Fertilizer International 505 Nov-Dec 2021
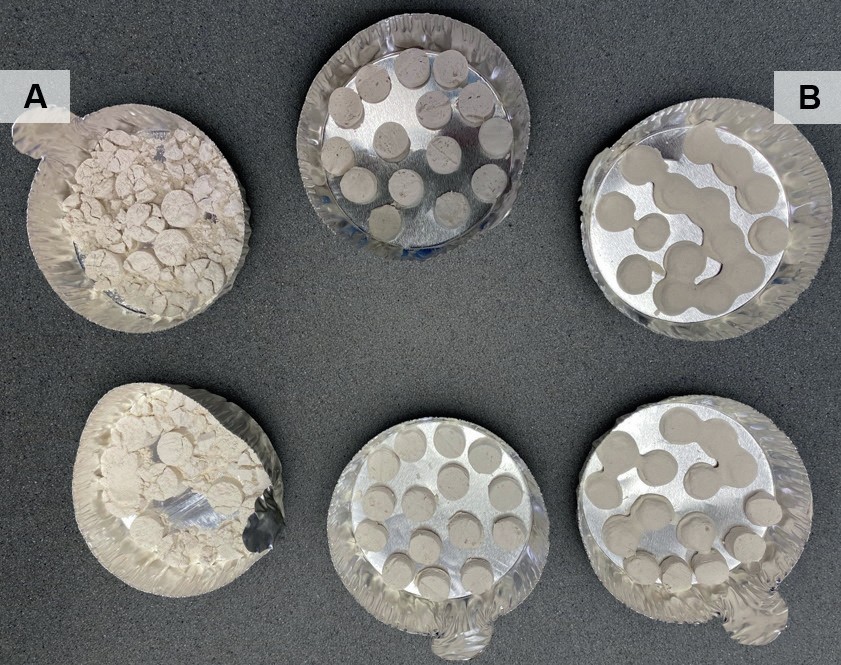
30 November 2021
Evaluating the performance of granulation aids
GRANULATION
Evaluating the performance of granulation aids
The consistency and integrity of fertilizer granules are key when producing a high-quality product for crop nutrition. Granulation aids help achieve this by increasing crush strength, improving size distribution and reducing recycling volumes during manufacturing. Christina Konecki of Arkema-ArrMaz outlines how their performance can be properly evaluated.
Granulation aids – also known as granulation binders – are valued for their ability to help build granule mass and improve size distribution. Yet they can also make granules more prone to crumbling due to moisture absorption. Assessing moisture impact, crush strength and size distribution is therefore critical when evaluating granulation aids.
What are granulation aids?
Granulation is a proven process for manufacturing high-quality fertilizer products with tight size distribution and good handling properties. Fertilizer granules are generally produced from a slurry of fine crystalline particles through a process of agglomeration. The function of granulation aids is to improve the interactions between the crystals that hold fertilizer substrates together1,2 . Granulation may occur via two agglomeration mechanisms – layering or coalescence – this being dependent on the chemistry of the fertilizer matrix and the binder used.
While granulation aids may exhibit similar agglomeration mechanisms, it is generally their bonding strength – derived from chemical characteristics – that contributes to final granule hardness. This point was illustrated by a study on biochar granulation3 . This found that granule size was dependent on the type of agglomeration mechanism. Large granules, for example, were formed via coalescence with a polymer binder. The strongest granules, however, were formed using a sugar-based binder that agglomerated through layering. This study therefore showed that the bonds formed between sugar and biochar were stronger than those created with the polymer binder3 . Another granulation study, for ammonium chloride, found that the best binder had a very strong ionic charge which promoted better agglomeration4 .
In the last decade, scientific research has shown that fertilizer binders can provide added value that goes beyond improved granulation. The surprising secondary benefits include:
- The controlled release of fertilizer nutrients
- Better soil aeration
- Improved fertilizer consumption
- Heavy metal chelation
- The ability to add nutrients.
Key factors to consider
The fertilizer industry typically uses clay, starches, sugars, lignosulfonates and polymers as granulation binding agents. When selecting a granulation aid, it is important to consider:
- Fertilizer type
- Regulatory requirements
- Added nutrient factors
- Application method
- Binder viscosity
- Loading rate.
The chemical structure of both the fertilizer and binder plays an important role in granulation, but it can also impact the release profile of the fertilizer.
In a study of the effect of binders on the release profile of urea, a more hydrophobic granulation aid (corn starch) had a longer release profile than a hydrophilic polymer (hydroxypropylmethylcellulose), for example5 . Similarly, the use of a chitosan binding agent extended the release profile of urea-kaolinite granules. Approximately 60 percent of the urea was released after 30 days, compared to 99 percent for urea on its own6 .
Inevitably, there are trade-offs between the cost of adding a binder and the resulting improvements in granule properties. The cost-benefit ratio is therefore an important consideration for granulation binders. Polymer additives, for example, usually continue to increase granule strength as their concentration is raised, but they are a more expensive option. Sugars and starch binders, meanwhile, may be cheaper, but they do not impart the same level of granule hardness.
When evaluating granulation aids or binding agents, in order to optimise the granulation process, it is always good practice to consider several chemical types and different dosages. Dosage rate can alter the viscosity of the fertilizer solution – which also contributes to granulation. The method of binder addition must also be considered, with particular attention paid to temperature, pH, moisture and the physical state of the binder.
Evaluation methodology
To demonstrate how granulation aids should be evaluated, Arkema-ArrMaz measured the performance of a selection of binders from its granulation aid product line. Various properties can be tested for and analysed, depending on the fertilizer producer’s individual needs. These range from granular hardness to the impact of moisture absorption and nutrient release.In this case, Arkema-ArrMaz evaluated the ability of binders to improve granulation performance by measuring their impact on the granule crush strength of the fertilizer manufacturer’s product – both before and after exposure to humidity. Granule crush strength measures the kilograms of force (fkg) required to break the fertilizer material.
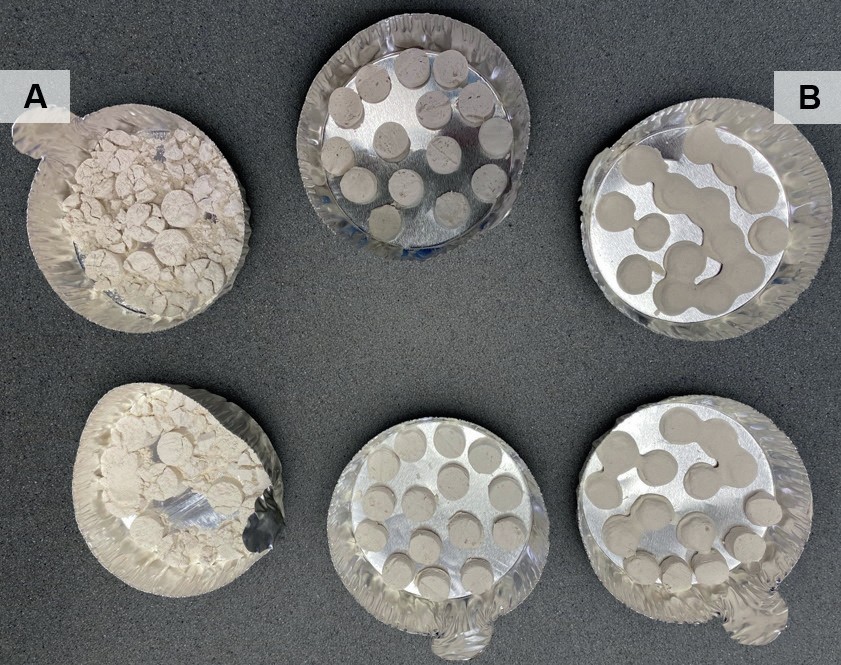
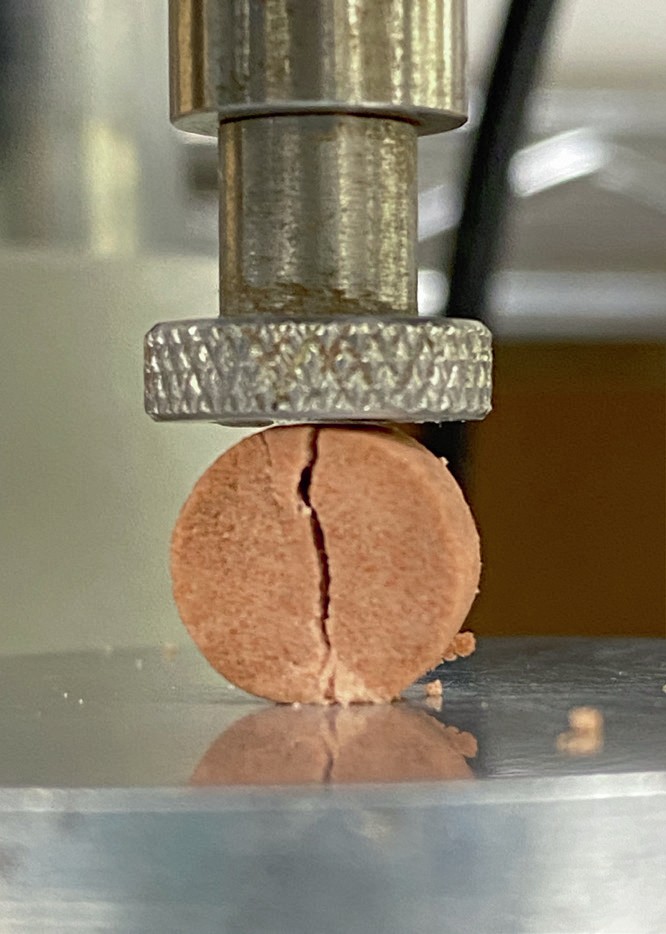
The evaluation methodology proceeded in three stages.
Simulating the granulation process:Firstly, to successfully measure granulation performance on a small-scale, dry fertilizer powders were collected and the binders formulated. The binders were next mixed into the fertilizer at the desired loading level, either as a liquid solution or as dry powder. Then, to simulate the granulation process, these fertilizer-binder mixtures were extruded as pellets.
Identify fertilizer-binder incompatibilities: Once the pellets have been made, and before hardness is evaluated, signs of incompatibility with the fertilizer salt should be identified. Figure 1 shows examples of incompatible binder-fertilizer interactions after drying. Example A shows crumbling where granules are unable to form, while example B demonstrates that the binder-fertilizer is not firm enough to produce individual granules. Performance testing can begin once dry and intact granules are produced.
Measure initial and post-aging granule hardness/moisture absorption: Granule hardness is the most common laboratory metric used by producers to measure how a binder will perform in the field (Figure 2). However, depending on the fertilizer type, moisture absorption is another factor that can also be considered. Changes in moisture absorption can be evaluated by monitoring mass gain over time in humid environments and/or by measuring post-moisture granule hardness. If, after the addition of binder, the granule can withstand exposure to humidity while maintaining granule hardness, then it is likely that the binder will not cause harmful effects under real-life storage, handling and transportation conditions.
Granulation aid performance across different fertilizer substrates
The three fertilizer substrates examined here were potash (KCl), gypsum (calcium sulphate) and an NPK mixture. Depending on the substrate, specific binders from Arkema-ArrMaz’s granulation aids product line were selected for testing at different additive rates. Each fertilizer type was, however, compared to the same water-only control sample.
Substrates were evaluated for binder selection by measuring initial and ‘postaging’ granule hardness. Pellets were produced by combining the fertilizer powder with water and the binder agent, and then extruding these into 4 mm thick pellets. The initial hardness value was measured once these pellets were dry. The postaging samples were exposed to 65 percent relative humidity (RH) for 24 hours at 30°C and then allowed to dry before hardness was again measured.
Potash was granulated with six different binders at 0.5 weight percent (Figure 3). Both initial and post-aging granule hardness improved for all of the binders evaluated, versus the control. This improvement was greater than 150 percent in all cases. Binders 2 and 6, however, showed the most consistent improvement in initial and post-aging hardness. This level of performance would be beneficial for fertilizer granules being exposed to varied temperature and humidity cycles during storage, handling and transportation.
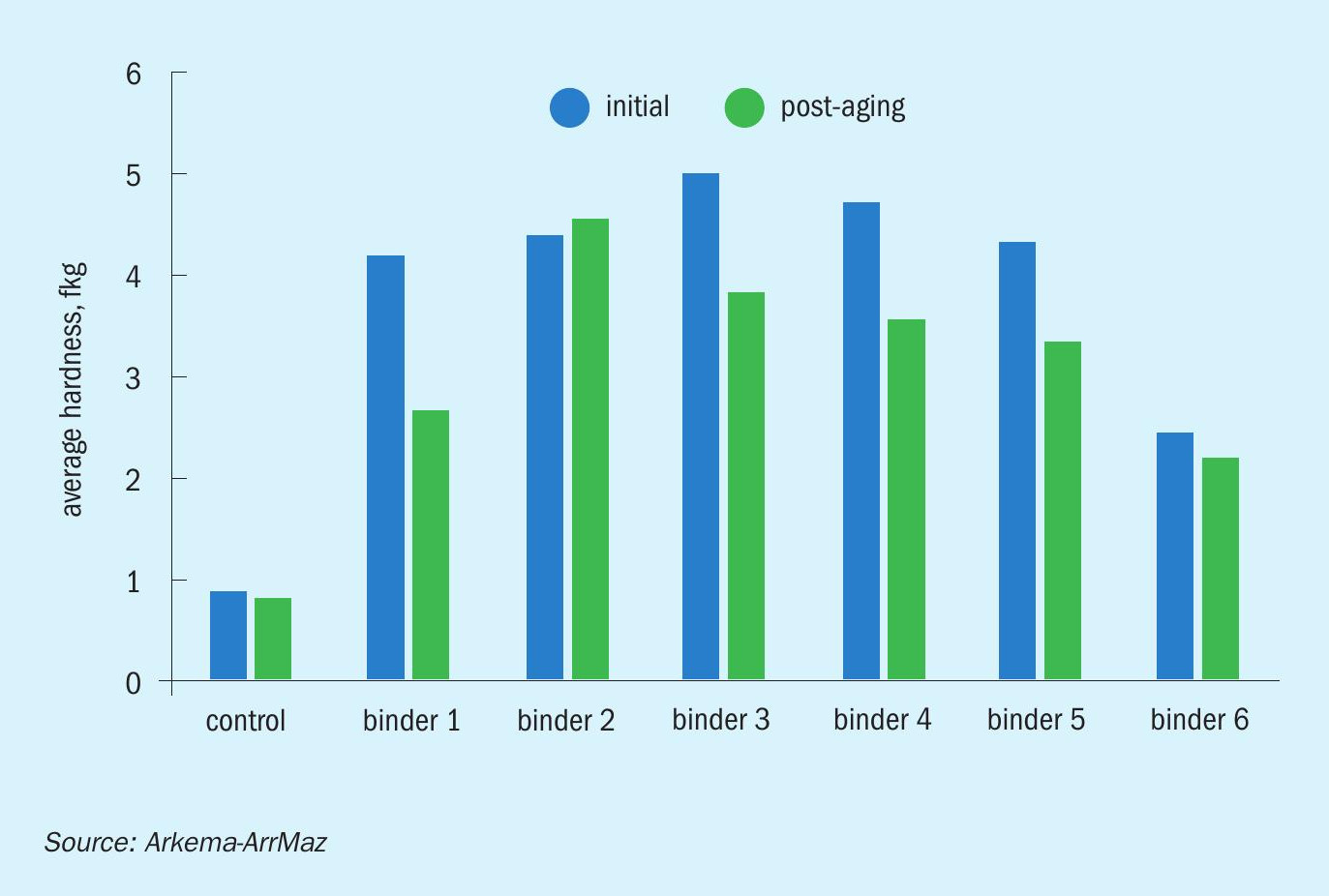
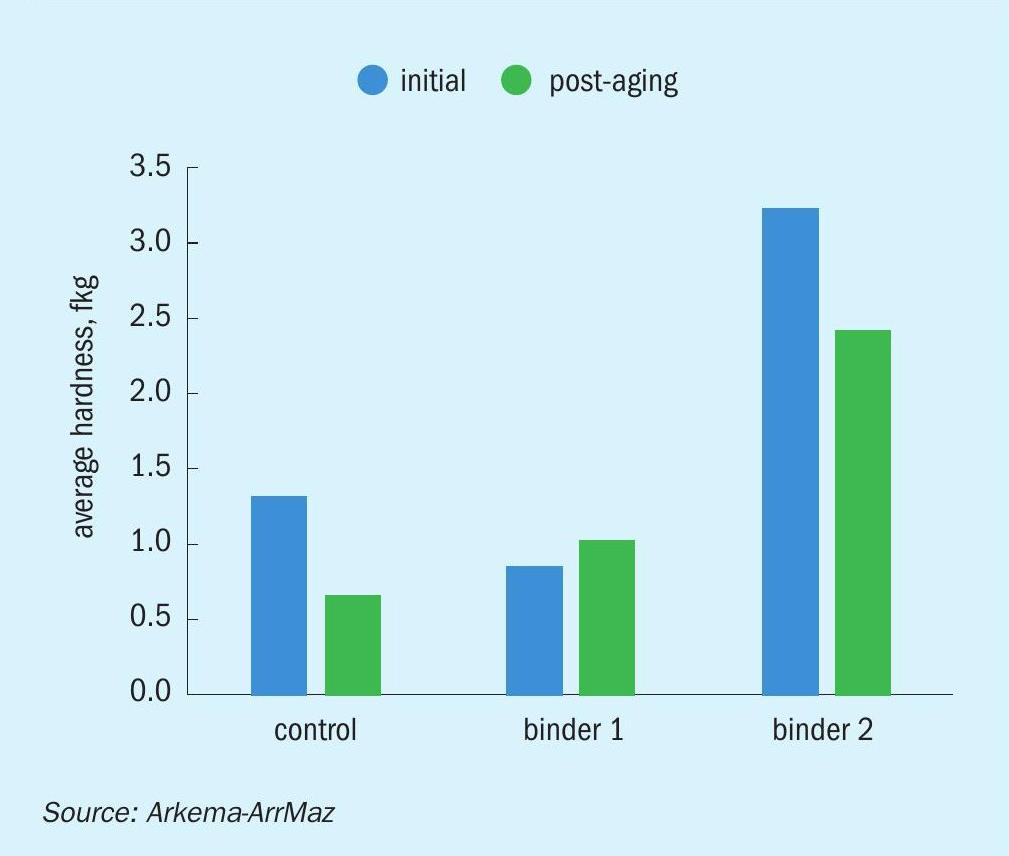
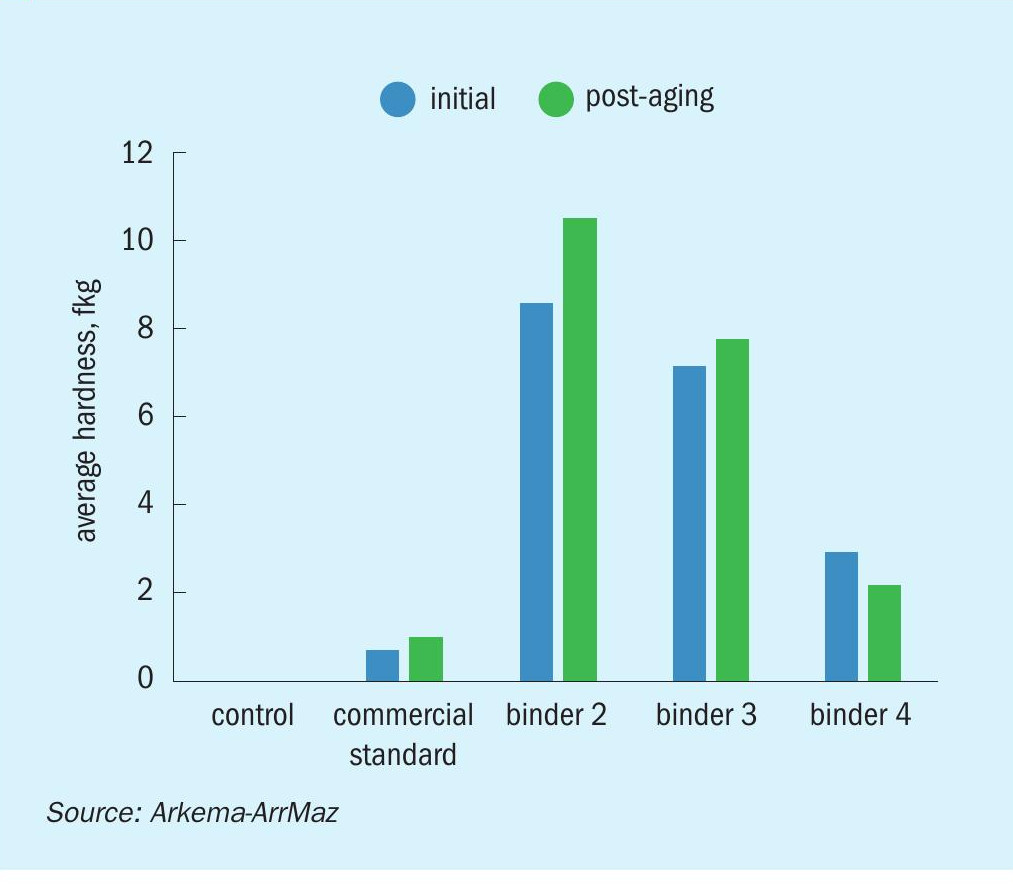
Similarly, the NPK substrate was granulated with two binders at 0.5 wt% load (Figure 4). Binder 2 showed improvements in both initial and post-aging granule hardness of more than 80 percent, compared to the control. Binder 1, meanwhile, performed slightly less well than the control. This confirmed that binder 1 and the fertilizer were chemically incompatible for granulation.
The calcium sulphate samples were tested at a high binder loading of six wt% (Figure 5). However, it was not possible to form an intact, solid pellet for the control samples as these crumbled. Consequently, it was not possible to measure and obtain an initial or post-aging hardness value for the control. This itself indicates that calcium sulphate would benefit greatly from a granulation aid. For calcium sulphate, the efficacy of three Arkema-ArrMaz granulation aids was instead tested in comparison to a standard offthe-shelf commercial binder.
All four binders improved calcium sulphate granule hardness. But the improvement obtained with the commercial binder was less significant than that delivered by the Arkema-ArrMaz binders, particularly binders 2 and 3. Both these binding agents are likely to provide high strength granules in the field at a much lower loading level. The higher than normal binder loading used with calcium sulphate (6 wt% versus 0.5 wt%) suggests there is further scope for fine-tuning binder concentration to deliver the desired improvement in granule hardness.
“This evaluation approach demonstrates the effectiveness of custom-formulated granulation aids for improving product quality.”
Summary
Fertilizer producers wishing to produce granulated products of consistent high-quality may find that standard commercial granulation aids are unsuccessful – and that custom-formulations, such as those available from Arkema-ArrMaz, are necessary instead. Indeed, binder selection is unique to the individual fertilizer, the type of process, and the exact needs of the end-user.
Choosing the right granulation aid will produce fertilizer granules with improved strength and consistency. Valuably, it may also provide a range of secondary benefits that make the fertilizer product more marketable. These include more sustainable, natural or organic compositional characteristics, controlled-release properties, or the ability to improve nutrient uptake.
In this article, we show how granulation aid performance can be successfully evaluated by simulating the granulation process on a small scale in the lab. The hardness and moisture absorption of pelletised samples are measured before and after (postaged) exposure to specific relative humidity and temperature. As the above data show, this evaluation approach demonstrates the effectiveness of custom-formulated granulation aids for improving product quality and optimising the fertilizer production process. We recommend that producers request this type of data from their supplier. This will ensure that the best granulation aid or binder is selected for your unique fertilizer product and process.
Author
Christina Konecki is the North America manager of coating technologies at Arkema-ArrMaz. Baziela Cabrera, Arkema-ArrMaz lab technician, is thanked for providing the data.
References