Sulphur 395 Jul-Aug 2021
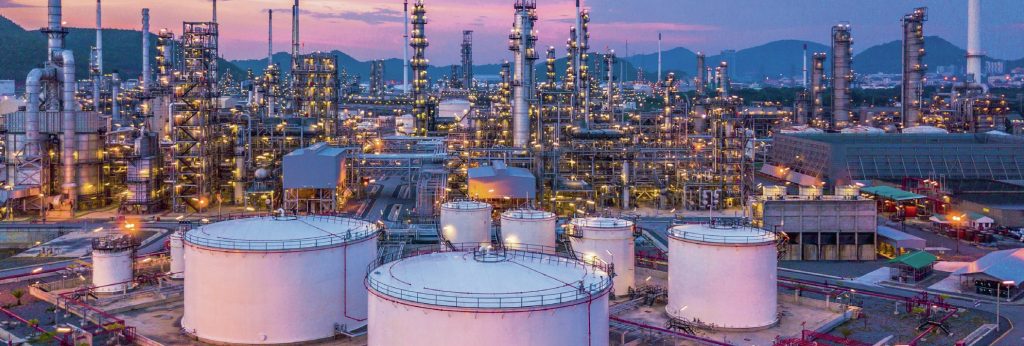
31 July 2021
Crude to chemicals
CRUDE TO CHEMICALS
Crude to chemicals
With demand for conventional fuels projected to peak and fall over the next decade, some refiners are looking to petrochemical production as a way of diversifying their product slate.
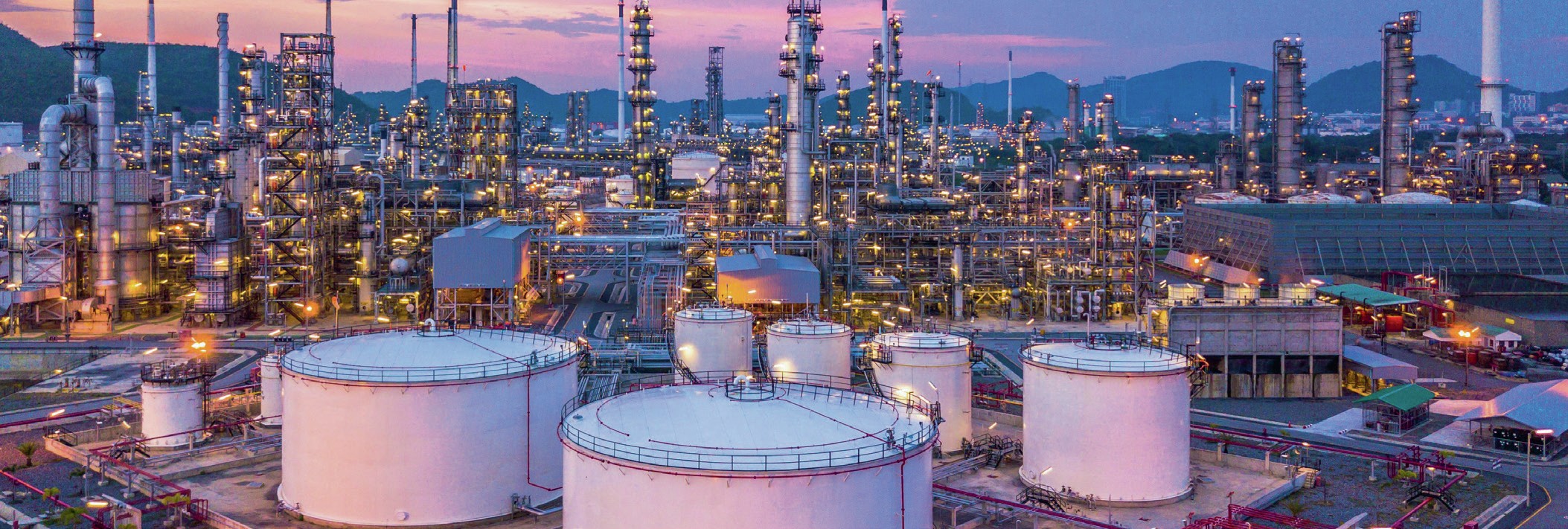
Most refineries are reliant on the production of liquid fuels. On average, around 55% of all refinery products are sold as gasoline, diesel and other middle distillates, kerosene etc, as well as bunker fuels, and refineries depend upon the difference between the price of oil that they buy and the price of the fuels that they sell to make their margin. Conversely, petrochemicals like olefins such as ethylene and propylene, aromatics, glycols, and polymers represent currently collectively only 5-20% of refinery output, depending on the refinery’s configuration.
Traditionally, the relationship the relationship between refining and petrochemicals has been at one remove; refineries focused on fuels production, and sold the naphtha that they produced to operators of steam crackers, who would then turn it into ethylene, propylene, and other basic chemical building blocks. However, changes in the market for oil products, on both the supply and demand sides, are now encouraging refinery operators to integrate petrochemical production into their product slate.
Market changes
On the demand side, car sales have been tapering off even in the developing world, and vehicles are becoming more fuel efficient, requiring less gasoline per unit. Also, while currently still only a small sector of the market, there is the growing push for hybrid and electric vehicles – many countries in the developed world are planning to ban the sale of fossil fuel driven vehicles from about 2030. Overall, the US Energy Information Administration predicts that US fuel consumption for light-duty vehicles will decline by 1% annually through 2050. At the same time, there are tightening regulations on sulphur content of fuels and the carbon dioxide that they produce when burnt, which are placing increasing pressures on refineries to invest in expensive process equipment items to remove more sulphur and produce less, e.g., high sulphur fuel oil as against more middle distillates. US fuel oil demand is predicted to fall by 25% this decade.
In contrast to fuels, petrochemical markets continue to be relatively buoyant. In spite of a growing backlash against ‘single use plastics’ in the developed world, global demand for plastics products and synthetic fibres continues to grow, and with them demand for olefins such as polyester and aromatics like paraxylene. Urbanisation and rising wealth in the middle classes of developing nations are also driving above-GDP growth rates, and China’s consumer boom in particular has led to increasing demand for packaging, consumer goods, and car parts.
One the supply side, the past decade has seen a surge in output from US tight oil production. This lighter crude slate has meant higher light distillate yields for LPG, naphtha and gasoline, resulting in higher light products with potential for chemical integration. At the same time, increased output of natural gas liquids from US shale gas production also encouraged ethane cracker investments, with a lower ethylene production cost than naphtha, especially given how low US natural gas prices have gone. But US tight oil production has also moved the US close to self sufficiency in oil and led to significant US oil exports for the first time in decades, bringing down the price of oil globally and shutting out some medium and heavy grades as OPEC cuts production.
IHS Markit suggests that the pull of changing demand means that oil refiners are seeing an opportunity to convert lower value oil into higher value chemicals and therefore seeking to “push” barrels of oil (displaced and new) into chemical markets. This is leading to increasing interest in crude to chemicals technologies, which in effect merge a refinery and petrochemical plant into one; in theory returning higher margins to refiners relative to more traditional fuels products. Figure 1 shows projections by Wood Mackenzie that over the next 15 years most new demand for oil-based products is going to come from the chemical sector.
Three ‘generations’ of crude to chemicals
There are three ‘generations’ of crude to chemicals technology, but all have the common feature of increasing the refinery yield of light olefins (ethylene or propylene) or aromatics such as benzene, toluene, and xylene. In general, to maximise the conversion of crude oil into petrochemicals, the refiner must utilise streams that would otherwise be used for the production of fuels such as kerosene and diesel to produce naphtha, as well as upgrading heavy bottom of the barrel products into steam cracker friendly feedstocks.
The first ‘generation’ depends upon existing refinery units and can typically produce chemical yields of 15-20%. The second generation of technologies now being integrated into new and existing refineries can lift this to 40-50%. Future, ‘third’ generation designs could potentially convert up to 80% of a crude barrel into petrochemicals.
As far as existing technologies go, a typical refinery begins with fractional distillation, breaking down the crude feed into its constituent parts, ranging from light, shortcarbon-chain molecules such as gasoline, naphtha, and propane to heavy diesel and vacuum gas oil (VGO). VGO is usually then further processed in a downstream hydrocracker or fluid catalytic cracker (FCC), depending on the desired product output. Hydrocracking is targeted towards diesel production and generates no olefins, since any double bonds are hydrogenated, but naphtha from the hydrocracker can be sent either to an ethylene steam cracker to produce olefins or to a reformer to be refashioned into aromatics. To increase chemical output, hydrocracker operators can target naphtha rather than diesel production. FCC units meanwhile break down VGO into gasoline. The process generates propylene at around 5-20% of output, but refiners can run FCCs at higher severities (higher temperatures and longer residence times) to increase propylene yield further.
Crude to chemicals options
A variety of ‘second generation’ options now exist for refinery crude to chemicals processing. One is the direct processing of crude oil via steam cracking to produce ethylene and a small quantity of propylene. The direct use of crude oil in steam cracking for the production of light olefins has historically been hampered by coke formation and fouling of crackers, but ExxonMobil have a process using light crude which has been in operation in their Singapore refinery since 2014 (see below).
Saudi Aramco has filed patents for the integration of hydroprocessing/de-asphalting with steam cracking for olefin production. The hydro-processing/de-asphalting step produces a highly paraffinic, de-asphalted and de-metalised stream, which can later be processed in the steam cracking unit.
Middle distillates such as diesel and residues from vacuum distillation can be hydrocracked to produce a naphtha range stream, which then be processed to produce aromatic compounds.
Axens offers its H-Oil process in association with naphtha fixed-bed hydrocrackers. Light naphtha is routed to a steam-cracker, whose olefinic streams have to be selectively hydrogenated. Heavy naphtha is dedicated to the aromatics block, designed to synthesise benzene, toluene and xylene. It also has a high severity FCC (HSFCC) process using deep feed pretreatment and its patented permutable reactor system (PRS) upstream of the HSFCC to maximise the overall olefins yield.
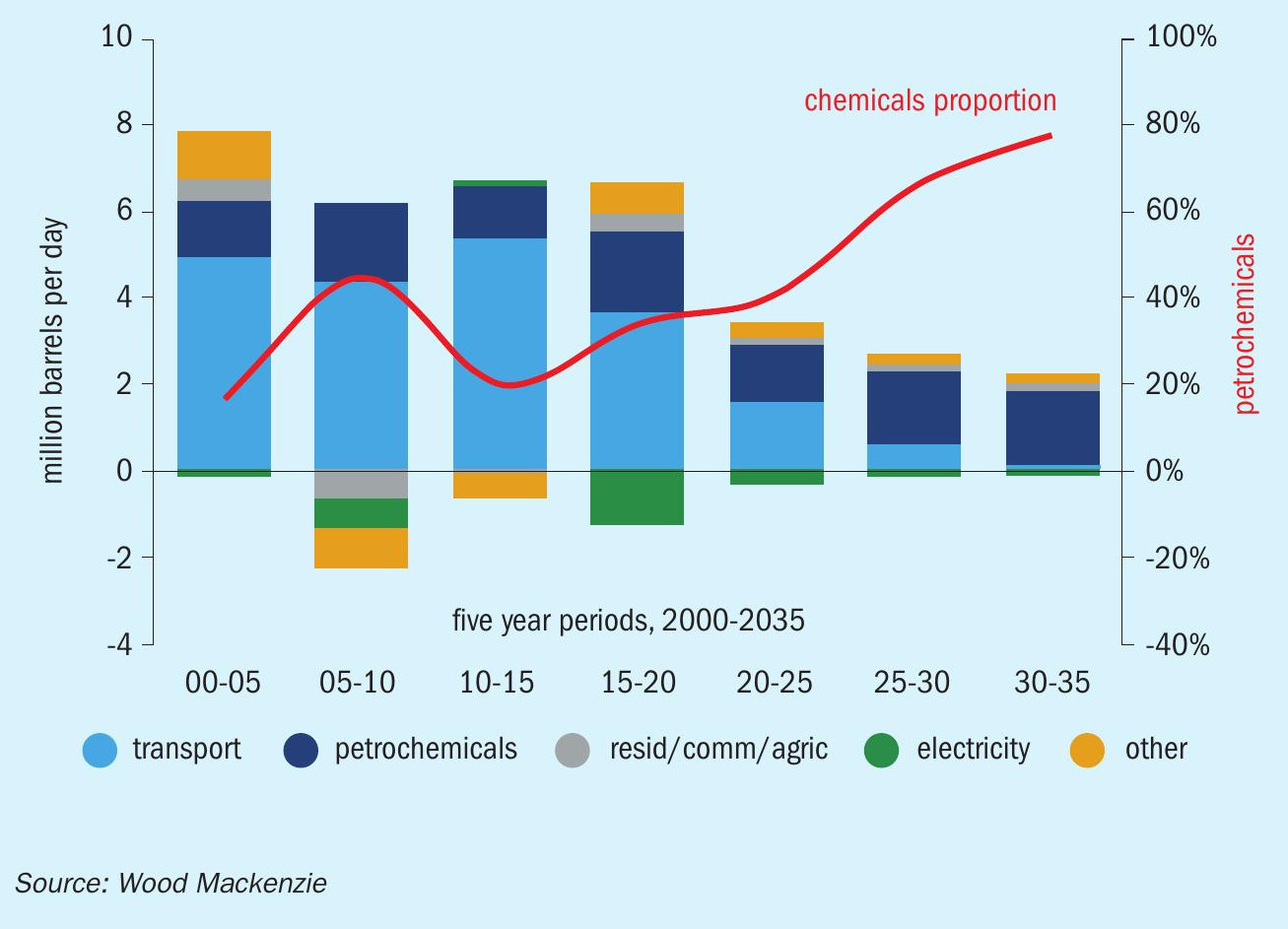
Benefits of integration
One of the benefits that can come from integrating petrochemicals production with refining is that it provides an opportunity to integrate and optimise allocation of resources and feedstocks, maximise the process streams that can be shared and exchanged between the two halves of the facility, and allow the sharing of utilities, logistics and energy costs. It may also allow a producer to switch product yields between refining and chemicals, depending on where the greatest value lies at the time. All of this can help to reduce cost and improve overall profitability. It can also decrease capital intensity through scale; refinery scale petrochemicals production can be much larger than standalone petrochemical sites and offer corresponding efficiency gains.
Aramco said that its thermal crudeto-chemicals technology (developed with Axens and TechnipFMC) could cut capital costs by 30% compared to conventional refining by allowing several oil treatment steps to be combined into one operation – removing sulphur, cracking heavy fractions etc into a suitable feedstock for steam cracking via several ‘layers’ of catalyst.
Asia
The majority of crude to chemicals plants planned or operational have been in Asia and the Middle East. One of the first movers was ExxonMobil, which opened an ethylene cracker in Singapore in 2014 based on crude feedstock rather than naphtha. ExxonMobil has its own proprietary technology which allows the processing of light crude directly by pre-heating of the crude oil, partially vapourising the heated crude in a flash tank and feeding the vapor from the flash tank to the steam cracker to produce ethylene, propylene, and related products.
In India, Reliance has a crude oil to chemicals project under development at its Jamnagar refinery – the world’s largest – which plans to more than double crude conversion to chemicals. The project will convert the site’s entire FCC capacity to Petro-FCC, and will add large naphtha catalytic cracking, steam cracking, and aromatics blocks to raise chemicals conversion to over 35% for the site.
S-OIL at Ulsan in South Korea has recently built the world’s first commercial high severity FCC unit coupled with heavy oil hydrodesulfurisation and associated units to reduce high sulfur fuel oil production. The project has raised crude conversion to chemicals from 8% to 13% for the refinery.
China
China’s huge demand for petrochemicals and the fall in global oil prices around 2014-15, along with the opening up of crude import licences to private companies, and the ban on Chinese refiners from exporting fuels have all combined to encourage Chinese refiners to cross into crude to chemicals production. The first was Hengli Petrochemical’s 400,000 bbl/d refinery and paraxylene complex in Dalian, which came on-stream in 2019. The plant is capable of processing 20 million bbl/year of crude, using Axens technology, including H-Oil ebullated bed hydroconversion technology for processing vacuum residue, a Solvahl de-asphalting unit for processing of unconverted residue, hydrocracking for processing atmospheric gas oil to produce the maximum yield of naphtha and hydrotreating for naphtha processing. Continuous catalytic regenerative reforming maximises aromatics production from naphtha, with paraxylene purification for full isomerization of other C8 aromatics into paraxylene. The plant overall yields around 40% chemicals production, mostly paraxylene for polyester fibre and polyethylene terephthalate (PET) production.
A similar sized project is underway at Zhejiang Petrochemical, which is building a crude-to-chemicals complex in two phases in China’s Zhejiang Province. Each phase has a capacity of 400,000 bbl/d of crude processing, with around 50% of this going to make chemicals. UOP is providing technologies for the complex, including hydrocracking to break down vacuum gas oil into naphtha and reforming and extraction to make aromatics from the naphtha. At capacity, it will produce 8.8 million t/a of paraxylene, as well as 500,000 t/a of propylene using UOP propane dehydrogenation technology.
Shenghong Petrochemical is another large project, looking to process 300,000 bbl/d of crude, again with paraxylene as the main chemical output. The first crude distillation unit at Zhejiang Phase 1 came onstream in November 2020, and the second in March 2021.
Saudi Aramco
One of the largest crude to chemicals projects on the horizon was to have been at Yanbu in Saudi Arabia, where state oil company Saudi Aramco and state petrochemical giant Sabic – itself now 70% owned by Aramco – were planning a $20 billion petrochemical complex based on processing 400,000 bbl/d of Arabian light crude into 9 million t/a of downstream chemicals and base oils, with an on-stream target date of 2025. The facility would sell 45-50% of its output as chemicals, including olefins, aromatics, glycols, and polymers. It was seen as an acknowledgement by the world’s largest oil producer that the future of oil was in petrochemicals. Aramco had targeted $100 billion in chemical investments out to 2035, to convert 3 million bbl/d of oil – one third of its output – into chemicals. The company has been developing its own patented crude to chemicals technology in partnership with Chevron Lummus Global and McDermott. The company has also signed an agreement with Axens and TechnipFMC to work on a high-severity FCC process for chemicals.
However, in October 2020 came signs that Aramco and Sabic were reassessing this plan, with an announcement that they were instead considering integrating Aramco’s existing refineries in Yanbu with a mixed feed steam cracker and derivative olefins units. The companies said in a joint statement that this would increase cost efficiency and competitiveness as well as creating value opportunities for petrochemicals. The reassessment was prompted in the covid-related collapse in global oil demand and prices, and a need for Aramco to cut costs, particularly on the capex side.
According to Sabic, however, the two companies maintain that they are still committed to “advancing crude to chemicals technologies through existing development programs with the goal to increase cost efficiency.”
A glut of chemicals?
The scale of production from refinery crude to chemicals plans can be large. A 400,000 bbl/d refinery producing chemicals at 45-50% of output will be generating 10 million t/a of petrochemicals, compared to 2 million t/a for a typical naphtha-based ethylene cracker. East Asia in particular could face a problem with the combined paraxylene output of China’s new crude to chemicals plants and consequent oversupply in the Asia-Pacific aromatics market; China imports 11 million t/a of paraxylene per year, and will temporarily more than achieve self sufficiency (although demand is continuing to increase), displacing product from South Korea, Taiwan and Japan.
On the other hand, olefins markets are likely to be less affected, as they are generally already quite large. Furthermore, while large crude to chemicals projects can cost billions of dollars, increased crude to chemicals production might lead to a rethink in the scale of a typical refinery. Refineries are often large because margins are slim, but the higher margins achievable from chemicals might mean smaller facilities were more profitable.
Changing the industry
Crude to chemicals offers the possibility of radically reconfiguring the refining industry, at least as far as some of the large scale operators are concerned. The impact on the sulphur industry may not be a profound one – most sulphur is already recovered from a barrel of oil. However, it has the potential to prevent any future decline of the refining industry in the face of falling fuel demand, as well as switching refining activity towards more advantaged feedstock locations as well as places where petrochemical demand is rising. Research and analysis company FutureBridge suggests that the type and level of refinery and petrochemical integration will primarily be driven by feedstock advantage, and hence will vary from region to region. In the US and the Middle East, which are not dependent on crude oil imports where there is sufficient availability of cheap natural gas liquids, direct production of crude oil to chemicals could become the prevailing option, whereas for regions, such as Europe and Asia, dependent on crude oil feedstock import and with limited availability of NGLs, the adoption of crude-to-chemicals technology will be governed by the capital efficiency of the project and demand for the petrochemicals output.