Nitrogen+Syngas 374 Nov-Dec 2021
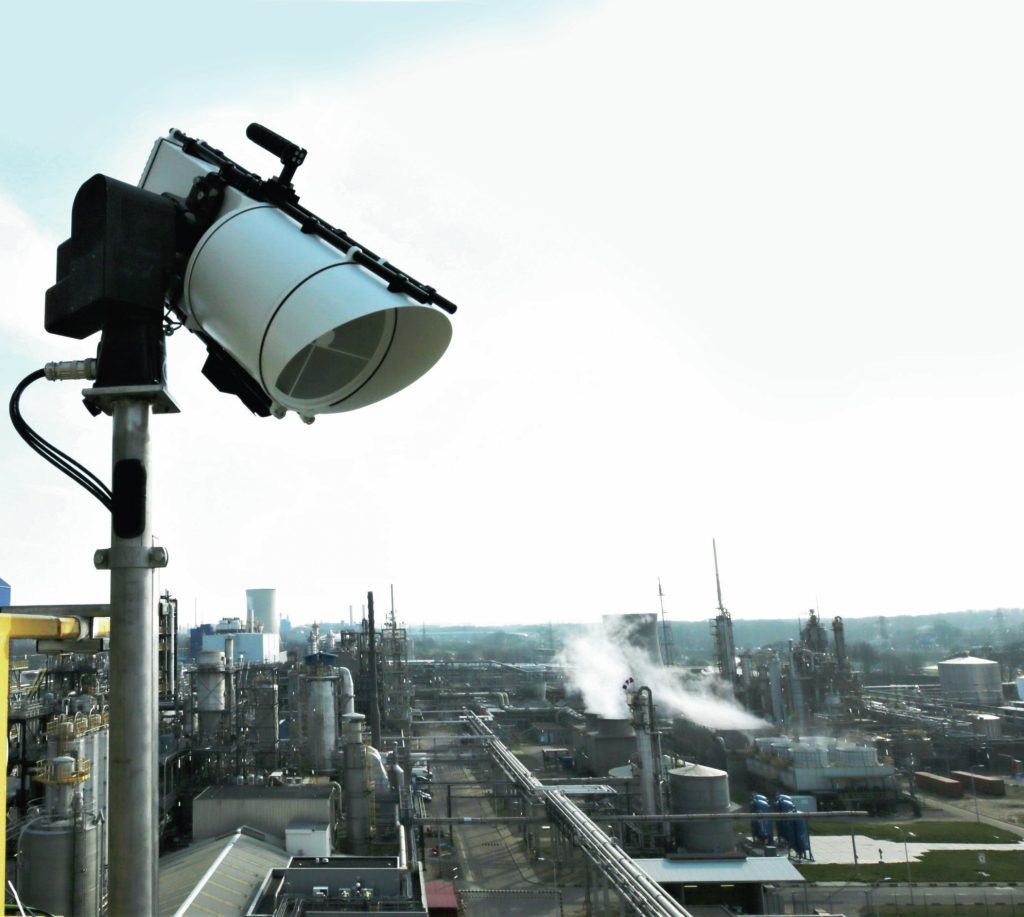
30 November 2021
On the lookout for gas leaks
AMMONIA EMISSIONS MONITORING
On the lookout for gas leaks
Scanfeld™ is the world’s first remote sensing solution for fully automated early-warning gas leak detection for chemical plants. Using FTIR spectroscopy, Scanfeld™ identifies hundreds of different gases in real time from kilometres away. With just a few Scanfeld™ sensor units, large production sites, tank farms, or gas loading areas can be monitored reliably. Gas leaks are quickly detected, and the formation of dangerous gas clouds is monitored, measured, and visualised. René Braun of Grandperspective discusses how the system works and how it is being applied in industry.
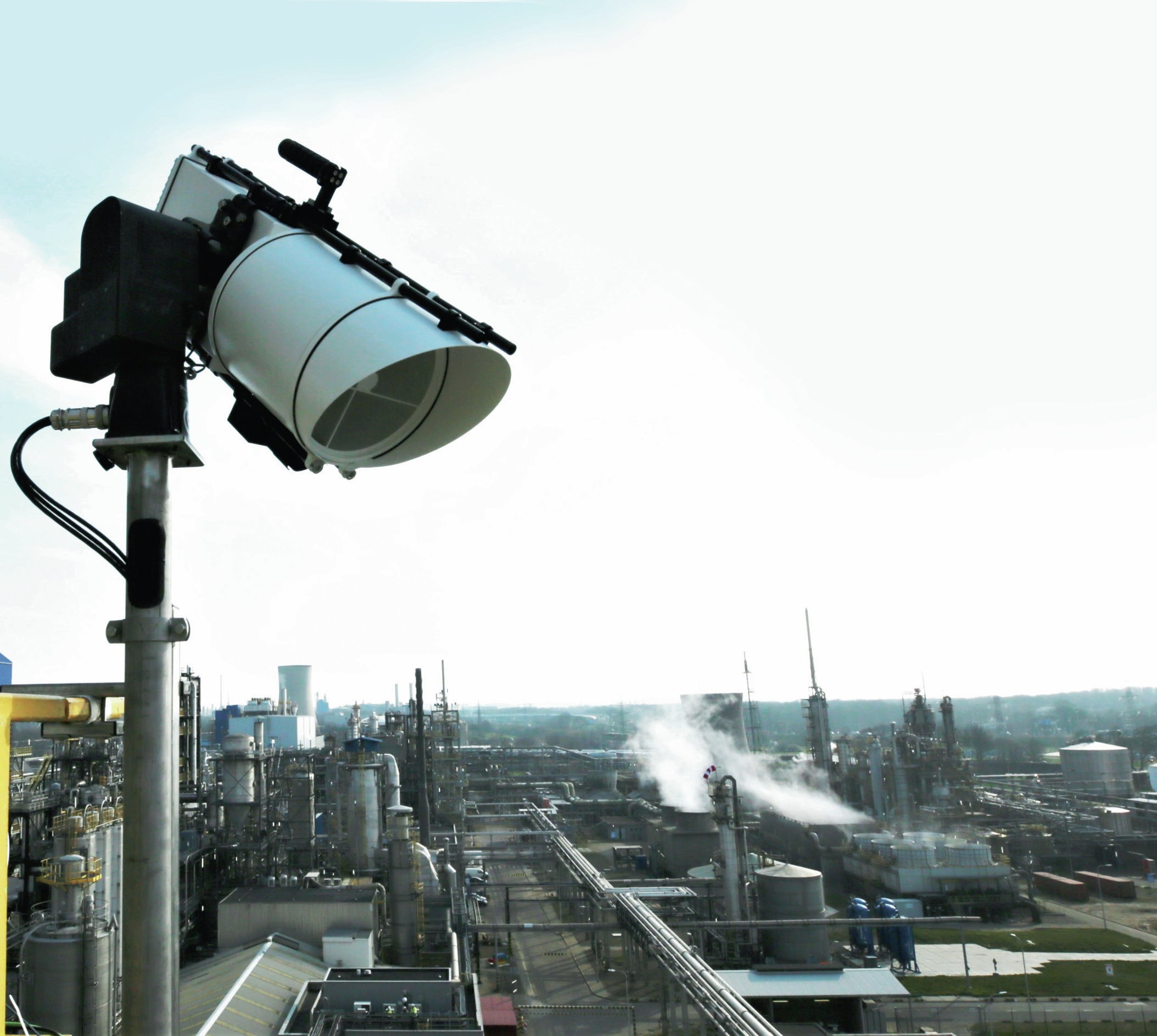
Industrial-scale chemical processes continue to expand year on year, and the volume of hazardous gases handled by these processes has equally grown, especially in the last ten years. One of the key bulk chemicals that requires tight monitoring is ammonia, and there has never been a more important time to monitor ammonia emissions than today.
The need for more efficient monitoring of ammonia, and other similar hazardous gases, has become paramount for a number of reasons. On the one hand, the global production of nitrogenous fertilizers continues to grow every year. These fertilizers use ammonia as the base material and are responsible for a production output of over 200 million t/a. On the other hand, the development of compact production sites, longer turnaround times, and fewer staff to man these plants are different factors that are enabling more emissions to be released into the surrounding environment, exacerbating any potential hazard risk.
Luckily, there are now solutions available, such as the Scanfeld™ monitoring system, that can help to monitor the emission of toxic gases. High-level monitoring is going to be paramount in the coming years for ammonia because new markets are starting to emerge, including using ammonia for fuel and in hydrogen storage, which will increase the demand and production of ammonia globally.
A concern to public health
Industrial sites are looking to be more carbon efficient and lower their carbon output (with the aim of having zero carbon emissions) and are regularly monitoring the output of gases into the local environment. This has become a more pressing matter in recent years because of the expansion of urban areas, as well as an increase in population densities, that are putting more and more people within reach of chemical sites that emit hazardous gases in sufficient quantities for it be recognised as a health concern.
Despite there being more concerns due to urban sprawl, a study published by the UK Health and Safety Executive (HSE) showed that around 30% of all major leaks go unnoticed and are silently contributing to health issues, physical damage, and even fatalities. In 2019 alone, billions of euros of damage were caused by undetected gas leaks, and in China alone, there were more than 800 undetected leaks and 400 fatalities. If you then look at the bigger picture across the whole world, then you start to understand the need for more efficient chemical monitoring operations in industrial-scale plants.
The challenges of remote chemical monitoring
Detecting gas leaks has always been a challenge, especially in industrial settings, and it’s no different today. It’s just that the dynamics have changed, and different technological options are now available to us. In years gone by, canary birds were used as a warning system to alert miners to high levels of carbon monoxide levels in deep coal mines. Since then, sulphur sticks have been used to detect ammonia leaks in refrigeration units, and the modern-day equivalent of early warning gas leak detectors is gas sensors that can report on minute levels of hazardous gas in a target area.
Gas sensors are a suitable option for many small-scale setups, but when it comes to industrial-sized plants, it’s a different scenario altogether. Setting up a system that can survey a large area, i.e., over a whole chemical plant, is the only viable solution for monitoring the industrial sites that are near populated areas. Having early warning systems in place is also key for any monitoring system, as the ability to detect hazardous gas clouds early not only protects the local workforce, but it also helps to protect the local urban areas as well.
The common approach to detecting hazardous gases has typically been to use a gas detector which provides a gas concentration as their output. Many gas detectors in use today are only single point detectors, meaning that they only analyse a single location of interest, so they can create a false sense of security as they don’t construct the entire emission picture across the entire plant. This means that pockets of gas can escape in areas where there is little to no analysis taking place, and these gas leaks will ultimately go undetected.
The only way to overcome this issue with single point sensors, is to place a sensor at every potential point of release. This is not only cost prohibitive, it is also a time-consuming solution, because each sensor needs to be calibrated and maintained by qualified personnel. The data also needs to be interpreted as well (introducing more cost), and if the sensors are not perfectly positioned, then the data can often be difficult to interpret and provide little value despite the cost and time investment.
These issues become more apparent when the production and storage areas of an industrial site become larger, as more sensors and personnel are required to operate these ineffective systems. Another issue of single point systems, especially in larger sites, is that they are not well-equipped for outdoor measurements where the wind will rapidly spread any gases in the different directions, preventing detection from taking place in a timely manner.
The openness to the elements is a factor that renders a lot of monitoring systems ineffective, because while the concentration of the gas is 100% at the initial point of release, the gas cloud can propagate in all directions and dilute very quickly, leading to undervalued results for major leaks and overstated results for minor leaks. So, rather than looking at single points of measurements that are inaccurate, the future of remote chemical monitoring needs to look at the whole industrial landscape as a complete measurement, rather than as a collective of individual data points that don’t give the whole picture and the true gas concentrations in the area.
FTIR to the rescue?
While there are a lot of issues with remote chemical monitoring systems in place today, there are alternatives to these ineffective and costly systems. Optical gas imaging (OGI) systems, for example, can provide coverage over much larger areas using infrared red (IR) light, but they lack the sensitivity and specificity required to measure real-time gas leaks. Also, like other detection systems, OGI sensors can only detect a single substance in a particular area of interest, so any deviation from a ‘normal situation’ can lead to false readings that are interpreted to be a gas leak.
On the other hand, there is Fourier transform infrared spectroscopy (FTIR). FTIR is known for its use in routine laboratory chemical analysis, but it is also a well-established remote sensing technique and is already used by security forces to supervise large areas in case of chemical release or terrorist attacks. One of the key features of FTIR is that it is a selective technique for hundreds of chemicals, and it is extremely sensitive to ammonia and other organic compounds. The other key feature of FTIR is the ability for it to be used like a giant gas camera from miles away.
The characteristics of FTIR mean that it offers a solution to the challenges of remote chemical monitoring: it is a sensitive technique for toxic gases, and it can be used to build a much wider gas leak picture compared to other sensing systems. These FTIR monitoring systems measure gas clouds by the spectroscopic analysis of infrared radiation. The internalised temperature within every object means that all object emits IR waves, and these waves can be chemically analysed from a distance.
For monitoring gaseous substances remotely, there is one wavelength region, from 500 to 1,500 cm1 , that is most relevant when analysing the chemical composition of a gas. This is known as the fingerprint region, and it is a spectral region where many chemical species interact with the IR radiation. This leads to an interaction with the radiation, a spectral absorption or an emission feature known as the spectral fingerprint, that is unique for each chemical compound, enabling the gas to be identified.
A modern-day solution for large chemical plants
Installing an FTIR sensing instrument is simply not enough for mapping hazardous gases over large areas of industrial-sized plants, you need something that has been designed and tailored to solve this particular problem from the ground up. This is what has been achieved by Grandperspective with its Scanfeld™ system, and it is the first FTIR remote monitoring solution to hit the market for probing suspicious spectral fingerprints within the chemical industry.
The Scanfeld system is more than just a gas camera. The Scanfeld sensors are a series of completely passive FTIR spectrometers that will continuously scan an area of interest and because they are attached to a sophisticated mechanical positioning system, the system allows for both imaging motion and 360° coverage of multiple scan areas. Each scanning point (a very narrow cone known as a Toxel) is represented by an infrared spectrum, which can then be analysed for the chemical composition of the gas and its concentration. The sensors are connected to an on-premises server which provides real-time control and measurement evaluation. The system then provides graded alerts based on the total amount of gas in the air, the gas cloud size, and the persistency of the event.
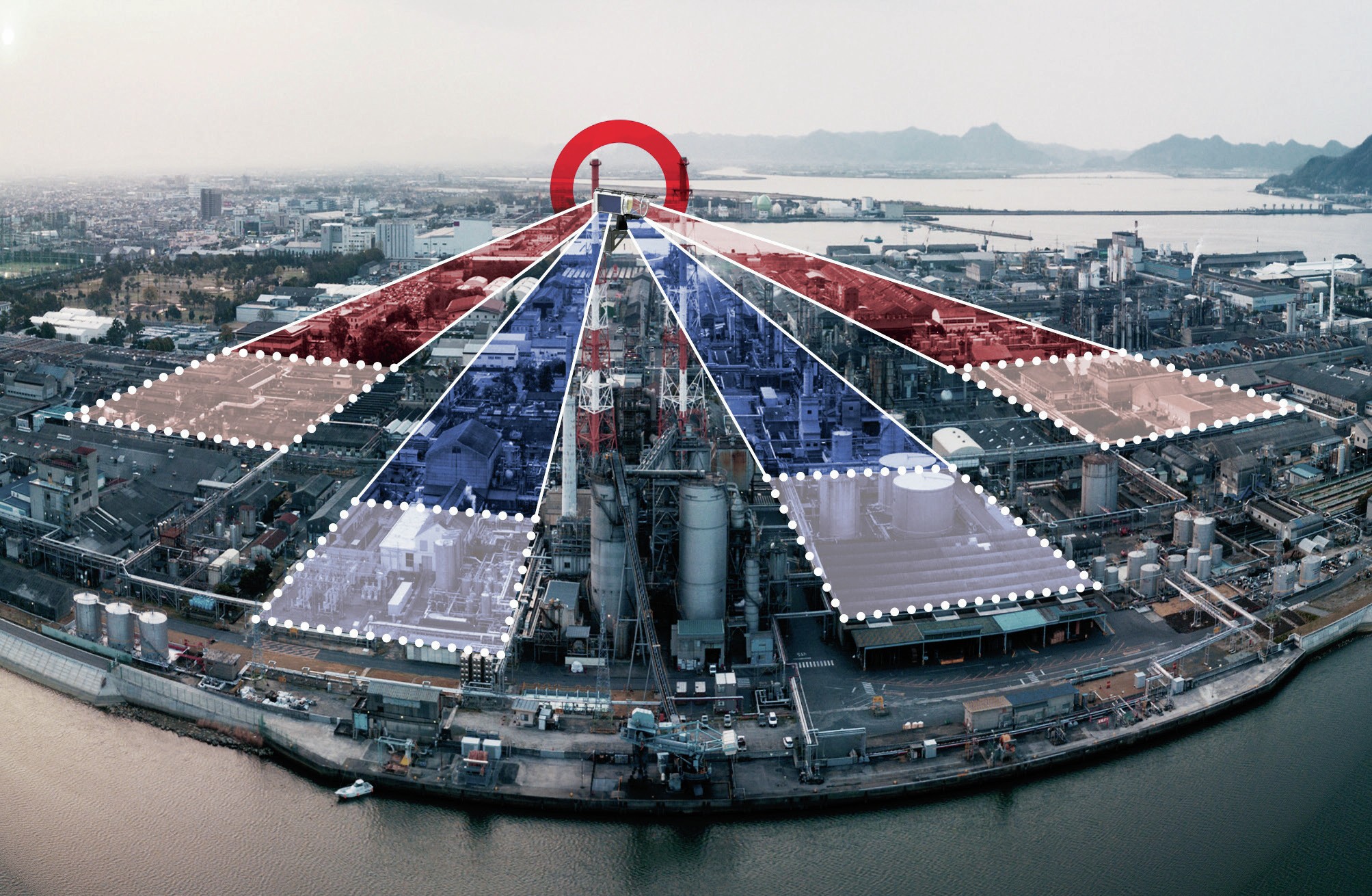
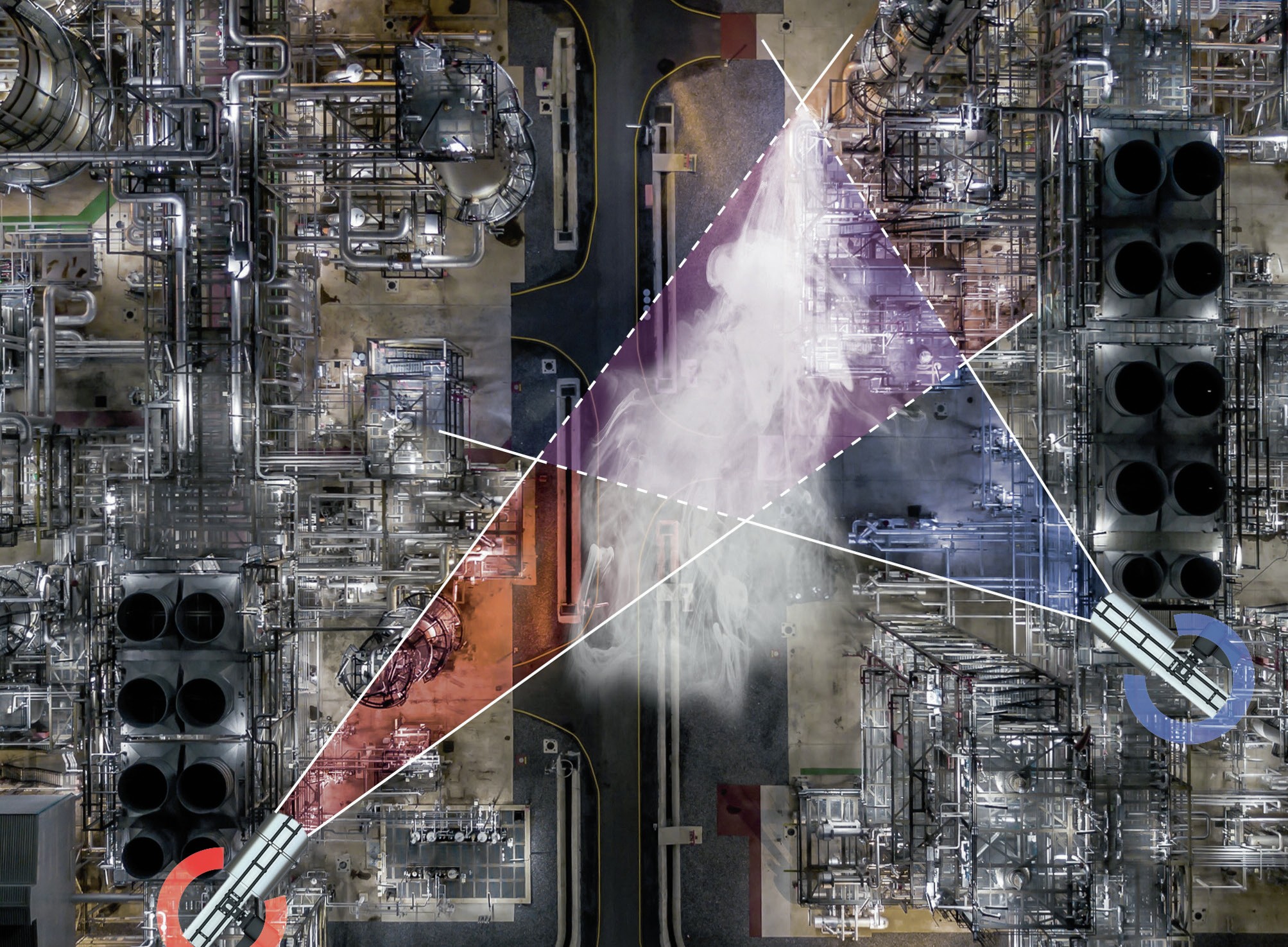
Key characteristics of Scanfeld
There are typically four functional pillars, the four Ws, to the Scanfeld system, which are where, what, how much and since when. This essentially means, that for over 400 chemical compounds, the Scanfeld system can tell you where the gas leak is, what gas has leaked out, how much of it there is, and when the event started. One of the defining features of the system is that only a single installation is required (so long as it is a tall spot) to scan multiple areas up to 4 km away from the sensing unit.
Compared to other remote sensing systems, Scanfeld has superior monitoring capabilities that extend beyond long-view sensing and a high specificity. Scanfeld has also been specially designed to be suitable for outside environments, and the propagation of a gas can not only be tracked over several square kilometres, but the local weather does not affect the capabilities of the measurement, including adverse weather conditions such as rainfall, fog, and low light.
The low light capabilities also means that Scanfeld can monitor in real-time 24/7, both day and night, and the concentration distribution of any gas clouds is measured in real time (including the actual concentration of the released gas). Unlike ground sensors, Scanfeld can change its field of view at any point and analyse any gas clouds at different heights.
A typical scan provides a real-time situation assessment with a timeline of events, but how quickly and how much you want to scan is completely up to you. The scan can be set up to automatically scan a pre-defined area, and the slower the scan speed the better the spatial resolution, but the faster scan speeds can cover larger areas in a single scan.
Most scans are performed within seconds and once a gas is detected the location and dimension of the gas cloud is measured. The user interface then provides an overlay image and details about the gas leak, including the leak location, the near-field propagation of the gas accumulation, and the concentration of gas in the air.
According to Peter Schmitz, HSE Manager OCI Nitrogen B.V.: “The Scanfeld system makes us feel safer in a couple of ways, first of all, the operators, as they have a second pair of eyes looking at the plant from a distance. And secondly, we have an early warning not only to our emergency response system, but also to our communities nearby, and I think that’s a great added value of the system.”
All these characteristics enable Scanfeld to improve safety in and around industrial chemical plants. The visualisation and alert system provide additional barriers to prevent the escalation of a gas leak when it has occurred, where the operator is first alerted to the leak, followed by the image visualisation of the leak so that appropriate action can be taken. While all the different characteristics of the scanning system are key to enhancing safety, it is the early warning and advanced mapping capability that set Scanfeld apart in terms of being a safe choice for chemical plants.
An effective early warning system
Time is the most crucial factor whenever there is a hazardous substance in the air, especially when it is a substance that is either toxic, flammable and/or combustible, such as ammonia. There is even more of a need for speed if these leaks are close to urban areas. If these types of leak events are not detected early on, there can be severe consequences to the environment and surrounding population, as well as posing a risk to infrastructure (including damage, production loss, and downtime).
“Time is the key element. You have to respond within minutes. Therefore, you need to get a picture in minutes to quickly inform the responders, the community, the operators, and everyone involved. I would say the present gas monitoring systems are not able to respond in a time frame like the Scanfeld system does,” explains Peter Schmitz.
Knowing every exact detail of these events when they occur is crucial to containing the spread of the leaked substance, but many other methods beyond Scanfeld fail to provide the detail required by first responders and firefighters who are responsible for managing gas leaks. The Scanfeld system combines the capability for early warning (no matter how small the leak) with precise information about the gas emissions and how they change over time. Once the release has stopped, the sensors also play a vital role in de-escalating the situation by confirming that the released gas has dissipated.
Mapping toxic gas clouds
The cloud profile of leaked gases is very different if the leak is outside compared to in confined spaces. Inside, detectors can spot the rising gas levels much more easily, regardless of where the source of the leak originated from. In wide open spaces, the gas rapidly dilutes when it moves away from the release point, so tracking the source of the leak with a traditional gas sensor is a near impossible task.
Scanfeld can not only perform near-field mapping for detecting the origin of gas leaks in real-time, but it can also perform wide field mapping for determining the concentration of the gas in the local area, no matter how much it has diffused and diluted. The speed of the scanfeld scan is also fast enough to map the propagation of gas releases, and this is what also provides an early warning when a gas leak occurs.
“Scanfeld is creating an overview. It is a totally different approach from traditional instrumentation, where you are only looking at certain points where we expect the ammonia to be. But a leak can be anywhere. You cannot be prepared for leakages in your whole plant by installing traditional sensors just everywhere. With the scanfeld system on a spot with a good overview it’s like having a million traditional transmitters,” said Patrick Thijssen, Lead Discipline Engineer Sitech Services B.V.
Being able to map the gas cloud dynamics across a wide area is a key factor in why Scanfeld is so effective, as it allows the gas concentrations to be determined across a wide radius of the incident. This allows the appropriate measures to be put in place to mitigate the effects of the leak. These analyses can all be done without any prior knowledge regarding the location of the gas accumulation, or the wind conditions, and allows for much wider areas of a chemical plant to be monitored automatically.
Assessing the gas concentration becomes inherently more difficult as the gas spreads and the affected area becomes larger. As the wind sweeps the gas cloud in different directions, the localised concentrations can rapidly change, and this is where local gas sensors become very ineffective as they present a false interpretation of the concentration of the gas cloud and a false sense of safety in the local area. This is where the wide field mapping function showcases the value proposition of the scanfeld system, as any widespread gas cloud can be continuously mapped and monitored in an ever-changing environment.
Chemelot: Scanfeld in real-world situations
Now, you might be thinking that the Scanfeld monitoring system is an interesting development and solution to the modern-day chemical monitoring challenges, but can it be used in commercial settings? Has it been tried and tested? The answer to both of those questions is yes. Scanfeld was recently implemented at the Chemelot industrial park in the Netherlands, because it is one of the largest chemical parks in Europe and is located in a densely populated region near Maastricht and Düsseldorf. The campus houses many chemical producers, with oil processing, hydrocarbons, ammonia, and fertilizers all being present on the site. So, in terms of safety, it’s a site that could pose more risk than a lot of others.
The first phase of the pilot project centred around a melamine and urea production unit and looked to reduce the risks associated with unexpected airborne releases, with the second phase being a feasibility study about the possibility to monitor the whole north side of the industrial park. There were four stacks of OCI Nitrogen in the industrial park that needed to be monitored for accidental ammonia release, with a focus on early warning.
Specifically, Scanfeld was also employed to protect the adjacent Brightlands Campus by monitoring any significant gas releases from the chemical plants. Each of the sensors covers a km range, so despite the large size of the site, only two sensor units were required to cover the entire area.
The installation at the Chemelot site provides an early warning detection within minutes of a critical gas release and can monitor the emissions that reach the Brightlands Campus. Once a gas release is detected, the software can generate a georeferenced representation of the cloud and track its progress. Scaling up the Scanfeld monitoring system with a just few more sensor units at the Chemelot site will cover the entire north side of the campus and provide enhanced safety measures over a much wider area.
Overall outlook
There are many options for gas monitoring. If you’re looking to monitor gas leaks in a closed environment, then conventional gas sensors will be fine, but if you’re looking to measure outside and over wide areas, then the Scanfeld solution provides the ability to monitor hazardous gas leaks and their diffusive spread in real-time.
Scanfeld is a highly automated monitoring solution that will continuously survey large areas in real-time and has been proven to be an effective tool at Chemelot, where the installation provides a very short response time to unexpected gas releases. The scanfeld system operates under a minimal time-to-alert principle and provides the exact information about the what, where, when, and how much of unexpected gas emission incidents.
Overall, Scanfeld offers additional protection barriers for large chemical sites while protecting the local area and population. Scanfeld also provides a quicker post-incident resolution by detecting when the released gas cloud has dispersed and is no longer posing a threat. While conventional gas sensors are advantageous in inside environments, Scanfeld offers a more cost-effective solution for remotely monitoring gas leaks in outside environments – with both wide and near field functionalities – because only a few installations are required to cover even large industrial parks containing multiple chemical plants.