Nitrogen+Syngas 372 Jul-Aug 2021
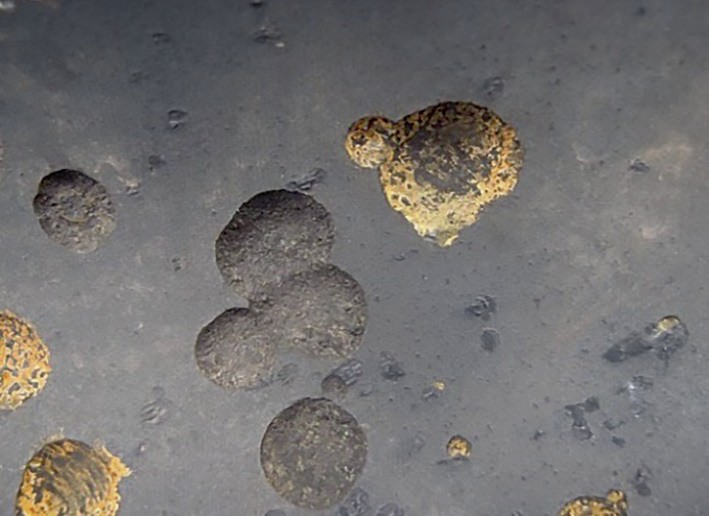
31 July 2021
Metal dusting attack on steam reformer components
METAL DUSTING
Metal dusting attack on steam reformer components
Metal dusting corrosion damage on steam reformers is no longer a major issue in modern methane steam reformer units. Nevertheless, failures related to metal dusting corrosion attack still take place in some specific designs and configurations that are more prone to experience this damage. Poor maintenance or deterioration of insulation components on transition areas might expose metallic surfaces to metal dusting attack. In this article, Dr P. Cardín and P. Imízcoz of Schmidt+Clemens Group describe different case studies, where the end users benefited from the experience of a collaboration to address potential risks and improve plant reliability against metal dusting corrosion damage.
Metal dusting is a type of corrosion damage similar to oxidation attack of carburised metal, reported in Fe, Ni and Co alloys. It is typically observed in industrial furnaces, boilers, and heat exchangers that operate in strongly reducing atmospheres (CO/H2 ). Final corrosion products are powderygraphite-metal mixtures. Compared with normal corrosion, it occurs randomly and progresses much faster. Ellipsoidal pits, found on the metal surface, are a characteristic indication of metal dusting1, 2 .
Metal dusting occurs due to the absorption of carbon into the metal, leading to the precipitation of metastable carbides and later decomposition of these carbides into metal particles and carbon (graphite). Metal dusting requires carbon activities greater than one (ac >1), to allow carbide formation and involve no-equilibrium gas compositions. Additionally, metal areas where a carbon-rich gas atmosphere (CO/ H2 ) becomes stagnant, are more prone to suffer from this severe corrosion attack2, 3 .
Steam reformer process gas, with its high carbon activity (ac ), can induce metal dusting corrosion attack on “cool” reformer zones. Modern steam reformer designs tend to avoid critical temperature areas where metal dusting attack might take place.
Nevertheless, damage or deterioration of insulation equipment in the outlet portions of tubes can produce metal dusting corrosion attacks as seen in Fig. 1. In this case, a standard material 25Cr35NiNbTi in a process gas heater, experienced severe pitting (maximum pitting depth up to 100 mm) after a relatively short period of time (1-2 years). Lower process gas temperatures, due to production restrictions, placed part of the heater into the critical temperature range for metal dusting corrosion damage.
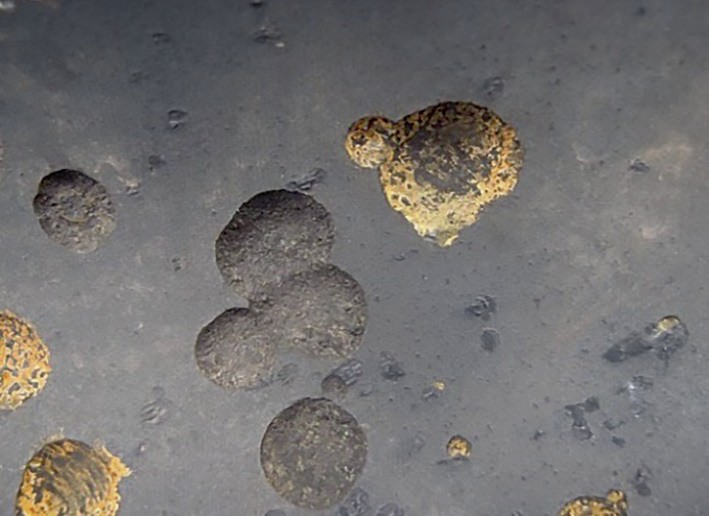
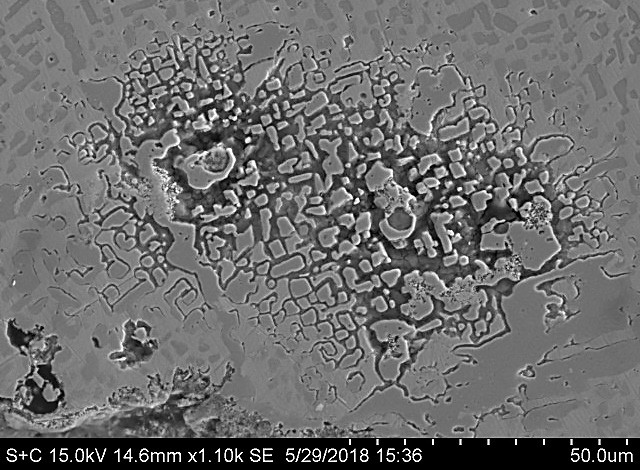
Factors influencing metal dusting damage
The metal dusting attack mechanism was widely described by Grabke et al and other authors, for different types of steel materials. For high alloy steels and Ni-alloys, several steps lead to metal dusting damage incidence4,5,6,7,8 :
- The presence of local defects or damage to the protective oxide layers allowing the transfer and dissolution of carbon into the metal phase.
- Inward carbon diffusion causes carbide precipitation within the alloy material.
- Carbon concentration rises, leading to carbon activity values higher than one.
- For iron-based alloys, metastable carbides (Fe3 C) form as an intermediate phase that decomposes to graphite and metal particles. For Ni-alloys, graphite formed on the supersaturated solid solution destroys the alloy into graphite and metal particles.
- Metal particles formed by alloy disintegration act as catalysts for further carbon deposition and coke growth on affected areas, leading to an extension of the corrosion attack.
As mentioned, several factors influence the incidence of metal dusting on alloy materials:
- Temperature and pressure: It is commonly accepted that the temperature range where metal dusting takes place is within the range 480 to 815°C and the maximum rate of attack occurs at around 600 to 620°C. The lower temperature indicated should be taken as a practical temperature limit below which the rate of metal dusting damage will be acceptable/negligible for a wide range of steel materials8 .
- Pressure has a direct influence on carbon activity in the gas phase. Higher pressures lead to more severe metal dusting attacks.
- Protective oxide layers: In high alloy materials, oxide scales play a significant role in providing metal dusting resistance as carbon diffuses at a much lower rate through these protective layers. High Cr and Si contents favour the formation of strongly protective spinel/chromia/silica layers. Disruption/damage of these protective layers leads to alloy corrosion damage incidence. Cyclic operation between carburising and oxidising atmospheres could lead to metal dusting occurrence as oxide layers are no longer protective4, 6, 8 .
- High nickel contents: Ni-base alloys tend to exhibit a better resistance to metal dusting attack than Fe-base alloys, due to lower carbon diffusivity in Ni alloys. The lattice of Fe3 C almost perfectly matches the lattice of graphite, indicating that carbon atoms moving from the lattice of Fe3 C to the lattice of graphite is easier than that from Ni to graphite. Consequently, the energy barrier for the precipitation of carbon on the surface of Ni is higher than that needed for precipitation on the surface of Fe3 C, which leads to a lower carbon precipitation rates in Ni-alloys7 .
- Sulphur addition: It is also generally accepted that sulphur additions into the process gas can inhibit or delay the incubation of metal dusting damage on metal surfaces. Sulphur (S) deactivates metal surface catalytic activity and prevents carbon ingress and graphite nucleation by stabilising carbide structures formed. Nevertheless, S presence is mostly unwanted due to its impact on the activity of the steam reforming catalyst4,8 .
- Gas composition: Most studies described in the literature indicate that metal dusting is only driven by carburisation. Nevertheless, syngas in real plants is far more complex than laboratory metal dusting experiments. Steam (oxygen potential) in syngas mixtures is playing a major role in metal dusting. Consequently, metal dusting should not only be considered as a catastrophic carburisation, but as an active corrosion mechanism where both carbon and oxygen play a role in material degradation8 .
In industrial plants, the gas composition often remains relatively constant, and equipment suffering metal dusting corrosion is exposed to non-equilibrium gas. Areas where process gas becomes stagnant are more susceptible to metal dusting corrosion damage as in these areas, gas composition is most likely to shift to CO generation, increasing gas carbon activity9 .
Metal dusting attack on steam reformer components
Metal dusting damage is not a problem for “hot” steam methane reformer components (SMR) like reformer tubes and outlet manifolds. Metal temperatures are either much higher than the equilibrium temperature of carbon deposition reactions (Boudouard reaction) or much lower on the metal shell of refractory-lined outlet manifolds (cold collectors).
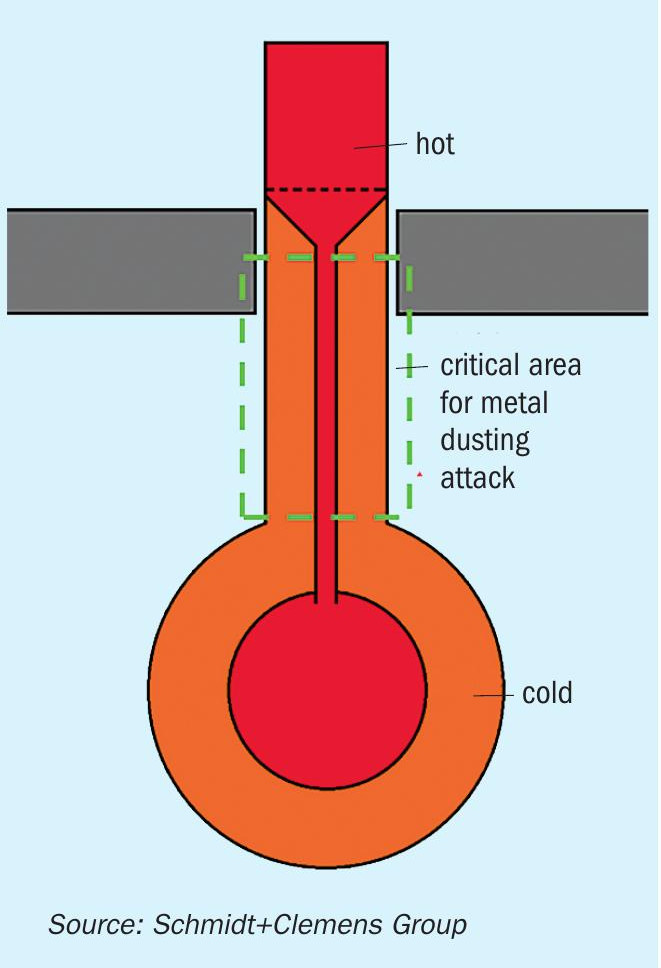
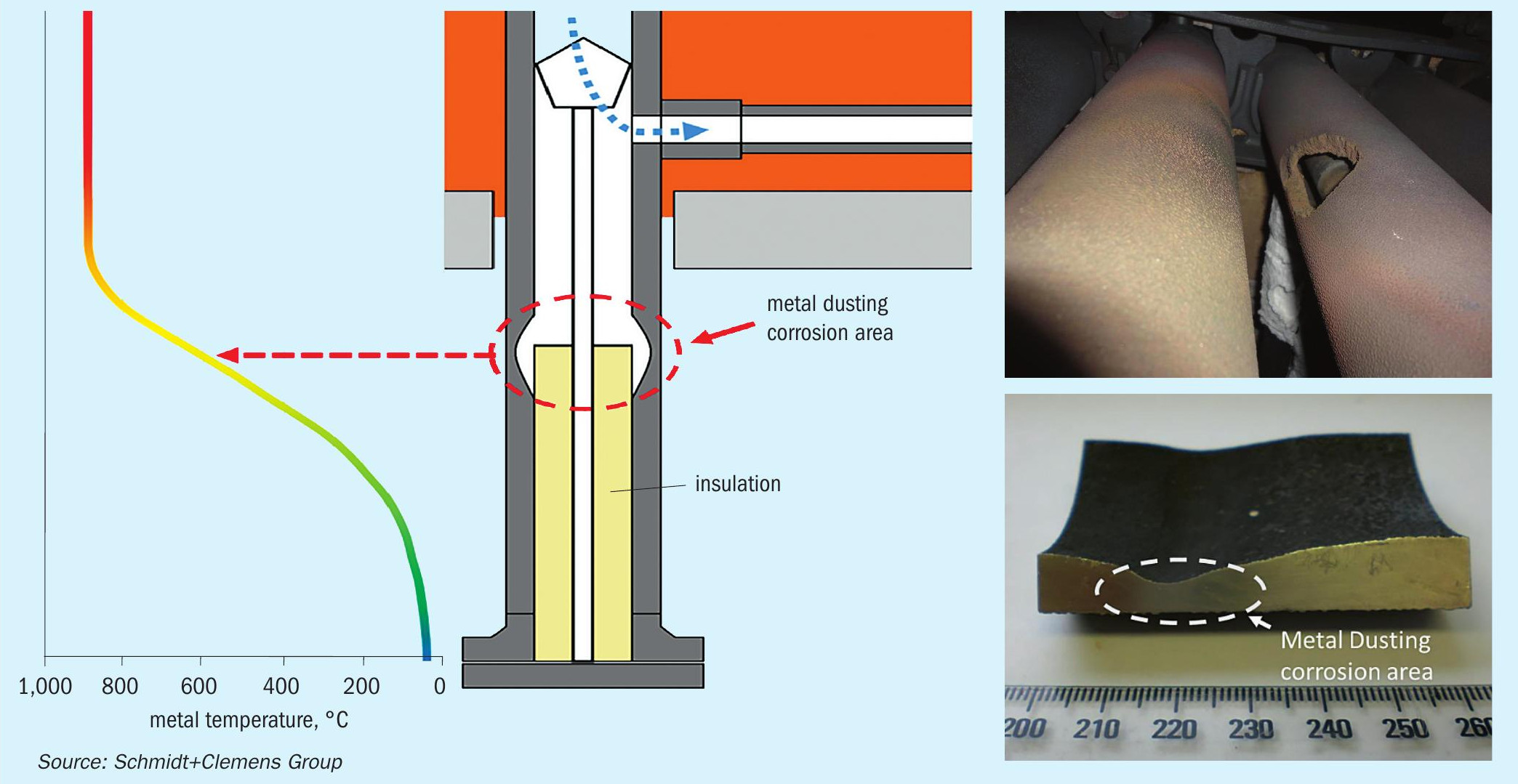
“Cold” outlet manifold designs are in principle more prone to suffer metal dusting corrosion damage. Problematic areas for metal dusting corrosion are located between “cold” and “hot” zones (see Fig. 2), like transition areas from the hot reformer tubes to refractory-lined manifolds or cold collectors. In such transition areas (see Fig. 3), metal temperatures might reach a critical temperature of 600°C. Modern “cold” outlet manifold designs make extensive use of a refractory lining system to maintain metal temperatures well below 450°C. Nevertheless, metal dusting corrosion issues still take place in such designs. Refractory components suffer deterioration over time, requiring inspection and maintenance to ensure they remain capable of controlling metal temperatures. Excessive thermal cycling also affects refractory components on a larger scale than metallic ones, opening cracks and cavities between refractory lining and metal components, leaving stagnant gas zones where tube metal temperatures reach the critical range of 600°C and the stationary gas is more aggressive due to CO enrichment. Consequently, initial pitting takes place on these metal surfaces. Further process gas recirculation increases the incidence of metal dusting corrosion on affected surfaces. Some designers are considering high Ni-Cr materials (like Schmidt+Clemens’ Central-loy® ET 45 Micro), to minimise metal dusting damage incidence on these critical transition zones.
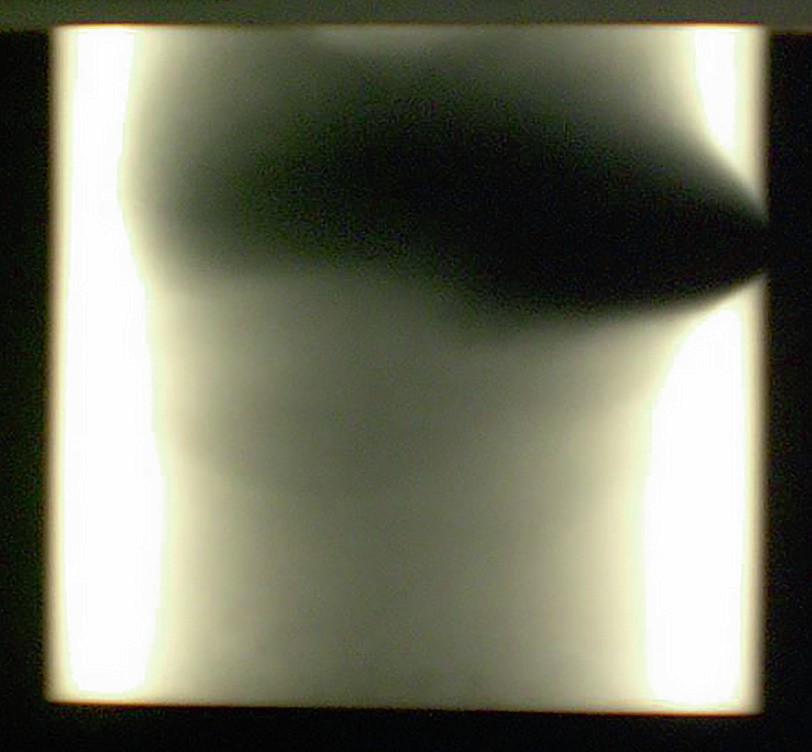
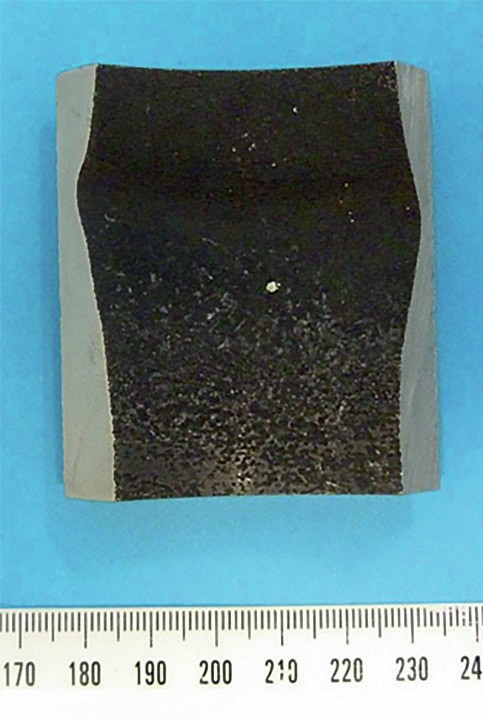
Although “hot” outlet manifold systems are in principle less susceptible to metal dusting damage, some designs may experience such corrosion damage in transition areas, as shown in Fig. 3. Critical areas for metal dusting damage are transition zones where temperatures might reach the critical metal dusting range and gas flow restrictions could lead to metal dusting damage incubation. Although actual design is intended to prevent these critical points, process issues like refractory deterioration could leave some gaps, as illustrated on Fig.3, between the insulating refractory and the tube metal surface. Lack of insulation of these transition areas, leads to an increase in tube metal temperature, approaching the critical temperature of 600°. Gaps created between the refractory and tube are filled with a stationary process gas. Since gas recirculation rate is relatively limited, it becomes more aggressive due to CO enrichment. Both effects combined promote metal dusting damage incubation. In many cases, end users are not aware of this damage incubation until the part fails due to corrosion damage. Replacing tube material with more resistant high Ni-Cr alloys might mitigate the incidence of metal dusting damage in these transition zones. Design modifications, re-designing these critical areas, could also minimise metal dusting in such specific cases.
Damage awareness is complicated due to the relative complexity of these transition areas. The presence of refractory insulation complicates access to metal surfaces, as these refractories may not be easily removed and inspection work could induce further damage on them, increasing the risk of metal dusting damage. Non-destructive inspection techniques (NDT), like radiography and ultrasonic inspection, can be used to assess metal dusting damage presence within these transition areas, without the need to perform more complicated operations (see Fig. 4). Frequent maintenance of critical insulation components, helps to minimise metal dusting occurrence on steam reformer transition zones.
Schmidt+Clemens experiences in metal dusting corrosion
Process gas heaters (PGH) in the direct reduction of iron, suffer from severe metal dusting damage. For such applications high chromium and nickel cast alloys, like Centralloy® ET 45 Micro, provide excellent corrosion and creep resistances. Schmidt+Clemens has also supplied high Ni alloys for steam reformer components (SMR) suffering from metal dusting corrosion damage, replacing standard cast tube materials, like alloy Centralloy® G4852 Micro. Based on Schmidt+Clemens’ extensive experience, sufficient metal dusting resistance can be achieved if the following criteria are met:
- High chromium contents (>25 wt-%) are required in order to form fully protective an stable oxide layers. Lower contents might not be able to provide enough resistance for more demanding applications.
- Presence of other additions like Si, Mn and Al could improve the formation of stable oxide layers. Additions of selected rare earth elements would enhance oxide layer adhesion, thus increasing metal dusting resistance.
- High Ni contents reduce inward diffusion of carbon into alloy material. Consequently, protective alloy effect is strongly favoured, as well as high temperature resistance.
- Sulphur (S) additions in the range of 35-50 ppm delay incubation of metal dusting damage. Carbide decomposition in metal dusting atmospheres is effectively retarded by the presence of S, while coke formation might be delayed. Unfortunately, process gas “contamination” with S additions is undesired on steam reforming applications, due to catalyst deactivation issues.

Centralloy® ET 45 Micro is a high alloyed nickel base material consisting mainly of a Cr-Ni-Fe-Si matrix (see Table I). High chromium level, rare earth additions and primary carbide formation provide the best compromise between good high temperature corrosion resistance and high temperature creep rupture strength, offering a superior metal dusting resistance than standard reformer tube material Centralloy® G4852 Micro (25Cr35NiNbTi) (Table 1).
Alloy ability to maintain a protective and stable oxide layer under metal dusting conditions is the main barrier to prevent material corrosion4,6,7,8 . Once this protective oxide layer is penetrated, lower diffusion of C within material can delay the incubation of metal dusting damage. Superior corrosion resistance of alloy Centralloy® ET 45 Micro versus alloy Centralloy® G 4852 Micro is summarised on the following SEM images (see Figs 5 and 6), exhibiting more protective oxide layers after several corrosion cycles. While Centralloy® ET 45 Micro alloy is capable of maintaining a fully protective oxide layer after these corrosion cycles, alloy G 4852 Micro was unable to maintain a protective oxide layer under the same aggressive conditions, showing unprotected metal surfaces that could incubate metal dusting damage.
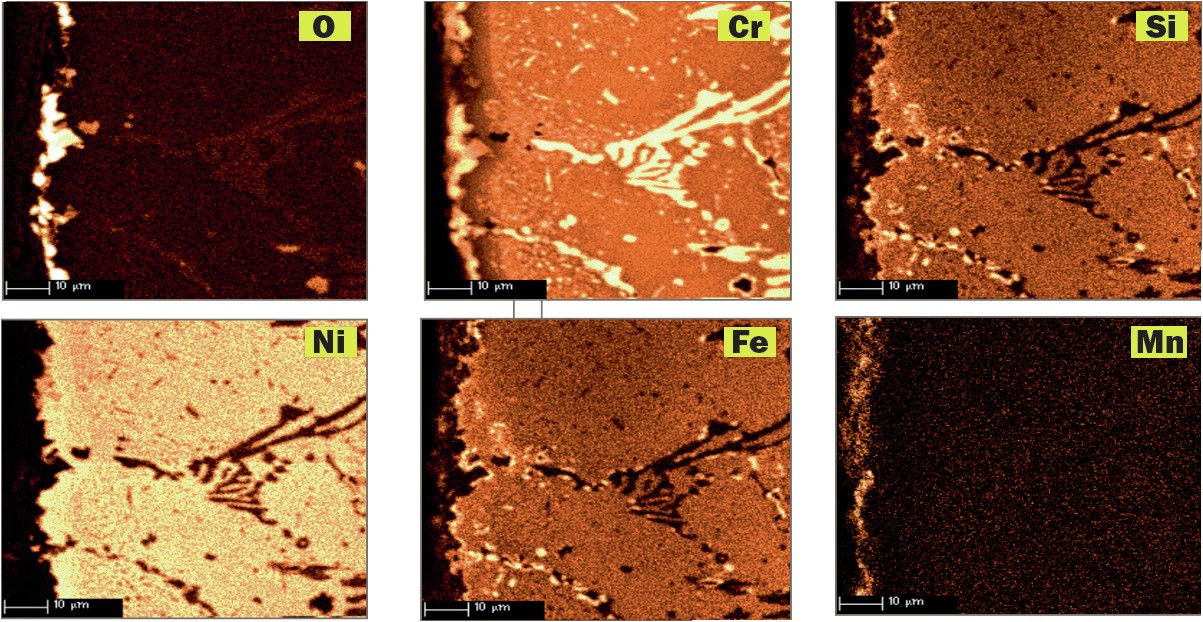
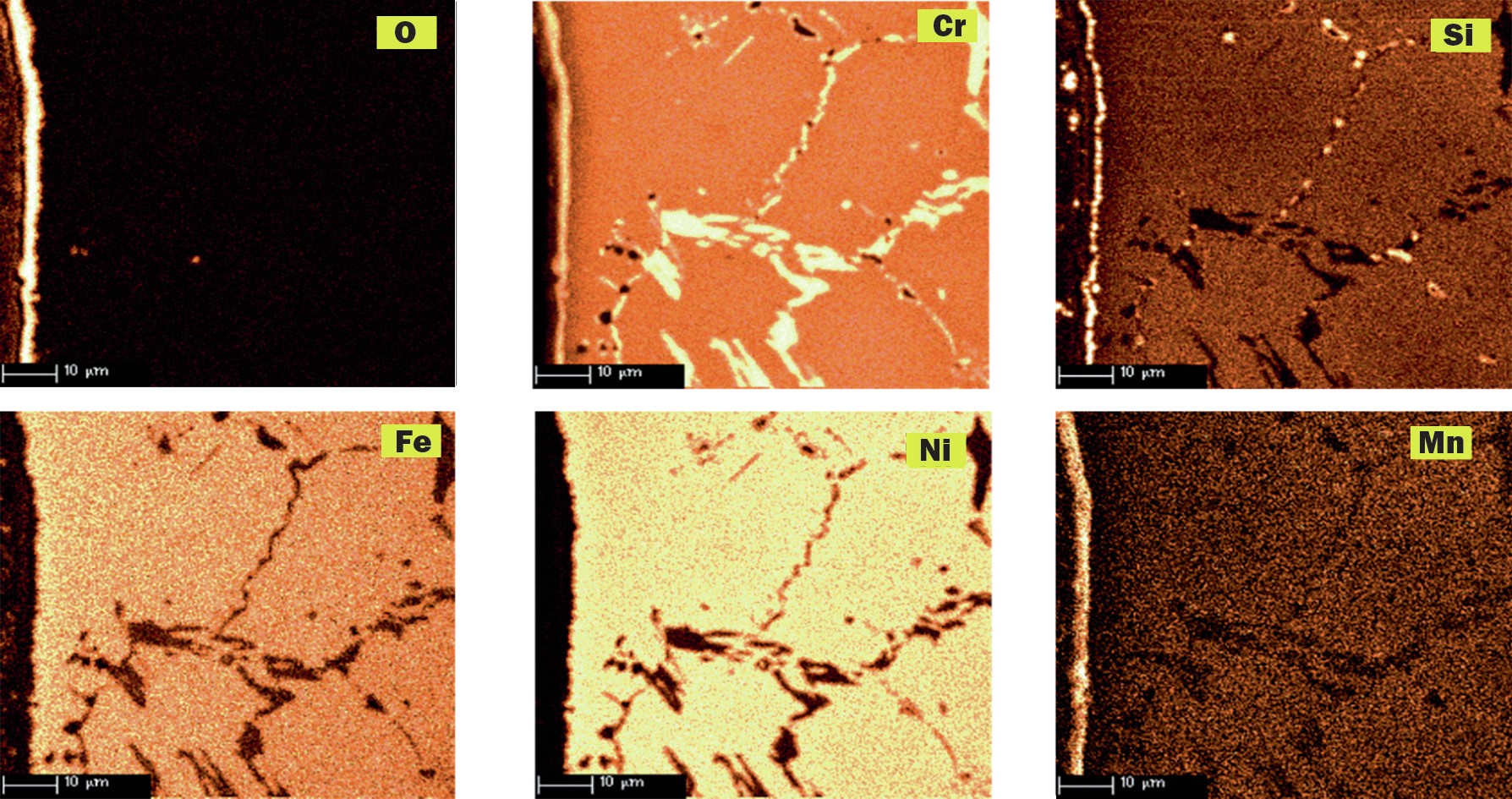
Schmidt+Clemens has worked in a research programme at TNO Science and Technology Research Centre (Netherland), studying the incidence of metal dusting corrosion on typical alloy materials used for high temperature applications. As an example, a comparative corrosion test between alloys Centralloy® ET 45 Micro and G4852 Micro is presented. Samples of both alloys were exposed to a typical metal dusting gas at 600°C and 9 bar, with the following gas composition: 10% CO, 2% H2 O, 4% CO2 and 76% H2 (ac = 226).
Centralloy® G4852 Micro samples were pre-oxidised in order to form a protective oxide layer and indications of metal dusting corrosion damage were detected after 24 hours of exposure. After 1,500 hours of exposure, severe pitting was detected (pit depth up to 300 µm) as illustrated in Fig. 7, with relevant mass loss after this exposure.
Pre-oxidised Centralloy® ET 45 Micro (see Fig. 8) exposed to this highly corrosive atmosphere for 1,500 hours of exposure, showed carburisation related with carbon ingress into alloy material, but no pitting or mass change was measured. Consequently, higher Ni and Cr alloyed material offer a superior metal dusting corrosion resistance that less alloyed elements.
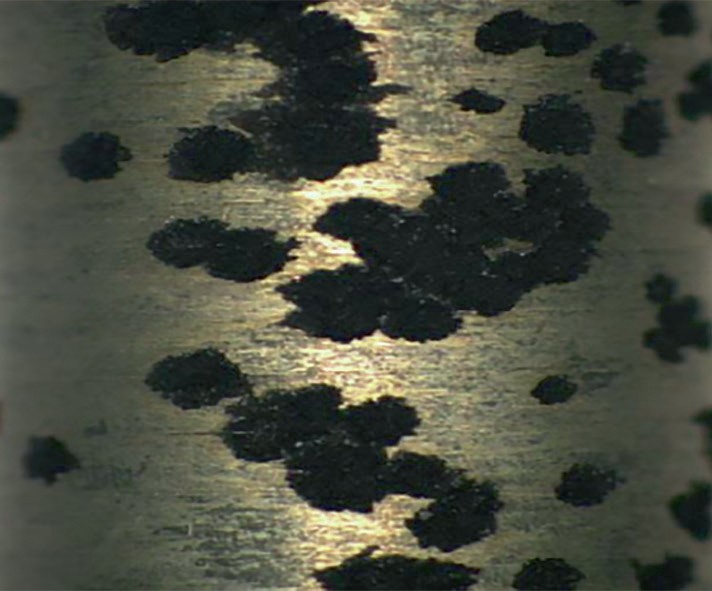
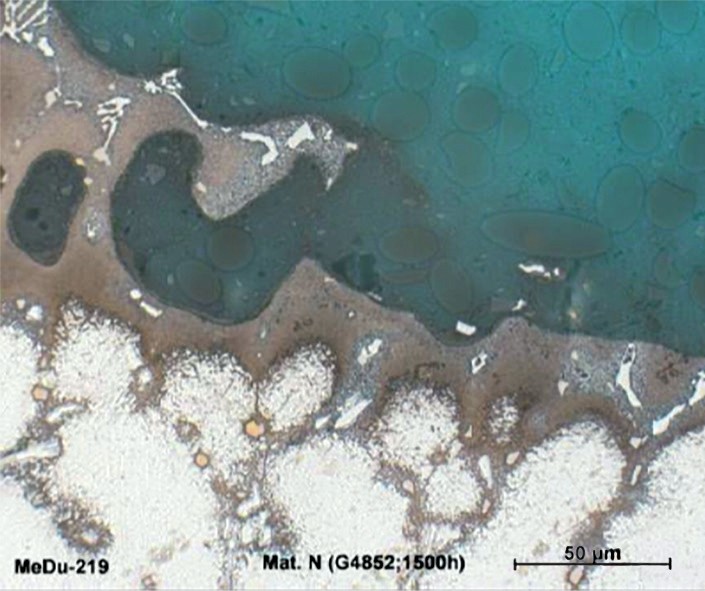
Conclusions
Transition areas from “hot” to “cold” metal surfaces are susceptible to exhibit metal dusting corrosion damage. Methane steam reformer component designs tend to minimise incidence of metal dusting corrosion by avoiding metal exposure to temperature ranges where high rates of metal dusting corrosion damage occur. Use of refractory insulation components, keep metal temperatures below critical metal dusting zones. However, poor maintenance or deterioration of insulation components could lead to part failure due to corrosion damage. Subsequently, metal dusting related failures in steam reformer components still take place nowadays.
Frequent inspection and maintenance of critical areas where metal dusting damage might take place, could minimise appearance of such corrosion damage. Non-destructive techniques, can help the inspection of critical areas where access to the metal surface is complicated or restricted.
In specific cases, where metal dusting damage incidence cannot be avoided easily, replacement of standard steam reformer materials like 25Cr35NiNbTi (HP-Nb) with more resistant 35Cr45NiNbTi (Centralloy® ET 45 Micro) materials, helps to minimise metal dusting damage extent. Metal dusting corrosion damage in high alloy steels takes place due to the presence of defects or damages on protective oxide layers allowing transfer and dissolution of carbon into the metal phase. High chromium contents, help to maintain strongly protective chromium oxide layers. Additions of selected elements in our alloy Centralloy® ET 45 Micro enhance oxide layer adhesion, thus increasing metal dusting resistance
High Ni contents play a significant role in metal dusting, as Ni helps to reduce inward diffusion of carbon into alloy material. Alloy Centralloy® ET 45 Micro has a 45 wt-% nominal content of nickel. Consequently, protective alloy effect against metal dusting damage is strongly favoured, as well as high temperature resistance. Centralloy® ET 45 Micro has been selected in several steam reformer designs, where higher metal dusting resistance was demanded.
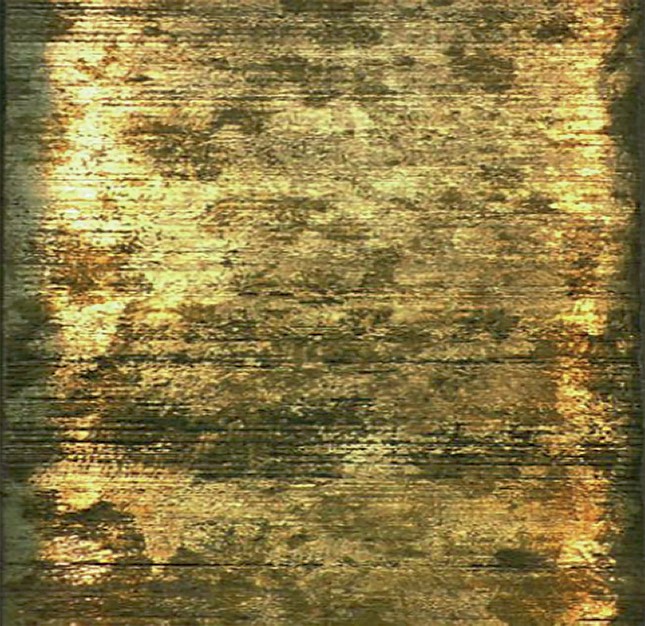
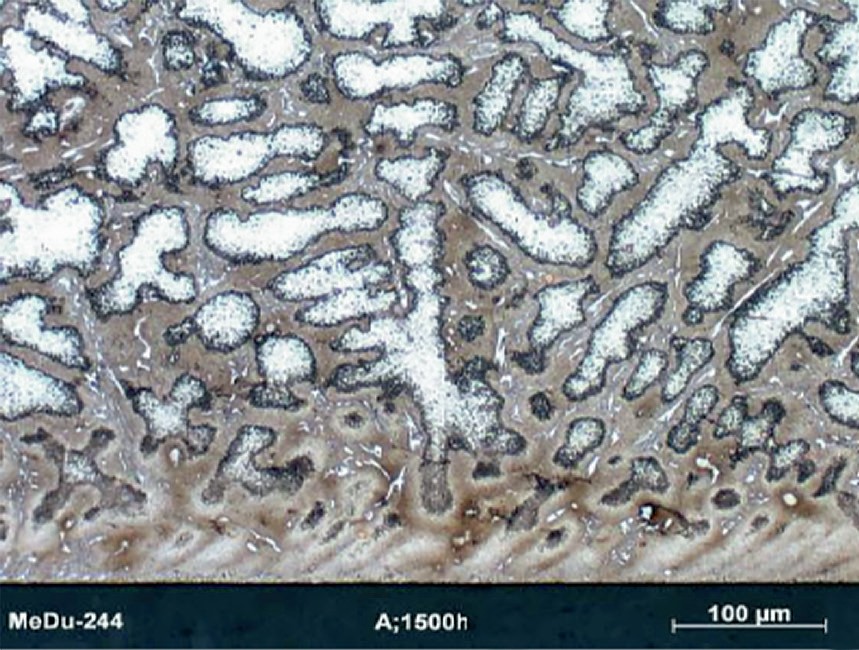
Risk of metal dusting occurrence on steam reformer components can be minimised by identifying those transition areas where metal dusting incubation is favoured. Inspection/maintenance of these critical areas, including refractory insulation components, help to prevent unexpected metal dusting related failures. Specific cases where metal dusting damage cannot be easily avoided, might require upgrading existing alloy to more protective ones like our alloy Centralloy® ET 45 Micro.
References