Fertilizer International 507 Mar-Apr 2022
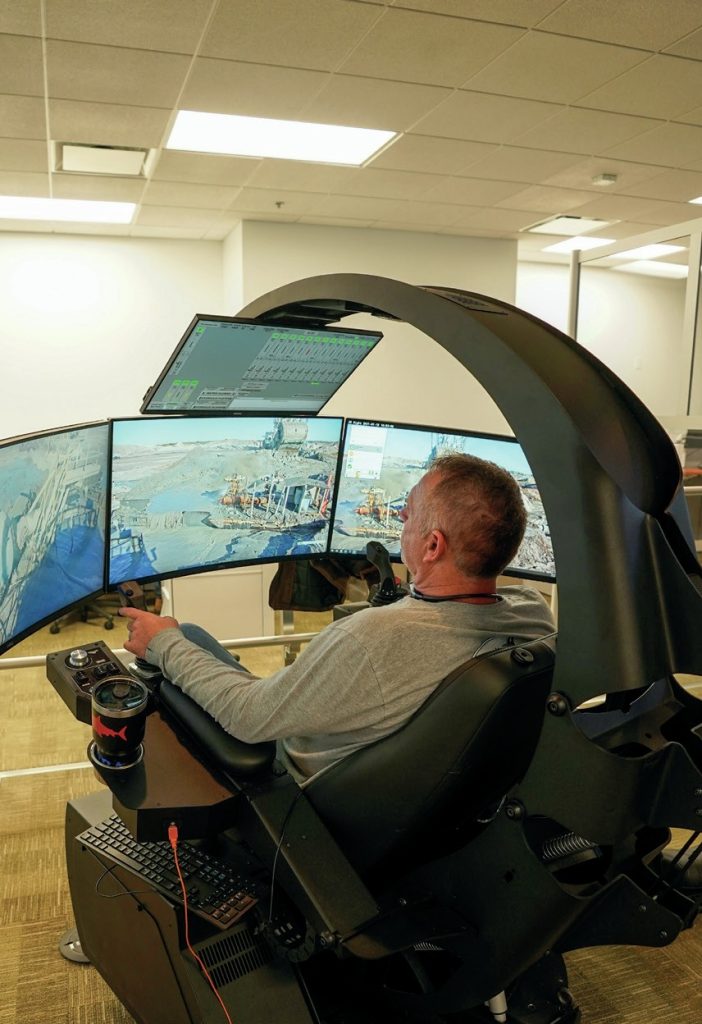
31 March 2022
Crushing, conveying & screening
P&K TECHNOLOGY
Crushing, conveying & screening
Efficient size preparation and ore transport are key prerequisites for successful potash and phosphate production. We highlight the range of equipment options.
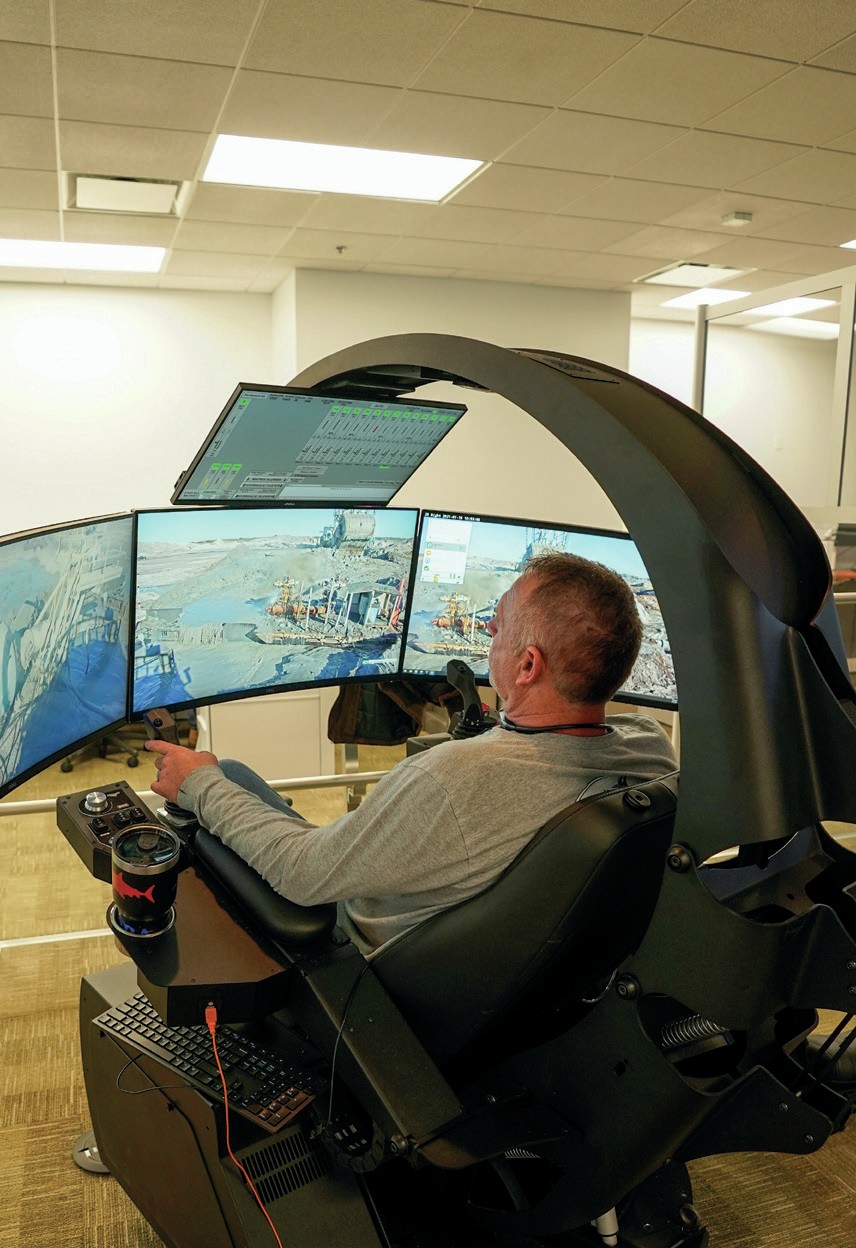
Phosphate and potash mining technology is undoubtedly changing. Wider mining industry innovations are being taken up by P and K producers to improve their operational and resource efficiency and meet sustainability objectives.
Mosaic for example, has opened an Integrated Operations Center at Lithia, Florida. This allows operators to remotely control high-pressure water guns used to extract phosphate ore from mining areas located many miles away (see photo).
Other phosphate producers such as PhosAgro have introduced in-pit crushing & conveying (IPCC). This improves mining efficiency, introduces mine electrification/ decarbonisation and reduces reliance of diesel-powered trucks.
New entrants to potash production such as EuroChem have also invested heavily in electrically-powered mining machines to extract potash ore underground.
The mining technology sector is also seeing merger and acquisition activity. In a major move, Denmark’s FLSmidth agreed to purchase thyssenkrupp’s mining business in July last year. Both businesses will, however, continue to operate independently as competitors until the necessary regulatory clearances are granted. This is expected to happen later this year.
Phosphate mining: excavation
The main digging equipment options for phosphate mining are set out in Table 1.
Selection criteria for digging equipment include1 :
- Capital cost
- Material handling characteristics
- Type of face and bench operations
- Required ore throughput
- Productivity (cycle time per pass)
- Ease and cost of electricity distribution at the mine site.
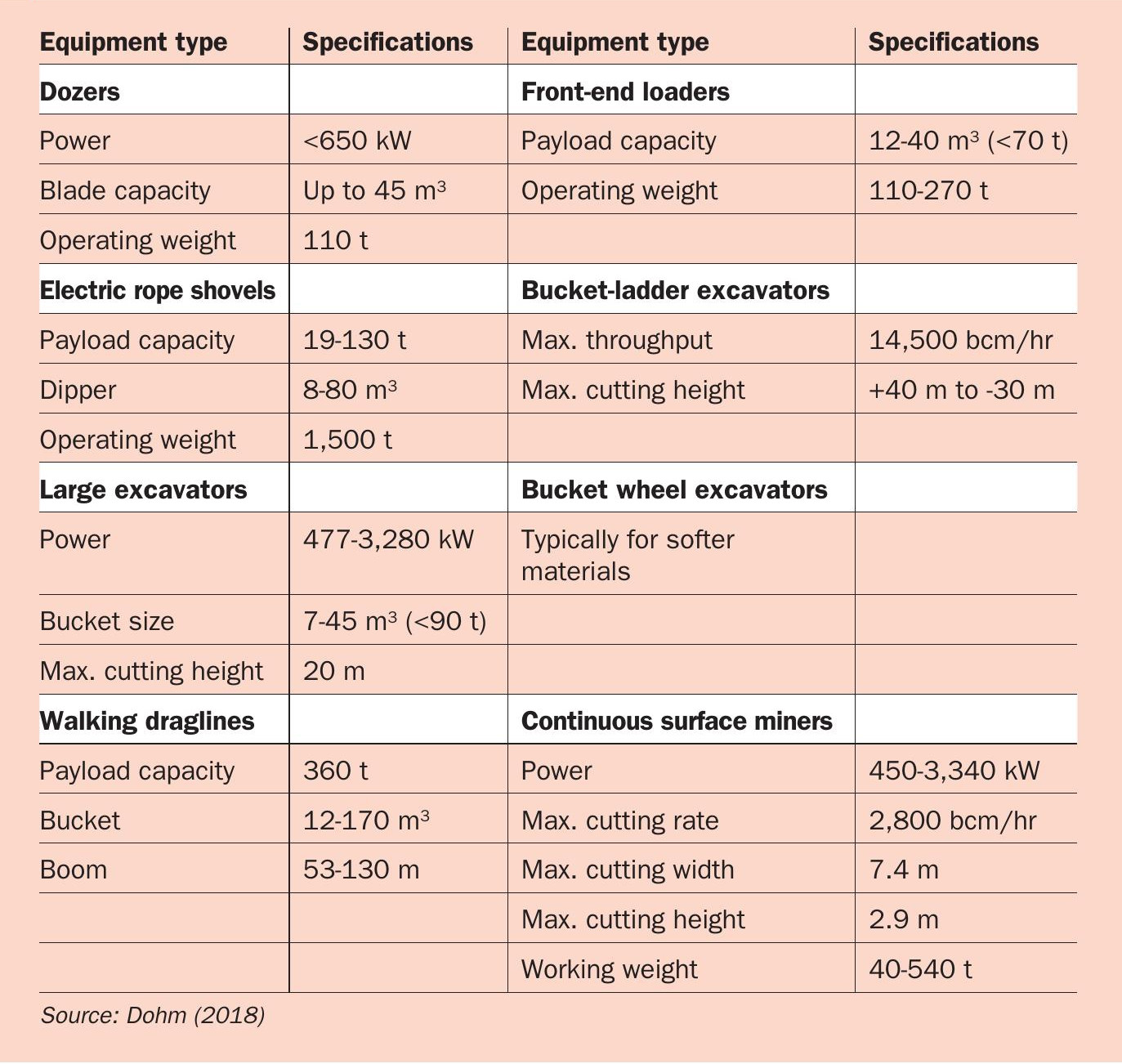
German engineering giant thyssenkrupp has a strong equipment offering for phosphate mining. The company introduced its new Barracuda range of bucket wheel excavators in 2016 (Fertilizer International 495, p37). These compact mining machines use a larger number of teeth per bucket to cut materials with a compressive strength of up to 50 MPa.
The Barracuda’s innovative design allows harder materials to be excavated, including phosphate rock, potash and limestone, without the need for drilling or blasting operations. By combining ore excavation, loading and the transport within a single machine, the Barracuda can seamlessly replace a complex system of multiple machines with a single mining unit.
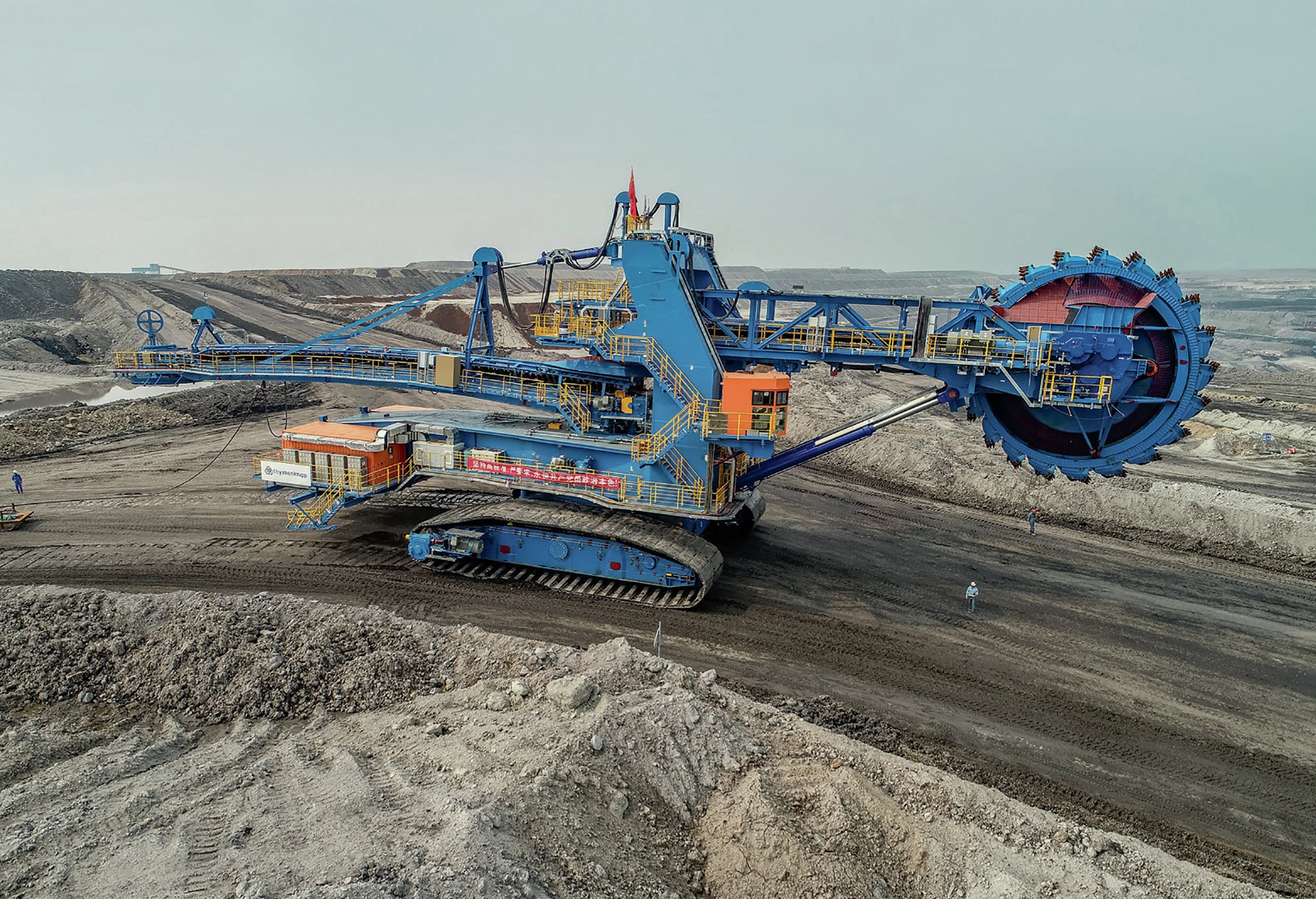
thyssenkrupp offers four versions of the Barracuda, each with different ore transport configurations. They range from a compact machine and conveyor – for a basic extraction process – to the advanced Barracuda C machine. This combines a compact bucket wheel excavator with a discharge boom operating in tandem with a conveyor system.
The Barracuda has three particular features that make it an attractive excavation option for mine operators, according to thyssenkrupp:
- Streamlines ore transportation
- Offers predictable operational costs
- Able to eliminate pre-blasting.
In ore transport, integrating the Barracuda with continuous mining/conveyor systems widens the range of potential mine applications and also delivers major cost reductions in comparison to conventional truck transportation. The machine’s electrical drive can also reduce the carbon footprint of mining operations. One Barracuda machine, by potentially replacing more than 10 other mining equipment units, also streamlines both operations and maintenance efforts, according to thyssenkrupp.
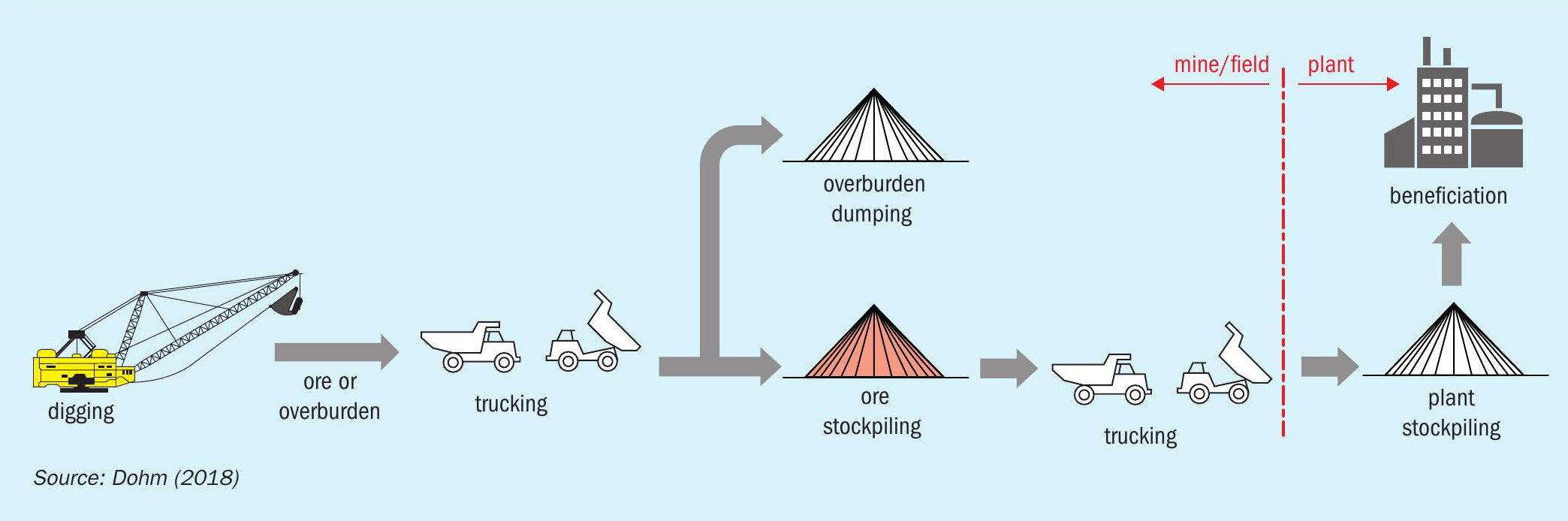
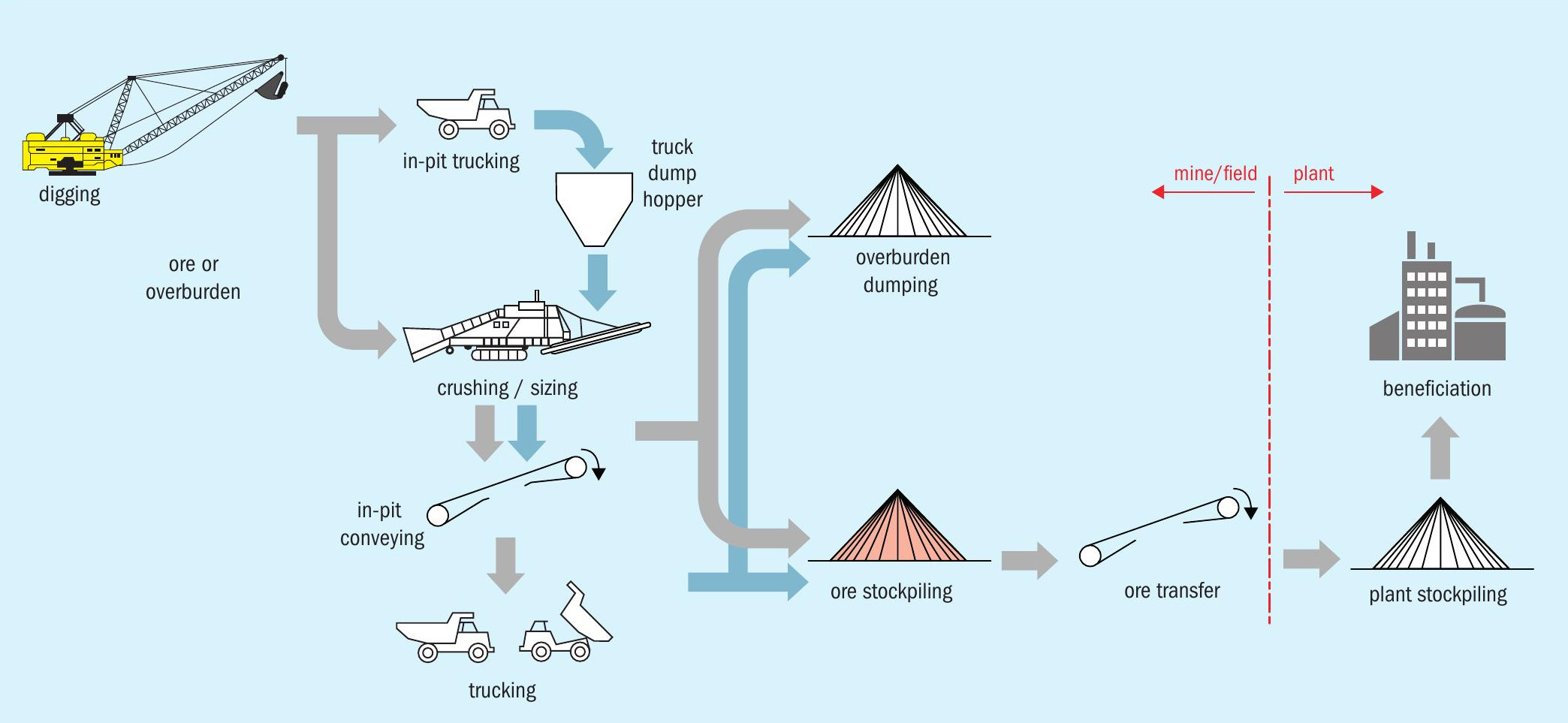
But is the elimination of pre-blasting that is the main overall factor which makes the Barracuda a leaner, more cost effective and safer mining process option. Conventional bucket wheel excavators are unable to cope with harder ore materials and – unlike the Barracuda – still require blasting to fracture rock in-situ prior to extraction. The need for pre-blasting can add more than $0.2 per tonne to extraction costs – a major cumulative cost for multimillion tonne mining operations.
The Barracuda, by removing the need for drilling and blasting, can therefore offer significant cost reductions, especially for mine expansions or new mine projects which require investment in new equipment anyway. The use of Barracuda mining machines also offers a more sustainable alternative to blasting, which is subject to increasingly stringent environmental regulations for noise, fumes, dust and vibrations.
In-pit crushing & conveying (IPCC)
Conventional phosphate mining is heavily reliant on diesel-driven truck haulage and is typically divided between several separate and discrete stages (Figure 1):
- Excavation of ore and overburden
- Trucking of these excavated materials to ore stockpile and overburden dumping area, respectively
- Trucking of ore from the mine stockpile to the plant stockpile for onward beneficiation.
In-pit crushing & conveying (IPCC) (Figure 2) can offer an attractive alternative to truck haulage due to its ability to1 :
- Reduce operating costs and lower carbon emissions
- Substantially cut diesel consumption
- Reduce expensive consumables (tyres, filters, lubricants etc.) associated with truck haulage.
In certain circumstances, IPCC can also be a viable alternative to slurry pipelines as it2 :
- Eliminates large-scale water use and consumption during mining and onward transport
- Improves efficiency of draglines and minimise delays in ore transport
- Achieves maximum operational efficiency by immediately evacuating ore from the vicinity of the dragline
- Offers the ability to measure and segregate ore based on quality using cross-belt analysers.
thyssenkrupp’s IPCC system
In-pit crushing & conveying is a key capability offered by thyssenkrupp Mining (Fertilizer International 475, p54). The company’s market leading IPCC system is designed to limit truck haulage to the movement of ore materials within the mine pit. Truck use is generally restricted to shuttling material, horizontally or downwards, to the semi-mobile crushing plant.
In terms of operational expenditure (opex), IPCC has the following advantages versus a conventional system using diesel trucks:
- It is electrically driven with a higher efficiency than diesel motors
- Has a lifetime of up to 40-50 years with regular maintenance
- Significantly reduces operating personnel due to partial automation
- Increases mine safety
- Increases utilisation
- Reduces CO2 emissions, the amount depending on the origin of the electricity used.
Although the investment costs are generally higher for a mobile or semi-mobile IPCC system, opex reductions can typically generate a return on investment within 2-4 years.
In 2015, thyssenkrupp successfully installed an IPCC system at the Koashvinsky phosphate mine near the city of Kirovsk on the Kola Peninsula in northern Russia. This is operated by OJSC Apatit, a subsidiary of fertilizer producer PhosAgro (Fertilizer International 475, p54).
The IPCC system designed for the Koashvinsky mine is a combined crushing unit with the capacity to handle up to 30 million tonnes of waste a year. The system needed to be able to accept materials with compressive strengths averaging 50-190 MPa up to a maximum of 320 MPa.
The hoppers installed have sufficient design capacity to accept trucks with a payload of up to 220 tonnes. The direct-feed crushing plant is also equipped with a gyratory crusher designed to accept 6,200 tonnes of material per hour.
IPCC also replaced previous truck haulage of waste materials outside of the mine. Instead, these materials are crushed to a conveyable size and transported by a curved conveyor over a distance of around four kilometres to an external waste site. At the end destination, a crawler-mounted spreader with an hourly capacity of 6,200 tonnes then discharges material from the conveyor.
The IPCC system has substantially cut the Koashvinsky mine’s operating costs, maintenance costs and CO2 emissions. It also provides a higher level of operational safety.
Conveying
Conveying is an integral function for:
- The movement of potash and phosphate ore and waste during mining operations
- Transporting materials between equipment and process stages during fertilizer production.
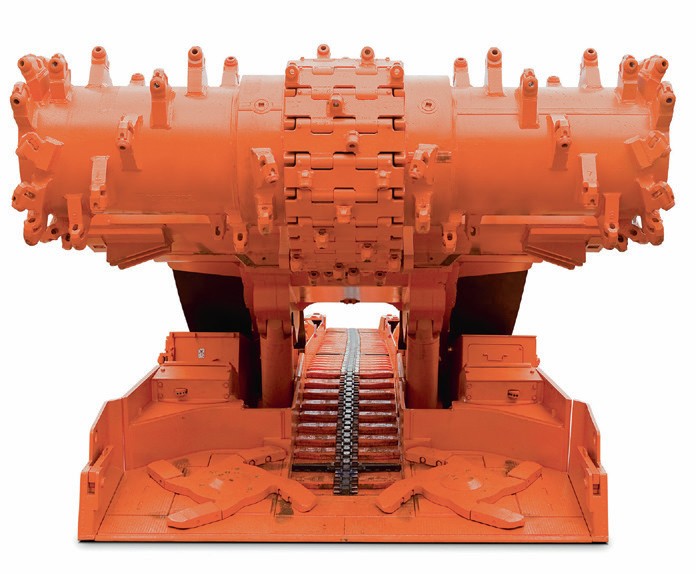
For IPCC systems at phosphate mines, equipment options for in-pit conveying are generally selected based on the following criteria2 :
- Capital cost
- Mobility requirements
- Whether there is the flexibility for reconfiguration
- Potential for standardising the main equipment components and modularisation
- Incorporation of features that reduce opex costs and downtime
- Ability to upgrade the system to increase production.
Portable modular conveyors, mobile conveyors, beltwagons and bridge conveyors can all be installed as part of an IPCC system2 .
Portable modular conveyors are short (<60 metre) relocatable or crawler-mounted structures. Multiple units can be connected in series to mine irregular areas, or to extend the reach of the mine face conveyor. They can also be used when transfer angles make it difficult to connect two conventional relocatable conveyors. Mobile conveyors, in contrast, are up to two kilometres long, capital intensive, yet can be easily moved out of the way during blasting.
Beltwagons and bridge conveyors are typically used for cross-bench conveying. Beltwagons are available in various configurations and lengths and can be used to convey materials up or down a bench, or transfer material between the face conveyor and a mobile sizer/crusher unit. Bridge conveyors can move material up or down two benches maximum. They can also be used for the dumping of materials cross-pit.
Continuous potash mining and haulage machines
Continuous miners have a long history. They were first popularised by the underground coal industry in the 1960s and have since become a mainstay of potash, gypsum and salt mining (Fertilizer International 475, p54). Caterpillar, for example, supplied four CM345N continuous miners for the Vanscoy potash mine in Saskatchewan, then owned by Agrium, while a fleet of five automated Sandvik (formerly Marietta) continuous miners were put into operation at the province’s Rocanville mine formerly owned by PotashCorp’s. PotashCorp subsequently ordered a fleet of Sandvik MF420 borer miners for the now mothballed $1.5 billion Picadilly mine in New Brunswick. These massive borers were the world’s largest self-propelled mobile underground mining machines at the time.
The productivity of continuous miners has more than tripled in the last decade. Increases in their size, weight and power means they can now operate at more economic production rates than traditional drill and blast methods.
Joy Global, the US mine machinery manufacturer, has sold over 6,000 continuous miners globally. The company was purchased by its Japanese rival Komatsu for $3.7 billion in 2016. Joy introduced the first single-operator continuous haulage system, the Flexible Conveyor Train (FCT), to the industry in the late 1980s. This optimised production by offering true continuous mining and haulage without the delays typical of batch loading. The firm also pioneered innovations such as radio remote control and AC traction drive systems in continuous miners.
Potash miners have placed more than 70 orders for Joy continuous miners, FCT systems and other equipment. The firm’s continuous miners are used by US producer Intrepid Potash at its New Mexico mine in the US and by ICL at its Boulby mine in the UK.
Komatsu’s Joy 12HM46 electrically-powered continuous mining machine, released in 2016, is specifically designed for excavating salt, potash, gypsum and trona (see photo). It incorporates upgrades, designed to increase service life and reduce total cost of ownership, as well as delivering a production increase of up to 20 percent on earlier models.
The 12HM46 has a production rate of up to 1,000 tonnes per hour. It also provides greater cutting stability, due to its greater mass, and also employs an upgraded traction drive system. Outputs above 8,000 tonnes per day should now be achievable, suggests Komatsu, by combining the 12HM46 with continuous haulage in a herringbone or multi-pass production system.
Continuous haulage
When it comes to continuous haulage, the 1,200 t/h capacity Flexiveyor designed and produced by Prairie Machine and Parts (PM&P) in Saskatoon has proven to be a popular choice in the potash industry (Fertilizer International 475, p54).
The Flexiveyor employs a number of interconnected 20-foot-long cars. These form a fixed-length, train-like haulage system. Each Flexiveyor consists of a loading car, which accepts ore from the miner, and conveys this via a series of intermediate cars to a final car which discharges the ore onto a panel belt. They can be used in combination with PM&P’s continuous miners, the Xcel series rotary boring machines, or installed behind other types of mining machine.
Some 20 Flexiveyor systems are installed in potash mines in Saskatchewan – Nutrien’s Vanscoy mine being one – and other locations worldwide, including the UK and New Mexico. A 300-foot long 15-car Flexiveyor configuration is typically used in Saskatchewan’s potash mines. Haulage is controlled via an operator interface using an industrial computer.
Potash mining machine investments
In the last few years, EuroChem has invested heavily in the latest generation of electric mining machines at its $2.1 billion Usolskiy potash mine in Russia’s Perm region its sister $2.9 billion VolgaKaliy mine in the Volgograd region The same potash mining equipment is being installed at both mines (Fertilizer International 495, p37). The following mining machines, transfer hoppers and shuttle cars have been installed at both sites to excavate and transport potash ore to the main underground conveyor systems:
- Ural-20R mining machines. These cut an arched roof 3.1 metres high and 5.1 metres wide. Each machine is approximately 12 metres long and weighs 100 tonnes. They are crawler-mounted and electrically-powered each with an average annual capacity of around 600,000 tonnes.
- Transfer hoppers. These operate immediately behind the Ural-20R. Being electrically-powered, and approximately 8.4 metres long and 2.3 metres wide with a capacity of 16 tonnes, they are equipped with a conveyor system to transfer ore to waiting shuttle cars.
- Shuttle cars. These shift the mined potash to the conveyor system, which in turn transports the ore to the shaft where it is lifted to the surface. The cars operate using a trailing cable on a reel, allowing them to travel a distance of up to 400 metres. Each shuttle car is approximately 9.0 metres long and 2.6 metres wide, weighs 19 tonnes, and has a 17-tonne payload capacity.
Ural-20R mining machines are manufactured by Kopeysk Machine-Building in Russia’s Chelyabinsk region. The Usolskiy mine, for example, originally purchased 20 Ural-20R units, with these being added to during its ramp up to full capacity.
References
Screening at phosphate granulation plants
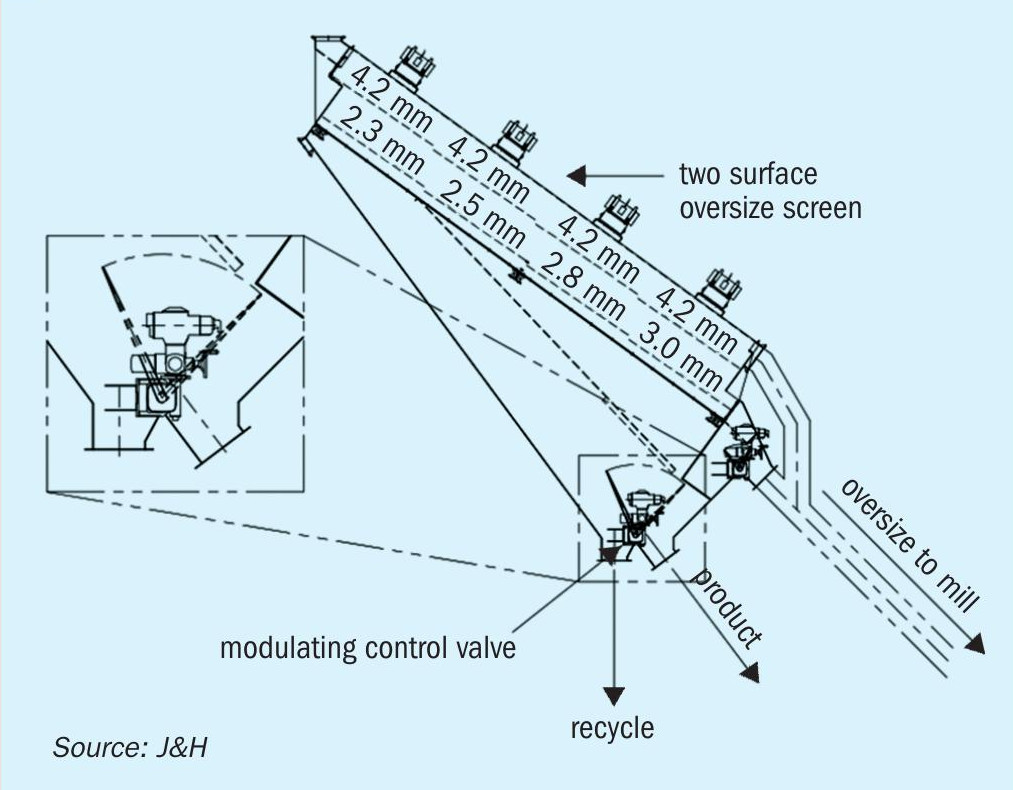
J&H Equipment, Inc
J&H was founded in 1974 by Allen Jackson and Cliff Hollyfield. The company has since grown to become a world leading supplier of screening equipment to fertilizer granulation plants globally. Notably, J&H was the first company to design and manufacture rotary-driven vibrating wire screening machines. These overcame many of the shortcomings of conventional machines, such as noise, high maintenance requirements and poor efficiency.
Thousands of J&H screening machines now operate around the world. The company’s wide range of plant machinery also includes crushers, bucket elevators, lump breakers, feeders, stream splitters and modulating control diverters – all of these essential components of modern fertilizer granulation plants (Fertilizer International 490, p54).
J&H offers complete screening equipment packages for the fertilizer industry. These operate as fully-controllable and integrated screening process systems. J&H chain mills also optimise the crushing of oversize fertilizer product. For the phosphate industry, a screen fines hopper fitted with an integrated modulating control valve allows precise computer-control of recycle material to the granulation process. This in turn reduces oversize, generates a closer sized final product and – most importantly of all – increases production by ensuring that the other machinery in the granulation plant is operating optimally.
The major design innovation and biggest performance breakthrough in process screening in recent years has been the adoption of double-deck oversize screening machines. This configuration was first introduced by WMC Resources (subsequently BHP and Incitec Pivot) in Australia. The top deck of these machines has a standard 4.2-4.4 mm opening. The openings in the bottom deck, in contrast, vary across their length, starting at 2.2 mm in the first panel and ending with 2.7-3 mm in the last panel (Figure 3). This double-deck arrangement, when used in conjunction with modulating control valves in the hoppers below the fines deck, allows the operator to select the size and amount of recycle returned to the granulator.
The RHEWUM Company
Germany’s RHEWUM has been manufacturing screens for more than 70 years now. Founded in Remscheid in 1927, its name is derived from ‘Rheinische Werkzeug und Maschinenfabrik’ – which simply translates as ‘tool and machine production company’. The company’s overriding goal is to maximise customer satisfaction by delivering the highest quality standards in screening technology.
RHEWUM has been able to react to changing market preferences by constantly improving its equipment portfolio to meet the new demands of customers. It has remained a market leader in screening technology for fine particles such as fertilizers by developing modular ‘plug-and-play’ screens.
The latest modern screening technologies introduced by RHEWUM are designed to maximize quality and efficiency. Its RHEsono and RHEmoto screening machines (see photos), for example, can meet the demanding specifications required for screening phosphate fertilizers.
These two types of machine prevent clogging by direct excitation of the screening meshes at high acceleration. Inclining the mesh at an angle (see bottom photo) maximises throughput by allowing materials to flow at high velocities. Their static machine body, meanwhile, allows maintenance to be carried out without stopping production. This intelligent design allows the replacement of motors and settings to be changed while operations continue.
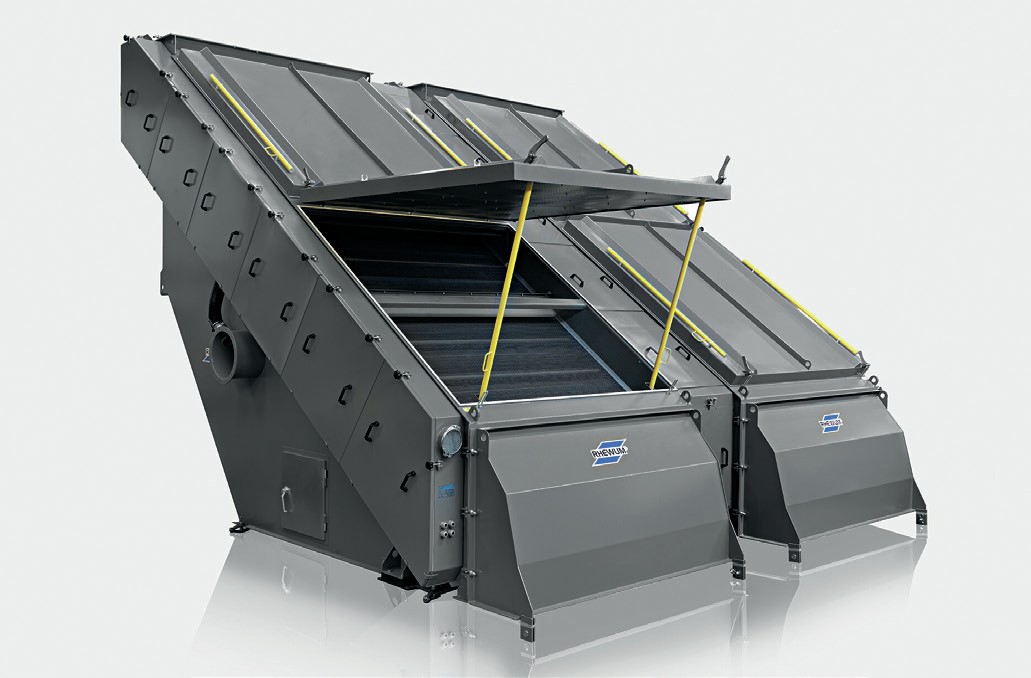
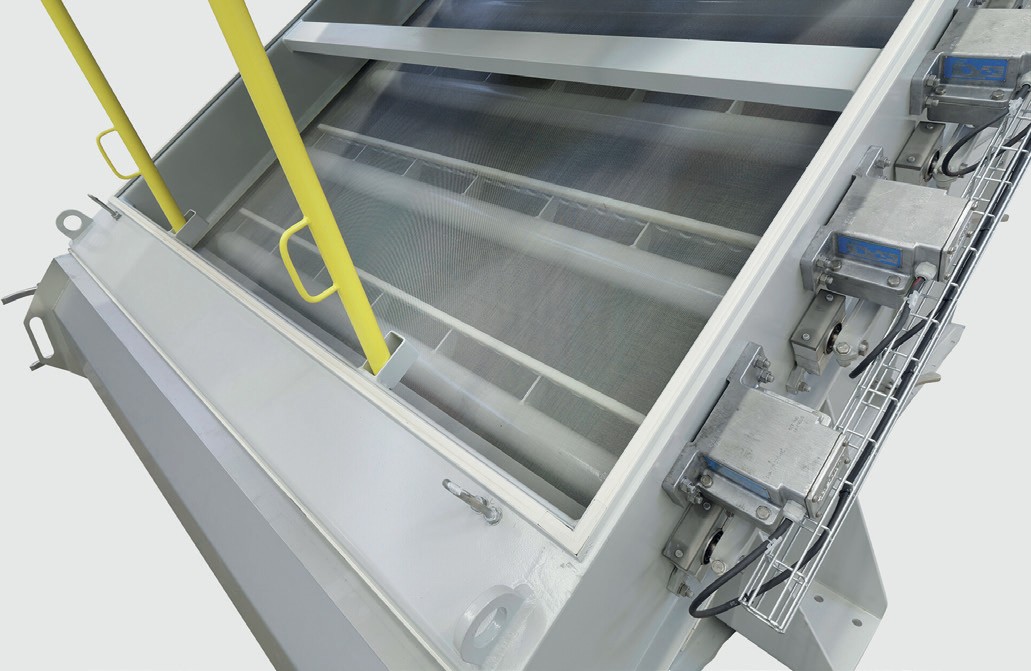
The main requirements for phosphate screening machines are to deliver a high-quality product at high throughput with minimal downtime for maintenance. The desired size separation (typically 90 percent sized between 2-4.5 mm) is a screening challenge due to factors such as clogged meshes. Furthermore, customers demand a high-quality, closely-sized product to ensure that the fertilizer will function efficiently and have a low environmental impact.
Directly-excited screens
The main design concept behind the RHEsono/RHEmoto screening machines is directly-excited screen meshes. These are positioned at an angle to ensure the transport of materials across the whole screen. With direct excitation, it is possible for the screen to reach an oscillation frequency of 50 Hz with particle accelerations of up to 15g. These performance values – which cannot be replicated by other screening machine designs where the whole body moves – result in much higher screening efficiencies per unit area.
Key features are as follows:
- RHEWUM drives. The screen oscillation and beating movement is generated by two available types of drive – the RHEsono and RHEmoto drives – each of which is suited to different tasks. The RHEsono drive is a special, easy-to-install technology developed by RHEWUM. It can be adjusted electrically via a potentiometer and needs little maintenance. The simple and more robust RHEmoto drive, meanwhile, is based on an unbalanced motor. It is more suitable for dry and easy flowing materials that tend not to clog the meshes.
- Mesh tensioning system. Each deck has its own screen cloth. These can be changed individually without requiring the removal of other cloths. This is a very useful option, as different wear rates mean every screen cloth will have its own individual maintenance interval. Overflows from each deck are collected and discharged via an overflow chute. This is pivoted to allow access to the cloth tensioning system for the outlet half of each deck. The inlet half, in contrast, is easily accessed via back inspection doors on top of the screening machines. The tensioning system is also designed for quick tensioning and the easy changing of the cloths.
- Flexible screening process. The capability to adjust every single drive is what keeps the screening process flexible. Ensuring that the inlet drives are on a stronger setting than the outlet drives, for example, mixes up materials and breaks down agglomerates. A lower amplitude outlet setting also improves the probability that near-sized particles will pass the mesh. The steep deck angle keeps material moving across the screen, even if individual drives are switched off. This maintains screen availability even when individual drives fail. The timing of the cleaning cycle, being flexibly programmed, is adjustable during production. The cycle is generally determined by how long and how often the drives need to be turned to maximum to free clogged particles from the mesh.