Sulphur 395 Jul-Aug 2021
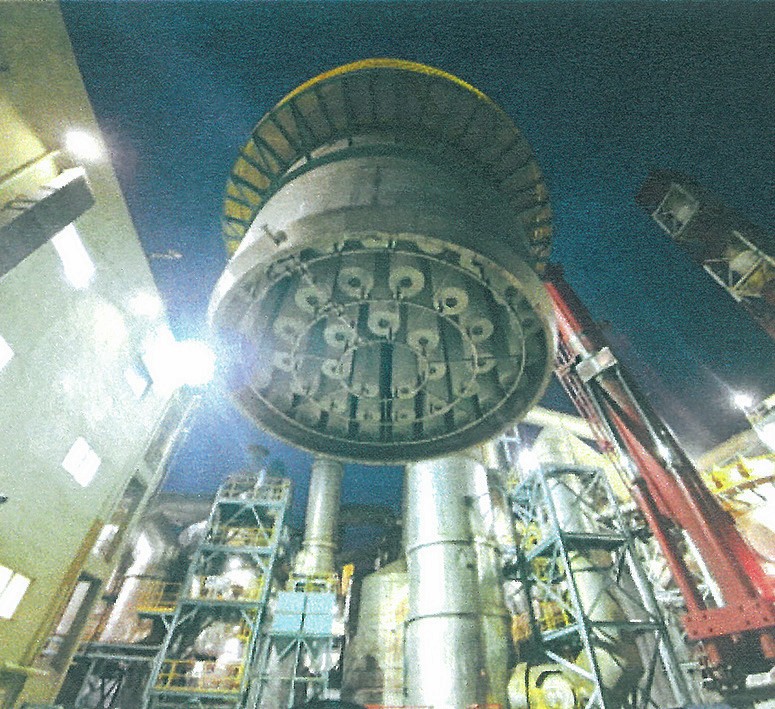
31 July 2021
Reducing NOx emissions in metallurgical oleum tower production
NOX EMISSIONS REDUCTION
Reducing NOx emissions in metallurgical oleum tower production
A. Goudarzi of CECO Industrial Solutions discusses the science behind NOx content and how it impacts sulphuric acid producers. In a recent project in Korea, TWIN-PAK® candle filter technology was successfully used to reduce NOx emissions in metallurgical oleum tower production. After installation of the candle filter mist eliminators the plant was compliant with environmental regulations enabling the producer to operate the plant without penalties or shutdowns.
Everchanging regulations and air pollution control is a major global concern, organisations are looking for smart solutions to reduce emissions to meet stipulated limits by governing bodies. Elevated temperatures required for metallurgical roasters often create higher levels of nitrogen oxides (NOx) which require abatement or exceed emission limits. As the gas flows through the operation from the roaster to the final stack output, mitigating NOx levels has become a major global initiative which has transgressed to the metallurgical sulphuric acid industry. CECO Filters in development with a major Korean metallurgical producer “Company K”, utilised the last line of defence, candle filter mist eliminators, to remove NOx outputs to meet the local requirements.
Using CECO Filters TWIN-PAK® & Graded Bed™ technology the operator was able to further enhance performance to meet regulations.
NOx content and how it impacts sulphuric acid producers
The reaction between nitrogen and oxygen results in nitric oxide (NO) and nitrogen dioxide (NO2 ) formation – otherwise known as NOx or nitrogen oxides.
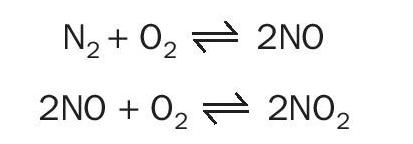
A common day problem for most metallurgical sulphuric acid producers is high levels of NOx formation and output at the stack.
There are three common sources of NOx formation:
- above 815°C NOx formation starts to increase exponentially and reach higher than 800 ppm at temperatures of 1,650°C;
- unbalanced oxygen concentrations and higher combustion residence times;
- wet electrostatic precipitators (WESP) are commonly known to spark NOx formation.
With stricter controls on air pollution regulations and implementation of NOx emission reductions to mitigate the impact on our ecosystem, more producers are experiencing stringent changes in environmental permitting and are required to take action to comply with new local norms. These changes have been geographically noticeable throughout the last decade.
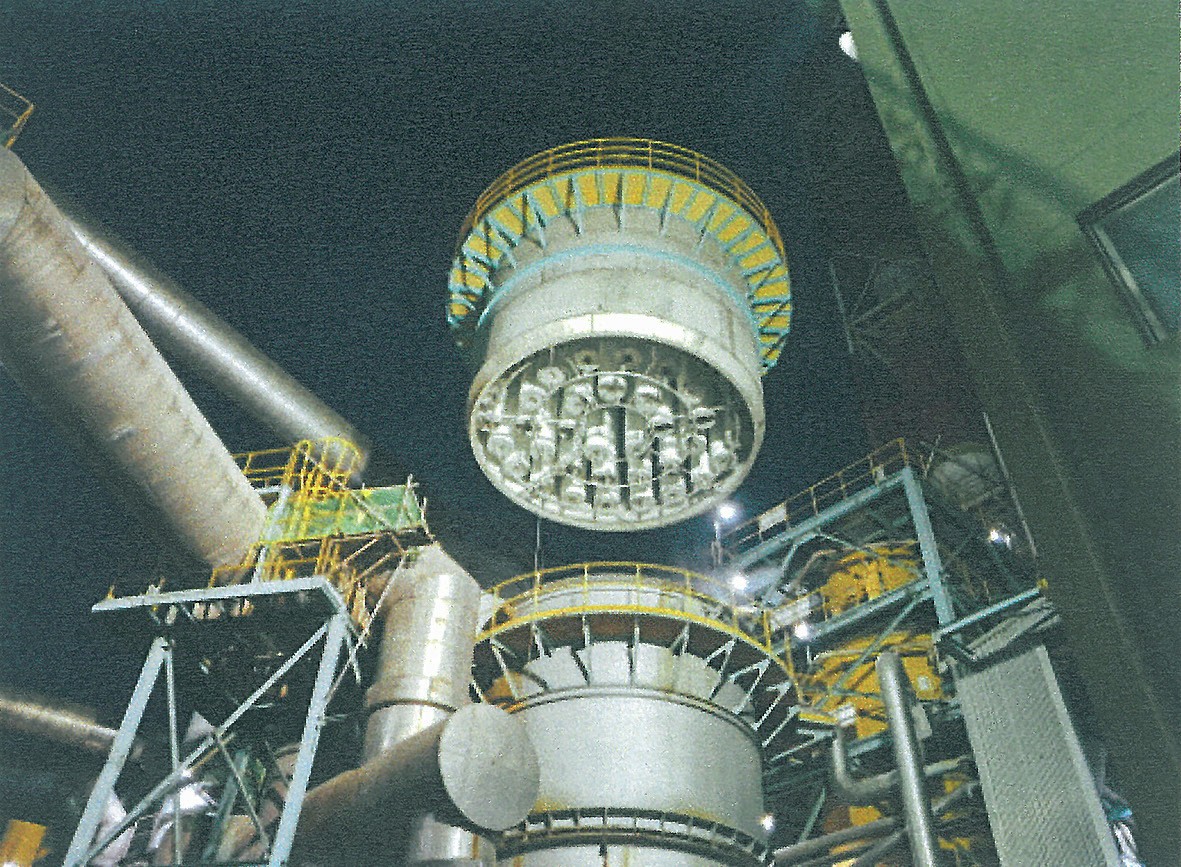
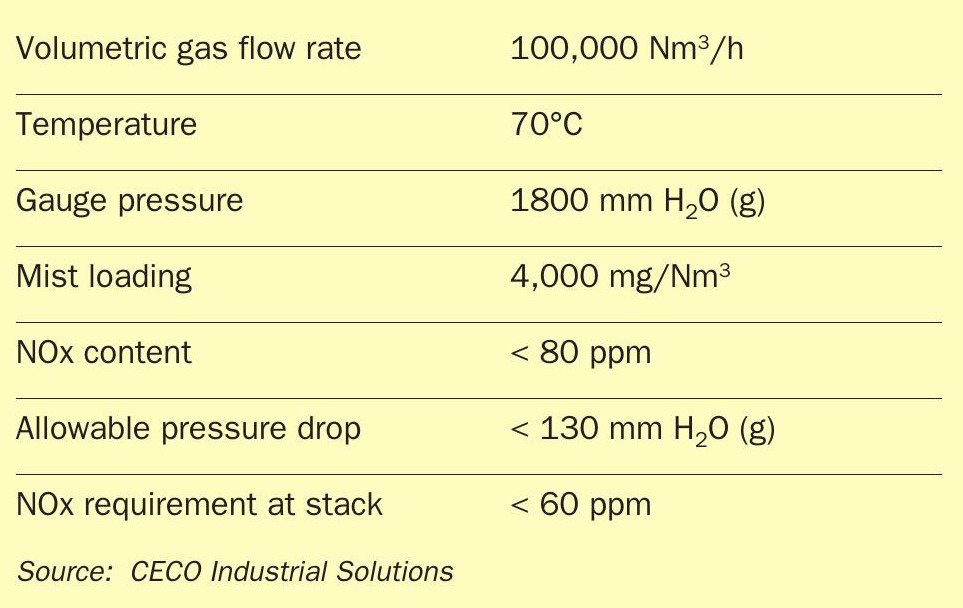
NOx has an affiliation to sulphuric acid and absorbs onto molecules to form nitrosylsulphuric acid. This enables candle filters with highly dense fibres to create a liquid film layer of sulphuric acid to absorb NOx contaminants in the gas streams passing through the candle filter media bed.
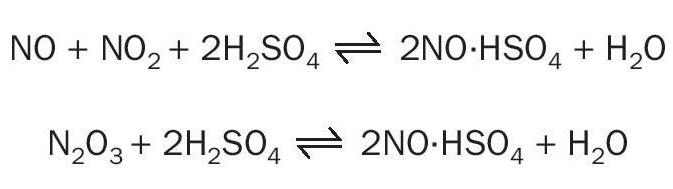
An optimised solution to a common problem
A Korean producer faced local laws swiftly changing on NOx emissions from 120 ppm to 60 ppm. They contacted CECO Filters for mist eliminator solutions to help resolve the problem. CECO proposed adding candle filter mist eliminators to the oleum tower. The current tower didn’t house any filters and required retrofitting the top compartment of the tower to install filter units.
The oleum production presented pressure drop concerns and restrictions through the existing plant set-up and the customer was limited to solutions with a compact design to fit into the existing constraints and increased throughput capacity while meeting the pressure drop limitation for the existing blowers (Fig. 1 & Table 1).
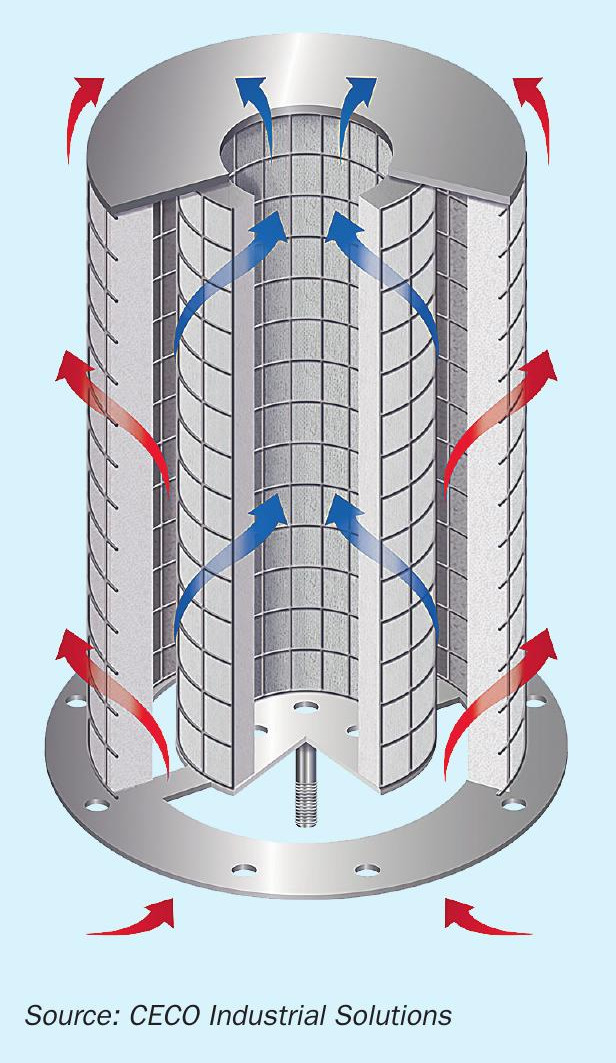
TWIN-PAK® candle filters
TWIN-PAK® was developed specifically to address conventional candle filter restrictions through arrangement reconfiguration by optimising performance through increased filtration area to give additional capacity flow, reduced pressure drop, better filtration efficiency and output performance, ideal for retrofitting solutions, as well as compact design solutions for greenfield projects to reduce capital expenditures without impacting operation expenditures and maintaining an overall economical solution by optimising the total cost of ownership for operators.
In this project, the TWIN-PAK® filter arrangement offered greater reductions in pressure drop compared to conventional filters, decreasing the pressure drop by 50% (180 mm H2 O (g) to 90 mm H2 O (g)), as well as creating more surface area to enable better NOx absorption (Fig. 2).
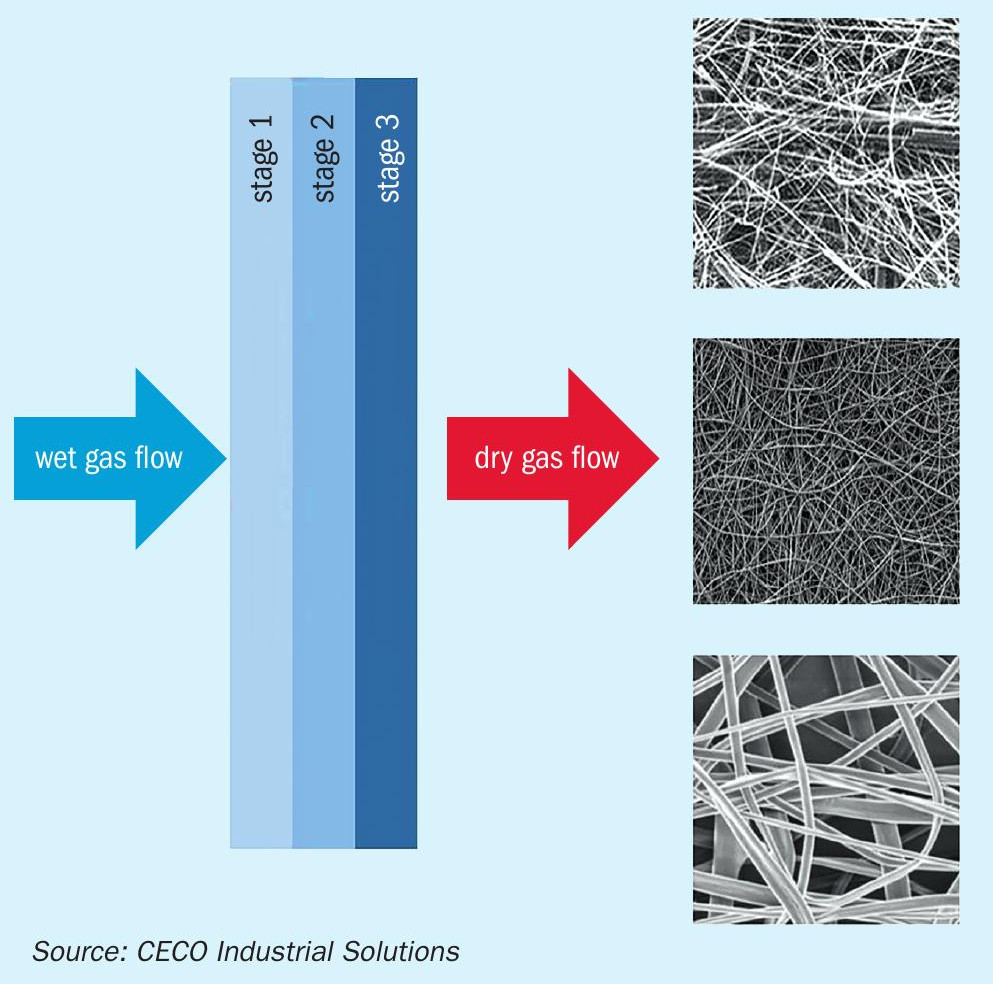
Graded Bed™ candle filter media technology
Candle filter technology operates under wetted or partially flooded mechanisms to effectively remove sub-micron oleum mist using closely packed fibrous media in multiple density arrangements to enhance performance. CECO’s Graded Bed™ technology was cleverly designed to balance the level of flooding contained within the media and create a fine oleum film layer for contact.
The affiliation of absorption between sulphuric acid or oleum and NOx gases is utilised to reduce NOx concentrations in the gas stream to effective levels and in compliance to local norms (Fig. 3).
Pilot testing and results
During the validation and prior to testing of media, CECO worked with the customer to offer multiple design case studies based on CECO’s graded bed filtration arrangements. As the project evolved, it became apparent that the client’s need was primarily focused on available pressure drop and the constraints which they faced for the retrofit solution. The client opted for the lowest case pressure drop design with a value of less than 100 mm H2O.
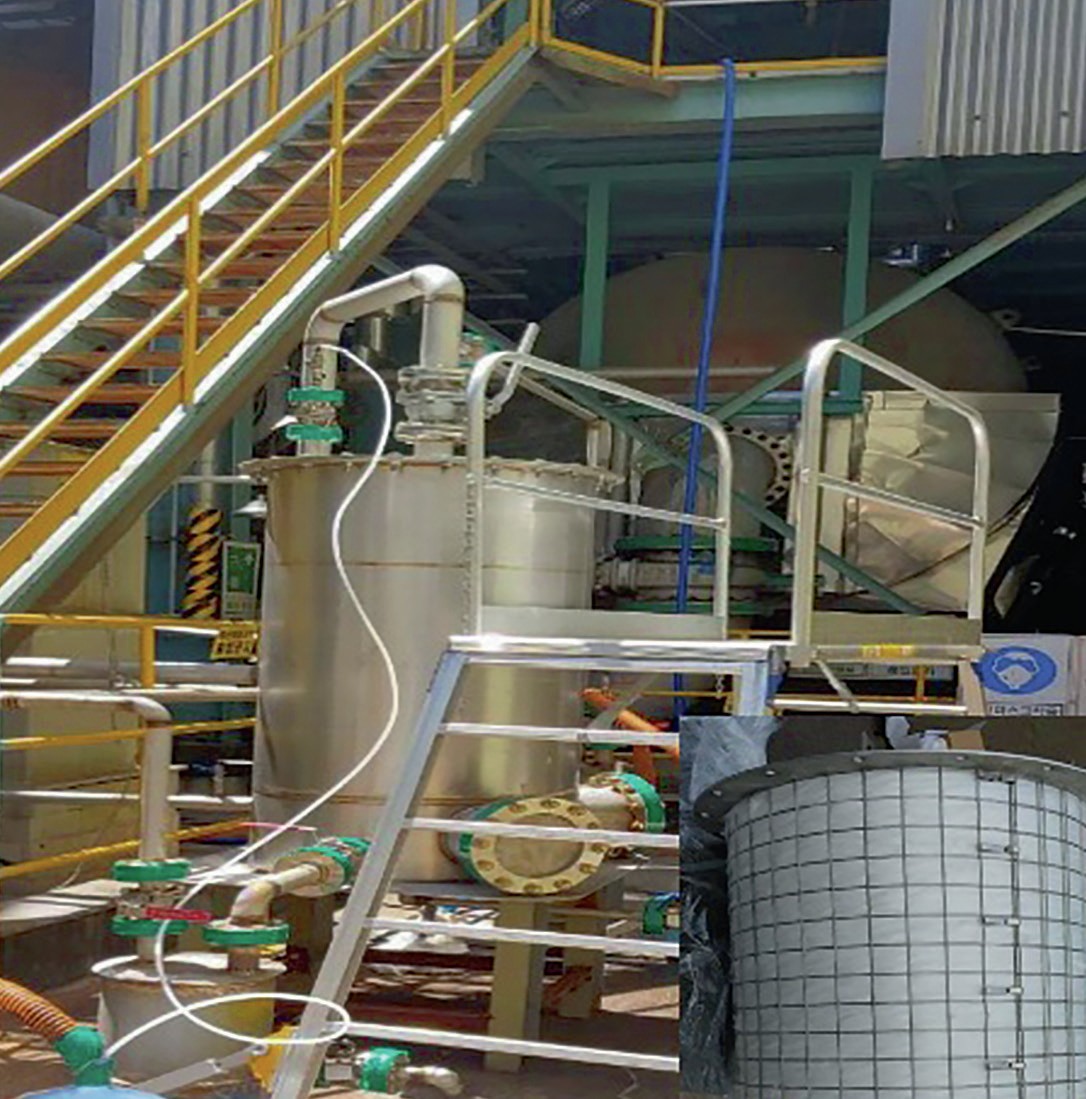
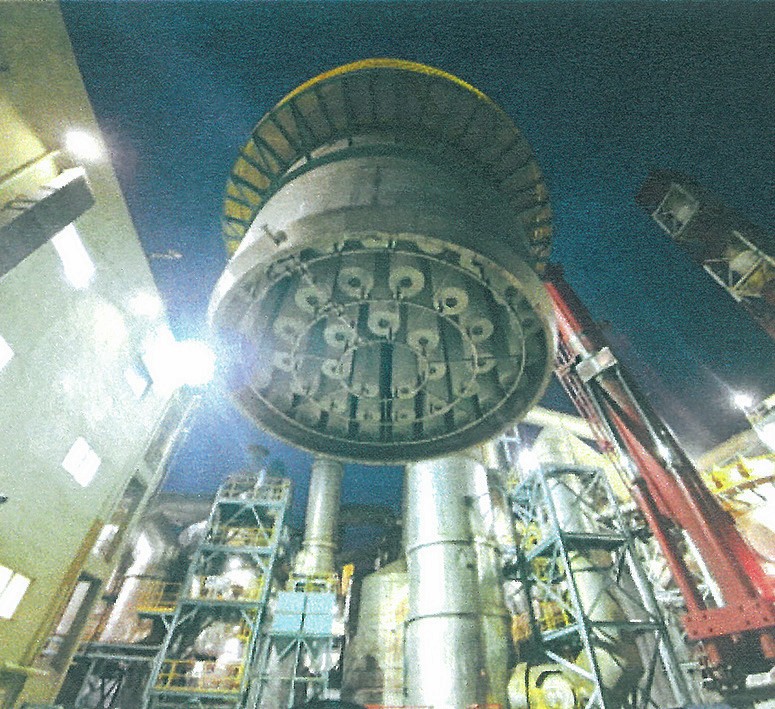
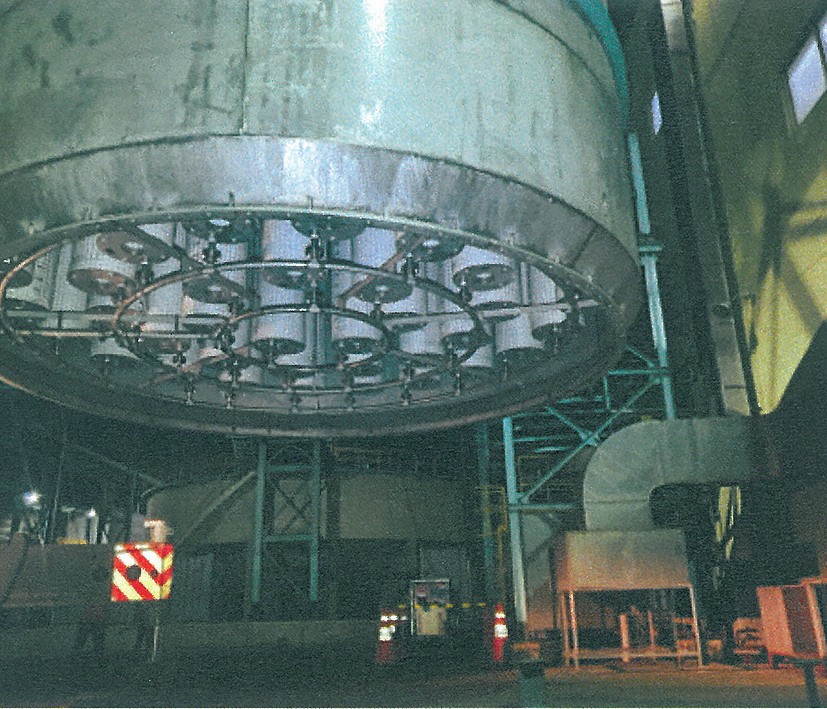
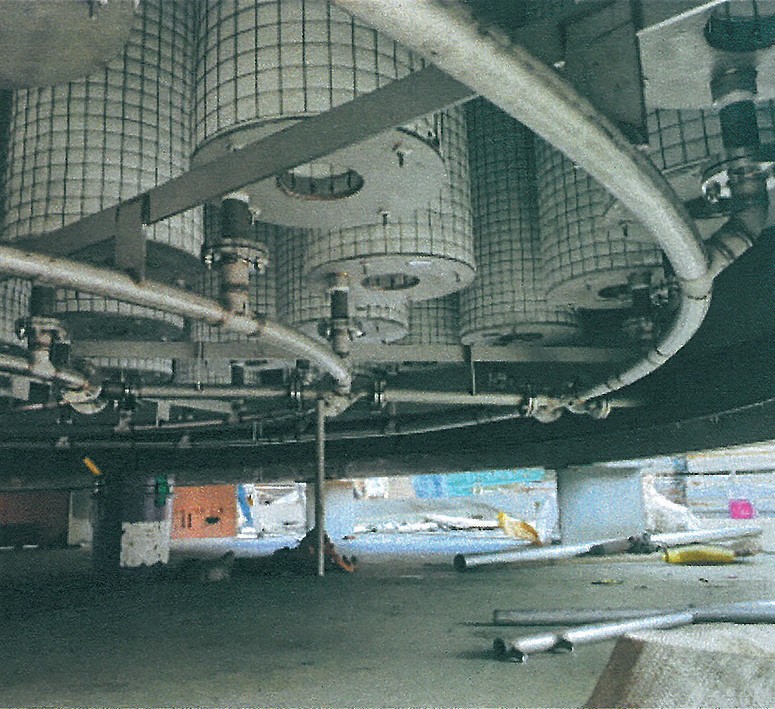
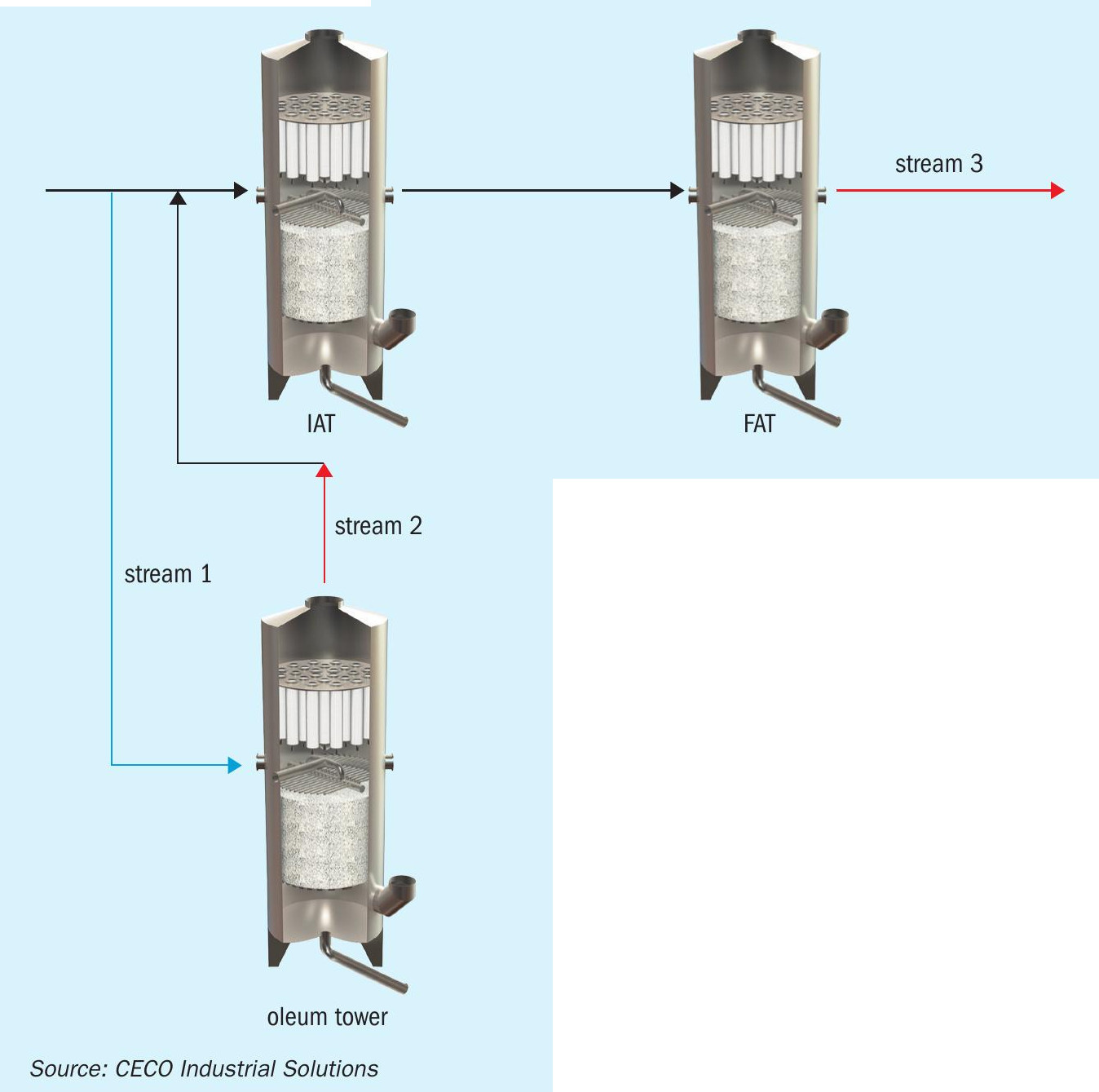


“A smart solution that reduces the total NOx output of the plant in accordance with environmental regulations and enabling the producer to operate the plant without penalties or shutdowns”
CECO supported and provided pilot testing filters to ensure that the filter was able to achieve the reductions of NOx and meet the pressure drop requirement. This was done to validate the theoretical data and convert theory into empirical data using pilot testing and validation of performance. The results from the pilot testing were positive and provided confirmation of the pressure drop at given flow rates and also, significantly reduced NOx removal rate. CECO collected multiple data points and developed further empirical knowledge of absorption rates of NOx and sulphuric acid at multiple operating conditions (Figs. 4 & 5).
After installation and adding additional filtration area, the commissioning results from CECO Filter’s TWIN-PAK® technology confirmed the units were able to remove NOx levels more effectively to 32 ppm or less from 80 ppm (at commissioning stage), while reducing the pressure drop from 130 mm H2 O (conventional filters) to 90 mm H2 O with TWIN-PAK® filters. The oleum output levels were also enhanced by higher efficiency performance, ultimately, providing a smart solution that reduces the total NOx output of the plant in accordance with environmental regulations and enabling the producer to operate the plant without penalties or shutdowns (Fig. 6 & Tables 2 & 3).