Nitrogen+Syngas 377 May-Jun 2022
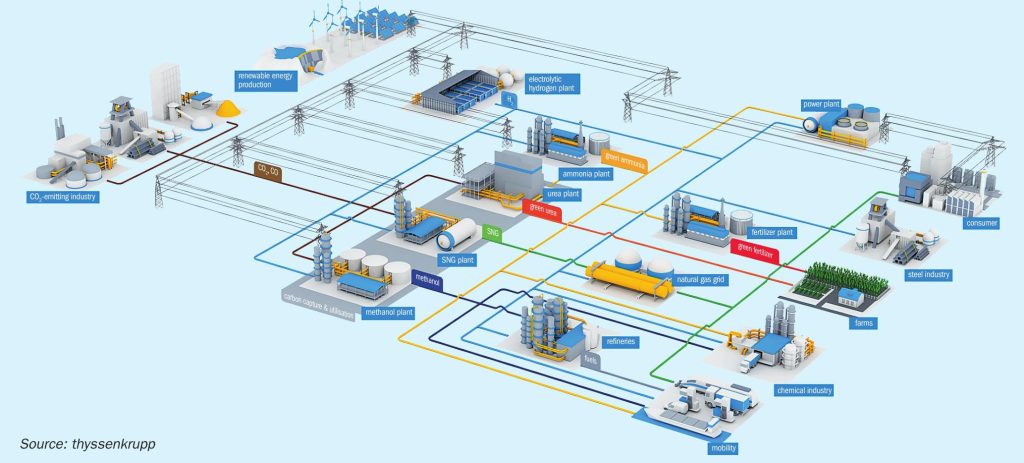
31 May 2022
Ready for large-scale decarbonisation
GREEN HYDROGEN
Ready for large-scale decarbonisation
Erika Niino-Esser of thyssenkrupp Industrial Solutions explains the importance of thyssenkrupp’s technologies for sustainable hydrogen and ammonia value chains in the global energy transition, and how they are contributing to a climate-neutral world. Several novel green hydrogen projects are also highlighted.
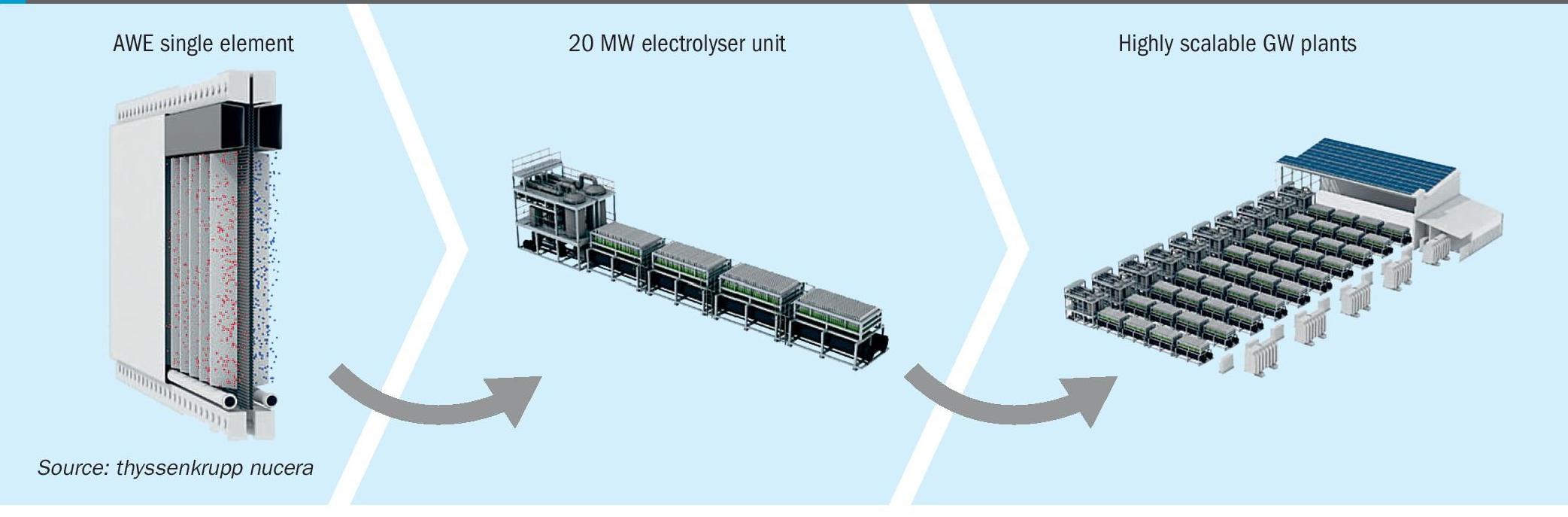
How is thyssenkrupp contributing to a climate-neutral world? Well, both companies thyssenkrupp nucera and thyssenkrupp Uhde have chemical engineering DNA and jointly offer technologies for the whole sustainable hydrogen and ammonia value chain, which are necessary for the global energy transition. thyssenkrupp nucera offers world-leading technologies for high-efficiency electrolysis plants. The company, a joint venture with Industrie De Nora, has extensive in-depth knowledge in the engineering, procurement, and construction of electrochemical plants and a strong track record of more than 600 projects with a total rating of over 10 GW already successfully installed.
With its water electrolysis technology to produce green hydrogen, the company offers an innovative solution on an industrial scale for green value chains and an industry fuelled by clean energy – a major step towards a climate-neutrality.
Water electrolysis
Water electrolysers are electrochemical devices where purified water as well as electricity is fed to produce hydrogen and oxygen. The most mature and commercially available technologies are alkaline water electrolysis (AWE) and polymer electrolyte membrane (PEM). Other types of water electrolysis use solid oxide electrolyser cell (SOEC) and anion exchange membrane (AEM) technologies. thyssenkrupp nucera offers alkaline water electrolysis and has developed modules with a standard size of 20 MW. Schematic designs of this 20 MW module as well as its key component, the electrolysis cell, are shown in Fig. 1.
During operation of the electrolyser, a mixture of demineralised water and electrolyte is fed into the electrolysis cell. When green electricity is applied, water is split into green hydrogen and oxygen. This chemical reaction inside the cell element is illustrated on the left side of the figure. The design of the cell element is based on thyssenkrupp nucera’s knowledge and experience in chlor-alkali electrolysis.
By increasing the number of these cell elements, shown in the middle of Fig. 1 as four electrolyser stacks within the 20 MW module, a larger amount of hydrogen and oxygen can be produced. In the next step, both gases are purified in the process unit section inside the module. One 20 MW module can produce a maximum of 4,000 Nm3 of hydrogen per hour with a high purity of 99.9 vol-%. Oxygen is usually a by-product in this process, which can be vented into the atmosphere.
By scaling up the alkaline water electrolyser, thyssenkrupp nucera was not only able to reduce the footprint of its plant, but it has also achieved a significant cost reduction. Picturing the current situation where electrolysers of several hundred MW are needed, the number of 20 MW modules can be increased as shown on the right of Fig. 1. These large-scale water electrolysers are key for reducing the CO2 emissions, especially in hard-to-abate industrial sectors such as the steel or chemical industries.
Hydrogen and ammonia value chain
Further technologies complementing the hydrogen value chain are provided by thyssenkrupp Uhde, which owns a huge portfolio of chemical and process technologies. These include carbon capture and utilisation technologies, such as methanol, synthetic gases, and fuels. For enabling large-scale and at the same time sustainable chemical production, the in-house technologies have been adjusted to utilise green routes and green hydrogen as the basis. These green routes as well as the industrial sectors with huge potential for decarbonisation are presented in Fig. 2.
High hopes particularly lie on the value chain for green ammonia, where thyssenkrupp Uhde has been one of the market-leading players for about 100 years. Whereas conventional ammonia production relies on grey hydrogen based on steam methane reforming of natural gas, the feedstocks for green ammonia consist of green hydrogen produced by water electrolysis using renewable energy sources. The nitrogen required for the ammonia synthesis is produced by an air separation unit. thyssenkrupp’s modularised and standardised green ammonia plant designs can be developed for different plant capacities, ranging from 50 and 6,000 t/d.
Ammonia is not only an intermediate product for fertilizer production but is also a promising hydrogen carrier when it comes to global trading. The transportation of ammonia is state-of-the-art, and the existing infrastructure can be utilised for distribution. The most cost-effective solution is direct use of ammonia by the end-user, but it is also possible to convert the ammonia back into hydrogen and nitrogen. This process is called ammonia cracking and represents the reverse reaction of ammonia production. Due to the familiarity with the process, thyssenkrupp Uhde is developing this technology for large-scale applications with the aim of being market-ready by 2025. The plant for ammonia cracking can be operated with renewable energy sources in order to regain the green hydrogen.
Green hydrogen projects
With thyssenkrupp’s capabilities to provide the whole hydrogen and ammonia value chain, there are several existing and novel projects that can be highlighted as listed below.
CF Industries in USA
At the world’s largest ammonia production complex, hosting six ammonia plants and several fertilizer plants, CF Industries in Donaldsonville is going to partially decarbonise its current ammonia production. Many of these plants have been delivered by thyssenkrupp and are based on the proven Uhde® ammonia process. The new installation of thyssenkrupp’s 20 MW water electrolyser will produce green hydrogen by utilising renewable energy and will enable an annual production of 20,000 t of green ammonia by 2023.
Element One / NEOM green hydrogen project in Saudi Arabia
Another 20 MW water electrolyser will be installed at NEOM in the Kingdom of Saudi Arabia, which is expected to start up in 2023. The project, also known as “Element One” represents a milestone project and is funded by the German government.
The same location is ideally placed for utilising both solar and wind energy and is therefore optimal for a high-capacity factor for the water electrolysis.
Targeting a production of 650 t/d of green hydrogen from 2026, a thyssenkrupp water electrolyser of more than 2 GW will be engineered, procured, and fabricated. NEOM Green Hydrogen Company, consisting of NEOM, ACWA Power and Air Products, will operate the facility for sustainable hydrogen and ammonia production.
Air Products in the USA
Due to ambitious regulations in California, there is huge potential to decarbonise the transportation sector and neighbouring state Arizona has the ideal conditions for the production of low-cost renewable energy.
Air Product’s hydrogen facility in Casa Grande, Arizona, will provide around 10 t/d of green hydrogen via thyssenkrupp’s technology from 2023. A 40 MW water electrolyser will produce the clean gas, which will be liquefied by Air Products’ proprietary technology.
The production site will also include a terminal for Air Products to distribute the product for the mobility market in California and other locations in the US. This represents a second joint project with the strategic partner Air Products.
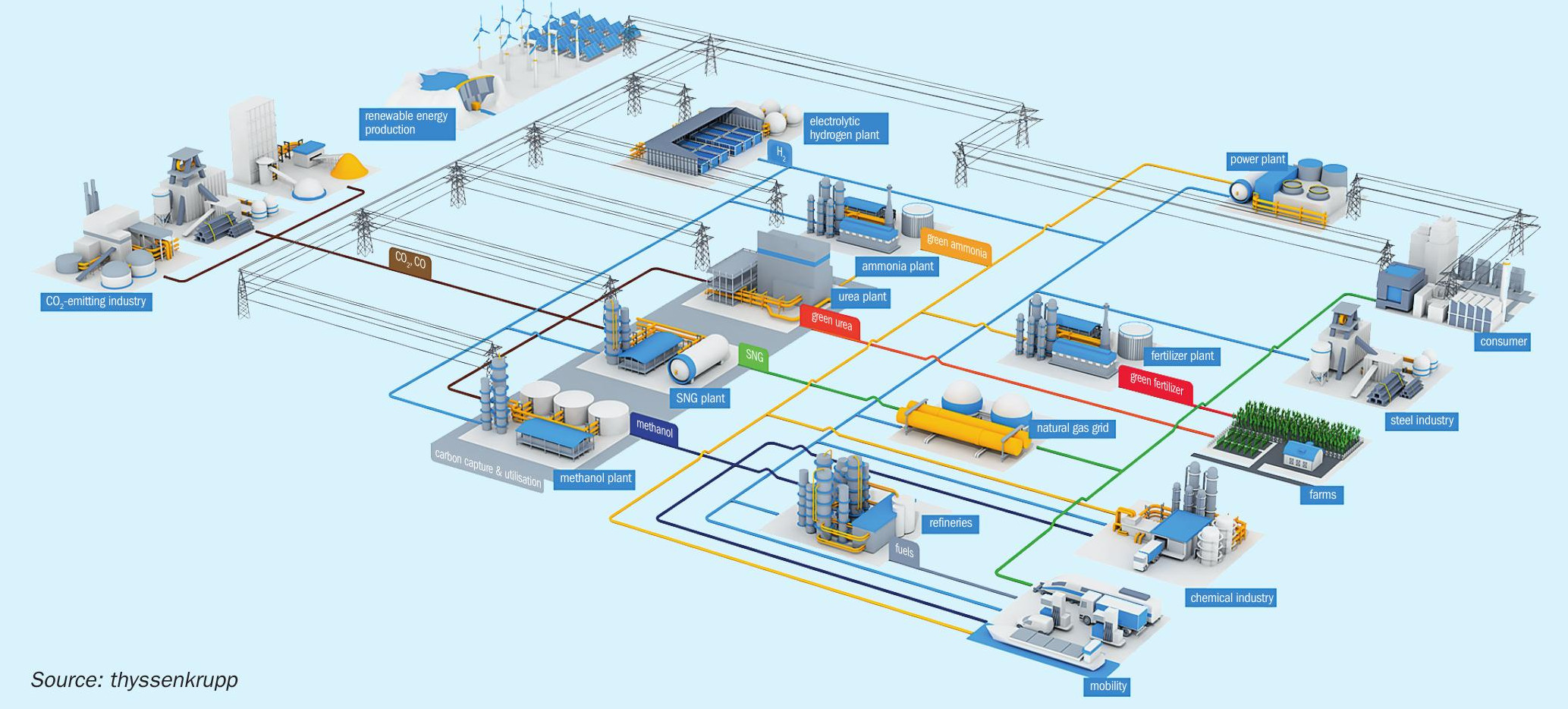
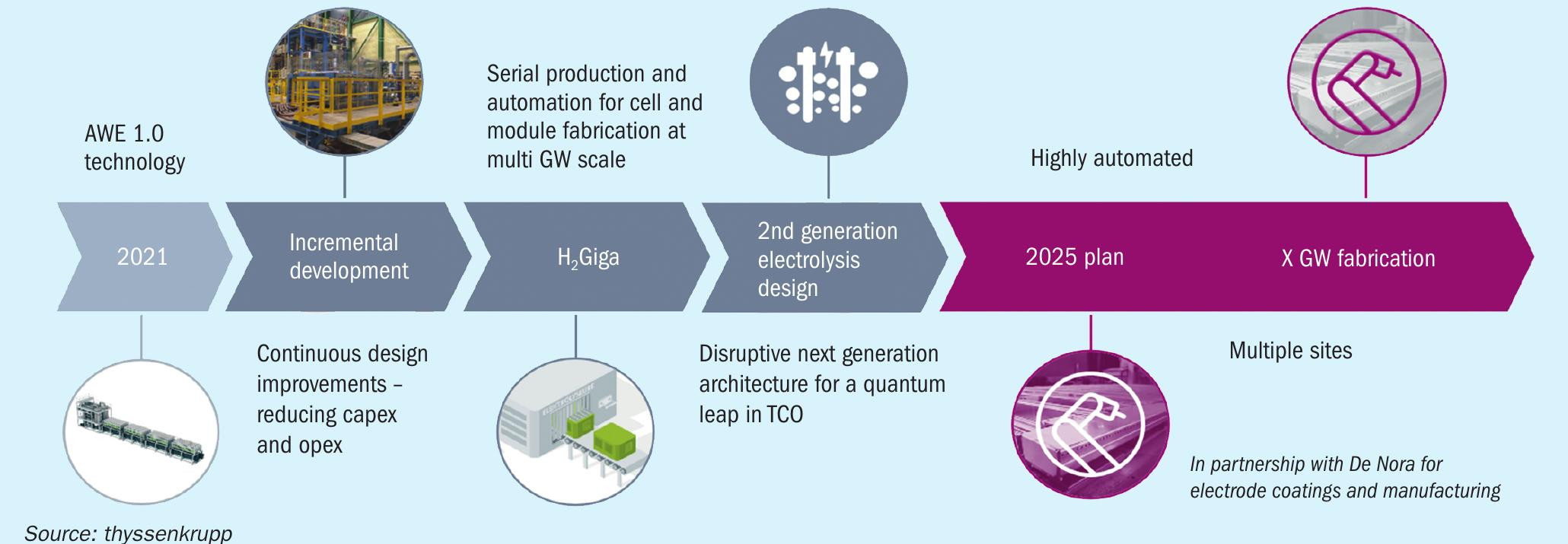
Shell in the Netherlands
A large-scale water electrolyser with a capacity of 200 MW will be installed for the large-scale project “Hydrogen Holland I” in the port of Rotterdam. This will represent a major hydrogen hub in central Europe to contribute to the energy transformation. After engineering, procurement, and fabrication of the 200 MW water electrolyser plant, the expected start-up of the plant is 2024. The source of renewable energy will be offshore wind coming from the farm Hollandse Kust (Noord). The produced green hydrogen can be transported through a pipeline with a length of around 40 km to Shell’s Energy and Chemical Park Rotterdam. With the aim of being climate neutral, reusable construction materials will be utilised where possible, and solar panels will be incorporated in the outside walls of the plant. The factory will be open to selected visitors once fully operational.
Hydrogen lead projects in Germany
thyssenkrupp is involved in all three hydrogen lead projects funded by the German Federal Ministry of Education and Research (BMBF). These projects are called H2 Mare, TransHyDE and H2 Giga, and have been initiated for the implementation of the National Hydrogen Strategy.
The aim of the H2 Mare project is to explore green hydrogen generation and other power-to-X products utilising offshore wind energy directly at sea. The direct coupling of offshore wind energy and water electrolysis will minimise production costs. thyssenkrupp is involved in the sustainable production of synthetic fuels, methane, green ammonia, and green methanol at sea for H2 Mare and conversion technologies such as ammonia cracking in TransHyDE. In the latter project several technologies for hydrogen transportation will be developed, evaluated, and demonstrated. Even though Germany will produce hydrogen within the country, a large amount needs to be imported from wind- and sun-rich regions. Therefore, an efficient infrastructure for transporting hydrogen is required.
In the H2 Giga project, the automated and serial production of water electrolysers will be enabled. Even though thyssenkrupp nucera has already built up an annual supply capacity of 1 GW of electrolysers in Germany, this is clearly just the beginning of an influential and far-reaching development process. Within four years by 2025, thyssenkrupp will expand the manufacturing capacity to 5 GW with this project.
The path forward
The product roadmap showing how thyssenkrupp nucera is going to further develop its cell elements for alkaline water electrolysers in the upcoming years is presented in Fig. 3.
The design of the current electrolysis cell is called “AWE 1.0 technology”. It is based on thyssenkrupp’s chlor-alkali experience and cell elements of this design already allow a manufacturing capacity of 1 GW. Continuous improvement and qualification are also taking place at the test plant for water electrolysis with a capacity of 2 MW, which has been in operation since April 2018. The test facility is called Carbon2Chem® and is located in Duisburg, Germany. With years of operational experience, the product has a high quality and is also highly reliable during dynamic operation.
The previously mentioned H2 Giga project aims for serial and automated production of cells as well as modules at GW scale. At the same time, the new cell design “AWE 1.x technology” will be developed to further reduce both capex and opex. The research outcome of H2 Giga will be implemented jointly with Industrie De Nora to have the automated cell and module manufacturing operational from 2025.
In parallel, a second-generation electrolysis cell called “AWE 2.0 technology” will be developed in the next four to five years. Major improvements in stack design will be implemented and can include any type of disruptive technologies in the field of water electrolysis. For the implementation of “AWE 2.0 technology” a further increase of the cell manufacturing capacity is planned, with expansion into multiple regions being considered.
Conclusion
thyssenkrupp owns a strong portfolio of chemical and process technologies, which includes large-scale water electrolysers and ammonia production plants. With these technologies being market-ready, both thyssenkrupp Uhde and thyssenkrupp nucera are ready for decarbonisation on a large scale. The large-scale green hydrogen and chemical projects with up to 2 GW capacity are just the beginning, with more to follow. n