Fertilizer International 505 Nov-Dec 2021
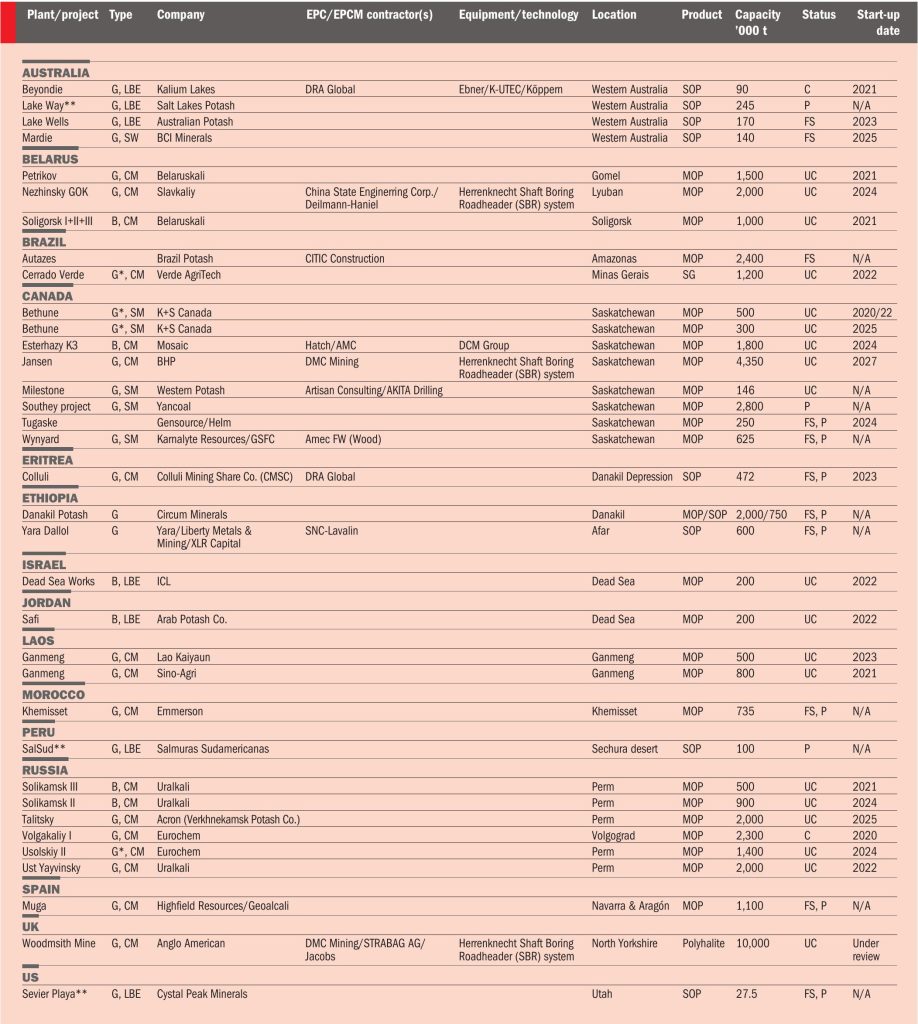
30 November 2021
Potash project listing 2021
PROJECT LISTING
Potash project listing 2021
Fertilizer International presents a global round-up of current potash projects.
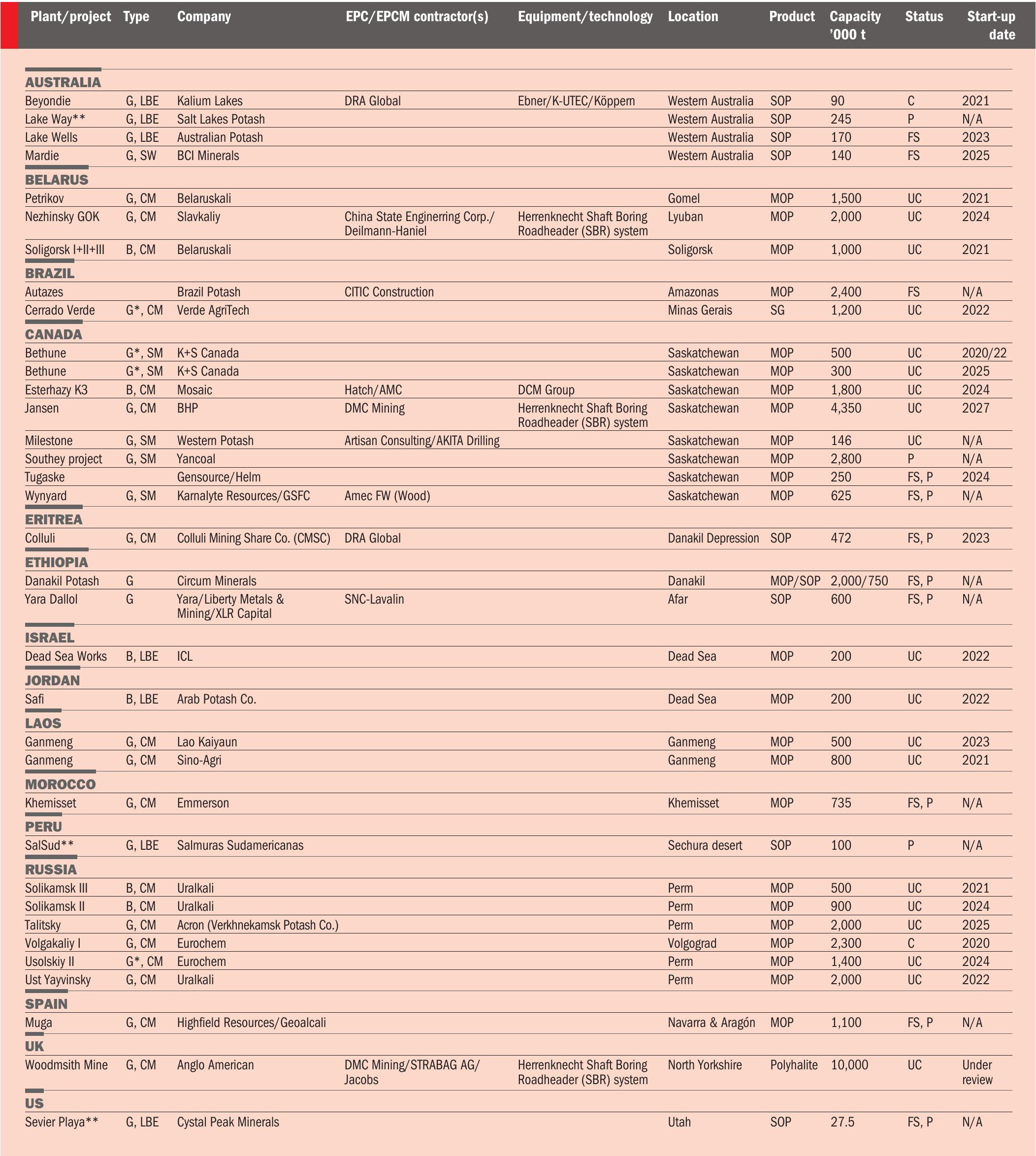
NOTES:
* Ramp-up/expansion ** Project on hold/under review
- Greenfield projects (G): generally, these must have reached the detailed/ bankable feasibility study (FS) stage for inclusion.
- Brownfield expansions (B): capacity indicates incremental additions, not total capacity.
PROJECT TYPE:
G Greenfield
B Brownfield expansion
CM Conventional mine
SM Solution mine
LBE Lake brine extraction
SW Seawater extraction
PRODUCT:
MOP Muriate of potash, KCl
SOP Sulphate of potash, K2 S04
SG Super Greensand, glauconite
STATUS:
N/A Not available or provided
PROJECT STAGE:
S Scoping
FS Feasibility study
P Permitted
UC Under construction
C Completed/commissioned
BHP
BHP greenlights Jansen potash mine
BHP has finally given the go ahead for stage one of its Jansen potash mine project in Saskatchewan, Canada. The delayed final investment decision, made on 17th August, commits the Australian mining giant to a further $5.7 billion investment to bring the project into production.
The Jansen project is located 140 kilometres east of Saskatoon, Saskatchewan, and is BHP’s most advanced under-development project.
The 4.35 million t/a capacity Jansen mine is now expected to produce its first potash ore in 2027, following a six-year construction phase. The mine will then take a further two years to ramp-up to full capacity.
BHP expects stage one of the Jansen mine (Jansen S1) to generate an internal rate of return (IRR) of 12-14 percent – equivalent to a payback period of around seven years – and operate at a healthy earnings (EBITDA) margin of around 70 percent.
“Jansen is located in the world’s best potash basin and is expected to operate for up to 100 years. Potash provides BHP with increased leverage to key global megatrends, including rising population, changing diets, decarbonisation and improving environmental stewardship,” BHP said in a statement.
Mike Henry, BHP’s CEO, said Jansen would help the company grow its portfolio of large, low cost and expandable world class assets.
“This is an important milestone for BHP and an investment in a new commodity that we believe will create value for shareholders for generations,” Mr Henry said. “In addition to its merits as a standalone project, Jansen also brings with it a series of high returning growth options in an attractive investment jurisdiction.”
He added: “Jansen is designed with a focus on sustainability, including being designed for low greenhouse gas emissions and low water consumption.”
The extra $5.7 billion investment in Jansen S1 covers the design, engineering and construction of a complete underground potash mine and all of its associated surface infrastructure. This includes a processing plant, a product storage building, and a continuous automated rail loading system. Jansen’s potash product will be shipped to export markets through Westshore in Delta, British Columbia, with the project’s new funding also covering the necessary port infrastructure.
“Jansen is located in the world’s best potash basin and is expected to operate for up to 100 years.”
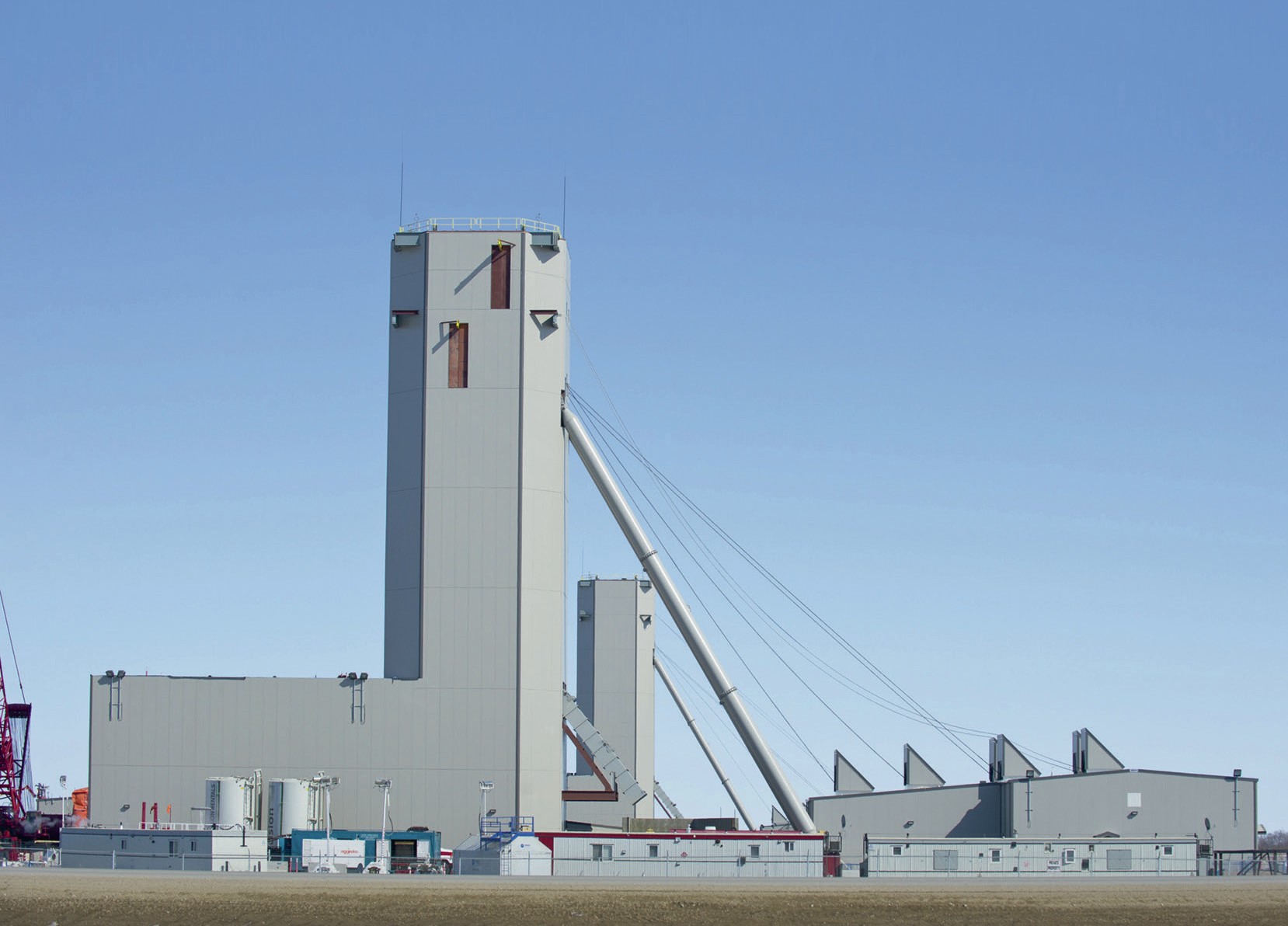
BHP said Jansen S1 is timed to arrive at an opportune moment for new potash supply: “We anticipate that demand growth will progressively absorb the excess capacity currently present in the industry, with opportunity for new supply expected by the late 2020s or early 2030s. That is broadly aligned with the expected timing of first production from Jansen.”
BHP predicts that Jansen will operate competitively, being positioned in the first quartile of the industry’s cost curve, especially given that it expects long-term potash prices to be set by Canadian solution mines. These tend to have higher operating and sustaining capital costs than conventional mines like Jansen, as well as consuming more energy and water.
BHP has already invested $4.5 billion of capital in the Jansen project to date. This includes a $2.97 billion investment in shaft construction and associated infrastructure, plus the funding of engineering and procurement activities, and preparatory work on underground infrastructure.
BHP acknowledged that the full project would yield a much lower IRR if its investment to date was included. “This resulted in a significant initial outlay and… our approach would be different if considering the project again today,” the company said.
The construction of Jansen’s two shafts is 93 percent complete currently, with both shafts and associated infrastructure due to be finished sometime next year. BHP estimates that around half of all the engineering required for Jansen S1 has now been completed, significantly de-risking the project.
Following a fresh valuation of its potash asset base, and a new calculation of the value of its investments in Jansen to date, BHP included an impairment charge of $1.3 billion ($2.1 billion after tax) against its potash assets in its latest financial results.
The Jansen S1 mine will convert approximately 20 percent of BHP’s 5.23 billion tonnes of measured and indicated resources into potash ore reserves. The mine’s earnings potential is based on average potash price assumptions for the decade 2027-2037 supplied by CRU ($341/t) and Argus ($292/t). Sustaining capital for Jansen Stage 1 is expected to be approximately $15/t, plus or minus 20 percent for any given year. n
ACRON GROUP
Acron triples Talitsky potash project investment
Acron Group is ramping up investment and speeding up construction at its Talitsky potash mine project in Russia’s Perm Krai region.
In a major step change, the company is more than tripling its capital investment in the project during 2021 and 2022, raising this from $60 million to $222 million. The company has also brought forward first production at the two million tonne capacity potash mine to 2025.
“Shafts are currently being reinforced and finished, construction of a motorway is near completion, and construction has started on the Ural 220/10/6 kV main step-down substation,” Acron said in a statement on 16th August.
Acron also revealed that it is currently tendering for equipment suppliers and contractors to fit-out the Talitsky mine, its surface complex, and external infrastructure. The project has also secured a package of Russian government support due to its positive impact on the regional economy.
Alexander Popov, Acron’s chairman, said: “In the current circumstances, we believe it is possible to accelerate construction to obtain the first batch of the product in 2025. Prior to the acute phase of the Covid-19 pandemic, we managed to dramatically improve the project’s risk profile by finalising the sinking of the shafts. Now, we can conduct construction operations both underground and on the surface at the same time.
“The project’s budget has been clarified. Remaining investments are estimated at $1.3 billion. Of this amount, approximately $700 million will be spent before the first batch of potash is produced. All of the project’s engineering and design solutions provide for further expansion of the mine’s capacity from 2.0 million to 2.6 million tonnes per annum of potash.”
“The project has also secured a package of Russian government support due to its positive impact on the regional economy.”
Famako Anlagenexport GmbH, with Ebner as subcontractor, secured the major engineering contract for the project. This encompasses project design and the manufacturing, delivery and start-up of a large-scale crystallisation plant (Fertilizer International 501, p52). n
OTHER PROJECTS
Kalium Lakes produces its first SOP batch
The Beyondie project produced its first batch of SOP in early October during commissioning, developer Kalium Lakes Limited (KLL) has announced. This makes Kalium Australia’s first SOP producer, the company said in an Australian stock exchange (ASX) release.
The 90,000-tonne capacity SOP project is located in the remote Pilbara region of Western Australia, about 1,400 kilometres north of Perth. The project reached financial close at the end of 2019. This financing included AUD 102 million of senior debt funding from KfW IPEX-Bank, with approximately half of this amount supported by a guarantee from Euler Hermes, the German government’s export credit agency. The company recently raised an additional AUD 50 million in capital to expand production output to 120,000 t/a.
Rudolph van Niekerk KLL’s CEO, said: “We are exceptionally pleased with the outcome of the capital raising. This is a very exciting time for Kalium Lakes especially having regard to the production of first SOP and subsequent ramp-up to 90,000 t/a production expected to be achieved by March 2022. “
Project commissioning entered its final stages in November. The performance of the SOP purification plant is said to be steadily improving, with some stages already running at or above nameplate capacity. Construction of the compaction plant is also nearly complete with contractor DRA due to finish work on this before the end of November. Production expertise, equipment and technology for the project is being provided by Ebner, K-UTEC and Koeppern (Fertilizer International 501, p52).
Major equipment purchase for Muga potash project
Highfield Resources has signed a contract with Weir Minerals to supply processing plant equipment.
The Australian developer is purchasing the items for its flagship Muga potash project in Northern Spain. This under-development project has an annual production target of 540,000 tonnes of muriate of potash (MOP) under current plans, with the potential to double output over the longer-term. Highfield plans to access international markets by shipping potash through the Port of Pasajes, San Sebastian, 150 kilometres to the west of the proposed mine. Production costs of $91/t (cost to port) are anticipated.
Weir Minerals is supplying the Muga project with both primary and secondary concentrate screens. These will be used for size separation during crushing, grinding and desliming. Hydrocyclones supplied by Weir will also be used to remove fine particles from the froth flotation feed (desliming).
Highfield Resources CEO, Ignacio Salazar, said: “The signing of this supply contract with Weir Minerals is key to ensure that we are ready for construction. This is another important milestone for Highfield and continues to highlight the progress and commitment of the company to the efficient construction of Muga.”
The purchase contracts for these long-lead equipment items, announced in late September, followed a successful AUD18.1 million ($13.5 million) capital raise by the company. Highfield said it expected to complete the purchase of all remaining items for the processing plant (cross-flow separators, dryers, thickeners and flotation columns) “in the next few weeks”. Any remaining equipment, mainly needed for mining, will be acquired prior to the start of operations, according to the company.
Having been granted a mining concession in July, Highfield is currently focussed on moving Muga to the construction phase. The project received its ‘DIA’ (Declaración de Impacto Ambiental) environmental permit – another major milestone – from the Spanish government in June 2019. Highfield says it is working closely with advisors Endeavour Financial on raising finance for the project. It is also negotiating a construction agreement and project implementation plan with preferred contractor Acciona.
High-Purity SOP production using Veolia technology
Veolia’s HPD ® crystallisation technology is capable of manufacturing high-quality water-soluble potassium sulphate (SOP, sulphate of potash, K 2 SO 4 ) using a range of different feedstocks. These can vary in quality and include sodium sulphate or other natural brines such as polyhalite, schoenite and even kainite.
World class R&D ensures project success
In the United States, Veolia’s state-of-the-art evaporation and crystallisation R&D facility, outside Chicago, offers a wide array of evaporators, crystallisers and ancillary equipment. These unique capabilities can be used to design, test and validate process flowsheets for commercial-stage production. The facility is an excellent tool when it comes to the identifying the most cost-effective process options and potential performance enhancements.
SOP production case studies
Upgrading potassium chloride to SOP: Importing chloride-free fertilizer for crop production can be prohibitively costly. To make SOP more affordable and locally available in Turkey, Turkish-based Alkim Alkali Kimya A.S. (Alkim), one of the largest sodium sulphate producers in the world, decided to invest in its Koralkim facility to produce up to 50,000 t/a of soluble-grade SOP.
Alkim awarded Veolia a contract to supply HPD ® crystallisation technology to produce SOP in crystalline, fully soluble form. The process involves a multi-stage chemical reaction between potassium chloride and brine saturated with sulphate salts from Alkim’s existing operation. This takes place inside draft tube baffle crystallisers that promote the growth of highly pure SOP crystals.
Veolia’s solution optimises capital investment by also including multiple-effect crystallisers that generate almost 35,000 t/a of food-grade sodium chloride as a by-product.
Producing SOP from brine: North American crop nutrient and salt producer Compass Minerals needed to expand SOP production at its US operations. Veolia successfully integrated its HPD PIC ® ™ crystalliser unit into the existing plant. This converts a brine feed containing schoenite into a high-purity SOP product, marketed by Compass as Protassium+ ® . Veolia simulated the process design and then validated this at its research facility. Veolia’s installed process, thanks to more efficient recycling, has enabled Compass to significantly reduce water consumption, relative to the existing SOP plant.
Creating SOP from pulp & paper wastewater: Another production option is to manufacture SOP from the waste streams of pulp and paper mills. In this process, glaserite (a double salt of SOP and sodium sulphate) is initially recovered via a black liquor ash treatment system and then converted into high-quality SOP crystals for fertilizer use. For this and other feedstock options, the crystallisation process holds the key when it comes to controlling the purity and size of the final SOP crystals.
“Veolia’s SOP production process has enabled Compass Minerals to significantly reduce its water consumption.”
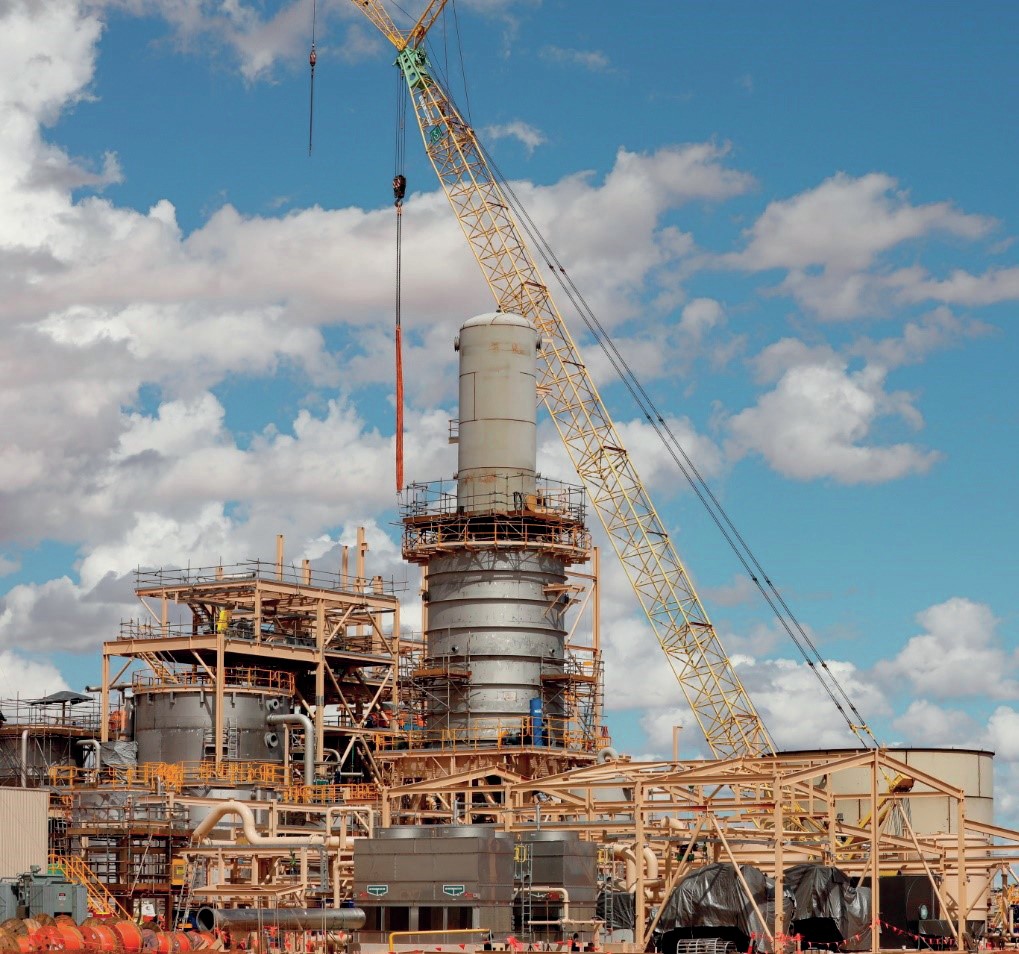
A pulping production plant in Brazil uses a washing process to increase the purity of the pulp. This generates an organic-rich liquor stream that is recovered for energy production. It is necessary, however, to remove chemicals from this liquor to avoid the undesirable build-up of chloride and potassium during the recovery cycle, as these can create corrosion and boiler fouling if left uncontrolled.
Veolia has successfully prevented this fouling and corrosion by treating 650 t/d of precipitator ash from the boiler using proprietary HPD ECRP ® ™ (Enhanced Chloride Removal Process) crystallisation technology. The ECRP ™ technology is highly effective at removing undesirable impurities from the client’s process. Valuably, it also takes a previously unwanted waste material and turns it into a useful fertilizer product for growing the next crop of trees for pulp production.
SOP for the future
As we move to a more ‘circular’ economy, companies will increasingly be looking to minimise their waste generation by investing in sustainable processes. This will shift the focus onto proven and successful production technologies that offer a triple win – for the bottom line, the environment and society.
As the above case studies show, forward-looking producers can now seize on higher-margin opportunities in the fast-growing agricultural market by producing specialty products. These can be manufactured from previously unexploited feed stocks, both profitably and sustainably, by incorporating innovative processes such as HPD ® crystallisation technologies.