Sulphur 397 Nov-Dec 2021
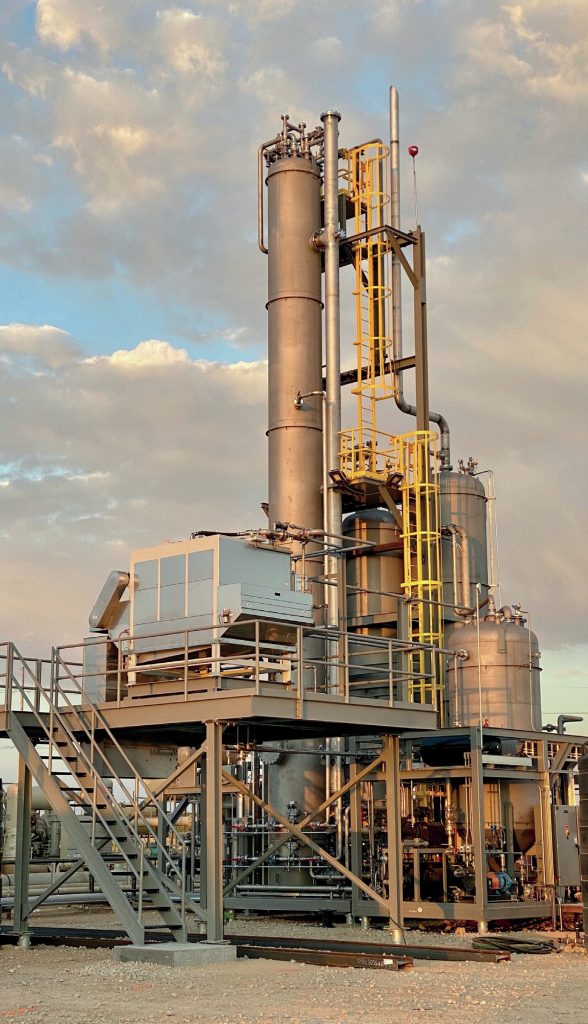
30 November 2021
Liquid redox going beyond the expected
LIQUID REDOX TECHNOLOGY
Liquid redox going beyond the expected
The Valkyrie™ process was first introduced as a reborn version of redox technology for treating H2S in natural gas processing.In this article Streamline Innovations Inc. highlights some of the new developments and successful applications of the Valkyrie process and its redox technology, in both gas and water streams.
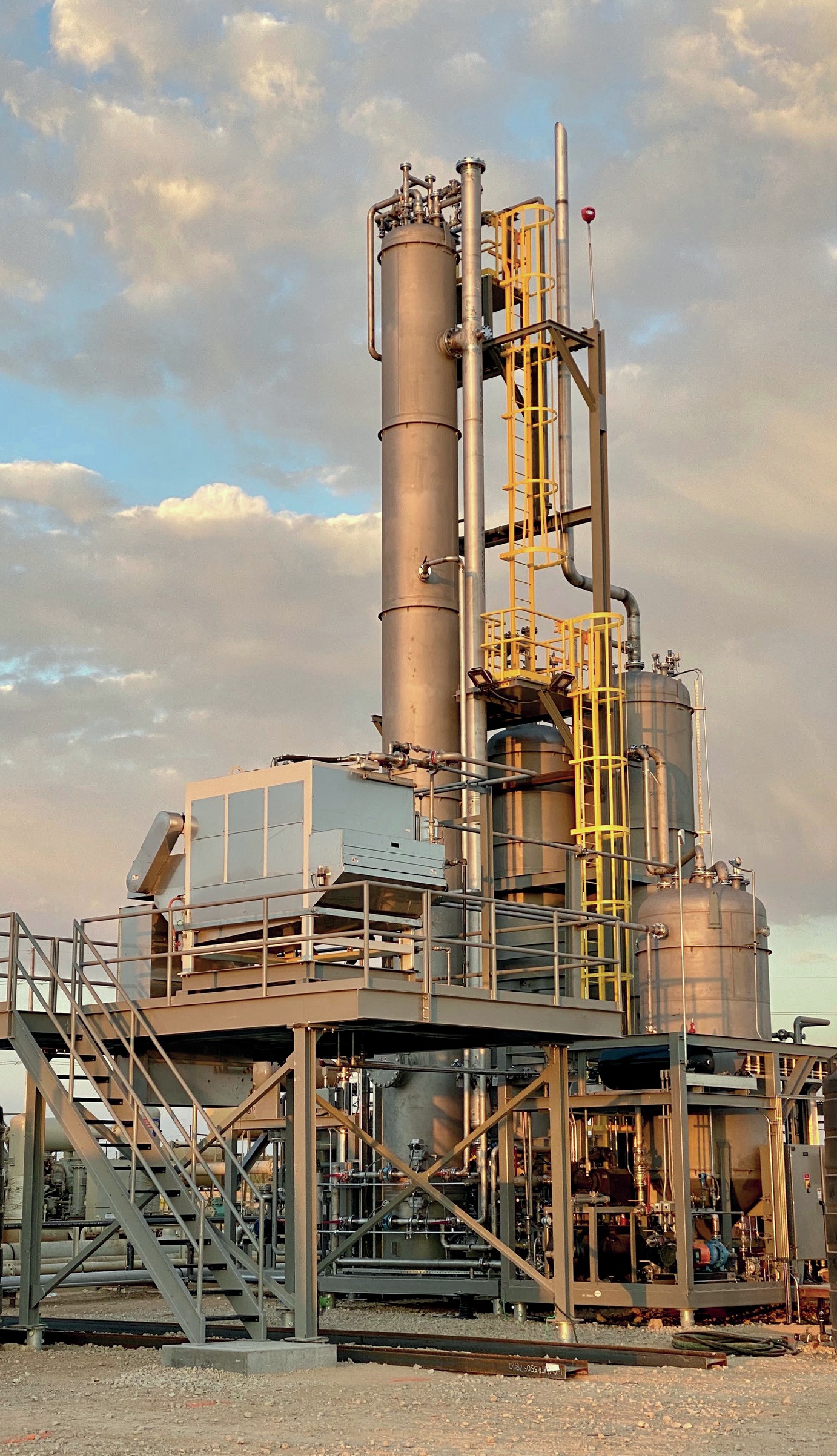
In Sulphur No. 387 March-April 2020, pages 46-52, Streamline Innovations Inc. introduced the Valkyrie ™ process as a reborn version of redox technology for treating H2S in natural gas processing. The Valkyrie process is a derivation of the original liquid redox process in which the chemical, Talon ™ , converts hydrogen sulphide (H2S) into elemental sulphur in a reduction reaction and regenerates when exposed to oxygen from air in the oxidation process. With a high specificity towards sulphides and a fast reaction rate, the Valkyrie process provides the efficiency of a scavenger with a significantly lower opex due to its regenerative chemistry.
The primary chemistry of the Valkyrie process, Talon, was designed to be environmentally forward and biodegradable. The recent rise in ESG and zero-flare initiatives has made its green characteristics an attractive alternative to hazardous triazine-based scavengers in the upstream oil and gas market, specifically in the U.S. shale gas sector.
Since 2018, Streamline has deployed 20 Valkyrie systems, with nearly a dozen more in development, and has expanded its technology to industries beyond upstream natural gas processing. Since the process is agnostic to the carrier gas (natural gas, CO2 , air, N2 , water), applications in landfill gas, renewable fuels, municipal and industrial wastewater treatment, and aerobic foul air scrubbing have all been added to Streamline’s repertoire.In parallel to its gas-based applications, water-based Talon is equally robust and efficient to treat dissolved sulphides in water and wastewater streams. In these aqueous applications, hydrogen peroxide, rather than oxygen, is generally used as the oxidation source due to its efficiency and ease of application. Streamline has commercialised and deployed its Talon Sulphide Elimination System (TSES), which provides a flexible process that destroys the underlying sulphide in the aqueous phase in either lead or lag configurations, providing odour control and preventing H2S off-gas scenarios in wastewater.
Some of the new developments and successful applications of the Valkyrie and its redox technology, in both gas and water streams are highlighted.
Acid gas treating
An oil and gas exploration and production operator in the Delaware Subbasin of the Permian in West Texas discovered its gas contained higher than expected H2 S. This region of the basin typically produces a higher gas-to-liquid ratio resulting in large gas volumes. Surprisingly, the operator found the gas containing a moderate level of H2S, ranging from 300 to 700 ppm, and a CO2 concentration ranging from 2% to 3%. With only ‘sweet gas’ pipelines available, the producer was required to treat to a maximum of 4 ppm of H2S and 2% of CO2 . The decentralised production infrastructure (with three separate gathering facilities) and the total production of sulphur (2-4 long t/d total) meant that the construction of a Claus plant was not an economically feasible option, leaving the producer to initially assume that a scavenger would be the only practical sweetening solution available. However, the H2S concentrations continued to increase as more wells were drilled, and with no sour gas sales pipeline available, the scavenger-based treatment quickly proved economically unsustainable.
Streamline performed a cost-benefit analysis and determined that with the previous investment in NACE-capable compression, combined with the high volume of gas and moderate level of H2S, the optimal treating configuration was to separate the H2S and CO2 with an amine plant at pipeline pressure, followed by removal of the H2 S from the acid gas utilising a Valkyrie unit. The resulting unit, called “Super-Valkyrie”, is an integrated smart amine plant directly coupled with a Valkyrie acid gas treating unit (Valkyrie AGTU).
Three units were constructed in parallel. Each unit was designed to treat 60 MMSCF/D at 900 psig on the 50 gpm amine plant, with a 1 long t/d Valkyrie AGTU. The Valkryie AGTU was modified from the direct treat Valkyrie to treat the acid gas stream with H2S concentrations ranging from 35% to greater than 50%. The design allows the desulphurised acid gas stream of nearly pure CO2 and water vapour to be sent to a small flare – without H2S present, dropping emissions of SO2 to below levels requiring Title V air permitting regulations.
Unique aspects of the Valkyrie AGTU include the following:
- Balance between low operating pressure and high H2 S in acid gas: The Valkyrie AGTU was designed to treat the extremely high H2S of acid gas at much lower operating pressure than a standard direct treat Valkyrie operating at field pressure. Because liquid redox treating is purely chemically driven and therefore less dependent on pressure of the gas, the primary design consideration was to balance the height of the Valkyrie contactor (required to provide enough reaction time) versus the amine overhead still pressure, which generates the head pressure required to overcome the liquid head in the Valkyrie contactor. A balance was achieved between increasing the pressure of acid gas off the amine still and the design of the contactor to achieve the desired treating units required to meet the outlet acid gas spec of <4 ppm of H2S.
- Temperature considerations due to high H2S exothermic reaction: Liquid redox treating of H2S creates an exothermic reaction. When treating extremely high H2S in acid gas, there is a significant reaction resulting in an increase in process chemistry temperatures of over 25°F. Design considerations for this temperature increase included process coolers, elimination of insulation to allow cooling from ambient air, and improving the efficiency of the reaction with a novel patent-pending contactor design.
- Smart amine integration with Valkyrie AGTU: To ensure seamless operation of the SuperValkyrie process, the process control logic of the amine needed to not just maintain temperature of the amine in the regeneration still, but also the pressure to ensure the gas can make its way through the Valkyrie contactor and out to the flare. This required some additional logic in the unit; future approaches will include model predictive control of the amine plant to provide efficient and automated operations. Additionally, logic was required to optimise the extent-of-reaction control in the Valkyrie unit that is crucial to the process; thus, integrated communications between the two units were required. For example, the Valkyrie unit predicts the outlet H2S concentration of the amine plant in advance to correct for treatment rates before the additional H2S even makes it to the tail gas treater.
Treating non-H2S sulphur species
Generally, upstream oil and gas operators in U.S. shale are only concerned with treating H2S in order to meet sulphur specs for the sale of natural gas into pipelines. Therefore, treating non-H2S sulphur species does not play into facility design, and often presents a post start-up challenge to operators. Treating these sulphur species can be difficult and many times require multiple processes to achieve success.
Whilst Talon is designed for hydrogen sulphide treatment, the highly reductive nature of the chemistry will also reduce other sulphur species, notably aryl sulphides (including COS), short-chained mercaptans, thiophenes, and even carbon disulphide. The resulting products are presumably disulphides that are eliminated with the elemental sulphur generated from the H2S.
A recent study in a gas containing significant fractions of mercaptan and other sulphur species being treated in a direct treat Valkyrie unit was performed and determined that carbonyl, methyl, and ethyl mercaptans were 95%+ removed from the gas stream, as well as a significant reduction in the corresponding sulphides. Thiophenes and CS2 were also reduced in the gas stream (see Fig. 1).
These sulphur species would otherwise present problems to the operator, or the corresponding midstream treatment facility.
Ultra low pressure packed tower treating
With the current trend towards renewable energy and the number of landfill gas, biogas, biofuel, and renewable fuel refineries increasing daily, adaptation of treating and production facilities must occur to match new design considerations. Many of these “non-geologic” gas production sources produce smaller volumes of gas and operate at pressures far below, what is seen in the oil and gas industry. As such, there is no appreciable pressure for the gas to transit production facilities.
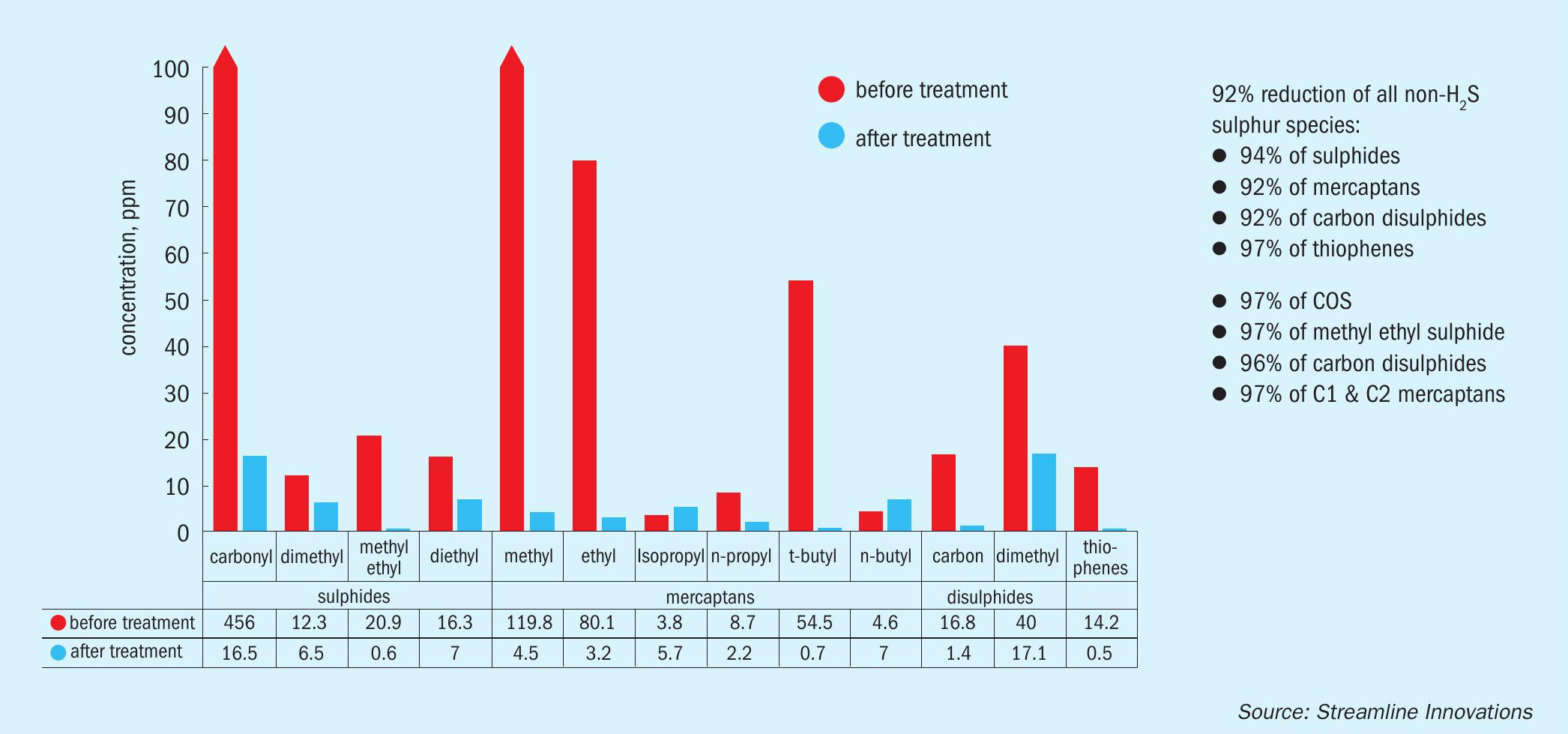
Additionally, and perhaps most notably, virtually every non-geologic gas production has some level of H2S. Achieving a low-pressure solution with a high sulphide removal capacity is imperative for these green energy sources. Talon, with its strong affinity for H2S even at low partial pressures, its biodegradability, and non-hazardous byproducts of elemental sulphur and water, is an ideal candidate for these applications. Utilising the sulphur for agricultural soil amendment even contributes to the ‘circular economy’.
Towards that end, Streamline has adapted its Valkyrie process to these applications. A small test unit is currently in operation treating approximately 30 lbs of sulphur per day at a small landfill in a pilot project, treating from 3,100 ppm to non-detectable levels, through a packed-tower system operating at 1 psig.
That project led to the construction of a large-scale plant at one of the busiest landfill sites in the U.S. situated in Northern Illinois. This unit contains a 70 ft tower with two sections, one containing a 25 ft packed tower and one as a gas-liquid separator. This system treats 7,500 scfm or 10.8 MMSCFD of gas at H2S levels ranging from 2,500 ppm to 5,000 ppm and is expected to come online by the end of 2021. The landfill gas gathering system operates with the assistance of a compression system that will pull 60 inches of H2O with an output of approximately 4 psig, and the unit will only require a pressure drop of less than 1 psi. This outlet pressure will allow the gas to be recompressed using a non-NACE compressor to undergo membrane separation to remove the CO2 and upgrade the gas to sales pipeline spec.
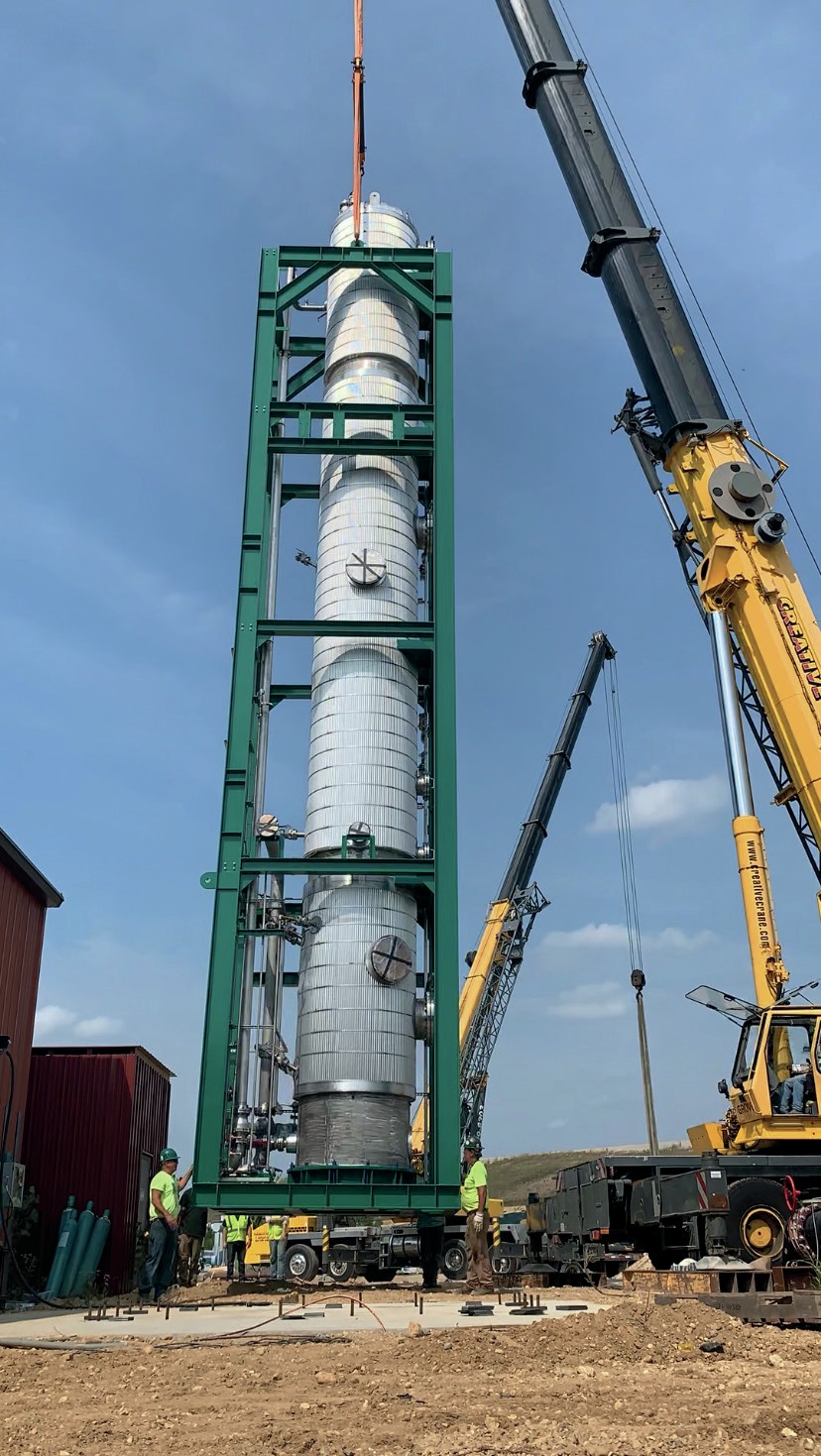
Sour water treating
Streamline’s Talon™ is equally effective at destroying sulphides in both the water phase and gas phase. At low pH, sulphide ions (sometimes called hydrosulphide, bisulphide, or HS– ) can bind to free protons in water and release gaseous H2S in the surrounding air. Commonly called ‘sour water’ in oil and gas processing and refining, sulphides are also regularly found in municipal and industrial wastewater. Streamline’s Talon is designed to eliminate the sulphides before this reaction can occur and volatise into H2 S.
The biodegradable redox chemistry is deployed in the aqueous phase through the Talon Sulphide Elimination System™ (TSES) where it breaks apart the sulphide in the same manner as in gas phase. The HS– in the sour water reacts with the Talon reagent where it first undergoes reduction, converting the HS– to hydrogen ions and sulphur, followed by oxidation and regeneration, through the application of an oxidant, generally hydrogen peroxide (Fig. 2). Hydrogen peroxide is a preferred oxygen source due to its ease of application as a liquid and its efficiency in reacting with Talon for the regeneration. The reactions are:
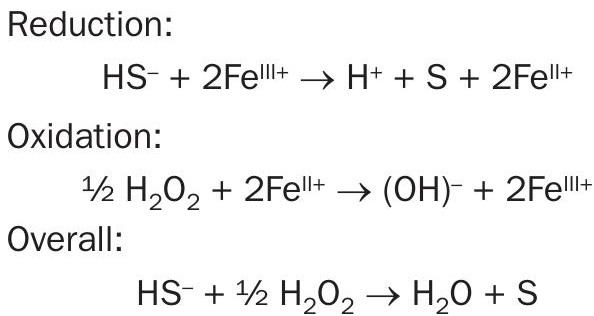
This process occurs nearly simultaneously in the same liquid stream, and therefore the application can be done in a pipeline setting, until all of the oxidant is consumed. The Talon-peroxide combination can also be very effective in more advanced processes, such as those used for reducing other organics and metals when little or no sulphides are present. When dosed correctly, the TSES will eliminate more than 95% of the sulphides in the first few minutes and will continue its redox reaction until no sulphides are remaining.
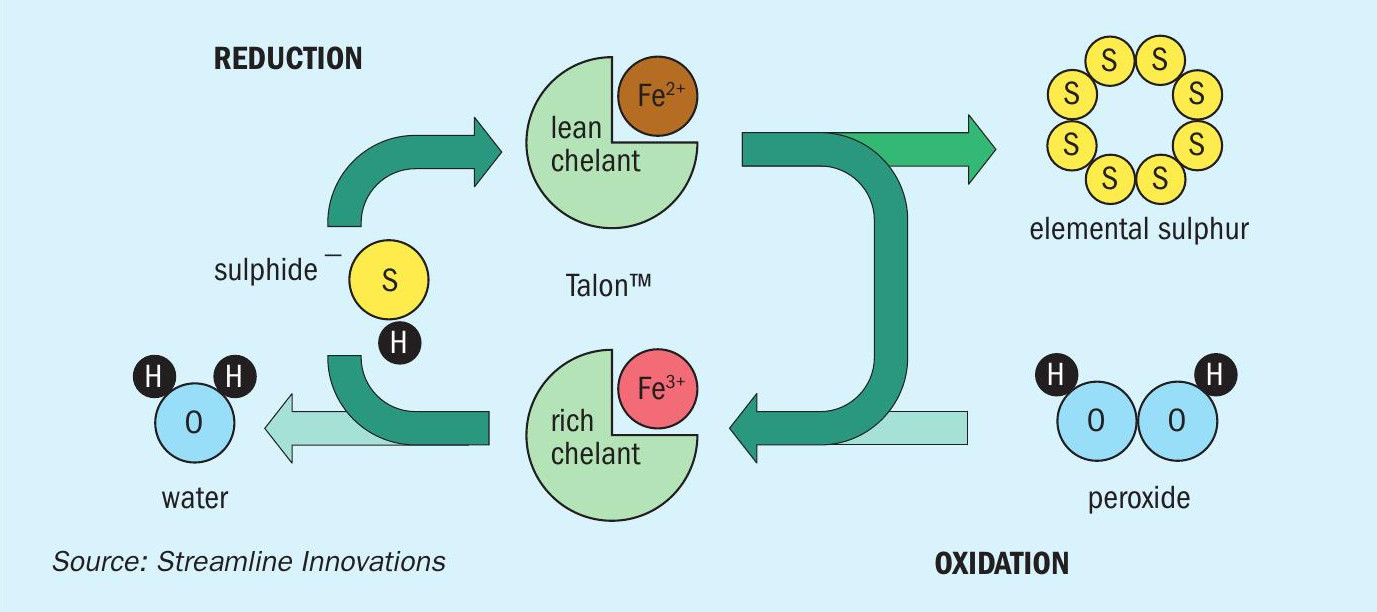
The TSES can be deployed across a range of applications including inline treating or after the water has been stored in a tank or pit. The TSES can also be deployed in a very simple manner or automated for flow pacing. In most applications, the sour water, Talon, and peroxide mixture flows through a pipeline or a reaction vessel where sufficient time is provided for the reaction to progress to completion. In automated systems, pH and ORP analysers will compare the oxidation-reduction potential, along with H2S analysers to ensure that sufficient chemicals have been added to completely destroy the sulphides. The sulphur formed in the reaction is a solid with an average particle size of 25 microns.
With automated analysers reading H2S, pH, ORP, and a flow meter, the data is used in a feedback loop to determine the quantity of Talon and peroxide necessary to react with the sulphides present in the water. Talon is injected into the water stream from a chemical storage vessel and is pumped using a metering pump into the sour water pipe through an injection quill. After adding the Talon reagent, hydrogen peroxide is likewise injected from its storage vessel using a chemical metering pump into the sour water pipe through a similar quill. The mixture then requires agitation to ensure proper contact between the chemistry and the sulphides. In certain cases, a static mixer or inlet side of a pump can maximise chemical contact with the sulphide.
Depending on the system configuration, the sulphur and any other oxidised precipitants can either be removed as part of a larger solids management program or direct filtration. If settled, the sulphur generally sinks to the bottom of the pit; in other cases, it rises with floating scum. The removal of the elemental sulphur solids can be accomplished by running the treated water through a self-cleaning back wash filter with dewatering box for the filtered solids. The filter is automated and can be spared for continuous operation.
Since the process relies on a straightforward chemical reaction, the equipment required for the TSES process is relatively simple, notably storage tanks for the Talon and peroxide, corresponding chemical injection pumps and quills, and instrumentation for reaction monitoring. This low-cost H2S alternative provides an efficient yet cost-effective method to remove sulphides in water.
There are a number of projects in which Streamline is deploying this technology, and the applications range from wastewater in industrial applications, produced water in upstream environments, and refinery wastewater. One of note is at a Claus SRU in the Middle East, where treatment has been successful in treating 500 ppm sulphides in a water stream down to non-detect levels.
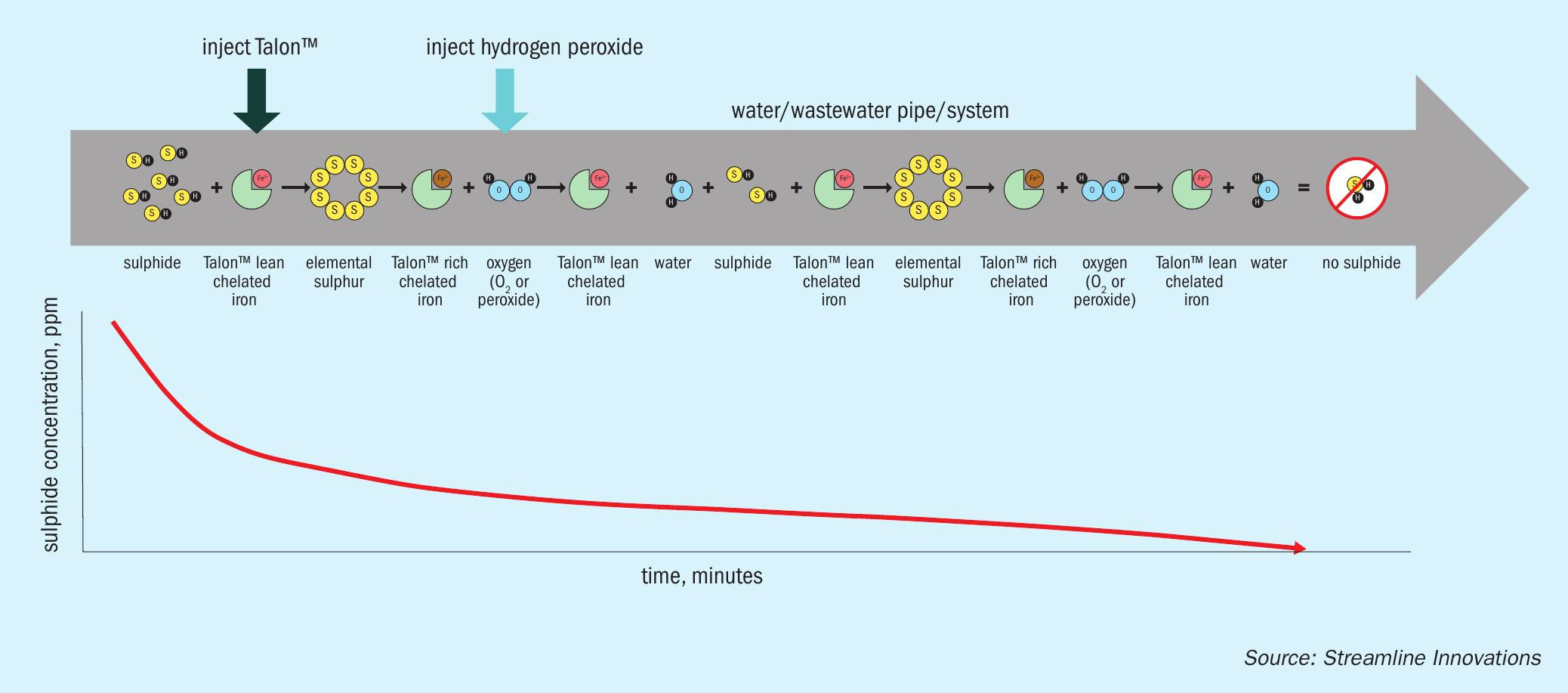