Fertilizer International 504 Sept-Oct 2021
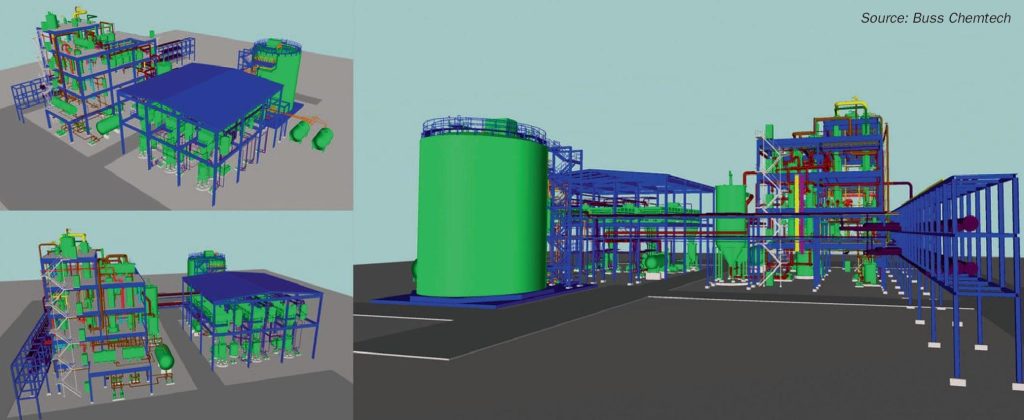
30 September 2021
Converting fluorosilicic acid into value-added hydrogen fluoride
SUSTAINABLE PHOSPHATE PRODUCTION
Converting fluorosilicic acid into value-added hydrogen fluoride
Buss ChemTech AG offers the international phosphate industry a robust solution to create added-value products from fluorosilicic acid (FSA). Thomas Dahlke, the head of the company’s process engineering department, and Emre Sen, sales manager for fluorine technologies, explain how this can be done in a sustainable manner.
Sustainability is becoming ever more important across all industries – with the phosphate industry being no exception. Because of this, value creation needs to be built around a comprehensive sustainability strategy embracing ecological, technological, social and economic aspects.
One route to perfecting sustainability involves the conversion of low-value co-products into value-added products, without any compromise to the four aspects mentioned above.
One of the most promising phosphate industry co-products, from both a value-added and sustainability point of view, is fluorosilicic acid (FSA).
Shift away from limited, traditional FSA markets
The consumption of FSA in conventional end-uses is very low compared to overall production capacity. The three traditional markets for FSA are small and/or in decline:
- The main end-use for FSA – low bulk density aluminium fluoride (LBD AlF3 ) – is limited and ever shrinking.
- The market for water fluoridation, another key application, is also limited, as well as being controversial due to increasing public health awareness.
- The other principal application, fluoride salt manufacture, again, has very limited market size.
Fortunately, these market obstacles can be overcome. Buss ChemTech AG (BCT) offers the international phosphate industry a robust solution to create added-value products from FSA in a sustainable manner. For phosphoric acid producers, BCT’s technology opens the door to the manufacture of anhydrous hydrogen fluoride (AHF) from FSA – bringing with it new higher value markets such as organic and inorganic fluorochemicals or high bulk density aluminium fluoride (HBD AlF3 ) (Figure 1).
Diversification into such revenue streams, given the competitive challenges faced by the phosphate industry, improves not only the bottom-line but also balances and protects producers from market volatility in their core business. To summarise, BCT’s anhydrous hydrogen fluoride technology allows phosphoric acid manufacturers, who operate in a highly price sensitive industry, to generate a high value-added co-product for the first time.
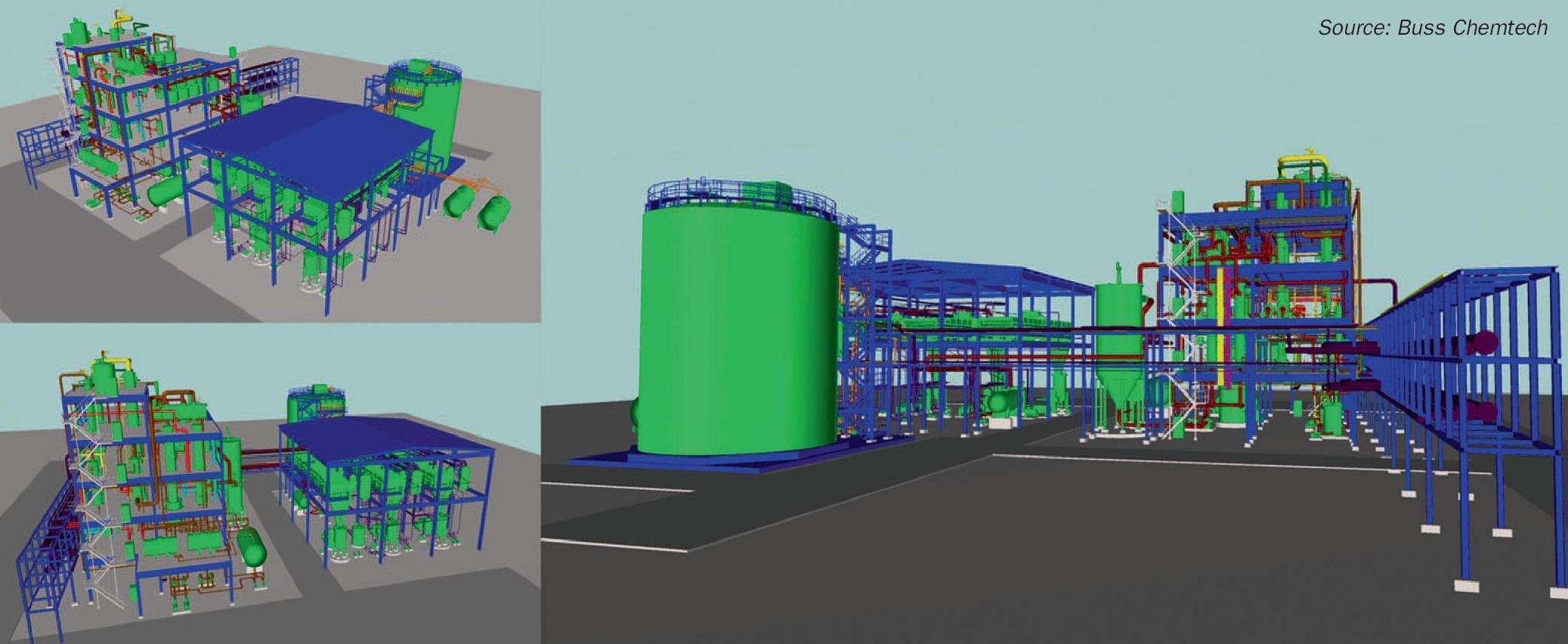

The anhydrous hydrogen fluoride (AHF) process
On arrival at the AHF plant, the FSA initially undergoes a concentration step. The absorption of SiF4 is used to raise the FSA concentration from approximately 18-24 weight percent to levels above 45 weight percent. Silica is also precipitated and filtered from the concentrated acid solution at this stage.
The concentrated FSA is then pumped to a reactor where it is contacted with sulphuric acid. As a consequence, HF and SiF4 form and are separated. Following on from this, the crude HF is condensed and purified, while the SiF4 is routed back to the initial concentration step to concentrate the FSA. The diluted sulphuric acid generated is stripped of residual HF within a stripping column, using steam and air, before being recycled back to the phosphoric acid plant.
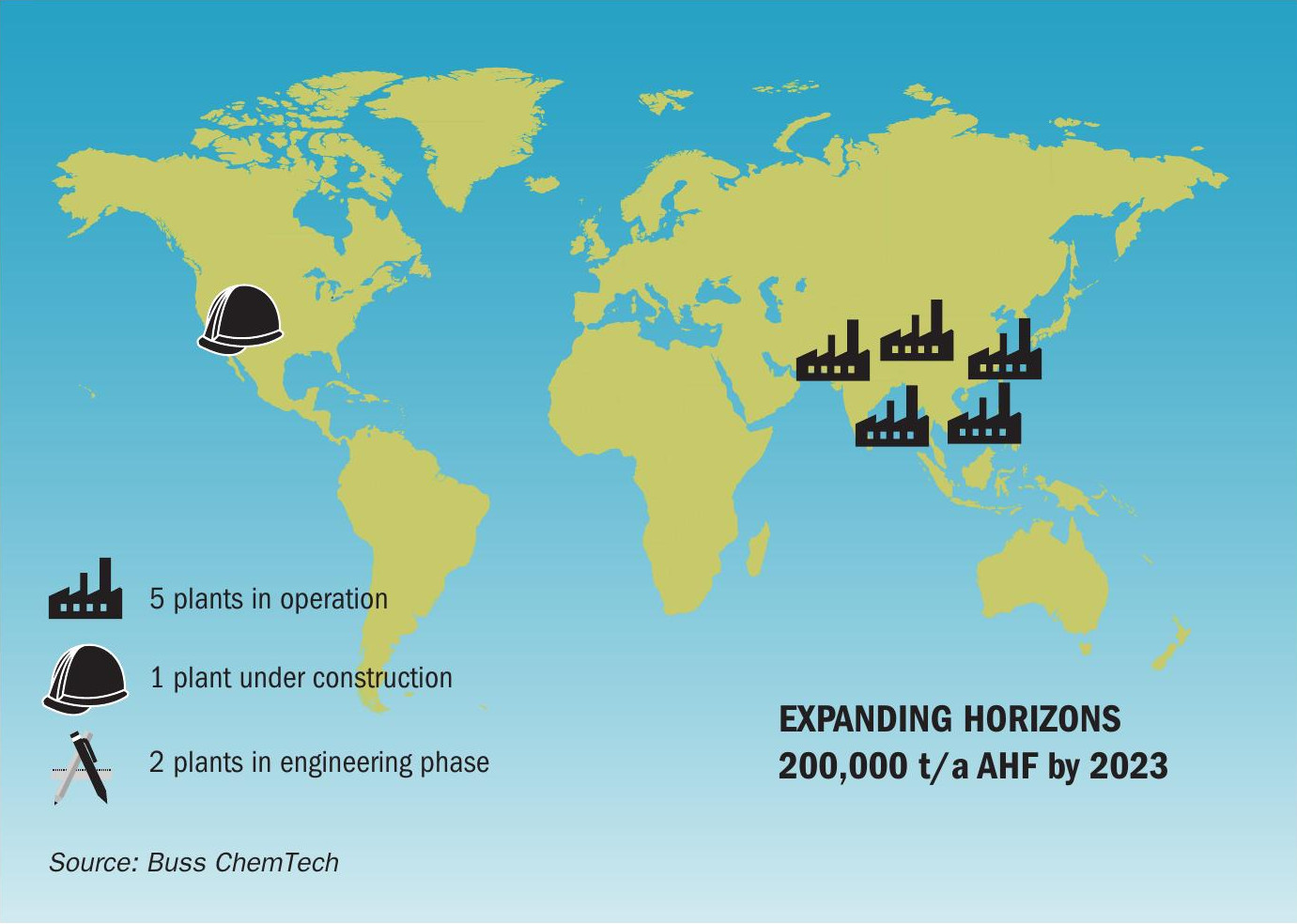
The AHF production plant has to be attached to and integrated with the phosphoric acid plant to close the sulphuric acid and water process loops (Figure 2).
Commercial installations
BCT first commercialised FSA-to-HF conversion technology in the early 2000s. The company subsequently signed a contract with Chinese phosphate producer Wengfu (Group) Co Ltd to supply the first industrial plant in February 2006. Project engineering began in mid-2006 and was followed by two years of construction which ended with the commissioning of the AHF plant in mid-2008.
Regular communication between Wengfu and BCT, following on from this successful first AHF project, ensured that new developments in process design, construction materials and plant operations continued to be implemented. Currently, Wengfu operates five BCT-constructed AHF plants, with a sixth under-construction plant due to commence operation in late 2022 (Figure 3).
BCT signed the first AHF project contract outside China with PCS Phosphate Company, a PotashCorp subsidiary, in 2017. This US-based project has continued in phases after Agrium and Potash-Corp merged in 2018 to form Nutrien, with Arkema also participating as the HF consuming partner. The project, located at Nutrien’s Aurora site in North Carolina, is now nearing completion and is expected to be commissioned in coming months.
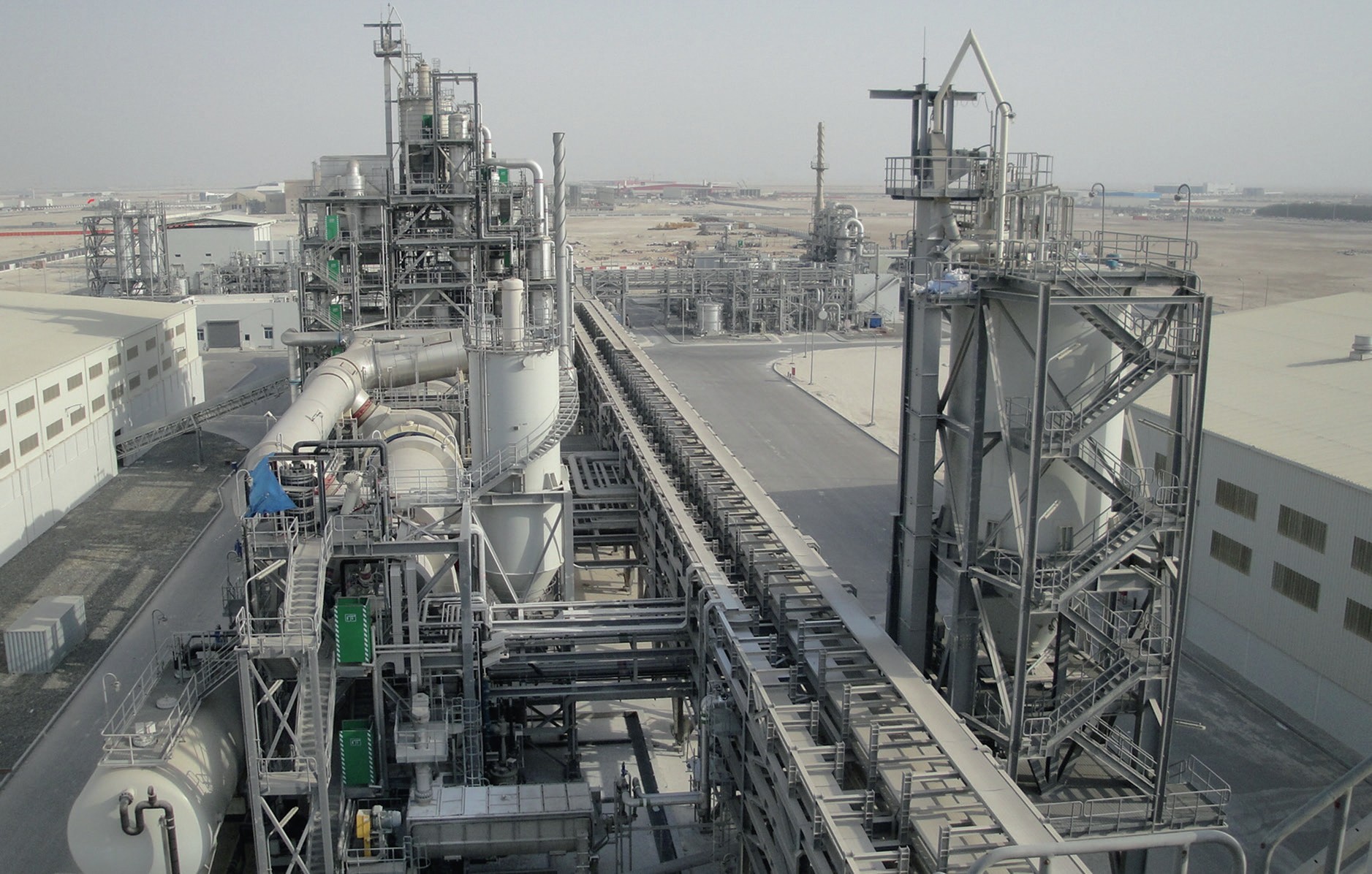
BCT also signed a contract with another renowned fertilizer company in 2020. This project is expected to be commissioned by mid-2023. Combined, the total global capacity for all the FSA-to-HF technology projects mentioned above will have reached more than 200,000 t/a of AHF by 2023.
Comparison with the fluorspar (CaF2 ) route
Traditionally, HF has been produced by reacting fluorspar (CaF2 ) with sulphuric acid. Indeed, since the 1960s, Buss ChemTech has completed more than 30 plants globally based on its proprietary technology for the CaF2 route.
The FSA process, meanwhile, also needs sulphuric acid, but only as a dehydration medium, meaning it can be sent back to the phosphoric acid plant. This makes the overall economics of the process more attractive in terms of operational expenditure (opex).
The payback period for a traditional HF plant may exceed 10 years at current CaF2 price levels. This, however, can be reduced to just 3-4 years by switching to the FSA route. While the investment costs (capex) are similar for both process routes, operation and maintenance are simpler for the FSA process
Importantly, FSA-to-HF technology – by valorising a co-product – also checks all the boxes for sustainability. Moreover, it also adds indirect value, both for environmental protection and to the economy, by substituting for large amounts of CaF2 which would otherwise have been mined.
HF and its derivatives
HF is widely consumed by many industries and BCT technology offers a high purity product suitable for a wide variety of applications. BCT’s technology portfolio also covers the following HF derivatives:
- High bulk density (HBD) aluminium fluoride (AlF3 ) – see Figure 4
- Lithium fluoride (LiF)
- Lithium hexafluorophosphate (LiPF6 ).
HBD AlF3 is used in primary aluminium production. It reduces energy consumption by lowering the bath operating temperature, as well as acting to replace fluorine losses and maintain the cryolite (Na3 AlF6 ) ratio.
In contrast, LiF is most widely used as a flux in the production of ceramics, such as enamels, glasses and glazes. Similarly, it is also used in brazing and welding fluxes and molten salt chemistry in metallurgy.
Consumption as a raw material for LiPF6 production is another area of use. LiPF6 is used as an electrolyte ingredient in lithium-ion batteries. The demand for LiPF6 has increased tremendously in the past ten years due to the shift towards electric and hybrid electric vehicle manufacturing.
About Buss ChemTech AG
BCT is a well-established technology provider located in Pratteln, Switzerland. The company has a long history in the field of fluorine chemistry. This is in addition to capabilities in various gas-liquid reaction technologies and phosgeneation technology. When these are combined with the competencies in fertilizer technologies of its parent company Desmet Ballestra – including phosphoric acid, sulphuric acid, nitric acid and complex fertilizers – BCT can offer a comprehensive solution for the whole phosphate value chain.