Nitrogen+Syngas 372 Jul-Aug 2021
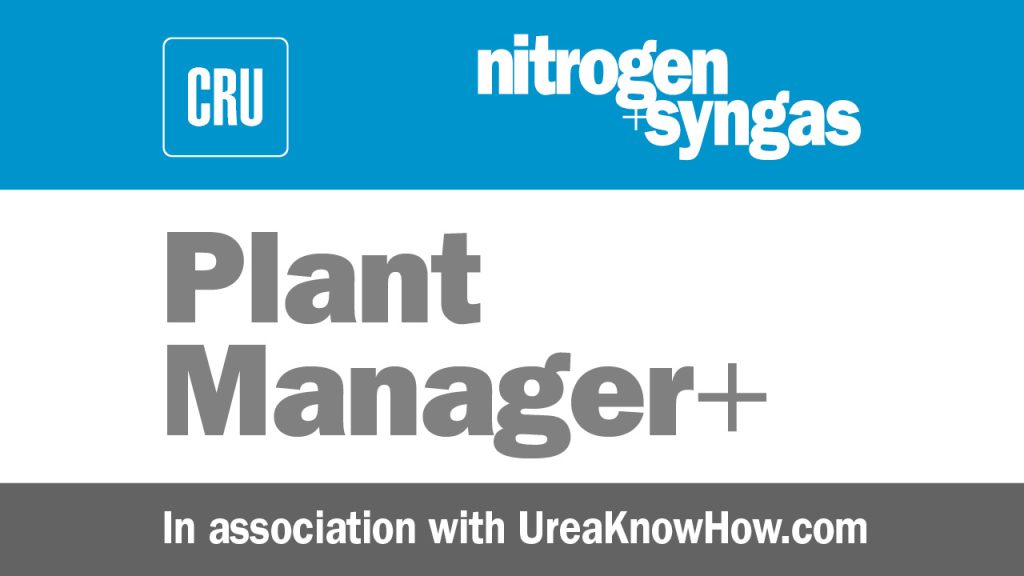
31 July 2021
Problem No. 61: Carbamate safety valve problems
Traditional safety valves suffer from crevice corrosion problems causing small leakages which often go undetected. These small leakages can lead to the risk of crystallisation of ammonium carbamate in the outlet line of the safety valve even when heat tracing is applied (see picture).
Furthermore, due to the increased effective seat area the safety valve can open before reaching the set pressure. This round table discussion considers options to improve the reliability of carbamate safety valves in urea plants.
Muhamad Reda of Pupuk Kujang in Indonesia kicks off the round table discussion: Does anyone have records of trouble with high pressure safety valves in the high-pressure carbamate condenser? Is it possible to add a block valve or isolation valve upstream of the high-pressure safety valve (171 kg/cm 2 g) in a urea plant? Does anyone have any brand recommendations for safety valves/angle valves or any valve for the high-pressure system in a urea plant?
Mark Brouwer of UreaKnowHow.com, The Netherlands replies: The safety valve company LESER in Germany has solved the reliability issues with high pressure carbamate safety valves.
Muhamad replies: Thank you Mark, our licensor also recommends LESER. But they don’t recommend a block valve upstream of the safety valve, especially for high pressure ones. Has anyone installed a block valve upstream of a safety valve?
Mark continues: Indeed, it is not normal practice to have a block valve upstream of the safety valve. Please note:: 1. One should assure the block valve is open. 2. Normally a block valve is used to enable maintenance of the safety valve in case one has a spare in service. However, due to corrosion phenomena and the relatively large valve size, it is risky to rely on one block valve. A block and bleed system would be preferable, but this kind of system is not easy to make reliable due to the corrosion and crystallisation issues.
Khaled Seliem of Abu Qir Fertilizers in Egypt asks another related question: Is it possible to install a rupture disc upstream of the safety valve and is it applied with high-pressure reactor safety valves?
Mark responds: There have been some trials in the past, mainly in the US. Some risks to consider: l Part of the rupture disc may get stuck in the safety valve. l What happens when there is a small crack in the rupture disc? l How do you avoid crystallisation? l How do you ensure that no pressure will build up between the rupture disc and the safety valve?
The most reliable solution in my view is the LESER carbamate safety valve solution.
Emmanuel Ogoh of Notore Fertilizers in Nigeria provides valuable information: Installing a rupture disc upstream of the high-pressure reactor is common practice in my plant (Stamicarbon process). The rupture disc (easily replaceable) provides protection from corrosion to the safety valve.
Moreover, there have been reported cases of high-pressure safety valves passing and not seating properly after lifting. The presence of a rupture disc upstream will reduce the chance of these occurrences. However, replacing a ruptured disc requires total draining and purging of the high-pressure loop which may increase downtime. Having a block valve (normally in open position) upstream of the rupture disc will reduce replacement time.
Mark replies: Although it is in a Stamicarbon plant, I do not think the rupture discs have been there right from first start up. Best to doublecheck with Stamicarbon, but as far as I know licensors do not like rupture discs upstream of the carbamate safety valves the same goes for block valves.
Muhamad replies: You are right that there have been reported cases of high pressure safety valves passing and not seating properly after lifting. It happened twice last year in our plant, and now some safety valves are passing. But is it really OK to install a rupture disc and block valve upstream a safety valve?
What if the rupture disc gets ruptured and stuck in the safety valve? We asked our licensor (TOYO) but they don’t recommended a block valve.
Mark replies: LESER in Germany has solved the reliability issues with high pressure carbamate safety valves. They have developed two successful improvements: the LESER flush system, which eliminates passing after blow off and a support loading system, which reduces the blow off amount with some 75% and increases the blow off pressure to a level very close to the set pressure. LESER safety valves have been the standard in all new Stamicarbon plants for more than ten years.
Andreas Caldonazzi of LESER in Germany adds valuable information: There is a strong recommendation in the relevant standards not to use isolation valves upstream of the safety valve.
Some extracts from the relevant standards are shown below: For example, ISO 4126-9: “Isolation of safety devices, 8.4.1 Basic requirement, The equipment shall be protected against excessive pressure at all times during operation. There shall be no isolating valve in a pressure relief system, except for the cases in 8.4.2, 8.4.3 and 8.4.4.”
Also, in API 520-2 there is a relevant specification on this topic: “8 PRD Isolation (Stop) Valves, 8.1 General, Isolation block valves may be used for maintenance purposes to isolate a PRD from the equipment it protects or from its downstream disposal system. Since improper use of an isolation valve may render a PRD inoperative, the design, installation, and administrative controls placed on these isolation block valves should be carefully evaluated to ensure that plant safety is not compromised. A PRD shall not be used as a block valve to provide positive isolation.
8.2 Application: If a PRD has a service history of leakage, plugging, or other severe problems that affect its performance, isolation and sparing of the PRD may be provided. The use of isolation valves and/or sparing permits the PRD to be inspected, maintained, or repaired without shutting down the process unit. However, there are potential hazards associated with the use of isolation valves. The ASME Boiler and Pressure Vessel Code, Section VIII [7], Appendix M, Section M-5.6 discusses proper application of these valves and the administrative controls that shall be in place when isolation block valves are used. Local jurisdictions may have other requirements.”
Conclusion: The LESER view is to minimise all possible risks in the upstream line. The exceptions should not be used for a very critical application like a high-pressure carbamate condenser protection.
Prem Baboo in India joins the discussion with a valuable contribution: ASME code does not allow operating any equipment without a pressure safety valve (PSV) on-line. If you have two PSVs then you can have car seal open isolation valve. Isolating the PSV when the plant is in operation is unsafe and risky.
Isolation valves upstream and downstream of PSVs are usually only required if there are two PSVs in parallel. The interlock also appears in the DCS system of both PSVs. This then allows one PSV to be removed for maintenance / recalibration / certification while the other remains in service.
Of course, it is necessary to interlock the isolation valves in such a manner that the vessel is always connected to a PSV. Be careful that the downstream valve is specified for the correct duty or ensure that both the upstream and downstream valves around the PSV are either both open, or both closed. The off-line PSV should never sit there with its inlet open and outlet closed while the other PSV is in line.
The function of rupture is different, generally used for burst disc, bursting disc, or burst diaphragm, it is a non-reclosing pressure relief safety device that, in most uses, protects a pressure vessel, temperature system equipment or system from over pressurisation or potentially damaging vacuum conditions.