Sulphur 395 Jul-Aug 2021
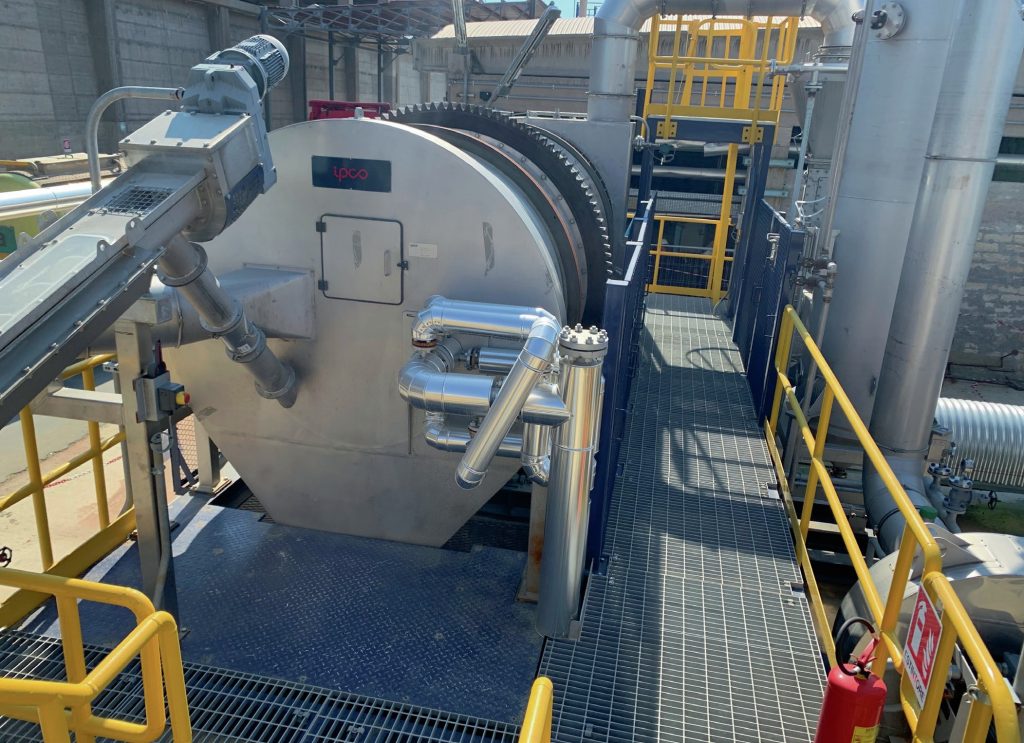
31 July 2021
New showcase drum granulator commissioned
SULPHUR FORMING
New showcase drum granulator commissioned
Sulphur processing and handling equipment manufacturer IPCO has completed the commissioning of a groundbreaking new drum granulator in Italy that will serve as a global showcase for this patented system. C. Metheral of IPCO, describes the innovative approach and key features of the SG20 sulphur granulation system.
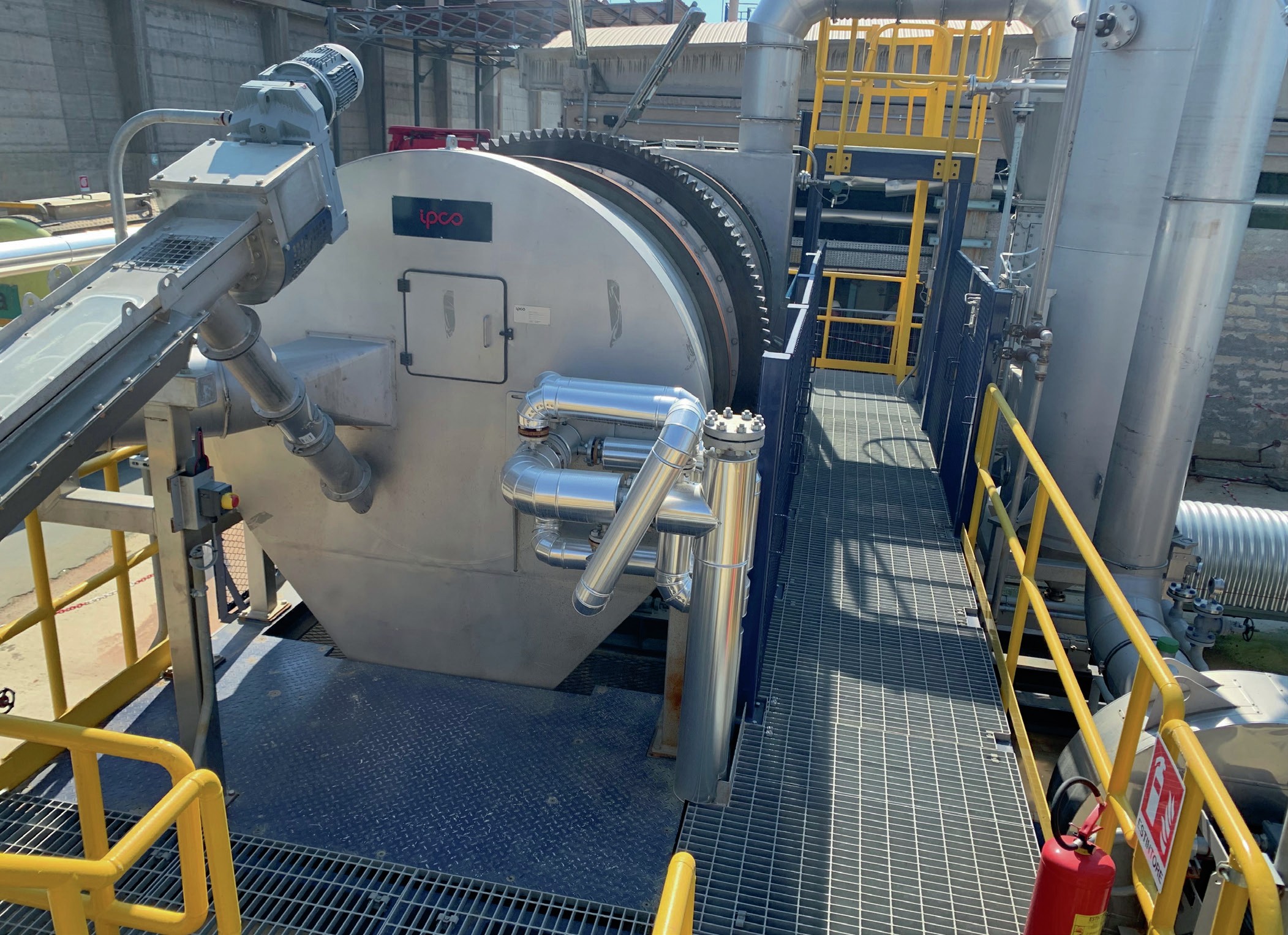
The IPCO SG20 is a fully automated sulphur granulation system based on rotating drum technology. Its high productivity ‘once through’ operation delivers a solidification capacity of up to 800 t/d. The unit has been delivered to a long-standing customer in Italy, a company operating multiple sulphur solidification lines, and an agreement is in place that will enable prospective customers to visit the site and assess the system in operation.
The SG20, a scaled-down version of the company’s 2,000 t/d SG30 model, is designed for medium-range capacities. The newest model is notable for its remarkably quiet operation, well below standard noise limits, and for easy access to all components for monitoring and maintenance.
The system delivers a high quality product satisfying the shape criteria and Stress Level I and II friability parameters of the SUDIC product specification. This ensures efficient, clean and environmentally safe storage and handling during transportation. The SUDIC specification also limits moisture content; excess moisture not only adds weight, leading to unnecessary transportation and melting costs, but also results in increased acidity, risking corrosion in storage, handling and transportation equipment.
The same operating principles apply to both models. This is a single-pass process, which eliminates any need for screens or recycle conveyors to send sulphur back through the drum. The sulphur seed or nuclei particles are created outside the drum by freezing sprays of liquid sulphur in a water bath. Generating the particles externally simplifies the process and allows wider flexibility with the incoming liquid sulphur temperature. It also provides an innovative way to recycle the sulphur waste stream from the wet scrubbing system, which is explained later.
Fig. 1 shows a basic process flow diagram of the drum granulation process.
Innovative approach to drum granulation
The IPCO patented SG system has been designed to resolve the drawbacks often associated with traditional drum granulation technology, in particular cleaning, maintenance and process control. IPCO’s experience in the supply of sulphur solidification and handling equipment extends all the way back to 1951 and this gives the company an unparalleled insight into the problems encountered by operators and maintenance personnel. The design of the SG series involved identifying the root cause of each issue, and then working out how it could be eliminated or, at the very least, its effects minimised.
Substantial reduction in sulphur build-up
Older drum technologies have always required regular shutdowns to clean out the build-up of sulphur within the system. This could be as frequent as every 12-24 hours, with an obvious and significant impact on overall system productivity. And even when systems could be run for longer than this, the cleanout process would be much more challenging, leading to longer shutdown periods.
Having identified the points within the system where sulphur build-ups occur (Fig. 2), and studying each one, IPCO has designed the system to minimise this issue. The specifics remain confidential but the result is a dramatic reduction in cleaning requirements: the SG20 can run continuously for a full week before requiring a shutdown. Even then, the cleaning requirement is minimal compared with traditional drum granulation systems.
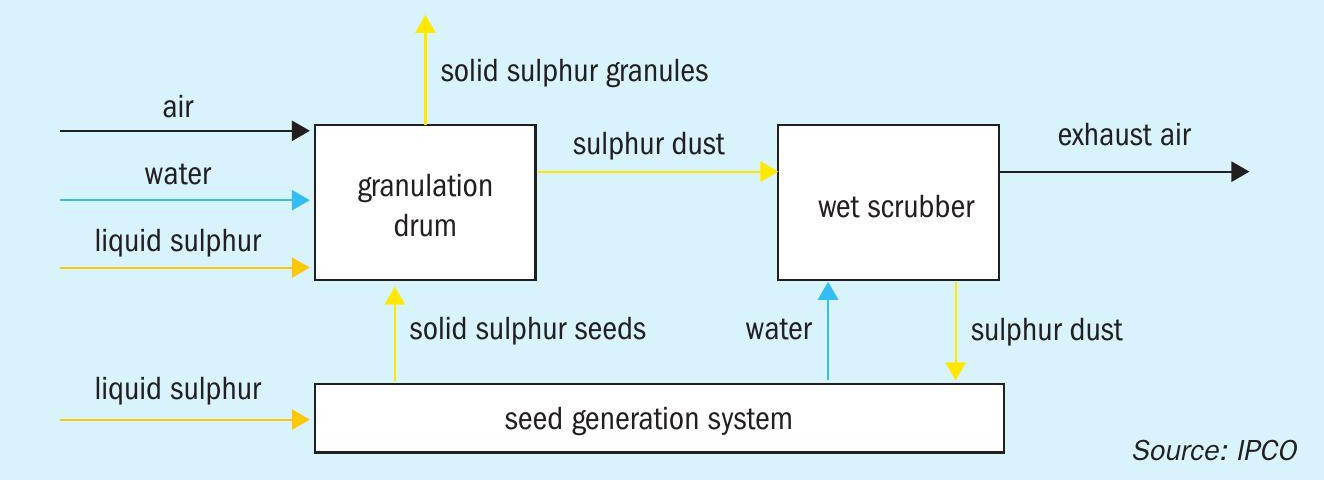
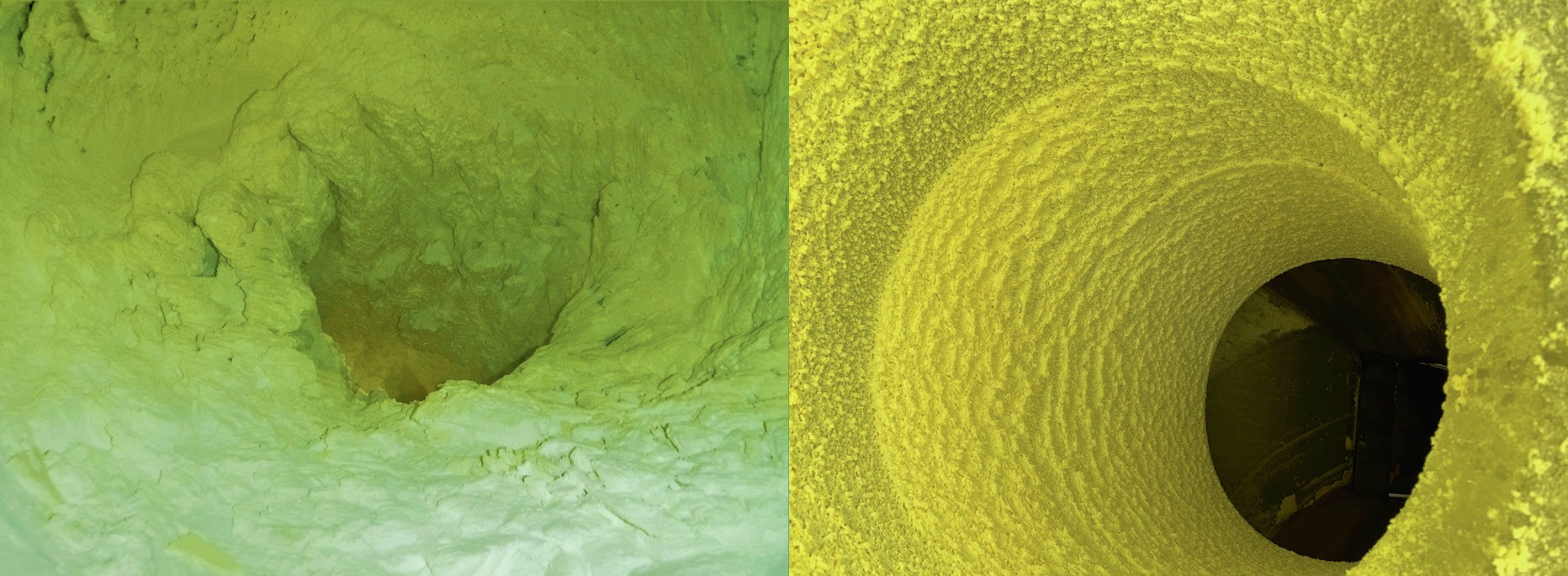
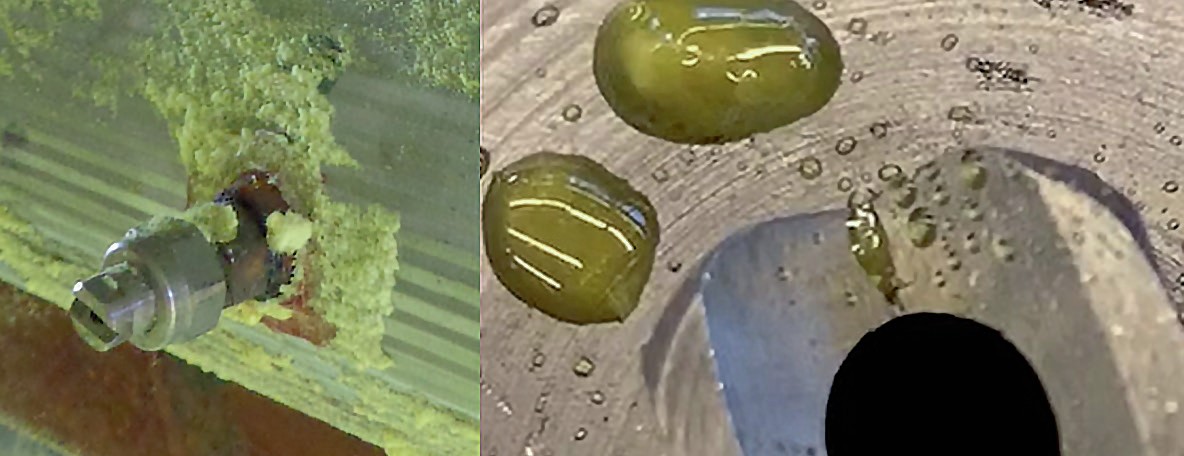
Heated sulphur nozzles
Liquid sulphur has to be maintained at a specific temperature range (around 120 to 160°C), so any cold spot in a processing system has the potential to cause problems. In the case of traditional drum granulators, the problem area in this respect has often been the sulphur spray nozzles, due to the fact that they extend outside the steam-jacketing (Fig. 3).
If liquid sulphur remains in the nozzle when the system is shut down it will freeze in the tip, blocking flow at the next start-up. Even if the nozzle is clear, sulphur vapour from inside the header can condense and freeze in the tips if the system is shut down for an extended period. In either case, rectifying the problem will require an operator to manually clean out the nozzle or replace it before starting up the system. A single frozen or plugged nozzle can make the difference between premium granules and off-spec product.
IPCO has overcome this issue by incorporating the industry’s first heated sulphur spray nozzle. Again, the technical specifications are protected by IPCO, but the outcome is that the nozzles in the SG series will not freeze up, and the time-consuming task of sending an operator into the drum to resolve the problem has been completely eliminated.
Redesigning the drum to minimise roller wear
The drum granulation process is based on the use of a rotating drum to form curtains of falling granules. As the nuclei particles travel along the drum, they are progressively enlarged to the required size by means of sulphur sprayed from a bank of nozzles running the length of the drum.
In older systems, the drum would be positioned at an angle so that gravity would advance the granules towards the outlet end of the system. However, granulation drums are large and heavy pieces of equipment and the need to rotate on an angle inevitably creates high levels of stress on the rollers that support the drums, resulting in alignment issues requiring ongoing maintenance.
IPCO’s SG series granulators (Fig. 4) take a different approach. Instead of turning on an angle, they operate on a completely level base, using angled internal flights to advance the product instead of gravity. This means no unnecessary wear and tear on the rollers, and no maintenance to keep the unit aligned.
Dust emissions and scrubber waste
Drum granulators work by removing heat from the product to convert it from a liquid state into a more easily handleable solid. In the case of sulphur solidification, this heat exchange is carried out using air and water: air is pulled into the drum, water is evaporated into the air as the sulphur cools, and the air is then discharged to the atmosphere. However, as the exhaust air contains sulphur dust, it has to be treated in order to prevent atmospheric pollution.
Managing this has traditionally meant choosing between two options, the steam-jacketed cyclone and the wet scrubber with dust collection system, and there are drawbacks to both.
The steam-jacketed cyclone melts the sulphur dust that has been captured to create sulphur vapour. The result is high levels of dust emissions, a major problem for systems operating in environmentally sensitive areas. The process also requires high volumes of steam in order to heat up the air stream while melting the sulphur dust.
The second technology, the wet scrubber with dust collection system, captures the fine sulphur particles with water to form a sludge, which in turn needs processing. The usual approach is to melt and filter the waste, then feed it back into the liquid sulphur supply system. Although a more complicated process than the steam-jacketed cyclone, it results in lower dust emissions.
IPCO has taken a new approach. As a wet scrubbing system has the lowest sulphur dust emissions (and therefore lowest impact on the environment), this was chosen as the basis of the solution. However, instead of requiring a second stage of processing, the waste stream is recycled directly into the external seed generation system (Fig. 5).
Injecting the sulphur dust captured by wet scrubbing back into the process, it is consumed as seed in the drum (Fig. 1). This is a simple and energy efficient solution, one that requires no extra work in terms of operating and maintaining the sulphur melting/filtering equipment.
Managing H2S emissions
As is the case with all sulphur produced as part of the oil refining process, the sulphur processed at this facility in Italy contains levels of hydrogen sulphide (H2 S). The drum granulation process involves spraying liquid sulphur through nozzles, which releases a portion of this H2S into the air stream.
Levels of H2S vary depending on the liquid sulphur supply and acceptable stack emission levels will differ around the world too. European regulations place strict limits on H2S so measur es have to be taken to prevent it from entering the atmosphere.
The solution here is the addition of an H2S scrubbing system, an option that can be incorporated to ensure compliance with the most stringent of emission requirements, anywhere in the world (Fig. 6).
Consistent operation
While technology is key to successful sulphur forming, there are many other factors at play, all of which can impact on the quality of the end product.
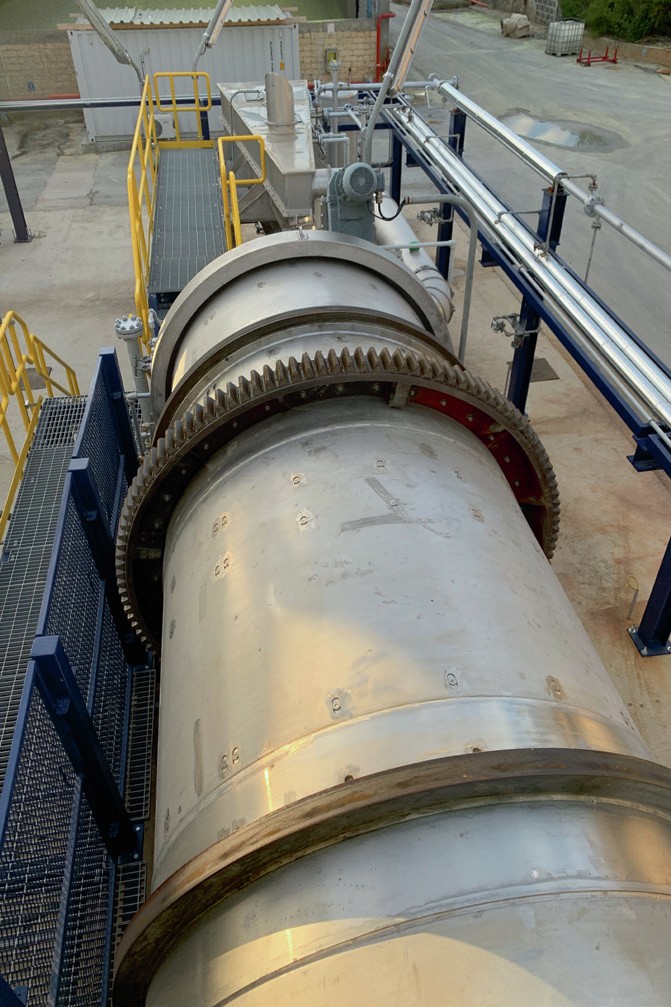
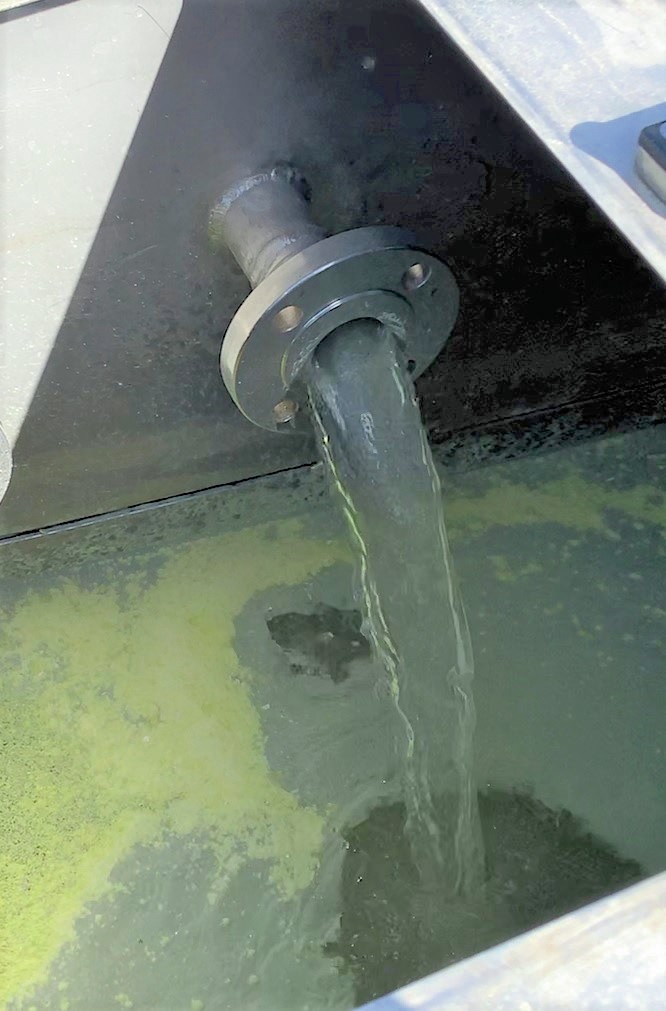
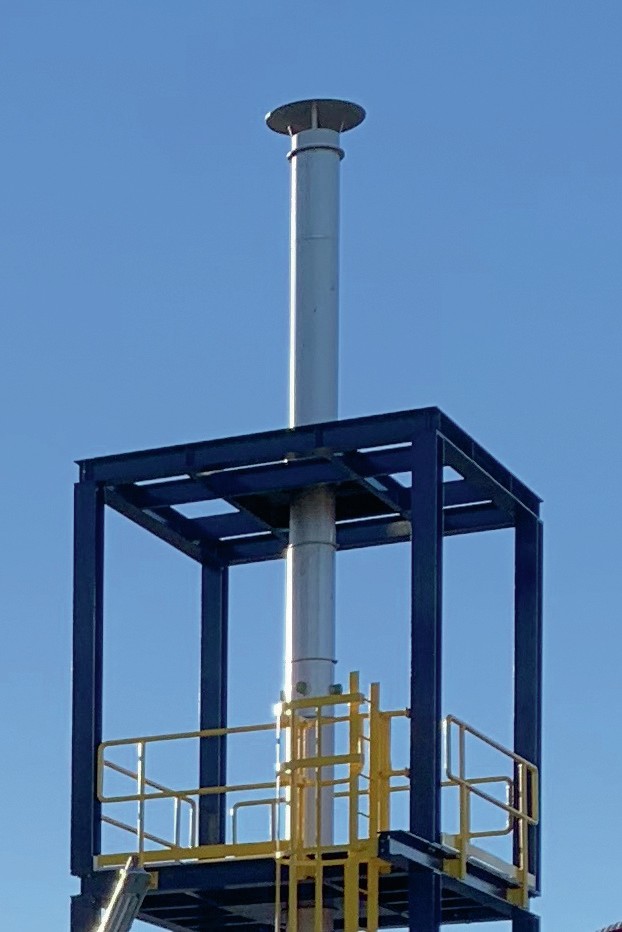
Throughput rates, liquid sulphur feed temperature, geographic region, ambient temperature, humidity levels, seasonal conditions, the weather; all need to be taken into account as part of the solidification process and this can place a high degree of responsibility on the operator. It is possible to set up a drum granulator to operate to fixed parameters but this is likely to result in sub-optimal performance if and when conditions change.
The ability to adjust operating parameters relies on the operator having sufficient experience to understand how the system will react under varying conditions. Get it right and the result will be consistently high-quality sulphur granules; get it wrong and product quality will suffer, water will be wasted, and build-ups will occur, resulting in shutdowns.
While operator training and follow-up support visits can help build the necessary skills over a period of time, there is a risk of a system operating at less than 100 percent efficiency – and producing less than premium quality product – until the required level of in-house expertise has been developed.
IPCO has overcome this by developing a process simulation solution that takes all guesswork out of realising the full potential of its patented drum granulation system.
The SG series operator guidance system – an industry-first in the field of sulphur drum granulation – was developed by analysing a wealth of operating data collected from both the SG20 and SG30 systems, and building a process simulation that can be applied to any operating conditions.
Summary
In designing the SG series, IPCO has taken all the inherent advantages of drum granulation – highest capacity, highest quality end product – and enhanced the technology in ways that overcome the challenges previously associated with this approach to sulphur forming (Table 1).
Cleaning and maintenance requirements have been significantly reduced, resulting in increased equipment availability. Emissions of both sulphur dust and H2 S are well within the limits of prevailing environmental legislation. Noise levels are far below standard limits. A new approach to drum design minimises stress of rollers to increase equipment life, and, perhaps most important of all, operation has been simplified: the unit can be stopped and started at the touch of a button, and a game-changing operator guidance system means that a high-quality product can be produced at all times, regardless of operator experience.
IPCO is a world leader in sulphur processing and handling, having delivered complete end-to-end systems to hundreds of companies around the globe since 1951. In addition to granulation drums, IPCO’s well-known Rotoform system meets small to medium capacity requirements for sulphur, offering excellent product uniformity, environmentally friendly operation and premium quality pastilles of uniform shape and size. More than 700 Rotoform pastillation systems have been installed for sulphur processing to date.
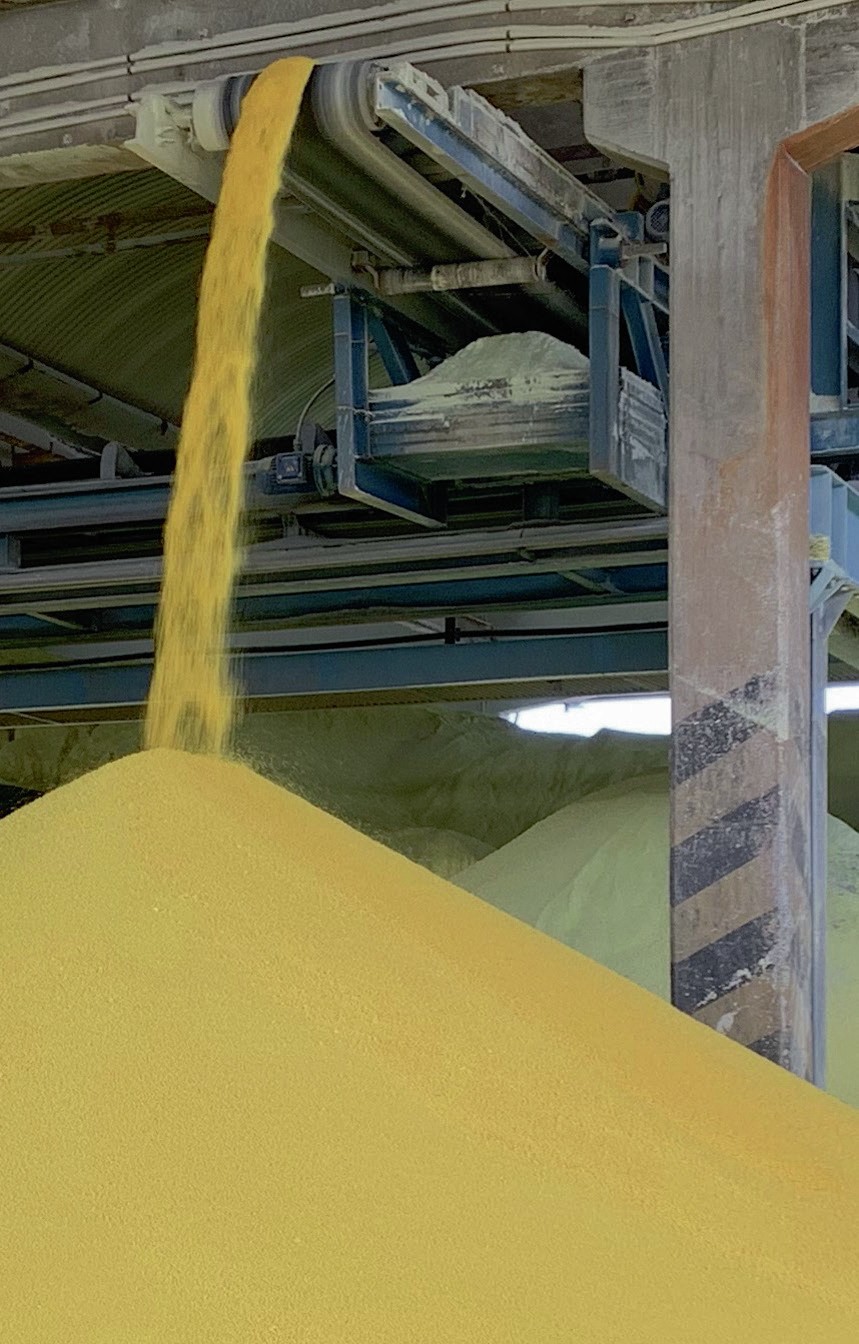
Together, the drum and pastillation options make up IPCO’s premium forming product range, giving customers access to all technology options under a single brand.
The IPCO SG20 drum granulation system installed in Italy is available for customer visits on request. Interested parties are invited to contact their local IPCO office to organise a visit.
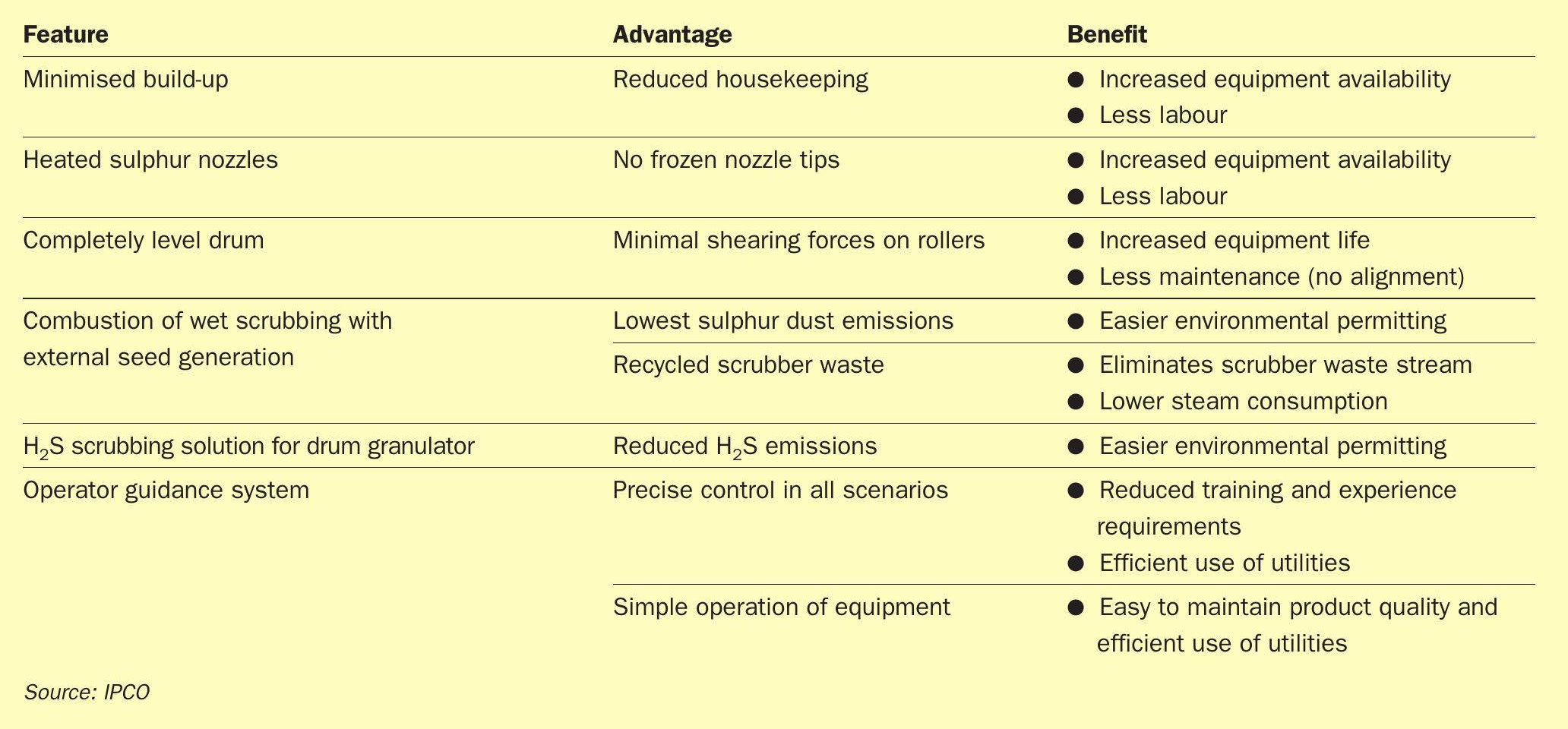