Nitrogen+Syngas 374 Nov-Dec 2021
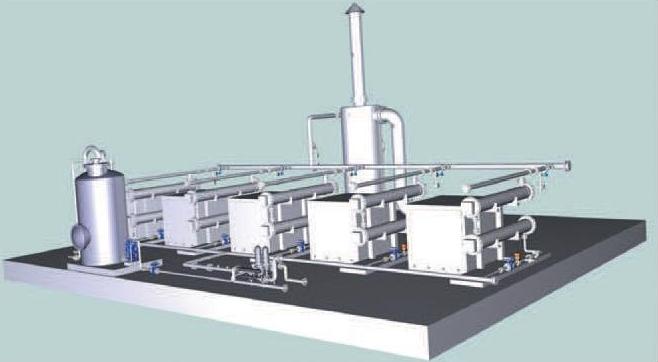
30 November 2021
Redefining the sustainability of effluent treatment processes
WASTEWATER TREATMENT
Redefining the sustainability of effluent treatment processes
Nitrogen-rich wastewaters remain a major issue for fertilizer and other industries. Saipem’s new electrochemical technology, SPELL, is an important step towards the overall objective of zero industrial pollution. A complete engineering review of the technology, its alignment with all international applicable standards, and optimisation has now been concluded and the technology is ready for deployment for the removal of ammonium nitrogen from industrial waters and wastewaters. Saipem discusses the key features of SPELL and reports on the first two industrial references.
Awareness of the sustainability of processes is changing; a renewed approach and rules for environment safeguarding are maturing worldwide, while technology innovation cells fight for domination of new markets. The new energy scene emerging in the coming years will be a mosaic of many competing forces, which is quite difficult to forecast today. What is clear, however, is that the speed of innovation and the adoption of new technologies will be fundamental to push continuous improvement towards the energy transition process.
Saipem is aware that all of its activities, from the planning and design stages to construction and operation, have an impact on the environment, both directly and along its business value chain. Saipem’s participation in the vision of a more sustainable future translates into the commitment to identify, assess, and manage environmental impacts tied to business management. To offer a distinguishable value proposition as system integrator, Saipem is committed to using advanced technologies, in the most efficient process schemes, and to deliver affordable management solution for specific purposes.
Growing pressure on water resources has driven Saipem to intensify its efforts on the development of new water technologies as a further improvement to its water resource management strategy. Of utmost importance are the investments in research and development programmes to create technologies that minimise the environmental impact of operations and associated services. For instance, one success story, as a result of effort spent on innovations for wastewater management, is the development of a special electrolytic technology capable of removing nitrogenous contaminants from waters and wastewaters.
Contamination of (waste)waters with nitrogenous compounds is one area of particular concern; this is a typical challenge for many industrial and municipal plants, and nitrogenous fertilizer plants are a primary example. The contamination caused by nitrogenous compounds is associated with severe environmental impacts including eutrophication of surface waters, toxic phenomena, and decline in biodiversity. Nitrogen (as well as phosphorus) is a natural part of aquatic ecosystems; it is a nutrient supporting the growth of algae and aquatic plants, which provide food and habitats for fish, shellfish and other smaller organisms that live in water. But high concentration of nitrogen in waters causes a perilous unbalance in the ecosystem: significant increases in algae harm water quality, food resources and habitats, and decrease the oxygen that fish and other aquatic life need to survive. Algal blooms can severely reduce the oxygen in the water, leading to illnesses and even death in marine life. Some algal blooms produce elevated toxins and bacterial growth, which are also harmful to humans coming into contact with polluted water, consuming tainted fish, or drinking contaminated water.
Current technologies to treat this kind of pollution are complex, costly, and unreliable, while nitrogen-rich (waste) waters remain a major issue for fertilizer and other industries. On the other hand, regulations and environmental limits are becoming more and more severe to limit the impact of this kind of pollution, even introducing bioassay practice with special requirements.
In response to the issue of nitrogen-rich waters and wastewaters, Saipem sought to find a solution by promoting a campaign to scout for innovative technologies; particular attention was paid to novel electrochemical technologies.
Many electrochemical processes for water treatment have been developed over the years, with the aim of reducing costs compared to traditional processes; the on-site production of necessary chemicals (e.g., by electrochlorination) is a common example. Moreover, electrochemical treatments are usually very efficient and reduce process retention times, thereby allowing smaller plants. With regard to the treatment of (waste)water, electrochemical processes have various advantages over other methods. They are robust, easy to operate and flexible in case of fluctuating wastewater streams. In addition, a relatively broad spectrum of organic and inorganic impurities can be removed1 .
The novelty of the electrochemical processes and their potential is widely recognised, and their specific applicability as an emerging technique for water treatment is captured in the BAT revision of 20162 .
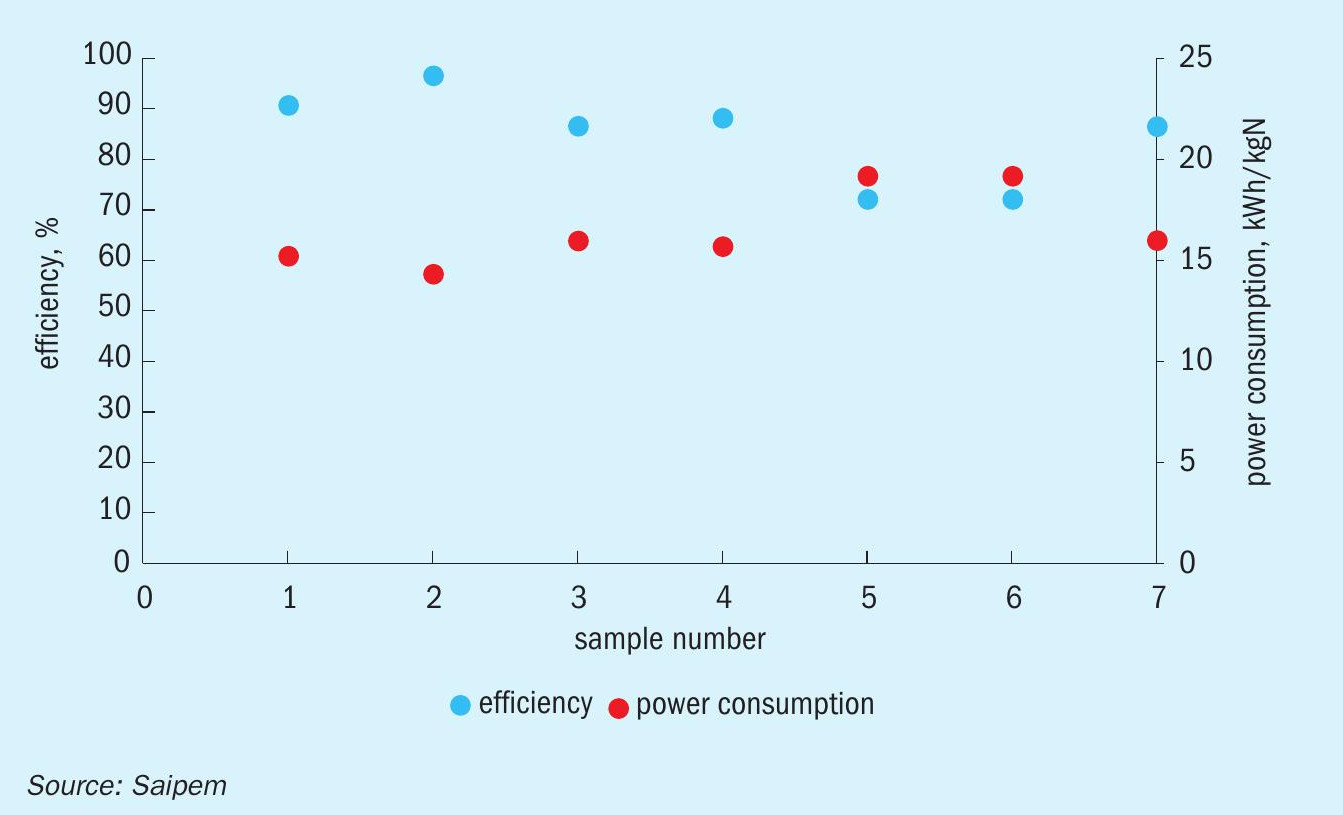
Electrochemical processes are associated to material transformations forced by or generating electric current. A distinction is made between electrolysis, in which the electric current is supplied from outside, and galvanic elements, for which the electrical current is generated by the reactions among the substances contained in the water (the latter not being implemented yet in practice or on a technical scale). Reactor designs are very specific regarding the various (waste)water compositions and the intended application; the designs and modes of operation of electrochemical reactors are therefore diverse.
In 2017, following a rigorous evaluation process, Saipem established a collaboration with Purammon Ltd., a technology start-up specialising in electrolytic technologies and processes. Since then, the technology has been optimised and adapted ready for exploitation on a full industrial scale basis. A complete engineering review of the technology, its alignment with all international applicable standards, and optimisation has now been concluded and the technology is thus ready for deployment for the removal of ammonium nitrogen from industrial waters and wastewaters.
Saipem’s electrolytic process, named SPELL, transforms ammonium nitrogen contaminants (i.e., ammonia and urea) into their elemental and harmless components (namely nitrogen, hydrogen, and carbon dioxide if urea is in the feedwater), according to the following reactions:
Ammonia reaction:

Urea reaction:

These reactions are triggered by the electric current when it is applied to the electrolytic cells. By nature of the electrolytic process itself, the promoted reactions have zero-order kinetics; the reaction rate is independent of the contaminants concentration in the feed stream, and unlike other common treatments, the removal capacity remains stable over the entire process design range.
The distinctive characteristic of SPELL is its simple one-step reaction, which is intrinsically more efficient than the conventional biological processes that are commonly used for the same objective. The electrolytic process directly oxidises the ammonia consuming only three electrons provided by the external power connection. The energy consumption is directly associated to the reaction, or rather, to the contaminants load. For this reason, the energy costs are directly proportional to the contaminant load. Moreover, the high selectivity of the SPELL process excludes any unwanted reaction and thus any generation of sludge or byproducts, thus avoiding extra power consumption. On average, the specific energy consumption is around 17 kWh/kg of total nitrogen contaminants (see Fig. 1).
By contrast, the biological treatments are inherently inefficient, as they oxidise the ammonium nitrogen in two complex and sensitive steps: nitrification and denitrification, respectively performed by specific autotrophic and common heterotrophic microorganisms (e.g., Pseudomonas, Micrococcus, Archromobacter, Bacillus, Spirillum). During the nitrification process, the autotrophic bacteria extract energy for their life function though the ammonium nitrogen oxidation to nitrate ion (equation 3), using carbon dioxide as their source of carbon instead of organic compounds. Nitrification is an aerobic process and requires eight electrons commonly provided by system aeration, which is a cost element of the process.
Nitrification reaction:

The denitrification process is operated by the heterotrophic microorganisms under anoxic condition and requires five electrons (equation 4). These electrons are usually provided by a carbon source and, while municipal waters are usually rich in carbon, industrial streams are usually inorganic and require dosage of a supplement (e.g., acetic acid or methanol) which translates into additional costs and more polluting materials. This represents another typical and significant cost element of biological treatments.
Denitrification reaction:

Furthermore, biological systems are prone to the intrinsic weakness of bacteria-based processes: occasional failures due to toxic shocks, low/high temperatures sensitivity, process inhibition by fluctuations of nitrogen inflow, and high operational complexity. Nonetheless, the biological treatment is the most widely used technology today and it is generally accepted to cover the widest range of cases and combine reasonable efficiency with deployment costs. In the present scenario, SPELL promises to be an innovative, sustainable, and advantageous alternative to biological systems for the removal of nitrogenous contaminants.
The intrinsic effectiveness of the reaction is translated in the compactness of the system. The core of the system consists of only the SPELL reactors and the degassing tank.
The SPELL reactors contain electrodes coated with special catalysts, the unique feature of the technology. When the contaminated effluent water comes into the reactor, a selective reaction is triggered by the application of the electric current.
Each reactor is fed through a dedicated rectifier, providing the necessary electricity. The ammonia and the urea contained in the water are decomposed into nitrogen, hydrogen, and carbon dioxide in the gaseous state. A mixed-phase stream exits the reactor and enters the degassing tank. Here, the gases are separated by the water to be released to the atmosphere or, in case of reasonable quantities of released gases, are captured for useful applications. A blower installed on top of the tank ensures the proper separation of gases, while the treated water is pumped away, to be possibly recycled back into the process, or eventually discharged.
To complete the system, a filtration unit and chemical dosing packages are usually provided. The filtration unit is often required to reduce the suspended solids in the incoming stream, thus avoiding damage to the cells and reducing maintenance. A minimum chemical dosing is often required to balance the conductivity and the alkalinity of the effluent water.
The system is surprisingly flexible in its operability and can be properly designed to manage wide fluctuations of contaminants and flows thanks to a generous turndown ratio. In the event of exceptionally high levels of contaminant, the design capacity of the system can be conveniently limited by means of a simple recirculation of the effluent water into the electrolytic reactor.
The SPELL process is able to treat effluent water with contamination from tens to hundreds of ppm of nitrogenous compounds and remove them to near zero levels. Inlet streams may be pre-treated to ensure proper operation and protection of the system. Table 1 reports thresholds for the main parameters with which the inlet stream must comply to guarantee the design system availability and design life. Three main levels are described to identify: the “design basis” values, which are defined for the normal operation of the electrolytic cells, the “maximum recommended” values, which can be considered as the “design conditions”, and the “maximum allowable” values, over which the technology should not be exposed. Limitations for the total suspended solids are envisaged to keep the electrolytic cells free of depositions, thus reducing the system maintenance. In fact, the total suspended solids figure is related to relevant particle size: the lower the size of the particles, the higher the value of TSS can be considered, over certain limits.
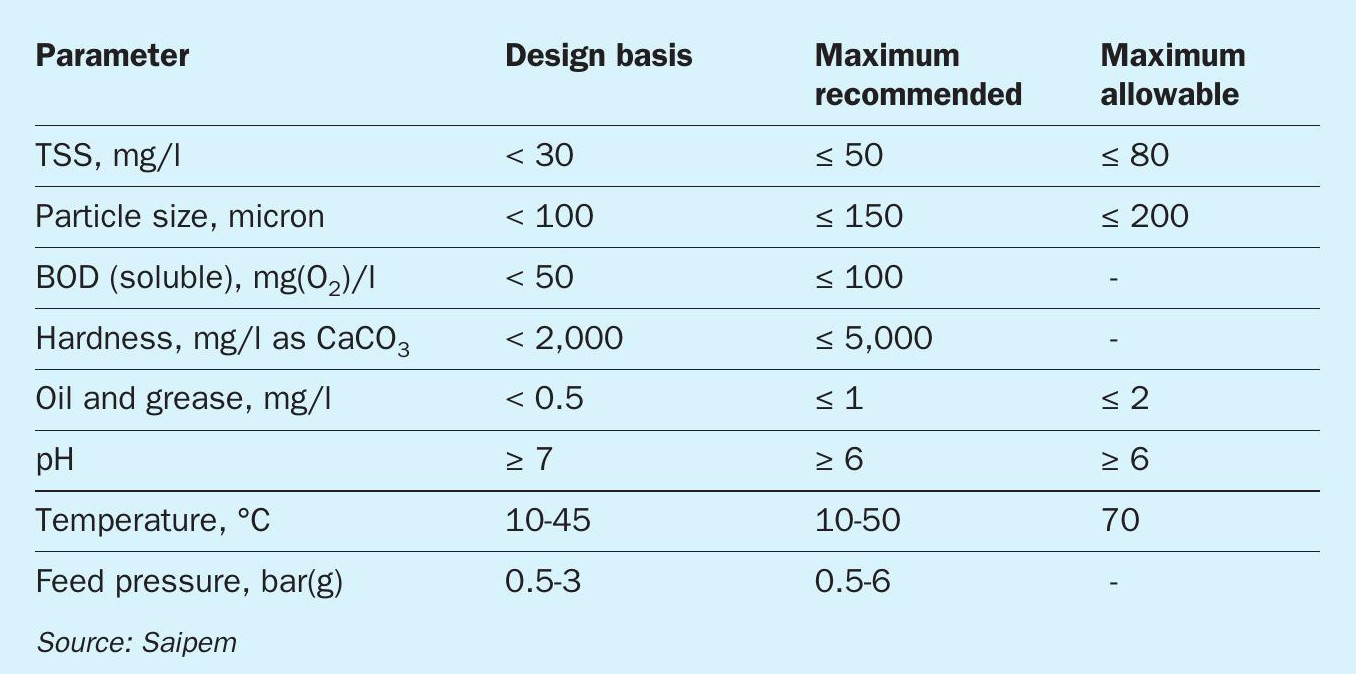
No technology failure or serious drawbacks are associated with high values of biological oxygen demand (BOD) and/ or hardness; good process response and experience have been gained within these conditions.
On the contrary, oil and grease should be minimised as much as possible as these contaminants are able to compromise the proper operation of the system and its integrity.
The pH has its own reference operating range and can be easily managed by chemical dosage.
The temperature of the incoming water should be limited to the values given; higher water temperatures could compromise the coating of the special electrodes.
The system is simple and modular, different contaminant loads and flow volumetric capacities may be fitted by multiple cells, units, and different configurations. It can be simply deployed for brownfield applications, plant enhancements, and greenfield installations. For treatment of complex wastewaters, the SPELL technology can also be used economically in combination with different physical, biological, and chemical processes. A standard N+1 philosophy is usually applied for the electrolytic cell installation to provide adequate system availability.
Figs 2 to 5 provide examples of the performance of the SPELL technology.
Fig. 6 represents a simplified benchmarking exercise comparing the features and advantages of a standard biological treatment versus SPELL.
The first considerations are relevant to the chemical process and its direct implication. Both the biological treatment and SPELL allow for the removal of both ammonia and urea from wastewaters. Urea decomposes in water to ammonium nitrogen by a two-step reaction which is then further processed either via the sequence of nitrification and denitrification processes in the case of a biological system, or through direct oxidation in the case of SPELL. The two systems are quite different in process efficiency and effectiveness. This difference is amplified by the respective reaction order: biological processes are characterised by first order reactions, suffering a slowdown in rate as the contaminants decrease in concentration, while the electrochemical process is a zero-order reaction, maintaining the same reaction rate independently from the concentration of the contaminants at the inlet. Furthermore, while the biological treatment allows limited concentrations of nitrogen at the inlet, because of inhibition phenomena, the SPELL technology can also treat highly contaminated streams. In fact, the electrochemical technology is not limited by the concentration of the contaminants, but by the cost competitiveness of other technologies in such conditions (e.g., the stripping process becomes the technology benchmark for inlet concentrations of thousands ppm). Since the electrolytic process does not use bacteria, it does not produce any sludge, unlike biological systems. Sludge removal, treatment, and disposal incurs an operational cost which is a feature of biological systems that can be completely avoided by the deployment of SPELL. Another operational cost which can be avoided by the deployment of the electrochemical process is the use of an external carbon source required by bacteria during the denitrification process. Both biological and SPELL processes need chemical dosage; the required quantities are significant for biological systems, but lower for SPELL.
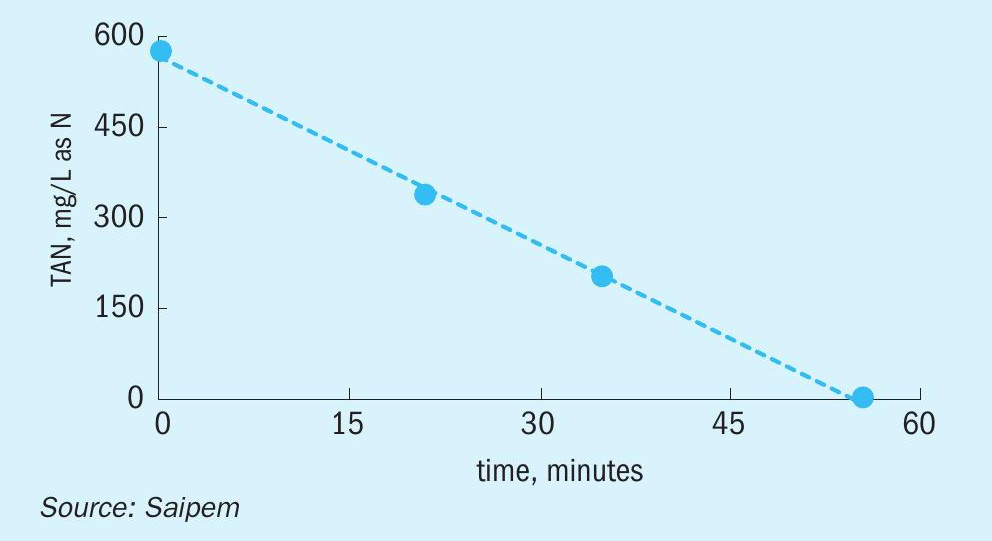
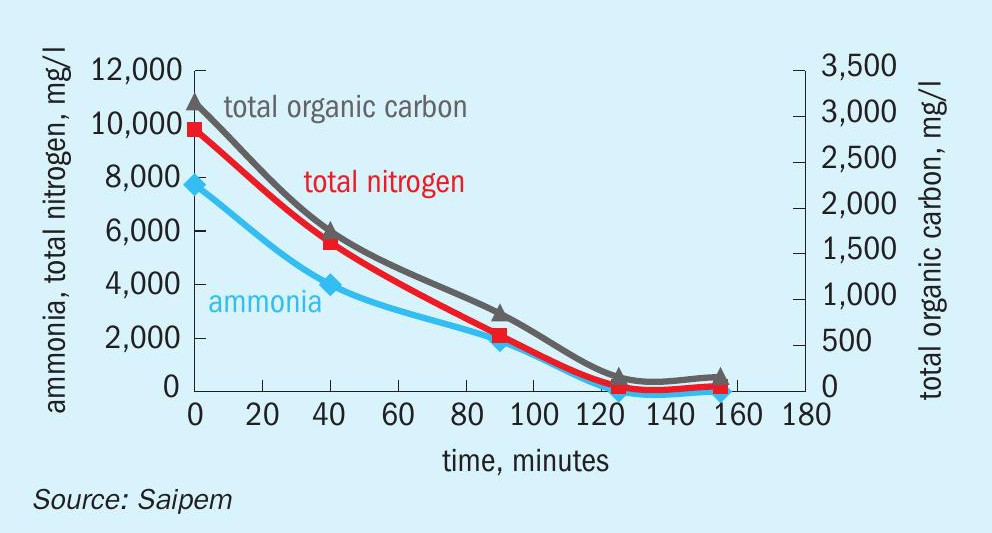
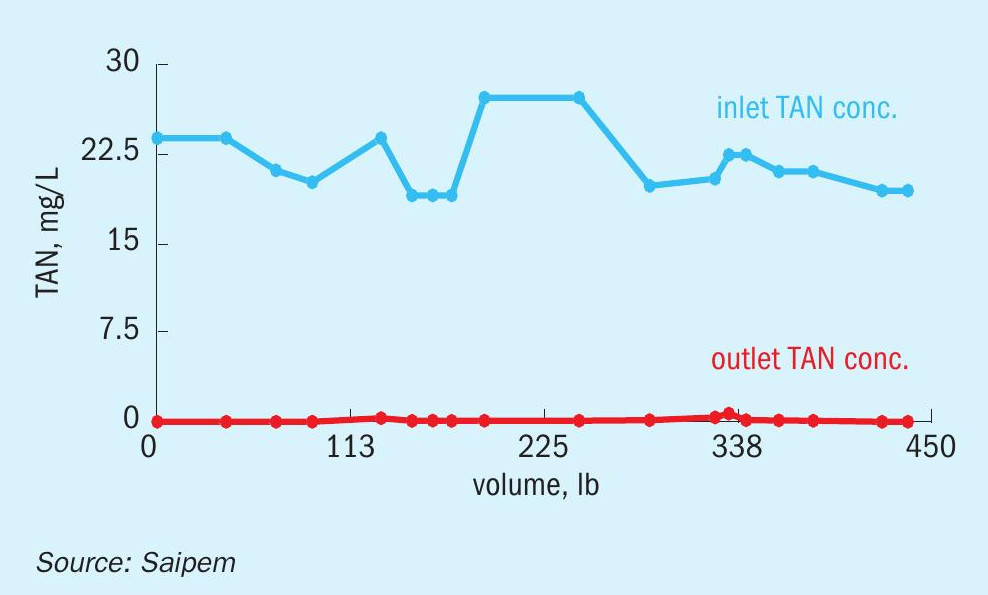
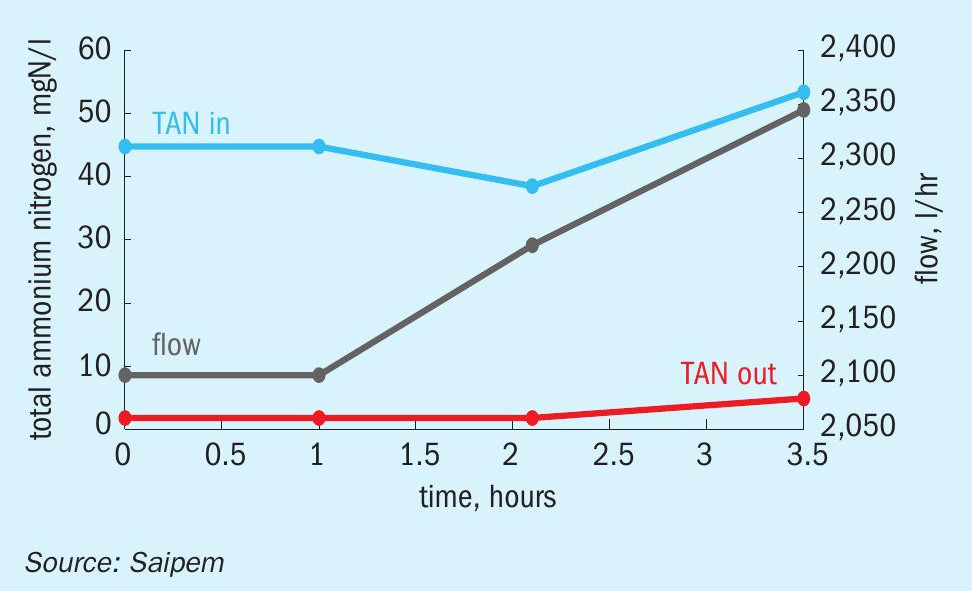
Other parameters relevant to the system operability include robustness and flexibility. While biological systems do not adapt well to load and contaminant fluctuations, SPELL manages changes in the inlet parameters much more readily. Even variations of the water temperature can destabilise a biological process, while the electrolytic process allows a wider range of inlet temperatures. Operators commonly find biological processes can be very difficult to manage, and the effectiveness of the process is too often impacted by external conditions. On the contrary, the SPELL process is simple, easy to operate and achieves expected results. The system can be fully automated and even work on a start and stop basis, with immediate start-up and shutdown procedures.
The two processes are also quite different in the number of installed items. For the whole system footprint, biological systems need big concrete basins and operational space, while SPELL is typically more compact requiring limited space.
Based on these considerations, there is clearly a substantial difference in the operational costs, related to typical consumptions: carbon sources and other chemicals, sludge disposal, electricity for aeration, pumps, etc. for biological processes, which exceed the cost for electricity (for the reactions) and the small amounts of chemicals required for the operation of an entire electrolytic system.
Based on Saipem experiences and projections, the operational cost for SPELL operational cost is at least half the typical cost for a biological system, with further optimisations possible in certain applications.
The capital expenditure for SPELL may be lower, or at least comparable, to the cost of a biological system designed for the same service, depending on process and site conditions. In some installations, alternative materials (like plastic) can be used instead of steel, thus reducing the overall cost.
Saipem’s newly introduced electrochemical technology is an important step towards the overall objective of zero industrial pollution, showcasing the company’s deep commitment to global sustainability. SPELL technology is regarded as a breakthrough solution for fertilizer plants as well as other sectors and is ready for commercialisation on a large industrial scale. Saipem’s technology partner, Purammon Ltd, already has two industrial references, demonstrating the effectiveness and advantages of SPELL.
Both of these existing installations are a good example demonstrating technology application for plant enhancements.
The first installation was delivered to a fertilizer plant in the Middle East, with a basic standard configuration for direct ammonia removal. The delivered system treats wastewaters to reduce the contaminating ammonia from 800 to 1.5 ppm. The client (a local fertilizer company), being subject to restricted environmental regulations for effluent discharge to sea, had to plan a dedicated wastewater treatment unit. The electrochemical technology was selected after comparing three leading biological processes for their cost effectiveness, system operability, system reliability, and effluent quality. The system was built, installed, and integrated within the existing facilities in six months and with no requirements for civil engineering works. The new system allowed the client to overcome specific site challenges, including a wide fluctuation in nitrogen load at the inlet, and limited availability of space.
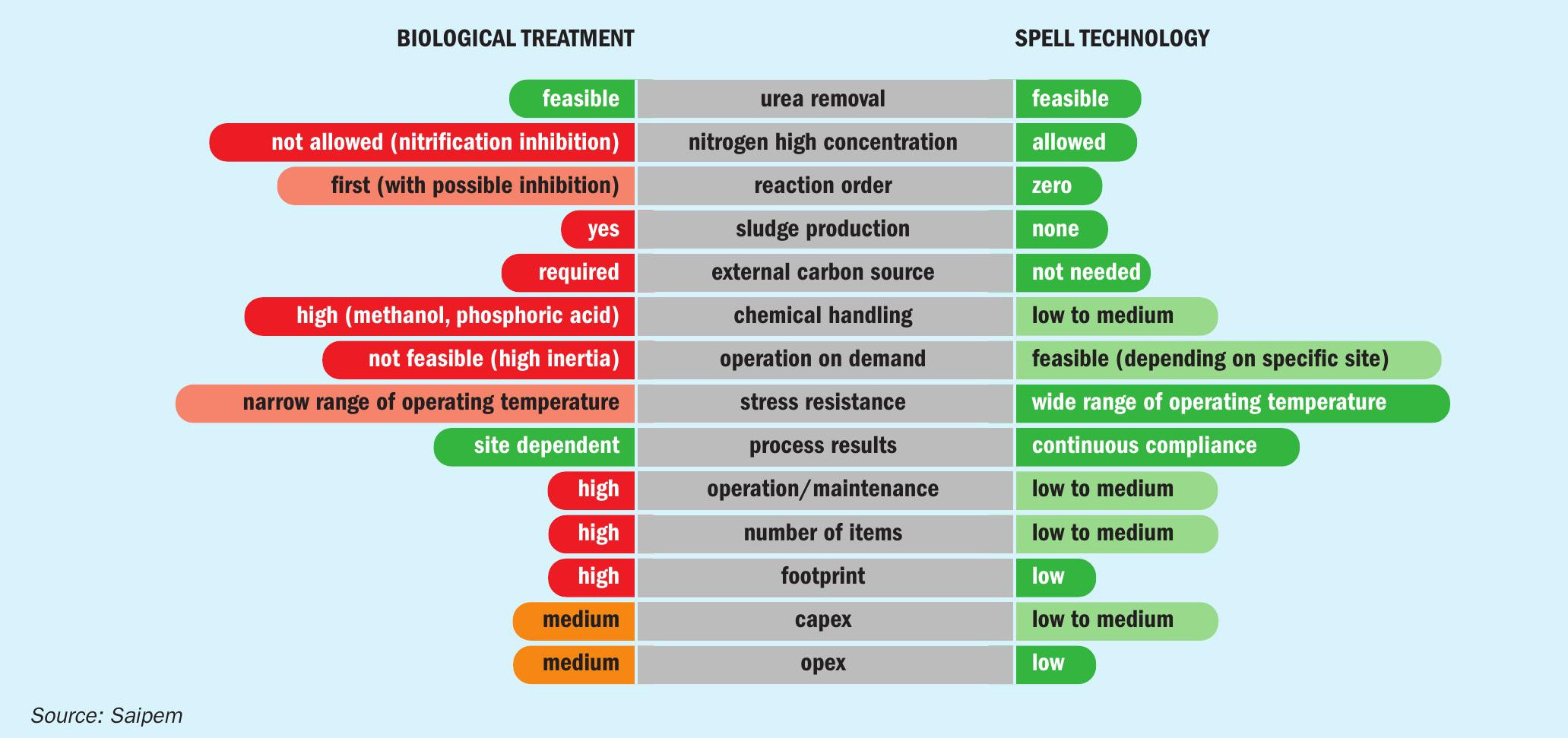
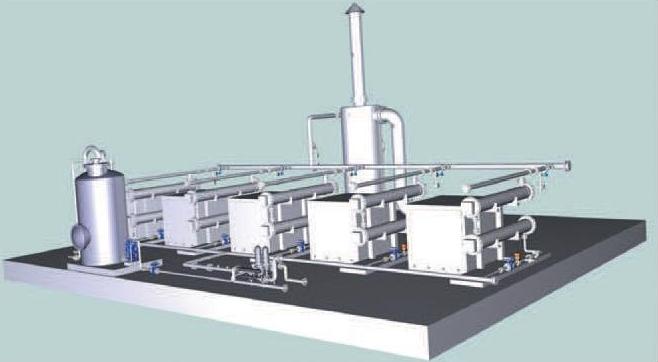
Fig. 7 shows a 3D model for a 2.15 m x 16 m plant for a flow of 40 m3 /h and effluent ammonia of below 1.5 mg/L, based on the new electrochemical technology.
The second installation was delivered for a chemical production facility in Southeast Asia. The client, an international chemical company, had occasional incidents of environmental pollution with ammonia. The existing biological treatment needed a second barrier against such failures since, occasionally, toxins and inhibitors heavily affected the autotrophs in the biological reactor: the existing bacteria based treatment could no longer guarantee consistent compliance with the regulations. A 7-m3 /h electrochemical unit was installed in combination with the existing ion exchange resins to work on an on-demand operating mode and was designed to reduce ammonia levels from 30 to 5 ppm. The unit was smoothly integrated within the existing wastewater treatment plant, requiring minimum footprint, and causing no interference with the ongoing chemicals production.
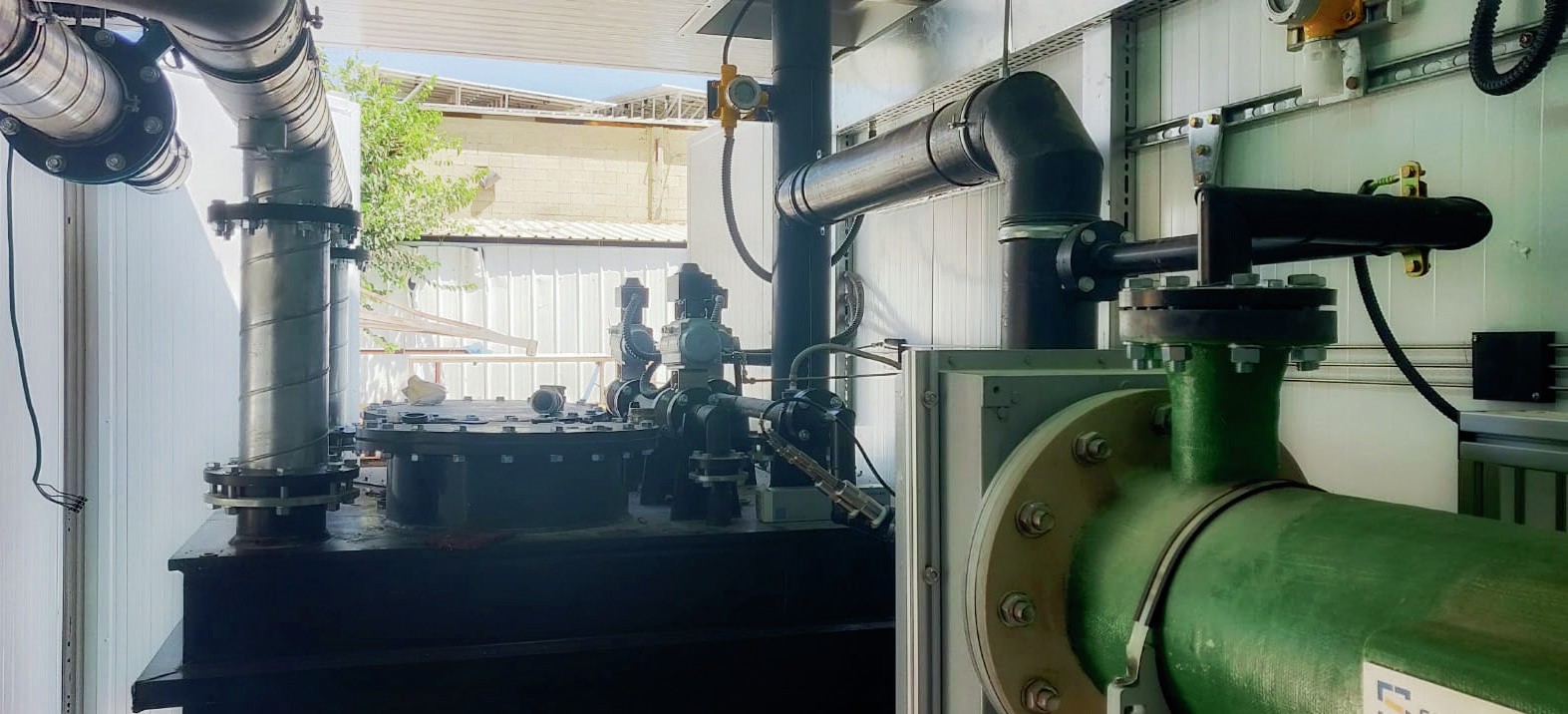
In addition, to provide evidence of the effectiveness, simplicity, and operability of SPELL technology, Saipem has a demonstration unit (Fig. 8) that can carry out online tests, directly at the clients’ premises. The SPELL demo plant is fully enclosed in a high-grade, 40-foot container, which can be easily transported everywhere and easily connected with existing, running plants. The system is “plug and play” and is equipped with a few standard connections for the minimum utilities that are required for its operation, namely: pressurised air for instrumentation, electricity supply to sustain the reaction, potable water for safety eye showers.
The system can be fed with a wastewater side stream of the running plant: the volumetric capacity of the system is 2 m3 /h, with a design nitrogen load of 170 g N/h (a concentration which is quite typical for fertilizer plants). The unit is complete with all safety and shutdown systems and is fully compliant with applicable international standards.
The system is ready and is presently undergoing its factory acceptance test. First on-site tests have already been booked.
References