Nitrogen+Syngas 373 Sept-Oct 2021
30 September 2021
Latest catalyst provides more methanol for longer
METHANOL SYNTHESIS CATALYST
Latest catalyst provides more methanol for longer
Johnson Matthey’s latest methanol synthesis catalyst, KATALCO™ 51-102, was introduced in 2018 to offer improved catalyst stability and therefore higher end-of-life activity and extended lifetimes than conventional methanol synthesis catalysts. Since launch, KATALCO 51-102 has been successfully installed in two methanol plants and a third is planned for later in the year. In this article Johnson Matthey provides an update on the proven performance of KATALCO 51-102 during lab and pilot scale testing as well as in customer plants. The application of catalysts made using the KATALCO 51-102 technology for methanol synthesis via new ‘green’ routes, such as using captured and purified CO2 in conjunction with ‘green’ hydrogen, is also discussed.
Many catalysts have been developed and successfully commercialised by JM (previously ICI) since the development of the original copper-based industrial catalyst and low-pressure process back in the mid-1960s. Detailed understanding of the sintering mechanism and the role of the structural promoters in the CuZnAl catalysts has led to the development of KATALCO™ 51-1021 , which was introduced in 2018. KATALCO 51-102 offers higher sustained activity over time compared to any of its predecessors. The improved performance was achieved via the addition of a stability promoter to the formulation. This change to the formulation is relatively minor and has no impact on further catalyst characteristics such as selectivity, strength, or attrition resistance.
Although not discussed in detail in this article, the structural ‘backbone’ of the catalyst is also crucial to a long, stable catalyst life without significant increases in pressure drop. Simply ‘adding more copper’ to increase activity can have a detrimental effect on pellet stability and JM’s formulation and manufacture is carefully designed to avoid issues with pressure drop increase in service. This is unchanged between KATALCO 51-102 and previous generations.
Synthesis of methanol from CO2 (potentially captured directly from the atmosphere or from streams that would otherwise be emitted to the atmosphere) and hydrogen streams is attracting much attention and presents some additional challenges to the catalyst. In contrast to traditional syngas streams, the higher CO2 leads to high concentrations of water in the process, putting additional demands on the catalysts’ hydrothermal stability. JM’s conventional catalysts have demonstrated lives of around four years and stable performance in such duties, but materials developed using the same scientific principles as KATALCO 51-102 demonstrate further advantages in such conditions.
In this article the properties and benefits of KATALCO 51-102 are reviewed and evidence is provided of its proven performance at lab and pilot scale testing as well as in customer plants, since its launch in 2018. The performance of catalysts made using the same technical principles as KATALCO 51-102 under CO2 to methanol conditions is also discussed.
Methanol synthesis catalyst deactivation
The deactivation of a catalyst over time ultimately determines the catalyst life and end-of-run plant rate. The two main mechanisms that drive the deactivation of copper-based catalysts used in the synthesis of methanol are sintering and poisoning, sintering being the dominant process in the majority of applications. It is generally accepted that the activity of a methanol synthesis catalyst is directly proportional to the active surface area, which is that of metallic copper. Other factors in the catalyst may also play a role in defining the activity, such as copper-zinc interactions2,3 , however, the degree of copper dispersion is universally accepted as one of the main descriptors for catalyst activity. Therefore, as a general rule, a good methanol synthesis catalyst requires high copper surface area, which is achieved by having small nanoparticles of copper, typically 2-10 nm. In order to reach a reasonable lifetime cycle and the desired productivities in a plant, these nanoparticles should be as stable as possible. However, the small copper crystallites present have a high surface to volume ratio and most of the copper atoms occupy high energy surface sites. There is therefore a significant thermodynamic driving force towards sintering; small particles become larger in order to reduce this surface energy4 . Moreover, the relative low melting point of copper makes this metal prone to sintering, since at the temperatures required for methanol synthesis the copper atoms can become mobile.
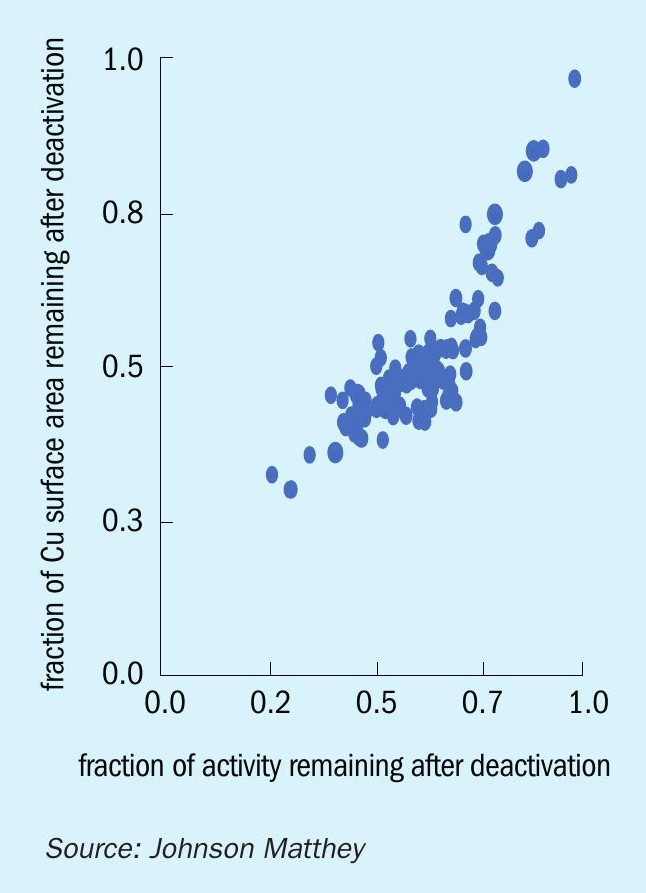
As sintering requires the physical movement of atoms or clusters, it is an activated process and therefore the rate of sintering will increase with increasing temperature. Temperature is, in fact, one of the dominant variables leading to sintering, although other factors such as gas composition may also be important. The rate of sintering and therefore deactivation of methanol synthesis catalysts normally follows an exponential decay, in which the rates are faster at the start of life of the catalyst, when the copper surface area is the highest, and slows down as copper crystallites become larger and the driving force for sintering decreases. For the greater part of the catalyst operating life, the catalyst activity is significantly lower than that of the fresh material. Once the activity is too low to maintain the required level of productivity, a catalyst change-out will be required. There is therefore a significant incentive to have a stable catalyst, such as KATALCO 51-102, which minimises the impact of thermal sintering and thereby improves the productivity and life of methanol synthesis catalysts.
The science behind KATALCO 51-102
Most industrial methanol synthesis catalysts are composed of copper, zinc and aluminium. The current generation of KATALCO 51-series methanol synthesis catalysts also contains magnesium. Copper oxide is the main component (~64 wt-%) and is the active phase upon reduction to metallic copper; the reduction is carried out in situ in the methanol converter before the charge is brought into service. The dispersion of copper is directly related to the activity of the catalyst as reflected by the relationship between copper surface area and remnant activity shown in Fig. 1.
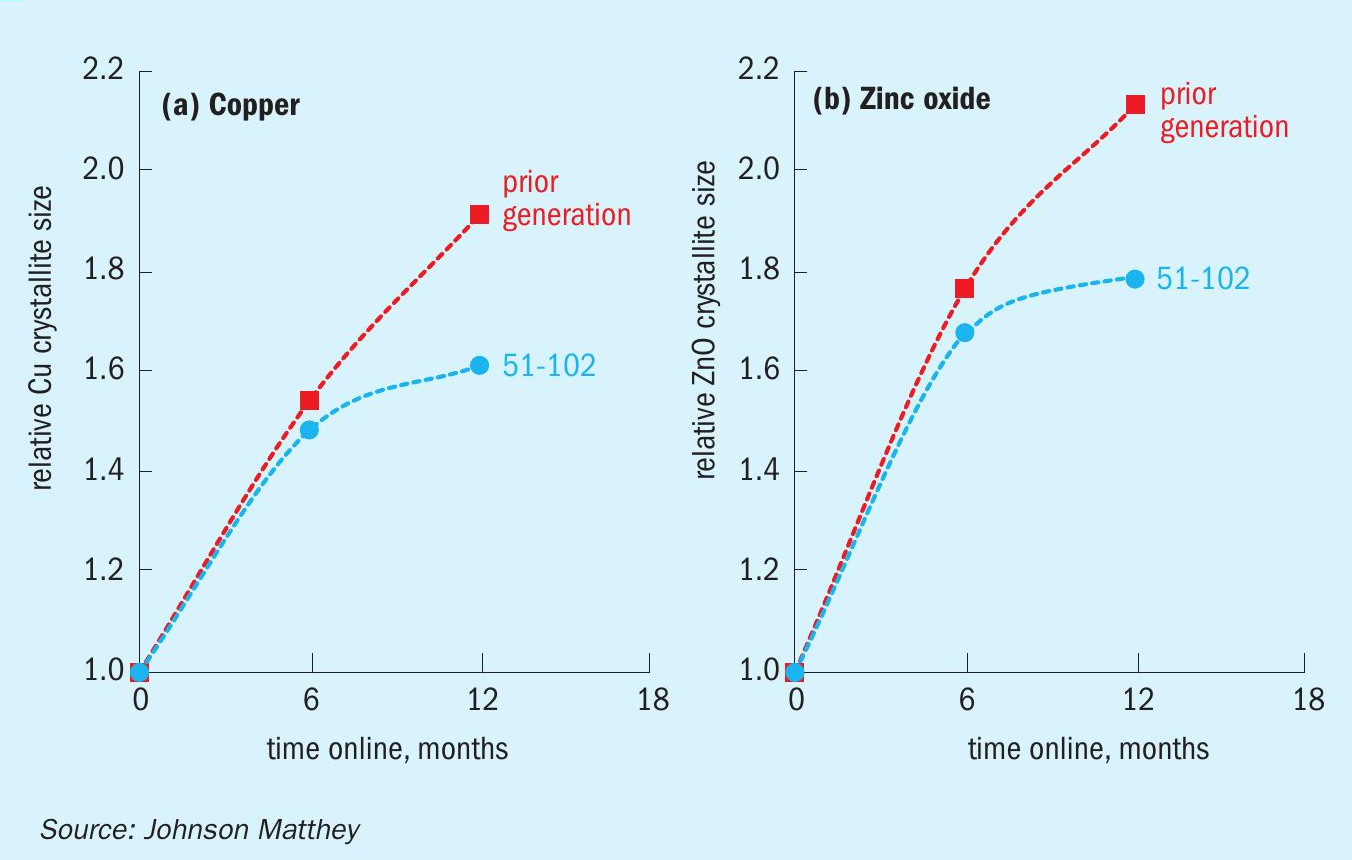
While a high initial activity is desirable, the retention of activity/copper dispersion over time is far more important. Zinc oxide (ZnO) and aluminium oxide (or alumina, Al2 O3 ) are included in the formulation with the main purpose of stabilising the copper phase. The alumina also gives physical strength to the pellets of catalyst.
There is a close interaction between copper and zinc, which starts during the manufacturing of the methanol synthesis catalysts. During the precipitation process a mixed copper-zinc hydroxycarbonate phase is formed as an intermediate, that upon decomposition to oxides by heating, generates small copper crystallites in close contact with small zinc oxide crystallites that help to stabilise the copper. Zinc oxide also acts as a sulphur guard, to provide further protection in case of sulphur slipping through the purification section and reaching the methanol converter. It also helps neutralise acid sites and stabilise the alumina phase. Acid sites may promote the formation of dimethyl ether (DME) via dehydration of methanol, affecting the selectivity of the catalyst. The alumina phase is stabilised by zinc via the formation of zinc aluminate during service, which is a more hydrothermally stable phase than alumina.
Magnesium oxide (MgO) is incorporated to maximise the initial dispersion of copper and therefore boost the initial activity of the methanol synthesis catalysts. The increase in copper surface area in Mg-containing copper-based catalyst can be of the order of 20% versus a Mg-free variant.
A detailed understating of these complex multicomponent catalytic systems at start-of-life and during service has led to a new optimised and patent pending formulation5 , in which a small amount of a fifth component, silica, is added as a stability promoter. This new formulation is commercialised as KATALCO 51-102, which provides improved activity in service via a higher retention of initial copper surface area over time when compared with the conventional CuZnAlMg systems.
The addition of SiO2 slows down the rate of copper and zinc sintering. As mentioned above, zinc crystallites of similar size to those of copper are fundamental in stabilising the copper phase. This is better exemplified in Fig. 2, where the relative crystallite size of copper and zinc oxide with time online are shown for KATALCO 51-102 in comparison with a Si-free formulation. In the next section the superior performance of KATALCO 51-102 over time is analysed, proving the benefits expected due to stabilisation of the active component.
KATALCO 51-102 performance
KATALCO 51-102 has been extensively evaluated, during its development and after launch for quality purposes. Approaching 100 batches of KATALCO 51-102 have been manufactured since 2018, all presenting the expected performance in terms of activity over time as well as pellet robustness and integrity.
Lab testing
Lab testing protocols have been specially developed by our R&D team to evaluate the long-term performance of KATALCO 51-102, which is the key benefit of this new product. Methanol synthesis catalysts may be online for many years, however, lab testing of catalysts for such long periods of time is impractical and economically unfeasible. It is therefore paramount to accelerate the deactivation of the catalyst in a controlled manner during lab testing to predict the long-term performance of the catalysts. The deactivation of the catalyst can be accelerated during lab testing by increasing the temperature above the operating temperature expected for methanol synthesis; this temperature should be such that the sintering of the copper is accelerated, but the mechanism of sintering should not be affected. In other words, the activation energy for sintering when using accelerated deactivation conditions should be the same as that when the material is subjected to milder deactivation conditions. Testing protocols for accelerated deactivation that fulfil that criterium were defined and validated by carrying out tests at several deactivation conditions in JM’s accelerated aging rig. Deactivation models that predict the performance of KATALCO 51-102 at different plant conditions were also developed, which enable the link between the accelerated aging results and the real-world performance.
The accelerated aging rig is a multi-reactor laboratory-based automated microreactor system that was designed to evaluate the effect of sintering upon the deactivation of methanol synthesis catalysts in the absence of poisons. A set of data for KATALCO 51-102 from the accelerated aging rig at different accelerated deactivation conditions is shown in Fig. 3. The data set is shown in terms of relative activities over time online for KATALCO 51-102 vs. a prior generation catalyst. All the relative activities shown in Fig. 3 are above unity at any time, indicating that methanol is made faster over KATALCO 51-102 than with the prior generation catalyst. These relative activities increase over time at all conditions as a result of KATALCO 51-102 being more stable than the prior generation catalyst. The stability benefit is better reflected in Fig. 4, where a smaller loss in activity over time at a set of accelerated deactivation conditions can be seen for KATALCO 51-102 than for the prior generation material.
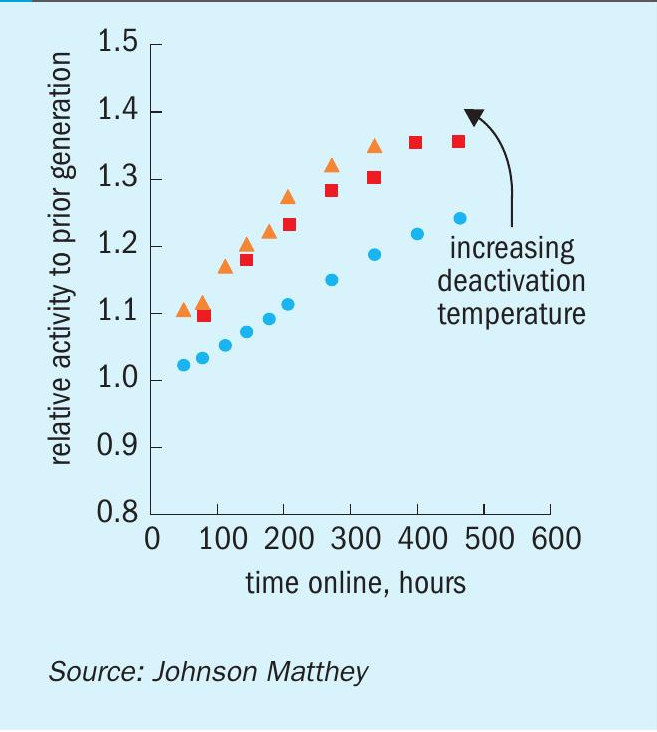
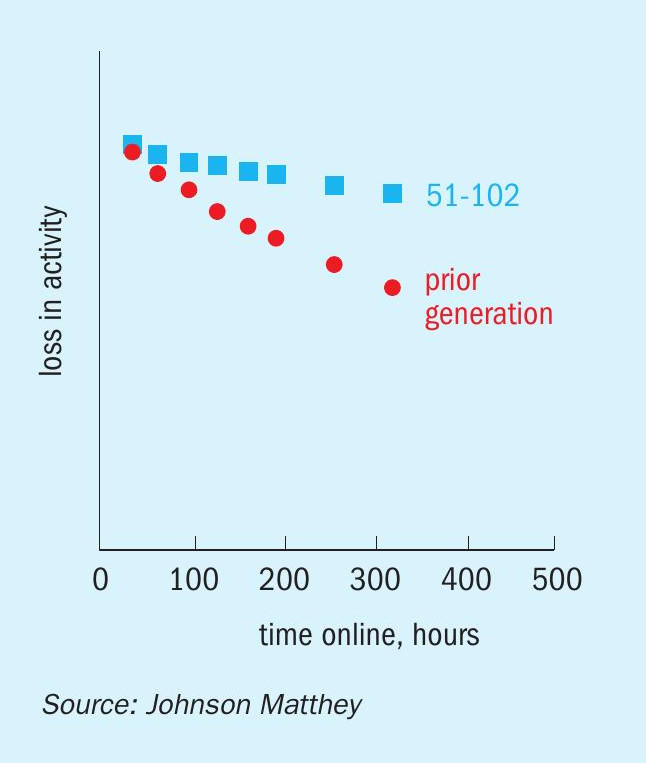
It is worth pointing out that the stability benefit of KATALCO 51-102 vs. the prior generation catalyst is greater as the deactivation conditions are harsher, as shown by larger relative activities as the deactivation temperature is increased (Fig. 3). This is due to a lower dependence of the deactivation rates on deactivation conditions for KATALCO 51-102 in comparison to the prior generation catalyst, as reflected by the relative deactivation rates at different deactivation temperatures in Fig. 5.
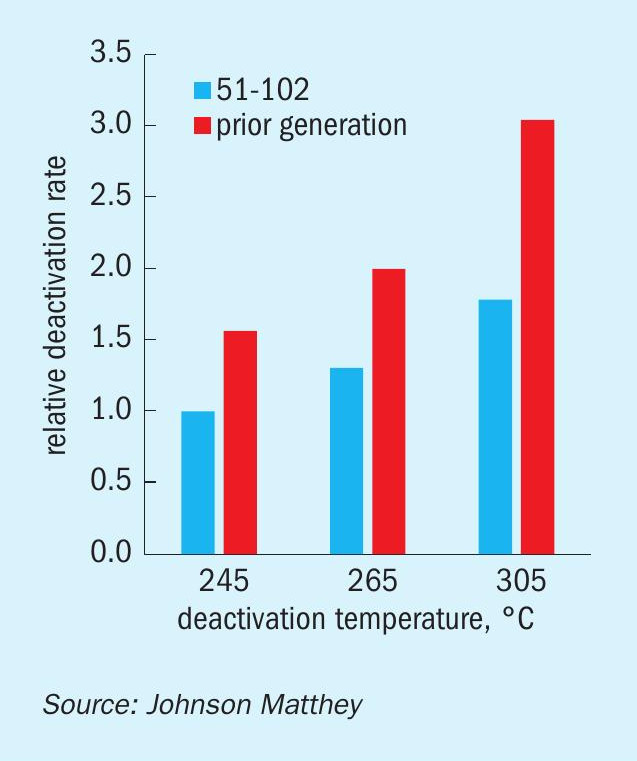
As a standard part of the JM quality assurance and control procedure, all batches of KATALCO 51-102 are carefully sampled and analysed for the key properties that define the performance of the catalyst such as chemical composition, density, impurity levels, copper surface area and strength (among others); all these properties are part of the specifications of the product and the defined values must be met. Moreover, a significant number of batches are randomly selected and further tested for reduced crush strength, activity/stability and a second measurement of copper surface area, to further corroborate the relationship between the established specifications of the products and their catalytic performance. The performance of KATALCO 51-102 batches has been consistent and clearly shows the stability benefit over the prior generation catalyst, as reflected by the relative activities for the randomly selected samples shown in Fig. 6, measured after subjecting the catalysts to accelerated deactivation conditions for a defined period of time.
The strength, attrition resistance, shrinkage on reduction, mass loss on reduction, copper loading and zinc loading for KATALCO 51-102 are comparable to the prior generation of catalysts from the KATALCO 51-series, these properties are not changed by the small addition of silica to KATALCO 51-102. While the addition of silica has not caused any change to the physical properties of the catalyst pellets, work on pelleting during the development of KATALCO 51-102 has helped JM improve the strength of a number of products, as shown by the increase in mean horizontal crush strength (MHCS) for catalysts from the KATALCO 51-series in Fig. 7.
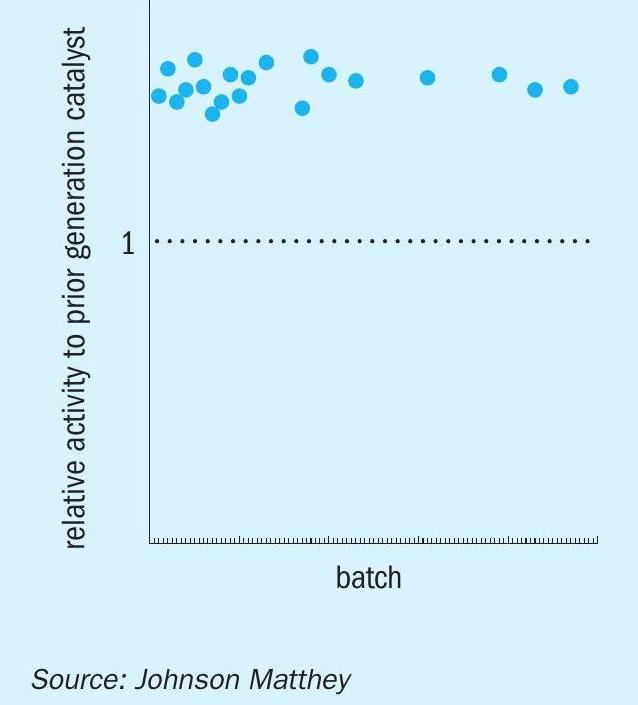
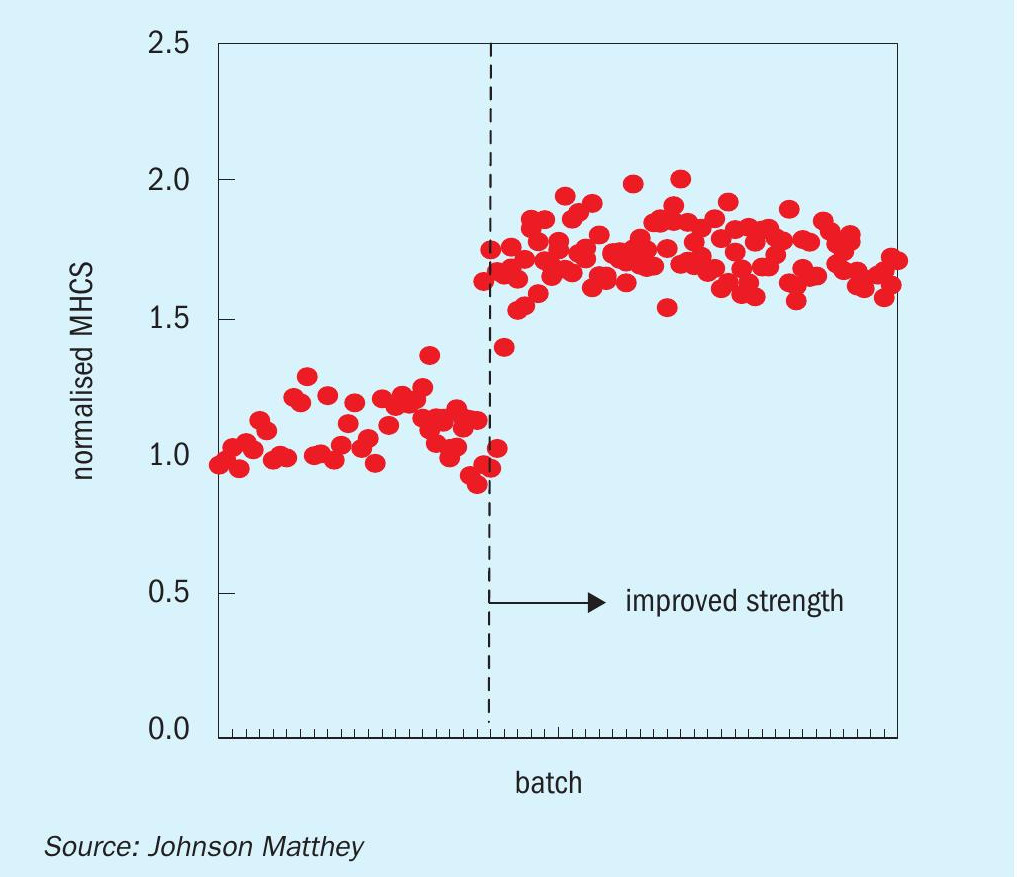
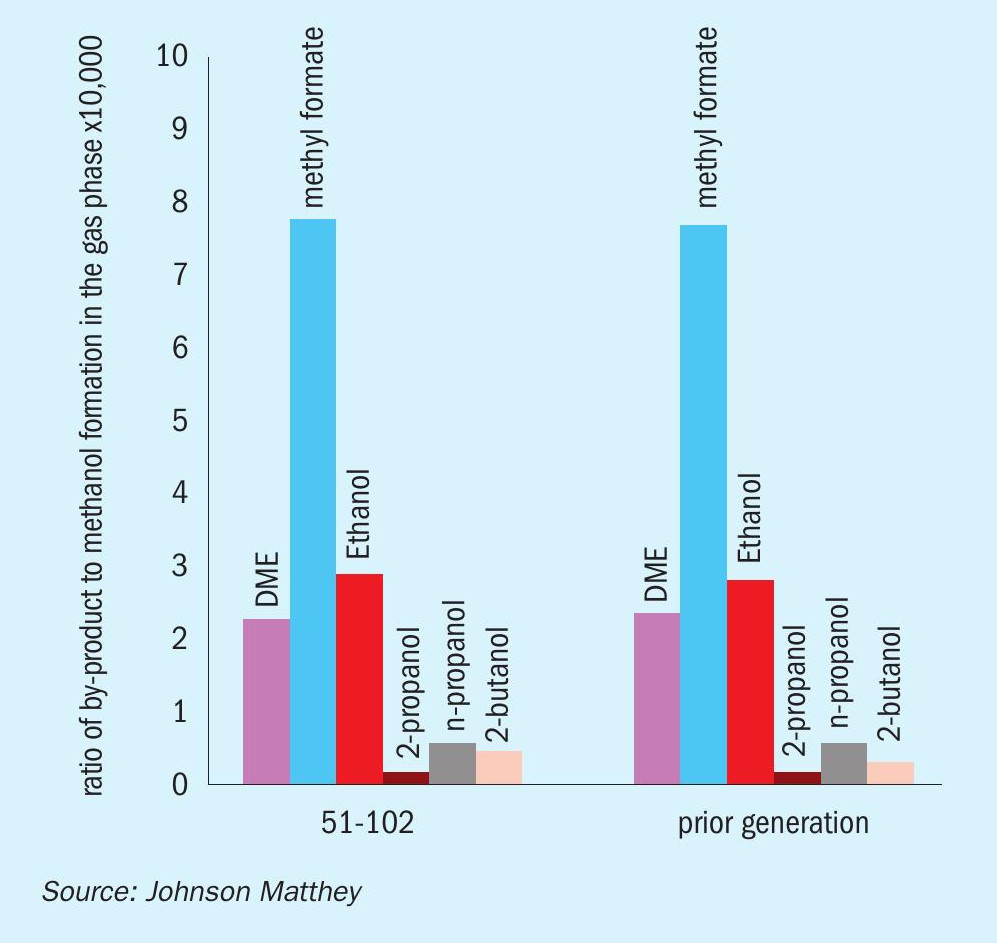
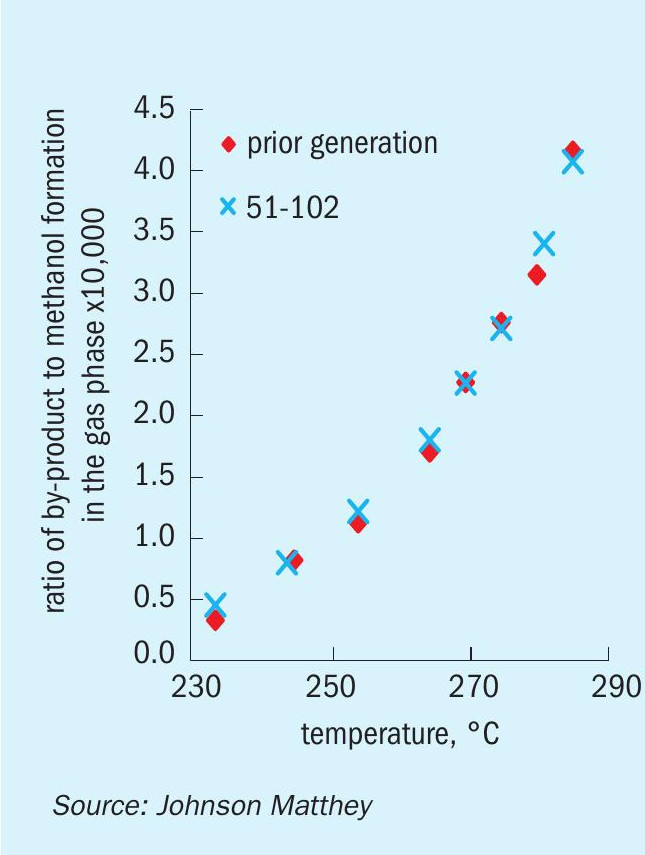
The formation of most of the by-products during the synthesis of methanol is kinetically limited and therefore increases with temperature. As the methanol synthesis catalyst deactivates over time online and the temperatures in the converter are ramped-up to compensate for the loss in activity, the formation of by-products is expected to increase accordingly. However, the selectivity achieved with KATALCO 51-102 is likely to be improved over prior generation catalysts due to the slower deactivation and consequently slower ramp-up of temperature.
Pilot scale testing: methanol sidestream unit
As part of the development and post-launch evaluation of KATALCO 51-102, this product has been tested for long periods of time (6-12 months) at real plant conditions in JM’s methanol side-stream unit. The methanol side-stream unit is attached to a customer’s plant; a small fraction of the converter feed in the plant is directed to the unit. JM is grateful that the side-stream unit is currently hosted by Proman USA Pampa Plant, Texas. This unit has six pairs of adiabatic converters that expose the catalyst to plant conditions in real time. Reactors may be withdrawn at different intervals to assess the catalyst activity after different lengths of time online. The reactors can be boxed up and shipped to our facilities under an inert atmosphere to avoid re-oxidation of the copper component before catalysts are analysed.
Fig. 10 shows the relative activity for KATALCO 51-102 vs. a prior generation catalyst installed in the same reactor pair for six and 12 months. KATALCO 51-102 was 1.30 and 1.70 times more active than the prior generation catalyst after six and 12 months online in the side-stream unit, respectively. These results from the side-stream unit are in line with the performance of KATALCO 51-102 in customer plants, as exemplified in the next section.
Industrial references
The first industrial reference for KATALCO 51-102 was a 25 tonne (27.5 short ton) charge installed in a tube cooled converter at Proman USA Pampa Plant, which is operating on average at 120% of design capacity. This charge was brought online in early November 2018 and has been running without issues since then. The KATALCO 51-102 charge has demonstrated a substantial improvement in activity retention over time with respect to the prior generation catalyst, as can be seen in Fig. 11, where the activities at start of life are similar to those for the prior generation catalyst and then decrease at a much slower pace. The stability benefit is even clearer when plotting this set of data in terms of relative activity (Fig. 12), which shows a relative activity of around 1.6 after 24 months online. As mentioned in the previous section, the relative activities for the KATALCO 51-102 charge at Proman USA Pampa Plant are in line with the relative activities measured in the methanol side-stream unit (Fig. 10).
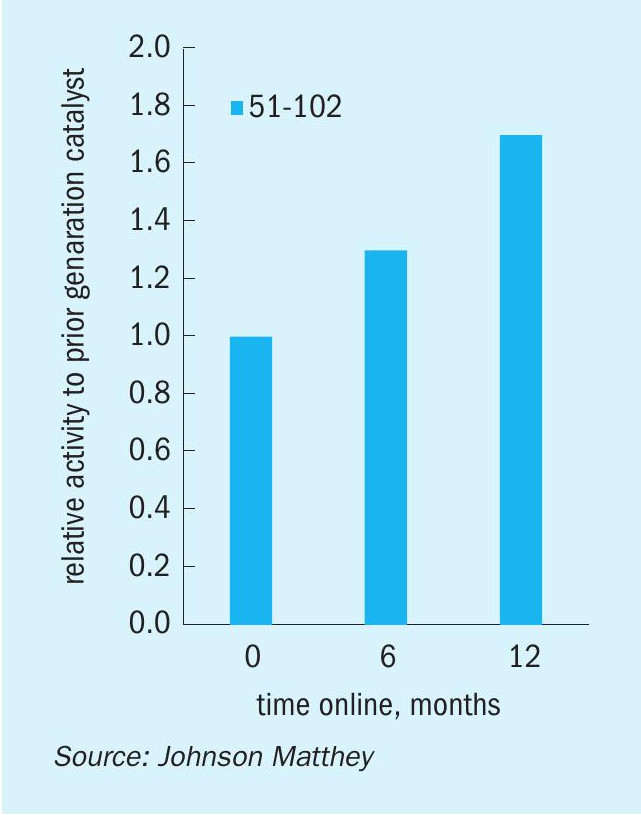
Consistent with lab data for by-product formation on KATALCO 51-102 (Fig. 8), the ethanol production at Proman USA Pampa Plant with the KATALCO 51-102 charge has shown no significant differences in ethanol formation when compared to the previous charge of a prior generation catalyst, as seen in Fig. 13.
After the successful performance of KATALCO 51-102 at Proman USA Pampa Plant, a second charge of KATALCO 51-102 has also been installed in a larger methanol plant and a third charge is planned to be installed later this year. The second charge of KATALCO 51-102 has been loaded in a world scale methanol plant, operating at high rates; at the time of writing the plant has been online for just over six months and the performance is slightly above expectations at start of life and substantially above the performance of the prior generation catalyst from the KATALCO 51-series (see Fig. 14; relative activity to prior generation catalyst is around 1.3-1.4 at 6 months online). The third charge will be installed in a methanol plant with a capacity of over 1,600 t/d.
CO2 hydrogenation to methanol
Methanol is a key product in the chemical industry, and it is currently mostly produced from fossil fuels. The production and subsequent use of methanol generates emissions in the region of 0.3 gigatons of CO2 per annum, approximately 10% of the total for all chemicals6 . Nowadays there is a growing concern about global climate change due to emissions from carbon intense processes and that has intensified the search for ways to ‘green’ our activities. Global megatrends are accelerating towards net zero emissions and we all should play a role in this. In this context, CO2 hydrogenation to methanol can be part of the pathway to eventually achieve the decarbonisation of the chemical and transport sectors.
Catalysts from the KATALCO 51-series are already being used successfully in these applications. To name an example, our catalyst is in use for the production of renewable methanol using hydrogen from electrolysis of water and captured CO2 . The catalyst has been successfully operating in one cycle of more than five years and it is now in the third year of the second cycle.
Methanol synthesis is an equilibrium limited reaction and therefore a recycle is essential to maximise the production of methanol and make the process economically feasible at large scale. Therefore, the actual operating partial pressures of CO2 for the production of green methanol are not massively higher than those observed during the production of methanol from conventional sources (see Fig. 15). However, these will still lead to a larger formation of water and it is beneficial to use an even more hydrothermally stable catalyst made using Si as a stability promoter in these duties. Relative activities for a Si-promoted catalyst to a prior generation material are shown in Fig. 16. This data set was acquired during an accelerated deactivation test at conditions relevant for green methanol production. This curve shows how catalysts made using this technology are more stable and perform better than the prior generation materials in this duty, yielding large benefits for plants using CO2 as a feedstock.
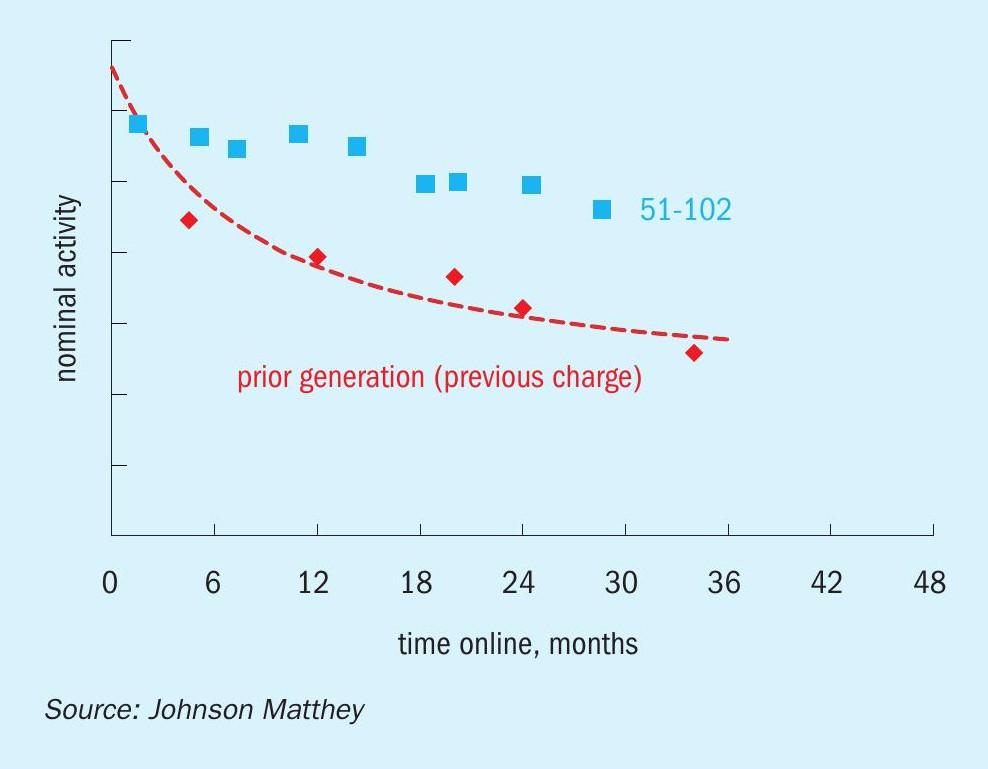
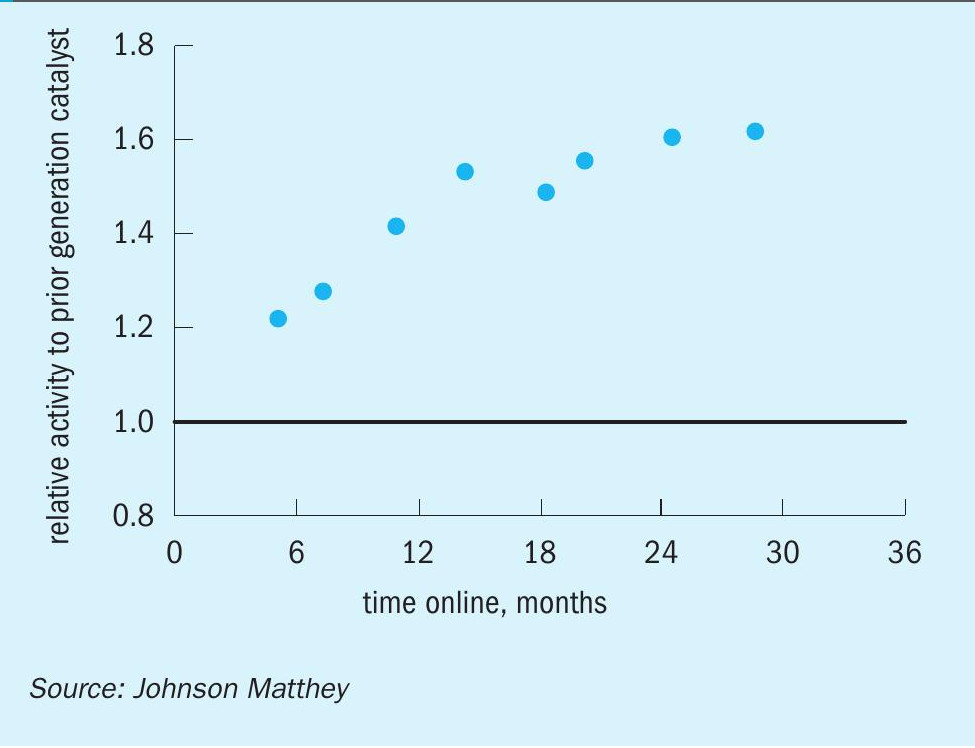
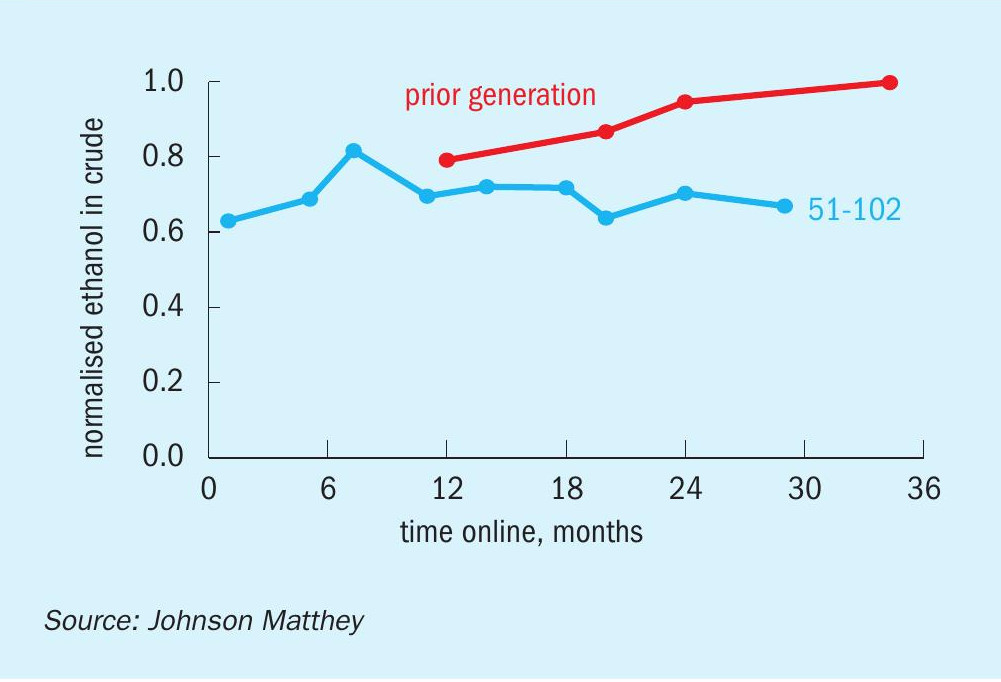
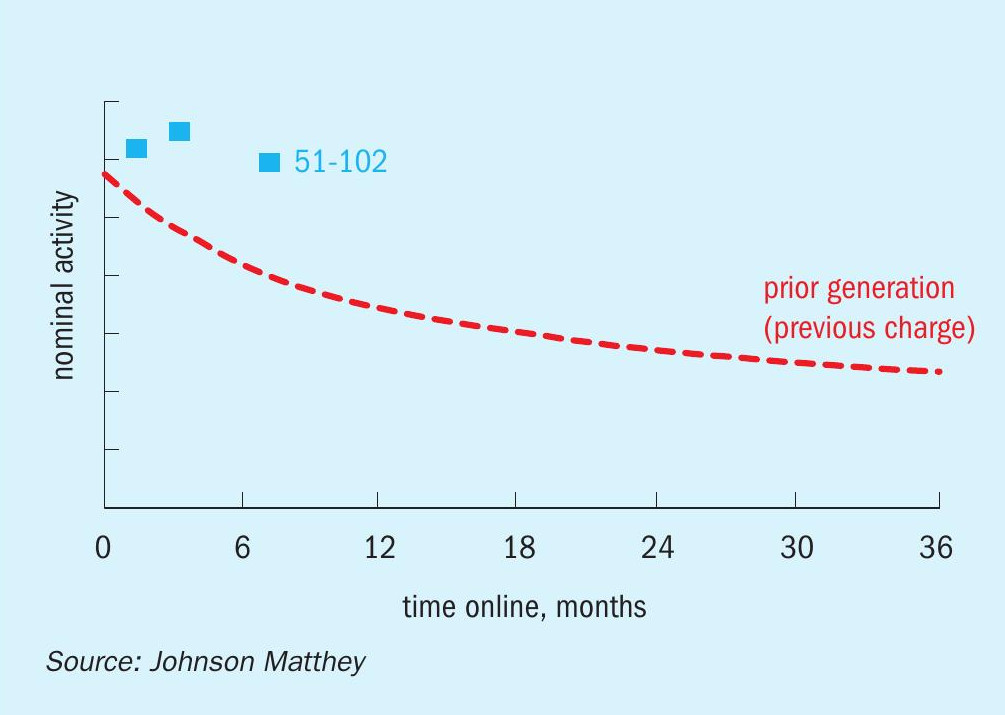
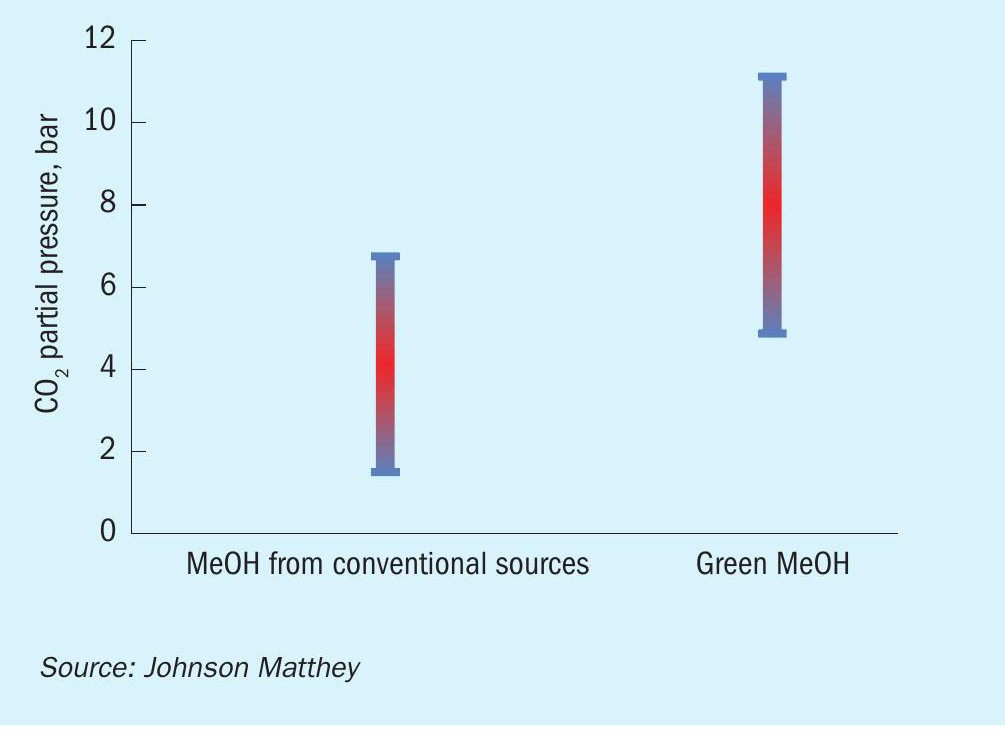
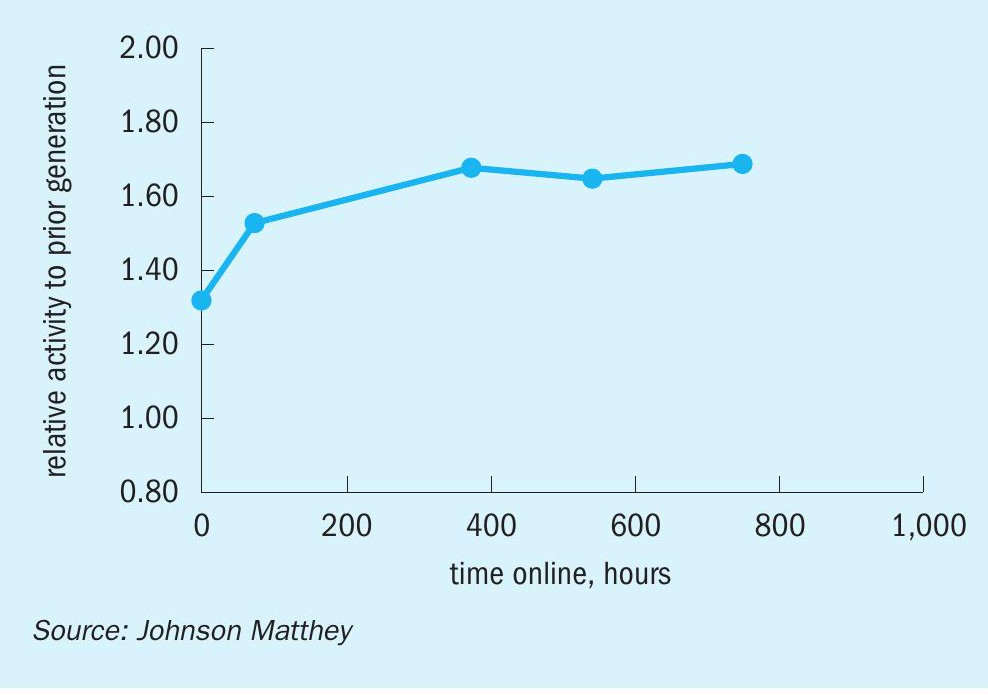
Conclusions
KATALCO 51-102 is the latest methanol synthesis catalyst developed and commercialised by Johnson Matthey. It offers higher sustained activity over time compared to any of its predecessors which is obtained via a small addition of silica to the formulation. This tailored modification to the recipe has no significant impact on other important catalyst performance metrics such as selectivity, strength, or attrition resistance, however, the effect on the stability of the catalyst over time is remarkable. The improved stability over time for KATALCO 51-102 has not only been proven by extensive testing at lab and pilot scale, but also in commercial methanol plants. All the evidence to date points to significant value generation for customers in terms of additional methanol make over the normal catalyst life, plus potential increased time between change-outs. A typical 3,000 t/d plant switching to KATALCO 51-102 could make an additional 2.5% methanol over four years, worth $9 million in extra margin (assuming $100/t margin). An extra year on the change-out cycle would be worth a further $0.8 million per year. A more stressed or revamped plant could generate even more value. Additionally, the technical developments that are intrinsic to KATALCO 51-102 will also yield major benefits for ‘green’ methanol plants utilising CO2 as a feedstock.
References