Sulphur 400 May-Jun 2022
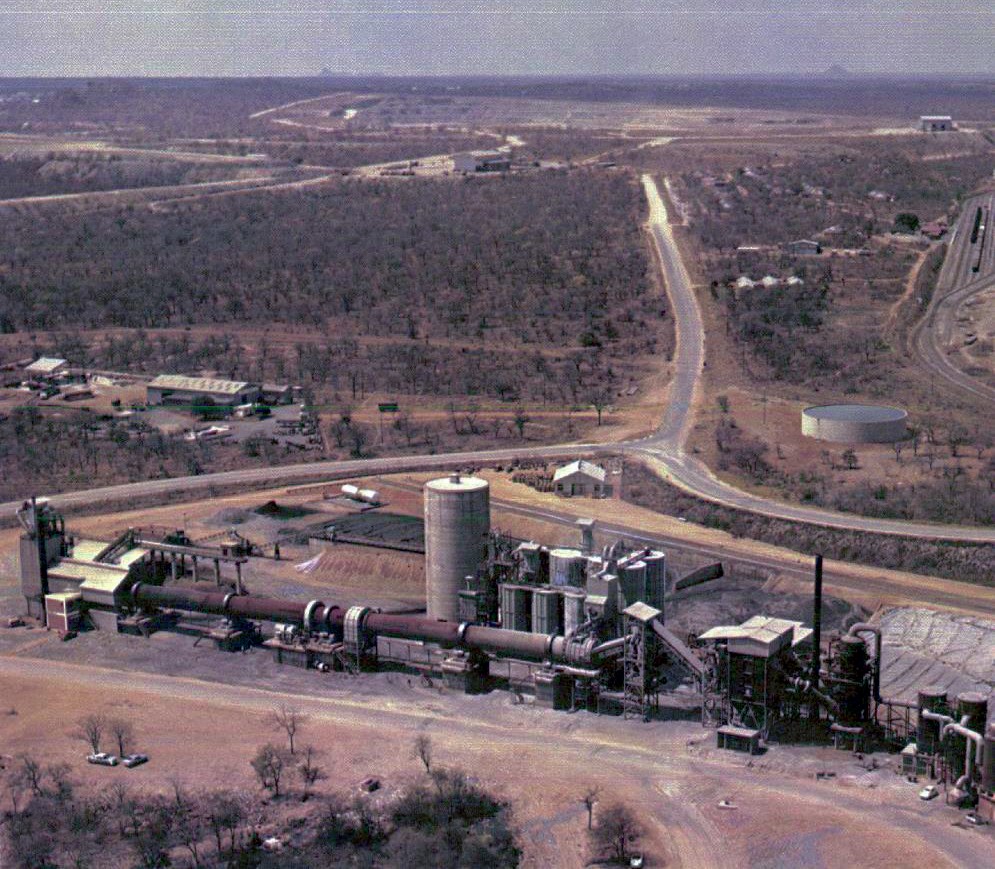
31 May 2022
Phosphogypsum use in a circular economy
PHOSPHOGYPSUM USE
Phosphogypsum use in a circular economy
The economic conversion of phosphogypsum waste into a valuable product has been pursued for decades. Although phosphogypsum is still generally disposed of as waste, industry attitudes are changing and greater use of phosphogypsum will be expected in a circular economy.
The global expansion of phosphate fertilizer manufacturing is generating ever larger volumes of phosphogypsum waste. The conventional manufacturing route for phosphate fertilizers involves treating phosphate rock with sulphuric acid to make phosphoric acid. This intermediate is then used to produce a range of finished fertilizers (e.g., MAP, DAP, TSP). But although commercial fertilizer is the primary objective, a gypsum-rich waste known as phosphogypsum is the most abundant material produced by this wet process route. About 4-6 tonnes of phosphogypsum are generated as a waste by-product for every tonne of phosphoric acid produced. This corresponds to annual phosphogypsum production of around 250 million tonnes globally.
Billions of tonnes of this material are currently being managed at great cost within giant waste stacks. Although gypsum is the main constituent of phosphogypsum, a range of other impurities can also be present, including residual phosphate, fluoride, organic matter, iron, aluminium, heavy metals, and radionuclides. Certain countries have placed legal restrictions on the disposal and use of phosphogypsum due to the presence of these impurities.
Table 1 shows the impact of phosphogypsum impurities on plaster and cement quality1 .
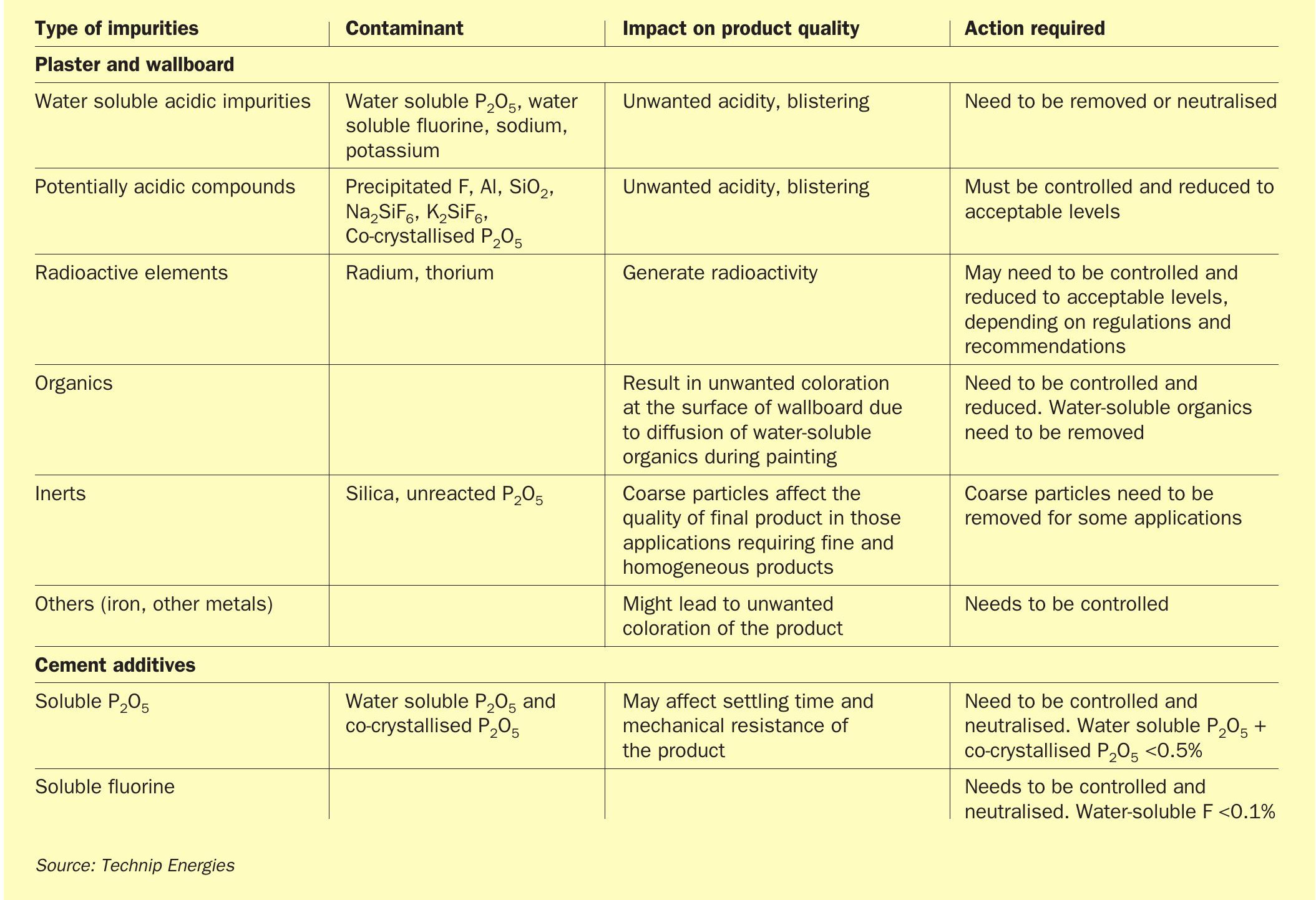
This raises two fundamental questions: How is phosphogypsum best managed and to what extent can it be transformed from waste into a valuable resource?
Impact of the phosphate rock
The phosphate rock used in phosphoric acid production is the main source of residual impurities present in the phosphogypsum generated. For this reason, the composition and purity of phosphate rock raw materials have an important impact on the quality of the phosphogypsum.
Igneous phosphate rock types, such as apatite ore from Kola, Russia, and Phalaborwa, South Africa, and calcined rock have lower impurity levels and organic content compared to sedimentary rocks.
The phosphogypsum produced from these rock types, depending on the phosphoric acid production technology used, can be sufficiently pure to avoid further treatment, or only require simple washing of the repulped gypsum to reach the required purity. However, these phosphate rock types only represent 15-20% of overall world production and are generally more expensive compared to sedimentary phosphates.
Sedimentary phosphate rocks, in contrast, generally contain higher levels of mineral and organic impurities relative to their igneous counterparts. Consequently, when sedimentary rocks are consumed as raw materials for phosphoric acid – as is the case in most plants globally – the amounts of impurities remaining in the phosphogypsum are correspondingly higher, and a purification step is therefore generally necessary.
Regardless of the technology used for phosphoric acid production, some contaminants, such as soluble impurities and organics, will still affect the quality of phosphogypsum and therefore need to be removed prior to reuse.
Processing phosphate rock
There are several options for producing phosphoric acid from phosphate rock via the wet process route. Differences between these process options are mainly determined by calcium sulphate (gypsum) crystallisation conditions. Generally, gypsum is either precipitated in di-hydrate (DH) or hemihydrate (HH) form, or as a combination of both in successive steps. Crystallisation is a particularly important parameter when selecting a process technology that generates ‘clean’ gypsum as the desired by-product.
Standard single step DH process
The single-step DH process is widely used to produce phosphoric acid. The phosphate rock is treated with sulphuric acid to precipitate calcium sulphate as DH in one step in a reactor under agitation. A large recycling flow is achieved by agitation and/ or by external circulation associated with a flash cooling system.
The single-step DH process is a longstanding and mature industrial-scale technology that has been implemented since the 1950s. This process is by far the most flexible, compared to other phosphoric acid production routes, especially in terms of tolerance to phosphate rock impurities. Because of this, the DH process can handle a wide range of phosphate rock types. Its flexibility, together with low capex and high operability, are probably the main reasons why a large majority of the world’s phosphoric acid plants utilise the DH route.
It is generally accepted that the standard DH process achieves recovery yields of approximately 95-96% – this corresponding to typical reaction yields of 96-97% P2 O5 . If left untreated, with no removal of soluble impurities, this leaves approximately 0.8-1.1% residual P2 O5 remaining in the gypsum, unfortunately exceeding the quality standards for plaster or cement production.
The hemihydrate (HH) process
The single-step HH process has been successfully implemented in different countries around the world as an alternative to the DH route. The HH route presents several advantages, such as the production of higher strength acid (39-42%) containing less impurities. But the process does have a lower P2 O5 recovery (typically around 92%) compared to the DH route.
The PG produced from the HH route also contains more P2 O5 and more impurities, compared to phosphogypsum produced via the DH route. The fact that HH gypsum reverts to the DH form, at a certain point post-production, is another constraint limiting the purification of phosphogypsum. For these reasons, the HH route is generally not an option when there is a need to recover phosphogypsum for industrial applications.
Recrystallisation processes: DH-HH and HDH
Those technologies based on recrystallisation – either Hemihydrate to Di-Hydrate (HDH) or Dihydrate to Hemihydrate (DHH) – offer the highest P2 O5 recovery. This is due to the liberation of the co-crystallised P2 O5 during recrystallisation. These processes can also produce acid at higher strength compared to DH.
These advantages are offset by other factors, particularly the lack of flexibility of recrystallisation processes towards impurities. Because of this, their performance can depend strongly on the nature of the phosphate rock used as a raw material. Plants based on recrystallisation processes, being more complex and requiring more equipment, have lower plant availability, higher capex, and higher maintenance costs, compared to DH plants. Neither do recrystallisation processes provide significant advantages in terms of contaminant levels in phosphogypsum (fluorine, sodium, organic matter etc.). This makes additional treatment of phosphogypsum necessary before further use.
The two-stage Diplo process
In the 1980s and 1990s, a new approach to the DH method was developed by the French company Rhône Poulenc, the phosphoric acid technology predecessor to Technip Energies. The main purpose of this evolution in DH technology was twofold: firstly, to obtain higher P2 O5 yields and, secondly, to increase the concentration of the dilute acid produced at filtration.
This new approach successfully generated both higher P2 O5 yields and acid concentration, while keeping the original operational advantages of the DH route. This was of particular interest to producers in Europe who were sourcing from the merchant rock market and facing strong economic pressure to reduce their operating costs.
In the Diplo process, phosphate rock is digested using two reactors in series, with each reactor being fed phosphate rock, sulphuric acid and recycled phosphoric acid in set proportions (Fig. 1). The conditions of the reaction – including temperature, P2 O5 concentration, and concentration of free sulphate in the acid – are optimised at each stage. In doing so, the Diplo process allows overall process performance to be optimised, according to the requirements of the producer, while still retaining most of the advantages of the traditional DH process.
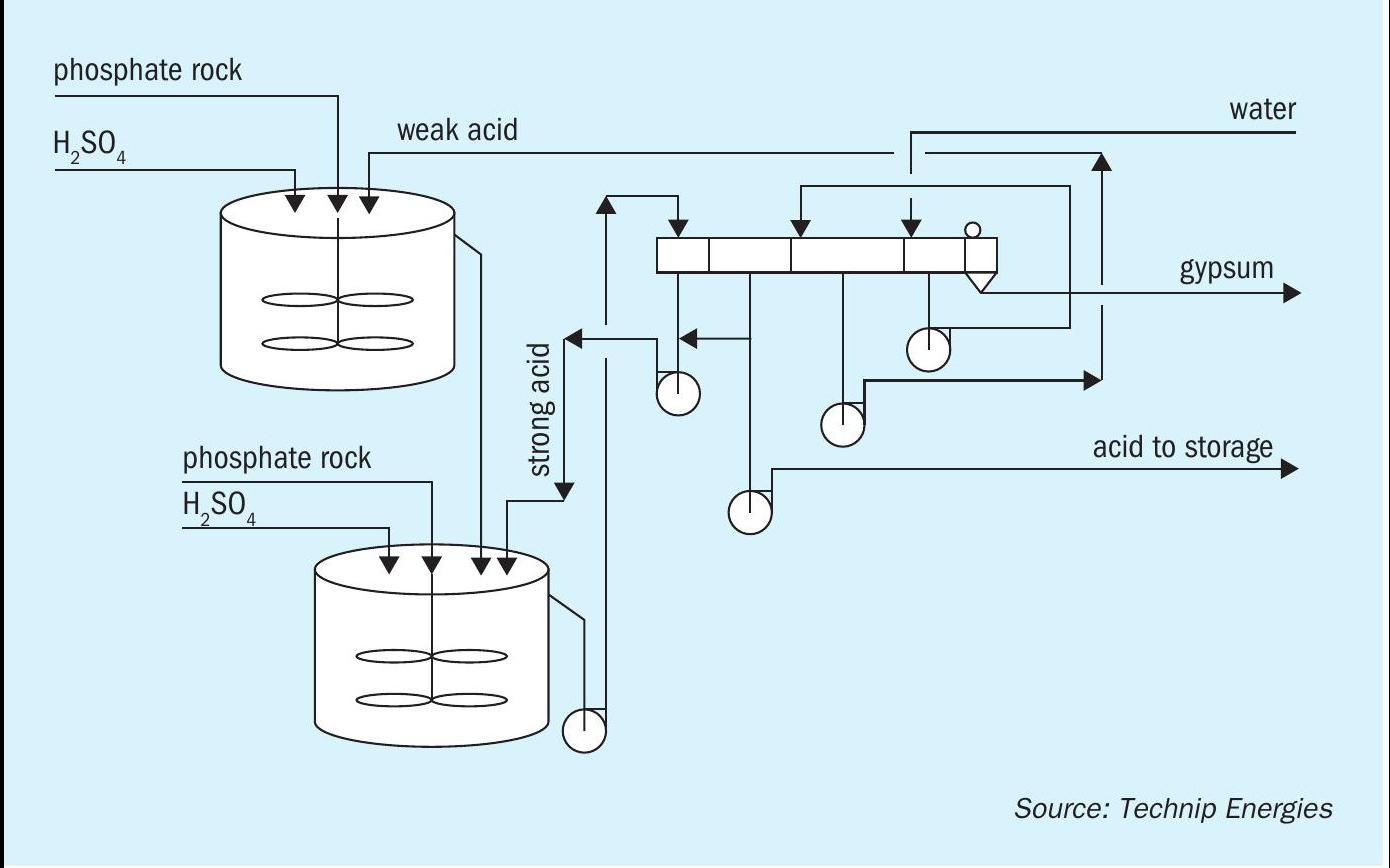
Diplo process for high P2 O5 recovery
When targeting high P2 O5 yields, 70-90% of the phosphate rock is reacted in the first reactor. The first reactor is operated at lower P2 O5 concentration, higher temperature and with higher excess sulphuric acid. Combined, these conditions tend to reduce co-crystallised losses in gypsum.
The remaining phosphate rock is reacted in the second reactor, increasing the P2 O5 concentration of the acid. Excess sulphuric acid in the second reactor slurry is typically regulated close to 25-28g/l. This limits unreacted P2 O5 losses and avoid excess sulphate in the phosphoric acid produced.
From waste into valuable product
It is estimated that some 50-60 million tonnes of phosphogypsum is now being utilised worldwide2 . A recently published study by the International Fertilizer Association (IFA) reveals that up to 25% of phosphogypsum produced annually is now reused for a range of applications, such as mine restoration, agriculture, plaster, and cement manufacture3 .
While other usage estimates are less optimistic, there remains a clear upward trend with more phosphogypsum recycling over the last decade. This trend is expected to continue in the 2020s, along with new regulations and industrial technologies promoting more sustainable resource use.
Notable examples of commercial phosphogypsum use include:
- In Belgium, phosphates producer Prayon sells high-quality phosphogypsum for the cement and plaster market.
- ln Brazil, most phosphogypsum now goes to agriculture (5 million t/a) following its reclassification.
- ln Canada, Nutrien uses phosphogypsum for agriculture and, working with forestry service, afforestation using man-made ‘anthrosols’ phosphogypsum mixed with soil in a 9:1 ratio.
- ln China, Wengfu Group uses more than half of phosphogypsum output in agriculture and construction or recycles it as ammonium sulphate/calcium carbonate.
- In Kazakhstan, phosphogypsum is use in the large-scale remediation of saline/sodic soils.
- ln India, phosphogypsum was reclassified as a co-product, not waste, in 2008 and is widely sold for construction, agriculture, soil additive, cement and as bagged fertilizer (Paradeep). Examples include afforestation for green energy (Coromandel) and road construction (Paradeep).
- ln Russia, PhosAgro uses phosphogypsum in agriculture, construction, and road building.
- ln Tunisia, phosphogypsum is used for remediation and to return land to productive use in Sfax, brickmaking, road construction and housing.
Phosphogypsum in construction
Phosphogypsum for cement and plaster in Belgium
Prayon provides a leading example of a successful circular economy approach to phosphogypsum use. The leading technology licensor, phosphates producer and equipment manufacturer has actually been selling gypsum as a co-product for more than forty years4 .
The company sells virtually all of the phosphogypsum it produces at its phosphoric acid plant in Engis, Belgium, compared with 80-90% 5-6 years ago5 . In 2018, for example, Prayon sold 708,000 tonnes of phosphogypsum for plaster and cement manufacture, with a further 60,000 tonnes sold for agronomic use, from output totalling 790,000 tonnes.
When it comes to selling phosphogypsum, Prayon attributes its successful track record to several factors: notably the quality of its product, which in turn is attributable to the Central Prayon Process (CPP) used at its Engis plant, and the company’s long-term partnerships with its gypsum customers.
The CPP, with its double crystallisation and two filtration steps, is exceptionally efficient. The process is, however, only responsible for about 1% of total phosphoric acid production globally. Key features of the CPP include:
- Flexibility: process can accommodate a wide range of phosphate rock types.
- High recovery: reduces phosphate rock consumption and generates a saleable gypsum co-product.
- High P2 O5 content in the filtered acid: reduces steam and therefore energy consumption.
- Self-drying gypsum: phosphogypsum from the CPP process naturally cures from wet hemihydrate (HH) to dry dihydrate (DH), meaning less fuel oil is required to process gypsum.
- Environmentally friendly interim storage: neutralised phosphogypsum with a low P2 O5 content is stored as a temporary ‘gypsum quarry’ rather than a waste stack.
Prayon’s commercial customer Knauf established a plaster production plant close to Engis in Belgium on the opposite bank of the River Meuse. Phosphogypsum from Prayon’s production plant istransported by conveyor belt across the river to a discharge point where it is temporarily stored.
Over a period of several weeks, the phosphogypsum cures naturally in-situ, reverting from wet hemihydrate (HH) cake (18% free water, 6% crystalline water) to rehydrated dry dihydrate (DH, 5% free water, 19% crystalline water). The resulting gypsum product requires no further treatment prior to its shipment down river by barge to Knauf’s stucco plaster factory.
In 2018, some 90 percent of phosphogypsum generated by Prayon at Engis met Knauf’s HH feedstock specifications, while eight percent was used in agriculture, leaving just a minor volume in the interim storage area.
Prayon is currently collaborating with the British company Carbon Cycle on the innovative PureGYP process. This novel purification technology is designed to clean phosphogypsum so that it can be sold, rather than stacked, and offers the following advantages:
- Extracts fluoride and phosphate making phosphogypsum suitable for cement and plasterboard manufacture
- Typically removes 96% fluoride and 99% phosphate
- Widens the range of usable phosphate rock sources
- Has the potential to convert phosphogypsum stacks into valuable raw material quarries.
Phosphogypsum for cement in Senegal
Industries Chimiques du Senegal (ICS) is the largest producer of phosphate fertilizer products in sub-Saharan Africa and the third largest producer on the continent. The company began mining phosphate rock in 1960 and later started producing phosphoric acid in 1984.
Following the acquisition of ICS by Indorama in 2014, a rehabilitation programme has improved phosphoric acid output with levels expected to recover to 600,000 t/a P2 O5 . ICS Indorama currently operates two phosphoric acid trains – Darou 1 and Darou 2 – both based on Technip Energies’ technology.
Darou 2, the second train, was started in 2002 with a nameplate production capacity of 1,200 t/d (reaction-filtration), and a nominal capacity for 53% phosphoric acid of 1,015 t/d. This unit, which is based on Technip Energies’ two-stage Diplo technology, is designed to consume a blend of Taiba rock phosphate concentrate and slimes. This allows Darou 2 to achieve a reaction yield of 97.7-98 percent P2 O5 recovery. The corresponding 2-2.3%reaction losses represent insoluble P2 O5 , this consisting of a 50:50 mixture of unreacted P2 O5 and co-crystallised P2 O5 locked in the gypsum. The total insoluble P2 O5 remaining in the gypsum is below 0.5%. At ICS Indorama, the phosphogypsum produced by the phosphoric acid plant is discharged dry and stacked, where it is then exposed to the prevailing weather including both rain and sun. Under these repeated wetting and drying conditions, a decrease in mainly soluble P2 O5 and fluorine occurs. The residual humidity – an important factor for the economics of phosphogypsum reuse – is also reduced below 10% free water due to natural drying.
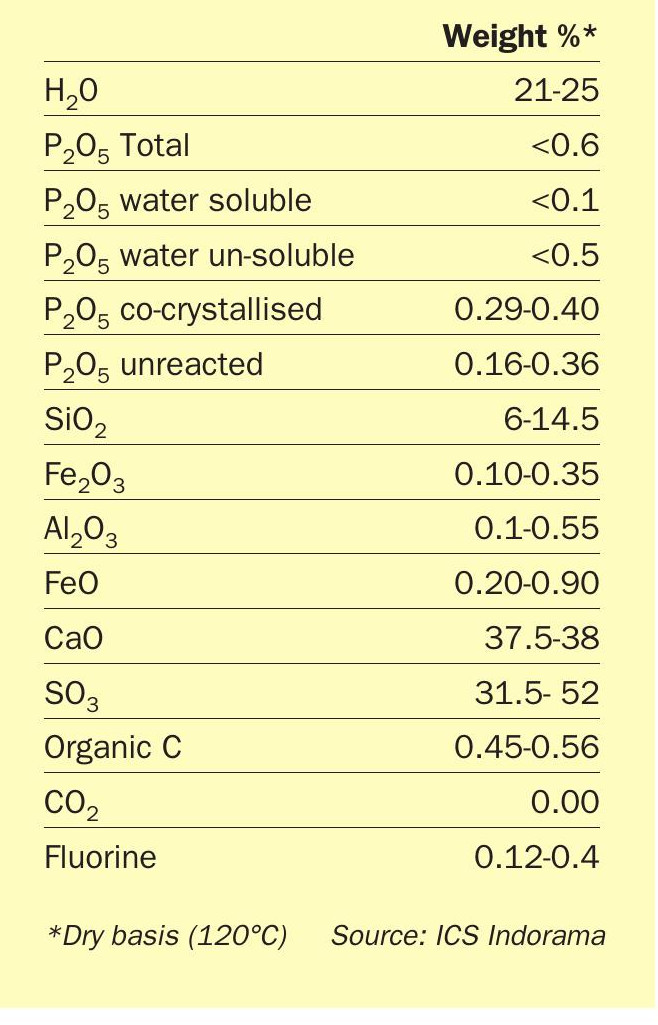
Aged phosphogypsum is reclaimed and directly used as an additive for clinker production without further treatment. An analysis of ICS phosphogypsum sampled from various depth in the stack is provided in Table 2.
ICS Indorama is exploring other potential markets for phosphogypsum, including use as an agricultural soil amendment and use in the remediation of saline soils. The company has developed a new phosphogypsum formulation for soil amendment purposes. This granulated product functions as a calcium source and contains residual P2 O5 and useful secondary elements such as magnesium and sulphur, all of which contribute to soil fertilisation.
This use of phosphogypsum as a constituent in roadbed construction is another potential application being targeted by ICS Indorama. As a result of these efforts, industrial and agricultural sales of phosphogypsum have increased substantially in recent years, generating additional revenues for the company.
Phosphogypsum treatment processes
The OSW-Krupp process
The OSW-Krupp phosphogypsum process was responsible for some promising early examples of commercial phosphogypsum use. This process combined phosphogypsum with additional clay, sand, coke, and natural gypsum to generate equal amounts of sulphuric acid and Portland cement.
A number of OSW-Krupp plants were built between 1956 and 1980 in South Africa, Poland, Austria, and Germany. Although their main purpose was to recover sulphuric acid from phosphogypsum via thermal decomposition, valuable clinker for the cement industry was also produced. Cement clinker is an intermediary in the manufacture of Portland cement and is conventionally produced by sintering limestone and clay in a cement kiln.
The OSW-Krupp plant in Phalaborwa, South Africa, is a typical example (Fig. 2). This conversion plant, which had a design capacity of 105,000 t/a each for sulphuric acid and cement, was commissioned in 1972 and subsequently operated for 15 years.
The OSW-Krupp plants were eventually closed for economic reasons – with access to lower cost sulphuric acid being a deciding factor – although meeting cement quality and environmental standards were also issues.
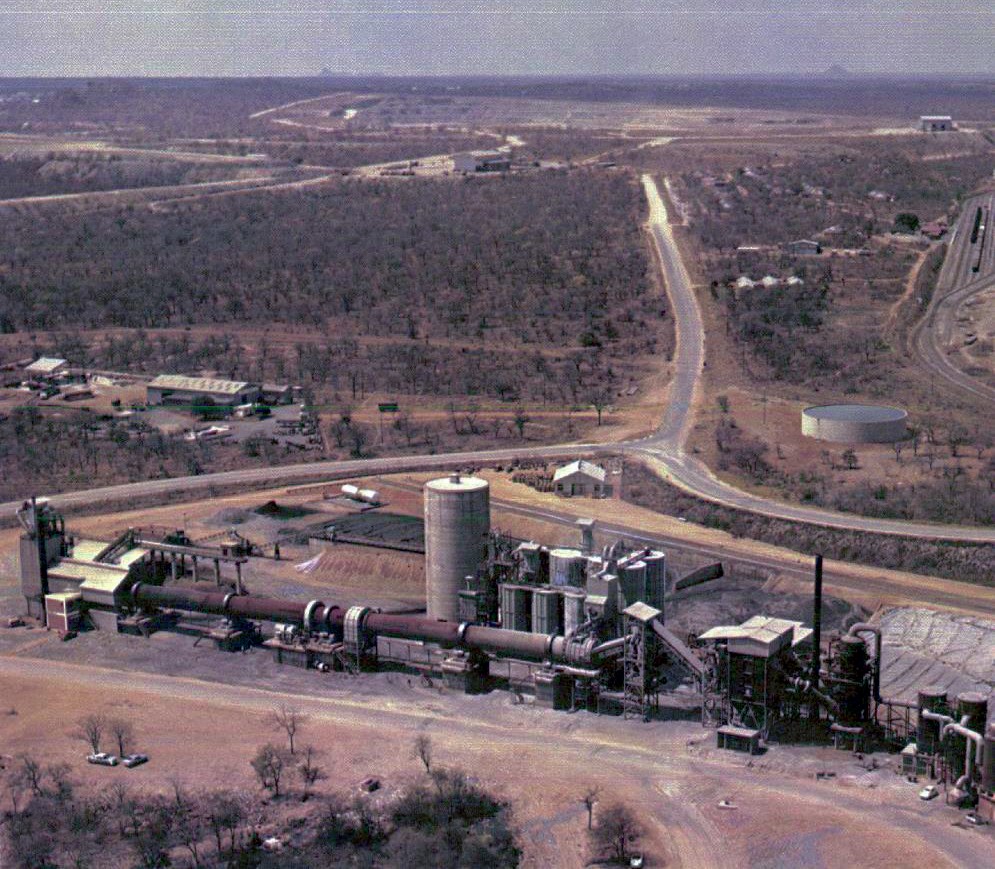
New tkIS phosphogypsum treatment process
thyssenkrupp Industrial Solutions (tkIS) has conducted intensive research with the aim of developing a technology to convert phosphogypsum into a valuable product for the circular economy6 .
The latest phosphogypsum treatment process from tkIS is based on the original conversion process for the OSW-Krupp plants. An investigation of the performance of these plants revealed that pre-treatment is required before phosphogypsum is suitable for downstream production of high-quality clinker/cement or other building materials. The literature on other approaches to phosphogypsum treatment were also reviewed7,8 .
Phosphogypsum from various phosphoric acid plants was chemically and mineralogically analysed prior to developing the treatment process. Additionally, information was also gathered on the specifications and quality requirements for cement and other building raw materials. Once this data had been collated, a laboratory-scale phosphogypsum treatment process was developed and tested using a step-by-step approach.
Once the laboratory tests were completed, results were transferred into a kinetic process model. This model was then used to predict the treatment process parameters needed to achieve the necessary phosphogypsum quality. In this way,only a few laboratory tests are required to confirm a suitable process design for the new PG treatment method.
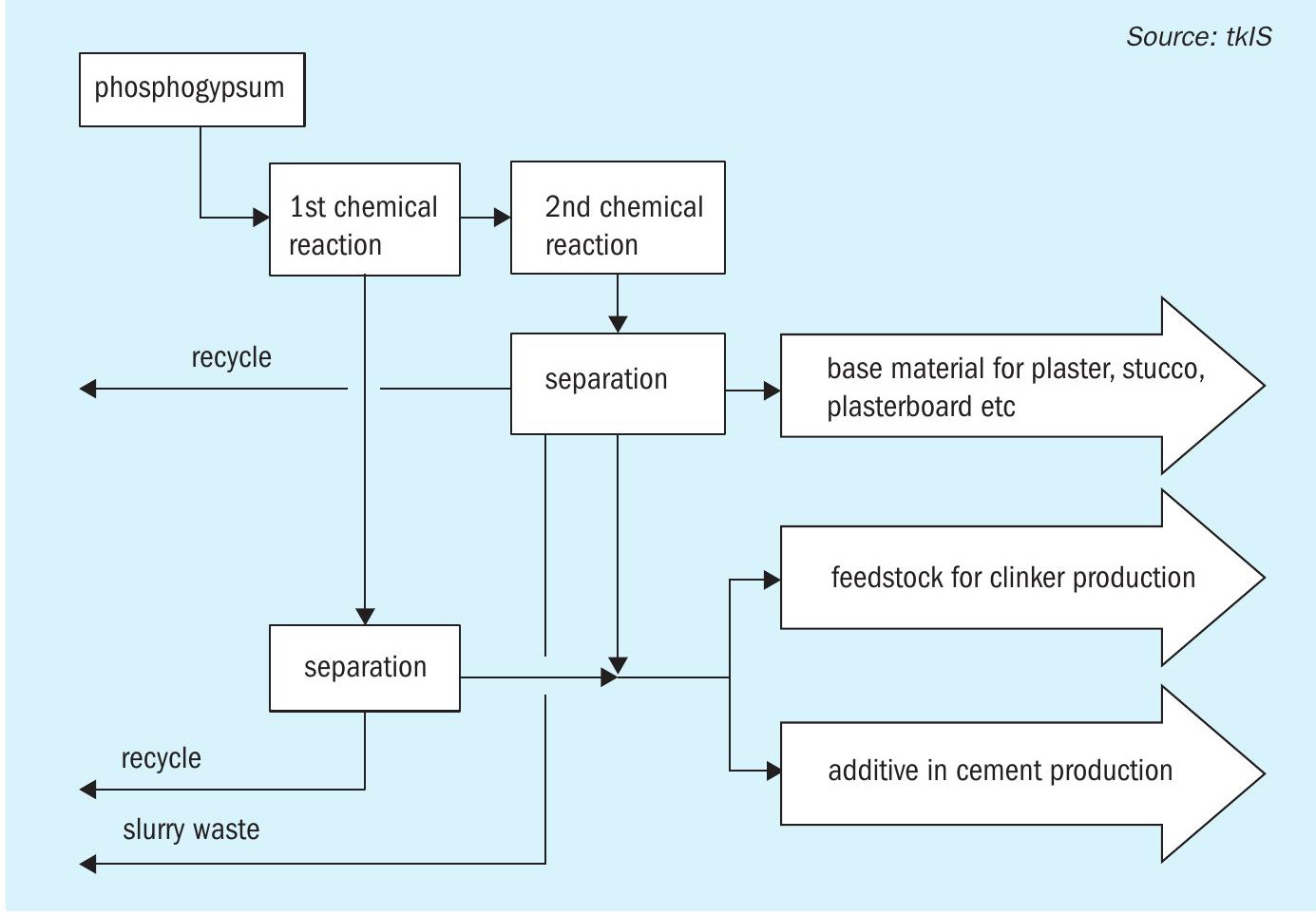
Treatment process results
The new phosphogypsum treatment process consists of two main steps in sequence. Each step involves a chemical reaction followed by liquid-solid separation (Fig. 3).
In the first treatment step, chemical impurities (P2 O5 , fluorides and others) are separated from the phosphogypsum and removed in the liquid phase. This can, if required, be recycled to the phosphoric acid plant. After this step, the quality of the treated phosphogypsum obtained should meet clinker/cement production requirements.
The aim of the second treatment step is to reduce radioactive components, especially radium, so the quality of the resulting phosphogypsum meets building materials requirements. This treatment step is optional, depending on the composition and quality of the untreated phosphogypsum.
The first treatment step performs well, being very effective at P2 O5 reduction (see Fig. 4). A typical recovery rate of significantly more than 90% of P2 O5 is possible, the exact reduction depending on the process regime. Importantly, the liquid phase containing the dissolved P2 O5 is fully reusable in the phosphoric acid plant – and therefore contributes to the overall P2 O5 efficiency of the production complex. The first treatment step has also been shown to be equally effective at reducing the fluoride content of phosphogypsum.
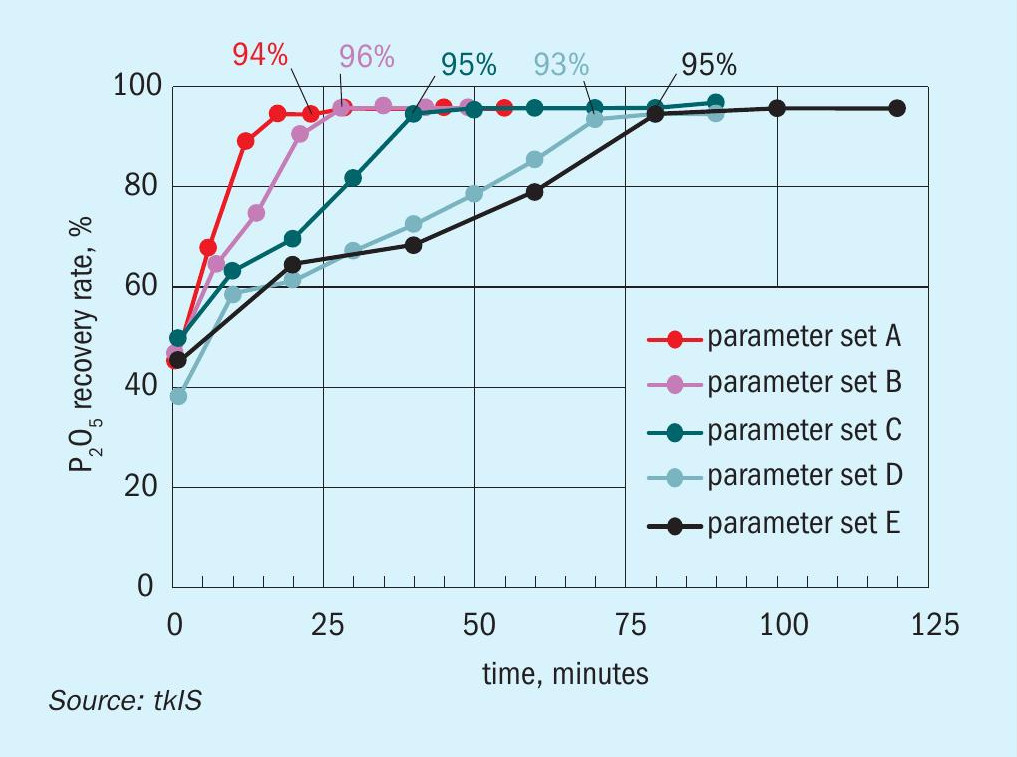
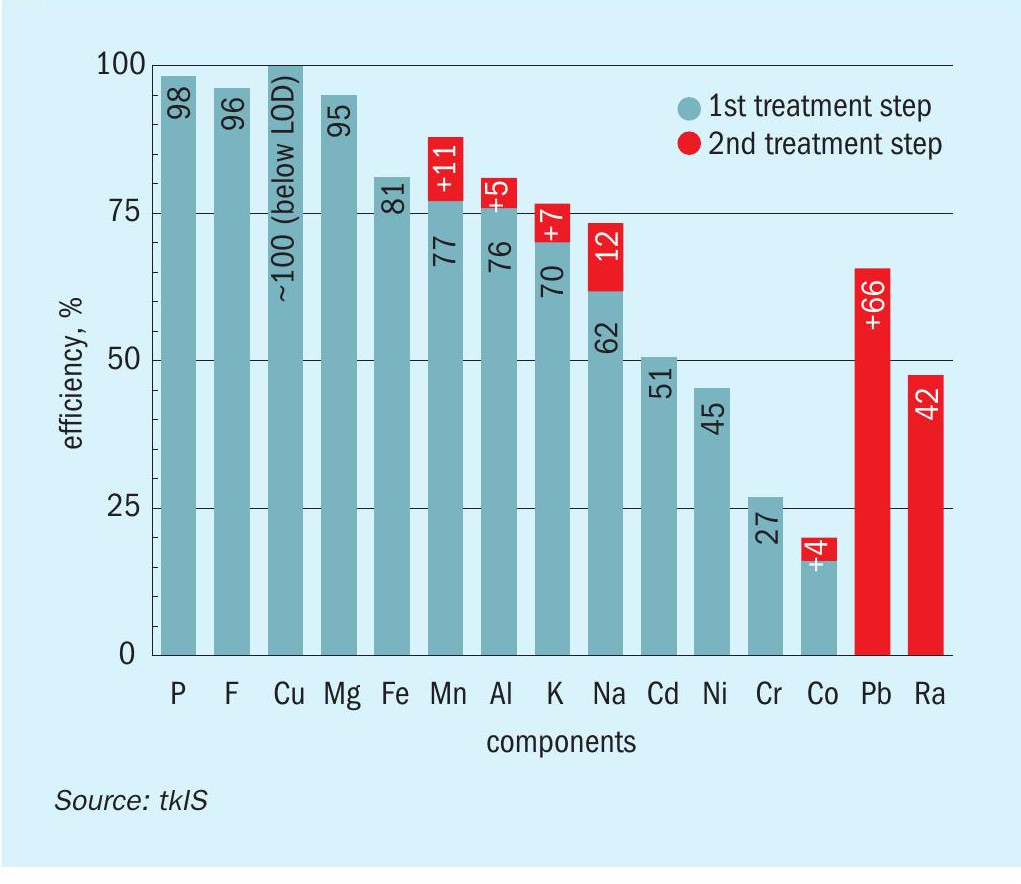
Generally, understanding the reaction kinetics of P2 O5 recovery is critical, as this holds the key to optimising the whole process. Reaction conditions have a large impact on the recovery rate, with harsh reaction conditions, for example, typically leading to shorter release periods compared to mild conditions.
The overall reduction in phosphogypsum impurities achieved by both treatment steps is shown in Fig. 5 (first treatment step in blue, second treatment step in red).
In the first treatment step (Fig. 5, blue colour), P2 O5 and fluoride are removed at efficiencies of up to 98% and 96%, respectively. In parallel with this, significant reductions in other elements (Cu, Mg, Fe, Mn etc.) are also achieved. This is highly beneficial for the potential use of phosphogypsum as a plaster industry raw material. The efficacy of this first treatment step has also been tested and confirmed on phosphogypsum generated by both sedimentary and igneous phosphate rock types.
The main aim of the second treatment step is radium removal (Fig. 5, red colour). Treatment was found to reduce radium activity by approximately 40%, down from 570 Bq/kg originally to an eventual value of 330 Bq /kg. Typically, this would be expected to reduce the ACI of phosphogypsum from 1.4 to 0.9 approximately. Further studies are nevertheless underway to improve and optimise the removal of radioactive elements, particularly for more radioactive types of phosphogypsum.
With regard to radioactivity, and despite what is achievable technically, decisions on the ultimate usage of treated phosphogypsum will still require discussions between manufacturers, users and authorities.
Outlook
Building on these positive lab-scale results, the next step of process development will scale-up capacity and optimise energy consumption. A strategy for achieving full integration of the phosphogypsum treatment process within existing production plants will also be pursued. The opportunities for plant integration will be evaluated in cooperation and partnership with interested phosphate producers.
References
Using phosphogypsum to create soil and combat climate change
The conventional way of reclaiming phosphogypsum stacks is to cover their surface with a thick layer of soil. When Nutrien began researching alternative methods of phosphogypsum stack reclamation in Alberta, Canada, in 2005, the company discovered that reclamation could be improved by mixing small amounts of soil directly into weathered phosphogypsum. This created a man-made soil known as an ‘anthrosol’.
Creating healthy soils for trees
It was found that any amount of soil mixed into weathered phosphogypsum grew larger, healthier biomass than plants grown in soil alone. Nutrien then investigated the possibility of growing trees in the phosphogypsum mix to reduce long term maintenance costs and increase sustainability – while also creating value and sequestering carbon.
Approximately a thousand hybrid poplar (Populus spp) and hybrid willow (Salix spp) cuttings were planted into a phosphogypsum/soil mix in 2015 and found to grow extremely well. Based on this success, approximately twenty hectares of phosphogypsum stacks were reclaimed and planted to high yield afforestation plantations in 2016 and 2017 following the protocols developed by the Canadian Wood Fiber Center, Natural Resources Canada.
The tree plantations established at Nutrien are predicted to sequester 30 tonnes CO2 equivalents per hectare per year.
Thus, in 20 years, the gypsum stack area reclaimed to date will sequester 12,000 tonnes of CO2 equivalents. This same area is also predicted to produce 10 oven dry tonnes/ha/year of above ground woody biomass.
Food production
The phosphogypsum/soil (anthrosol) can also be used to grow many other types of high value crops. Nutrien has established a small research garden on top of the phosphogypsum stack and has tested various flowers, fruits and vegetables such as raspberries, potatoes, tomatoes and pumpkins.
Analytical results indicate that the quality of the vegetables is the same or better than plants grown on regular soil. Future research will include expanding pollinator habitat and working with local beekeepers to investigate other opportunities to create value in situ.