Sulphur 400 May-Jun 2022
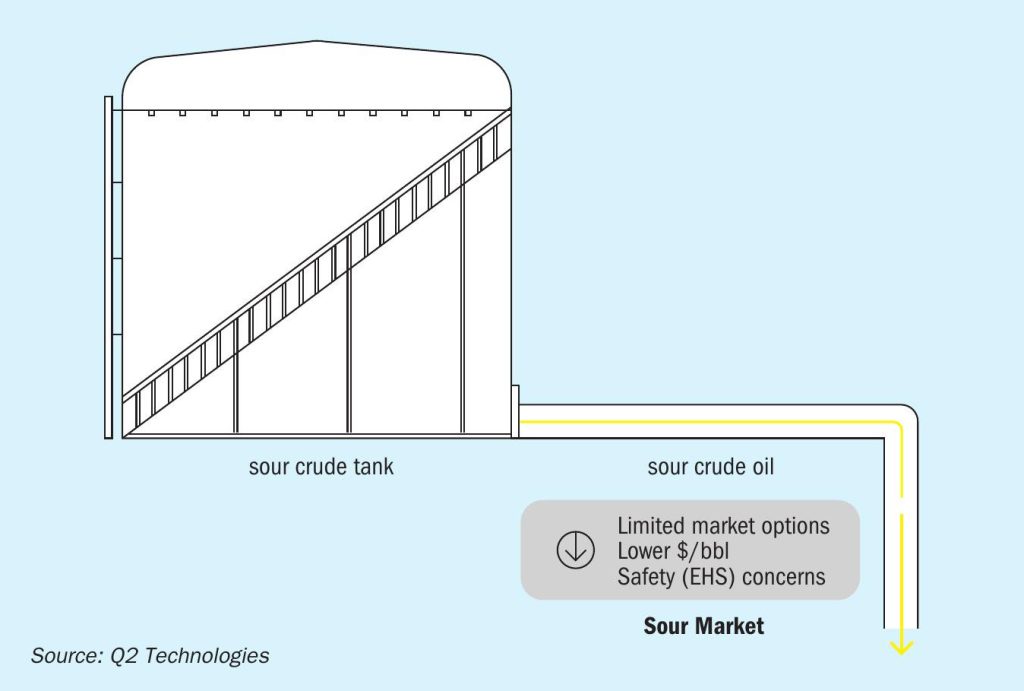
31 May 2022
Meeting oil and gas pipeline quality specifications
H2 S TREATMENT
Meeting oil and gas pipeline quality specifications
A new fully automated process has been developed that combines real time H2 S readings from an H2 S analyser and Q2 Technologies’ proprietary scavenger chemistry to treat high H2 S crude oil on demand. The process provides an efficient and effective way to administer the chemical product to avoid overtreating or undertreating. In some cases, the end user is seeing greater than 50% savings. It is a unique confluence of technology including IoT, advanced chemistry, and oil and gas personnel incentivised to demonstrate continuous improvement.
Meeting commercial oil and gas pipeline quality specifications with regards to hydrogen sulphide (H2 S) is of the utmost importance when it comes to the overall merchantability and safety of a barrel of crude oil. A new automated process for H2 S mitigation using a refiner-friendly H2 S scavenger chemistry is presented. Hydrogen sulphide is an extremely toxic and corrosive gas that can be present in all stages of development in oil and gas, originating deep in geologic formations, the noxious substance can be found in upstream to midstream as well as downstream infrastructure. To be safely managed, H2 S levels need to be lowered.Hydrogen sulphide can cause extensive corrosion and damage to equipment and even at low ppm levels it has the potential to cause death. By successfully treating H2 S and permanently removing this problematic compound, crude oil quality is elevated, which translates into higher netback prices of the barrel. Traditionally,the oil and gas industry has relied on testing methods designed for refined products that do not measure H2 S in crude oil reliably. New technology has emerged that allows for greater accuracy and repeatability that also opens the way for automated H2 S treatment.
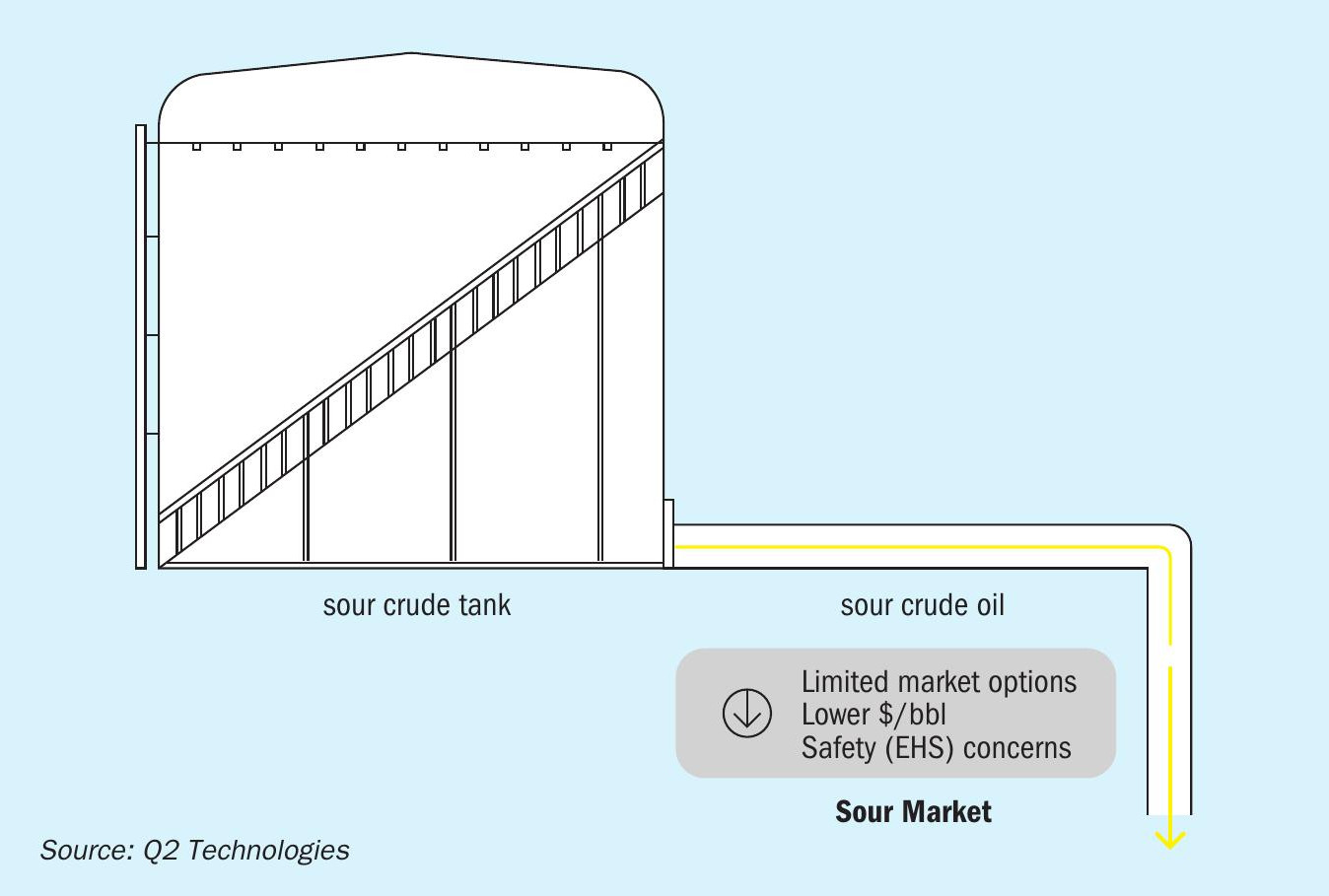
Dealing with H2 S
Historically, if faced with H2 S in crude oil or liquid hydrocarbons, producers had limited options to mitigate the problem (Fig. 1). Both H2 S treatment and measurement options have proven to be a constant challenge. Mechanical H2 S removal solutions have limited scalability and economic feasibility at production sites, so chemical scavenging solutions have become prevalent. Triazine-based scavengers have traditionally been used since the late 1980s to remove H2 S from both natural gas and oil streams. However, using triazine-based compounds may lead to equipment fouling and corrosion. Refiners and consequently midstream companies have banned the use of amine/triazine-based scavengers for these reasons. Alongside treatment, H2 S measurement is key for both quality and safety purposes. Traditionally, testing involves having field personnel responsible for pulling stain tubes on a nearly continuous basis which can be operationally burdensome and potentially exposes operators to the toxic gas. Test methods that have been adopted as industry standard for H2 S measurement in crude oil were first developed for refined products and offer limited accuracy and repeatability.Accuracy is fundamental in how a chemical programme is administered and negating human error and time variability is a critical notion for how Q2 Technologies strategically set a path to change this treatment and testing continuum.
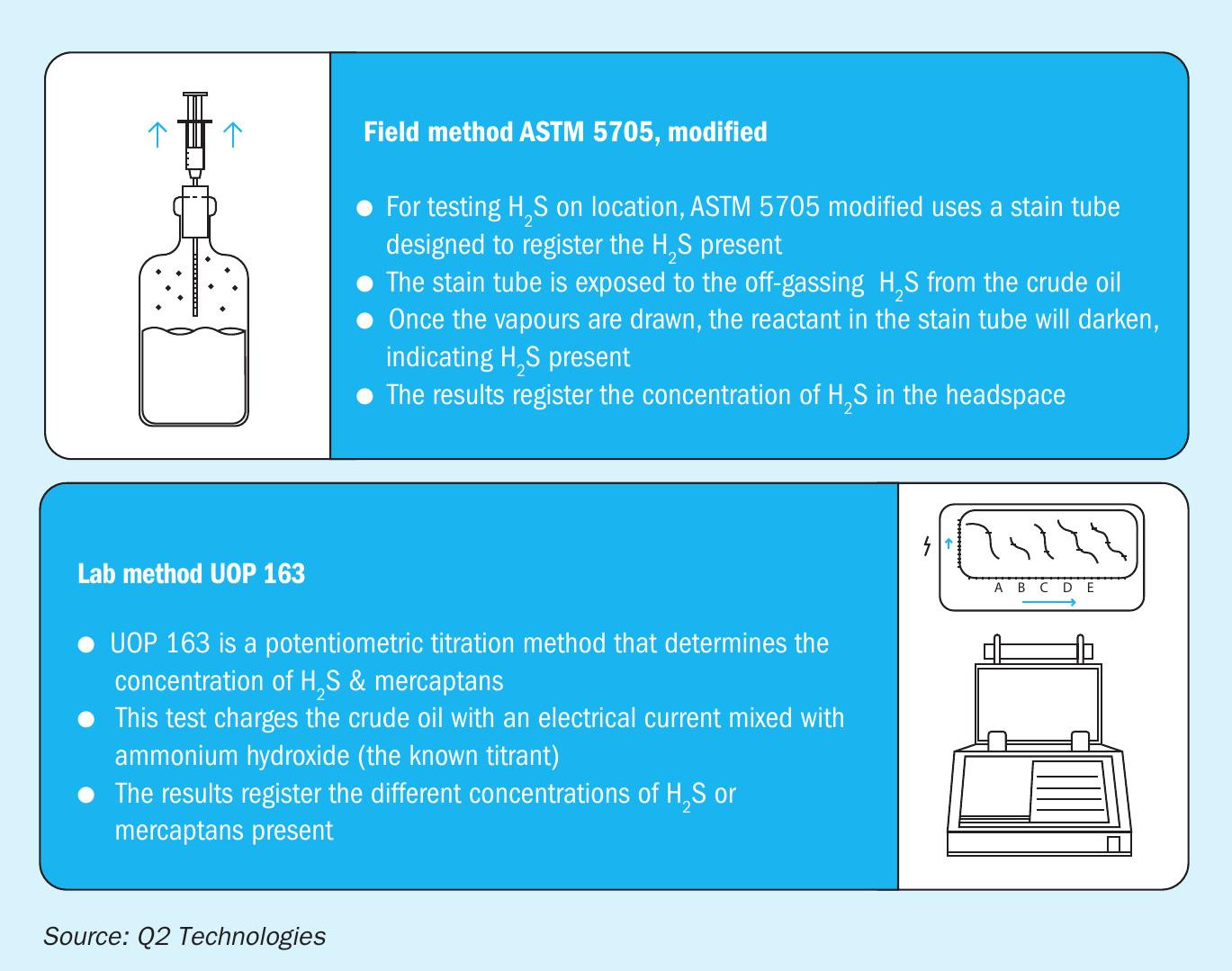
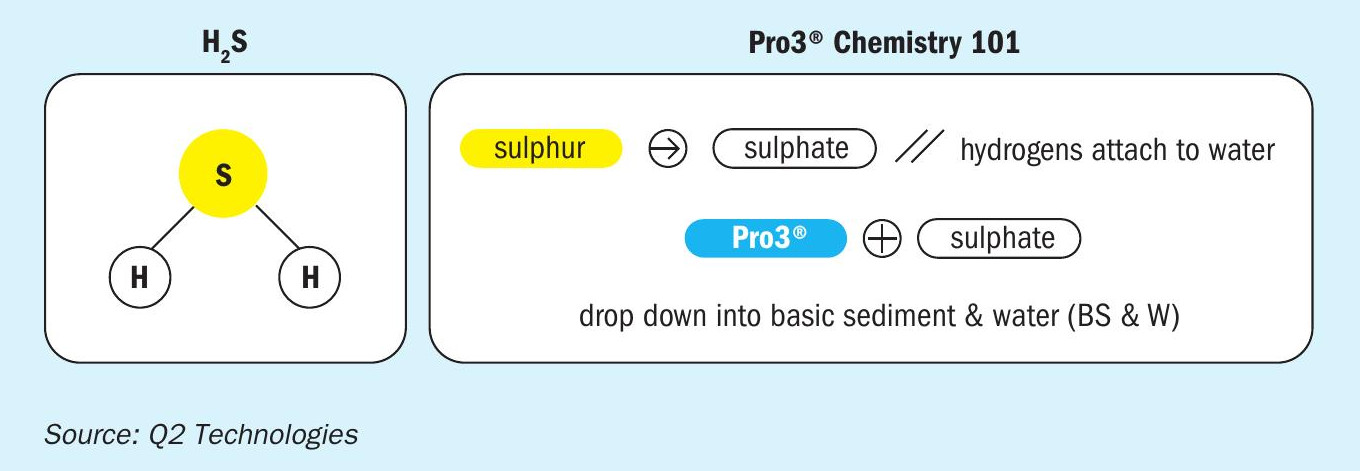
Next generation analyser
Treating H2 S starts with accurate measurements. For field and certification tests in the oil and gas industry, the approved methods (Fig. 2) are ASTM-5705 (modified) and UOP 163. These methods not only offer limited repeatability and accuracy but are not suited for constant monitoring in the field. In addition to testing H2 S, UOP 163 also determines total mercaptans present in a sample.
ASTM-5705 (modified) measures concentrations in the vapour space or ppm/v. UOP 163, alternatively, measures the liquid phase and gives a reading by total weight, or ppm/w. Unfortunately, there is no standard method for aligning the two readings, as they are registering the components of different states of matter, and the properties in one, do not always match the other. So how to determine which test is correct? It depends on what the commercial contract stipulates.
Next-generation H2 S analysers that offer companies the ability to constantly measure H2 S in pipelines on a real time basis, equating to thousands of readings per hour have been developed. Taking manual readings in the field is rife for quality control issues, inasmuch as the manual process cannot take account of the vast amount of variability when taking a stain tube sample. Variabilities include swings in ambient temperature, pipeline pressures, quality of the stain tubes, or the overall operator know-how on taking a sample. Inline H2 S analysers are now becoming more common as pipeline companies need sustainable solutions to continuously manage their crude quality as it pertains to H2 S. Several long-haul pipelines transporting millions of barrels of crude oil per day from West Texas to coastal markets have adopted this new methodology. The analyser works in a closed loop fashion, as the crude oil sweeps past a probe in the pipeline, where a small oil sample routes through an enclosure that analyses the crude for H2 S. Taking the best of both worlds: fresh samples, immediate readings, consistent amount of volume, with lab quality equipment in a temperature-controlled housing. The compact analyser can take up to 70 readings per minute and calculate a ppm/w measurement within 2% accuracy. The technology utilises a specialised membrane where the H2 S is stripped without letting the liquid pass through. With relatively few moving parts, the resulting reading is a continuous H2 S level. Comparing the two methods is one of extreme contrast: an inline analyser can give up to 400 high quality readings in the same time it takes one stain tube reading to be measured. Having access to annotated trends with maximum and minimum variability spread out over time versus a single data point is the equivalent to watching a 4k movie versus viewing a single photo.
Technologically advanced chemistries
Even though amine- and triazine-based scavengers have been widely used for H2 S removal in oil, refiners have been pressuring chemical producers for friendlier alternatives that are not corrosive to their equipment. This has led to commercial deducts placed on amine/triazine contaminated oil. Several midstream companies now monitor amine content in their crude quality assays to ensure oil marketers are not fined by their refining customers. To address the market need for non-amine and non-triazine chemistries, Q2 Technologies has engineered the Pro3® line which uses breakthrough non-amine/non-glyoxal H2 S and mercaptan removal technology. The Pro3® technology requires far less chemical use, up to 50-75% as compared to glyoxal and MEA-triazine. This innovative technology is currently used by producers, midstream companies, and commodity traders and it has been approved by major terminals and pipelines to treat millions of barrels of oil per month. The chemistry not only provides cost savings to producers needing to treat their oil to meet commercial requirements but allows midstream companies and traders to maximise market options for clean oil barrels. Refiners, in turn, reduce costly downtime brought by previously used amine/triazine-based chemistries.
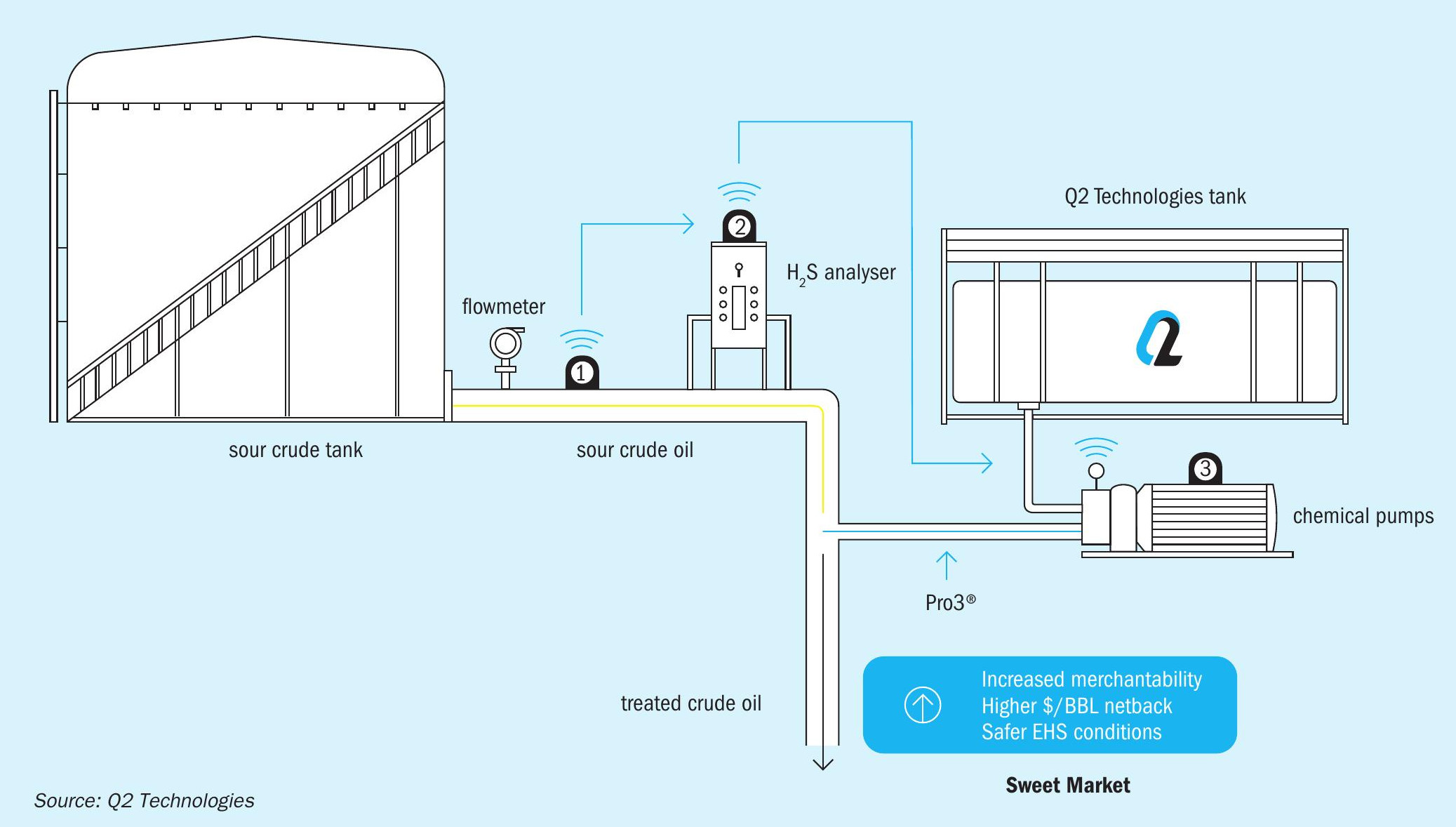
Some producers have invested in sulphur reduction treatment at the wellhead to reduce the fouling of gathering lines. Chemicals manufacturer Q2 Technologies is among the leading chemical suppliers partnered with E&P and midstream operators to clean up Permian barrels. In one case it helped bring more than 50,000 b/d of Permian production to mercaptan levels of less than 75ppm, compared with pretreatment levels of up to 600ppm.
What makes Pro3® so unique is its ability to chemically alter the base H2 S structure in a quick and scalable manner. The chemistry brings a proprietary blend of polymers that react with H2 S to form a non-hazardous sulphate molecule (Fig. 3). The efficient reaction allows for scalable treatment all the way from wellheads producing a few hundred barrels per day up to treating tens of thousands of barrels per hour when ships are being loaded. The chemistry is water based and oil dispersible which allows for easy separation in the desalting process at refineries.
Real time analyser + advanced chemistries
A fully integrated system has been developed to automate H2 S treatment in midstream applications that allows for costeffective and transparent treatment. Pairing the H2 S analyser with an accurate flow reading (reading from a flow meter) to a pump that has variability control, allows for a fully automatic system to respond accordingly in real time to throttle the appropriate chemical dosage on an on-demand basis. Due to the placement of the analyser upstream of the Pro3® injection point, if a spike of high H2 S is detected in the pipeline, the system can account for these surges and will treat accordingly. When the H2 S fluctuation drops back to normality, the pump will throttle down and back off the injection rate. Commercial and financial results are immediate: the resulting exact amount of chemical translates into not over treating or under treating, which in turn yields crude oil that meets pipeline specifications in an ongoing manner. With a hyper automated process running in the background, producers and midstream clients are able to redeploy their field personnel back to their current job and manage the automated system on an exception-basis.
Clients gain valuable insight into meaningful KPIs such as $/barrel treated or gallons/hour and can see in real time the effect the product is having on their bottom line.
An integrated solution
From a field personnel perspective, managing an H2 S programme can be a full-time job. Conceptually, it makes sense: ondemand treatment frees up field personnel to focus on their main asset objectives. But how does it work and is the technology compatible with current systems?
With a fully integrated H2 S treatment system, the sour crude is analysed and treated flawlessly as it flows through the pipeline. The flowmeter, the H2 S analyser, and the pump work together for appropriate dosage (Fig. 4).
For an effective measuring and dosing treatment solution, the programmable logic control or PLC, is another critical component for the combined system to run smoothly. The PLC runs a simple script that needs only a few inputs. First, as previously detailed, the H2 S analyser sends a signal to the PLC control via a variety of methods, be it a 4-20mA signal or via SCADA or other secure encrypted methods. Second, the operator will have a flow data meter near the analyser to give an accurate indication of how much volume is sweeping by at the point in time when the H2 S level is measured. There are a variety of ways flow is calculated and some of the units available today are quite sophisticated with the Coriolis and ultrasonic flow meters leading charge.
The PLC then communicates these inputs to a variable rated pump that follows a logic table for dosing, simply put, at a certain H2 S level with a specific bbl/ hr, the PLC configures a resulting dosage that the pump will inject. This action is then repeated and adjusted accordingly every 15 seconds. The constant fine tune adjustments ensure that the crude oil is being dosed appropriately in an ongoing manner. Storing chemical products in ISO tanks offers the client ways of monitoring tank levels via satellite telemetry and potentially optimised resupply configuration that standard totes cannot provide. Offering these added ease-in-operations benefits ensures that there is never a gap in treatment. Lastly, as with any automated system, the team members monitoring the setup are essential for long-term success. Having a logistics team dedicated to monitor all of the ISOs deployed, making sure the logic displayed on mobile and control room dashboards is sound, and that the updated predictive usage calculations are being configured correctly is critical for a successful treatment solution.
Highly automated systems also need to account for troubleshooting and be capable of defaulting into a safe or manual mode. Prudent service providers recognise this aspect of the process. If the analyser registers anomalous readings, the unit has the programming to recalibrate itself if these outliers are detected. Further, the PLC can acknowledge when these trips occur and will send the last verified H2 S reading and appropriate dose to the pump. A redundant pump and dual head configuration are always recommended, this ensures that if a component of the pump fails, the unit will compensate to avoid any downtime. Lastly, being able to view the equipment on a mobile device is essential. Dashboards provided on an encrypted web-based app, display visual representations of the current H2 S levels, injection rates of the pump, and allow for the operator’s field personnel, control room technicians, and chemical provider to remotely monitor and bypass the system if needed.
In conclusion, providing alternatives to treating H2 S with improved technologies is a path producers, midstream companies, and commodity traders are currently seeking to reassess their assets in order to gain efficiencies and increase their overall value. By accurately measuring H2 S on a consistent and repeatable basis, dosing parameters can be fine tuned to account for fluctuations. Furthermore, when comparing this next generation of H2 S and mercaptan chemistries to that of previous generations, the results are in the form of immediate savings, and ultimately, a better netback price on the barrel. And finally, a total H2 S treatment solution for the client puts the technology provider in a category of trusted partnership – where open communication and responsiveness is key in keeping a highly automated solution up and running.