Sulphur 396 Sept-Oct 2021
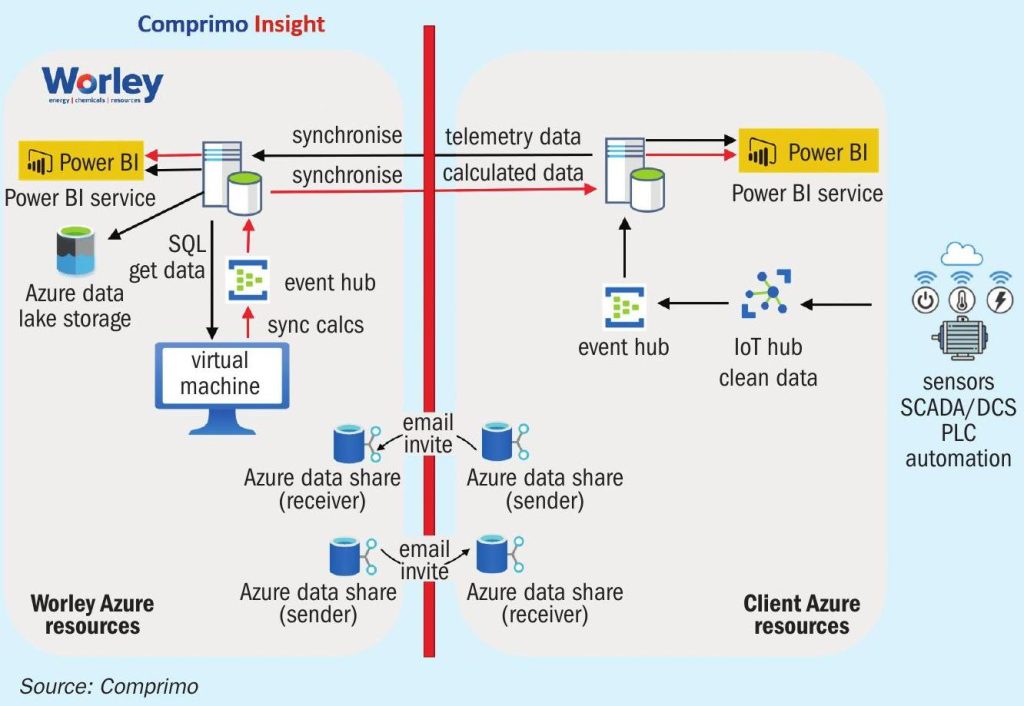
30 September 2021
Digital tools to optimise the operation of your sulphur recovery unit
DIGITAL TOOLS
Digital tools to optimise the operation of your sulphur recovery unit
Comprimo has recently launched two new solutions to make the most of existing data and to improve customer’s operations and customer knowhow: Comprimo Insight – an intelligent sulphur plant dashboard, and Comprimo Immerse – a dynamic sulphur plant simulator. In this article, Comprimo goes into the details of how Comprimo Insight and Comprimo Immerse are being implemented for its customers.
For over five decades, Comprimo has licensed gas-treating and sulphur recovery units (SRUs) for the oil and gas industry. Many of these licensees have chosen to engage with Comprimo in a so-called continuous services contract to stay in touch with Comprimo’s process experts and get advice in case of problems in the unit or on how to optimise their facilities with respect to emissions, catalyst lifetime and energy consumption. Also, in case of troubleshooting this provides a direct contact from the plant operations people to the assigned Comprimo technology experts. Traditionally, the communication related to the continuous services of the licensed units was done by sending screenshots with distributed control system (DCS) data, large data files in Excel and organising site visits for the Comprimo experts to interact with operations. During the site visits, sometimes a short training for operations was organised to highlight specific operational situations that had caused issues.
The sulphur recovery unit is not a profit-making unit in a refinery or gas plant, and is only required to obtain a license to operate from the local authorities with respect to sulphur emissions. Therefore, costly data transfer and 24/7 licensor support like there is for hydrocracker and fluid catalytic cracking units is typically not implemented. However, with the digital revolution, Comprimo recognised the potential for upgrading the current set of services to customers at an affordable price level. A quest for implementation of new digital services was described previously1 .
Comprimo has developed two tools that allow customers to understand their units better and provide the opportunity to improve the overall performance of the units. Using the first tool called Comprimo Insight, the historic data from the customer’s plant is periodically compressed as one-minute average values and shared with Comprimo via a secured methodology. The data is then automatically validated and processed and made available to the Comprimo technology expert for the interpretation of long- and short-term possible operational improvements. Key performance indicators are calculated automatically and trended as well as e.g., expected remaining catalyst life, energy optimisation, plugging, etc. This can be done without requiring customer data collection, communication, or site presence. Also, in case of troubleshooting, near real-time data will be available immediately and reasons for upsets can be identified. Remote assistance for start-up and optimisation of the units can also be organised on very short notice.
In addition to providing the ability to use the Insight tool, Comprimo also developed a training tool, called Comprimo Immerse, which mimics the operation of the SRU in a virtual environment. This tool can be fully customised to a customer’s DCS representation, thereby providing the ability to train operators and engineers on a digital replica of their SRU. The Comprimo Immerse tool can be used to reduce onboarding time of new operators and train operators to manage start-ups, shutdowns and upset situations in real time without impacting actual operations and related emissions.
Comprimo Insight
One of Comprimo’s customers was sending over a large Excel file with hourly average plant data from the whole past year and requested a detailed report about the performance of the units and optimisation recommendations. Processing all the data was done manually in Excel, preparing all the key performance indicators (KPIs), catalyst activity trends, virtual analysers, comparison with simulations, etc. The trends were copied to a Word report and the technology expert provided observations and recommendations for each trend. For a total of five plants, this was about four weeks of full-time work.
Comprimo recognised that for immediate assistance requests, this work method was not effective in providing correct and quick feed-back to the customer. After a few years of using this work method via Excel datafiles, cloud computing got the attention of the refinery world and Comprimo’s customer was interested to share its data in an automated way, not only for the sulphur recovery unit, but also for its other licensed units. Also at that time, Comprimo started efforts to develop a Proof of Concept (PoC) for data-sharing. Initially, the data was sent via a daily email that used Windows Scheduler and Excel-VBA to collect the data from the historian automatically. This method worked but was not very robust as it required a stable PC that was always on. And from a cyber security point of view, it’s not very elegant as there is no clear control of what data is sent over. The only positive, but also security wise weak point, is that it could be set-up by the customer unit engineer and Comprimo’s technology expert without heavy IT involvement.
Coincidentally, the customer in question started a project to collect all plant data from several sites in the cloud. Additionally, a PoC for data sharing via the cloud was set-up. Special licenses for the historian database were required to be able to transfer the data to the cloud, in this case Azure. Near real-time data, with a few minutes time delay, was available to Comprimo in read-only tables. Initially the data was processed on a single PC from one of the technology experts, but eventually Worley IT assigned an Azure subscription for Comprimo. Via this Azure subscription the data is processed in the Worley cloud environment and via the data-share utility, the customer has read-access to the results only. The schematic representation of the data flow and processing is shown in Fig. 1.
By sharing only the historian data and results from calculations and simulations, the intellectual property (IP) of the correla- tions and in-house design and simulation software can be kept with the licensor. The visualisation model, which includes the dashboard and trending of the data is done with Power BI. And since the visualisation model processes only data points, it can be shared with the customer, with the advantage that the customer engineer and the technology specialist use the same interface, which enhances communication. Although Power BI is not a common tool for customer engineers yet, it is used and known in most organisations. But in principle any visualisation tool can be used. It is even possible to feed back the results into the historian database and use the regular historian visualisation tools known to the customer engineers.
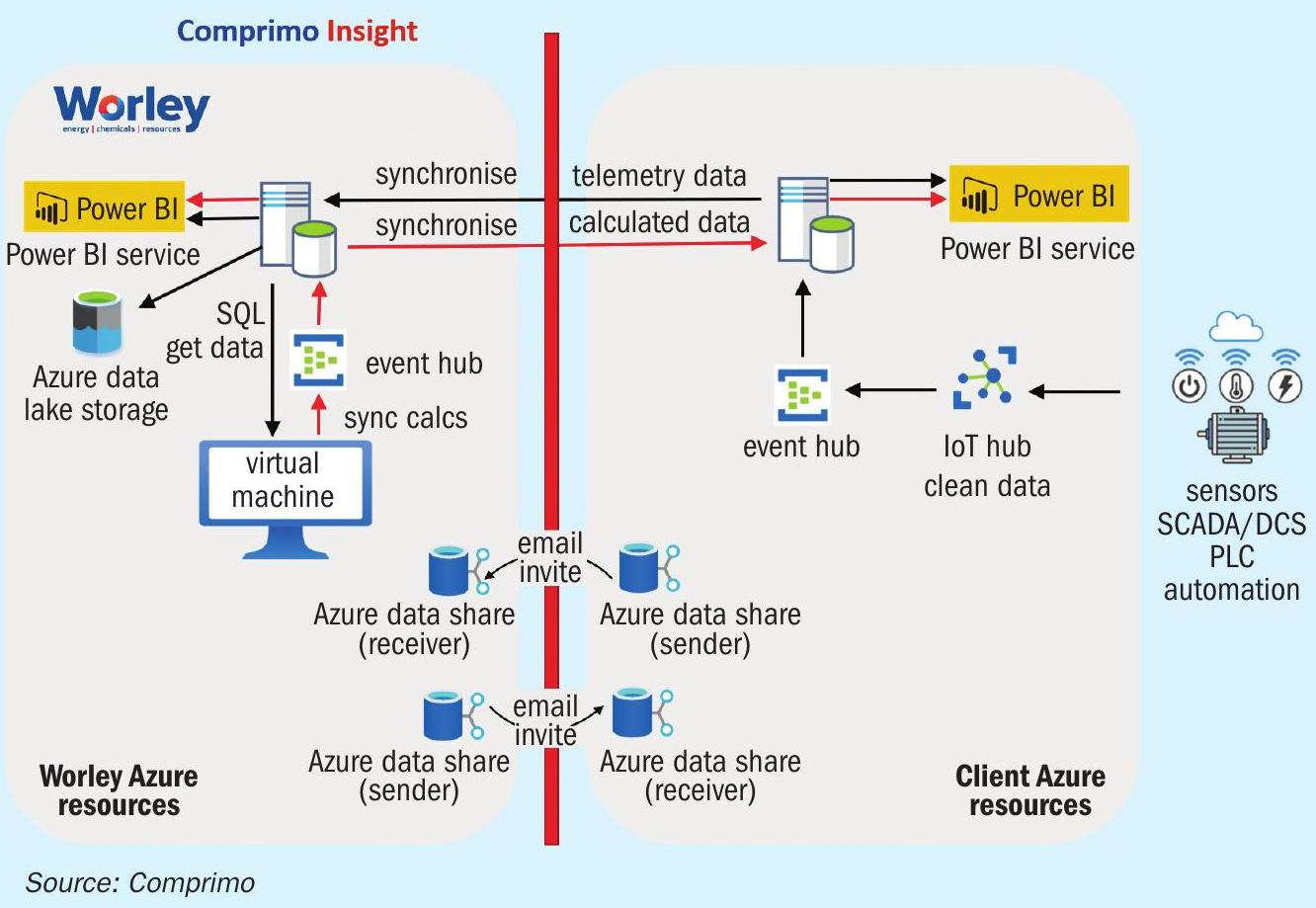
A snapshot of what the visualisation looks like is provided in Fig. 2, although this will be customised for each customer depending on the requirements.
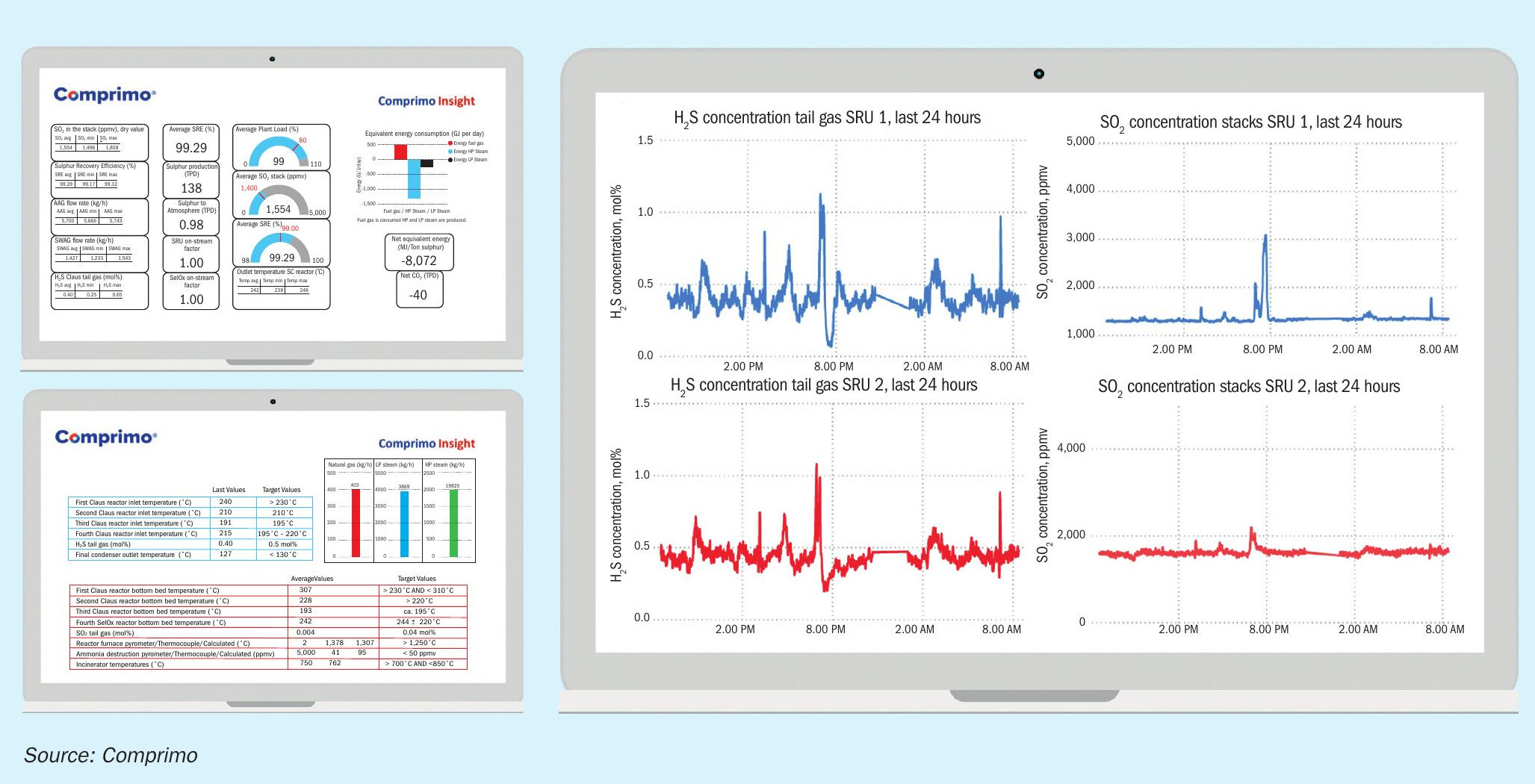
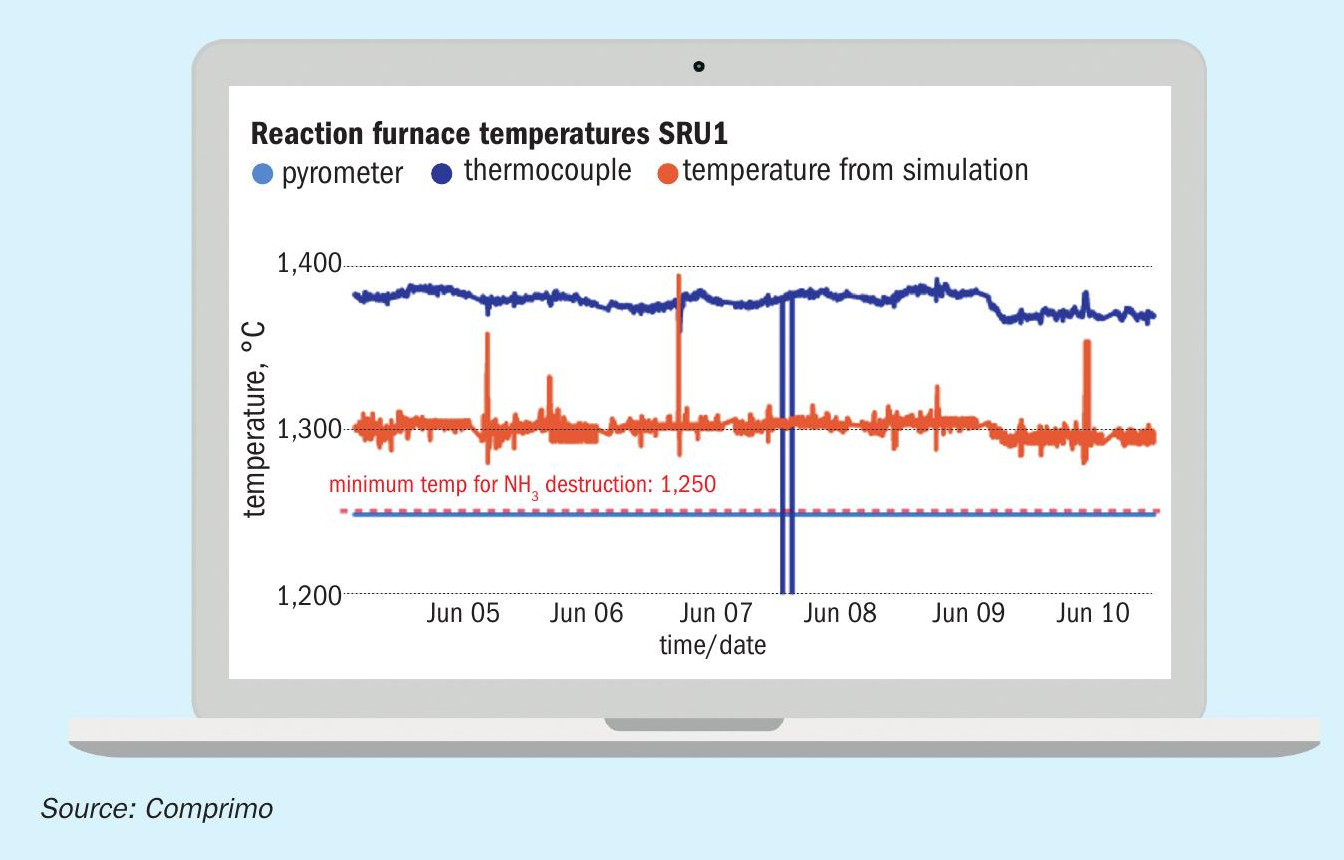
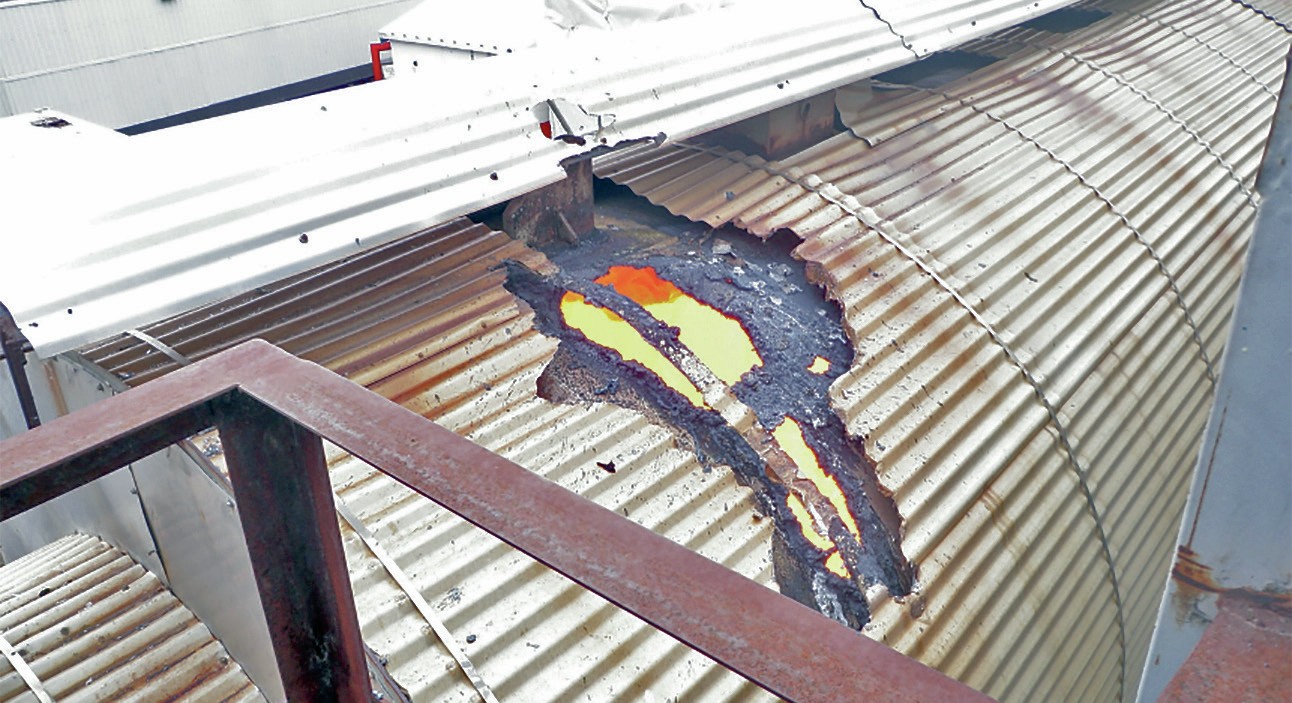
The visualisation is divided in a dashboard function, which gives the customer engineer a quick overview of the status of the unit. It also includes a trending part with all the KPIs and parameters that need to be followed over time to monitor the health of the unit. The customer engineer can use the dashboard to interact with operations in case there is a setpoint or parameter not within the normal operating window. Maybe there is a good reason that there is a deviation from the operating window, but the tool provides a way of monitoring and registering deviations. If the site has more SRUs, it is possible to compare operation parameters as shown in Fig. 2 for the H2S concentration in the tail gas and the SO2 concentration in the stack. This particular SRU line-up is a three stage Claus reactor followed by a SUPERCLAUS® reactor. As an example, in Fig. 2 there is indication of an upstream upset, because around 6 pm there is an H2S spike in both units at the same time. However, one of the SRUs has more difficulty to recover from the upset than the other one as is shown in the difference of height in the SO2 spike in the stack. This may have been caused due to tuning of the H2S feedback control loop. In both cases, the SO2 emissions were higher than allowed and local environmental regulations can be very strict when limits are exceeded.
Other features that have been developed are virtual analysers. Based on the plant data, some of the instrument readings, e.g., temperature in the combustion chamber or the H2S measured by the tail gas analyser, can be checked using specific algorithms or simulations. An example for trending the pyrometer and thermocouple readings next to the temperature obtained from simulation is provided in Fig. 3. The temperature obtained from simulation provides an independent method to verify the thermocouple and pyrometer, provided the flow measurements to the SRU are sufficiently accurate.
There have been incidents where incorrect temperature indications, especially during natural gas firing, have led to overheating of and damage to the combustion chamber as shown in Fig. 4. Alternatively, the temperature could be too low, leading to lack of BTEX or ammonia destruction, and catalyst deactivation or plugging of the unit respectively.
Other examples that have proven added value are:
- Trending a slowly increasing waste heat boiler outlet temperature, correlated to the simulated temperature. An increasing temperature is an indication of fouling and the temperature at the outlet must stay below 340°C to prevent excessive corrosion and early failures. By trending this correlation, a turnaround can be scheduled with more accuracy.
- Catalyst life-time trending allows for planning catalyst replacement, only when the predicted performance is below required before reaching the next planned turnaround.
- More and more parameters can be correlated when analysing the data as well as improving the visualisation to highlight certain trends that provide Insight into the health of the unit.
Some of the learnings from the first practical applications of Comprimo Insight are as follows:
- Each customer is unique in many aspects – the software they use, the work processes, the organisation, IT demands, and also the type of sulphur recovery processes. This requires tools such as Comprimo Insight, which offer a high degree of flexibility. The standard methodology for data handling in the Worley cloud has been standardised, however the interface with the customer with respect to data sharing and data visualisation will need to be flexible due to the different infrastructures set up by their IT.
- The customer unit engineer counterpart typically has little experience with data-sharing, cloud computing and difficulty in engaging the customer’s IT. It has been Comprimo’s experience that the biggest hurdle to overcome is support from the customer’s information technology experts. This is more evident in small sized refining companies.
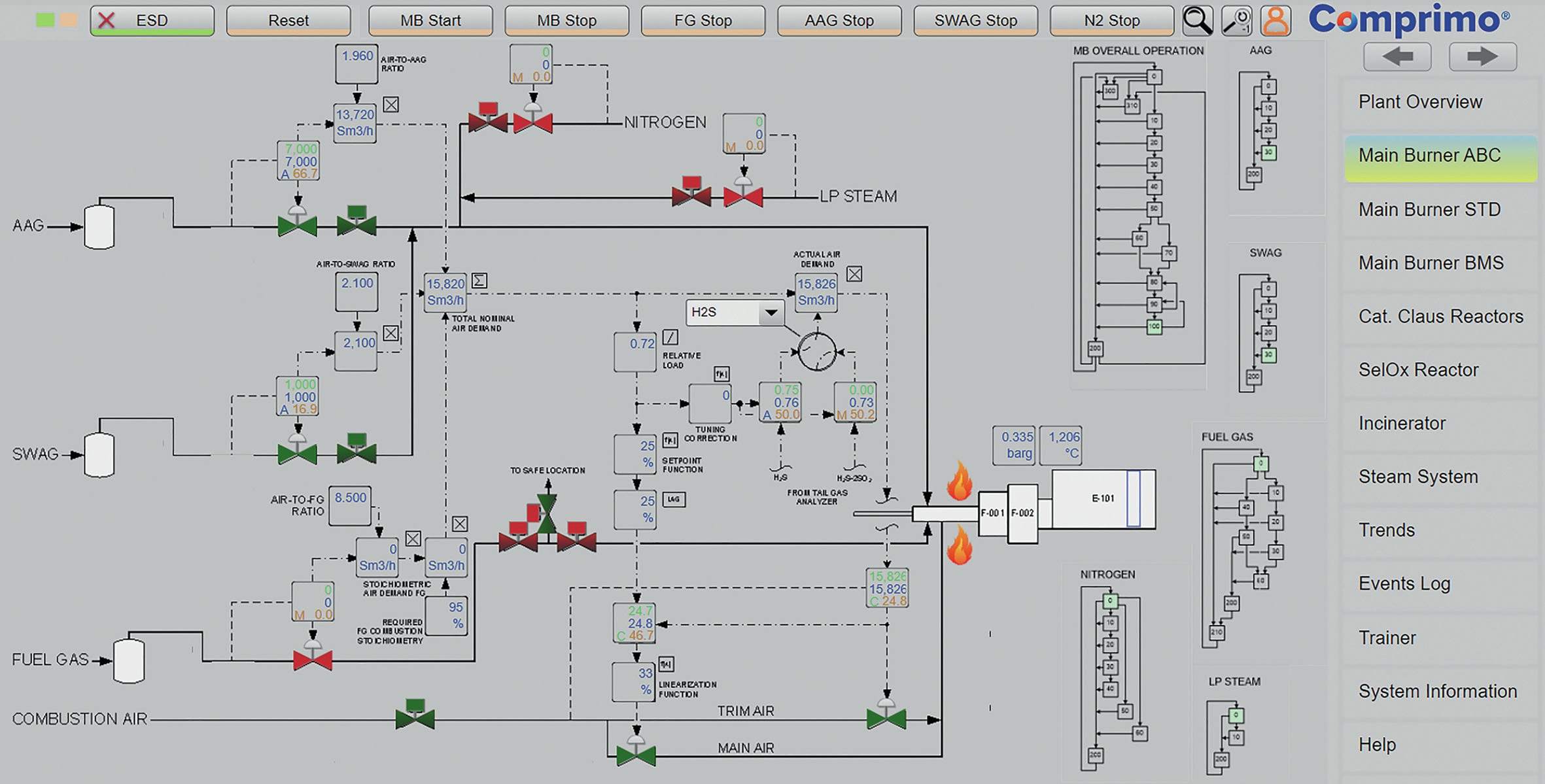
- The technology specialist must have a basic knowledge of cloud computing and have access to skilled IT people to set up and maintain the cloud systems. One of the main concerns that is brought from the customer is the cyber security of transferring data via the cloud. When one considers that credit card data is also processed in the cloud if purchasing goods in a webstore, this means that the cloud environment can be made very secure when using the right infrastructure, protocols, policies, and monitoring services.
- It is important to agree on who the owner of the data is and to formalise it in a contract. Preferably both parties are owners and free to use the data as needed within their own company.
- The data-sharing possibilities and cloud computing are evolving rapidly, and new features and services are developed all the time.
- It requires minimum effort to maintain the interface when using the right experts and tools for cloud computing and visualisations. There is a first-time investment required to discover and set up the systems and infrastructure. With the large volumes of cloud computing employed around the world, the costs are relatively low and make it possible to develop monitoring services at very affordable fees.
- With Comprimo Insight, the customer’s unit engineer and Comprimo’s technology specialist have a better connection to discuss optimisation targets, upsets, or special operating scenarios.
It is also a perfect interface to educate the customer’s staff on the specifics of the licensed process.
Moving forward, Comprimo is looking at the further improvement of the data processing, which is currently done with Excel on a virtual machine in the Azure cloud. This solution will be upgraded soon using the latest technology, e.g., Azure Functions. Also, the visualisation needs focus to improve performance and especially using techniques that can load the data faster. Besides the mentioned outstanding improvements, it is important to realise that a certain minimum continuous effort will be needed to develop, improve, and use latest technologies to maintain the systems. Additionally, each customer has different requirements on how the data is delivered and over time the customer engineer may want to modify the visualisation to fits its needs better.
The dataset may be large enough to train the models for machine learning once data has been flowing continuously for some years. It is expected that machine learning can have added value in preventing trips when data from upstream units, e.g., ARUs and SWSs, is available and when selecting the optimum setpoints for the reactor temperatures to meet e.g., SO2 emission requirements at minimum steam consumption. When maintenance inspection results are included in the dataset, even predictive maintenance is on the horizon.
In summary, with Comprimo Insight it is now possible to share data in a secured environment and monitor and optimise licensed SRUs. Further improvement of the data processing and visualisation methodologies is ongoing. And it is expected that in the near future the harvested datasets can be used for further analysis and optimisation strategies, using the latest machine learning technologies.
Comprimo Immerse
Comprimo provides operator training for their licensed sulphur recovery units to customer operations and unit engineers. The theory of the sulphur recovery process and all specific features of the unit installed at the customer’s facility are explained in detail. This includes attention to the details of equipment items and what is required during operation and a full explanation of the controls and safeguarding of the unit.
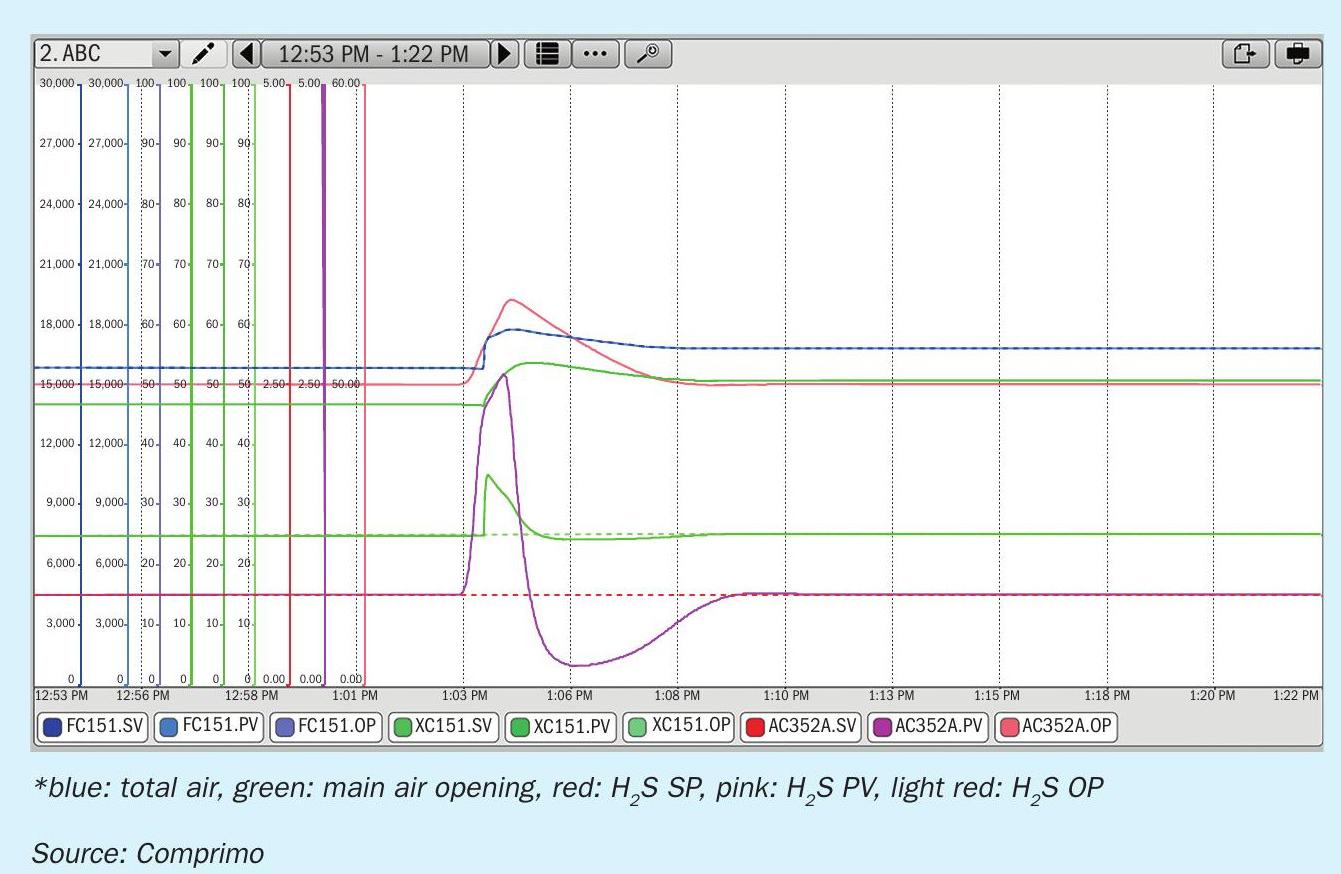
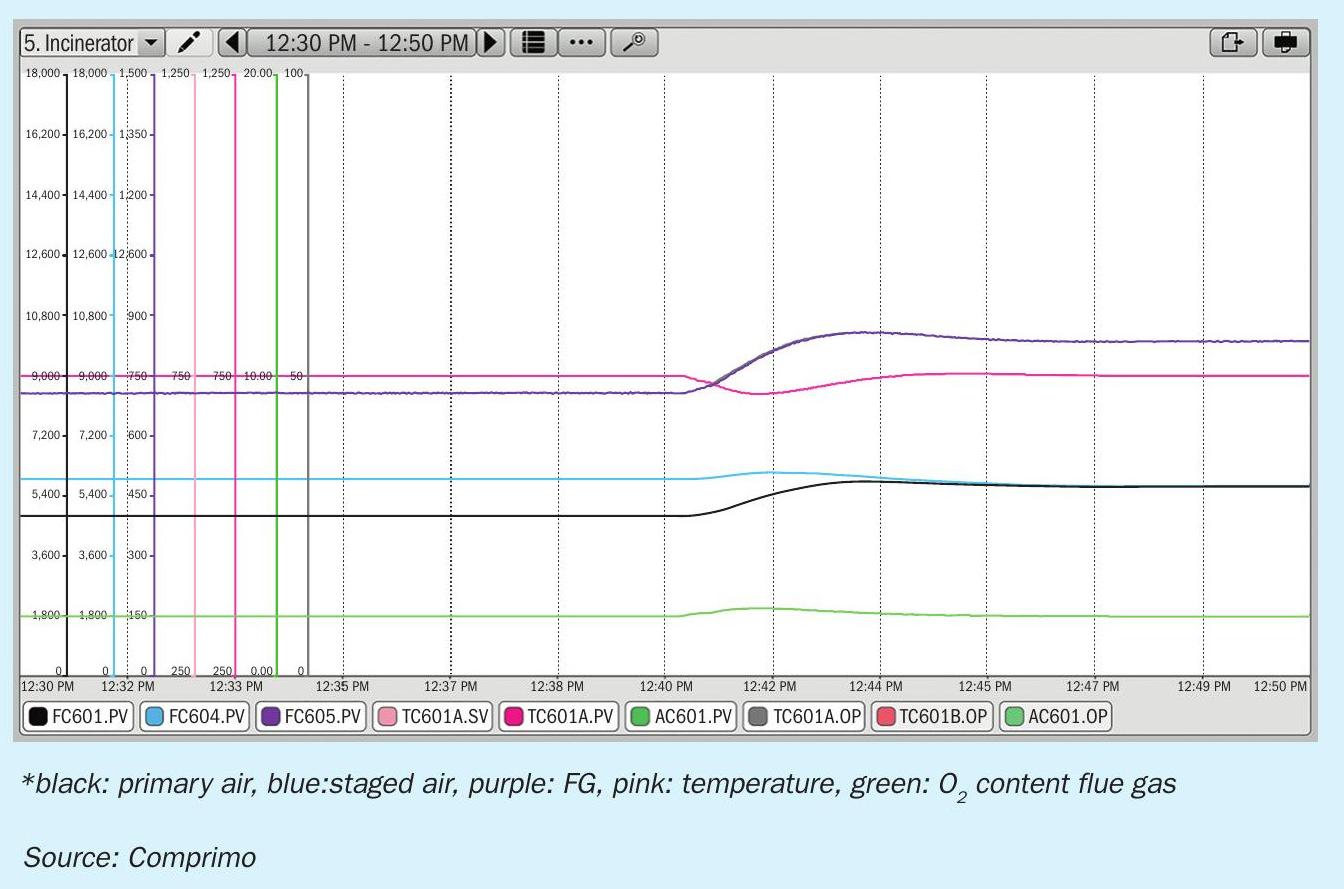
From experience, Comprimo realised that traditional classroom training did not cover all the dynamics of the process, especially the more complex loops like the burner controls which were quite difficult to get across so that they were fully understood by the audience. As a result, Comprimo developed an operator training simulator tool called Comprimo Immerse that allows a more dynamic approach to operator training.
Comprimo Immerse provides a simulation tool for an SRU (could be in a SUPER-CLAUS® configuration or other tail gas technology) in which the key process controls are implemented (advanced burner control, selective oxidation control, incinerator burner control), as well as the various safeguarding items (as per cause and effect diagram) and the start-up sequences with the required permissives.
The interface uses a representation of the DCS screens, with the various controllers showing setpoint (SP), process value (PV) and output (OP). It also shows in which mode the controller is operating (MANUAL/AUTO/CASCADE). This will give a clear overview and good representation of an SRU and of how the unit is controlled.
At first, Comprimo Immerse will be used to explain the controls in more detail including the dynamics of the system, in which parameters are changing due to a variation in for example the feed gas flow. It is also possible to introduce a change in feed gas composition to monitor the behaviour and response of the system in case it is in fully AUTO-CASCADE control but also what the impact is in case a controller is not in the correct mode. Each step in the control can be explained and followed repeatedly, without any consequences to an actual operating unit. The worst scenario that can happen is the activation of the safeguarding system, which will stop the simulated burner (low low air flow to the burner activating closure of air supply and acid gas supply to the burner).
The tool is also used to explain the safeguarding of the unit by simulating specific scenarios such as low acid gas flow, low air flow or high H2 S content to the selective oxidation stage. As per the cause and effect diagram, each scenario has its consequences depending on the actual operating mode of the unit (e.g. the difference when the burner is operating on “acid gas only” versus “co-firing” mode). When an initiator is activated, the required actions are taken by the system and the specific on/off valves are closed (like in a real unit).
When a good understanding of the controls and safeguarding is achieved, the next step is to explain the different sequences applied nowadays within the Comprimo SRU designs. For example, the ignition sequence of the thermal oxidiser burner is fully automated from purging of the burner up to the admission of fuel gas into the burner and successful ignition. The system check for the required permissives is part of the tool, so that a full understanding of the sequences and permissives is achieved as well.
Included in the tool is the ability to create trends of the various parameters. This means that the behaviour can be monitored as a function of time as well (as is done with a real unit to monitor the operation and analyse the behaviour of the system).
This gives operations detailed insight of the behaviour of the system and adds to the understanding of how the unit can be operated and controlled.
Comprimo Immerse can be integrated as part of the customised training where the theoretical training material is combined with the dynamic simulation tool for further explanation.
During the training, it is possible to schedule time to allow operations to bring in scenarios that they have come across which can then be simulated to see different responses and reactions on how it could potentially be handled better in the future.
All of this can be done in a safe environment disconnected from the real unit with freedom to play with the system.
The Comprimo Immerse tool can also be made available to the customer after the operator training, so that operations can continue working within the simulated environment. This will help to improve their understanding of the system and gain further confidence in the actual controls.
An example of how the Comprimo Immerse tool could be used to monitor the response of the control system is provided below. Fig. 6 shows the graphs of the trends taken during an upset situation of the plant.
The main burner was operating on AAG and SWAG with the tail gas H2 S concentration at a stable level. The SUPERCLAUS® stage was also in operation. By mistake, the total air controller was switched to MANUAL. As long as the unit was operating with a stable feed flow and composition, this would have no further consequences.
At around 13:02, the AAG flow to the main burner was increased from 7,000 Sm3 /h to 7,500 Sm3 /h. As the air supply was in MANUAL and thus did not follow the change in feed gas flow, the H2 S content in the tail gas showed a very rapid increase after about two minutes. Within one minute, the H2 S content exceeded already 2 vol-%. In the meantime, the operator was notified that something was not normal. He noticed the air control in MANUAL and switched it back to CASCADE. This gave a shot of air to the burner. With the increase in H2 S, the analyser controller started to increase its output as more air was required by the system. When the H2 S started to drop, the controller started to reduce its output again.
The thermal oxidiser was operating with all controls in the correct mode (AUTO-CASCADE) at a temperature of 750°C. After achieving stable operation on the main burner as well as on the thermal oxidiser, the SUPERCLAUS® stage was taken into operation. As a consequence, the amount of combustibles in the tail gas to the thermal oxidiser were reduced. This resulted in a requirement to increase the fuel gas flow to the thermal oxidiser to maintain the required temperature. With the increase of fuel gas flow, the air flow to the burner was increased automatically as well.
Conclusion and future outlook
Comprimo Insight and Comprimo Immerse add a comprehensive service to sulphur recovery operations. A combination of the two tools can be used to improve the understanding of the unit as well as provide the opportunity to work with the licensor to optimise the performance of the unit. Comprimo Insight provides real-time ability to address operating issues with the licensor and clear and accurate monitoring of the unit. Comprimo Immerse provides the ability to improve the training methods available to the operators currently, as well as the option to expose them to non-routine operating scenarios in a safe environment. By using the Comprimo Immerse simulation tool, new operators can be trained more effectively, and experienced operators can get refresher training by using an interactive tool that can mimic operationally experienced situations.
Reference