Fertilizer International 503 Jul-Aug 2021
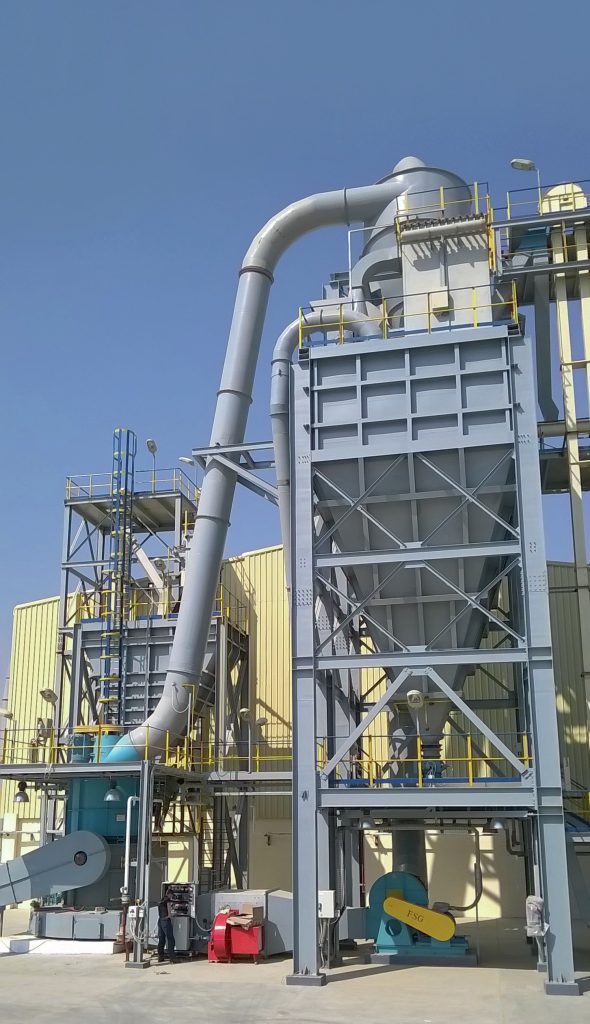
31 July 2021
The importance of phosphate milling
COMMINUTION TECHNOLOGY
The importance of phosphate milling
A holistic understanding of the phosphate milling process is necessary, says Ian Hancock of Bradley Pulverizer. This ensures maximum plant uptime, the highest process efficiencies, and ultimately guarantees profitability.
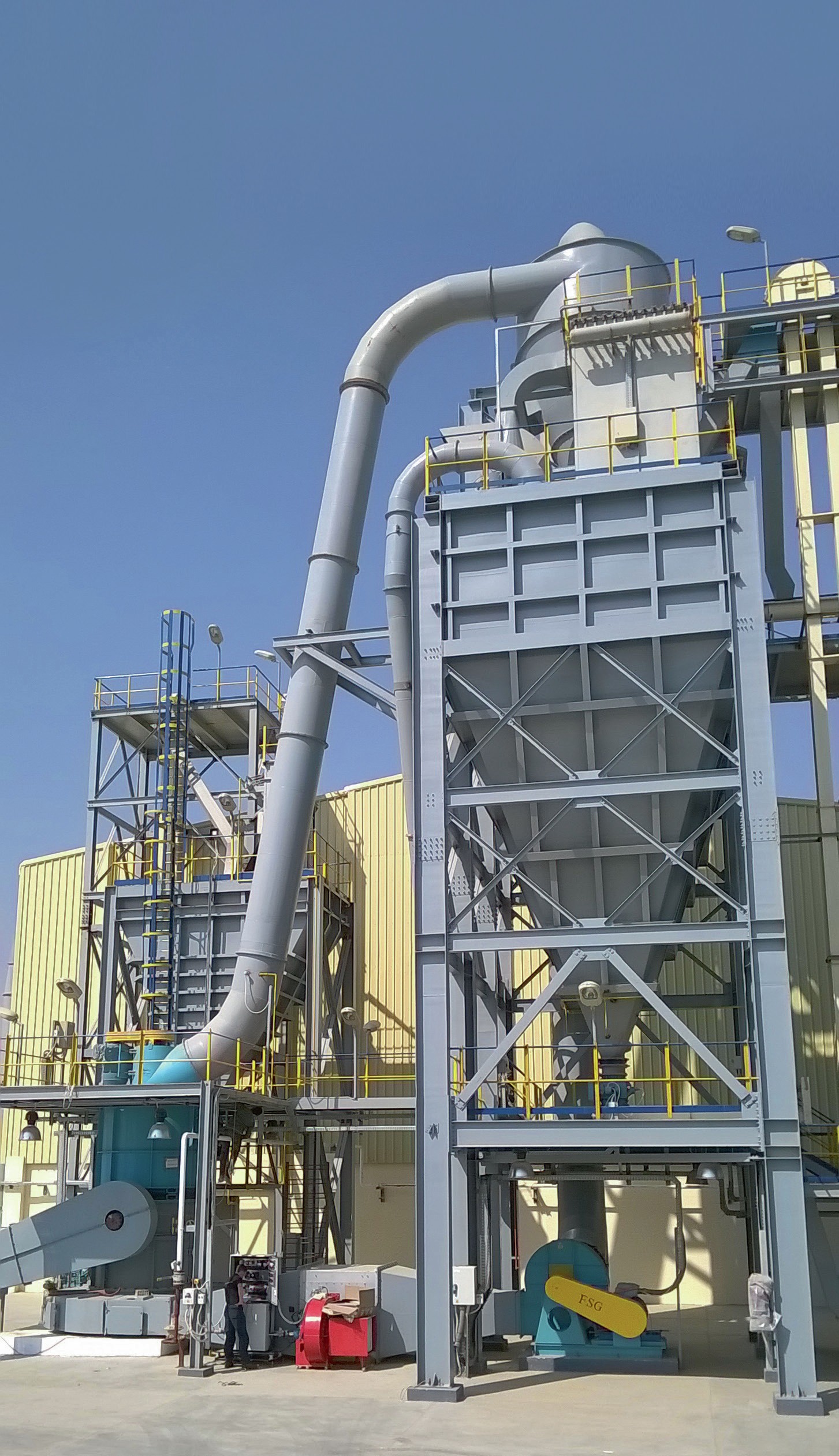
Grinding and pulverising mills are the furthest upstream process in phosphate fertilizer manufacturing. The continuous crushing of phosphate rock to meet particle size specifications is essential for efficient downstream processing. Yet mills are more commonly seen as the ‘noisy neighbour’ to other process steps, rather than the essential engine that drives phosphates production. Regrettably, this lack of recognition for the importance of milling can cause inefficiencies upstream that are further compounded downstream.
Phosphate milling – the essentials
Phosphate rock is fed into the front-end of a production plant and manipulated many times during its long process journey and eventual transformation into valuable end-products. This continual production process is central to efficient phosphate fertilizer manufacturing, with each process stage requiring specialised equipment.
The production process starts with crushing and grinding phosphate in a mill. This then feeds downstream processes such as acidulation, mixing, and pelletising through to final packaging. Every item of process equipment is interdependent, with the whole plant functioning as an interconnected network. In many ways, it is the upstream milling of phosphate rock that ultimately drives plant profitability and the overall quality and yield of the end-product.
It therefore follows that a holistic approach to fertilizer production is critical. That is because the continuous nature of the plant production process means adjustments to one piece of machinery will almost always require adjustments to other equipment, both upstream and downstream.
Unfortunately, however, this holistic approach is not always followed. The result is lower quality products, lower yields, and higher maintenance costs. In our view, this often occurs because fertilizer processing incorporates very different process steps – each one being covered by a separate engineering discipline. The upstream crushing and grinding of phosphate rock, for example, requires a comprehensive understanding of mechanical engineering and material properties, while downstream phosphoric acid production requires chemical engineering expertise. Metallurgists also make a vital contribution to phosphate beneficiation.
Expecting plant operators to employ large numbers of engineering graduates able to cover every single process step is not always going to be economically feasible. Nevertheless, staffing imbalances, in which one engineering discipline is overrepresented, can inevitably lead to an overemphasis on one process while others are overlooked.
To ensure a holistic approach, we would therefore encourage fertilizer manufacturers to view their processing plant as a series of specialised yet equally important circuits that work together as one whole system. To be managed properly, each circuit within the overall system should be staffed appropriately in our view.
In this article, we focus on the importance of the upstream milling system in a phosphate fertilizer production plant – explaining how a proper understanding of its role can enhance overall processing efficiency, yield and plant profitability.
The role of the mill
Simply stated, the role of the mill in fertilizer processing is to crush/grind/pulverise the raw phosphate rock. Typically, the aim is to reduce quarter inch-size crushed rock into fine particles to meet the required specification for downstream processing or acidulation.
The degree of fineness and what particle size is acceptable varies significantly according to the production process and type of rock being used. This, in turn, influences mill selection. For an igneous phosphate rock, for example, single superphosphate (SSP) production require a feed with 90 percent passing 53 microns. This falls to 90 percent passing 75 microns when sedimentary phosphate is consumed. When it comes to phosphoric acid production, 90 percent passing 150 microns is acceptable for the widely-used dihydrate (DH) process; whereas much coarser feed is acceptable for the hemihydrate (HH) process, with 90 percent needing to pass two millimetres instead.
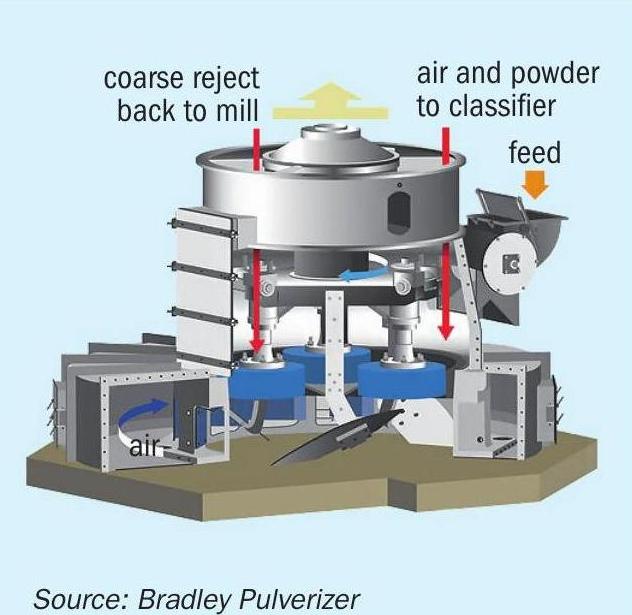
- Ring-roller mills: Vertical rollers rotate inside a fixed horizontal ring (Figure 1). Material fed between the rollers and the ring is ground to powder.
- Ball mills: A horizontal rotating cylinder contains a charge of steel balls. These balls tumble as the mill turns so that material caught between the balls is ground to powder.
- Table-roller mills: A horizontal table rotates with spring-loaded rollers mounted above. Material fed into the centre of the table passes underneath the rollers and is ground to powder.
Most phosphate processors choose air-swept milling systems due to their ability to remove fine particles from the grinding zone. Due to the cushioning effect from newly introduced feed, this allows the grinding action to be concentrated on the large oversize particles. This results in higher yields and, by minimising overgrinding, lowers energy consumption.
The air circuit is essentially the same for any air swept mill, being designed to maximise their inherent air sweeping effect. Inevitably, the high airflow needed to ensure all fines are swept from the grinding zone also carries over some oversize particles too. A classifier or separator is therefore needed to return these to the mill for further processing. Particles that meet the size specification, meanwhile, are removed from the conveying air by cyclones and bag filters.
Airflow is solely dependent on the milling rate. This means that similar capital and operating costs apply to every type of mill – making the selection of the correct type of mill a particularly critical factor.
While the mill remains a critical piece of fertilizer manufacturing equipment, it is fundamentally designed to be a reliable and largely unnoticed workhorse when functioning properly. Its role is to simply provide continuous pulverisation. Generally there is very little scrutiny beyond its ability to crush to specification while keeping noise levels and power usage within acceptable limits.
However, in fertilizer manufacturing, delivering the end-product downstream at the highest possible yield still requires precision-grinding of phosphate rock upstream. In practice, this means that mills need the help of classifiers to maximise their efficiency.
Classifiers: the brains of the operation
Fine grinding with air-swept mills involves the continuous return of oversize material to the grinding zone for further reduction to the desired size. The role of the classifier is to control both the amount of recirculation inside the mill and the particle-size distribution of the product.
Essentially, the classifier functions as the ‘brain’ of the grinding circuit. Critically, it automatically determines:
- What material should exit the mill as correctly sized product
- What should be returned for reprocessing.
Changing a classifier’s settings can significantly alter the milling system’s power consumption, capacity, vibration and product size distribution.
There are three main classifier types (Figure 2):
- Static classifiers. These are used for semi-fine grinding but have a very low efficiency and limited operational range.
- Dynamic classifiers. These incorporate a rotating rotor and, consequently, have a wider operational range.
- High efficiency classifiers. These combine useful elements both of the above technologies by using a static set of vanes to guide the airflow into a rotating rotor, alongside other optional features.
Upgrading an existing mill system with a new, correctly installed high efficiency classifier can deliver:
- Capacity increases of up to 25 percent
- Reductions in power consumption of up to eight percent
- Sharper classification curves.
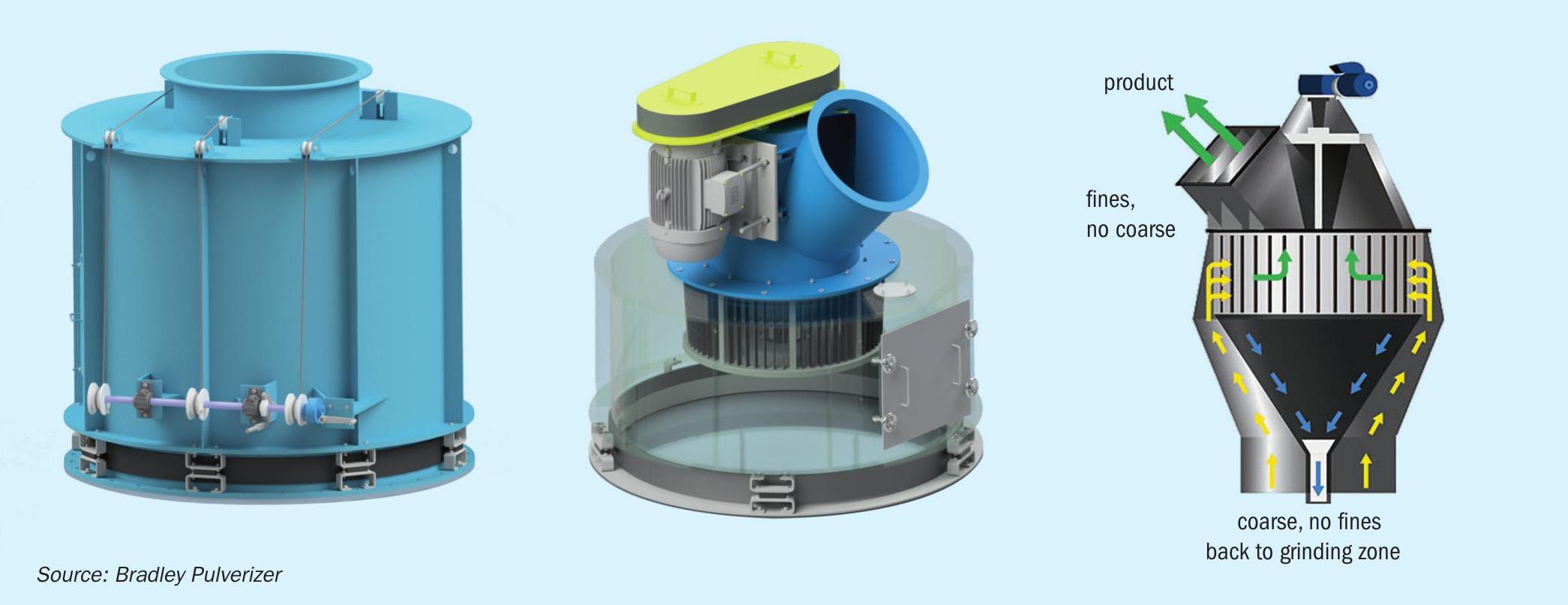
All classifiers have an efficiency rating, reflecting how well they separate material. Some are very efficient while others are less so. Inefficient classifiers are unable to achieve a good fine/coarse separation. This means the product stream will contain some coarse particles and the reject stream will contain fine material. This creates additional and unnecessary demand on the mill, resulting in higher recirculation rates which in turn requires more fan pressure and increases the power requirements of the fan drive.
A classifier’s operational efficiency is determined from the ‘Tromp Curve’ (Figure 3) – a graph plotting percentage classifier rejects against particle size. Essentially, this curve shows how much on-size recovery there is in the reject stream. Curves which are as close as possible to a vertical straight line at the cut point are theoretically ideal. Less efficient static classifiers typically show gently sloping lines, whereas more vertical lines – closer to the maximum theoretical limit – are shown by high efficiency classifiers.
In the fertilizer industry, dynamic vertical blade classifiers (VBC) are commonly specified for several reasons. VBCs are favoured because they offer high ‘uptimes’ with minimal maintenance and low percentages of reject particles. Another advantage is the ability for automating particle size control when coupled to an inverter (variable speed drive, VSD). The addition of a VSD is valuable as it makes on-demand adjustment of particle size possible. Lastly, the low pressure drop associated with VBCs helps propel particles through the classifier by maximising the air flow from the main mill fan.
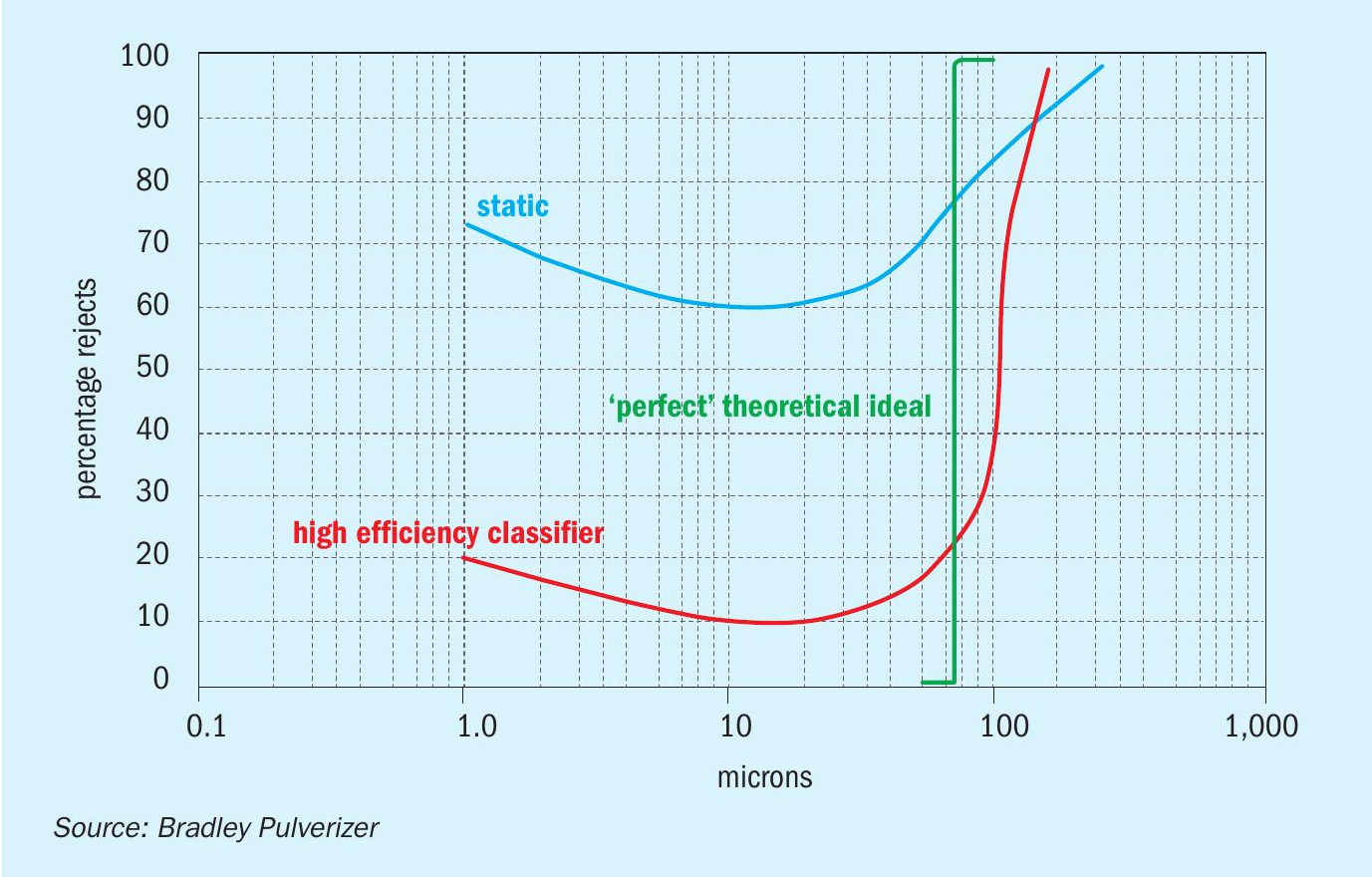
It is the classifier that ultimately controls the mill’s yield rate and hence the overall profitability of the plant. It is therefore imperative to evaluate both the mill and classifier together as a single system and not independent of one another.
The same ethos applies to post startup problem solving. We recommend a structured or holistic approach when troubleshooting production issues, with scrutiny of the process itself to identify the true cause of the problem. After all, the problem that presents itself may well have an indirect cause. If the mill is apparently lacking power, for example, the right solution may not be installing a bigger motor or investing in a new more powerful mill. Instead, the problem could be solved – and often is – by making air flow adjustments at the mill and/or classifier.
Unfortunately, we do encounter mill systems where the classifier was not evaluated properly prior to installation and cannot achieve the yields required to achieve profitability. In such cases, it is still more cost effective to replace the classifier than the mill.
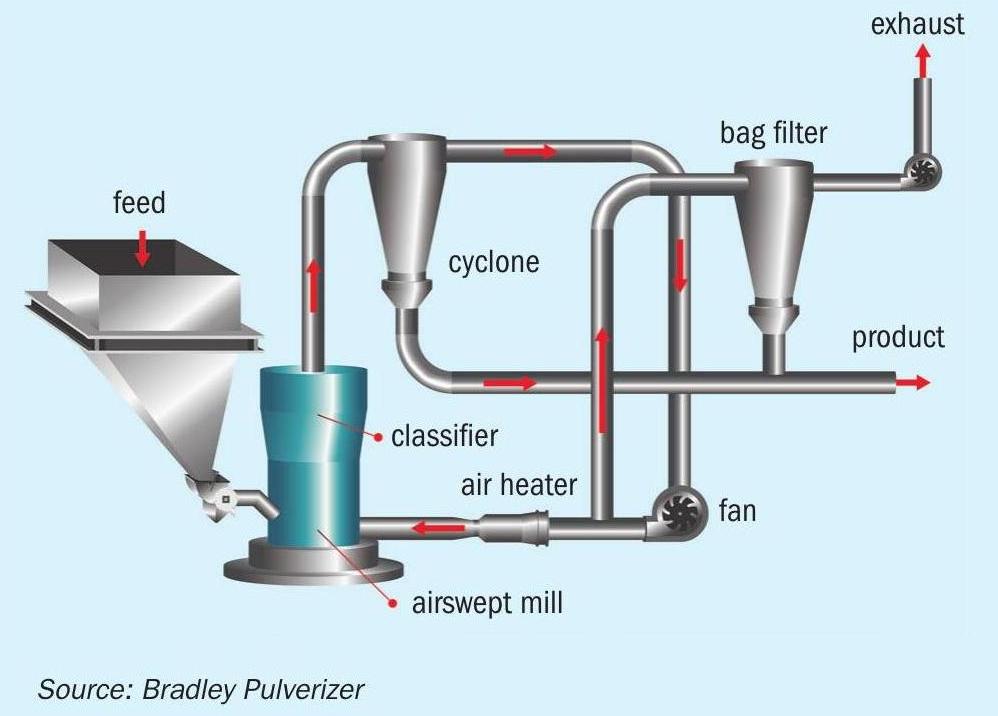
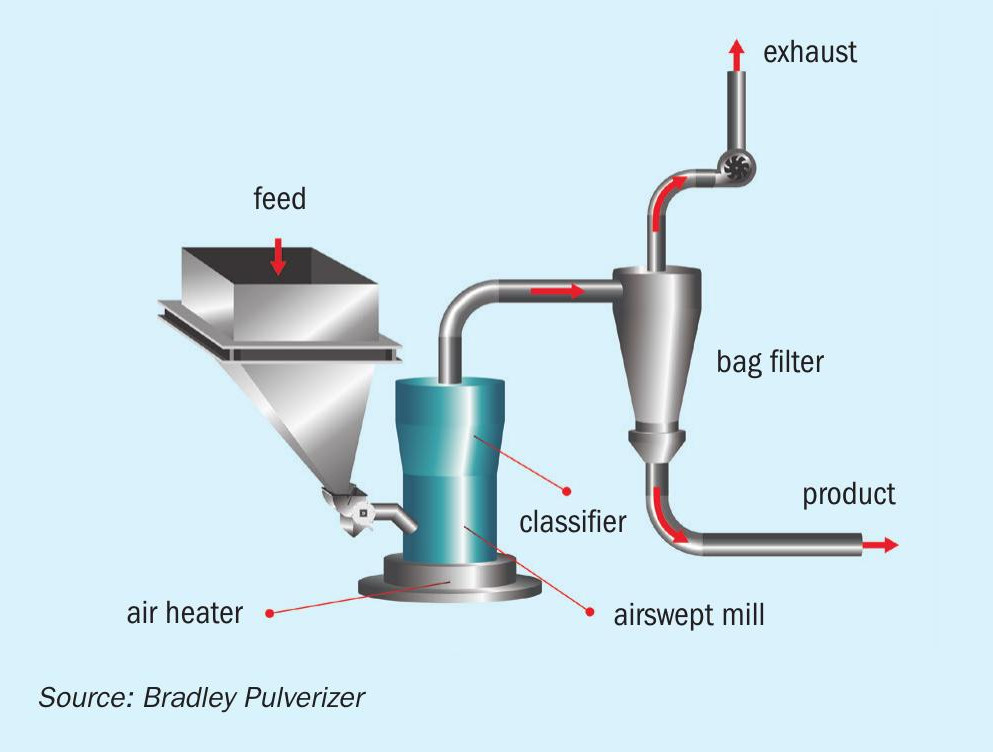
- A more thorough evaluation of classification requirements had been carried out pre-purchase, and/or
- If there was a better understanding of the process adjustments necessary to achieve maximum yields.
The complete mill system
After classification, the key to optimising system performance is the ability to effectively remove on-specification particles from the airstream and direct these as feed to the processing plant.
In addition to the air-swept mill and classifier, the other components of the mill circuit include:
- Fans and ducts for the pneumatic transport of crushed particles
- A bag filter that cleans dust-laden air in a single-pass mill system or maintains suction within recycled mill systems
- An integrated heater to reduce moisture and improve production.
Critically, these ancillary equipment items complete the circuit and minimise energy usage as well as ensuring continuous output.
Two main types of mill systems are available:
- Recycled mill systems (Figure 4) are optimal for the coarser grade materials encountered in phosphate processing
- Single pass mill systems (Figure 5), meanwhile, are ideal for fine to ultrafine grade materials and those materials with a high moisture content.
Recycled mill systems are most common in the fertilizer industry. This is due to their ability to maintain cyclone efficiency, when processing particles above 30 microns, as well as their lower maintenance costs.
Once again, properly specifying and maintaining all the ancillary equipment that completes the mill system is critical for optimum performance. This is yet another reason why we encourage both mill operators and project engineers to always evaluate the entire system whenever results are not as expected.
The mill itself tends to get the lion’s share of attention because it occupies the heart of the system where the most aggressive action takes place. Paradoxically, though, attempting to overcome low yields by cranking up the mill’s power usually ends up compounding the actual cause of the issue. In practice, an undersized exhaust fan or unmaintained bag filter, for example, can contribute to low yields and inefficiencies just as often, if not more so, than the mill itself. In fact, when performance issues with the mill are identified, they do tend to be of the obvious sort – such as significant wear on the rollers or wear ring where the grinding of phosphate rock is most intense.
Benefits of a holistic approach
The upstream mill system may seem simple, compared to other systems in a fertilizer manufacturing plant. Nevertheless, it should still demand equal attention due to the invaluable role it plays in the overall quality, yield and profitability of the end-product.
Any fertilizer product which contains P as a key ingredient will be partly derived from phosphate rock. It should always be remembered, therefore, that it is the mill which is responsible for crushing this hard, friable material to the specified particle size and supplying the feed to all downstream processes. The mill system often remains the forgotten workhorse in fertilizer processing plants and, consequently, often lacks the credit it deserves in helping transform phosphate ore into fertilizer.
The mill itself – to provide the uninterrupted tonnages required by fertilizer plants at high rates – must be rugged and function reliably in harsh operating environments. There are inevitable trade-offs and sacrifices, however. The primary requirement to supply a milled rock feed at high volumes will result in some inefficiency when it comes to meeting particle size specifications. Fortunately, this can be accounted for and corrected by incorporating equipment – such as an integrated classifier, baghouse, fan and heater – to create a complete mill system. Milling efficiency can be maximised, and downstream demands for both particle size and volume can be consistently met, by ensuring proper calibration, evaluation and maintenance of the entire mill system.
In our view, a holistic approach to the mill system is always imperative. This should be applied throughout the mill’s operating lifetime, starting from when the initial scope of the mill system is first defined. Adopting a holistic approach helps operationally by providing a better understanding during the troubleshooting of ongoing problems. It also directly benefits the bottom line and delivers higher profits by lowering maintenance costs and energy consumption, while also raising production efficiencies and yields.