Nitrogen+Syngas 373 Sept-Oct 2021
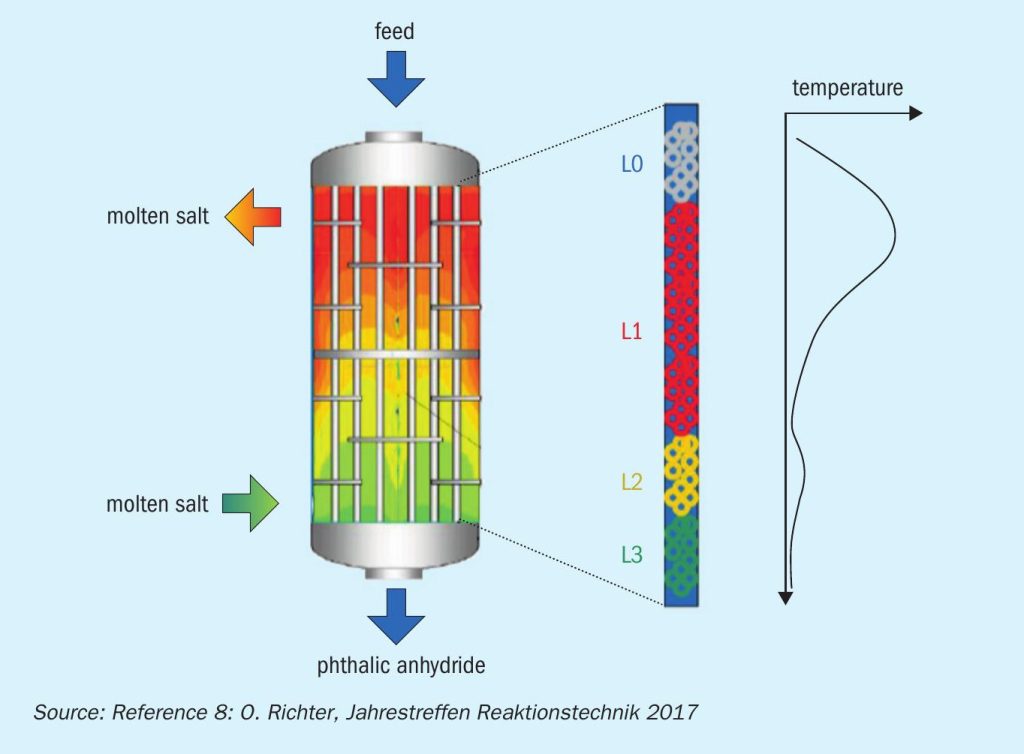
30 September 2021
A flexible tool for methanol synthesis
CATALYST LOADING
A flexible tool for methanol synthesis
MegaZonE™ is a newly introduced layered loading technology for boiling water-cooled reactors used for methanol synthesis. This new concept is one of the latest results of the long-standing collaboration between Air Liquide Engineering & Construction and Clariant Catalysts to improve the methanol process flowsheet and optimise catalyst performance in the complete reactor system.
Clariant has been producing industrial catalysts for methanol production for well over 40 years. However, Clariant’s efforts to continuously improve the catalyst performance are not limited solely to catalyst formulation, but also focus on the overall process and how the catalysts can be optimally utilised in the complete reactor system.
A cooperative relationship
Since the early 1970s, Air Liquide Engineering & Construction and Clariant Catalysts have been in a strategic collaborative partnership which has led to many innovations over the last 50 years.
One of the main goals in Clariant’s catalyst development has been to enable Air Liquide to achieve their future design goals as they continue to innovate and optimise their methanol process flowsheet.
In parallel, Clariant has been developing new catalyst generations such as the MegaMax® 700, 800 and 900 series. The development of innovative plant designs along with state-of-the-art catalysts is enabling producers to further maximise production at reduced total costs and increasing lifetime. Another result of the long-standing collaborative relationship with its partner Air Liquide is Clariant’s newly introduced layered loading concept called MegaZonE™ .
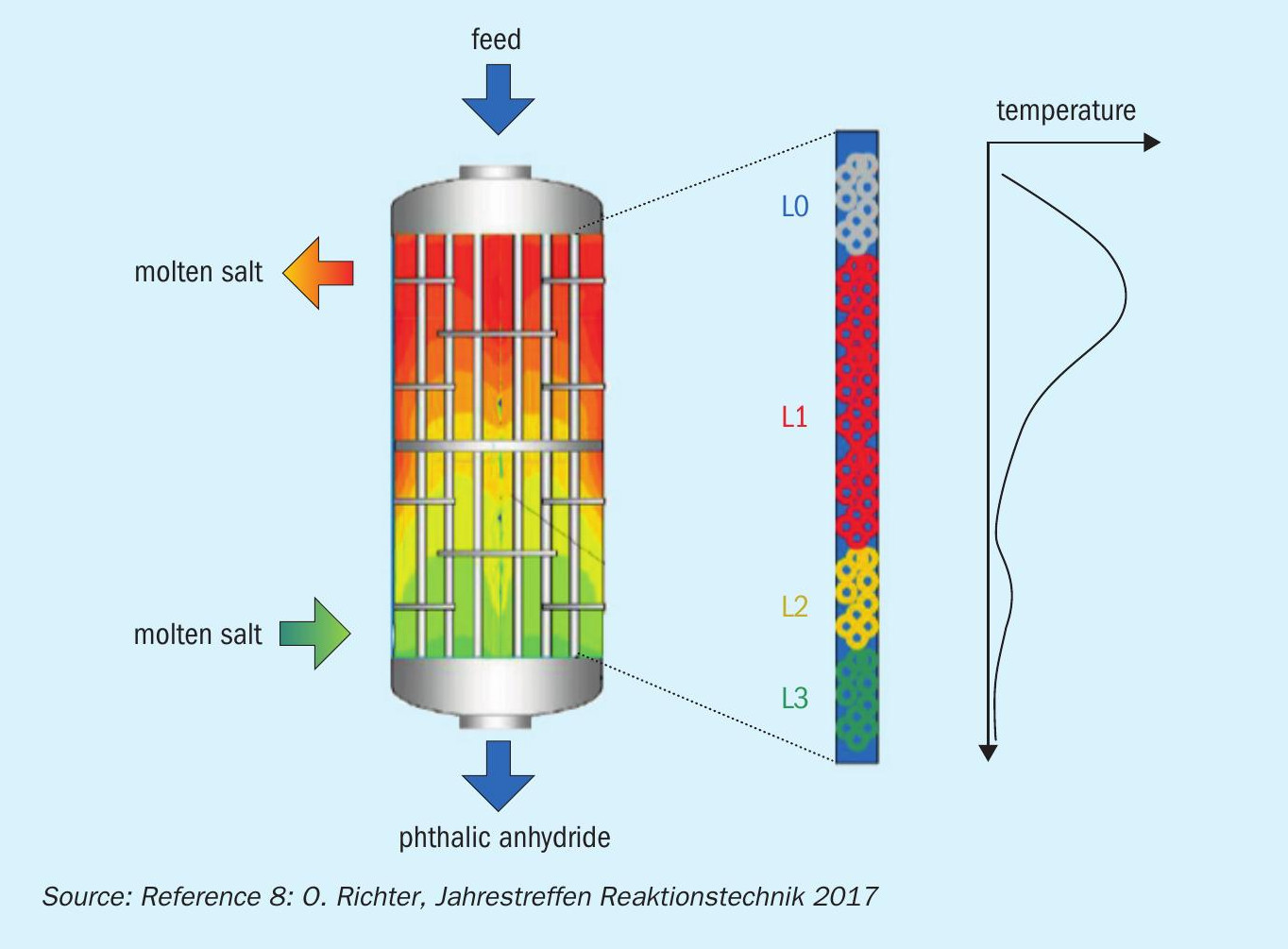
The concept
The Air Liquide reactor systems (water- and gas-cooled reactor designs) are already the benchmark for per pass conversion and heat management. Customarily, the reactor tubes are loaded with a single catalyst type only. However, Clariant is involved in various commercial application areas and speciality sectors that employ catalysts where different loading schemes are applied. Two relevant examples are the Phthalimax® series of catalysts used for phthalic anhydride production and the FAMAX® series for formaldehyde production. These are selective oxidation reactions utilising tubular reactors with catalysts in the tubes and a cooling medium on the shell side for temperature management, resembling the boiling water methanol reactor concept (Fig. 1). Both applications have been optimised over the years and benefitted dramatically from the use of multi-layer catalyst loadings. For these applications, a layered loading scheme is nowadays a standard approach and considered state-of-the-art. Each of the applications uses specially tailored catalyst layers that may incorporate different catalyst shapes, activity levels, and selectivities. The concept allows optimisation of the reaction rates over the reaction path, which improves the temperature profile and selectivity. It is particularly critical in these systems to control the peak or hot spot temperature as it can lead to premature aging, severe by-product make, and even the possibility of runaway reactions2,3,4,5 .
In the methanol reactor, peak reaction temperatures and reaction profiles also need to be considered to optimise the overall process efficiency. In contrast to the selective oxidation applications, for which hot-spot reduction is the major target, Clariant’s investigations focused on the possibility of improving the utilisation of the catalyst volume in the methanol reactor over the catalyst lifetime, i.e., increasing space-time yield and catalyst lifetime.
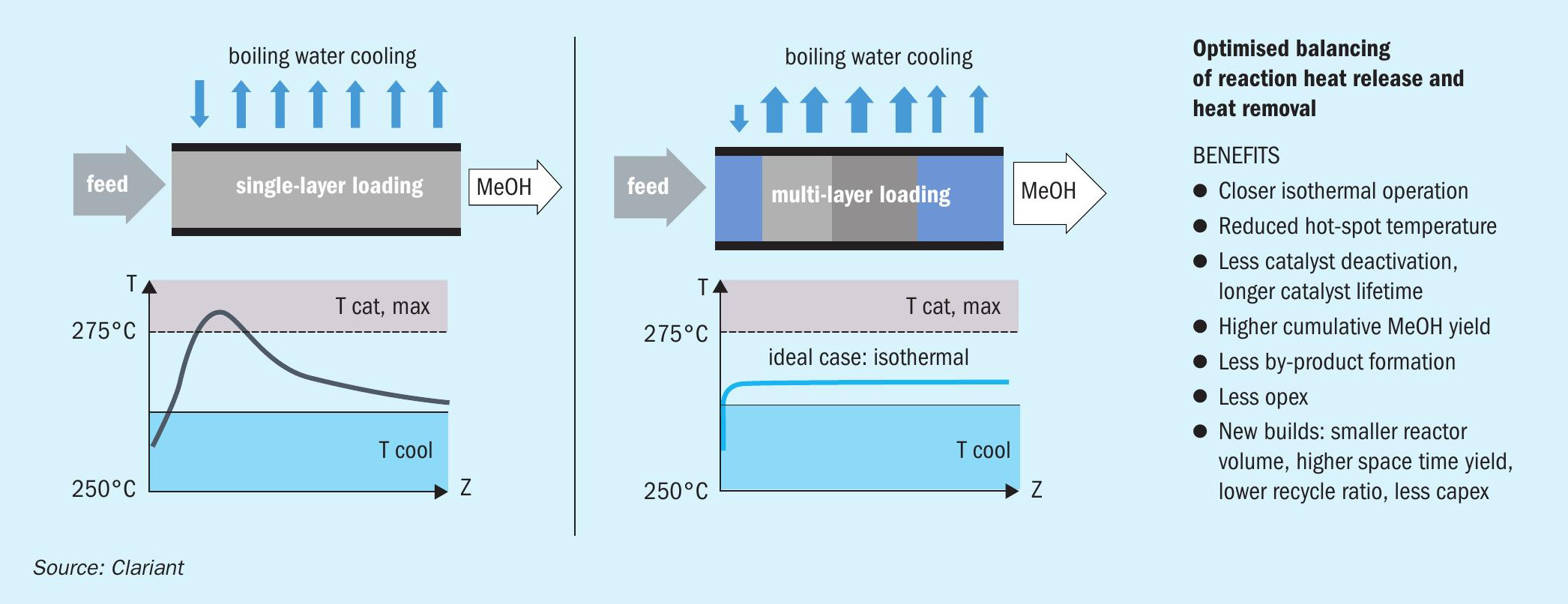
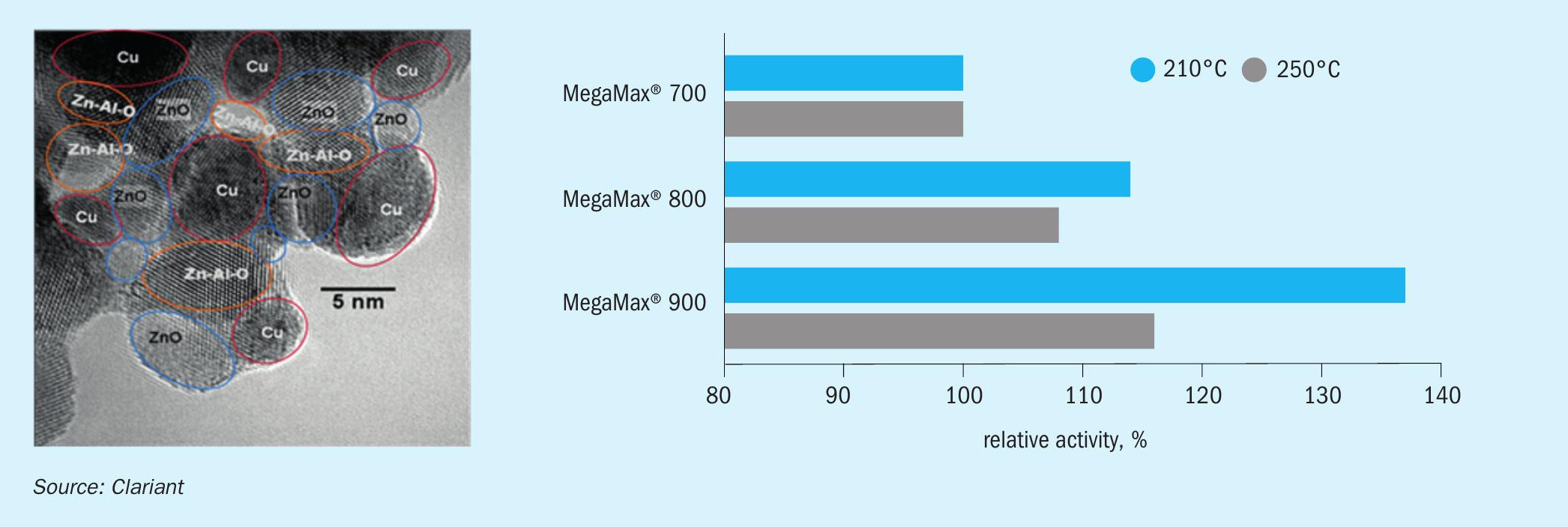
Based on the success in selective oxidation applications, it was felt that there would also be potential benefits when applied to methanol synthesis. The challenge was trying to determine the true potential. Several years ago, Air Liquide and Clariant initiated a cooperation with the University of Erlangen to perform an initial scoping study of the concept. It involved some detailed computational examination of multi-level layered loadings as applied to a methanol reaction system. The results were very promising and showed that it was possible to achieve more effective utilisation of the catalyst volume through multi-level layering. This data provided the confidence leading to the decision to proceed and further investigate and exploit the concept on a commercial scale.
Thus, what is the goal, and why is a layered loading concept of potential benefit in the boiling water-cooled style of methanol reactor? Fig. 2 illustrates a potential advantage of a layered loading which was conceptionally derived from the initial scoping study and then further evolved over the past years.
In the scenario depicted in Fig. 2, the scheme on the left shows a traditional steam raising reactor loaded with a single highly active catalyst layer. The desire is to maximise yield and ultimately provide the longest life possible. Much like in the previous selective oxidation type reactor, the incoming reactive gas, in the presence of a highly active catalyst, can result in high reaction rates with a corresponding rapid increase in the temperature. The ability of the reactor to remove this heat and reduce the peak temperature is a function of the reactor heat transfer and the temperature of the water/steam on the shell side. Unfortunately, this relatively high reaction rate can result in high peak temperatures, which can lead to an increased rate of deactivation and by-product formation, not to mention potential equilibrium limitations.
Ideally, it would be better to try and smooth out the profile to reduce the peak, resulting in a net lower average, more ideal temperature profile. By incorporating multiple layers of catalysts with specific properties related to reaction rates, heat transfer, selectivity, etc., it becomes possible to better control this overall temperature and reaction profile.
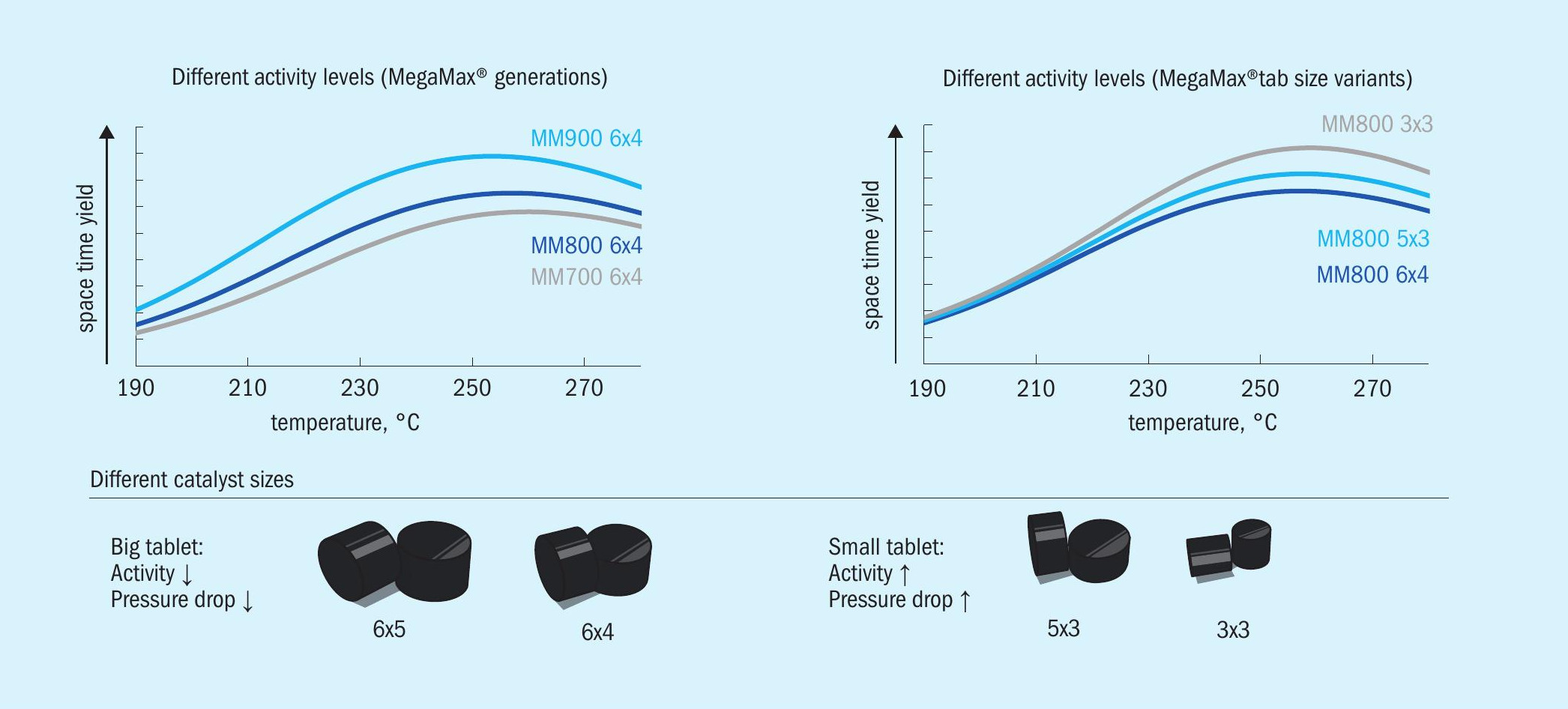
This can then yield a closer to isothermal operation, reduced hot spot, resulting in lower catalyst deactivation, higher cumulative methanol yield, lower by-product formation, ultimately resulting in reduced opex and higher lifetime yields. The benefit of increased lifetime yields achievable by using a customised arrangement of only two catalyst layers is described in detail based on a modelling case study in the following sections (see Figs 8 and 9).
For new plant builds, the concept can be further exploited, potentially leading to reduced reactor volume, higher spacetime yields, lower recycle ratio, and hence reduced capex.
MegaMax® methanol catalyst portfolio as a basis for MegaZonE™
Clariant is well known for its syngas catalyst portfolio, and in Air Liquide’s methanol process Clariant’s copper-based methanol catalyst (i.e., the MegaMax® series) is well established as a basis for their design. An extensive research effort and scientific collaboration helped unveil the intimate interplay of Cu, Zn, and Al and understand the fundamental kinetics of the Cu/ZnO/ Al2 O3 system, as illustrated in high-resolution electron microscopy images (Fig. 3 left)7 . Consequently, this allowed Clariant to improve the catalyst preparation route and the production process resulting in continuously increasing intrinsic activities from one catalyst generation to the next (Fig. 3 right).
To serve the concept of MegaZonE™ and allow rapid “in-silico” screening, Clariant has developed a catalyst library8 . This allows the simulation of various MegaZonE™ setups (consisting of tailored layers of different catalyst shapes and/or catalyst generations) in a methanol loop model developed jointly with Air Liquide (see Fig. 4). The catalyst model is based on a sophisticated heterogenous pellet model and uses a proprietary kinetic mechanism. In the MegaZonE™ concept, each layer can thus be attributed with a different function depending on the targets or boundary conditions of the reactor design (i.e., pressure drop, methanol yield, catalyst lifetime, by-products). Moreover, the overall process model allows simulations at an industrial scale and concurrent performance optimisation.
Clariant and Air Liquide developed modelling tools to predict the performance of a methanol reactor loop employing Mega-ZonE™ over the full lifetime of the catalyst. These modelling tools are continuously validated and improved based on pilot plant data and industrial feedback.
Model and concept validation with pilot plant
One of the strengths of Air Liquide’s experts is in generating data in a pilot plant and translating the data into a form that can be used to scale up results. To support these efforts, Air Liquide utilises a process development unit (PDU) which consists of a single reactor tube with a steam jacket, two separators at different pressure levels, and a recycle loop to feed unconverted gas back to the inlet of the reactor as depicted in Fig. 5. The single reactor tube translates directly to industrial-scale, multi-tubular tube-bundle reactors.
The comparison of one of the experiments and the respective modelling results are shown in Fig. 6. It shows that the temperature profile and the conversion obtained from the model are in line with the experimental observations. Therefore, the experiments confirm the validity and accuracy of the model developed by Air Liquide with the support of Clariant.
Catalyst deactivation in industrial processes
Deactivation is unavoidable in commercial methanol plants, so an industrial catalytic process cannot be designed or optimised without considering catalyst aging over the lifetime. Therefore, understanding and predicting catalyst deactivation behaviour is crucial to determine the lifetime yield and catalyst turnover. Based on the temperature profiles of commercial plants, an activity profile can be deduced using an optimisation approach. As can be anticipated, the result is a sigmoidal activity profile (Fig. 7, right) as a function of the normalised reactor dimension. In addition, routine evaluation of actual plant data by Clariant’s Applied Catalyst Technology (ACT) personnel allows Clariant to refine and update its models, ensuring excellent simulation accuracy.
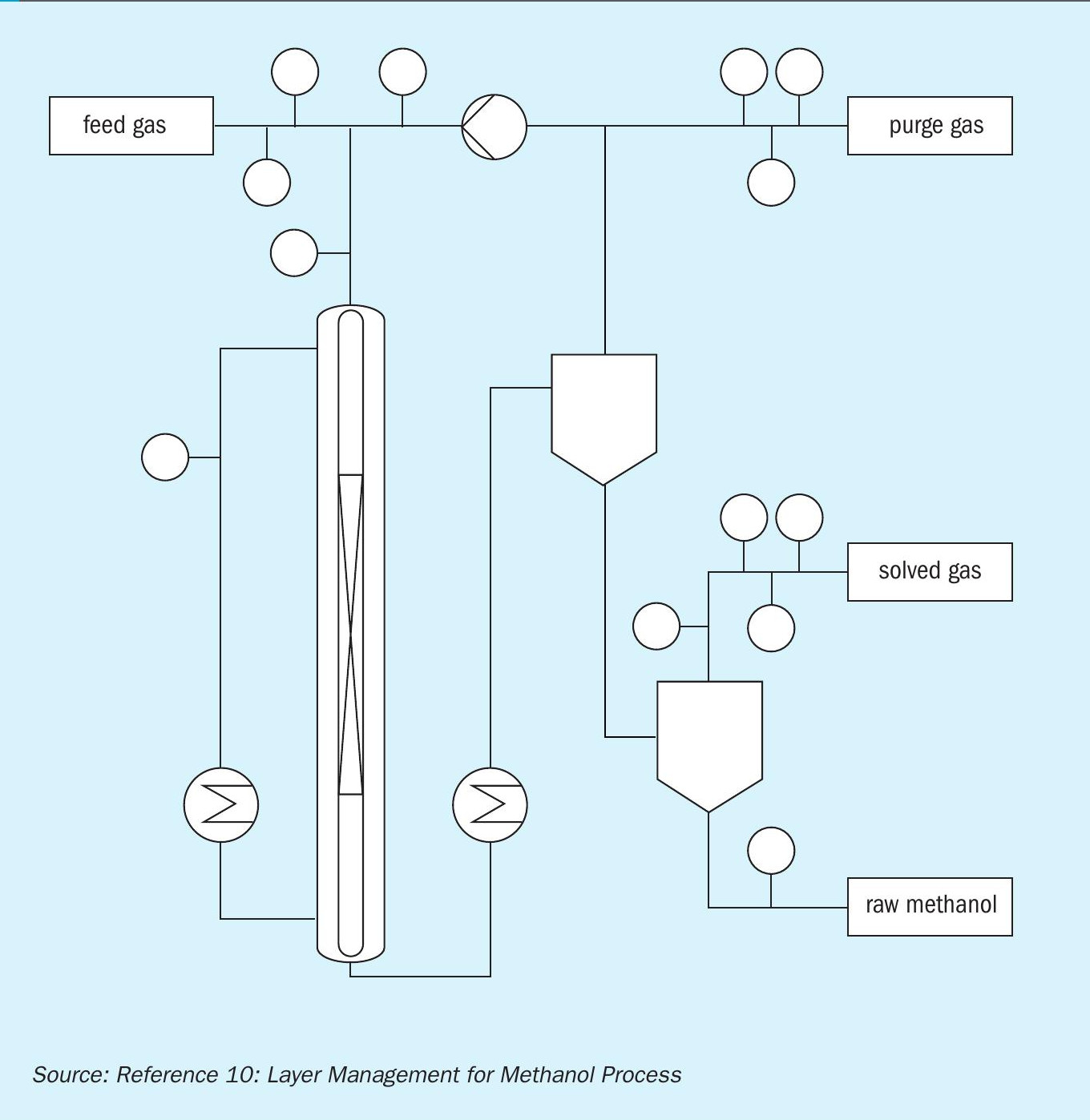
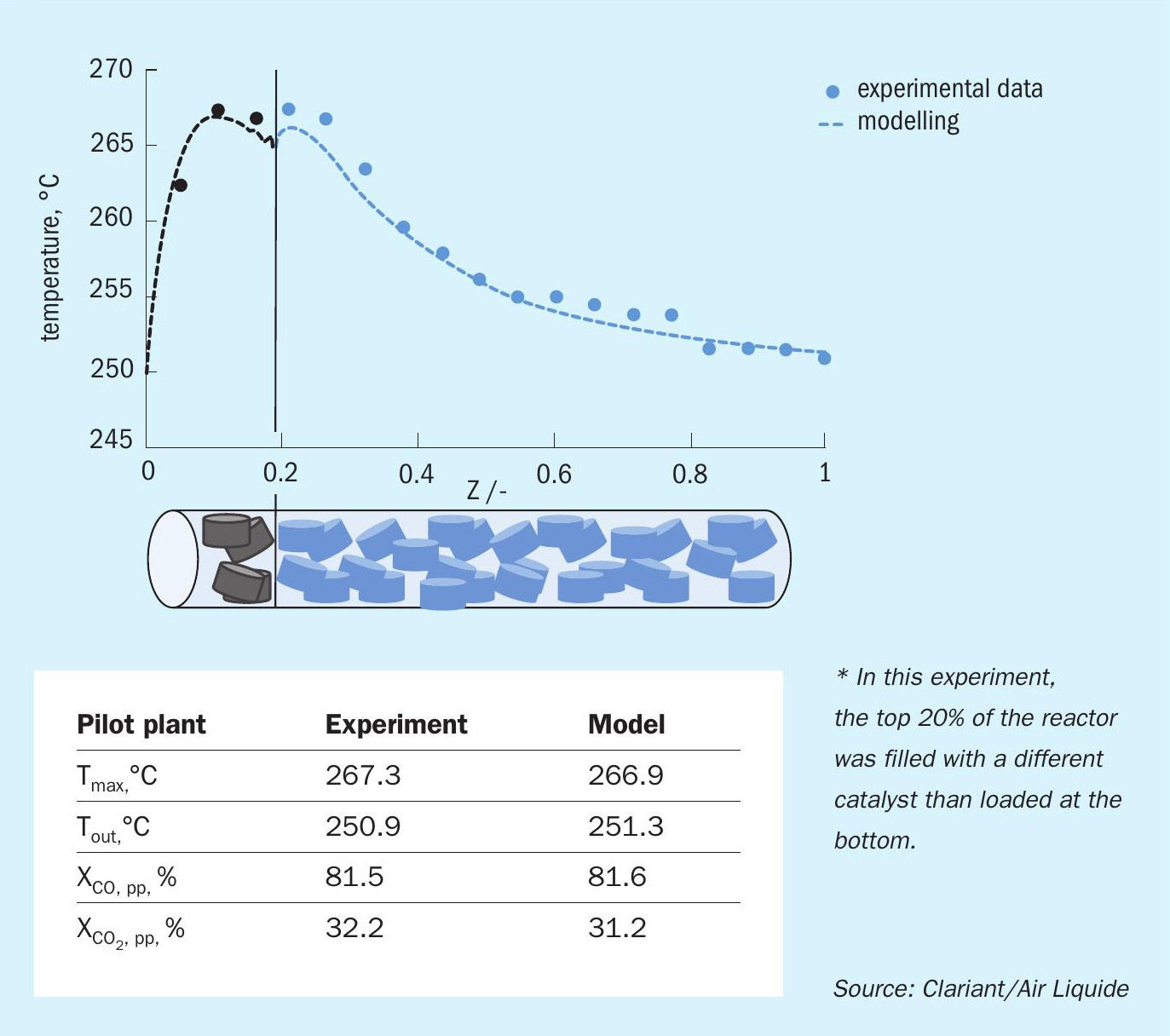
Concept for commercialisation
Commercialisation is envisioned through refill solutions that could meet the constraints of existing facilities and stepwise exploit the potential of the MegaZonE™ concept. The first MegaZonE™ reference has been in commercial operation since August 2018. In this case, the successfully achieved target was to optimise pressure drop in the gas-cooled reactor of a large-scale MegaMethanol™ plant. However, the main objective of MegaZonE™ for refill cases, besides pressure drop optimisation, is a longer lifetime of the catalyst and more accumulated methanol production over the lifetime (lifetime yield).
When evaluating MegaZonE™ for existing methanol processes, one of the critical factors to be considered is the pressure drop. Pressure drop can be a significant constraint to equip plants with MegaZonE™ , and it will impact the operating conditions of the whole synthesis loop. Therefore, the aim is to find a solution to improve the methanol production by using the Mega-ZonE™ concept within the design restriction of pressure drop. Case studies were taken into consideration to evaluate the benefit of MegaZonE™ on existing plants. All plant-specific constraints (i.e., pressure drop, recycle compressor, steam temperature…) are considered in the simulations, and an optimum solution for the specific plant is developed. In most methanol plants, recycle ratio, reaction temperature, and loop pressure in the methanol synthesis loop are increased over time to compensate for the deactivation of the catalyst. With MegaZonE™ , the loop efficiency would be increased, thus the loop could be operated at milder conditions, particularly at start-of-run and through the life of the charge. This would result in increased energy efficiency and extended catalyst lifetime. If more synthesis gas can be made available, MegaZonE™ would even be a solution for further increased capacity.
As highlighted earlier, the benefits of MegaZonE™ will ultimately be exploited in Air Liquide’s future design for grass-roots plants, resulting in lower capex and opex costs.
Modelling case study
Based on the validated model and the commercial deactivation behaviour, it is possible to make reliable lifetime yield predictions and optimise the reactor layout. In a modelling case study, a significant benefit in achievable methanol yield could be shown, especially at end-of-run (EOR) when local deactivation of the catalyst layers becomes important and the per pass conversion decreases (schematically shown in Fig. 8).
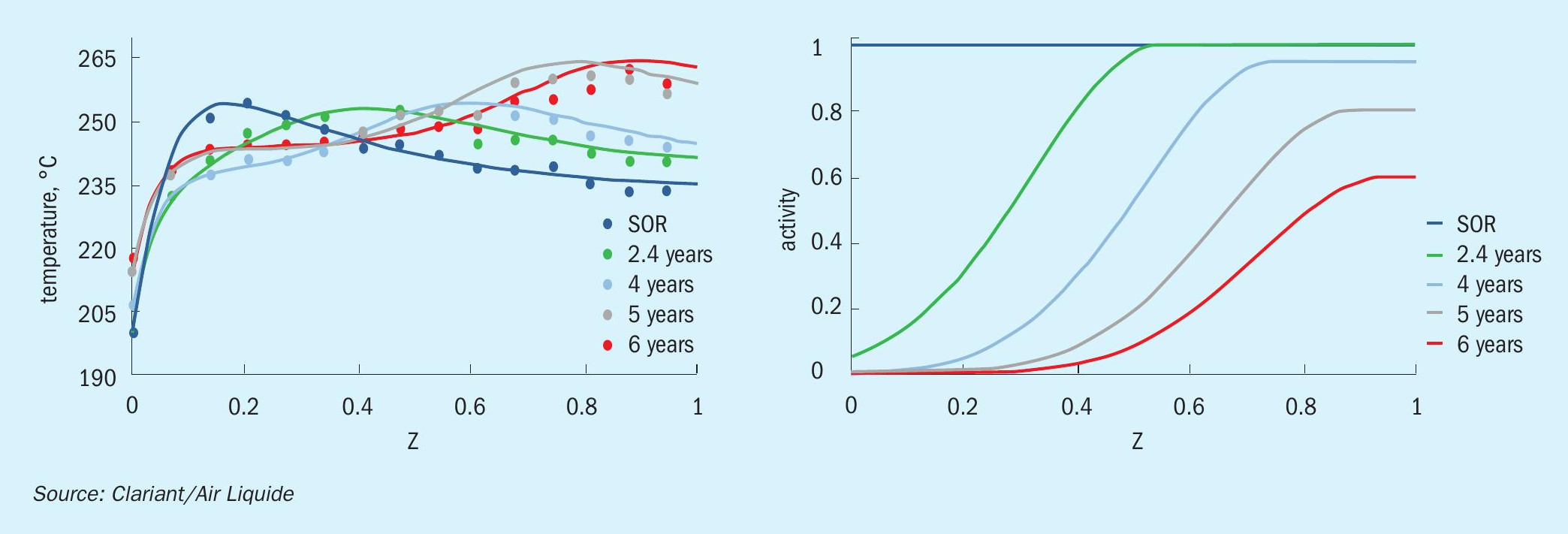
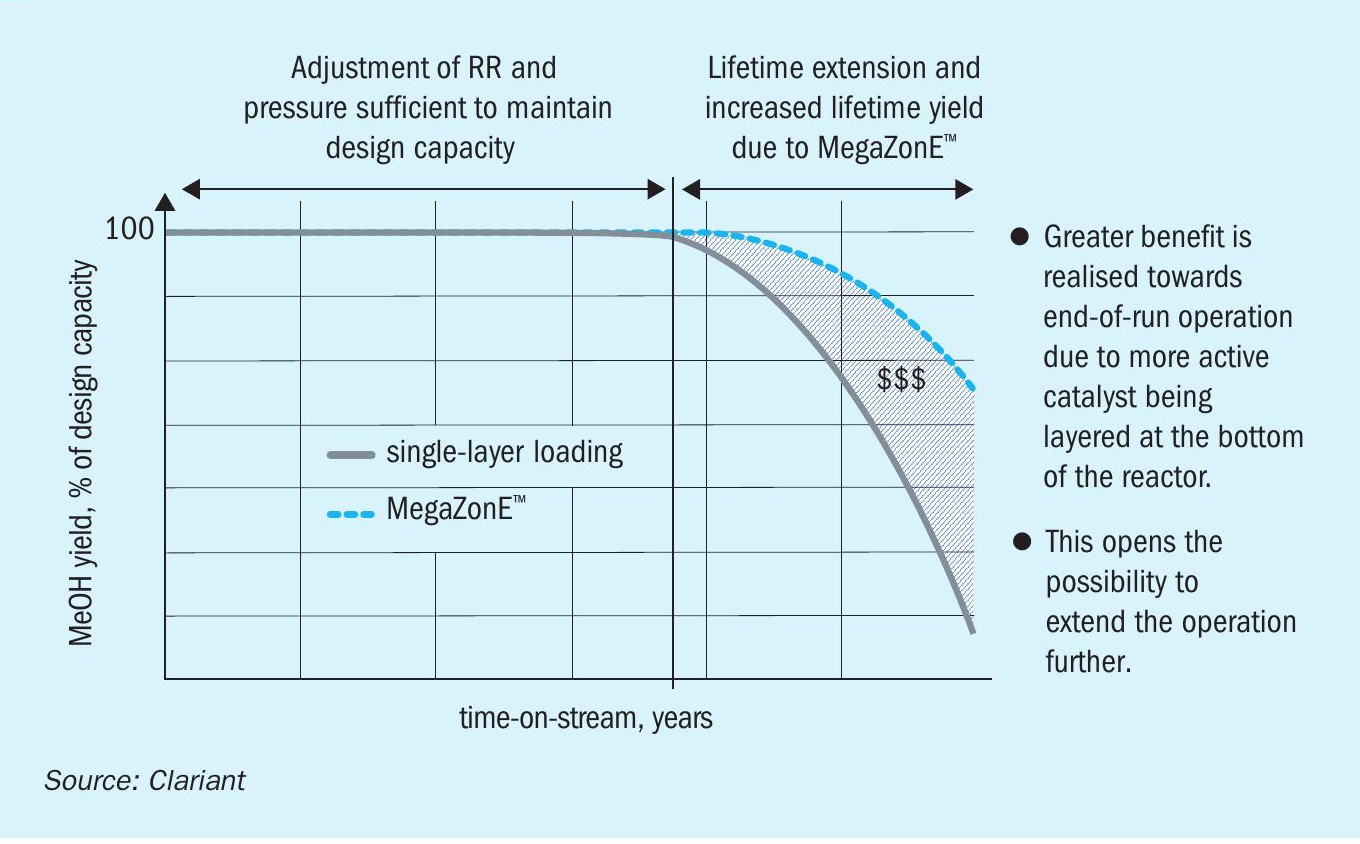
This opens the possibility to extend the operation lifetime and contributes significantly to the lifetime production of the catalyst. However, it should be considered that under typical plant operation with regular adjustments of operating conditions, e.g., RR or pressure, to keep methanol productivity close to 100% of design capacity, the benefits of MegaZonE™ will be less obvious at startof-run (SOR) and middle-of-run (MOR). Here catalyst activity is typically so high that per pass conversion is limited by thermodynamic equilibrium, and overall plant conversion is close to 100% also in a single catalyst loading scenario. The real benefit of MegaZonE™ can be seen when proceeding from MOR to EOR when adjustments of the operating con-ditions in a single catalyst loading scenario could no longer compensate for the deactivation effects. The benefit on lifetime yield achievable is visualised in Figs 8 and 9.
A specific study was performed for a plant proposal where a significant amount of optimisation studies and examination of different layered loading concepts was examined. It was important to adhere to design limits related to maximum make-up gas flow, compressor capacity, loop pressure, and overall pressure drop in the study (Fig. 9). The graph on the left shows the simulated performance of the single-layer concept compared to the MegaZonE™ optimised loading. As noted in the previous general example, the benefit is not particularly large in the early part of the charge’s life but does depend on specifics related to reactor heat transfer and loop constraints. After approximately three years on-stream, however, there is a noticeable production rate differential. This differential would appear sooner if poisoning mechanisms were higher. The chart on the right thus shows the incremental production associated with the MegaZonE™ loading versus the single layer loading. The potential benefit is quite significant in terms of both the total volume of additional methanol produced and the potential for lifetime extension between turnarounds. In the example, it could yield a total additional cumulative production level of over 30,000 tonnes by year 5.
Catalyst loading technology
Depending on the generation of the reactor, the traditional Air Liquide water-cooled reactors consist of 4,800 to 8,000 tubes per reactor with a loaded height ranging from 7 to 10 m long. Normal loading procedures are relatively simple and involve pouring the catalyst onto the tube sheet. Newer loading methods developed by Clariant’s Applied Catalyst Technology (ACT) team also incorporate a cassette loading system capable of achieving higher loaded densities with more uniform packing characteristics. These methods, however, were only applicable to standard single-layer loadings so far.
When implementing the MegaZonE™ layered loading catalyst system, it is necessary to ensure that all tubes are loaded uniformly in density and height. To accomplish this, it was also necessary to develop loading methods able to accurately load two or possibly more different layers of catalysts into the reactor tubes. This must not only be done accurately but also fast to avoid excessive additional downtime for the loadings. By leveraging extensive loading experience and customised loading equipment for multi-layer oxidation catalyst systems combined with expertise in single catalyst loading for methanol reactors, it was possible to develop and test new concepts. Based on the specific requirements for the layered loadings, it was further necessary to consider multiple methods adjustable to the reactor configuration and necessary loaded heights needed.
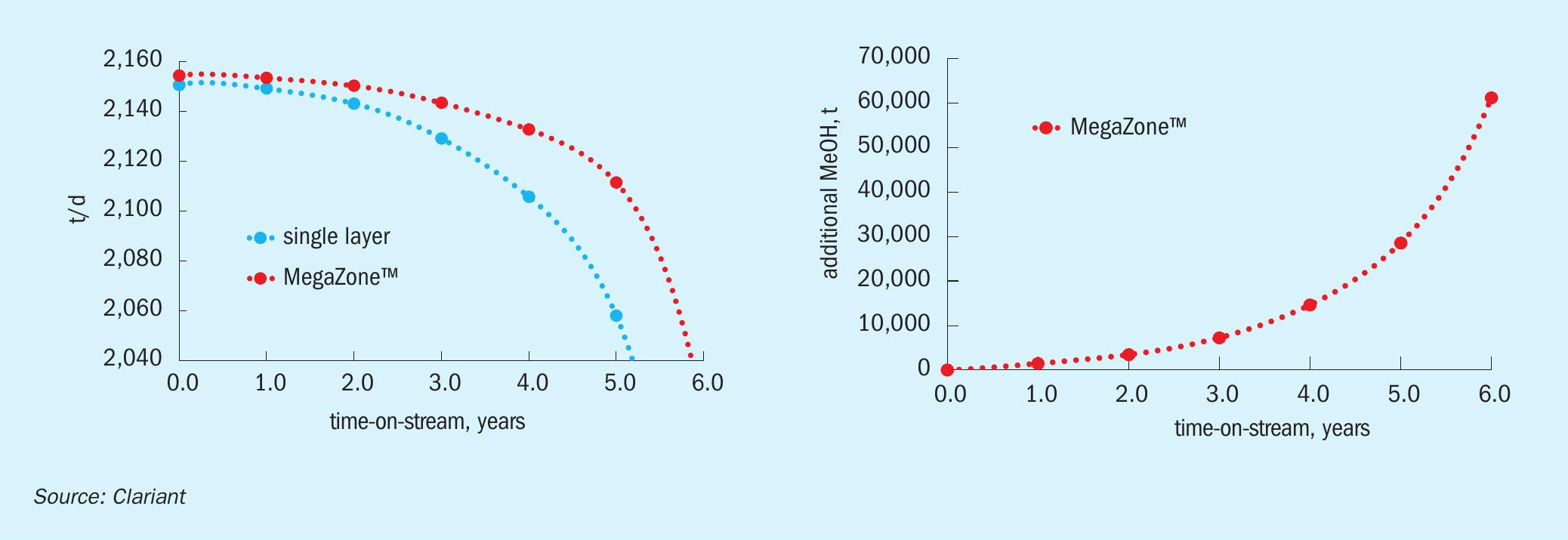
By adapting the oxidation catalyst loading technologies and developing innovative specialty equipment, it was possible to design and then test the systems in Clariant’s pilot-scale reactor system. The result of further fine-tuning is a set of loading systems flexible enough to handle all loading requirements and able to achieve both uniform loading densities but also outage variation typically under 50 mm for different layer configurations. These approaches then ensure that the catalyst is loaded optimally for performance and also time efficiency.
MegaZonE™ commercial implementation
Apart from the initial loading in August 2018 referenced earlier, the concept has now been successfully implemented in two other world-scale Air Liquide water-cooled reactors. Both plants were loaded and started up in early May of 2021. In both cases, the operating conditions and process/equipment constraints were carefully reviewed in the proposal stage to develop the best layering option given system limitations and maximise the overall benefit. Since start-up, both plants have performed as expected concerning overall conversion and pressure drop expectations. At one site, the enhanced activity of the Clariant catalyst MegaZonE™ loading has enabled further loop optimisation resulting in a substantial production rate and loop efficiency increase at the same time on-stream. Clariant continues to trend the performance and expects to see an increased benefit with additional time on-stream.
Conclusion
Clariant and Air Liquide have been collaborating in methanol synthesis for many decades and have successfully investigated the possibility of improving the interplay and overall performance of catalyst and the reactor system. The development of MegaZonE™ for methanol synthesis is another example of successful cross-market technology transfer and joint-development between an engineering company and a catalyst provider working in close collaboration. The potential of MegaZonE™ can be seen as a game-changer for current methanol producers and in the future for more compact and resilient designs. By utilising the rigorous modelling tools and expertise related to loading, operation, and optimisation within Clariant’s Applied Catalyst Technology group, the ideal solution for each application can be ensured. This combined catalyst and technology approach allows for a vast range of tailormade refill options and process optimisation to improve the catalyst usage in all existing units (for example, debottlenecking). Furthermore, in the context of a circular economy, different feed sources such as stranded gas, unused syngas capacities, and CO2 -rich gases, MegaZonE™ is a flexible tool to offer optimised methanol synthesis set-ups for a wide range of specific plant
References