Fertilizer International 505 Nov-Dec 2021
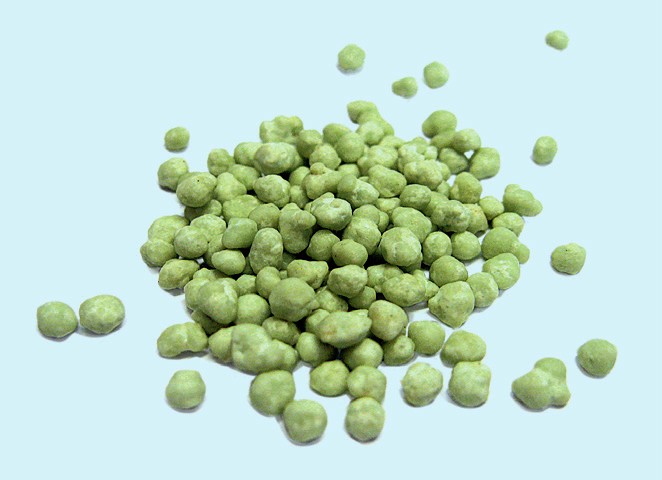
30 November 2021
Fertilizer finishing: last but not least
PROCESS TECHNOLOGY
Fertilizer finishing: last but not least
New innovations and the latest equipment options from FEECO International, Casale, thyssenkrupp Fertilizer Technology and Eirich are helping to perfect the fertilizer finishing process.
FEECO INTERNATIONAL
Coating and finishing techniques for advanced fertilizers
Fertilizer technology continues to advance to meet the ever-changing needs of modern agriculture. Market demand is shifting, as scientists continue to reveal the secrets behind optimal crop production, with growers seeking fertilizer products that offer enhanced performance and deliver precise nutrition.
In this article, we examine how fertilizer coating, particularly when carried out in a rotary drum, is being used to meet these new goals. Other finishing techniques used in the manufacture of advanced fertilizers are also explored.
Why coating?
Coating is a flexible and already-proven technology (Figure 1). The technique ensures that products satisfy the increasingly stringent quality criteria required in today’s fertilizer market, and can also deliver crop nutrient products in new formulations.
Importantly, coating allows producers to add value and create premium products by minimising dust and caking and improving flowability and appearance. As a result, coating provides granular fertilizer producers with entry into higher-value end-markets.
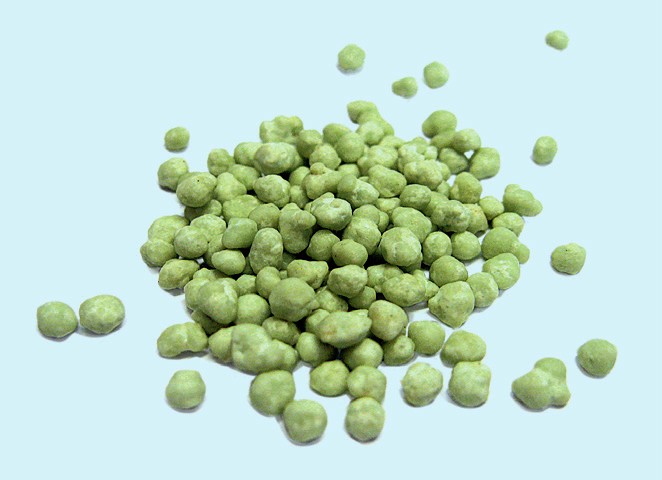
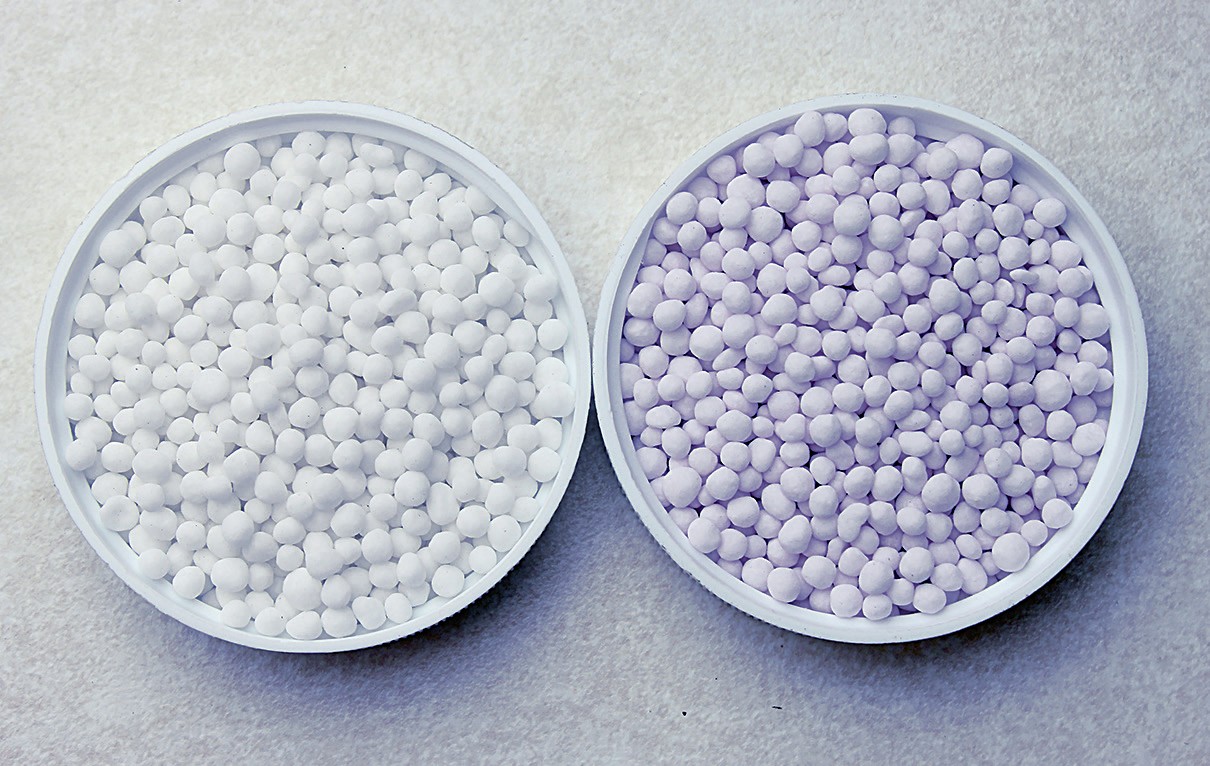
Anti-caking properties
Any fertilizer producer or distributor can attest to the numerous problems caused by caking. These include spoiled products, clogged equipment, poor handling, dust formation and workplace hazards. For these reasons, mitigating the potential for caking is a key objective during fertilizer production, handling and transport – with coating offering a simple solution to these issues and more.
By coating fertilizers with anti-caking agents and moisture inhibitors, producers can maintain the integrity of granular products throughout their lifecycle, so avoiding the potential problems associated with caking (Figure 2). Common anti-caking agents include:
- Oils
- Waxes
- Polymers
- Clay
- Diatomaceous earth
- Talc
- Speciality chemicals.
Dust prevention
Similarly, the creation of dust causes problems for both fertilizer producers and growers alike. Excessive dust can, for example, cause product losses, be a respiratory hazard, increase caking, and result in inaccurate field application.
Coating minimises the potential for dust formation by creating a protective layer around each granule. This prevents attrition and reduces fines generation due to product breakdown. Common dust -reducing coatings include:
- Oils
- Waxes
- Polymers
- Speciality chemicals.
Controlled-release and enhanced efficiency fertilizers
Another way in which coating technology is helping to meet the demand for advanced products is through the creation of enhanced efficiency and controlled-release fertilizers. Coating techniques can be used to either control the rate of nutrient release or deliver active ingredients. This enables fertilizer producers to tailor their products to meet the specific requirements of growers and the end application.
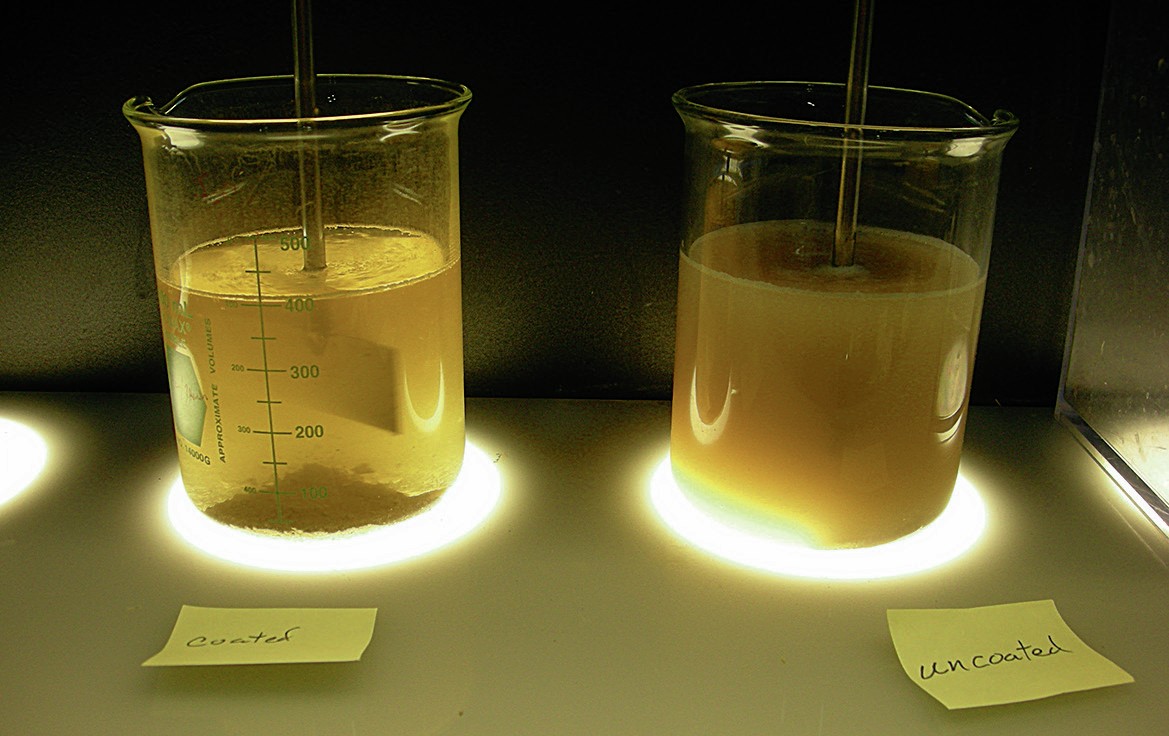
BENEFITS OF THE COATING DRUM
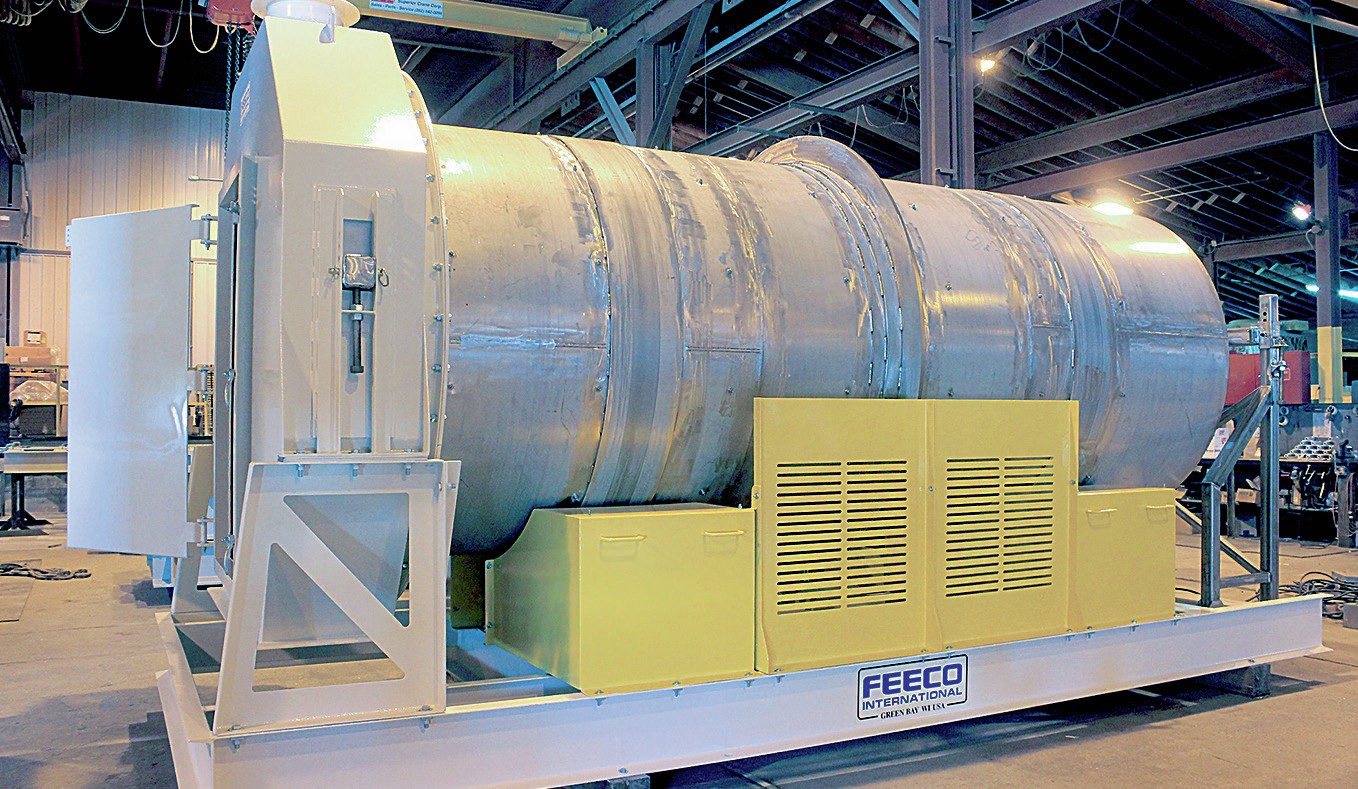
The coating drum is recognised within the industry as a high-capacity device able to provide superior results, compared to several other fertilizer coating options available on the market. Coating drums, being a well-established and proven technology, offer a number of advantages for creating uniformly coated products. These are summarised below.
Greater uniformity
Perhaps the most critical advantage of the coating drum – and the reason why it is often favoured – is its ability to provide highly uniform results. Because, when it comes to coating, uniformity is key.
Unfortunately, the benefits that advanced fertilizer formulations should provide are often lost due to inadequate and poorly applied coatings. Coating performance depends on a thorough and uniform surface coverage; even a small discrepancy in coating can create an entry point for moisture, negating the benefits of the coating altogether.
The tumbling motion that occurs within the coating drum, when combined with an expertly designed spray system, promotes a highly uniform distribution of the coating throughout the material bed via granule-to-granule transfer.
Higher production, lower maintenance, less coating
What makes coating drums an ideal fit for the fertilizer industry is their significantly higher throughput compared to other devices. Furthermore, a well-designed coating drum avoids the over-spraying that is characteristic of other devices. This results in increased production as less time is devoted to cleaning and maintenance requirements. Because over-spraying is avoided and wastage is reduced, coating drums also require less coating to achieve the desired results.
Gentle handling
Coating drums are able to provide the gentle handling required by many fertilizer products. This is a valued characteristic as it prevents premature product breakdown and the unnecessary generation of dust and fines.
Many of the advantages of coating drums, as described above, apply equally to glazing and tumbling/polishing drums as well. (Figure 4)
Valuably, coatings provide a way of improving nutrient use efficiency, by incorporating beneficial additives or by creating a physical barrier between the granule and the surrounding environment (Figure 3). Coating technology therefore provides a major tool for reducing nutrient runoff and, correspondingly, increasing plant nutrient uptake – two key objectives in modern crop production. Although the coatings used to control nutrient release or improve use efficiency are often product-specific, they include:
- Speciality chemicals
- Polymers
- Clays
- Waxes.
New nutrient formulations
Coating is also becoming a popular technique for improving the nutrient composition of fertilizer products and hence their value. Fertilizer producers can create an entirely new formulation simply by coating a fertilizer product with a micronutrient or other beneficial additive. Such customised nutrient formulations can be designed to match regional soil requirements or satisfy crop-specific needs – a rising trend in crop nutrient management. Coatings allow the incorporation of a wide range of additional secondary nutrients and micronutrients such as:
- Sulphur
- Boron
- Copper
- Magnesium
- Iron
- Manganese
- Zinc
- Molybdenum.
Glazing: a finishing technique for potash
Besides coating, glazing has now emerged as a favoured technique for improving potash products obtained via roll compaction. Roll compactors typically generate irregular-shaped potash granules. The resulting sharp edges increase attrition and generate fines as they rub together and break down.
Potash producers can, however, use glazing to combat this problem. In this technique, potash coming off the roll compactor is fed to a rotary drum where it is sprayed with a small amount of water and tumbled. This tumbling action smooths the edges and faces of the granules. The addition of water enhances this effect by causing a thin layer on the surface of granules to dissolve and recrystallize – resulting in the formation of smooth, polished granules during tumbling. This glazing technique – sometimes referred to as polishing or conditioning – may also be carried out in a pug mill or, when applicable, at the discharge end of a rotary dryer.
Tumbling/polishing for finishing granules
Similarly, other fertilizer producers also incorporate a tumbling or polishing drum into their processes to round and polish granules with hard edges and rough surfaces. This again creates a more rounded and smoother product less susceptible to dust and fines generation.
Developing advanced fertilizers with a rotary drum
One of the advantages of the rotary drum, whether used for coating, glazing, or polishing, is that it is a familiar technology that is easily incorporated at the end of a fertilizer production line. However, to achieve the best results – and ensure the desired product goals and objectives are delivered – the design of the rotary drum needs to be tailored to the intended application and the specific material characteristics.
In practice, the design of the coating drum often has a dual focus, being centred on both the bed action and spray system configuration (Figure 5). When optimising bed action, the following critical variables need to be considered:
- Bed depth
- Drum speed
- Flighting
- Drum size
- Retention time
- Granule shape and surface characteristics.
When properly configuring the spray system, the critical variables include:
- Spray rate
- Spray locations
- Nozzle type
- Coating and material temperature.
The most optimal design is typically identified through testing procedures – such as those provided at the FEECO Innovation Center. Here, experts work to gather process data, evaluate material behaviour, and design the most efficient and effective coating drum as possible for the application at hand.
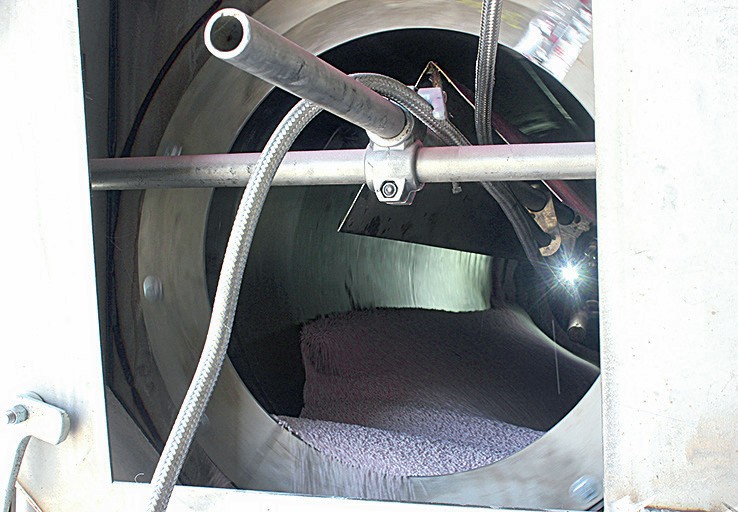
Concluding remarks
To meet the changing demands of modern agriculture, coating, glazing and tumbling/ polishing will play an increasingly important role as fertilizers become more advanced. These finishing techniques offer a wealth of opportunity to reduce nutrient runoff, improve nutrient use efficiency, and generally provide a better, more user-friendly product. This is particularly true of fertilizers processed in a rotary drum.
The incorporation of already-proven technology, such as a coating or glazing line, into an existing process is advantageous as it is relatively seamless compared to the incorporation of new technologies. Nevertheless, thorough testing remains essential when it comes to developing a coating drum that can efficiently and effectively produce the desired end results.
CASALE
Vibrating skin bucket technology improves urea product quality
Introduction
Nowadays, the ability to combine process efficiency with product quality is the main goal of urea producers. This is especially true for any company wishing to remain a market leader while, at the same time, also meeting increasingly stringent sustainability criteria. Indeed, quality and efficiency have now become mandatory and key requirements when adopting new technologies, as these need to encompass competitiveness, design for the environment and care of the customer.
With this in mind, Casale has recently developed an innovative technology for improving the product quality in the prilling finishing section. This is the last stage of urea production before the product is dispatched to end-users.
Casale has made developing innovative technologies for urea plant finishing sections a specific priority. These efforts have culminated in the successful development of an advanced vibrating prilling bucket – the so-called ‘vibrating skin bucket’. This is now available on the market following the completion of an R&D project. This successful research was carried out with the valuable support of Donald Snyder, the founder of Tuttle Prilling Systems.
Casale’s vibrating skin bucket (VSB) superimposes a continuous axial vibration on the bucket’s conventional rotational movement. This new design, in comparison with a traditional rotating bucket, offers increased plant production combined with improved urea prill uniformity (size and shape). Furthermore, the VSB achieves a reduction in both the fine particle content of the product and dust emissions from the top of the prilling tower.
Casale’s new vibrating skin bucket (VSB)
The VSB is the most advanced type of urea prilling bucket technology currently available on the market. It offers the following key features:
- Suitable for prilling tower with diameters up to 28 metres
- Uniform prill size distribution
- Low dust emissions
- Low prill temperature
- Performs well over a wide range of plant operating conditions.
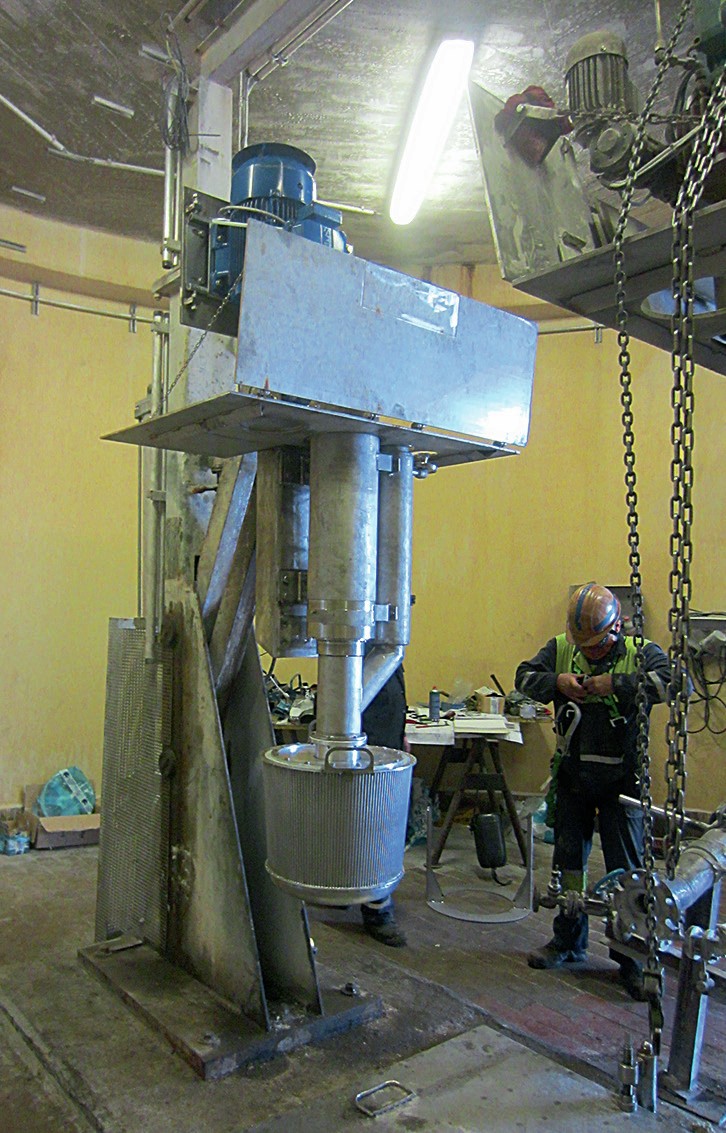
As stated above, the technology was developed in collaboration with Donald Snyder, founder of Tuttle Prilling Systems. This programme of cooperation initially led to the unique prilling bucket design. This was followed by the execution of pilot-scale tests to validate the theoretical calculations.
Following very promising pilot test results, Casale was able to prove VSB technology at industrial scale. Subsequently, Casale also successfully completed the first industrial VSB installation (Figure 1). This technology is now available on the market for both small-and large-capacity urea plants.
Description of the technology
The VSB rotates on a vertical axis like a conventional prilling bucket. Thanks to its innovative, patented design (‘Vibropriller’, Figure 2), the external conical wall of the bucket also vibrates in a vertical direction, while the liquid contained inside the bucket is kept in an almost vibration free state. This vibration is induced by an electronic actuator installed above the prilling bucket.
The operating mechanism of the VSB, based on Rayleigh’s principle of controlled breakup of liquid jets, guarantees the generation of liquid droplets with predictable diameters. The bucket’s vibrating skin, thanks to its unusual ridged shape and optimised hole size distribution, is specifically designed to enhance both the uniformity of the droplets generated and occupancy over the cross-sectional area of the prilling tower.
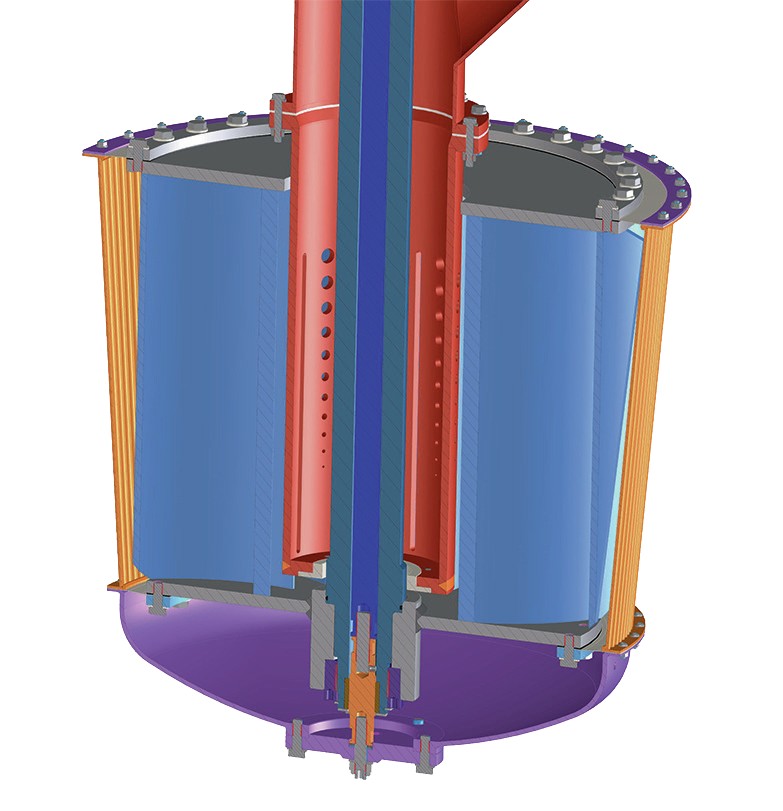
Compared to a conventional rotating bucket, the configuration of the VSB enables higher plant production while delivering improvements in prill uniformity (size and shape). In addition, the VSB achieves a reduction in both the fine particle content of the prilled product and the amount of dust emitted from the top of the prilling tower. Table 1 shows the product size distribution achieved with the first industrial installation of the VSB versus that obtained with a standard rotating bucket.
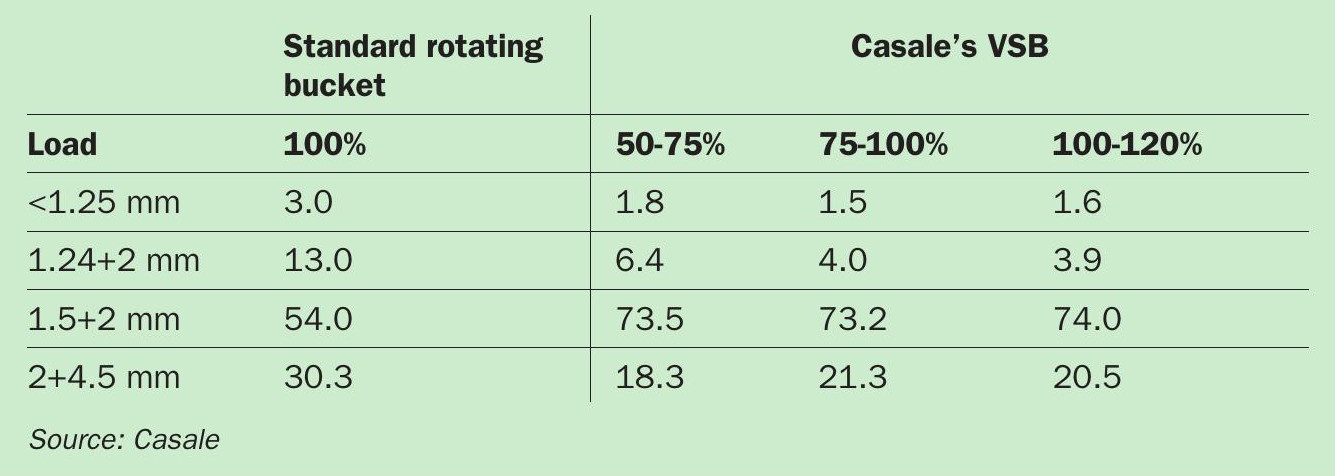
The VSB differs from other ‘vipropriller’ technologies currently available on the market, as the vibration is only transferred to the external wall of the bucket and not to the liquid inside. Its innovative assembly (Figure 2) therefore allows better control of liquid droplet generation to be achieved. The main components of the VSB (Figure 3) are as follows: Vibrating bucket: The complete bucket (excluding the urea melt distributor) rotates on its axis, driven by the electric motor. An electronic actuator, installed above the prilling bucket, transmits the vibration to the bottom cover and consequently to the conical perforated wall of the bucket. The bucket is fed with urea melt through a pipe distributor.
Shaft: The hollow-tube design of the driver shaft enables the electronic actuator to be installed inside it.
Electronic actuator: An electronic actuator located inside the rotating shaft transmits the vibratory motion to the external skin of the bucket. The actuator uses a sinusoidal current of controlled frequency and voltage for this purpose. The frequency of the supplied current determines the frequency of the vibration generated by the actuator, while the amplitude of the vibration is proportional to the applied voltage.
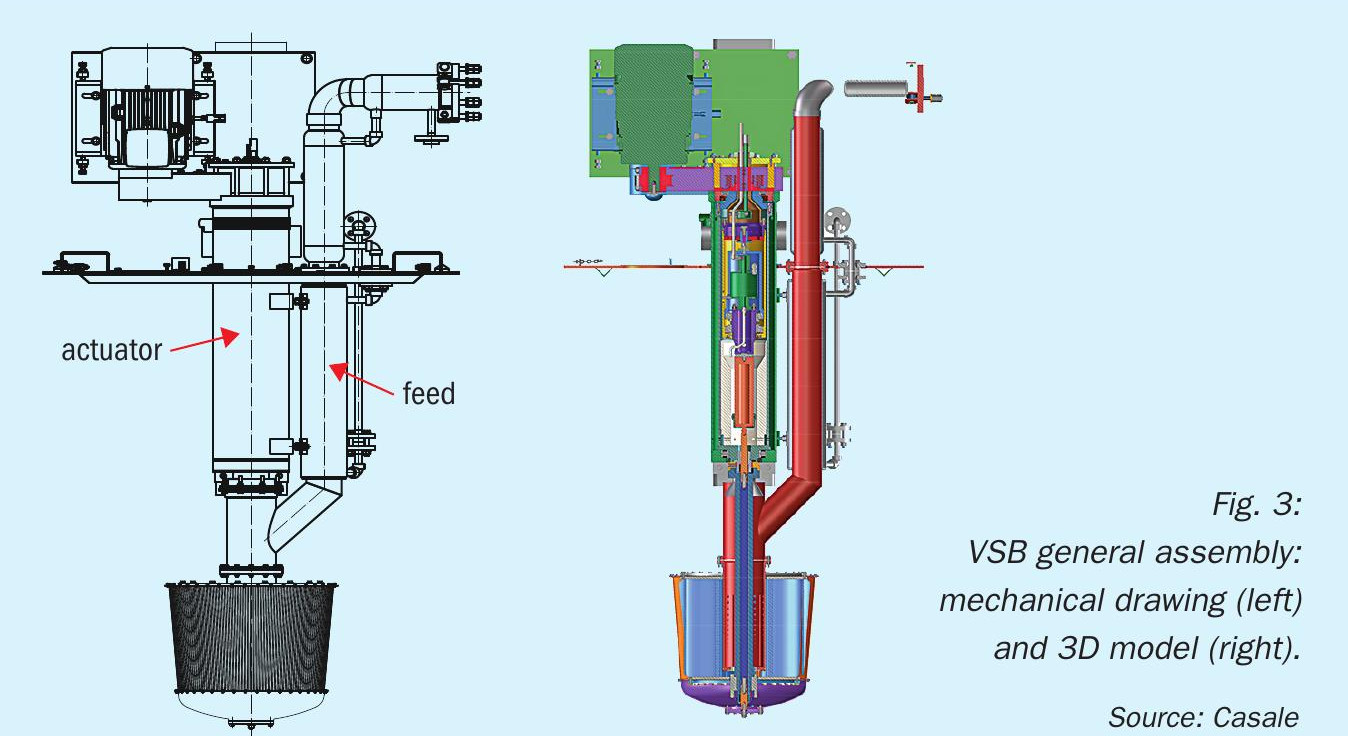
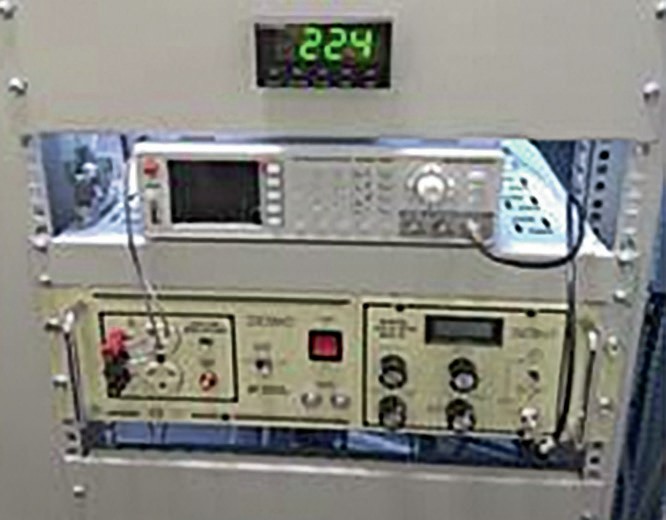
VSB control system
Casale has developed a patented control system for the VSB (Figure 4). This can be easily integrated within the plant’s existing distributed control system (DCS).
The rotational speed of the bucket is controlled by an inverter installed on the electric motor. The vibration, meanwhile, is controlled by means of a signal generator (powered at 220 Vac). This regulates the frequency and the voltage of the signal supplied to the electronic actuator. This signal generator can be operated manually from a local panel or via the DCS.
The patented VSB control system allows the vibration (frequency and amplitude) to be controlled remotely and automatically. By measuring the urea melt flow rate fed to the bucket, the DCS (using a simple function) automatically adjusts both the frequency and the amplitude according to the plant load, so avoiding the need for any manual input. Similarly, the rotational speed of the bucket can also be adjusted automatically from the DCS in accordance with the feed flowrate of the urea melt.
Performance improvements
The VSB offers the following performance improvements:
- Tighter product size distribution with 20 percent higher uniformity index.
- The design can be specifically tailored to meet the desired average prill diameter.
- Dust emissions reduced by 25 percent.
- Delivers a steam saving due to the lower urea solution recycle from scrubbing.
- Reduction in prill temperature.
- Able to maintain excellent product quality when operating at between 50-120 percent of urea plant load.
Conclusions
Casale’s vibrating skin bucket (VSB) design has been successfully tested and operated at industrial scale. This installed unit has delivered outstanding results in terms of uniform prill size distribution, low dust emissions and low prill temperature. The VSB has also been shown to function well over a wide range of operating conditions. In our view, these characteristics make the VSB the most advanced type of urea prilling bucket technology available on the market currently.
THYSSENKRUPP FERTILIZER TECHNOLOGY & GPIC
Advanced urea spray nozzles
Bahrain-based Gulf Petrochemical Industries Company (GPIC) was established in 1979 as a joint venture between the governments of Bahrain, Saudi Arabia and Kuwait. GPIC’s 1,700 t/d urea plant was initially commissioned in 1998. The plant produces granular urea using UFT® fluid bed urea granulation technology. Subsequent improvements to the plant have increased its daily output to 2,100 tonnes of urea in winter and 1,950 tonnes during the summer.
However, the high rate of dust formation from the urea solution spray nozzles remained an operational issue for GPIC, as is common with any plant running constantly above its nameplate capacity. Despite this, no loss of production occurred as any urea dust generated from the wet scrubbers was internally recycled back to the evaporation section.
Nevertheless, when operating the plant in this way, the overall process is limited by the capacity of the evaporation unit due to the high flowrate of recycled urea solution. It therefore became necessary to reduce the concentration of the feed urea solution to maintain reasonable operating parameters within the granulator. This in turn raised the moisture content, increased dust formation and created other operational issues.
All of these issues were addressed by thyssenkrupp Fertilizer Technology (tkFT) as part of continuous efforts to improve the UFT® fluid bed granulation process to meet customer needs. Specifically, tkFT investigated how to improve the two-fluid spray nozzle design – working together with one of the most renowned spray nozzle producers in this field.
Following phase doppler anemometry (PDA) lab tests, selected spray nozzles types were benchmarked against the standard UFT® spray nozzle at tkFT’s batch-operated pilot plant. The new spray nozzles were tested under identical conditions, in terms of urea concentration, formaldehyde content, fluidisation air, load per sprayer, etc.
The goal of these pilot plant tests was to improve the spray pattern of the urea solution droplets. The main aims being to reduce the amount of dust generated, as well as the build-up rate of scaling on the granulator walls, while maintaining excellent product quality and increasing stable operating time. Operationally, the objective was to significantly extend the duration between granulator washings (the running cycle intrinsic to all fluid bed granulation processes) and therefore reduce the flushing work carried out by the operator.
Based on the successful pilot-scale test results, a spray nozzle prototype was installed at GPIC’s commercial urea granulation plant in Bahrain. This was operated at very high production rates (more than 20 percent above nameplate capacity) under very harsh conditions, especially during the summer.
The results of the pilot- and industrial-scale demonstration tests proved that advanced spray nozzles can deliver a significant reduction in dust generation of 30 percent or more. This improvement is achieved while keeping the process parameters within an acceptable range. This makes a retrofit of an existing urea granulation plant feasible – without major mechanical modifications to any of the related equipment.
The advanced spray nozzles significantly reduce the dust load on the exhaust gas scrubbers. As a consequence, by reducing the amount of recycled urea in the evaporation unit, it is possible to increase plant output and improve the running cycle while maintaining final product quality.
The gains in operational performance of the GPIC granulation plant from reducing the amount of dust generation are clearly shown by process data. These were collected over a three-year period following the installation of the new spray nozzles in late 2018. The number of annual granulator washings was reduced by more than half, compared to the period before the newly developed UFT® spray nozzles were installed. Correspondingly, the average granulator run time between these washings was also doubled. The plant’s uptime and overall performance also benefitted from the shorter time required to wash the granulator.
This improved performance (Figure 1) was also due to the excellent learning curve resulting from the cooperation between the plant’s operator GPIC and the process licensor tkFT.
“Even three years after the installation of the new UFT® spray nozzles, I am amazed about the performance our plant can achieve,” said Abdulmunem Alnajjar, the urea superintendent at GPIC’s plants operation department. “The investment paid out in no time, especially since the implementation can be done in only a few hours and no big and expensive revamp is required.”
Subsequently, these new types of UFT® spray nozzles have been installed at two new large-scale urea plants (3,500 t/d and 1,750 t/d capacity) constructed in central Asia in 2018 and 2020. These have achieved outstanding results in terms of product quality, production flexibility and operational reliability. Based on these results, we are confident that many more urea granulation plants can be refurbished and adapted to benefit from advanced UFT® spray nozzles.
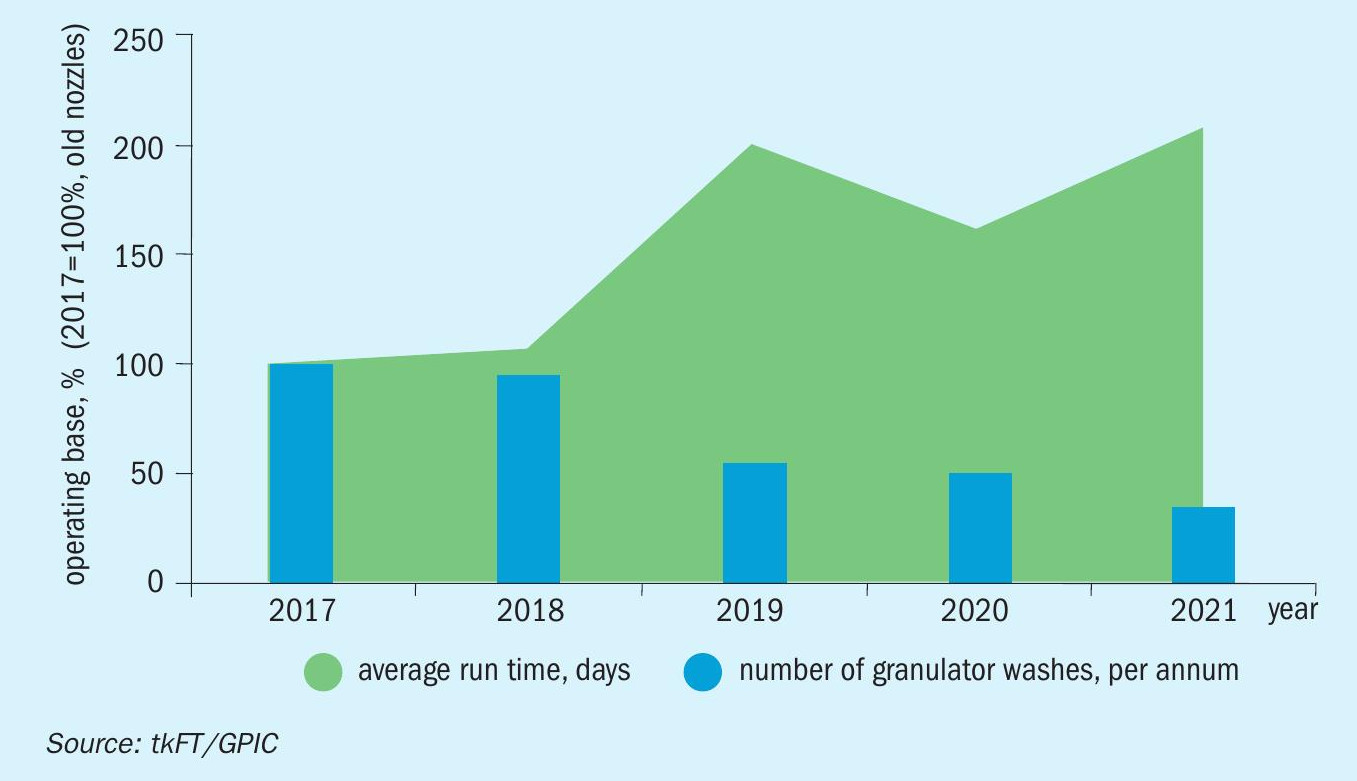
EIRICH
Granulating fertilizers for a cleaner environment
Thanks to the availability of fertilizers, we are able to produce enough food to feed the world’s ever-growing population. But, as with all natural resources, supplies of fertilizers such as potash and phosphate are inevitably limited. Fortunately, the ability to deliver fertilizers in granular form can play an important role in ensuring that valuable and finite plant nutrient resources are manufactured and used efficiently. Furthermore, Eirich’s innovative SmartMixer makes the production of fertilizer granules particularly simple and cost-effective.Rising demand and energy costs push up prices
Thankfully, the world economy has recovered significantly since the start of the global Covid-19 pandemic. But, as demand has recovered, energy costs and raw material prices have also reached record highs – making fertilizer production much more expensive. The costs of nitrogen and phosphate fertilizer production in particular rose substantially in the second-quarter of 2021, as shown by the World Bank’s Global Fertilizer Price Index.
Even if prices begin to stabilise in the short term, analysts still expect further rises over the next few years. This will make it more important than ever to manufacture and use fertilizers as efficiently as possible.
Granulation – keeping fertilizers in fine shape
Arguably, even the best fertilizers have little worth if nutrients cannot be applied to crops in the correct proportions at the right rate. This simple fact is what continues to keep the demand for granulated fertilizers high. Especially as stable, round and free-flowing granules are needed when applying fertilizers with a centrifugal broadcaster. Granules with these characteristics can be applied optimally across the field to deliver an even distribution of nutrients over the soil.
In commercially-available fertilizers, a range of different nutrients need to be combined together within each and every granule. This helps to ensure that individual plants are supplied with all the nutrients they require (Figure 1).
In addition, it is also best if a continuous supply of nutrients is available to crops during the growing season. Excess nitrogen in the soil, for example, can be harmful to the environment. In controlled-release fertilizers (CRFs), granules are coated to slow down the release of nutrients and ensure a more uniform supply to plants. The use of CRFs also avoids the need to frequently re-apply fertilizers. This significantly reduces the workload for farmers, saves resources and protects the environment.
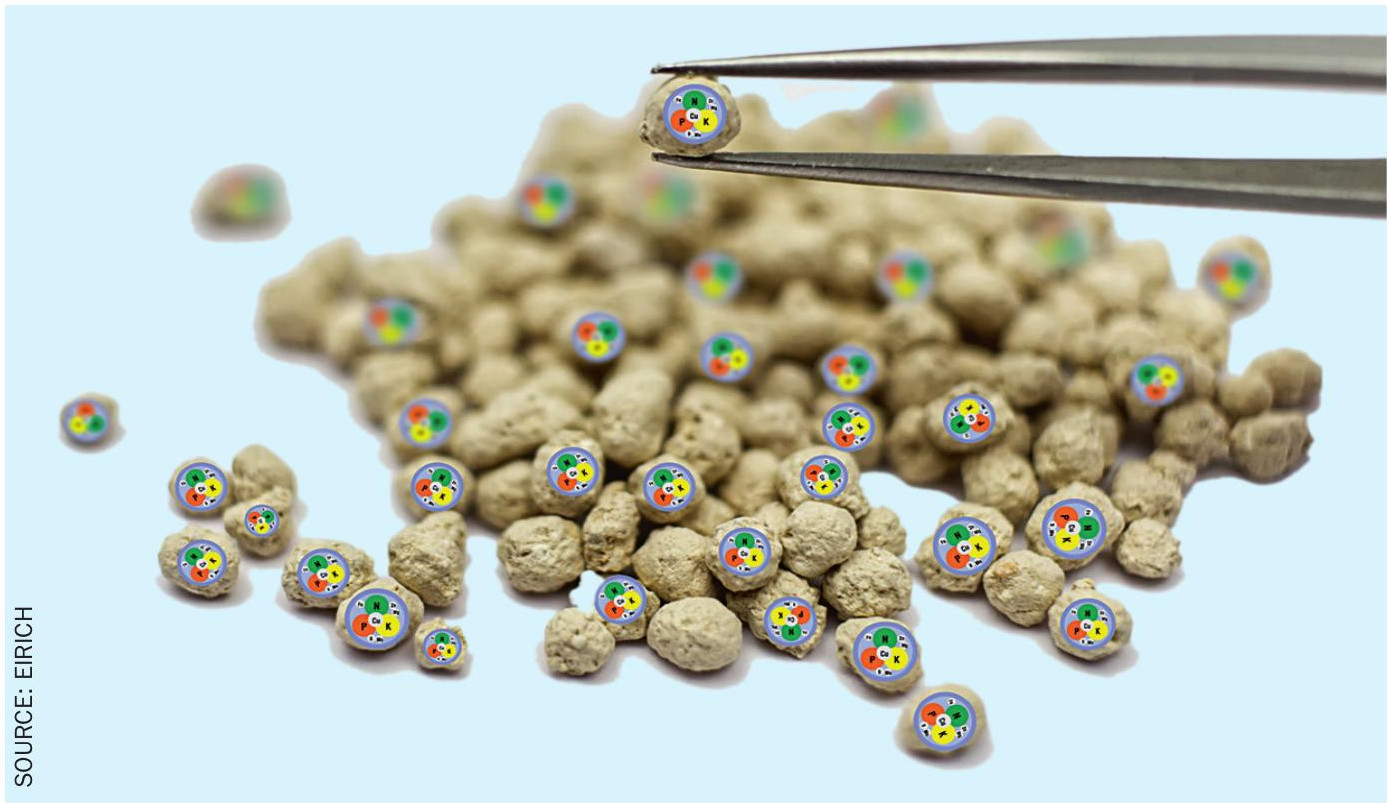
Eirich SmartMixer – an ideal granulator
The Eirich SmartMixer is capable of mixing, granulating and coating raw materials within one single item of equipment. It operates rapidly and can granulate powdered materials in a matter of minutes (Figure 2). Chemical reactions can also be carried out within the mixer quickly and completely. In many applications, the SmartMixer combines individual processes together – enabling, for example, a homogeneous mixture to be produced from filter cake, dusts and slurries etc.
Within the mixer, water is firstly added to uniformly moisten the powder mixture. Forces of adhesion then act between the particles leading to the formation of granules. It is also possible to add binding agents or other additives to the granulating fluid – typically water – as required. The addition of a binding agent increases the strength of granules to ensure that these will not disintegrate under mechanical stress. When required, larger pellets (510 mm size) can also be produced using a disk pelletizer unit.
The SmartMixer combines fully-automated mixing and granulation processes in a single system. By combining individual processes in this way, Eirich can create a complete fertilizer production plant – one that is capable of continuously manufacturing fertilizers to consistently high quality standards around the clock (Figure 3).
Many straight fertilizers are used as important constituents of compound fertilizer mixes. They can also be granulated individually to improve field distribution and reduce dust formation. Examples of popular straight fertilizers include:
- Potassium sulphate (sulphate of potash, SOP, K2 SO4 )
- Potassium chloride (muriate of potash, MOP, KCl)
- Ammonium sulphate (AS, (NH4 )2 SO4 )
- Diammonium phosphate (DAP, (NH4 )2 HPO4 )
- Polyhalite (K2 Ca2 Mg(SO4 )4·2H 2 O) etc.
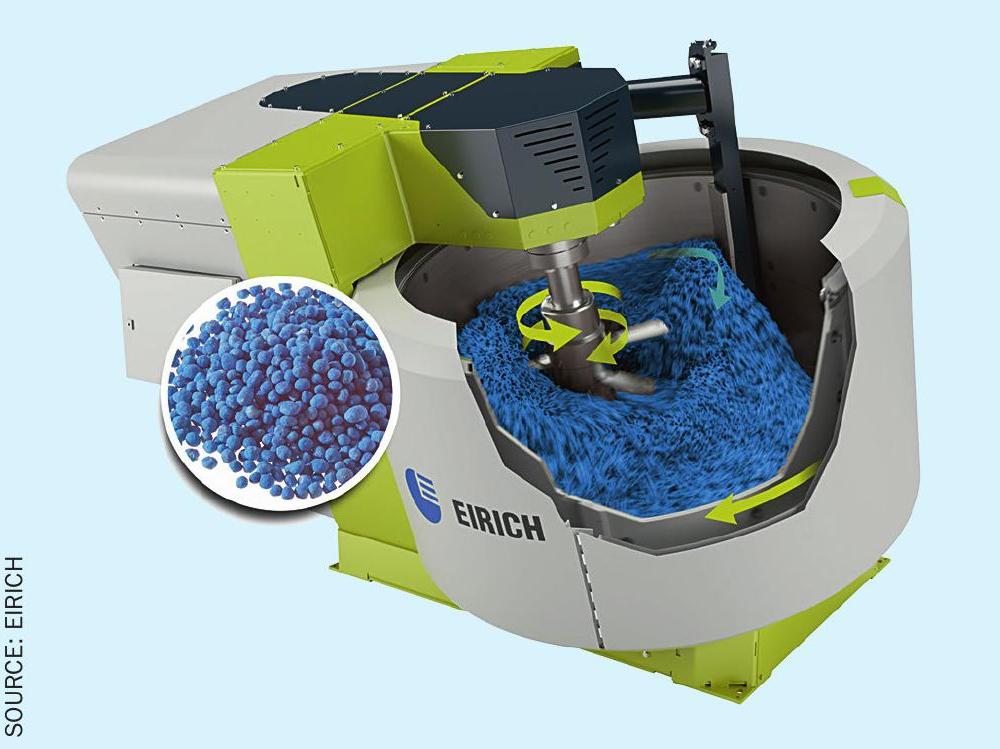

The goal of granulation is to produce uniform and round granules with a target size of 2-4 mm. High throughput rates of several tonnes per hour are required for the main straight fertilizers listed above. High capacity R28 and R33 type Eirich mixers are therefore used for this purpose (Figure 4). Eirich can offer a range of customised granulation processes capable of manufacturing large amounts of granular fertilizers.
Dissolving minerals with acids
Phosphate rock can be dissolved in sulphuric acid at industrial scale to manufacture superphosphate. This process can be carried out particularly quickly and efficiently in an Eirich mixer. Dissolution in acid transforms the insoluble apatite (calcium phosphate) present into a soluble and plant-available form of phosphorus. Similarly, the valuable nutrients present in other insoluble minerals can also be made more available to plants by treatment with sulphuric acid or phosphoric acid. Serpentinite, which contains magnesium silicate, is one example.
Eirich has installed a modern production plant in Paraguay which uses serpentinite to manufacture fertilizer. This plant combines a RV19 Eirich mixer with a TR36 disk pelletizer. The serpentinite rock is crushed, ground and then dissolved with sulphuric acid in the mixer. This generates a moist reaction product which readily forms granules in the disk pelletizer. The soluble end-product obtained via this process is applied as fertilizer to soils to improve the growth and yield of maize and grain crops.
Wood ash – a valuable resource
It has long been known that wood ash can be used to fertilize crops, as it contains many nutrients that were stored by the trees during growth. The phosphate content of the ash is particularly valuable, as is the potassium, magnesium, and calcium it contains. The presence of these elements as carbonates also helps to neutralise the pH of acid soils. However, highly alkaline ashes do need to be applied evenly. This fact has made the granulation of wood ash a very popular and successful option. Wood is consumed as a fuel on a particularly large scale in Sweden. Eirich mixers and disk pelletizers are employed to granulate the resulting ash which is then used as a fertilizer to replenish forest soils.
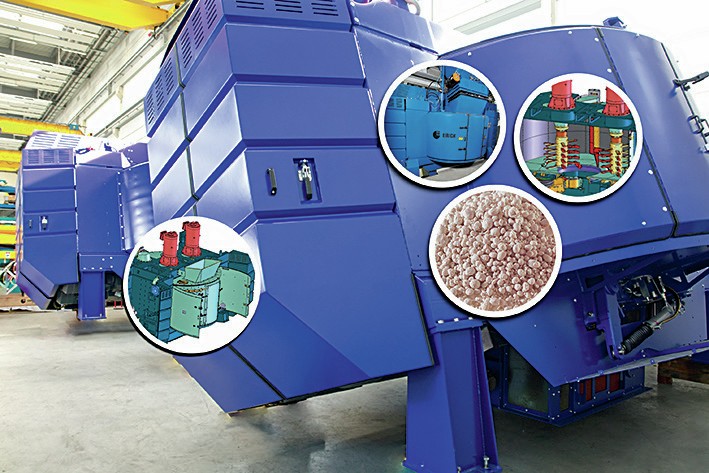
Recovering valuable resources
Because they are finite, it is becoming ever more important to use all natural resources both sparingly and sustainably. For example, phosphorus – which is in high demand as a fertilizer – is contained in large quantities in sewage sludge ash. This can be concentrated and recovered by the precipitation of struvite (magnesium ammonium phosphate). This can then be dried and granulated using an Eirich mixer which is capable of handling all the required process steps in a single unit.
The recovery and reuse of secondary raw materials is requiring new types of preparation processes and technologies. This is being done, for example, in Duisburg, Germany with an Eirich RV24 mixer and TR36 disk pelletizer. These produce nutrient-rich microgranules for agriculture from gypsum filter cake and other compounds such as kieserite and iron salts.
Conclusions
Energy prices and the costs of raw materials look set to rise in the future. This means that the sustainable use of finite resources will become increasingly important. Cost-effective fertilizer finishing techniques such as granulation – by ensuring that fertilizers are used efficiently – can contribute to more eco-friendly agriculture. Granulation helps ensure that plants receive the nutrients they require in the correct amounts during the growing season. At the same time, granulation also prevents fertilizer losses due to disintegration and wash-out from soils.