Sulphur 398 Jan-Feb 2022
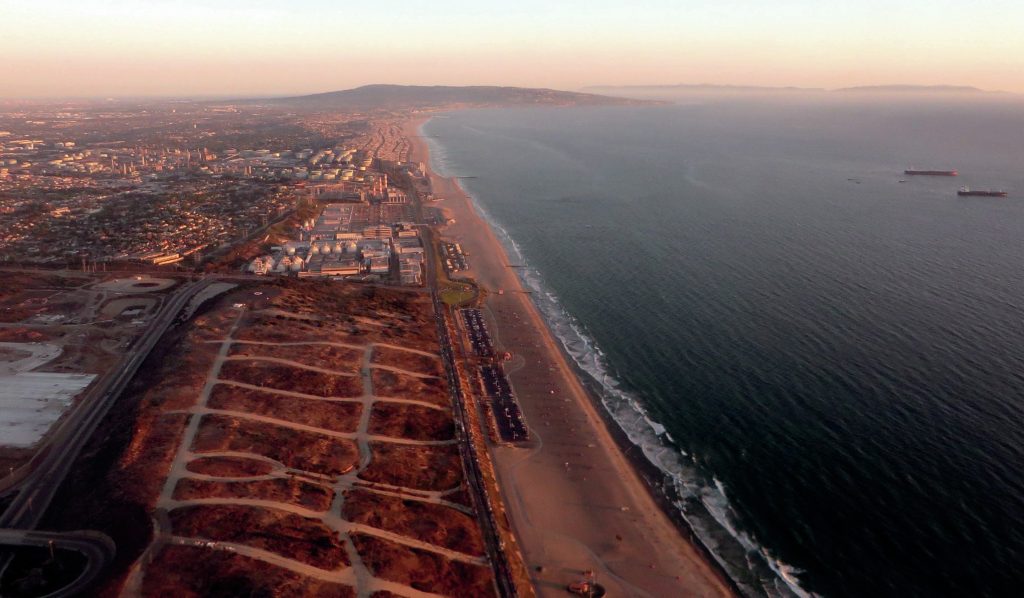
31 January 2022
Refineries and the energy transition
REFINERIES
Refineries and the energy transition
As the world looks to a lower carbon future, refineries are having to examine their operating models, and look to, for example, renewable hydrogen production for desulphurisation technologies.
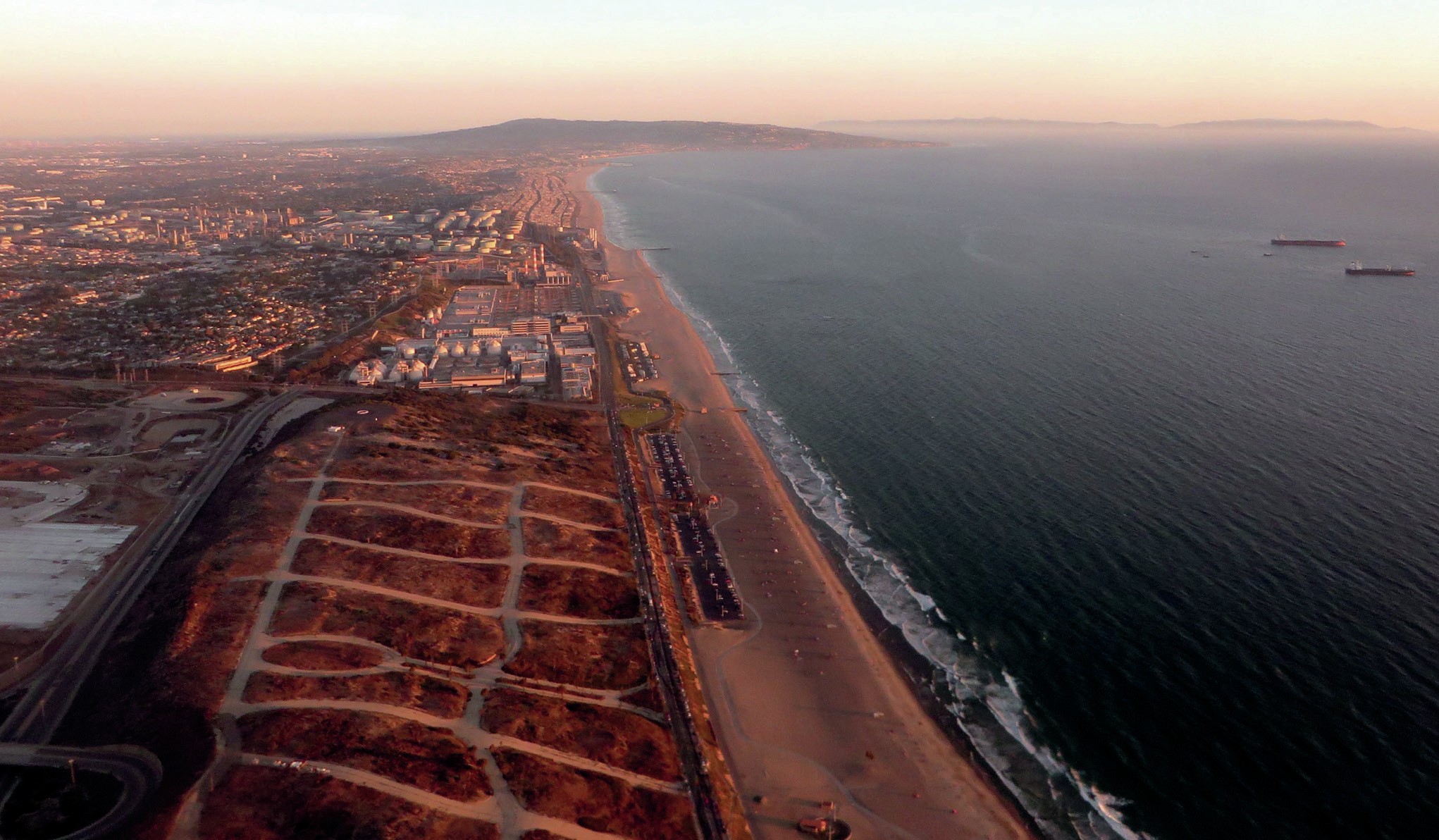
As international attention begins to focus more and more upon the potential threat posed by climate change, as witnessed, for example, at the UN COP-26 conference in Glasgow last October, so the fossil fuel industry, source of 95% of the world’s sulphur, finds itself increasing in the crosshairs of governments and regulators. At stake is a transition to a lower carbon model of living, envisaging a transformation of the global energy sector from largely fossil-based to zero-carbon by the second half of this century. And amongst the key goals of such a transition is a move from diesel and gasoline powered vehicles to biofuel or electric power trains. However, oil majors were conspicuously absent from COP-26; told, according to Shell CEO Ben van Beurden, that they were “not welcome”. So what does this mean for refiners? Although Shell and BP have both said that they aim for their operations to be carbon free by 2050, it seems clear that many governments, especially in Europe, are working on much shorter timescales, and refiners are likely to have to make considerable changes to their operations over the next decade if they are to remain operating.
Hydrogen
Aside from ammonia and methanol production, refineries are the key producer and user of hydrogen. With hydrogen set to play a major role in the energy transition, in some ways this places refiners in an advantaged situation, as already being used to handling and distributing hydrogen, and given them an expertise which could be a valuable lever. However, it is likely that over the next decade or two, refiners will be gradually forced to lower their carbon footprint is by switching from natural gas or naphtha feedstock for hydrogen production to greener methods.
Europe has been at the forefront of such moves. In Germany, one third of refiners are said to be moving towards some form of green hydrogen production. Shell’s 140,000 bbl/d Wesseling refinery began using 10 MW of electrolytically generated hydrogen in July 2021, though this will generate only 1,300 t/a of hydrogen. BP is planning to instal a 50 MW electrolyser at its Lingen refinery, powered by offshore wind from Ørsted, which will generate 9,000 t/a of hydrogen and replace 20% of the refinery’s hydrogen requirement. At Westküste, a 700 MW green hydrogen project is planned for 2030, powered by an offshore wind farm, with the Heide refinery one of the partners in the project consortium. Heide is planning a 30 MW electrolyser as an interim step, in 2025.
Meanwhile, India has also announced plans to force refiners to use some green hydrogen. The draft National Hydrogen Mission policy, prepared by the Ministry of New and Renewable Energy, would mandate that green hydrogen account for 10% of the overall hydrogen needs of refiners from 2023/24, rising to 25% in five years. Reliance Industries, which runs the world’s biggest refining complex at Jamnagar in western India, says that it plans to invest $10.1 billion in clean energy over three years in a drive to become a net carbon zero company by 2035, via four ‘giga factories’ at Jamnagar to produce solar cells and modules, energy storage batteries, fuel cells and green hydrogen.
However, financing such investments is an issue. There are some government incentives available. The Shell Wesseling refinery secured e10 million ($12 million) in funding from the EU through the Fuel Cell Hydrogen Joint Undertaking initiative, but there are several industries competing for grants to decarbonise, from steel to chemicals such as ammonia or methanol, and a limited pool of grants. Equally, the EU carbon market offers some incentive. EU carbon prices soared last year, from e32.72/ tonne of carbon dioxide equivalent at the start of the year, to a peak of e90.75/tCO2 e in December. High European prices for natural gas also help encourage a move to alternative methods of hydrogen production.
But there is also the question of how long the payback time for any large scale investment in green hydrogen generation is expected to be. The energy transition, particularly the shift to electric vehicles, threatens to undermine demand for transportation fuels within a decade or sooner. The UK has brought forward plans to ban sales of fossil fuel powered vehicles to 2030, and the EU is targeting 2035. BP says that its energy transition plan envisages cutting refining throughputs from 1.7 million bbl/d today to 1.5 million bbl/d in 2025 and 1.2 million bbl/d by 2030. Shell says it will divest itself of five of its 11 refineries by 2025, integrating the rest into large complexes.
Chemicals
One of the potential solutions is to see hydrogen generation not just as a tool for hydrodesulphurisation of fuel components, but as a business in its own right. It might also be a way into using CO2 for chemicals or even fuels production, perhaps via Fischer-Tropsch polymerisation, or methanol production with downstream processing into gasoline, or olefins. As we mentioned in our July/August issue last year, integration of refinery operations with chemicals production is becoming an increasingly attractive option for refiners. ExxonMobil says that almost 80% of its 4.5 million bbl/d refining capacity is now integrated with chemicals or lubricant manufacturing.
Carbon capture
Perhaps a cheaper way of achieving lower carbon emissions is a move to so-called ‘blue’ hydrogen, using conventional feedstocks but capturing the carbon dioxide emitted and sending it to storage (CCS) or using it for something else. This offers the possibility of large scale installations (>1,000MW) without the expense of electrolysis. ExxonMobil has been a big advocate of CCS. The company says it plans to invest $15 billion over the next six years in reducing its carbon emissions, and CCS forms a major part of this. It is working with several other companies in supporting a large-scale CCS hub in the Houston area, where 15% of US oil refining capacity and 40% of petrochemical processing capacity is located. The hub could capture up to 100 million t/a of CO2 from refineries, chemical plants and power generation facilities. Other major international players are looking to CCS, including Petronas, Pertamina, Rosneft and Saudi Aramco. Saudi Arabia, the world’s largest oil exporter, has said that it is targeting 2060 for achieving carbon neutrality, with initial investments of more than $187 billion.
“The UK has brought forward plans to ban sales of fossil fuel powered vehicles to 2030.”
But the technology remains new and tetchy. High pressure CO2 can be highly corrosive if it encounters water. Chevron announced in November 2021 that it had failed to meet a five year CCS target at its $3 billion Gorgon LNG project in Western Australia, and was buying A$40 million ($29.17 million) in carbon offsets to compensate for more than 6 million tonnes of carbon emissions, after only managing to capture 30% of what it had promised.
Biofuels
Production of biofuels is also another way forward for refiners, processing waste biomass or vegetable oils. Total says that its bio-refining operations have actually performed better financially than its conventional refineries since the start of the covid pandemic. The company has converted its 160,000 bbl/d La Mede refinery in France into a 500,000 t/ya hydrotreated vegetable oil plant, and says that it will end conventional refining at its 93,000 b/d Grandpuits facility near Paris this year, converting it to a biorefinery by 2024. Meanwhile Chevron began co-processing bio-feedstock in the FCC of its El Segundo refinery in California in 2021 using 2,000 bbl/d of soybean oil. This year, the plan is to convert the diesel hydrotreater to 100% renewable capacity, increasing capacity to 10,000 bbl/d of renewable diesel, rising to 100,000 bbl/d by 2030. Phillips 66 is looking to do similar, converting its Rodeo refinery at San Francisco in California from crude oil, to a variety of renewable feedstocks to produce lower-carbon transportation fuels by 2024.
Greater use of vegetable oil processing could also have an impact on hydrogen demand. According to IHS Markit, wider use of hydrotreated vegetable oil (HVO) as fuel would boost hydrogen consumption as the HVO biofuel process requires large amounts of it to remove the oxygen from the feedstock and isomerise the hydrocarbon chains. But large scale adoption of vegetable oil, even waste oil, has impacts upon the food sector, and would not be scalable to form a large fraction of transportation fuel needs.
Other tactics
In addition to the measures above, there are other ways that refiners can hedge themselves against the changes that are coming to the industry. The first and perhaps most obvious is to focus upon the most efficient and profitable assets, divesting standalone facilities and upgrading and integrating the best refining assets. Secondly, investment in digitalisation and process analytics should pay dividends in being able to optimise production, reduce expenses and increase margins. Finally, some refinery product sectors seem set to continue to grow rather than shrink – for example, aviation fuel is difficult to replace with alternate fuels and demand should continue to grow once the worst of the covid pandemic passes.
The sulphur block
The impact on refinery sulphur output will depend on the specifics of each technology used. In general, changing the hydrogen feed to ‘green’ or ‘blue’ from the present ‘grey’ is unlikely to impact much upon refinery output. Greater processing of biomass feeds however is likely to lead to higher CO2 but lower H2S levels in the acid gas, and much lower sulphur recovery levels, possibly down to levels that would be treated with a scavenger rather than a Claus plant.