Fertilizer International 509 Jul-Aug 2022
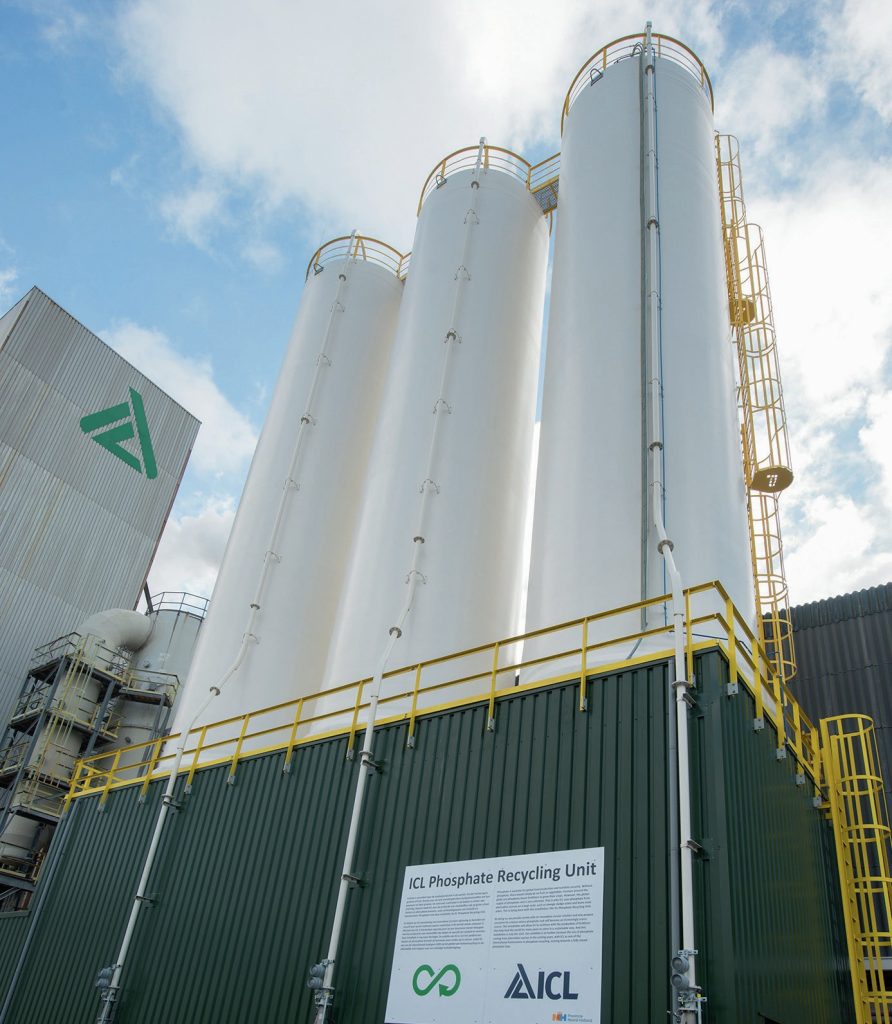
31 July 2022
Resource efficient phosphate production
PHOSPHATE TECHNOLOGY
Resource efficient phosphate production
The phosphate fertilizer industry is turning to production methods that are able to consume low-grade phosphate rock and/ or generate pure gypsum as a by-product. Gypsum-free processes, and technologies that capture phosphorus from waste streams, are also on the rise.
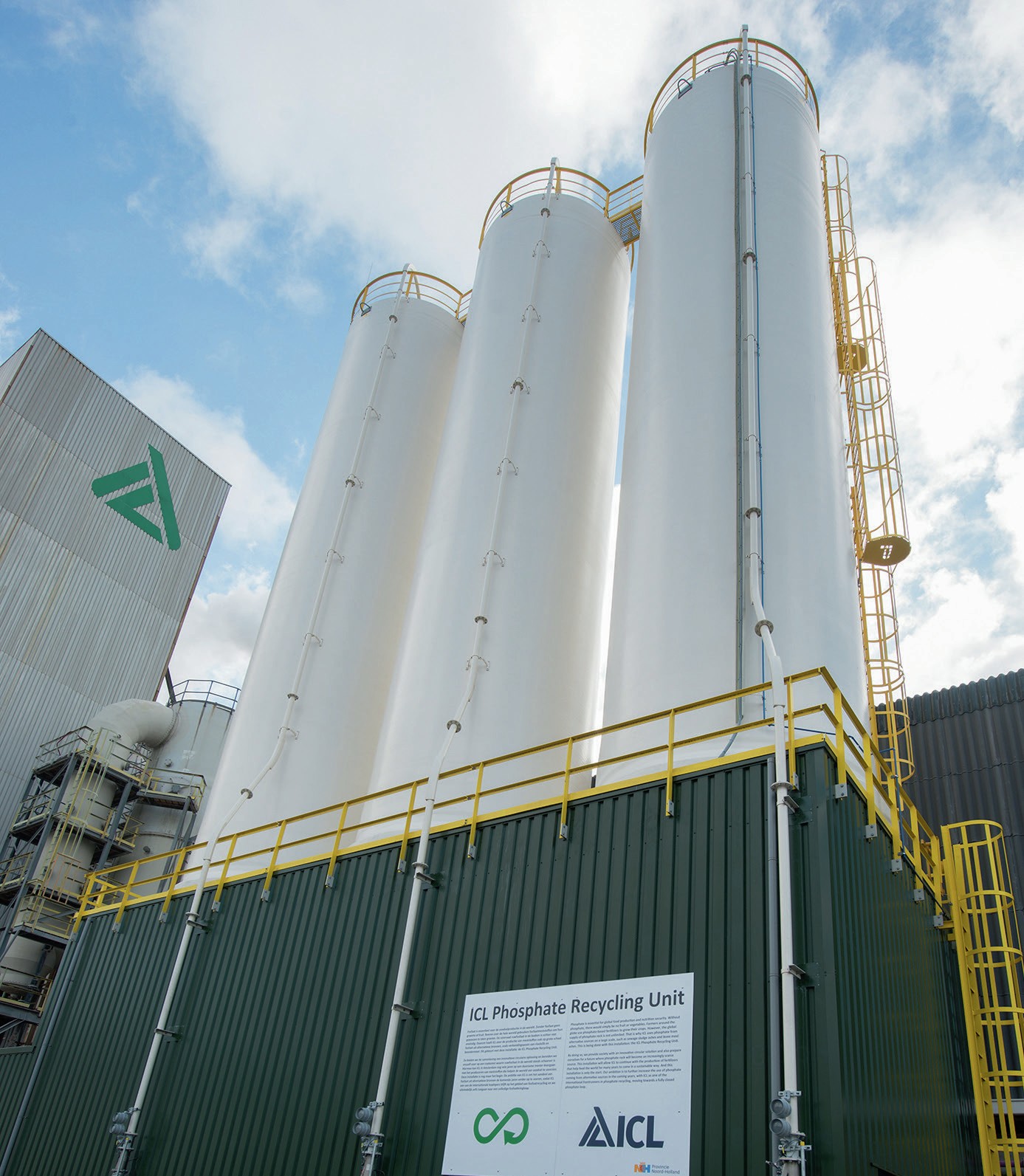
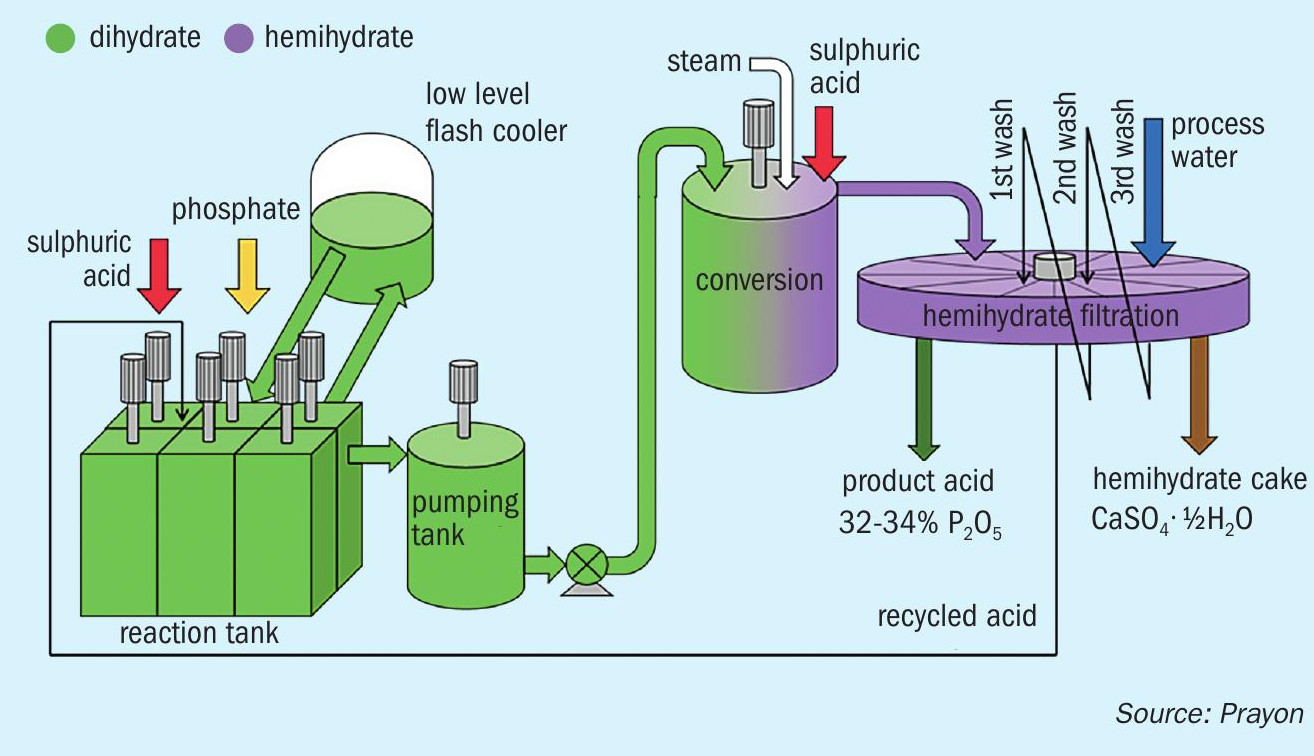
Prayon’s new DA-HF Process
Most of the world’s phosphoric acid is produced via the DH (Di-Hydrate) process route. For some years now, Prayon has been developing an improved phosphoric acid production process known as DA-HF (Dihydrate Attack-Hemihydrate Filtration). The new process (Figure 1) has been thoroughly tested at pilot-scale at Prayon’s Engis site in Belgium.
Compared to the standard DH route, Prayon’s DA-HF process has the following advantages:
- The weak product acid contains higher P2 O5 levels of up to 34 percent
- This allows merchant grade acid (MGA, 54% P2 O5 ) to be produced using smaller concentration units
- Has a higher process efficiency with P2 O5 recovery above 97 percent
- Consumes less water during washing of the calcium sulphate cake
- Yields a hemi-hydrate (HH) calcium sulphate by-product that is suitable for cement manufacture.
Unlike the very high efficiency CPP (Central Prayon Process) operated by Prayon in Engis, Belgium, only one single filtration stage is required in DA-HF. This makes DA-HF simpler and easier to operate compared to CPP. Beneficially, the process also removes undesirable cadmium at the concentration stage.
The DA-HF process has been successfully installed at Grupa Azoty’s plant in Police, Poland, as part of a revamp project (Fertilizer International 496, p52). This reference plant has demonstrated that DA-HF can be easily implemented at existing DH phosphoric acid plants with only a limited number of modifications. This first-of-itskind DA-HF plant increased:
- Plant P2 O5 capacity from 420 t/d to 500 t/d
- Its global efficiency – with total P2 O5 content in the discharged cake decreasing from 1.2 percent to 0.5 percent
- The P2 O5 content in the product acid to 32-33 percent
- The quality of the calcium sulphate by-product.
The EcoPhos and GetMoreP processes
Prayon also offers two chemical processes for beneficiating low-grade phosphate rock (Fertilizer International 500, p35):
- The EcoPhos process – an innovative acquired technology based on the use of dilute hydrochloric acid
- GetMoreP – a similar in-house technology developed by Prayon based on the use of dilute sulphuric acid.
Both processes generate dicalcium phosphate (DCP). This flexible end-product can be directly marketed as an animal feed additive. Alternatively, it can be used as a high purity intermediate feedstock (3941% P2 O5 and 32-34% CaO) for phosphoric acid plants, enabling the manufacture of a range of other phosphate products.
The EcoPhos and GetMoreP processes have a number of similarities:
- They are both modular
- They generate the same quality DCP product
- Each is capable of consuming low-grade phosphate rock.
Their main differences are:
- The stages at which impurities are removed
- The co-products are not the same due to the use of different acids to digest phosphate rock.
Prayon’s approach to phosphorus recovery
The depletion of phosphate resources raises questions about long term security of supp ly, especially in Europe. However, dependence on external primary resources – in Europe and elsewhere – could be reduced by the large-scale recovery of phosphorus from waste streams. This has dual benefits as it would also cut global phosphate losses.
The following technology options from Prayon are capable of recovering phosphorus commercially from various secondary/ waste sources:
- Recovery from phosphate beneficiation wastes (slimes, rejected rock) using the EcoPhos or GetMoreP processes
- Recycling industrial phosphoric acid waste by membrane purification
- Recovering phosphate from sewage sludge fly ash using methods such as ion exchange and nanofiltration.
Recovering phosphorus via sewage sludge incineration is highly challenging (see companion article on page 58) due to the complexity and composition of the iron- and aluminium-rich fly ashes obtained. These typically contain up to nine percent and eight percent iron and aluminium, respectively.
Prayon offers two types of recovery technologies for sewage sludge fly ash. These are selected according to the composition of the fly ash, its location and the required end-product:
- Technical-grade phosphoric acid production. This two-stage process firstly involves the digestion of fly ash in phosphoric acid, followed by the purification of the resulting solution by ion exchange and, optionally, nanofiltration. Phosphoric acid is partly recovered as the final product and partly recycled to digest more fly ash. The ion exchange resin is regenerated by hydrochloric acid. Depending on their composition, the solutions arising from regeneration can be valorised as a de-icing product (Ca/Mg Cl solutions) or sent for wastewater treatment (Al/Fe Cl solutions).
- Fertilizer-grade dicalcium phosphate (DCP) production. This process is very similar to the methods used to digest low-grade phosphate rock, as described above. The main difference is that, due to their high concentration in filtrates, both aluminium and iron need to be removed by ion exchange to obtain highquality DCP. The DCP product can be used directly as fertilizer or converted into triple superphosphate (TSP) instead.
tkIS phosphogypsum treatment process
thyssenkrupp Industrial Solutions (tkIS) has been developing a new technology that converts phosphogypsum (PG) into a valuable product for the circular economy. A two-step treatment process for reducing impurity levels in PG has been devised and tested at laboratory-scale. This has successfully achieved reduction rates of more than 95 percent for both P2 O5 and fluoride. Promisingly, the radium activity of PG was also reduced by more than 40 percent during initial tests – with higher reduction rates expected in future (Fertilizer International 501, p48).
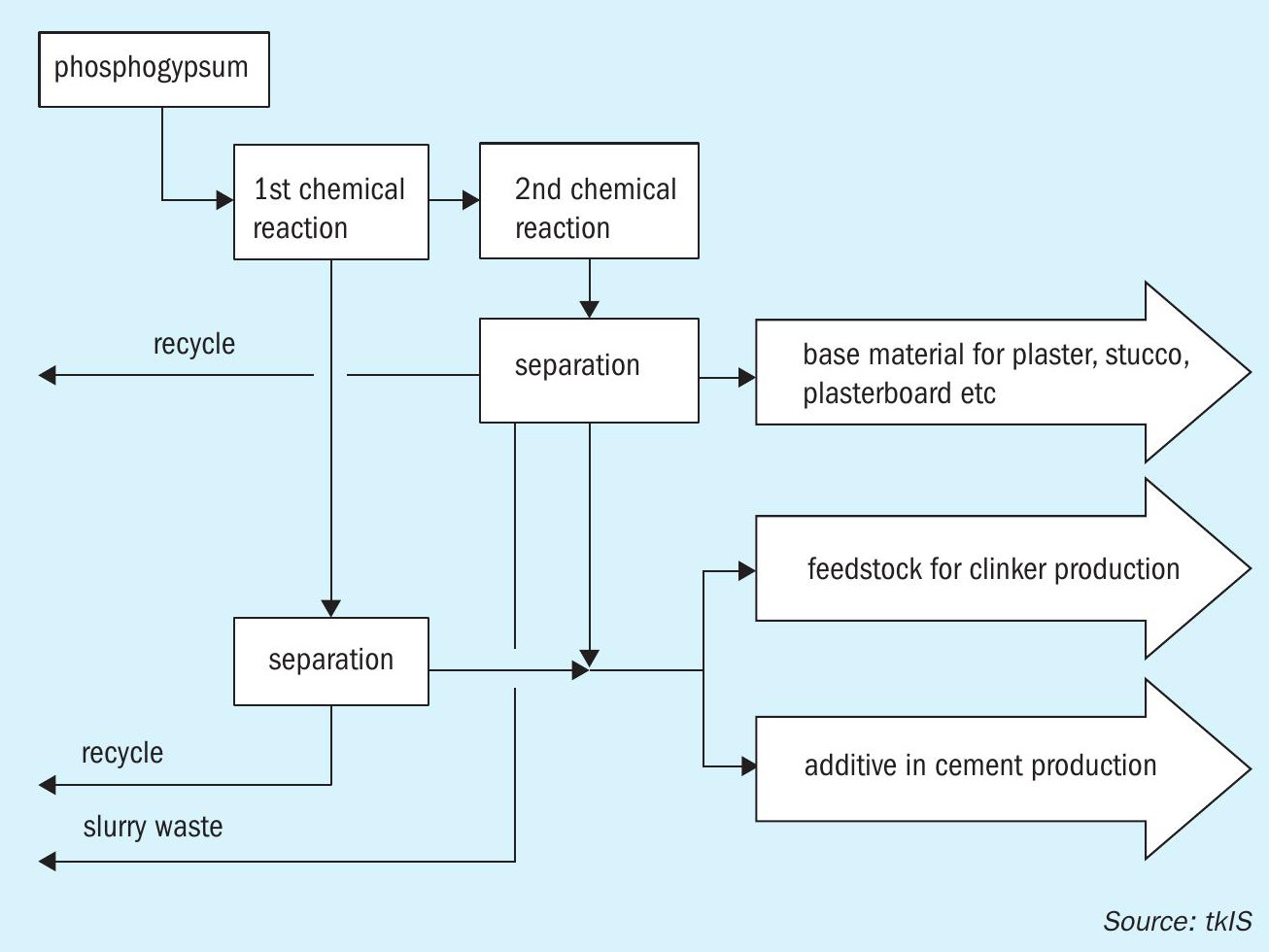
Technip Energies high recovery Diplo process
The two-step Diplo process from Technip Energies combines improved P2 O5 recovery with the operational advantages of the DH route, such as the flexibility to accept different phosphate rock types. Depending on the phosphate source, this high recovery process can digest around 97.5-98.5 percent of the P2 O5 present.
Its other benefits include:
- Process simplicity
- Ease of operation
- Low maintenance cost
- High plant availability
- Low capex.
The Diplo process can also be combined with a simple phosphogypsum purification process. This avoids the need to consume costly high-quality phosphate rock feedstock.
PG recycling and reuse
Currently, most phosphoric acid plants globally operate the DH process due to its advantages over other production routes. DH is also expected to remain the preferred production route for most phosphoric acid producers, at least in the medium-term. This suggests that increasing the recycling and reuse of phosphogypsum in future will require innovations and changes to the existing DH process.
This should favour high P2 O5 recovery technologies such as the Diplo process – due to their ability to reduce the residual P2 O5 content of phosphogypsum (PG) and generate higher quality PG suitable for industrial reuse. Industrial cases studies in Senegal and Austria have shown how PG from the Diplo process can be successfully recycled on a large scale for cement, plaster and other commercial applications – while either avoiding or minimising the need for purification prior to reuse (Fertilizer International 502, p58).
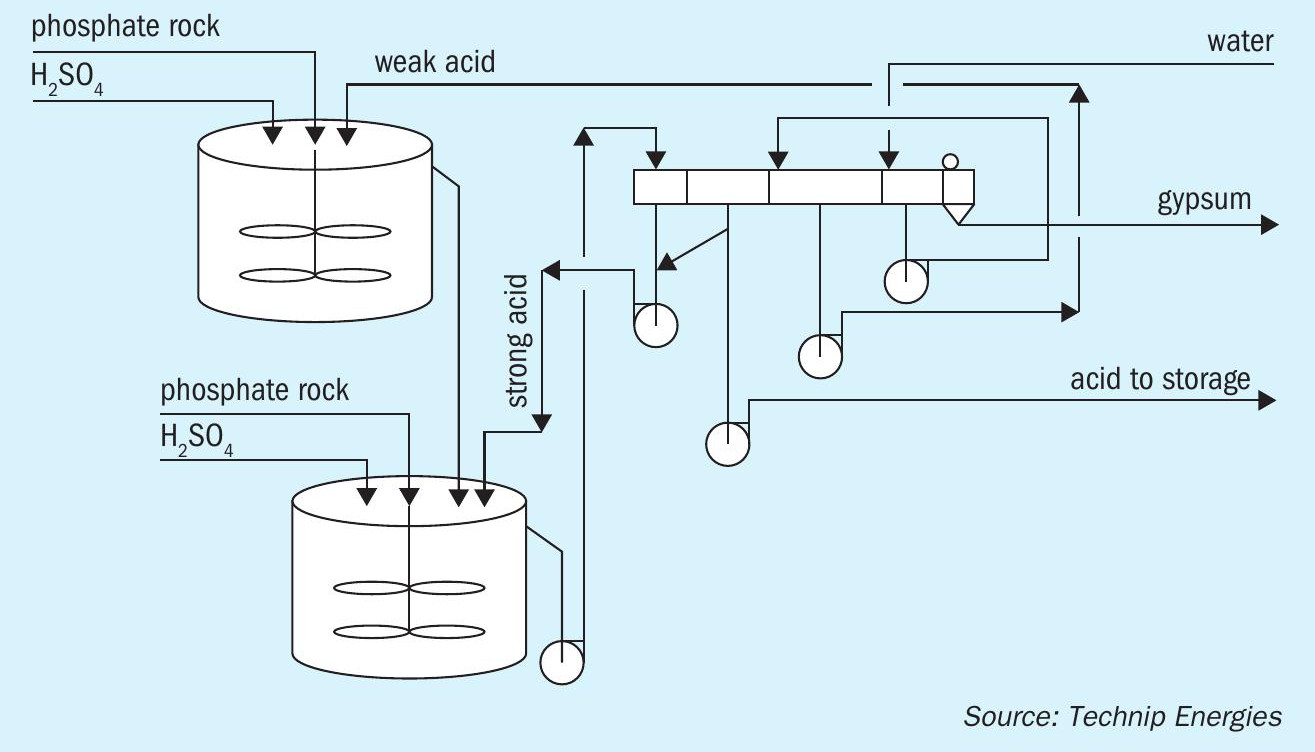
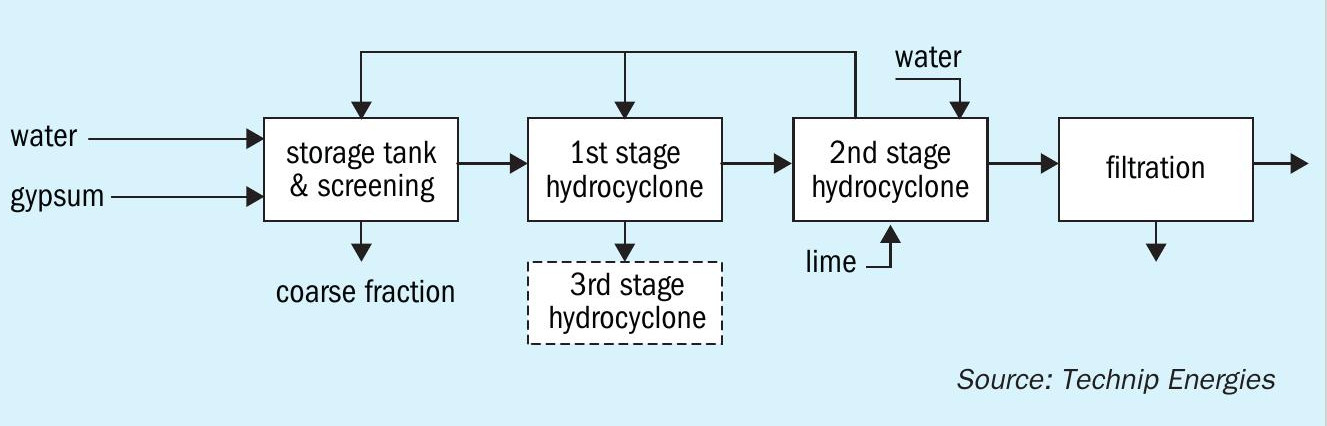
Two-stage, high yielding process
The two-stage Diplo process was developed by the French company Rhône Poulenc, the technology predecessor to Technip Energies, in the 1980s and 1990s as a new approach to DH production. The aims were two-fold: firstly, to obtain higher P2 O5 yields and, secondly, to increase the concentration of the dilute acid produced at filtration.
This new approach successfully generated both higher P2 O5 yields and acid concentration, while keeping the original operational advantages of DH production. This was of particular interest to producers in Europe who were sourcing from the merchant rock market and facing strong economic pressure to reduce their operating costs. Technip Energies has improved and refined the process subsequently.
In the Diplo process, phosphate rock is digested using two reactors in series, with each reactor being fed phosphate rock, sulphuric acid and recycled phosphoric acid in set proportions (Figure 3). This two-stage process is inherently more stable. Incorporating two separate reaction steps also allows the digestion conditions to be varied – including temperature, P2 O5 concentration, and concentration of free sulphate in the acid.
Around 70-90 percent of the phosphate rock is reacted in the first reactor. This is operated at lower P2 O5 concentration, higher temperature and with higher excess sulphuric acid. Combined, these conditions tend to reduce co-crystallised P2 O5 losses in gypsum. The remaining phosphate rock is reacted in the second reactor, increasing the P2 O5 concentration of the acid. Excess sulphuric acid in the second reactor slurry is closely regulated. This limits unreacted P2 O5 losses and avoid excess sulphate in the phosphoric acid produced.
Residual contaminants present in the phosphogypsum after filtration can be detrimental to phosphogypsum reuse, particularly for plaster manufacture. These can, however, be removed or reduced using a two- or three-stage PG treatment process (Figure 4).
This new PG treatment process from tkIS is based on the original conversion process used successfully at OSW-Krupp plants. It consists of two main steps in sequence. Each step involves a chemical reaction followed by liquid-solid separation (Figure 2).
In the first treatment step, P2 O5 and fluoride are removed at efficiencies of up to 98 percent and 96 percent, respectively. In parallel with this, significant reductions in other minor elements (Cu, Mg, Fe, Mn etc.) are also achieved. This is highly beneficial for the potential use of PG as a plaster industry raw material. The efficacy of this first treatment step has also been tested and confirmed on PG generated by both sedimentary and igneous phosphate rock types.
The main aim of the second treatment step is radium removal. This step was found to reduce radium activity by approximately 40 percent, down from 570 Bq/ kg originally to an eventual value of 330 Bq /kg. Typically, this would be expected to reduce the activity concentration index (ACI) of PG from 1.4 to 0.9 approximately. Further studies are now underway to improve and optimise the removal of radioactive elements, particularly for more radioactive types of PG.
Building on these positive lab-scale results, tkIS is carrying out process development work to scale-up capacity and optimise energy consumption. The ability to fully integrate the PG treatment process within existing production plants, through cooperation and partnership with interested phosphate producers, will be another priority (Fertilizer International 501, p48).
Novaphos produces high-quality acid
Florida-based Novaphos Inc (formerly JDCPhosphate) has successfully manufactured high-quality super-phosphoric acid (SPA) continuously using its proprietary improved hard process (IHP). This was demonstrated during prolonged operation of the company’s IHP demonstration plant in Fort Meade, Florida (Fertilizer International 494, p27).
IHP produces phosphoric acid from a low-quality phosphate rock feedstock in a kiln without creating phosphogypsum waste. Instead, the innovative process generates J-Rox, a commercially-useful aggregate, as co-product.
During operations in early 2019, Novaphos was able to continuously manufacture SPA via the IHP route using locally-sourced phosphate mine waste. This phosphate source was combined with clay and petroleum coke to provide feed for the kiln.
A high-grade SPA product was obtained (68 percent P2 O5 ) with minimal impurity levels (<2.5 percent). The process eliminated up to 90 percent of cadmium in the phosphate feed. This was captured in the plant’s pollution control scrubbing system, leaving levels of around two ppm in the SPA. The process also significantly reduced levels of lead and arsenic.
As a next step, Novaphos plans to commercially deploy IHP technology, after completing process design engineering for a full-scale production process.
“Spain’s Fertiberia has successfully developed bio-based NPK fertilizers as part of an EU-funded project.”
ICL opens phosphate recycling unit
ICL opened an innovative phosphate recycling unit at its Amsterdam fertilizer production site in 2019. In an industry first, the new unit allows ICL to incorporate recovered phosphate from secondary sources in the industrial-scale production of phosphate-based fertilizers (Fertilizer International 494, p27).
The unit, which uses large-scale alternative sources of phosphate such as sewage sludge ashes and bone meal ashes, was formally opened by local Dutch officials in March 2019. ICL says the unit is a “circular innovation” that shows its commitment to sustainability.
There are plans to expand this pathfinder project in future: “Our ambition is to further increase the use of phosphate coming from alternative sources in the coming years, with ICL as one of the international frontrunners in phosphate recycling,” the company said.
ICL sells recovered nutrients
In 2018, ICL entered into a long-term sales and distribution agreement with Vancouver-headquartered Ostara Nutrient Recovery Technologies. As part of the new agreement, ICL now markets and sells Ostara’s Crystal Green, a struvite-based phosphate fertilizer, into the EU and UK, supplying the turf and lawncare markets (Fertilizer International 494, p27).
ICL sells Cystal Green under the name Sierrablen Plus. Its sales and distribution agreement with Ostara was expanded in 2020 to include Australia and New Zealand and the Nordic countries.
Crystal Green is recovered from municipal wastewater at 15 plants worldwide using Ostara’s Pearl technology. It is a continuous-release fertilizer incorporating the company’s trademarked ‘root activated’ phosphorus.
Advantageously, Crystal Green contains virtually no cadmium or other heavy metals. It also only releases phosphorus, nitrogen and magnesium in response to the organic acids produced by growing roots. This ensures that phosphorus is available for uptake when required by plants, while at the same time reducing the environmental impact caused by leaching and nutrient run-off.
Fertiberia targets nutrient recovery
Spain’s Fertiberia has developed new bio-based NPK fertilizers as part of the EU-funded NewFert project. These were manufactured at pilot scale and successfully incorporated into commercial fertiliser production (Fertilizer International 494, p34).
The project validated the following three nutrient recovery processes at pilot plant scale:
- Phosphorus recovery from ashes via the DMphos process.
- Phosphorus and nitrogen recovery from pig slurry. These were extracted and crystallised as struvite using biological acidification.
- Nitrogen recovery and organic matter removal from pig slurry using bio-electrochemical systems (BES).
The DMPhos process extracts phosphorus present in ashes sourced from agriculture, the food industry and wastewater treatment plants and makes this plant-available. The ashes are firstly chemically treated by acid leaching and, after neutralisation, phosphate products (monocalcium phosphate and dicalcium phosphate) are then generated using a thermally-efficient reactor.
The NewFert project achieved the following results:
- The development of a new family of NPK fertilizers
- 15 percent of the nutrient content of these NPK products was derived from bio-based materials
- 100 percent of their nutrient content is plant-available
- More than 80 percent of their nutrient content is water-soluble
- At least 10 percent of the combined nitrogen (N) and phosphorus (P2 O5 ) content is bio-based.
The performance of these partly bio-based formulations was validated using greenhouse trials to determine crop yields.
Building on these positive results, a new project B-Ferst was launched in May 2019. Its main aim is to fully implement NewFert’s bio-refining technologies and produce eight new bio-based fertilizers at industrial scale.
From wastewater to liquid fertilizer
Fertiberia’s engineering subsidiary, Incro, S.A., has successfully transformed industrial wastewater into a liquid fertilizer (almost 13% P2 O5 and cadmium-free) as part of the flagship Oleofat project. This pioneering Spanish project also recycles water for farming and industrial purposes (Fertilizer International 494, p37).
The liquid fertilizer is manufactured using Incro’s proprietary mechanical vapour compression (MVC) technology to obtain a valuable concentrate and a clean distillate from the wastewater (Figure 5). This unit incorporates a highly efficient and low operating cost evaporator. Its dual-use design allows treatment with either sulphuric or nitric acid, depending on acid market prices and/or the end-destination of the concentrate.
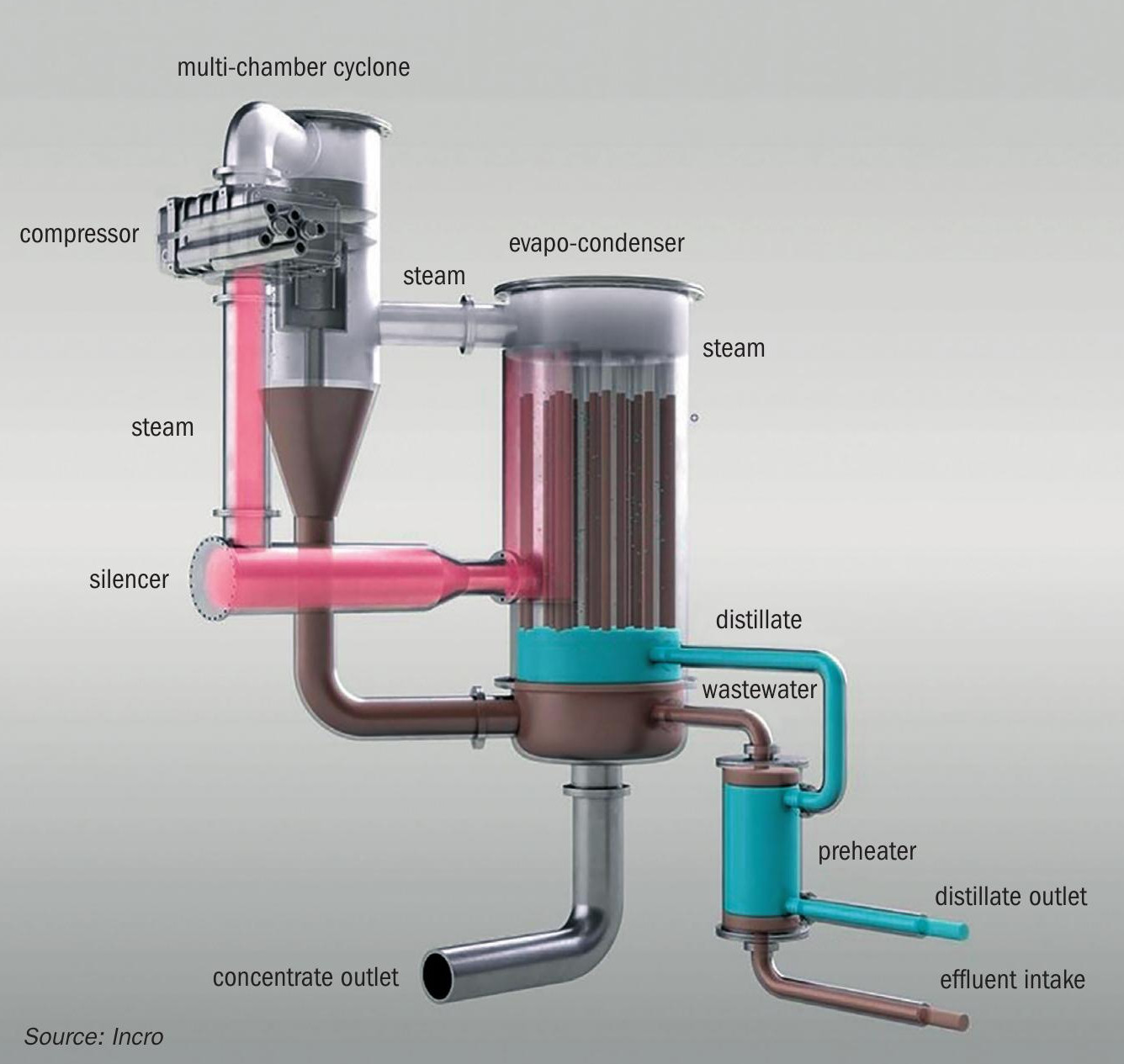
The concentrate obtained is suitable for use as a liquid NPK fertilizer, containing 4.0 percent nitrogen (as nitrate), 12.9 percent phosphorus (P2 O5 ), 0.7 percent potassium (K2 O) and 17.3 percent organic carbon, while also being free of heavy metals and pathogens. Its nitrate content is derived from the nitric acid used to extract the phosphate from the bio-waste. Incro’s MVC unit has the annual capacity to produce 3,000 tonnes of liquid fertilizer from around 10,000 tonnes of wastewater.