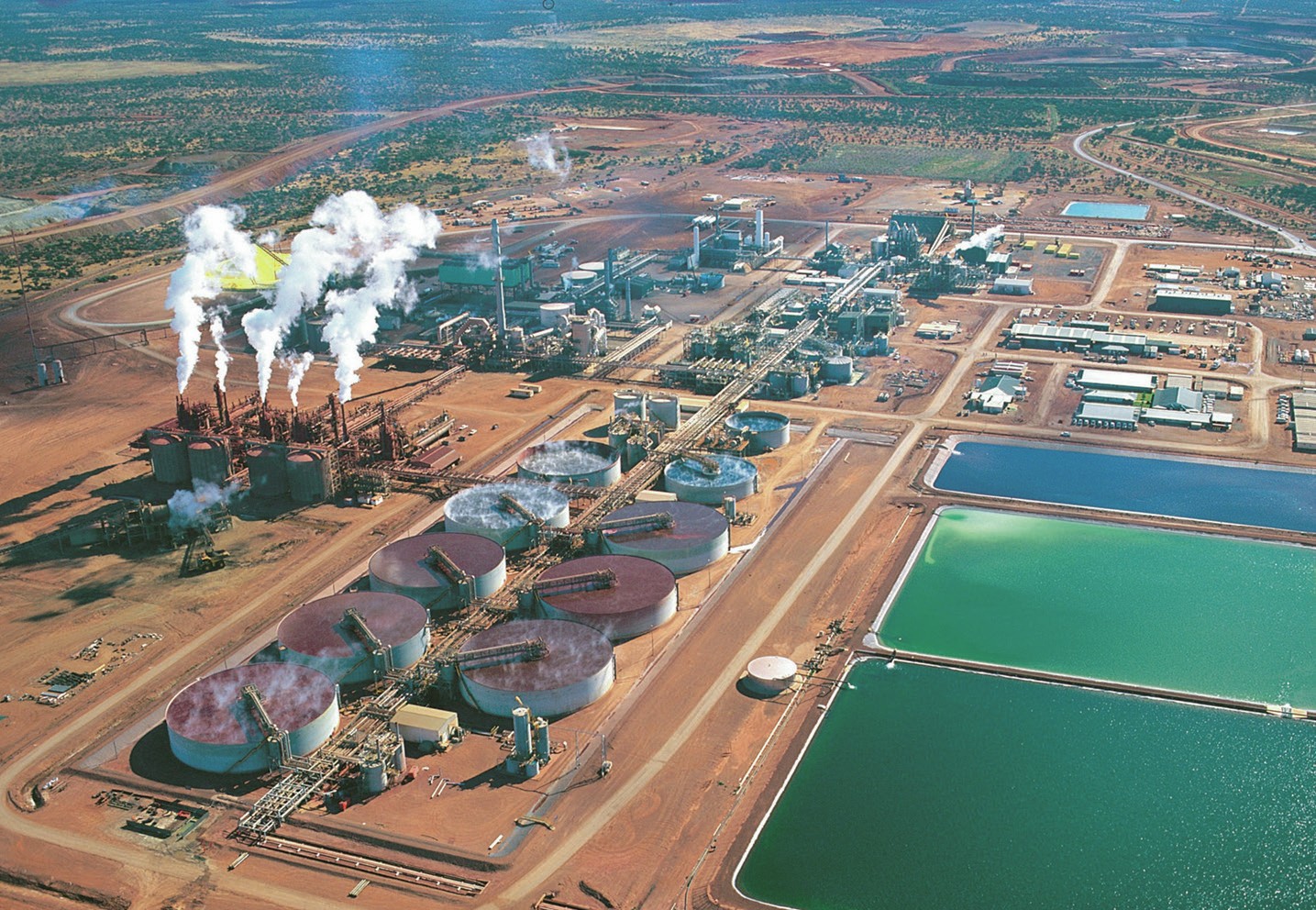
Doosan Škoda Power is on a tighter deadline than usual, having 12 months from the date of signing the contract to supply the turbine unit to the construction site. Foundation bolts and other built-in components are scheduled to be delivered by February 2022, said project manager Lucie Franková.
ZAMBIA
New acid plant for copper processing
Kumbele Mining Ltd, owned by a consortium of Chinese investors, has set aside $150 million to develop a small scale copper processing plant in Chingola. According to the environmental impact assessment (EIA) report submitted to the Zambia Environmental Management Agency, the copper reclamation project is expected to have a lifespan of 30 years. The plan is to process tailings from the Nchanga open pit mine, the second largest in the world, using a hydrometallurgical process. The company statement says that: “Kumbele Mining Limited intends to develop and operate a copper mine as well as construct and operate a copper processing plant, a sulphuric acid plant and tailing storage facility within the exploration area in Chingola.”
CHINA
Smelters taking enforced downtime
Tight supply in the copper market is squeezing copper smelters, especially Chinese ones, leading many to take maintenance downtime, according to Reuters. A lack of concentrates supply has caused smelter treatment charges to tumble and reducing the smelter sector’s profitability. China’s top smelters failed to agree a minimum floor price for second-quarter purchases, and Goldman Sachs estimates that 700,000 t/a of annual capacity will be affected in April, two million tonnes in May and a further 900,000 t/a in June. This could result in a loss of processed metal of up to 250,000 tonnes, and a corresponding dip in acid supply. Worldwide, copper smelting activity has slipped to its lowest in at least five years in March.
DEMOCRATIC REPUBLIC OF CONGO
Glencore reports acid spill
Glencore has confirmed that a tank containing sulphuric acid ruptured in March at its Kamoto Copper Company (KCC) mine in Katanga Province. The company said that a “limited release” of acid had occurred during maintenance at KCC. “At approximately 7pm on 16 March, KCC experienced a limited release of acid from Tank Farm 1 during maintenance work. There was no explosion,” Glencore said in a statement. “Follow-up with the community was conducted to advise of the event and our community officers have not registered any complaints nor concerns from their engagement with the surrounding communities.”
INDIA
New smelter for India
India’s Adani Enterprises says that it plans to build its first copper cathode facility via a new subsidiary three years after the country’s biggest copper smelter – Vedanta’s Tuticorin – was ordered to close.
In its submission to the Indian environmental regulator, Adani subsidiary Kutch Copper Ltd (KCL) said that the new copper complex will consist of 900,000 t/a of primary copper smelting capacity and 100,000 t/a of copper scrap smelting capacity.
The Tuticorin smelter remains idle after its closure by the Tamil Nadu Pollution Control Board (TNPCB). The company has recently suggested that the smelter’s oxygen plants could be utilised to meet India’s ongoing demand for medical oxygen as the Covid pandemic enters a new phase in the country. The Sterlite Copper plant has two oxygen plants with a combined capacity of 1,000 t/d of oxygen, according to the company.
INDONESIA
Finance deal for HPAL plant
Singapore bank DBS Group says that it has co-led a group of lenders in a $625 million financing deal for a nickel and cobalt project in Indonesia. The project by PT Halmahera Persada Lygend is expected to be the first plant in Indonesia to use high-pressure acid leach (HPAL) technology to produce nickel and cobalt chemicals used in making batteries for electric vehicles. DBS, Southeast Asia’s biggest bank, said it has joined BNP Paribas BNPP.PA to lead a consortium with seven other banks to launch a $600 million term loan facility and a $25 million working capital facility in a seven-year deal for the HPAL project. The other lenders were Indonesia’s Bank Mandiri BMRI.JK, Bank Negara Indonesia BBNI.JK, OCBC NISP NISP.JK, Bank Central Asia BBCA.JK, Malaysia’s Maybank MBBM.KL, Singapore’s Oversea-Chinese Banking Corp Ltd OCBC.SI and United Overseas Bank Ltd UOBH.SI.
Based in Indonesia’s Obi island, the HPAL project is a joint-venture between China’s Lygend Mining and Indonesia’s Harita Group.
“PT HPAL is committed to controlling the use of energy sources in every step of our production processes in pursuit of good environmental governance through implementation of low emission technology,” a PT HPAL spokesman said.
AUSTRALIA
Acid plant failure cuts production at Murrin Murrin
Glencore says that it has temporarily reduced production at the Murrin Murrin nickel-cobalt operation in Western Australia following a malfunction at an acid plant at the site. The plant, 880km east of Perth in the north-eastern Goldfields region, processes and refines nickel and cobalt to produce LME grade metal briquettes on site. Glencore said that a component failure occurred at one of the two acid plant fans at the site. Details were not disclosed regarding how long repair work may take.
Glencore’s Murrin Murrin site comprises a high-pressure acid leaching (HPAL) plant and a refinery, a 90MW power station, and a 4,400 t/d acid plant. In 2020, the mine accounted for about 31% of the company’s nickel production.